Page 201 of 600
Injector washer puller
2. SPECIAL SERVICE TOOLS
1) Using the Special Service Tools on Engine
Injector pullerGlow plug socket
HP remover/installerHigh pressure pipe
remover/installerCylinder head bolt wrench
Sealing caps
(fuel line)
Page 206 of 600
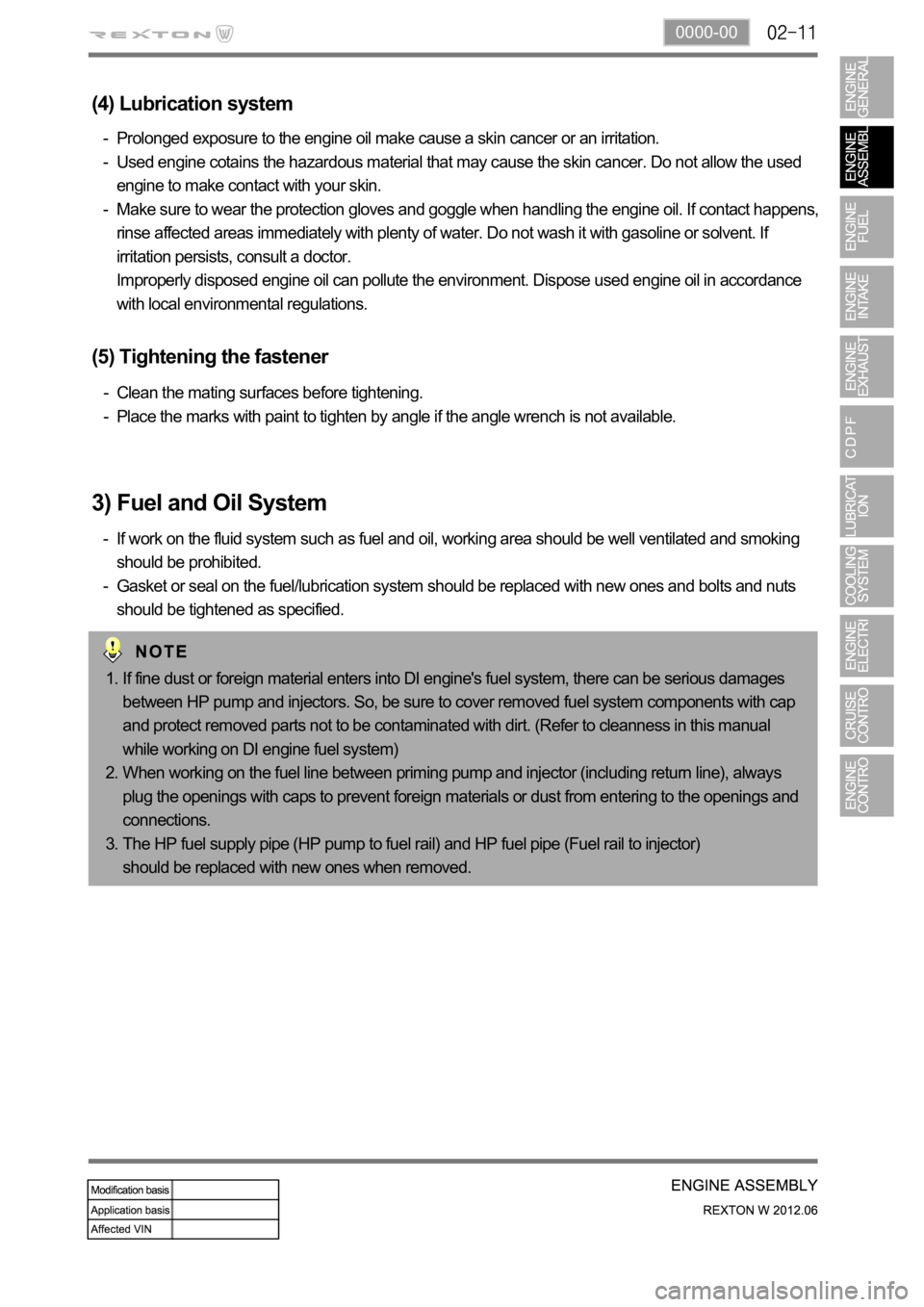
0000-00
(4) Lubrication system
Prolonged exposure to the engine oil make cause a skin cancer or an irritation.
