Page 122 of 557
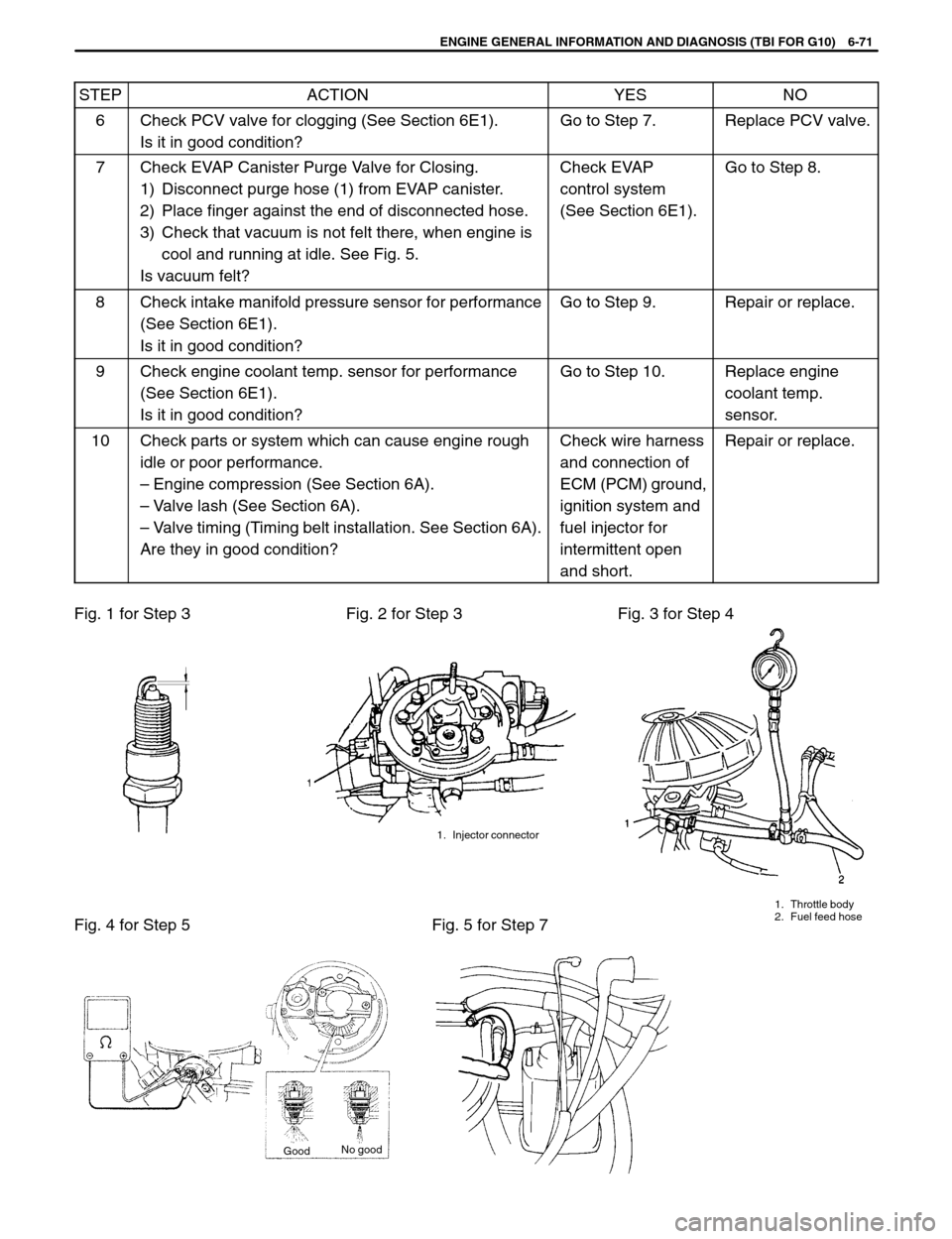
ENGINE GENERAL INFORMATION AND DIAGNOSIS (TBI FOR G10) 6-71
1. Throttle body
2. Fuel feed hose
GoodNo good1. Injector connector
STEPACTIONYESNO
6Check PCV valve for clogging (See Section 6E1).
Is it in good condition?Go to Step 7.Replace PCV valve.
7Check EVAP Canister Purge Valve for Closing.
1) Disconnect purge hose (1) from EVAP canister.
2) Place finger against the end of disconnected hose.
3) Check that vacuum is not felt there, when engine is
cool and running at idle. See Fig. 5.
Is vacuum felt?Check EVAP
control system
(See Section 6E1).Go to Step 8.
8Check intake manifold pressure sensor for performance
(See Section 6E1).
Is it in good condition?Go to Step 9.Repair or replace.
9Check engine coolant temp. sensor for performance
(See Section 6E1).
Is it in good condition?Go to Step 10.Replace engine
coolant temp.
sensor.
10Check parts or system which can cause engine rough
idle or poor performance.
–Engine compression (See Section 6A).
–Valve lash (See Section 6A).
–Valve timing (Timing belt installation. See Section 6A).
Are they in good condition?Check wire harness
and connection of
ECM (PCM) ground,
ignition system and
fuel injector for
intermittent open
and short.Repair or replace.
