Page 64 of 558
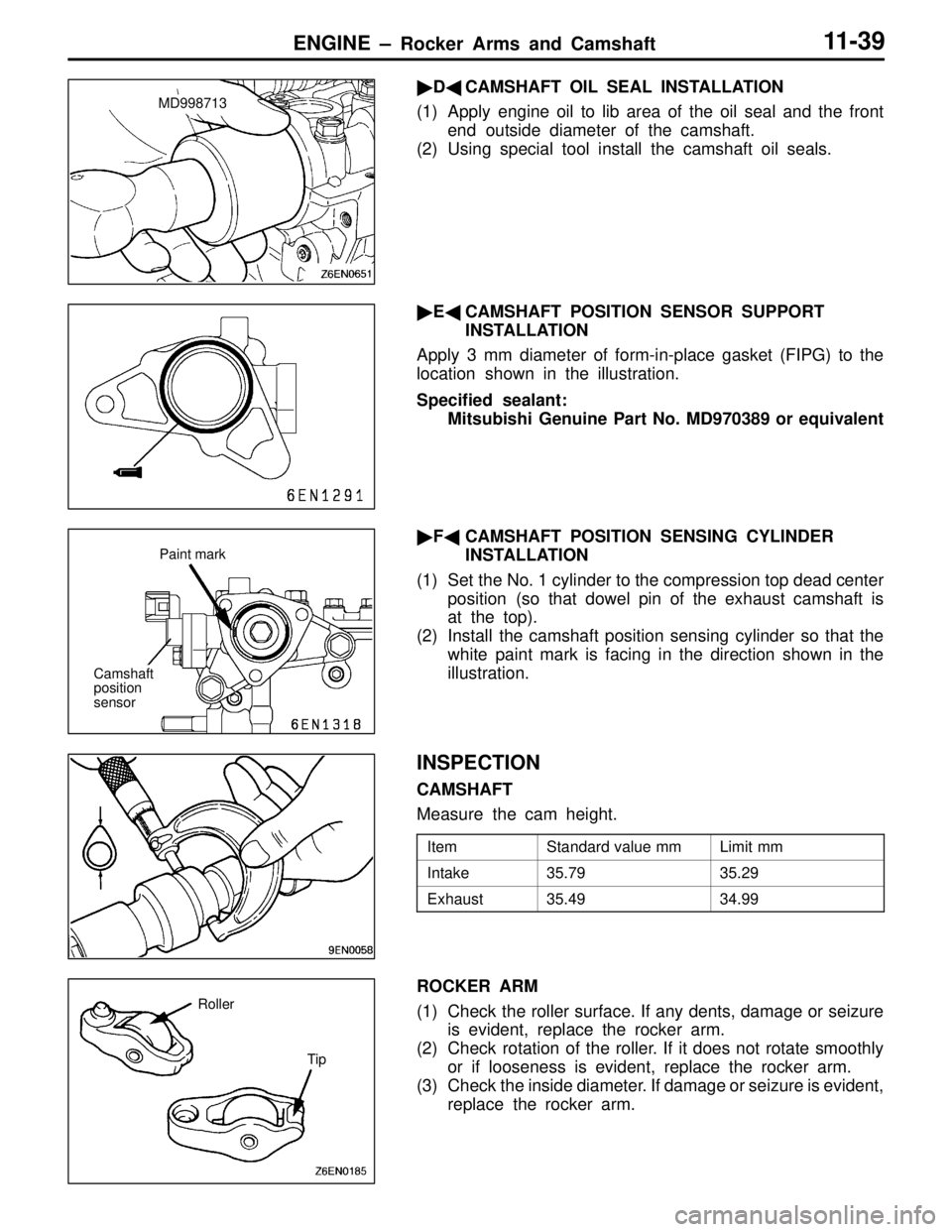
ENGINE – Rocker Arms and Camshaft11-39
DCAMSHAFT OIL SEAL INSTALLATION
(1) Apply engine oil to lib area of the oil seal and the front
end outside diameter of the camshaft.
(2) Using special tool install the camshaft oil seals.
ECAMSHAFT POSITION SENSOR SUPPORT
INSTALLATION
Apply 3 mm diameter of form-in-place gasket (FIPG) to the
location shown in the illustration.
Specified sealant:
Mitsubishi Genuine Part No. MD970389 or equivalent
FCAMSHAFT POSITION SENSING CYLINDER
INSTALLATION
(1) Set the No. 1 cylinder to the compression top dead center
position (so that dowel pin of the exhaust camshaft is
at the top).
(2) Install the camshaft position sensing cylinder so that the
white paint mark is facing in the direction shown in the
illustration.
INSPECTION
CAMSHAFT
Measure the cam height.