Used engine cotains the hazardous material that may cause the skin cancer. Do not allow the used
engine to make contact with your skin.
Make sure to wear the protection gloves and goggle when handling the engine oil. If contact happens,
rinse affected areas immediately with plenty of water. Do not wash it with gasoline or solvent. If
irritation persists, consult a doctor.
Improperly disposed engine oil can pollute the environment. Dispose used engine oil in accordance
with local environmental regulations. -
-
-
(5) Tightening the fastener
Clean the mating surfaces before tightening.
Place the marks with paint to tighten by angle if the angle wrench is not available. -
-
3) Fuel and Oil System
If work on the fluid system such as fuel and oil, working area should be well ventilated and smoking
should be prohibited.
Gasket or seal on the fuel/lubrication system should be replaced with new ones and bolts and nuts
should be tightened as specified. -
-
If fine dust or foreign material enters into DI engine's fuel system, there can be serious damages
between HP pump and injectors. So, be sure to cover removed fuel system components with cap
and protect removed parts not to be contaminated with dirt. (Refer to cleanness in this manual
while working on DI engine fuel system)
When working on the fuel line between priming pump and injector (including return line), always
plug the openings with caps to prevent foreign materials or dust from entering to the openings and
connections.
The HP fuel supply pipe (HP pump to fuel rail) and HP fuel pipe (Fuel rail to injector)
should be replaced with new ones when removed. 1.
2.
3.
Page 225 of 600
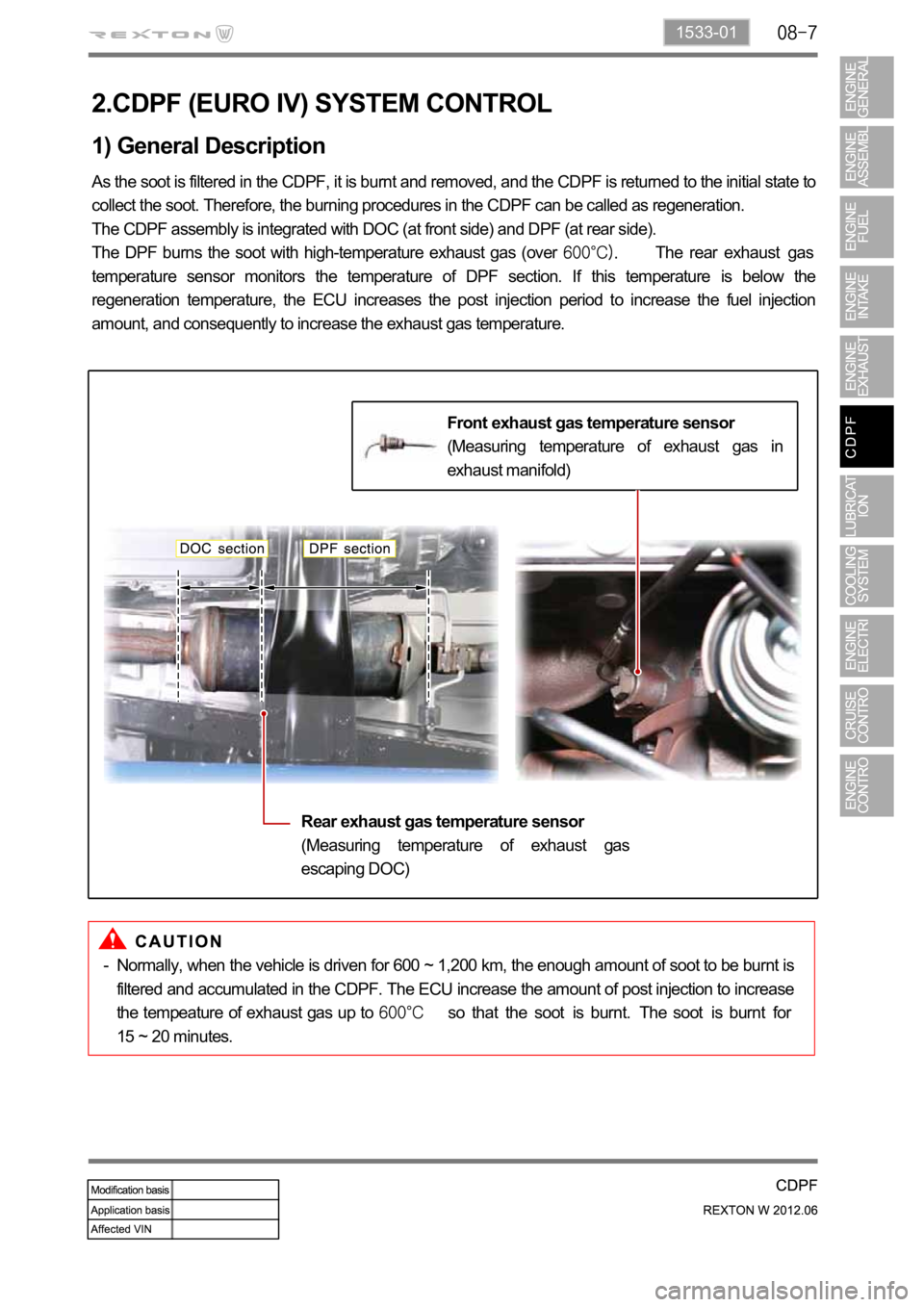
1533-01
2.CDPF (EURO IV) SYSTEM CONTROL
1) General Description
As the soot is filtered in the CDPF, it is burnt and removed, and the CDPF is returned to the initial state to
collect the soot. Therefore, the burning procedures in the CDPF can be called as regeneration.
The CDPF assembly is integrated with DOC (at front side) and DPF (at rear side).
The DPF burns the soot with high-temperature exhaust gas (over
The rear exhaust gas
temperature sensor monitors the temperature of DPF section. If this temperature is below the
regeneration temperature, the ECU increases the post injection period to increase the fuel injection
amount, and consequently to increase the exhaust gas temperature.
Front exhaust gas temperature sensor
(Measuring temperature of exhaust gas in
exhaust manifold)
Rear exhaust gas temperature sensor
(Measuring temperature of exhaust gas
escaping DOC)
Normally, when the vehicle is driven for 600 ~ 1,200 km, the enough amount of soot to be burnt is
filtered and accumulated in the CDPF. The ECU increase the amount of post injection to increase
the tempeature of exhaust gas up to
so that the soot is burnt. The soot is burnt for