Fig. 1 for Step 3 Fig. 2 for Step 3 Fig. 3 for Step 4
Fig. 4 for Step 5 Fig. 5 for Step 7
Page 124 of 557
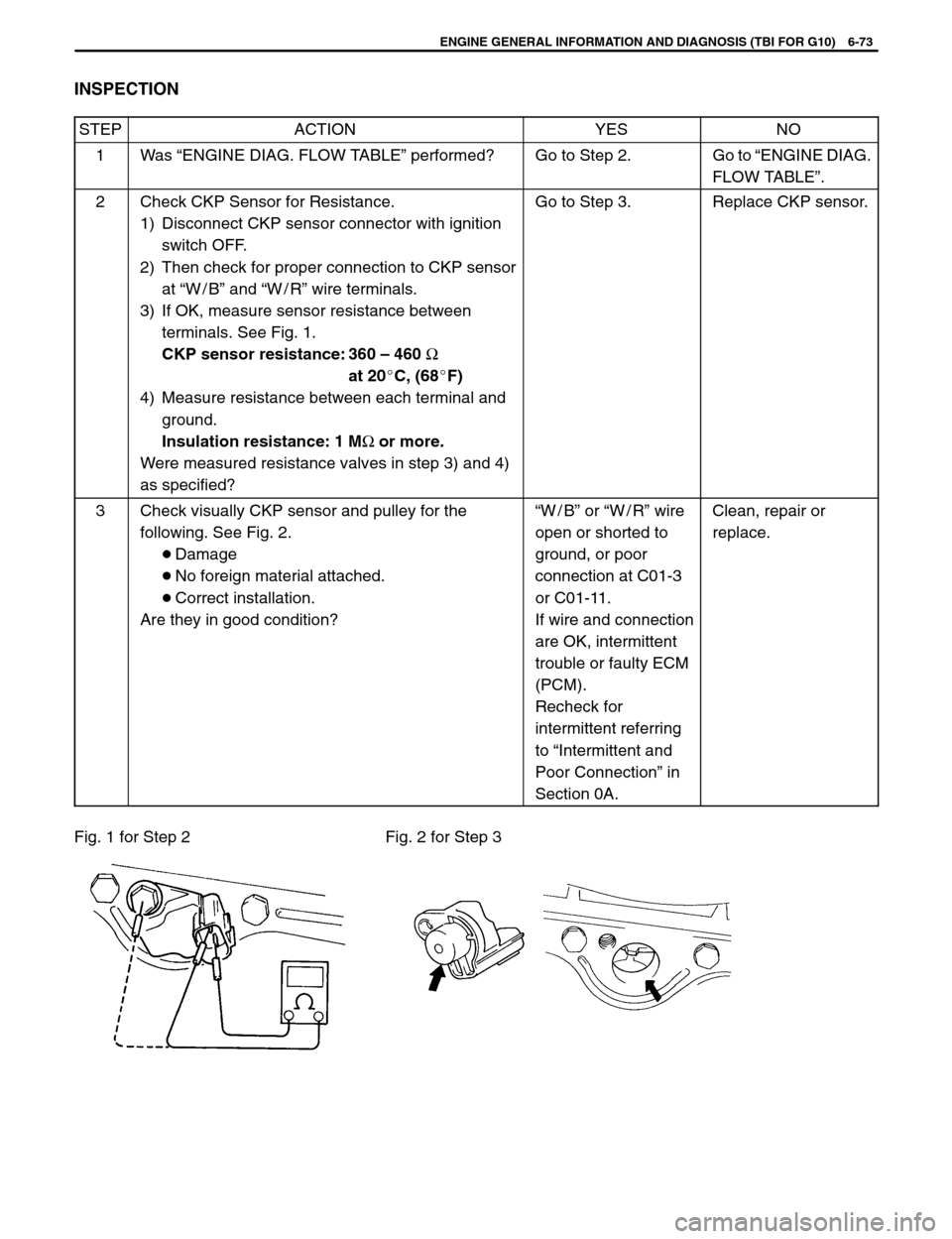
ENGINE GENERAL INFORMATION AND DIAGNOSIS (TBI FOR G10) 6-73
INSPECTION
STEPACTIONYESNO
1Was “ENGINE DIAG. FLOW TABLE” performed?Go to Step 2.Go to “ENGINE DIAG.
FLOW TABLE”.
2Check CKP Sensor for Resistance.
1) Disconnect CKP sensor connector with ignition
switch OFF.
2) Then check for proper connection to CKP sensor
at “W/B” and “W/R” wire terminals.
3) If OK, measure sensor resistance between
terminals. See Fig. 1.
CKP sensor resistance: 360 – 460 Ω
at 20C, (68F)
4) Measure resistance between each terminal and
ground.
Insulation resistance: 1 MΩ or more.
Were measured resistance valves in step 3) and 4)
as specified?Go to Step 3.Replace CKP sensor.
3Check visually CKP sensor and pulley for the
following. See Fig. 2.
Damage
No foreign material attached.
Correct installation.
Are they in good condition?“W/B” or “W/R” wire
open or shorted to
ground, or poor
connection at C01-3
or C01-11.
If wire and connection
are OK, intermittent
trouble or faulty ECM
(PCM).
Recheck for
intermittent referring
to “Intermittent and
Poor Connection” in
Section 0A.Clean, repair or
replace.
