Page 45 of 558
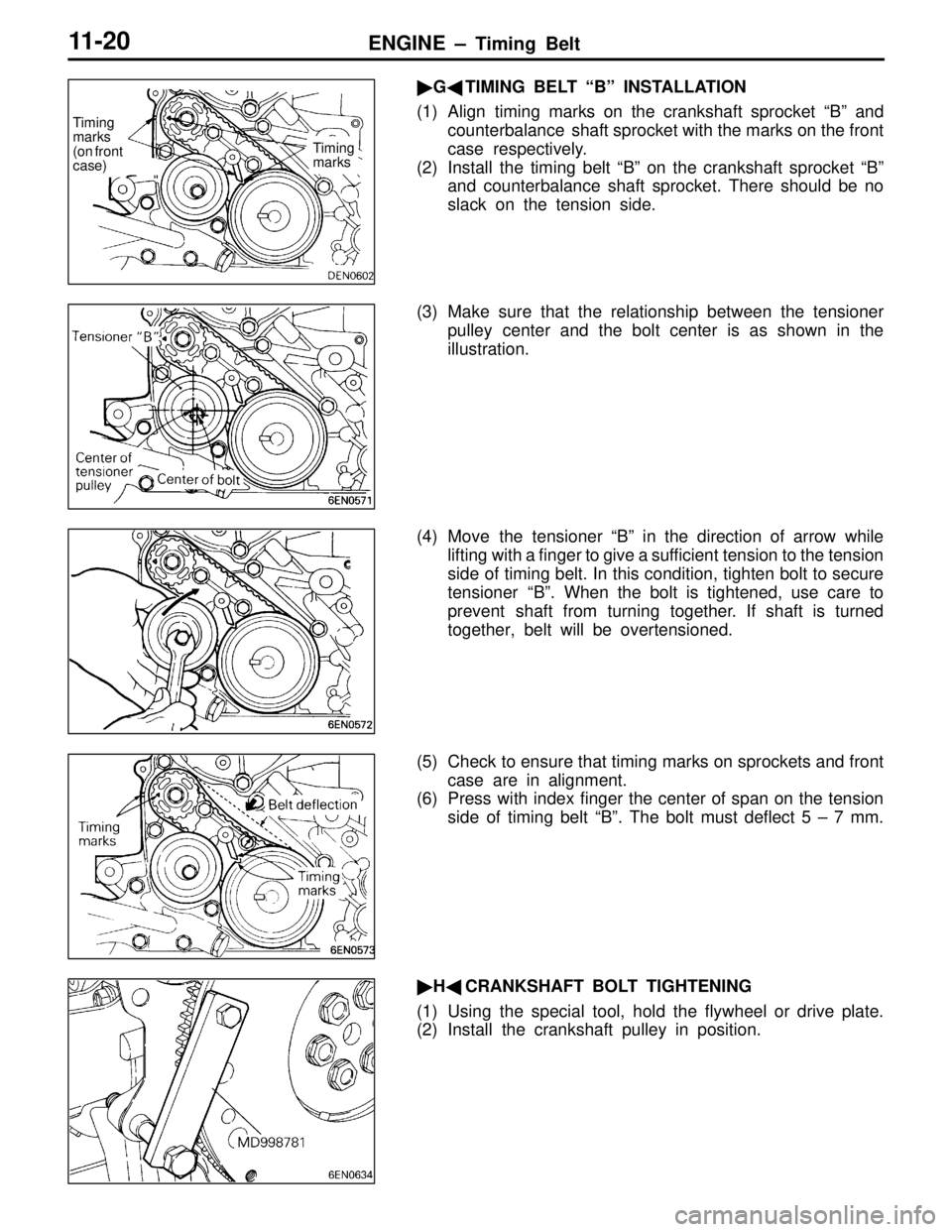
ENGINE – Timing Belt11-20
GTIMING BELT “B” INSTALLATION
(1) Align timing marks on the crankshaft sprocket “B” and
counterbalance shaft sprocket with the marks on the front
case respectively.
(2) Install the timing belt “B” on the crankshaft sprocket “B”
and counterbalance shaft sprocket. There should be no
slack on the tension side.
