Page 852 of 3039
1 Pin journal classification and plant identification 2 Main journal classification 3 Date and time codes The main bearings are numbered 1 to 5 starting from the front of the engine. There are five grades of main bearing available,
each being color coded. Journal sizes are marked on the rear of the crankshaft. For further information refer to Engine - 5.0L,
Vehicles With: Supercharger - General Procedures.
Crankshaft Installation
Page 853 of 3039
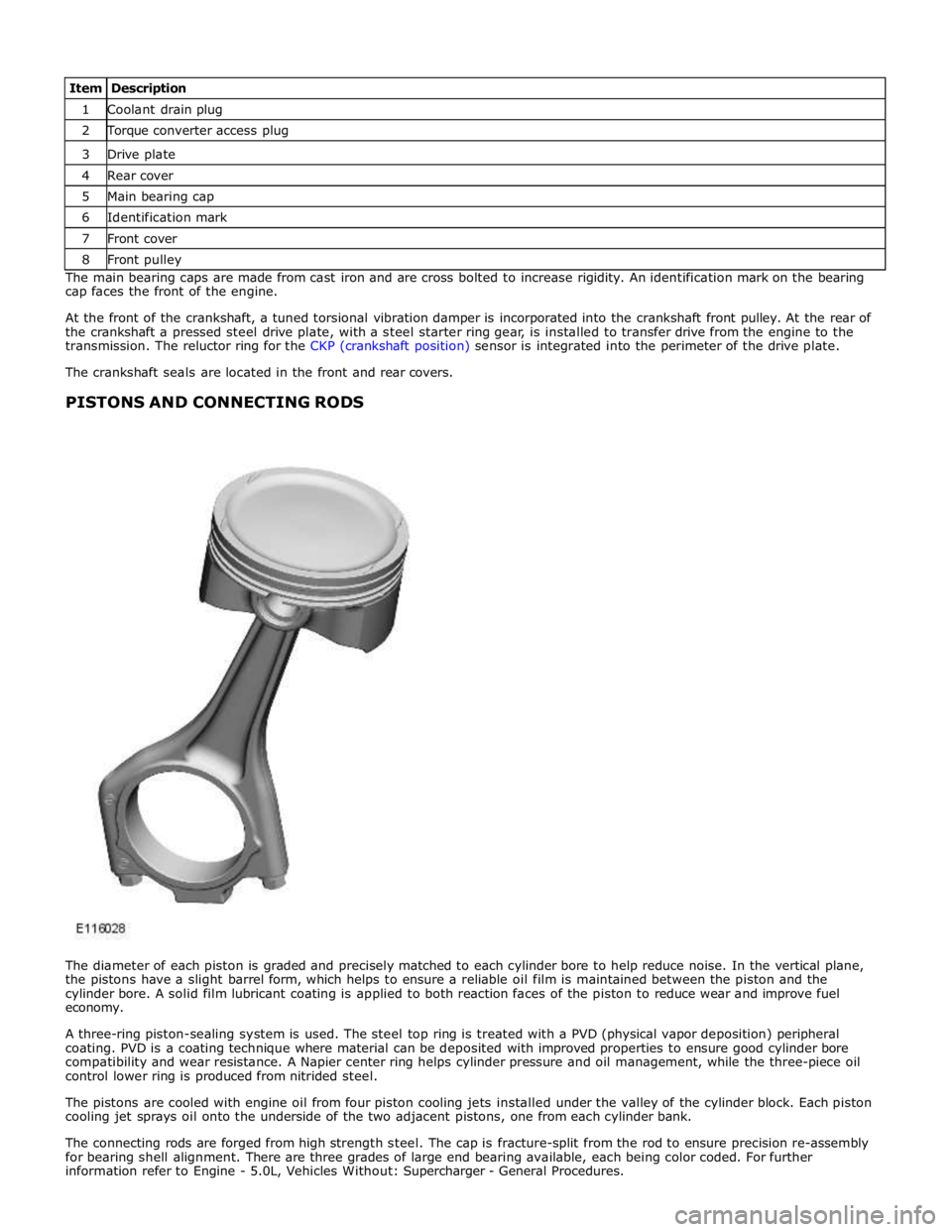
1 Coolant drain plug 2 Torque converter access plug 3 Drive plate 4 Rear cover 5 Main bearing cap 6 Identification mark 7 Front cover 8 Front pulley The main bearing caps are made from cast iron and are cross bolted to increase rigidity. An identification mark on the bearing
cap faces the front of the engine.