Fig. 1 for Step 2 Fig. 2 for Step 3
Page 126 of 557
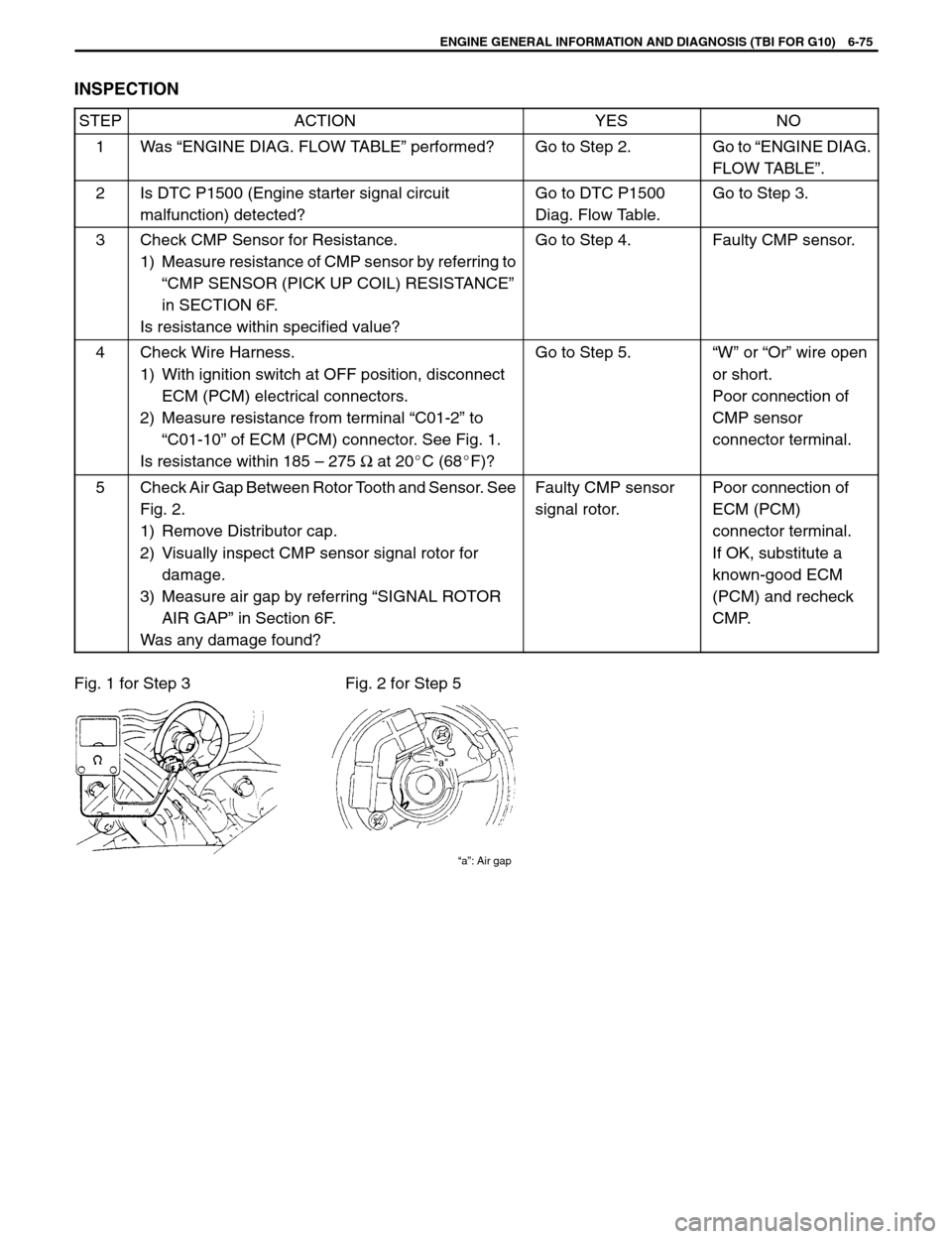
ENGINE GENERAL INFORMATION AND DIAGNOSIS (TBI FOR G10) 6-75
Fig. 1 for Step 3 Fig. 2 for Step 5
“a”: Air gap
INSPECTION
STEPACTIONYESNO
1Was “ENGINE DIAG. FLOW TABLE” performed?Go to Step 2.Go to “ENGINE DIAG.
FLOW TABLE”.
2Is DTC P1500 (Engine starter signal circuit
malfunction) detected?Go to DTC P1500
Diag. Flow Table.Go to Step 3.
3Check CMP Sensor for Resistance.
1) Measure resistance of CMP sensor by referring to
“CMP SENSOR (PICK UP COIL) RESISTANCE”
in SECTION 6F.
Is resistance within specified value?Go to Step 4.Faulty CMP sensor.
4Check Wire Harness.
1) With ignition switch at OFF position, disconnect
ECM (PCM) electrical connectors.
2) Measure resistance from terminal “C01-2” to
“C01-10” of ECM (PCM) connector. See Fig. 1.
Is resistance within 185 – 275 Ω at 20C (68F)?Go to Step 5.“W” or “Or” wire open
or short.
Poor connection of
CMP sensor
connector terminal.
5Check Air Gap Between Rotor Tooth and Sensor. See
Fig. 2.
1) Remove Distributor cap.
2) Visually inspect CMP sensor signal rotor for
damage.
3) Measure air gap by referring “SIGNAL ROTOR
AIR GAP” in Section 6F.
Was any damage found?Faulty CMP sensor
signal rotor.Poor connection of
ECM (PCM)
connector terminal.
If OK, substitute a
known-good ECM
(PCM) and recheck
CMP.
