Page 9 of 269
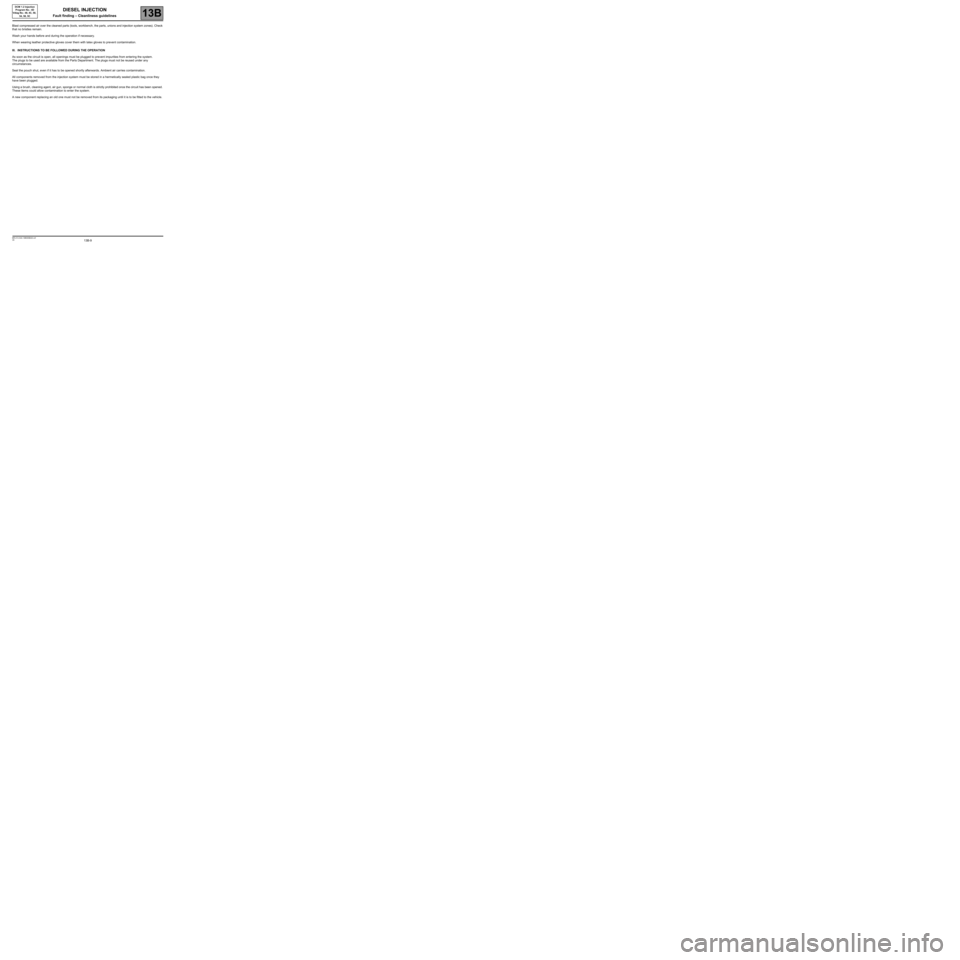
13B-9V6 MR-413-X44-13B000$020.mif
DIESEL INJECTION
Fault finding – Cleanliness guidelines13B
DCM 1.2 Injection
Program No.: 4D
Vdiag No.: 48, 4C, 50,
54, 58, 5C
Blast compressed air over the cleaned parts (tools, workbench, the parts, unions and injection system zones). Check
that no bristles remain.
Wash your hands before and during the operation if necessary.
When wearing leather protective gloves cover them with latex gloves to prevent contamination.
III. INSTRUCTIONS TO BE FOLLOWED DURING THE OPERATION
As soon as the circuit is open, all openings must be plugged to prevent impurities from entering the system.
The plugs to be used are available from the Parts Department. The plugs must not be reused under any
circumstances.
Seal the pouch shut, even if it has to be opened shortly afterwards. Ambient air carries contamination.
All components removed from the injection system must be stored in a hermetically sealed plastic bag once they
have been plugged.
Using a brush, cleaning agent, air gun, sponge or normal cloth is strictly prohibited once the circuit has been opened.
These items could allow contamination to enter the system.
A new component replacing an old one must not be removed from its packaging until it is to be fitted to the vehicle.