ItemStandard value mmLimit mm
Intake35.7935.29
Exhaust35.4934.99
ROCKER ARM
(1) Check the roller surface. If any dents, damage or seizure
is evident, replace the rocker arm.
(2) Check rotation of the roller. If it does not rotate smoothly
or if looseness is evident, replace the rocker arm.
(3) Check the inside diameter. If damage or seizure is evident,
replace the rocker arm.
MD998713
Camshaft
position
sensorPaint mark
Roller
Tip
Page 65 of 558
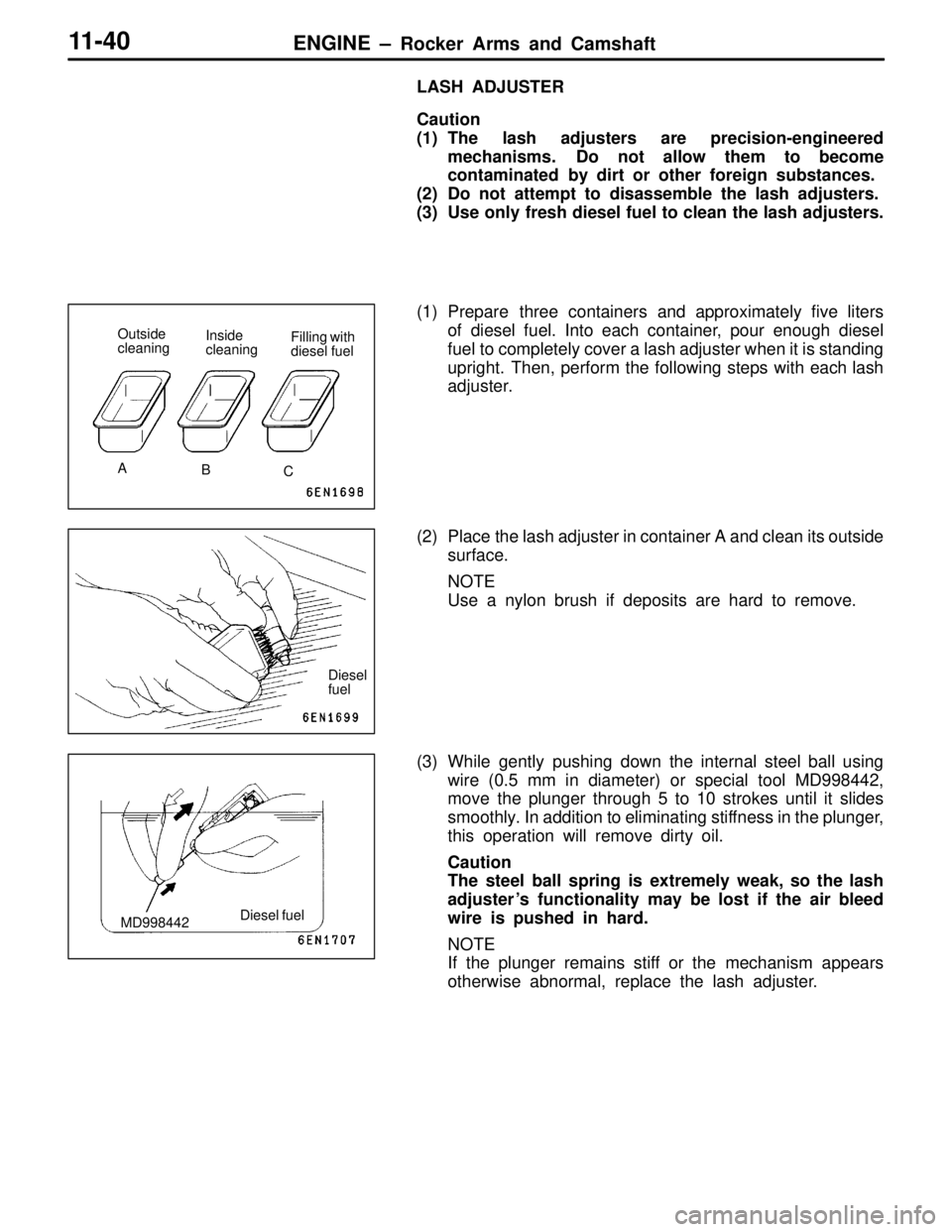
ENGINE – Rocker Arms and Camshaft11-40
LASH ADJUSTER
Caution
(1) The lash adjusters are precision-engineered
mechanisms. Do not allow them to become
contaminated by dirt or other foreign substances.
(2) Do not attempt to disassemble the lash adjusters.
(3) Use only fresh diesel fuel to clean the lash adjusters.
(1) Prepare three containers and approximately five liters
of diesel fuel. Into each container, pour enough diesel
fuel to completely cover a lash adjuster when it is standing
upright. Then, perform the following steps with each lash
adjuster.