(3) Make sure that the relationship between the tensioner
pulley center and the bolt center is as shown in the
illustration.
(4) Move the tensioner “B” in the direction of arrow while
lifting with a finger to give a sufficient tension to the tension
side of timing belt. In this condition, tighten bolt to secure
tensioner “B”. When the bolt is tightened, use care to
prevent shaft from turning together. If shaft is turned
together, belt will be overtensioned.
(5) Check to ensure that timing marks on sprockets and front
case are in alignment.
(6) Press with index finger the center of span on the tension
side of timing belt “B”. The bolt must deflect 5 – 7 mm.
HCRANKSHAFT BOLT TIGHTENING
(1) Using the special tool, hold the flywheel or drive plate.
(2) Install the crankshaft pulley in position.
Timing
marks
Timing
marks
(on front
case)
Page 95 of 558
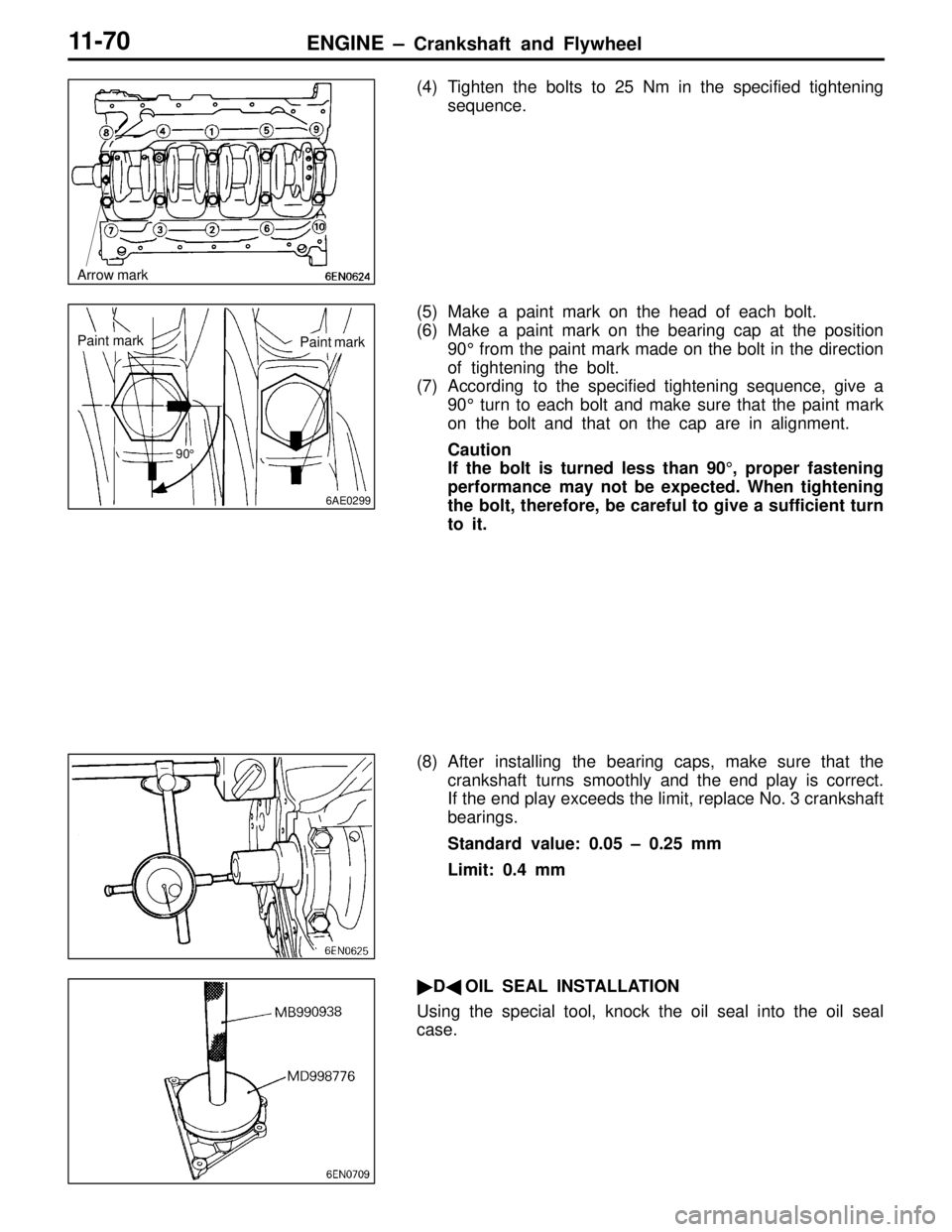
ENGINE – Crankshaft and Flywheel11-70
(4) Tighten the bolts to 25 Nm in the specified tightening
sequence.