At the front of the crankshaft, a tuned torsional vibration damper is incorporated into the crankshaft front pulley. At the rear of
the crankshaft a pressed steel drive plate, with a steel starter ring gear, is installed to transfer drive from the engine to the
transmission. The reluctor ring for the CKP (crankshaft position) sensor is integrated into the perimeter of the drive plate.
The crankshaft seals are located in the front and rear covers.
PISTONS AND CONNECTING RODS
The diameter of each piston is graded and precisely matched to each cylinder bore to help reduce noise. In the vertical plane,
the pistons have a slight barrel form, which helps to ensure a reliable oil film is maintained between the piston and the
cylinder bore. A solid film lubricant coating is applied to both reaction faces of the piston to reduce wear and improve fuel
economy.
A three-ring piston-sealing system is used. The steel top ring is treated with a PVD (physical vapor deposition) peripheral
coating. PVD is a coating technique where material can be deposited with improved properties to ensure good cylinder bore
compatibility and wear resistance. A Napier center ring helps cylinder pressure and oil management, while the three-piece oil
control lower ring is produced from nitrided steel.
The pistons are cooled with engine oil from four piston cooling jets installed under the valley of the cylinder block. Each piston
cooling jet sprays oil onto the underside of the two adjacent pistons, one from each cylinder bank.
The connecting rods are forged from high strength steel. The cap is fracture-split from the rod to ensure precision re-assembly
for bearing shell alignment. There are three grades of large end bearing available, each being color coded. For further
information refer to Engine - 5.0L, Vehicles Without: Supercharger - General Procedures.
Page 855 of 3039