(2) Place the lash adjuster in container A and clean its outside
surface.
NOTE
Use a nylon brush if deposits are hard to remove.
(3) While gently pushing down the internal steel ball using
wire (0.5 mm in diameter) or special tool MD998442,
move the plunger through 5 to 10 strokes until it slides
smoothly. In addition to eliminating stiffness in the plunger,
this operation will remove dirty oil.
Caution
The steel ball spring is extremely weak, so the lash
adjuster’s functionality may be lost if the air bleed
wire is pushed in hard.
NOTE
If the plunger remains stiff or the mechanism appears
otherwise abnormal, replace the lash adjuster.
Outside
cleaningInside
cleaningFilling with
diesel fuel
A
B
C
Diesel
fuel
MD998442Diesel fuel
Page 66 of 558
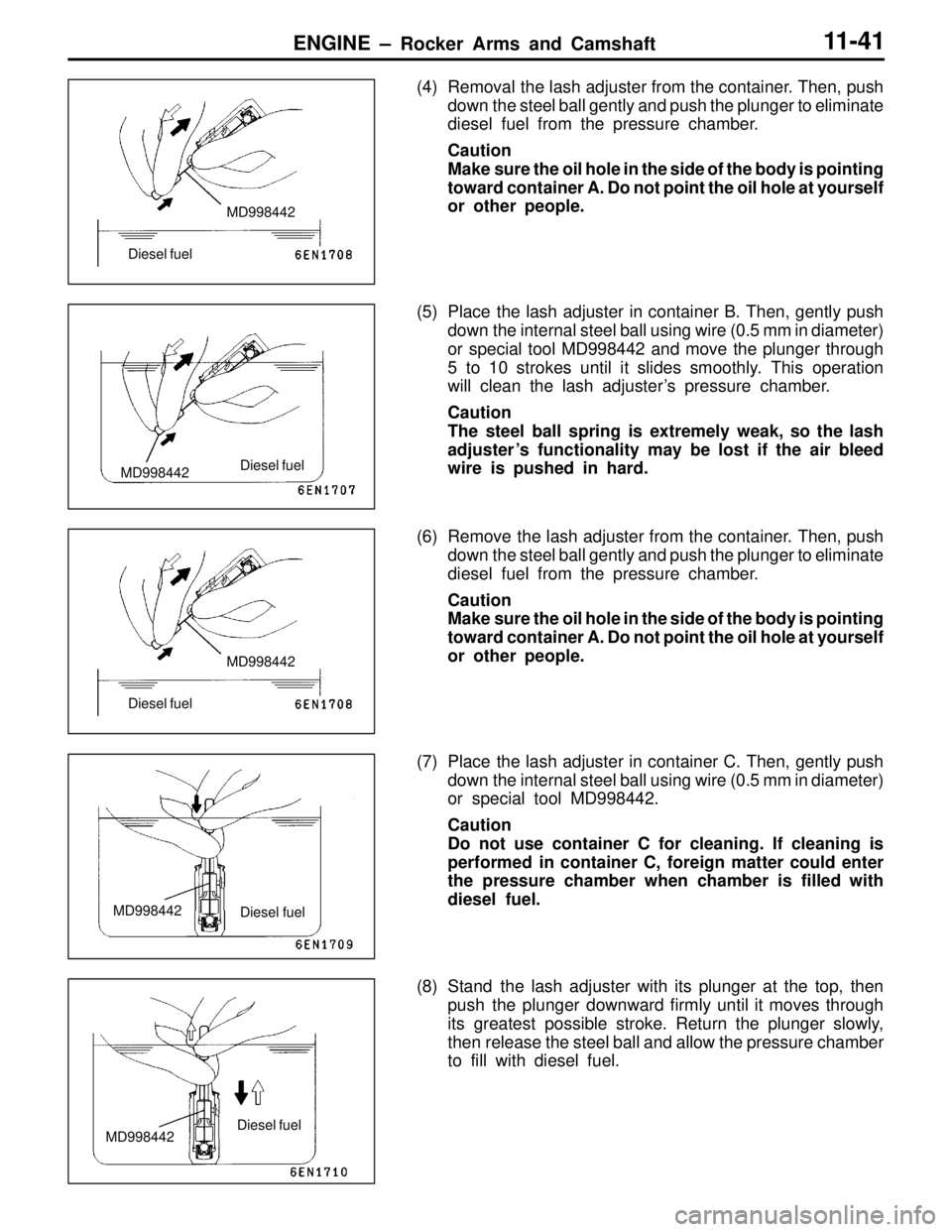
ENGINE – Rocker Arms and Camshaft11-41
(4) Removal the lash adjuster from the container. Then, push
down the steel ball gently and push the plunger to eliminate
diesel fuel from the pressure chamber.