(5) Make a paint mark on the head of each bolt.
(6) Make a paint mark on the bearing cap at the position
90° from the paint mark made on the bolt in the direction
of tightening the bolt.
(7) According to the specified tightening sequence, give a
90° turn to each bolt and make sure that the paint mark
on the bolt and that on the cap are in alignment.
Caution
If the bolt is turned less than 90°, proper fastening
performance may not be expected. When tightening
the bolt, therefore, be careful to give a sufficient turn
to it.
(8) After installing the bearing caps, make sure that the
crankshaft turns smoothly and the end play is correct.
If the end play exceeds the limit, replace No. 3 crankshaft
bearings.
Standard value: 0.05 – 0.25 mm
Limit: 0.4 mm
DOIL SEAL INSTALLATION
Using the special tool, knock the oil seal into the oil seal
case.
Arrow mark
6AE0299
Paint markPaint mark
90°
Page 200 of 558
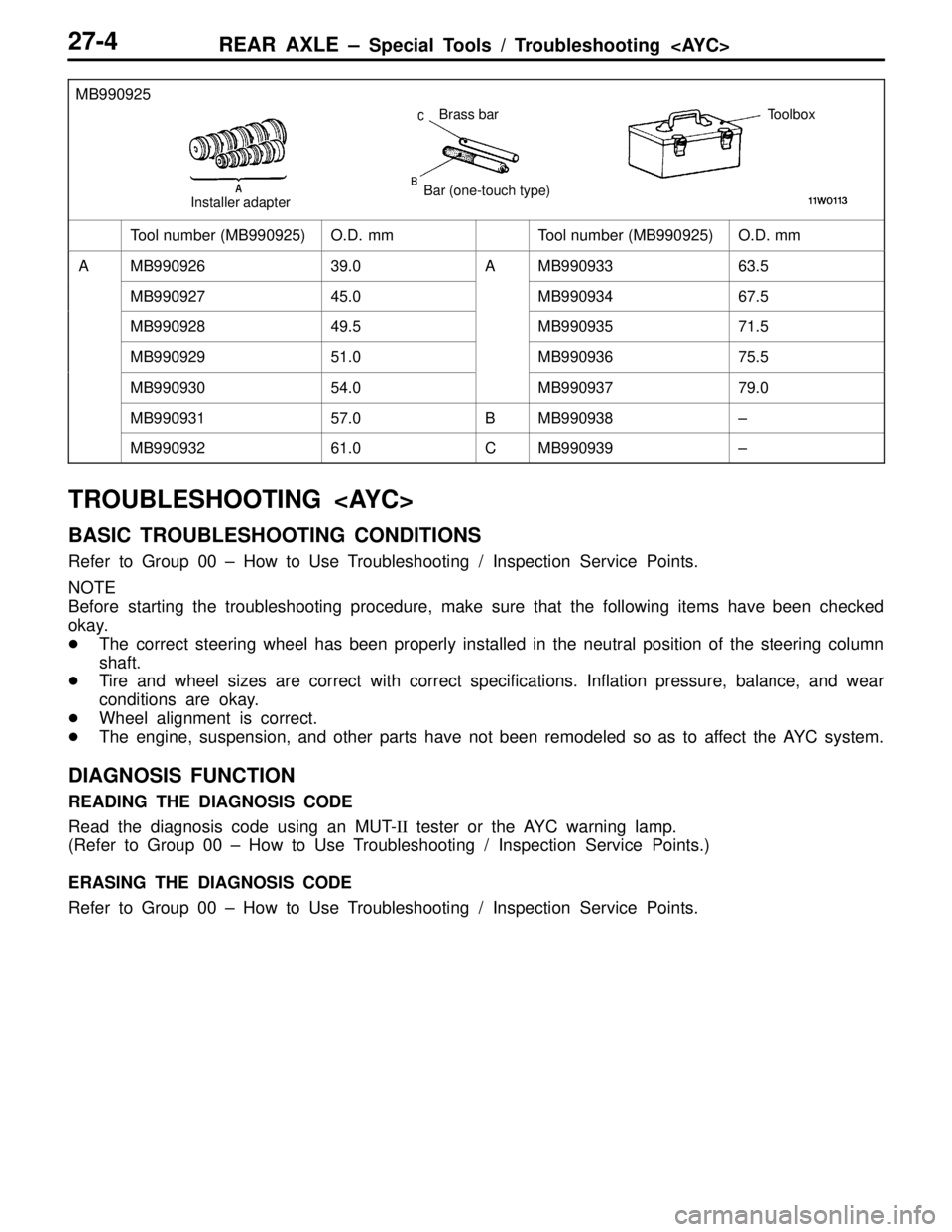
REAR AXLE – Special Tools / Troubleshooting 27-4
MB990925
Brass bar
Bar (one-touch type)Toolbox
Installer adapter
Tool number (MB990925)O.D. mmTool number (MB990925)O.D. mm
AMB99092639.0AMB99093363.5
MB99092745.0MB99093467.5
MB99092849.5MB99093571.5
MB99092951.0MB99093675.5
MB99093054.0MB99093779.0
MB99093157.0BMB990938–
MB99093261.0CMB990939–
TROUBLESHOOTING
BASIC TROUBLESHOOTING CONDITIONS
Refer to Group 00 – How to Use Troubleshooting / Inspection Service Points.
NOTE
