Page 21 of 751
01-4
2. MAJOR COMPONENTS
Front view ▶
Vacuum pump
Oil filter assembly
Camshaft position sensor
Power steering pump pulley
Water pump pulley
Alternator pulley
Idler pulley No. 2
A/C compressor pulley
Auto tensioner
Idler pulley No. 1
Isolation damper
Rear view ▶
E-EGR valve
Fuel temperature sensor
Fuel HP pump assembly
Coolant temperature sensor
IMV valve Crankshaft position sensor
Oil pressure switch
Page 30 of 751
01-130000-00
NameSizeNumbers of
fastener Tightening
torque (Nm) Note (total
tightening torque)
Idler pulley/tensioner pulley 1
45±4.5Nm -
Glow plug M5 4 20±2Nm -
Vacuum pump M6×25 3 10±1Nm -
Timing gear case cover M6×40 7 10±1Nm -
M6×45 1 10±1Nm -
M6×50 3 10±1Nm -
Cylinder head cover M6×35 21 10±1Nm -
Oil dipstick gauge cover M6×16 1 10±1Nm -
Oil filter cap 1 25±2.5Nm -
Fuel rail M8×25 2 25±2.5Nm -
Injector clamp bolt M6×44 2 9±1.0Nm
130˚±10˚ -
High pressure pipe
(between high pressure pump and fuel rail assembly) M17 1
30±3Nm -
High pressure pipe
(between fuel rail assembly and injector) M17 4
30±3Nm -
Crankshaft position sensor M5×14
1 8±0.4Nm -
Main wiring M6×16 5 10±1Nm -
Intake duct M8×25 425±2.5Nm -
Power steering pump M8×100 3 25±2.5Nm -
Cylinder head front cover M6×10
5 10±1Nm -
Ladder frame M8×355 30±3Nm
-
EGR pipe bolt
(to air duct) M6×16
2 10±1Nm -
EGR pipe bolt
(to EGR cooler) M8×25
225±2.5Nm -
Page 37 of 751
02-6
ComponentSizeBolt
Quantity Specified torque
(Nm) Remark
(Total torque)
Glow plug M5 4 20±2Nm -
Vacuum pump M6×253 10±1Nm -
Timing gear case cover M12×55 3 85±8.5Nm -
M6×25 7 10±1Nm -
M6×45 1 10±1Nm -
M6×50 3 10±1Nm -
Cylinder head cover M6×35 21 10±1Nm -
Oil gauge tube M6×16 1 10±1Nm -
Oil filter cap 1 25±2.5Nm -
Fuel rail M8×35SOC 2 25±2.5Nm -
Injector clamp bolt M6×60 2 10±1Nm,
120˚+10˚ -
High pressure pipe
(between HP pump and fuel rail) M17 1
30±3Nm -
High pressure pipe
(between fuel rail and injector) M17 4
30±3Nm -
Crank position sensor M5×14 1 5±1.0Nm -
Main wiring M6×16 5 10±1Nm -
Intake duct M8x25 4 25±2.5Nm -
Power steering pump M8×100 3 25±2.5Nm -
Cylinder head front cover M6×10 5 10±1Nm -
Ladder frame M8×16 5 30±3Nm -
Oil pump M8×35 3 25±2.5Nm -
EGR Cooler
MTG Bolt M8×16
225±2.5Nm -
M8×70 225±2.5Nm -
Idle pulley/Tensioner pulley 1
45±4.5Nm -
Page 38 of 751
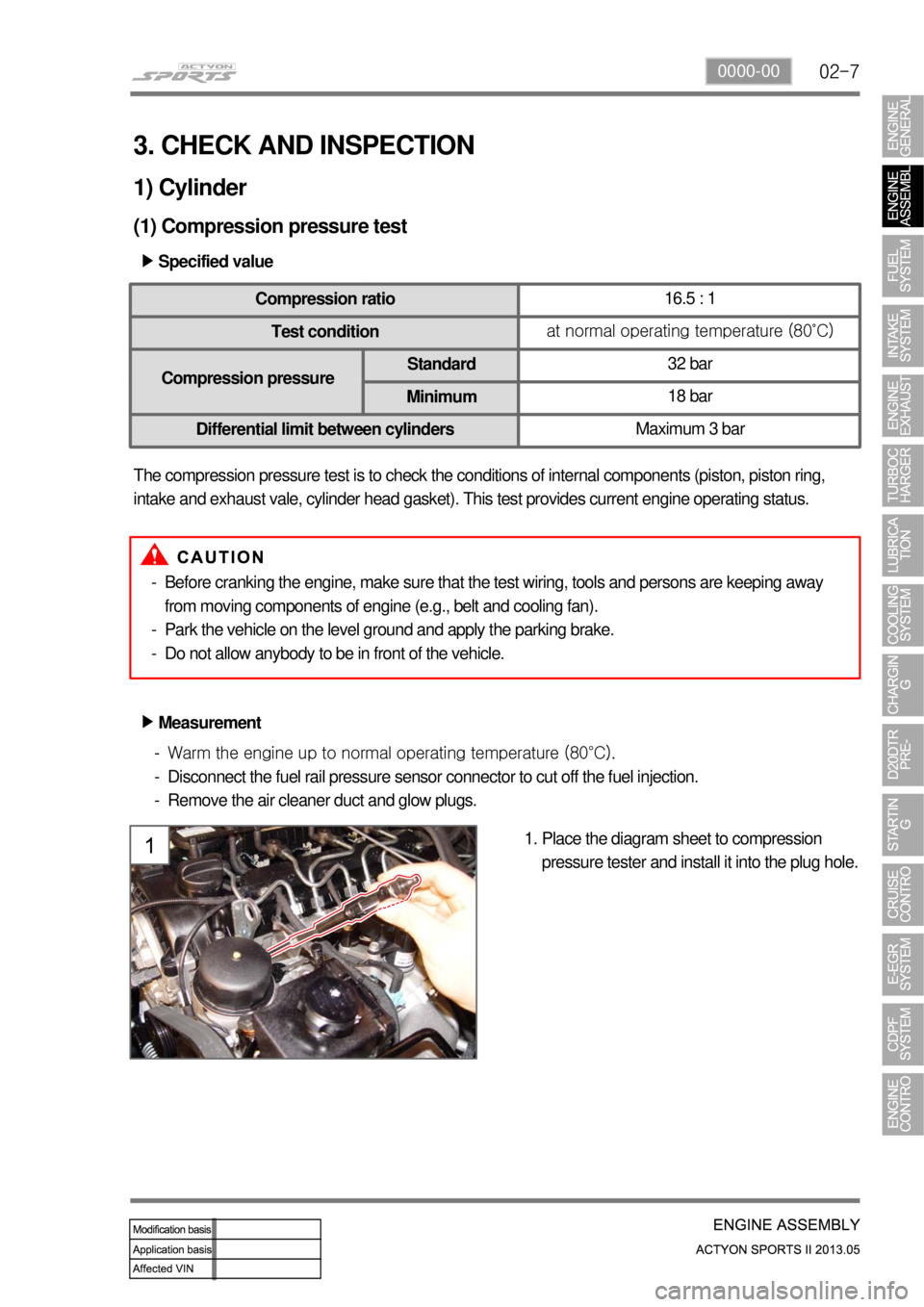
02-70000-00
3. CHECK AND INSPECTION
1) Cylinder
(1) Compression pressure test
Specified value ▶
Compression ratio16.5 : 1
Test conditionat normal operating temperature (80˚C)
Compression pressureStandard32 bar
Minimum18 bar
Differential limit between cylindersMaximum 3 bar
The compression pressure test is to check the conditions of internal components (piston, piston ring,
intake and exhaust vale, cylinder head gasket). This test provides current engine operating status.
Before cranking the engine, make sure that the test wiring, tools and persons are keeping away
from moving components of engine (e.g., belt and cooling fan).
Park the vehicle on the level ground and apply the parking brake.
Do not allow anybody to be in front of the vehicle. -
-
-
Measurement ▶