Caution
Make sure the oil hole in the side of the body is pointing
toward container A. Do not point the oil hole at yourself
or other people.
(5) Place the lash adjuster in container B. Then, gently push
down the internal steel ball using wire (0.5 mm in diameter)
or special tool MD998442 and move the plunger through
5 to 10 strokes until it slides smoothly. This operation
will clean the lash adjuster’s pressure chamber.
Caution
The steel ball spring is extremely weak, so the lash
adjuster’s functionality may be lost if the air bleed
wire is pushed in hard.
(6) Remove the lash adjuster from the container. Then, push
down the steel ball gently and push the plunger to eliminate
diesel fuel from the pressure chamber.
Caution
Make sure the oil hole in the side of the body is pointing
toward container A. Do not point the oil hole at yourself
or other people.
(7) Place the lash adjuster in container C. Then, gently push
down the internal steel ball using wire (0.5 mm in diameter)
or special tool MD998442.
Caution
Do not use container C for cleaning. If cleaning is
performed in container C, foreign matter could enter
the pressure chamber when chamber is filled with
diesel fuel.
(8) Stand the lash adjuster with its plunger at the top, then
push the plunger downward firmly until it moves through
its greatest possible stroke. Return the plunger slowly,
then release the steel ball and allow the pressure chamber
to fill with diesel fuel.
MD998442
Diesel fuel
MD998442Diesel fuel
MD998442
Diesel fuel
MD998442
Diesel fuel
MD998442Diesel fuel
Page 67 of 558
ENGINE – Rocker Arms and Camshaft11-42
(9) Remove the lash adjuster from the container, then stand