Before starting the troubleshooting procedure, make sure that the following items have been checked
okay.
The correct steering wheel has been properly installed in the neutral position of the steering column
shaft.
Tire and wheel sizes are correct with correct specifications. Inflation pressure, balance, and wear
conditions are okay.
Wheel alignment is correct.
The engine, suspension, and other parts have not been remodeled so as to affect the AYC system.
DIAGNOSIS FUNCTION
READING THE DIAGNOSIS CODE
Read the diagnosis code using an MUT-II tester or the AYC warning lamp.
(Refer to Group 00 – How to Use Troubleshooting / Inspection Service Points.)
ERASING THE DIAGNOSIS CODE
Refer to Group 00 – How to Use Troubleshooting / Inspection Service Points.
Page 232 of 558
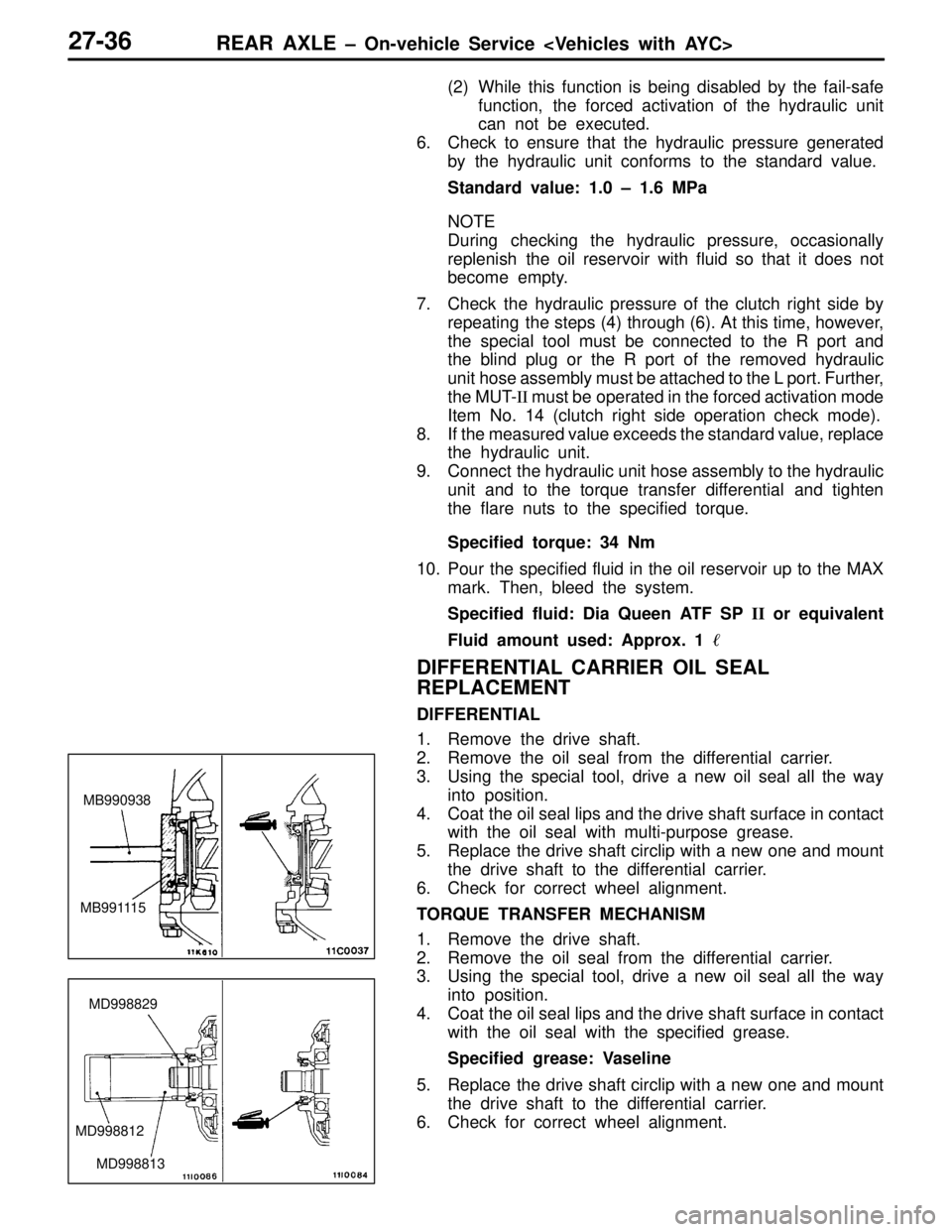
REAR AXLE – On-vehicle Service 27-36
(2) While this function is being disabled by the fail-safe
function, the forced activation of the hydraulic unit
can not be executed.
6. Check to ensure that the hydraulic pressure generated
by the hydraulic unit conforms to the standard value.
Standard value: 1.0 – 1.6 MPa
NOTE
During checking the hydraulic pressure, occasionally
replenish the oil reservoir with fluid so that it does not
become empty.
7. Check the hydraulic pressure of the clutch right side by
repeating the steps (4) through (6). At this time, however,
the special tool must be connected to the R port and