<007e0088009900940047009b008f008c0047008c0095008e00900095008c0047009c00970047009b00960047009500960099009400880093004700960097008c00990088009b00900095008e0047009b008c00940097008c00990088009b009c0099008c00
47004f005f005700b6006a00500055>
Disconnect the fuel rail pressure sensor connector to cut off the fuel injection.
Remove the air cleaner duct and glow plugs. -
-
-
Place the diagram sheet to compression
pressure tester and install it into the plug hole. 1.
Page 89 of 751
03-12
(5) High Pressure System Pressure Test
Fuel rail pressure test ▶
Disconnect the fuel rail pressure sensor
connector and then IMV connector. 1.
Connect the pressure tester to the fuel rail
pressure sensor connector. 2.
Crank the engine 2 times for 5 seconds. 3.
Read the highest pressure value displayed
on the tester display.
If the highest pressure value is 1,050 bar or
less, refer to the section "Fuel System
Check Process". -
-
Page 92 of 751
03-152210-01
Static test for backleak of injector ▶
Disconnect the injector return hose and cover
the openings with caps shaped screw (included
in the special tool). 1.
Connect the hose of the container for
measuring backleak to the return nipple of the
injector.
(prevent air entry to the low pressure line) 2.
Disconnect the IMV connector of the high
pressure pump and then fuel pressure
sensor connector. 3.
The connector of the injector can be easily
contaminated. Always keep it clean.
Crank the engine 2 times for 5 seconds.
Check the time for flow if injector backleak and
confirm that it is within the specified range. 4.
5.
If the value is out of the specified range,
replace the injector.
SpecificationBelow 20 sec.
Page 94 of 751
03-172210-01
HP pump pressure test ▶
Prepare a special tool for high pressure test
and clean it thoroughly to prevent foreign
materials from entering. 1.
Disconnect the high pressure fuel supply pipe
on the HP pump and install the close rail in the
tool kit. 2.
Connect the other end of the close rail to the
fuel rail for test. 3.
Disconnect the return hose for HP pump and
connect the clear hose and connect its the
other end to the return port of the fuel rail for
test. 4.
Connect the digital tester connector to the
sensor connector of the fuel rail for test.
Crank the engine 2 times for 5 seconds after
removing the IMV connector and fuel rail
pressure sensor connector.
Read the pressure value displayed on the
tester display is within the specified 5.
6.
7.
Specification1,050 bar or more
Page 98 of 751
03-212210-01
1. OVERVIEW
The components in fuel system supply the fuel and generate the high pressure to inject the fuel to each
injector. They are controlled by the engine ECU.
The common rail fuel injection system consists of fuel tank, fuel line, low pressure line which supplies lo
w
pressure fuel to the low pressure pump (including high pressure pump), common rail which distributes
and accumulates the high pressurized fuel from the fuel pump, high pressure line which connected to
the injector, and the engine control unit (ECU) which calculates the accelerator pedal position and
controls the overall performance of vehicle based on the input signals from various sensors.
1) Fuel Flow Diagram