15 ~ 20 minutes. -
Page 264 of 600
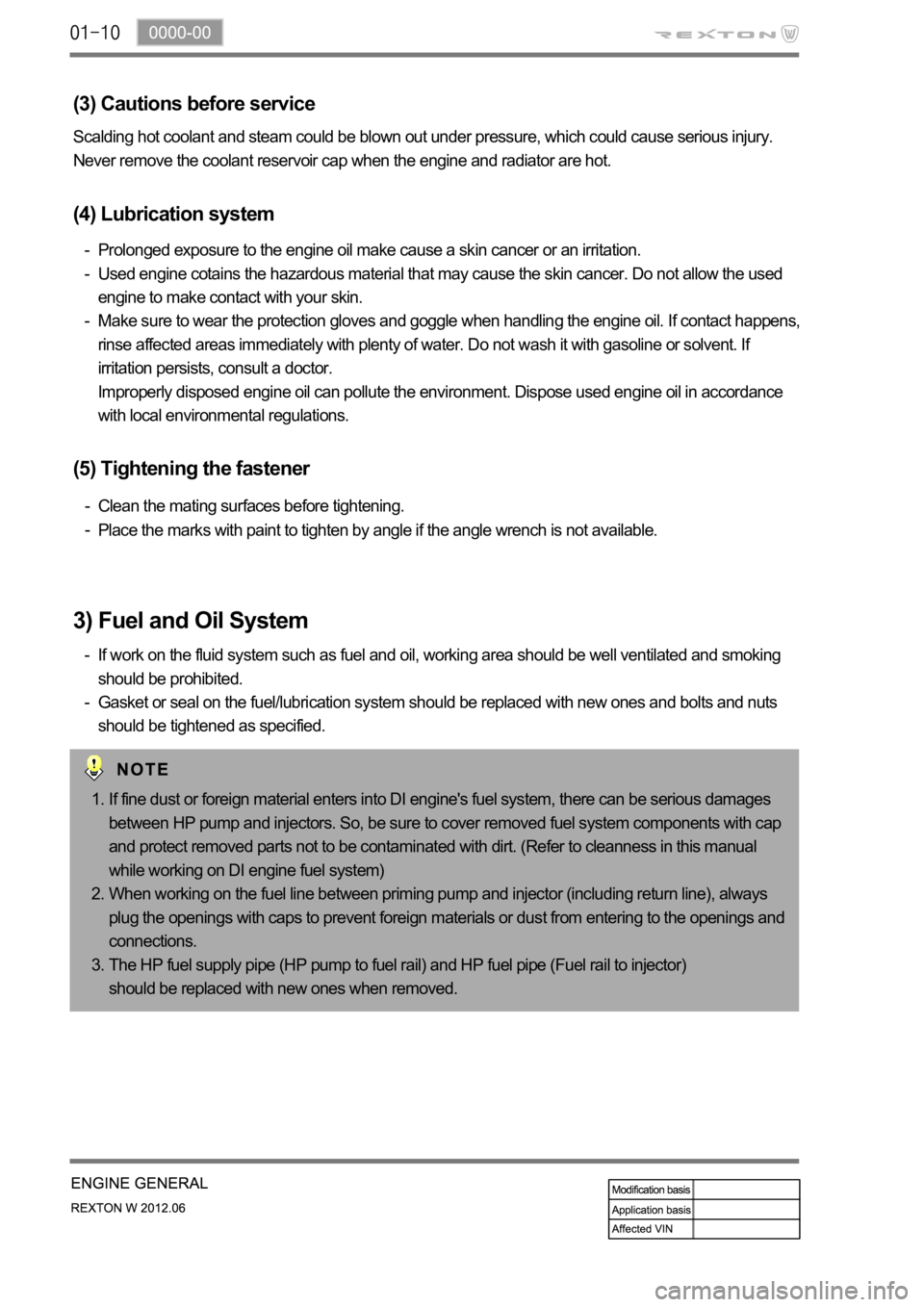
(3) Cautions before service
Prolonged exposure to the engine oil make cause a skin cancer or an irritation.
Used engine cotains the hazardous material that may cause the skin cancer. Do not allow the used
engine to make contact with your skin.
Make sure to wear the protection gloves and goggle when handling the engine oil. If contact happens,
rinse affected areas immediately with plenty of water. Do not wash it with gasoline or solvent. If
irritation persists, consult a doctor.
Improperly disposed engine oil can pollute the environment. Dispose used engine oil in accordance
with local environmental regulations. -
-
-
(5) Tightening the fastener
If fine dust or foreign material enters into DI engine's fuel system, there can be serious damages
between HP pump and injectors. So, be sure to cover removed fuel system components with cap
and protect removed parts not to be contaminated with dirt. (Refer to cleanness in this manual
while working on DI engine fuel system)
When working on the fuel line between priming pump and injector (including return line), always
plug the openings with caps to prevent foreign materials or dust from entering to the openings and
connections.
The HP fuel supply pipe (HP pump to fuel rail) and HP fuel pipe (Fuel rail to injector)
should be replaced with new ones when removed. 1.