A Front of engine 1 Alignment mark 2 LH side (bank B) 3 Alignment mark 4 RH side (bank A) 5 Piston orientation arrow The orientation of the connecting rods and pistons on the crankshaft are given below:
Bank A - The arrow on the piston crown must face the front of the engine and the cap and connecting rod alignment
marks must face the rear of the engine.
Bank B - The arrow on the piston crown must face the front of the engine and the cap and connecting rod alignment
marks must face the front of the engine.
Page 858 of 3039
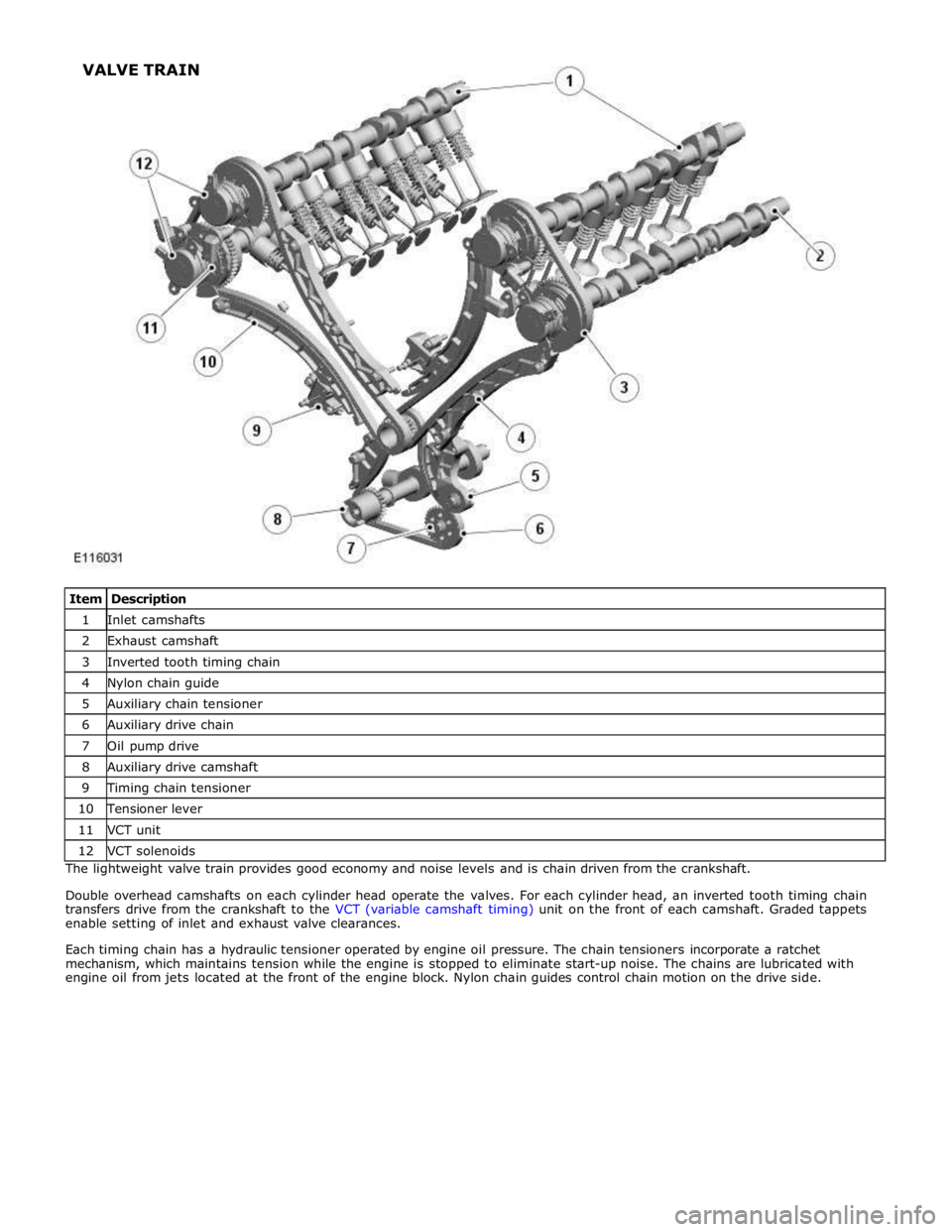
1 Inlet camshafts 2 Exhaust camshaft 3 Inverted tooth timing chain 4 Nylon chain guide 5 Auxiliary chain tensioner 6 Auxiliary drive chain 7 Oil pump drive 8 Auxiliary drive camshaft 9 Timing chain tensioner 10 Tensioner lever 11 VCT unit 12 VCT solenoids The lightweight valve train provides good economy and noise levels and is chain driven from the crankshaft.
Double overhead camshafts on each cylinder head operate the valves. For each cylinder head, an inverted tooth timing chain
transfers drive from the crankshaft to the VCT (variable camshaft timing) unit on the front of each camshaft. Graded tappets
enable setting of inlet and exhaust valve clearances.
Each timing chain has a hydraulic tensioner operated by engine oil pressure. The chain tensioners incorporate a ratchet
mechanism, which maintains tension while the engine is stopped to eliminate start-up noise. The chains are lubricated with
engine oil from jets located at the front of the engine block. Nylon chain guides control chain motion on the drive side. VALVE TRAIN
Page 859 of 3039
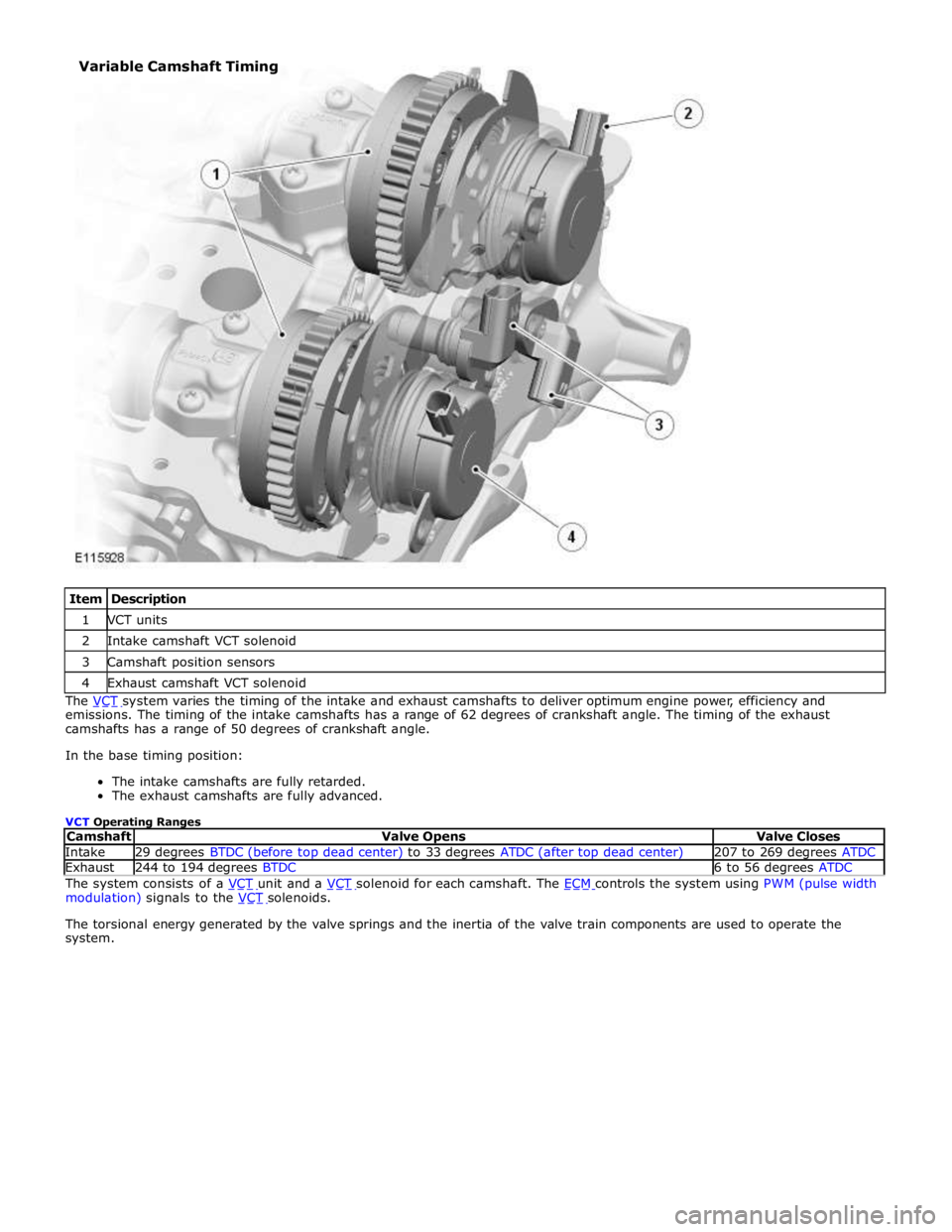
1 VCT units 2 Intake camshaft VCT solenoid 3 Camshaft position sensors 4 Exhaust camshaft VCT solenoid The VCT system varies the timing of the intake and exhaust camshafts to deliver optimum engine power, efficiency and emissions. The timing of the intake camshafts has a range of 62 degrees of crankshaft angle. The timing of the exhaust