the blind plug or the R port of the removed hydraulic
unit hose assembly must be attached to the L port. Further,
the MUT-II must be operated in the forced activation mode
Item No. 14 (clutch right side operation check mode).
8. If the measured value exceeds the standard value, replace
the hydraulic unit.
9. Connect the hydraulic unit hose assembly to the hydraulic
unit and to the torque transfer differential and tighten
the flare nuts to the specified torque.
Specified torque: 34 Nm
10. Pour the specified fluid in the oil reservoir up to the MAX
mark. Then, bleed the system.
Specified fluid: Dia Queen ATF SP II or equivalent
Fluid amount used: Approx. 1
DIFFERENTIAL CARRIER OIL SEAL
REPLACEMENT
DIFFERENTIAL
1. Remove the drive shaft.
2. Remove the oil seal from the differential carrier.
3. Using the special tool, drive a new oil seal all the way
into position.
4. Coat the oil seal lips and the drive shaft surface in contact
with the oil seal with multi-purpose grease.
5. Replace the drive shaft circlip with a new one and mount
the drive shaft to the differential carrier.
6. Check for correct wheel alignment.
TORQUE TRANSFER MECHANISM
1. Remove the drive shaft.
2. Remove the oil seal from the differential carrier.
3. Using the special tool, drive a new oil seal all the way
into position.
4. Coat the oil seal lips and the drive shaft surface in contact
with the oil seal with the specified grease.