2.
3. Scalding hot coolant and steam could be blown out under pressure, which could cause serious injury.
Never remove the coolant reservoir cap when the engine and radiator are hot.
(4) Lubrication system
3) Fuel and Oil System
If work on the fluid system such as fuel and oil, working area should be well ventilated and smoking
should be prohibited.
Gasket or seal on the fuel/lubrication system should be replaced with new ones and bolts and nuts
should be tightened as specified. -
-Clean the mating surfaces before tightening.
Place the marks with paint to tighten by angle if the angle wrench is not available. -
-
Page 268 of 600
Name SizeNumbers of
fastenerTightening
torque (Nm)Note (total
tightening
torque)
Idler pulley/tensioner
pulley1
-
Glow plug M5 4
-
Vacuum pump
3 -
Timing gear case cover
7 -
1 -
3 -
Cylinder head cover
21 -
Oil dipstick gauge cover
1 -
Oil filter cap 1
-
Fuel rail
2 -
Injector clamp bolt
2 -
High pressure pipe
(between high pressure
pump and fuel rail
assembly)M17 1
-
High pressure pipe
(between fuel rail
assembly and injector)M17 4
-
Crankshaft position
sensor
1 -
Main wiring
5 -
Intake duct
3 -
Power steering pump
3 -
Cylinder head front cover
5 -
Page 273 of 600
Component SizeBolt
QuantitySpecified torque
(Nm)Remark
(Total torque)
Glow plug M5 4
-
Vacuum pump
3 -
Timing gear case cover
3 -
7 -
1 -
3 -
Cylinder head cover
21 -
Oil gauge tube
1 -
Oil filter cap 1
-
Fuel rail
2 -
Injector clamp bolt
2 -
High pressure pipe
(between HP pump and
fuel rail)M17 1
-
High pressure pipe
(between fuel rail and
injector)M17 4
-
Crank position sensor
1 -
Main wiring
5 -
Intake duct M8x25 4
-
Power steering pump
3 -
Cylinder head front cover
5 -
Ladder frame
5 -
Oil pump
3 -
Page 279 of 600
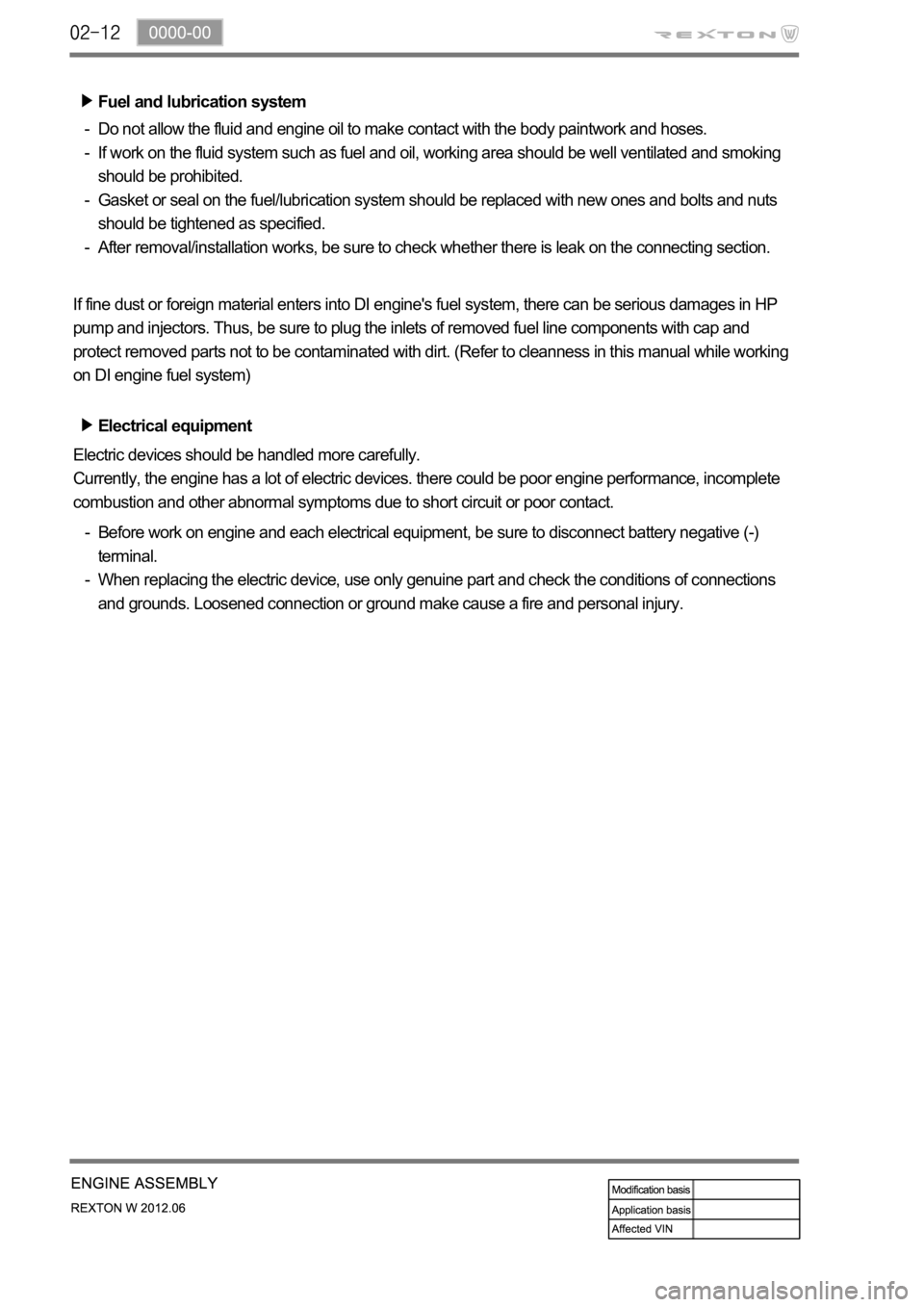
Electrical equipment
Electric devices should be handled more carefully.
Currently, the engine has a lot of electric devices. there could be poor engine performance, incomplete