camshafts has a range of 50 degrees of crankshaft angle.
In the base timing position:
The intake camshafts are fully retarded.
The exhaust camshafts are fully advanced.
VCT Operating Ranges
Camshaft Valve Opens Valve Closes Intake 29 degrees BTDC (before top dead center) to 33 degrees ATDC (after top dead center) 207 to 269 degrees ATDC Exhaust 244 to 194 degrees BTDC 6 to 56 degrees ATDC The system consists of a VCT unit and a VCT solenoid for each camshaft. The ECM controls the system using PWM (pulse width modulation) signals to the VCT solenoids.
The torsional energy generated by the valve springs and the inertia of the valve train components are used to operate the
system. Variable Camshaft Timing
Page 861 of 3039
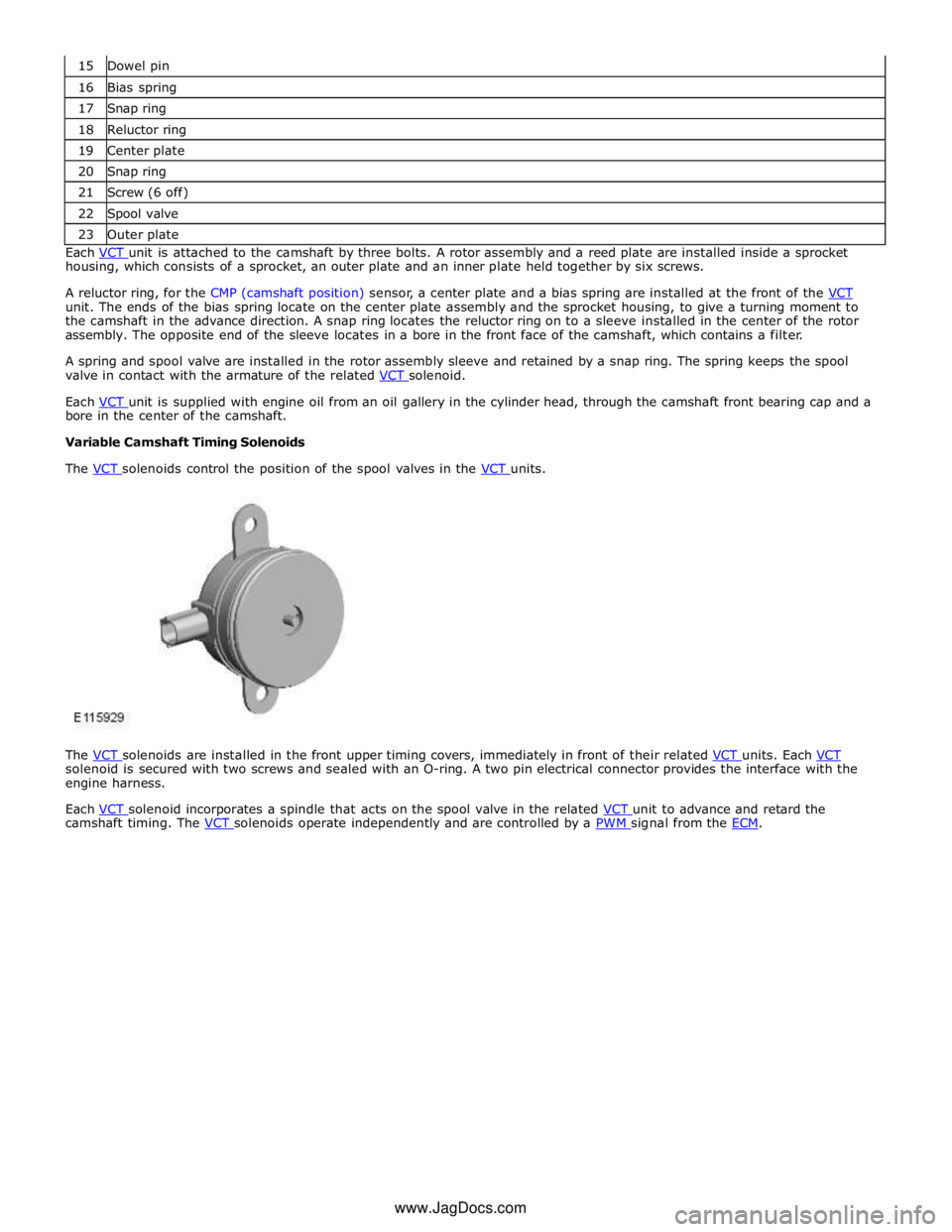
16 Bias spring 17 Snap ring 18 Reluctor ring 19 Center plate 20 Snap ring 21 Screw (6 off) 22 Spool valve 23 Outer plate Each VCT unit is attached to the camshaft by three bolts. A rotor assembly and a reed plate are installed inside a sprocket housing, which consists of a sprocket, an outer plate and an inner plate held together by six screws.
A reluctor ring, for the CMP (camshaft position) sensor, a center plate and a bias spring are installed at the front of the VCT unit. The ends of the bias spring locate on the center plate assembly and the sprocket housing, to give a turning moment to
the camshaft in the advance direction. A snap ring locates the reluctor ring on to a sleeve installed in the center of the rotor
assembly. The opposite end of the sleeve locates in a bore in the front face of the camshaft, which contains a filter.
A spring and spool valve are installed in the rotor assembly sleeve and retained by a snap ring. The spring keeps the spool
valve in contact with the armature of the related VCT solenoid.
Each VCT unit is supplied with engine oil from an oil gallery in the cylinder head, through the camshaft front bearing cap and a bore in the center of the camshaft.