Page 130 of 557
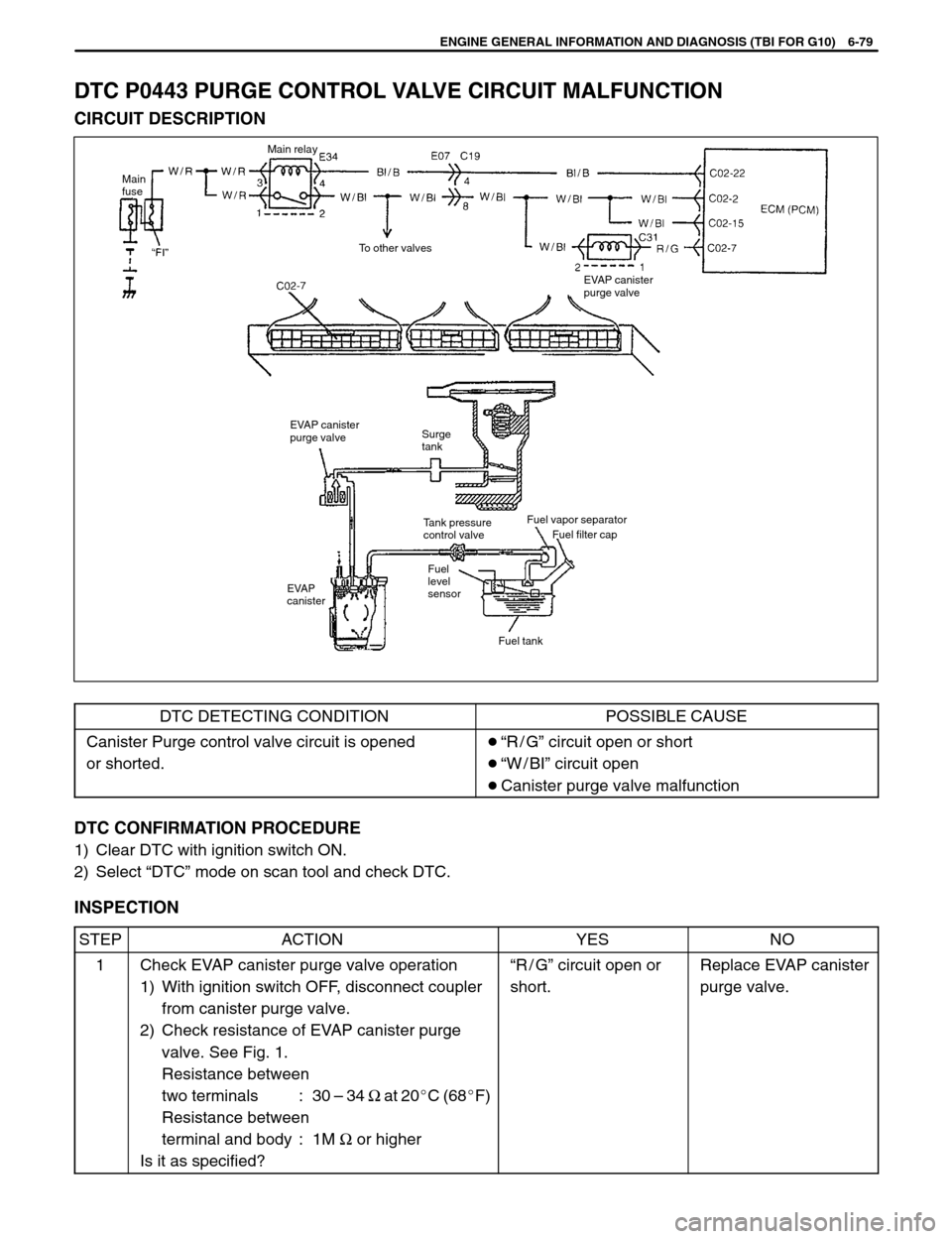
ENGINE GENERAL INFORMATION AND DIAGNOSIS (TBI FOR G10) 6-79
Main
fuseMain relay
To other valves
EVAP canister
purge valve
EVAP canister
purge valveSurge
tank
Tank pressure
control valveFuel vapor separator
Fuel filter cap
Fuel
level
sensor
Fuel tank EVAP
canister
DTC P0443 PURGE CONTROL VALVE CIRCUIT MALFUNCTION
CIRCUIT DESCRIPTION
DTC DETECTING CONDITIONPOSSIBLE CAUSE
Canister Purge control valve circuit is opened
or shorted.“R/G” circuit open or short
“W/BI” circuit open
Canister purge valve malfunction
DTC CONFIRMATION PROCEDURE
1) Clear DTC with ignition switch ON.
2) Select “DTC” mode on scan tool and check DTC.
INSPECTION
STEPACTIONYESNO
1Check EVAP canister purge valve operation
1) With ignition switch OFF, disconnect coupler
from canister purge valve.
2) Check resistance of EVAP canister purge
valve. See Fig. 1.
Resistance between
two terminals : 30 – 34 Ω at 20C (68F)
Resistance between
terminal and body : 1M Ω or higher
Is it as specified?“R/G” circuit open or
short.Replace EVAP canister
purge valve.