the lash adjuster with its plunger at the top. Push the
plunger firmly and check that it does not move. Also,
check that the lash adjuster’s height matches that of a
new lash adjuster.
NOTE
If lash adjuster contracts, perform the operations (7)
through (9) again to fill it with diesel fuel completely.
Replace the lash adjuster if it still contracts after performing
these steps.
(10)Stand the lash adjuster upright to prevent diesel fuel from
spilling out. Do not allow the lash adjuster to become
contaminated by dirt or other foreign matter. Fit the lash
adjuster onto the engine as soon as possible.
Page 115 of 558
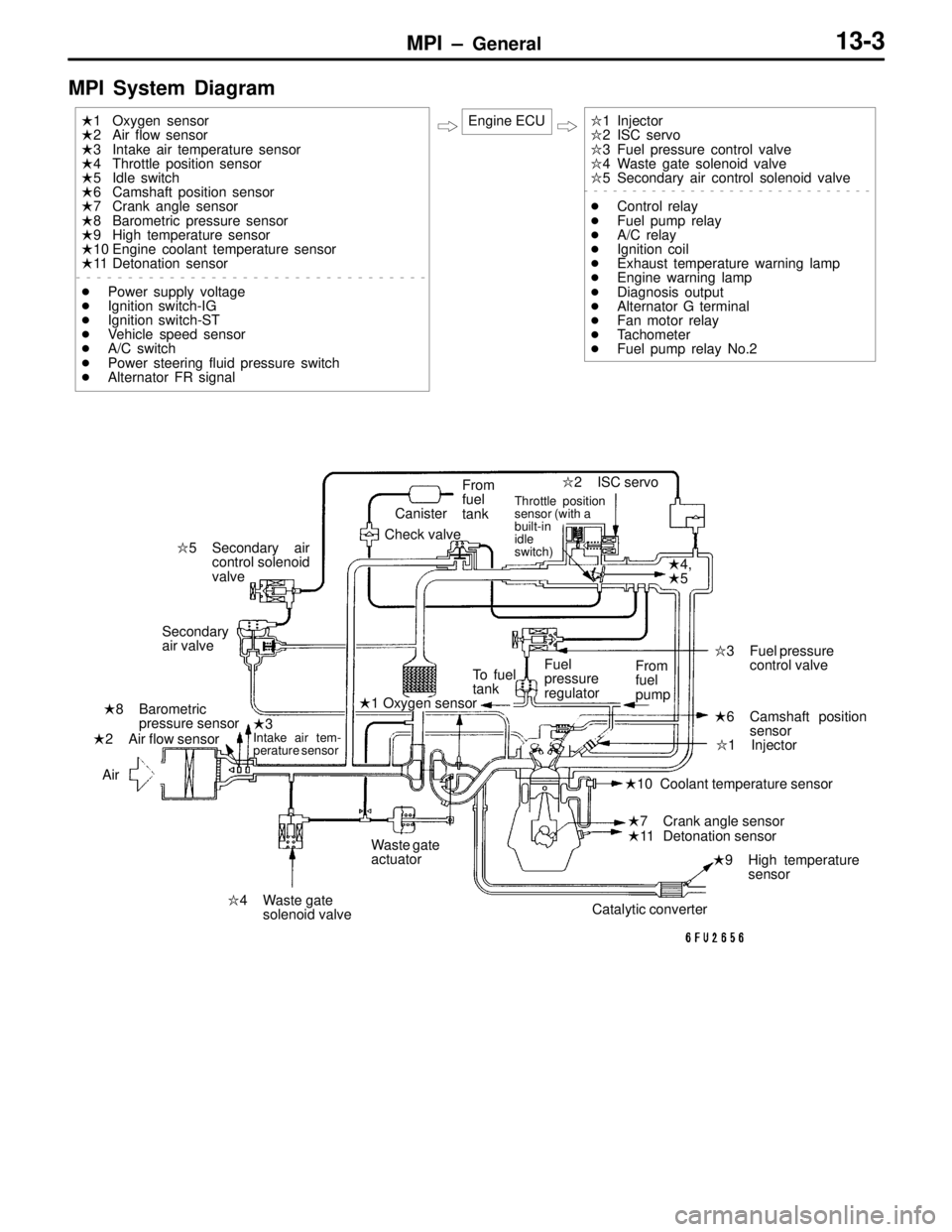
MPI – General13-3
MPI System Diagram
1 Injector
2 ISC servo
3 Fuel pressure control valve
4 Waste gate solenoid valve
5 Secondary air control solenoid valve
Control relay
Fuel pump relay
A/C relay
Ignition coil
Exhaust temperature warning lamp
Engine warning lamp
Diagnosis output
Alternator G terminal
Fan motor relay
Tachometer
Fuel pump relay No.2 1 Oxygen sensor
2 Air flow sensor
3 Intake air temperature sensor
4 Throttle position sensor
5 Idle switch
6 Camshaft position sensor
7 Crank angle sensor
8 Barometric pressure sensor
9 High temperature sensor
10 Engine coolant temperature sensor
11 Detonation sensor
Power supply voltage
Ignition switch-IG
Ignition switch-ST
Vehicle speed sensor
A/C switch
Power steering fluid pressure switch
Alternator FR signalEngine ECU
1 Oxygen sensor
2 Air flow sensor3
Intake air tem-
perature sensor
4,
5
6 Camshaft position
sensor
7 Crank angle sensor 8 Barometric
pressure sensor
9 High temperature
sensor 10 Coolant temperature sensor
11 Detonation sensor1 Injector 2 ISC servo