Specified grease: Vaseline
5. Replace the drive shaft circlip with a new one and mount
the drive shaft to the differential carrier.
6. Check for correct wheel alignment.
MB990938
MB991115
MD998829
MD998812
MD998813
Page 239 of 558
FRONT SUSPENSION – General / Lower Arm 33A-1
GROUP 33A
FRONT SUSPENSION
GENERAL
OUTLINE OF CHANGE
The installation method of the ball joint between the knuckle and the lower arm has been changed,
and accordingly the removal and installation procedures of the lower arm have been revised.
LOWER ARM
REMOVAL AND INSTALLATION
Caution
The part marked with * should be first temporarily tightened, then torqued to specification with the vehicle
on the ground in unloaded condition.
Post-installation Operation
Push the Dust Cover of the Lower Arm and Stabilizer Link Ball Joint with a Finger to Check for Possible Cracks or Damage.
Wheel Alignment Check and Adjustment
1
2
3
4
5
6
39 Nm
106 Nm*
5
98 – 118 Nm
74 – 87 Nm88 Nm
137 Nm
Removal steps
1. Stabilizer link mounting nut
2. Bolt
3. Stabilizer bracket
A4. Bushing assembly
5. Lower arm assembly6. Lower arm bracket assembly
NOTE
Follow the conventional procedures for installation service
points.
Page 254 of 558
STEERING – Steering Wheel and Shaft37A-4
DISASSEMBLY SERVICE POINT
ASTEERING LOCK BRACKET / STEERING LOCK
CYLINDER REMOVAL
If it is necessary to remove the steering lock cylinder, use
a hacksaw to cut the special bolts at the steering lock bracket
side.
REASSEMBLY SERVICE POINT
ASTEERING LOCK CYLINDER/STEERING LOCK
BRACKET / SPECIAL BOLT INSTALLATION