Page 10 of 269
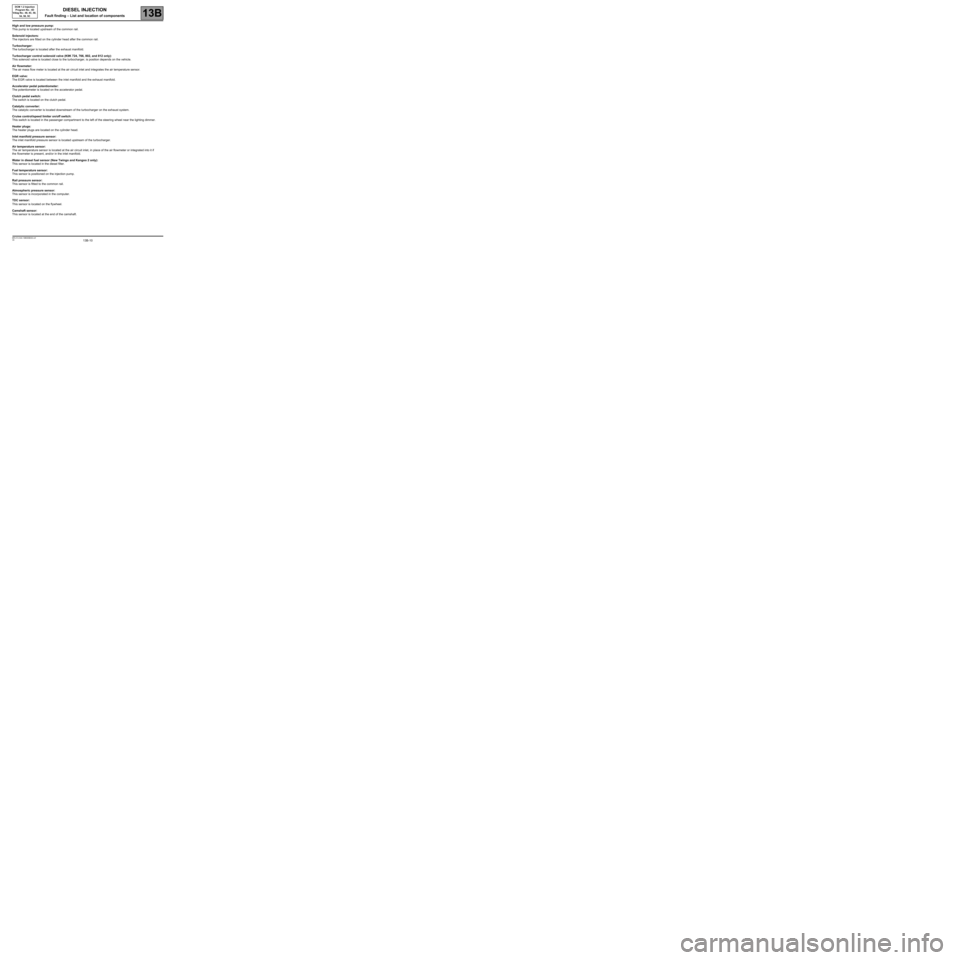
13B-10V6 MR-413-X44-13B000$030.mif
13B
DCM 1.2 Injection
Program No.: 4D
Vdiag No.: 48, 4C, 50,
54, 58, 5C
High and low pressure pump:
This pump is located upstream of the common rail.
Solenoid injectors:
The injectors are fitted on the cylinder head after the common rail.
Turbocharger:
The turbocharger is located after the exhaust manifold.
Turbocharger control solenoid valve (K9K 724, 766, 802, and 812 only):
This solenoid valve is located close to the turbocharger, is position depends on the vehicle.
Air flowmeter:
The air mass flow meter is located at the air circuit inlet and integrates the air temperature sensor.
EGR valve:
The EGR valve is located between the inlet manifold and the exhaust manifold.
Accelerator pedal potentiometer:
The potentiometer is located on the accelerator pedal.
Clutch pedal switch:
The switch is located on the clutch pedal.
Catalytic converter:
The catalytic converter is located downstream of the turbocharger on the exhaust system.
Cruise control/speed limiter on/off switch:
This switch is located in the passenger compartment to the left of the steering wheel near the lighting dimmer.
Heater plugs:
The heater plugs are located on the cylinder head.
Inlet manifold pressure sensor:
The inlet manifold pressure sensor is located upstream of the turbocharger.
Air temperature sensor:
The air temperature sensor is located at the air circuit inlet, in place of the air flowmeter or integrated into it if
the flowmeter is present, and/or in the inlet manifold.
Water in diesel fuel sensor (New Twingo and Kangoo 2 only):
This sensor is located in the diesel filter.
Fuel temperature sensor:
This sensor is positioned on the injection pump.
Rail pressure sensor:
This sensor is fitted to the common rail.
Atmospheric pressure sensor:
This sensor is incorporated in the computer.
TDC sensor:
This sensor is located on the flywheel.
Camshaft sensor:
This sensor is located at the end of the camshaft.
DIESEL INJECTION
Fault finding – List and location of components
Page 11 of 269
13B-11V6 MR-413-X44-13B000$030.mif
DIESEL INJECTION
Fault finding – List and location of components13B
DCM 1.2 Injection
Program No.: 4D
Vdiag No.: 48, 4C, 50,
54, 58, 5C
Refrigerant pressure sensor:
This sensor is located on the coolant circuit.
Engine coolant temperature sensor:
This sensor is located on the cylinder head near the engine water chamber.
Accelerometer:
This sensor is located on the cylinder block.
Passenger compartment heating resistor relay:
These relays are located in the engine compartment relay unit.
Air conditioning compressor relays:
These relays are located in the engine compartment relay unit.
Fan unit relay:
These relays are located in the engine compartment relay unit.