3 Fuel pressure
control valve
4 Waste gate
solenoid valve 5 Secondary air
control solenoid
valveCanister
Check valveFrom
fuel
tank
Throttle position
sensor (with a
built-in
idle
switch)
Secondary
air valve
AirTo fuel
tankFuel
pressure
regulatorFrom
fuel
pump
Waste gate
actuator
Catalytic converter
Page 118 of 558
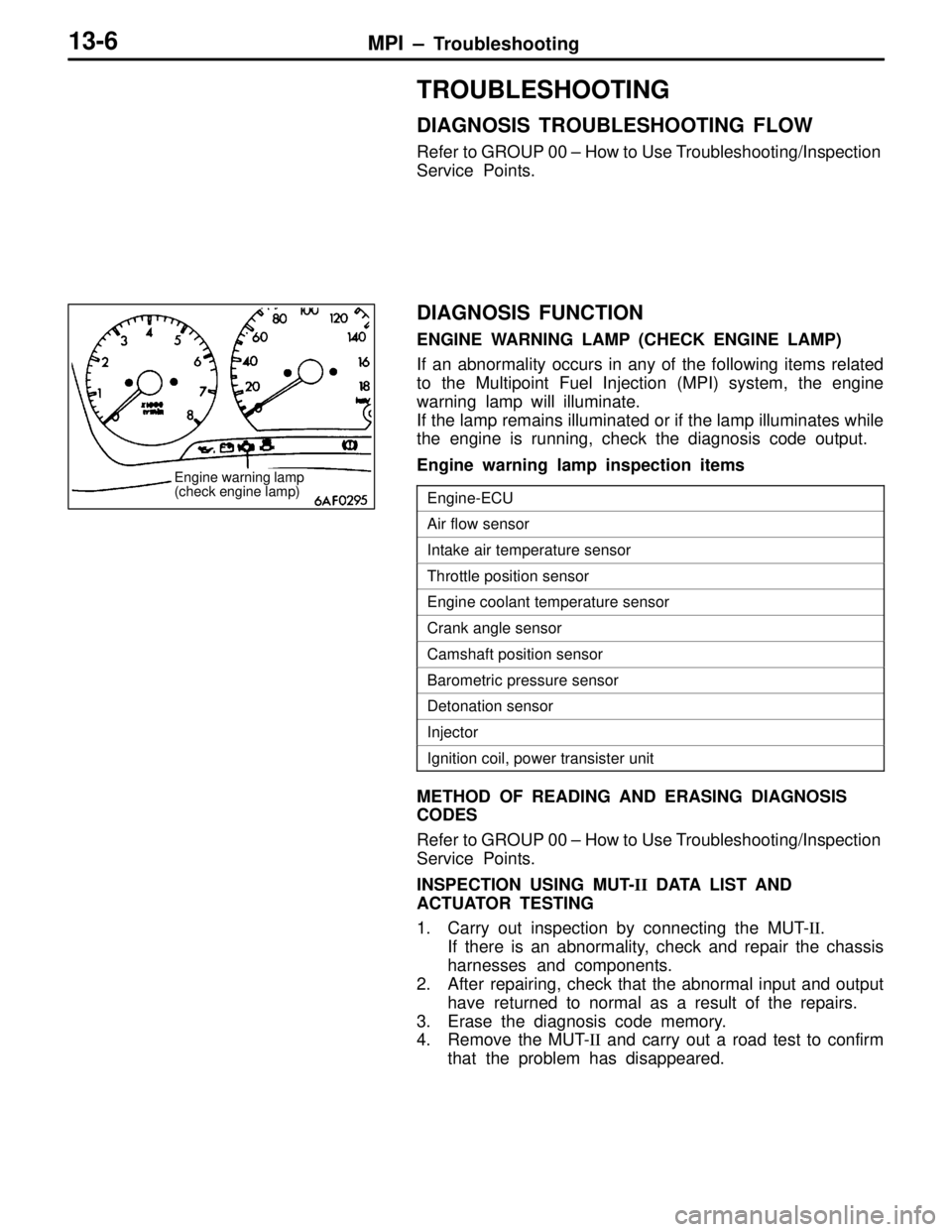
MPI – Troubleshooting13-6
TROUBLESHOOTING
DIAGNOSIS TROUBLESHOOTING FLOW
Refer to GROUP 00 – How to Use Troubleshooting/Inspection
Service Points.
DIAGNOSIS FUNCTION
ENGINE WARNING LAMP (CHECK ENGINE LAMP)
If an abnormality occurs in any of the following items related
to the Multipoint Fuel Injection (MPI) system, the engine
warning lamp will illuminate.
If the lamp remains illuminated or if the lamp illuminates while
the engine is running, check the diagnosis code output.
Engine warning lamp inspection items
Engine-ECU
Air flow sensor
Intake air temperature sensor
Throttle position sensor
Engine coolant temperature sensor
Crank angle sensor
Camshaft position sensor
Barometric pressure sensor
Detonation sensor
Injector
Ignition coil, power transister unit
METHOD OF READING AND ERASING DIAGNOSIS
CODES
Refer to GROUP 00 – How to Use Troubleshooting/Inspection
Service Points.
INSPECTION USING MUT-II DATA LIST AND
ACTUATOR TESTING
1. Carry out inspection by connecting the MUT-II.
If there is an abnormality, check and repair the chassis
harnesses and components.
2. After repairing, check that the abnormal input and output
have returned to normal as a result of the repairs.
3. Erase the diagnosis code memory.
4. Remove the MUT-II and carry out a road test to confirm
that the problem has disappeared.