Page 134 of 557
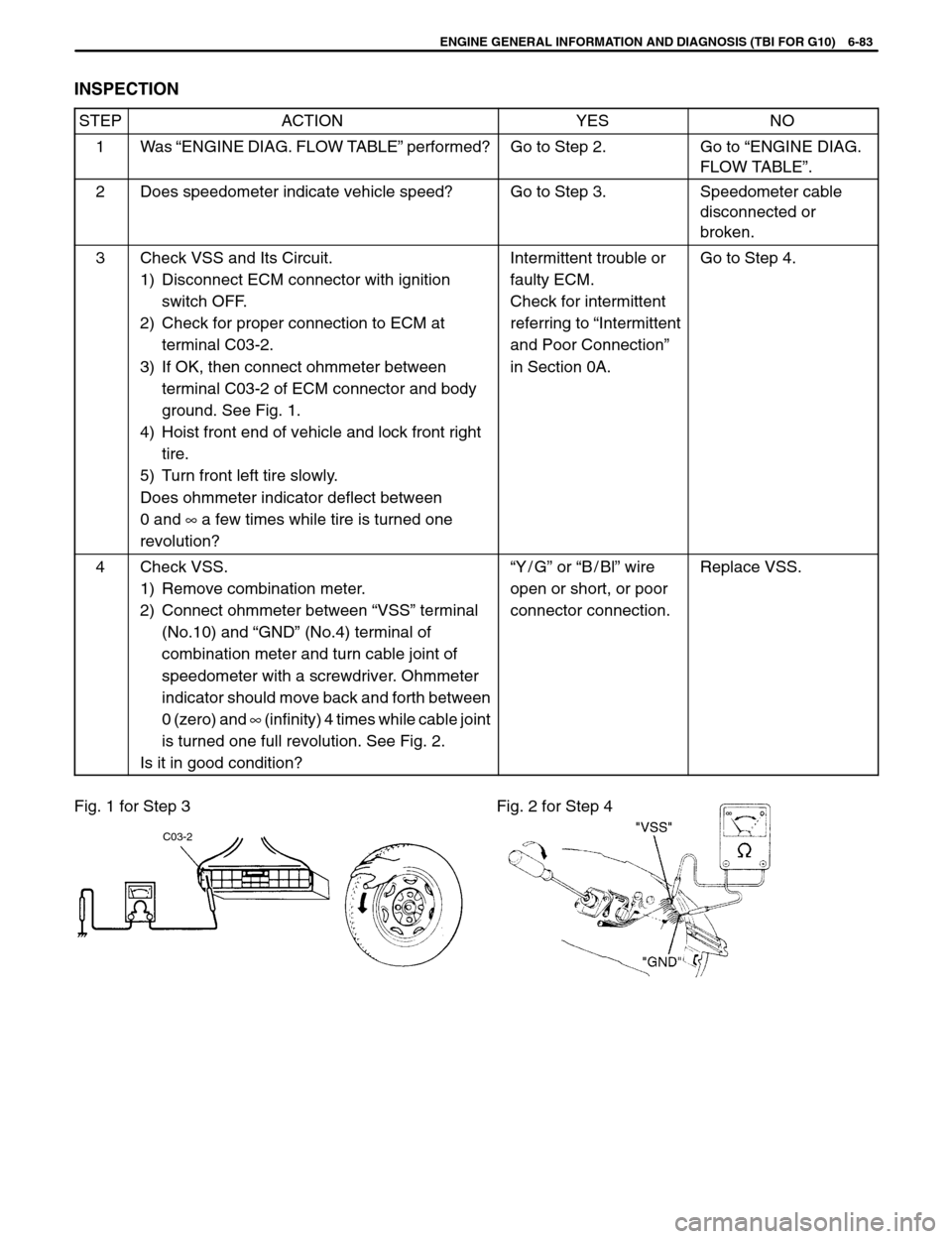
ENGINE GENERAL INFORMATION AND DIAGNOSIS (TBI FOR G10) 6-83
Fig. 1 for Step 3 Fig. 2 for Step 4
C03-2
INSPECTION
STEPACTIONYESNO
1Was “ENGINE DIAG. FLOW TABLE” performed?Go to Step 2.Go to “ENGINE DIAG.
FLOW TABLE”.
2Does speedometer indicate vehicle speed?Go to Step 3.Speedometer cable
disconnected or
broken.
3Check VSS and Its Circuit.
1) Disconnect ECM connector with ignition
switch OFF.
2) Check for proper connection to ECM at
terminal C03-2.
3) If OK, then connect ohmmeter between
terminal C03-2 of ECM connector and body
ground. See Fig. 1.
4) Hoist front end of vehicle and lock front right
tire.
5) Turn front left tire slowly.
Does ohmmeter indicator deflect between
0 and ∞ a few times while tire is turned one
revolution?Intermittent trouble or
faulty ECM.
Check for intermittent
referring to “Intermittent
and Poor Connection”
in Section 0A.Go to Step 4.
4Check VSS.
1) Remove combination meter.
2) Connect ohmmeter between “VSS” terminal
(No.10) and “GND” (No.4) terminal of
combination meter and turn cable joint of
speedometer with a screwdriver. Ohmmeter
indicator should move back and forth between
0 (zero) and ∞ (infinity) 4 times while cable joint
is turned one full revolution. See Fig. 2.
Is it in good condition?“Y / G” or “B / Bl” wire
open or short, or poor
connector connection.Replace VSS.