combustion and other abnormal symptoms due to short circuit or poor contact.
Before work on engine and each electrical equipment, be sure to disconnect battery negative (-)
terminal.
When replacing the electric device, use only genuine part and check the conditions of connections
and grounds. Loosened connection or ground make cause a fire and personal injury. -
-Fuel and lubrication system
Do not allow the fluid and engine oil to make contact with the body paintwork and hoses.
If work on the fluid system such as fuel and oil, working area should be well ventilated and smoking
should be prohibited.
Gasket or seal on the fuel/lubrication system should be replaced with new ones and bolts and nuts
should be tightened as specified.
After removal/installation works, be sure to check whether there is leak on the connecting section. -
-
-
-
If fine dust or foreign material enters into DI engine's fuel system, there can be serious damages in HP
pump and injectors. Thus, be sure to plug the inlets of removed fuel line components with cap and
protect removed parts not to be contaminated with dirt. (Refer to cleanness in this manual while working
on DI engine fuel system)
Page 317 of 600
2210-01
1. SPECIFICATION
Description Specification
Fuel Diesel
Fuel filterType Fuel heater + priming pump + water
separator integrated type
Filter type Changeable filter element type
Water accumulating capacity 200 cc
Heater capacity 250W 13.5V
Injector System pressure 1800 bar
High pressure fuel
pumpType Eccentric cam/Plunger type
Operating type Gear driven type
Normal operating temperature
Operating pressure 1800 bar
Operating temperature
Low pressure fuel
pumpType Vane type
Gear ratio (pump/engine) 0.5 : 1
Pressure 6 bar
Fuel tankCapacity 75 L
Material Steel
Fuel sender Single sender type
Change interval EU every 40,000 km
GEN every 45,000 km
Water separation
intervalEU every 20,000 km
GEN every 15,000 km