Engine warning lamp
(check engine lamp)
Page 119 of 558
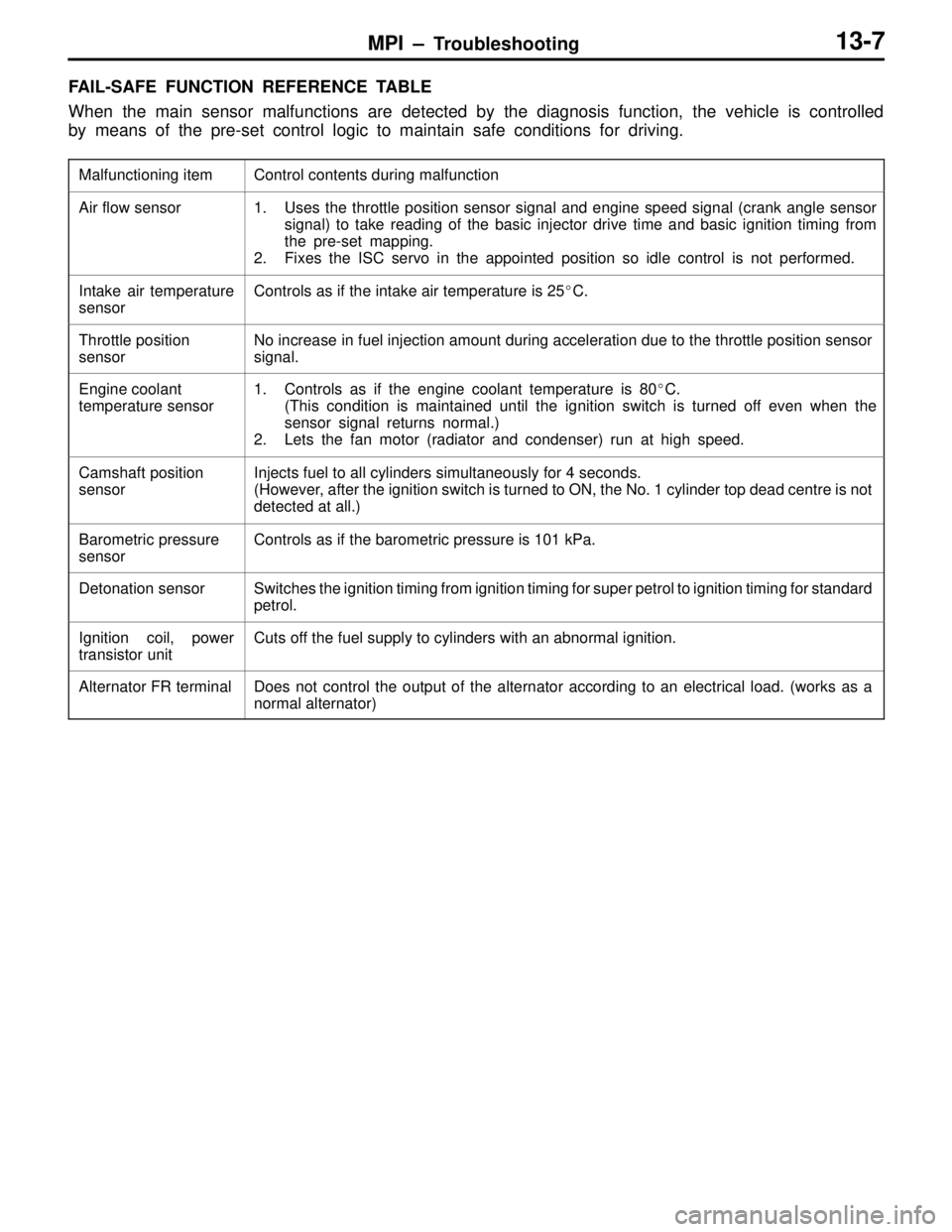
MPI – Troubleshooting13-7
FAIL-SAFE FUNCTION REFERENCE TABLE
When the main sensor malfunctions are detected by the diagnosis function, the vehicle is controlled
by means of the pre-set control logic to maintain safe conditions for driving.
Malfunctioning itemControl contents during malfunction
Air flow sensor1. Uses the throttle position sensor signal and engine speed signal (crank angle sensor
signal) to take reading of the basic injector drive time and basic ignition timing from
the pre-set mapping.
2. Fixes the ISC servo in the appointed position so idle control is not performed.
Intake air temperature
sensorControls as if the intake air temperature is 25C.
Throttle position
sensorNo increase in fuel injection amount during acceleration due to the throttle position sensor
signal.
Engine coolant
temperature sensor1. Controls as if the engine coolant temperature is 80C.
(This condition is maintained until the ignition switch is turned off even when the
sensor signal returns normal.)
2. Lets the fan motor (radiator and condenser) run at high speed.
Camshaft position
sensorInjects fuel to all cylinders simultaneously for 4 seconds.
(However, after the ignition switch is turned to ON, the No. 1 cylinder top dead centre is not
detected at all.)
Barometric pressure
sensorControls as if the barometric pressure is 101 kPa.
Detonation sensorSwitches the ignition timing from ignition timing for super petrol to ignition timing for standard
petrol.
Ignition coil, power
transistor unitCuts off the fuel supply to cylinders with an abnormal ignition.