Page 136 of 557
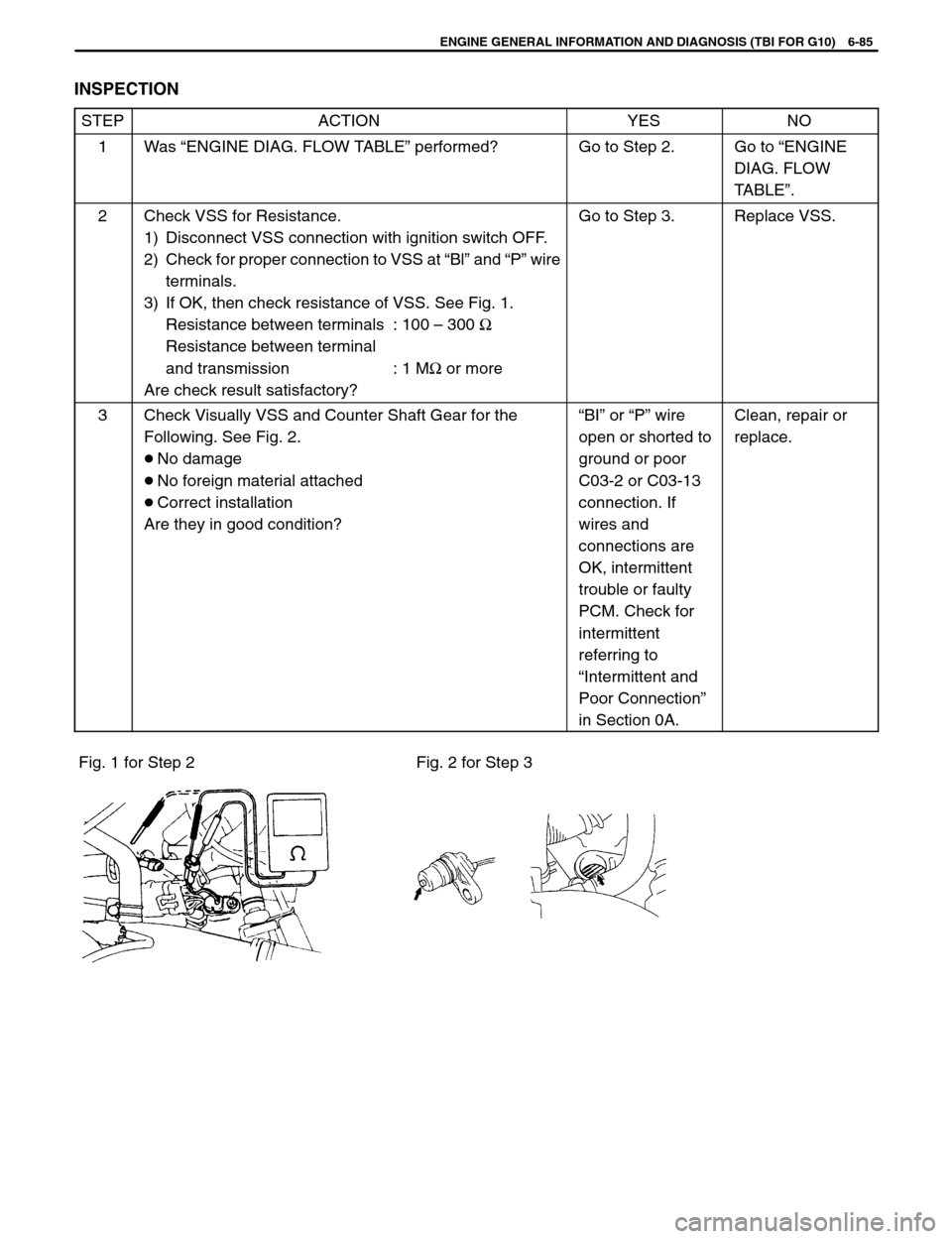
ENGINE GENERAL INFORMATION AND DIAGNOSIS (TBI FOR G10) 6-85
Fig. 1 for Step 2 Fig. 2 for Step 3
INSPECTION
STEPACTIONYESNO
1Was “ENGINE DIAG. FLOW TABLE” performed?Go to Step 2.Go to “ENGINE
DIAG. FLOW
TABLE”.
2Check VSS for Resistance.
1) Disconnect VSS connection with ignition switch OFF.
2) Check for proper connection to VSS at “Bl” and “P” wire
terminals.
3) If OK, then check resistance of VSS. See Fig. 1.
Resistance between terminals : 100 – 300 Ω
Resistance between terminal
and transmission : 1 MΩ or more
Are check result satisfactory?Go to Step 3.Replace VSS.
3Check Visually VSS and Counter Shaft Gear for the
Following. See Fig. 2.
No damage
No foreign material attached
Correct installation
Are they in good condition?“BI” or “P” wire
open or shorted to
ground or poor
C03-2 or C03-13
connection. If
wires and
connections are
OK, intermittent
trouble or faulty
PCM. Check for
intermittent
referring to
“Intermittent and
Poor Connection”
in Section 0A.Clean, repair or
replace.