1. When installing the steering lock cylinder and steering
lock bracket to the column tube, temporarily install the
steering lock in alignment with the column boss.
2. After checking that the lock works properly, tighten the
special bolts until the head twists off.
Caution
The steering lock bracket and bolts must be replaced
with new ones when the steering lock is installed.
Steering lock bracket
Steering lock cylinder
Page 255 of 558
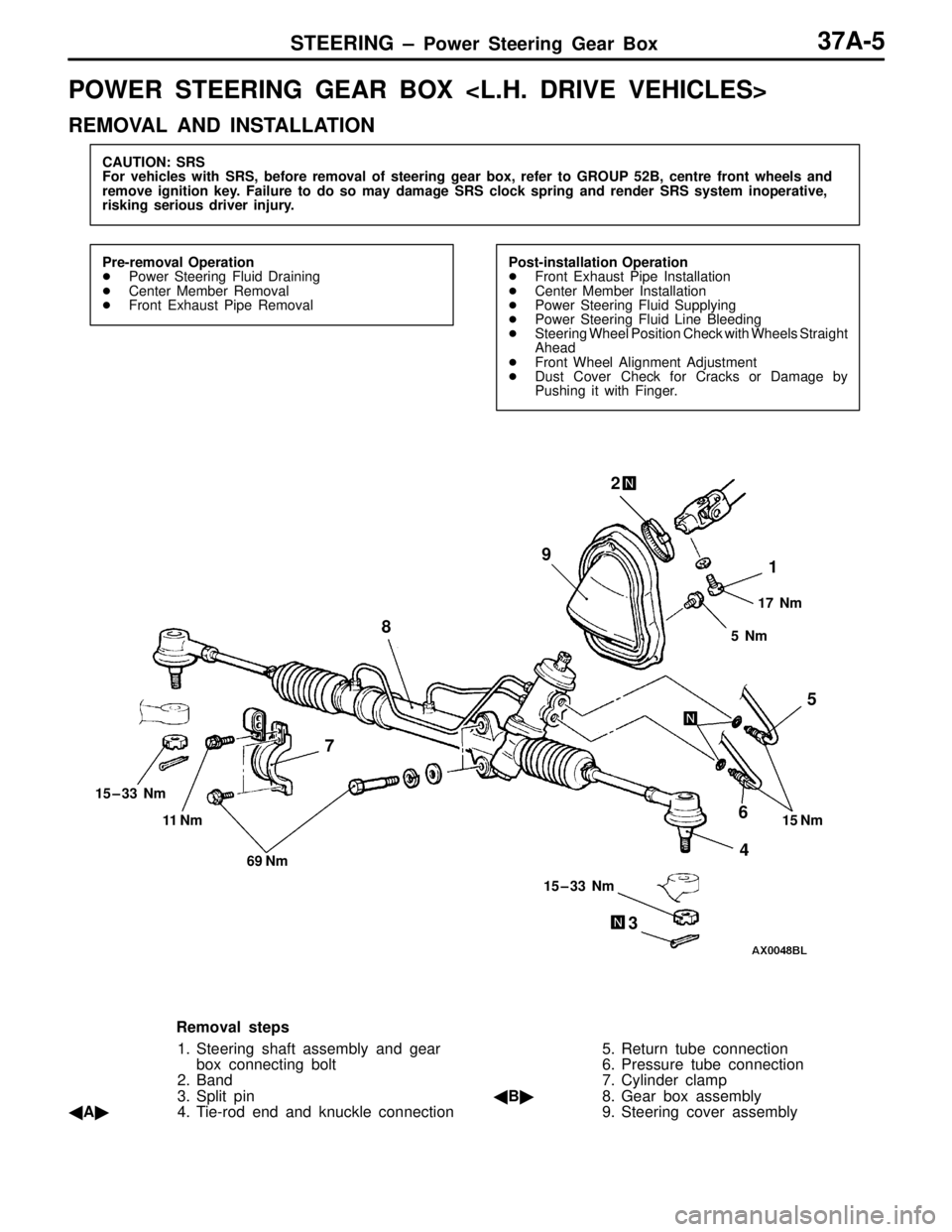
STEERING – Power Steering Gear Box37A-5
POWER STEERING GEAR BOX
REMOVAL AND INSTALLATION
CAUTION: SRS
For vehicles with SRS, before removal of steering gear box, refer to GROUP 52B, centre front wheels and
remove ignition key. Failure to do so may damage SRS clock spring and render SRS system inoperative,
risking serious driver injury.
Pre-removal Operation
Power Steering Fluid Draining
Center Member Removal
Front Exhaust Pipe RemovalPost-installation Operation
Front Exhaust Pipe Installation
Center Member Installation
Power Steering Fluid Supplying
Power Steering Fluid Line Bleeding
Steering Wheel Position Check with Wheels Straight
Ahead
Front Wheel Alignment Adjustment
Dust Cover Check for Cracks or Damage by
Pushing it with Finger.
15 Nm 15–33 Nm
69 Nm17 Nm
5 Nm
15–33 Nm
789
3
45 1 2
611 Nm
Removal steps
1. Steering shaft assembly and gear
box connecting bolt
2. Band
3. Split pin
A4. Tie-rod end and knuckle connection5. Return tube connection
6. Pressure tube connection
7. Cylinder clamp
B8. Gear box assembly
9. Steering cover assembly
Page 313 of 558
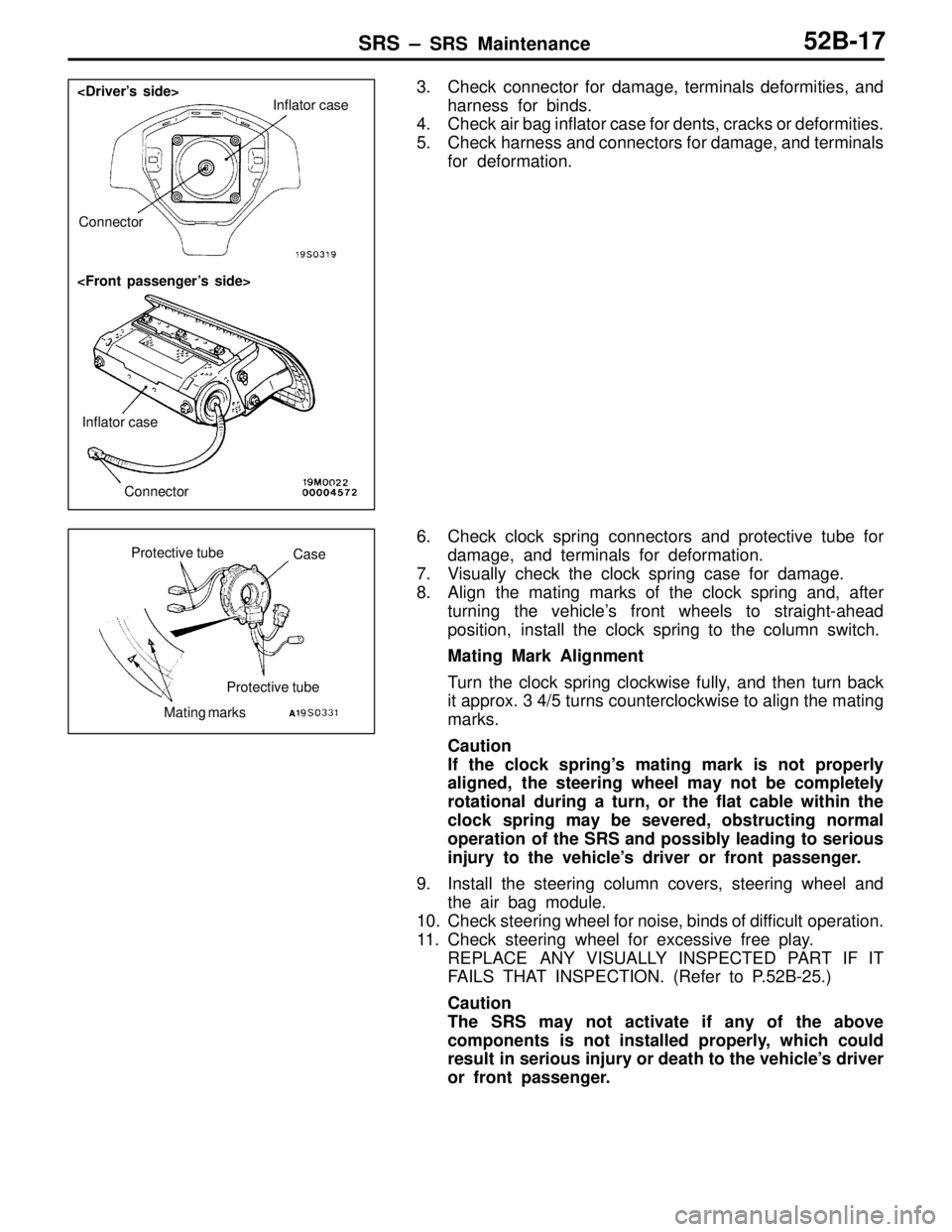