Variable Camshaft Timing Solenoids
The VCT solenoids control the position of the spool valves in the VCT units.
The VCT solenoids are installed in the front upper timing covers, immediately in front of their related VCT units. Each VCT solenoid is secured with two screws and sealed with an O-ring. A two pin electrical connector provides the interface with the
engine harness.
Each VCT solenoid incorporates a spindle that acts on the spool valve in the related VCT unit to advance and retard the camshaft timing. The VCT solenoids operate independently and are controlled by a PWM signal from the ECM. www.JagDocs.com
Page 862 of 3039
Variable Camshaft Timing Operation
When the engine is running, the compression and expansion of the valve springs causes momentary increases and decreases
in the torque acting on the camshafts. These momentary changes of torque are sensed in the VCT units and used to change the camshaft timing.
ItC
em Description A Camshaft torque B Camshaft rotation (degrees) Valve opening D Peak lift E Valve closing 1 1000 rev/min 2 4000 rev/min 3 7000 rev/min 4 Inertia effects from valve train rotating components 5 Force caused by valve spring 6 Bias torque from friction
NOTE: Intake camshaft VCT unit shown. For exhaust camshaft VCT unit, read advance for retard and retard for advance.
Page 863 of 3039
1 Advance chamber 2 Retard chamber 3 Sprocket housing 4 Rotor assembly 5 Lock pin 6 Sleeve 7 Engine oil supply from camshaft 8 Inlet check valve 9 Lock pin drain 10 Spool valve 11 Advance check valve 12 Retard check valve At engine start-up, once the engine oil pressure in the camshaft is sufficient to open the inlet check valve, engine oil flows
across the spool valve, through the advance and retard check valves and into the advance and retard chambers. During the
start cycle, the ECM signals the VCT solenoid to move the spool valve into the sleeve and connect the lock pin to inlet oil