Page 137 of 557
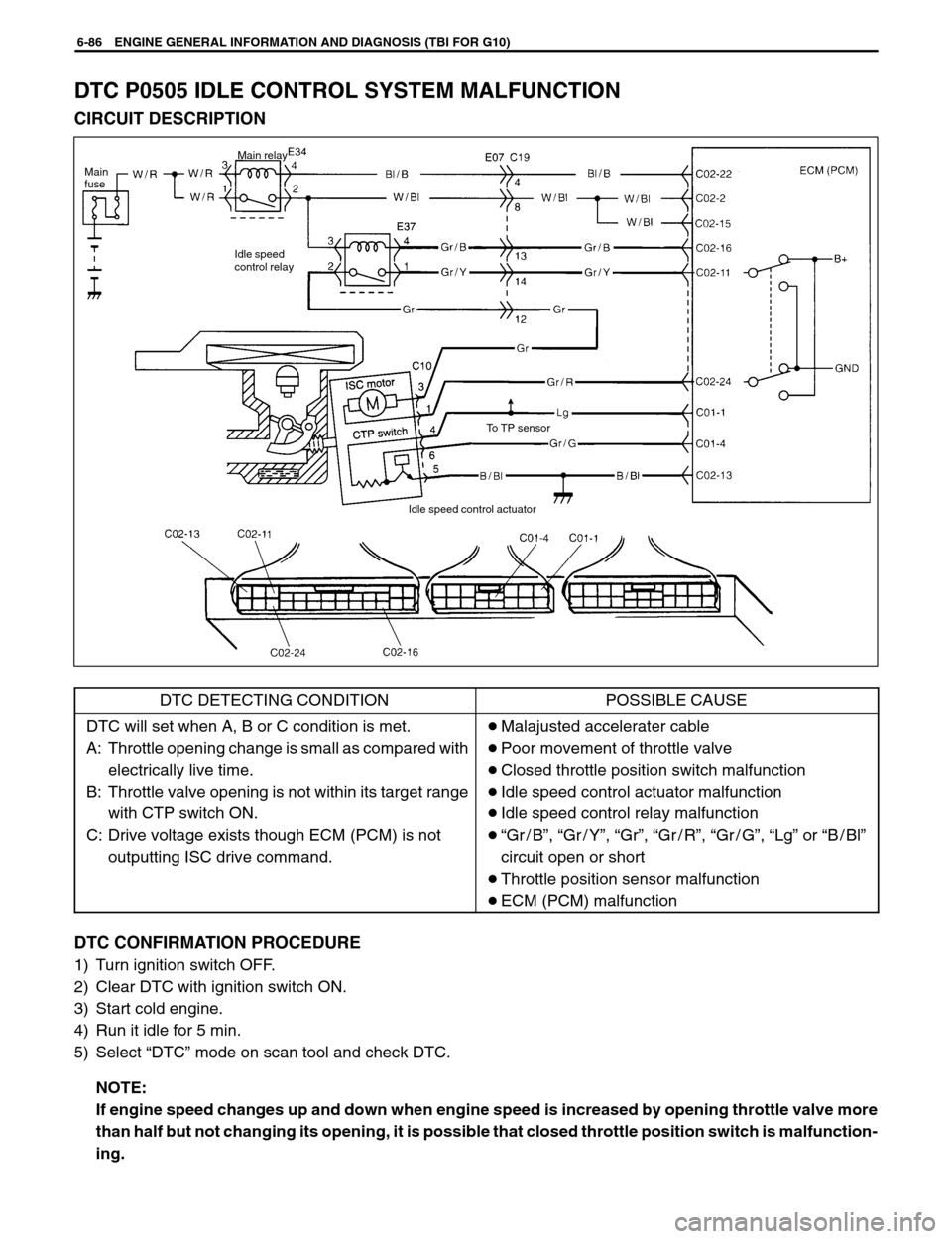
Main
fuseMain relay
Idle speed
control relay
To TP sensor
Idle speed control actuator
6-86 ENGINE GENERAL INFORMATION AND DIAGNOSIS (TBI FOR G10)
DTC P0505 IDLE CONTROL SYSTEM MALFUNCTION
CIRCUIT DESCRIPTION
DTC DETECTING CONDITIONPOSSIBLE CAUSE
DTC will set when A, B or C condition is met.
A: Throttle opening change is small as compared with
electrically live time.
B: Throttle valve opening is not within its target range
with CTP switch ON.
C: Drive voltage exists though ECM (PCM) is not
outputting ISC drive command.Malajusted accelerater cable
Poor movement of throttle valve
Closed throttle position switch malfunction
Idle speed control actuator malfunction
Idle speed control relay malfunction
“Gr / B”, “Gr / Y”, “Gr”, “Gr / R”, “Gr / G”, “Lg” or “B/Bl”
circuit open or short
Throttle position sensor malfunction
ECM (PCM) malfunction
DTC CONFIRMATION PROCEDURE
1) Turn ignition switch OFF.
2) Clear DTC with ignition switch ON.
3) Start cold engine.
4) Run it idle for 5 min.
5) Select “DTC” mode on scan tool and check DTC.
NOTE:
If engine speed changes up and down when engine speed is increased by opening throttle valve more
than half but not changing its opening, it is possible that closed throttle position switch is malfunction-
ing.