Alternator FR terminalDoes not control the output of the alternator according to an electrical load. (works as a
normal alternator)
Page 120 of 558
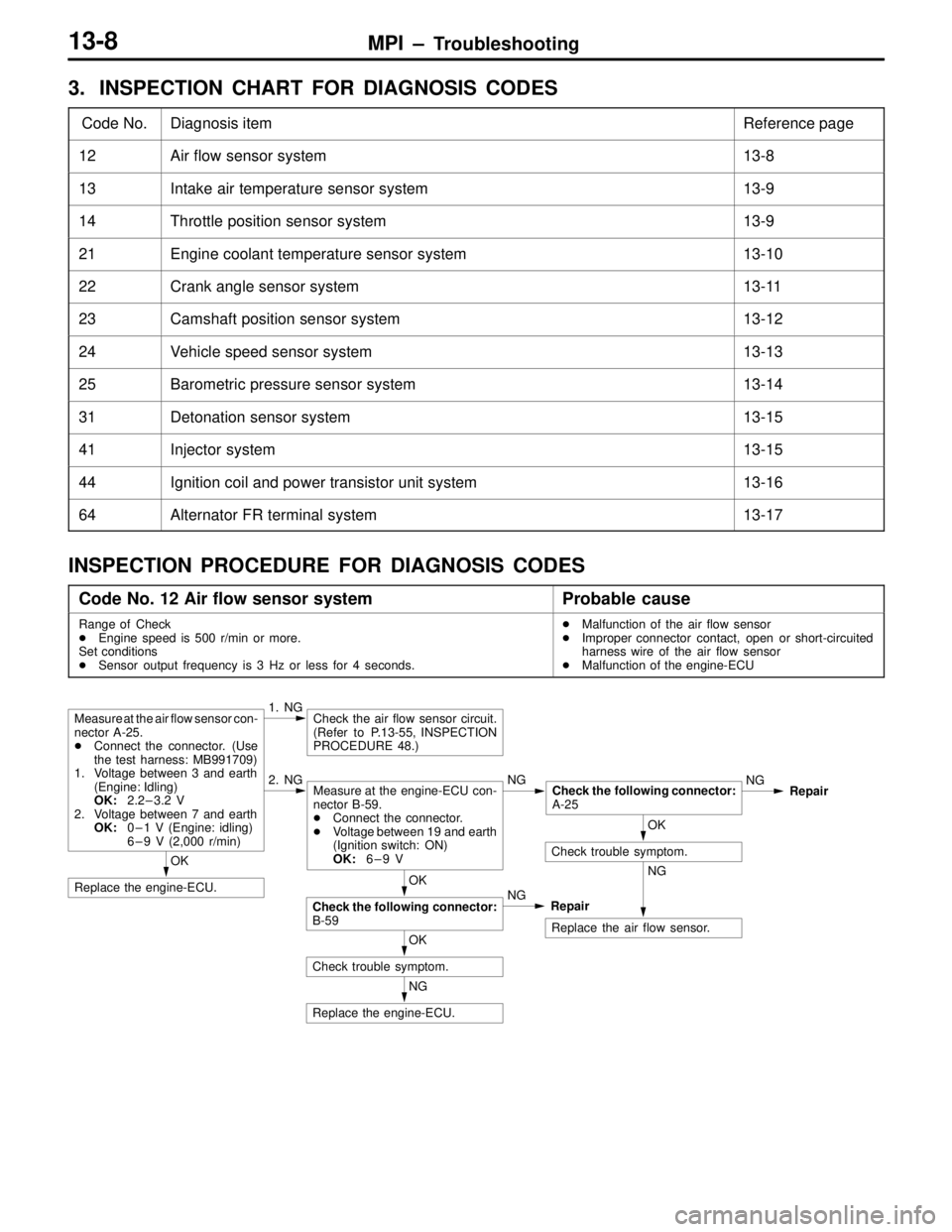
MPI – Troubleshooting13-8
3. INSPECTION CHART FOR DIAGNOSIS CODES
Code No.Diagnosis itemReference page
12Air flow sensor system13-8
13Intake air temperature sensor system13-9
14Throttle position sensor system13-9
21Engine coolant temperature sensor system13-10
22Crank angle sensor system13-11
23Camshaft position sensor system13-12
24Vehicle speed sensor system13-13
25Barometric pressure sensor system13-14
31Detonation sensor system13-15
41Injector system13-15
44Ignition coil and power transistor unit system13-16
64Alternator FR terminal system13-17
INSPECTION PROCEDURE FOR DIAGNOSIS CODES
Code No. 12 Air flow sensor systemProbable cause
Range of Check
Engine speed is 500 r/min or more.
Set conditions
Sensor output frequency is 3 Hz or less for 4 seconds.Malfunction of the air flow sensor
Improper connector contact, open or short-circuited
harness wire of the air flow sensor
Malfunction of the engine-ECU
Measure at the air flow sensor con-
nector A-25.
Connect the connector. (Use
the test harness: MB991709)
1. Voltage between 3 and earth
(Engine: Idling)
OK:2.2–3.2 V
2. Voltage between 7 and earth
OK:0–1 V (Engine: idling)
6–9 V (2,000 r/min)
OK
Replace the engine-ECU.1. NG
Check the air flow sensor circuit.
(Refer to P.13-55, INSPECTION
PROCEDURE 48.)
2. NG
Measure at the engine-ECU con-
nector B-59.
Connect the connector.
Voltage between 19 and earth
(Ignition switch: ON)
OK:6–9 V
OK
Check the following connector:
B-59
OK
Check trouble symptom.
NG
Replace the engine-ECU.NG
Check the following connector:
A-25NG
Repair
OK
Check trouble symptom.
NG
NG
Repair
Replace the air flow sensor.