SRS – SRS Maintenance52B-17
3. Check connector for damage, terminals deformities, and
harness for binds.
4. Check air bag inflator case for dents, cracks or deformities.
5. Check harness and connectors for damage, and terminals
for deformation.
6. Check clock spring connectors and protective tube for
damage, and terminals for deformation.
7. Visually check the clock spring case for damage.
8. Align the mating marks of the clock spring and, after
turning the vehicle’s front wheels to straight-ahead
position, install the clock spring to the column switch.
Mating Mark Alignment
Turn the clock spring clockwise fully, and then turn back
it approx. 3 4/5 turns counterclockwise to align the mating
marks.
Caution
If the clock spring’s mating mark is not properly
aligned, the steering wheel may not be completely
rotational during a turn, or the flat cable within the
clock spring may be severed, obstructing normal
operation of the SRS and possibly leading to serious
injury to the vehicle’s driver or front passenger.
9. Install the steering column covers, steering wheel and
the air bag module.
10. Check steering wheel for noise, binds of difficult operation.
11. Check steering wheel for excessive free play.
REPLACE ANY VISUALLY INSPECTED PART IF IT
FAILS THAT INSPECTION. (Refer to P.52B-25.)
Caution
The SRS may not activate if any of the above
components is not installed properly, which could
result in serious injury or death to the vehicle’s driver
or front passenger.
Inflator case
Connector
Inflator case
Connector
Protective tube
Case
Mating marksProtective tube