Page 138 of 557
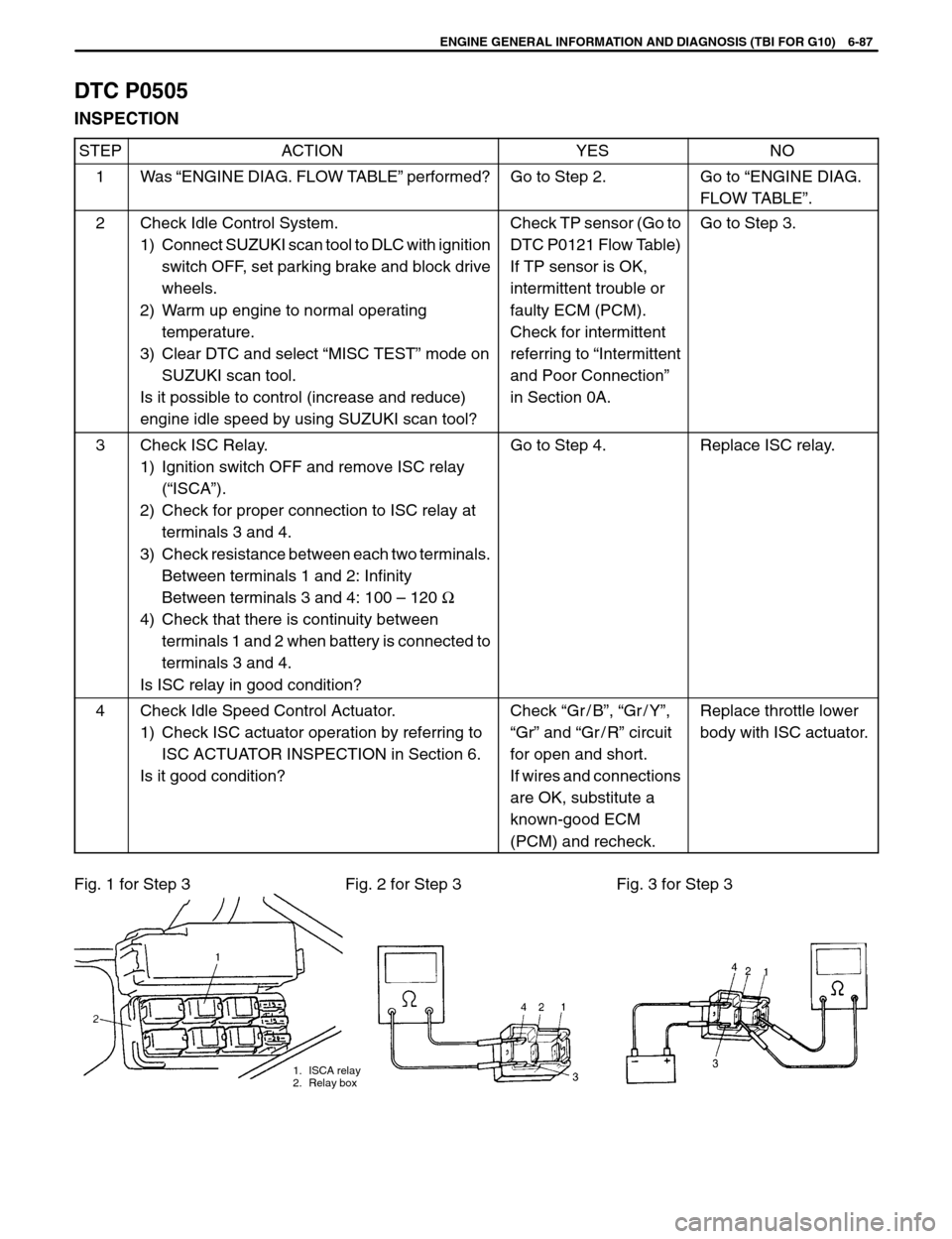
ENGINE GENERAL INFORMATION AND DIAGNOSIS (TBI FOR G10) 6-87
Fig. 1 for Step 3 Fig. 2 for Step 3 Fig. 3 for Step 3
1. ISCA relay
2. Relay box
DTC P0505
INSPECTION
STEPACTIONYESNO
1Was “ENGINE DIAG. FLOW TABLE” performed?Go to Step 2.Go to “ENGINE DIAG.
FLOW TABLE”.
2Check Idle Control System.
1) Connect SUZUKI scan tool to DLC with ignition
switch OFF, set parking brake and block drive
wheels.
2) Warm up engine to normal operating
temperature.
3) Clear DTC and select “MISC TEST” mode on
SUZUKI scan tool.
Is it possible to control (increase and reduce)
engine idle speed by using SUZUKI scan tool?Check TP sensor (Go to
DTC P0121 Flow Table)
If TP sensor is OK,
intermittent trouble or
faulty ECM (PCM).
Check for intermittent
referring to “Intermittent
and Poor Connection”
in Section 0A.Go to Step 3.
3Check ISC Relay.
1) Ignition switch OFF and remove ISC relay
(“ISCA”).
2) Check for proper connection to ISC relay at
terminals 3 and 4.
3) Check resistance between each two terminals.
Between terminals 1 and 2: Infinity
Between terminals 3 and 4: 100 – 120 Ω
4) Check that there is continuity between
terminals 1 and 2 when battery is connected to
terminals 3 and 4.
Is ISC relay in good condition?Go to Step 4.Replace ISC relay.
4Check Idle Speed Control Actuator.
1) Check ISC actuator operation by referring to
ISC ACTUATOR INSPECTION in Section 6.
Is it good condition?Check “Gr / B”, “Gr / Y”,
“Gr” and “Gr / R” circuit
for open and short.
If wires and connections
are OK, substitute a
known-good ECM
(PCM) and recheck.Replace throttle lower
body with ISC actuator.