Page 12 of 269
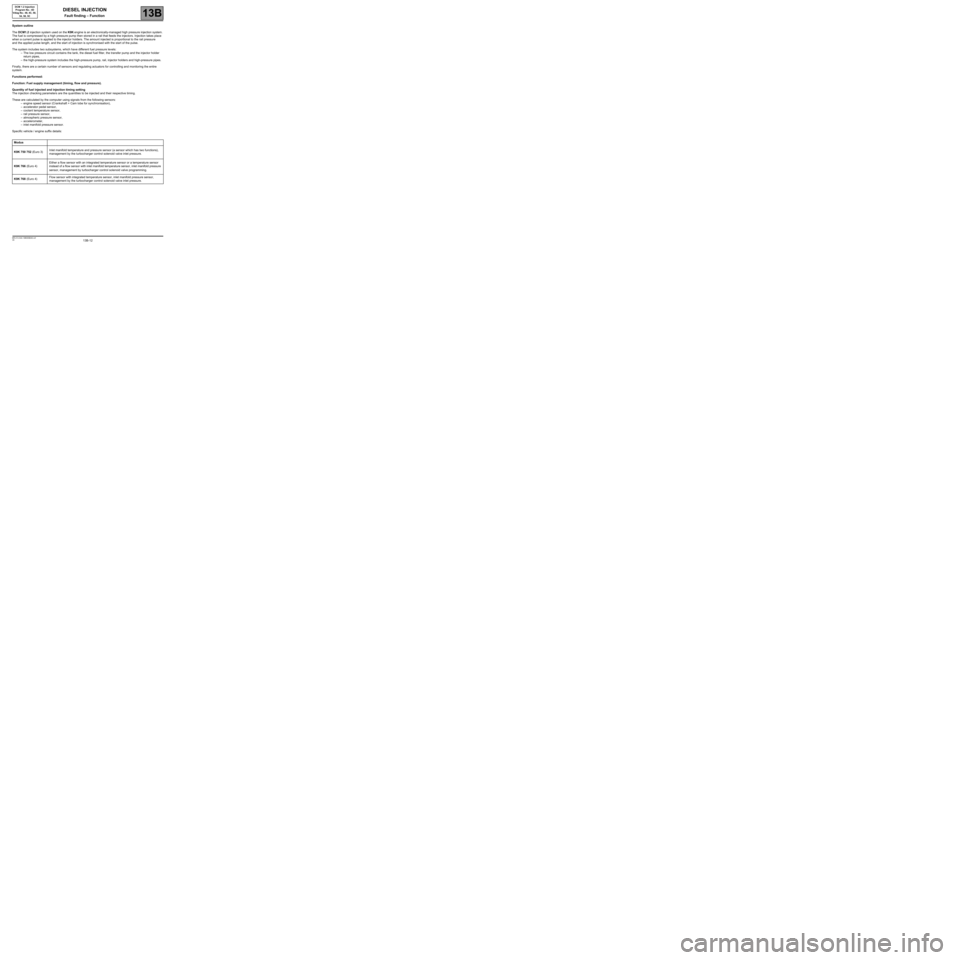
13B-12V6 MR-413-X44-13B000$040.mif
13B
DCM 1.2 Injection
Program No.: 4D
Vdiag No.: 48, 4C, 50,
54, 58, 5C
System outline
The DCM1.2 injection system used on the K9K engine is an electronically-managed high pressure injection system.
The fuel is compressed by a high pressure pump then stored in a rail that feeds the injectors. Injection takes place
when a current pulse is applied to the injector holders. The amount injected is proportional to the rail pressure
and the applied pulse length, and the start of injection is synchronised with the start of the pulse.
The system includes two subsystems, which have different fuel pressure levels:
–The low pressure circuit contains the tank, the diesel fuel filter, the transfer pump and the injector holder
return pipes,
–the high-pressure system includes the high-pressure pump, rail, injector holders and high-pressure pipes.
Finally, there are a certain number of sensors and regulating actuators for controlling and monitoring the entire
system.
Functions performed:
Function: Fuel supply management (timing, flow and pressure).
Quantity of fuel injected and injection timing setting
The injection checking parameters are the quantities to be injected and their respective timing.
These are calculated by the computer using signals from the following sensors:
–engine speed sensor (Crankshaft + Cam lobe for synchronisation),
–accelerator pedal sensor,
–coolant temperature sensor,
–rail pressure sensor,
–atmospheric pressure sensor,
–accelerometer,
–inlet manifold pressure sensor.
Specific vehicle / engine suffix details:
Modus
K9K 750 752 (Euro 3)Inlet manifold temperature and pressure sensor (a sensor which has two functions),
management by the turbocharger control solenoid valve inlet pressure.
K9K 766 (Euro 4)Either a flow sensor with an integrated temperature sensor or a temperature sensor
instead of a flow sensor with inlet manifold temperature sensor, inlet manifold pressure
sensor, management by turbocharger control solenoid valve programming.
K9K 768 (Euro 4)Flow sensor with integrated temperature sensor, inlet manifold pressure sensor,
management by the turbocharger control solenoid valve inlet pressure.
DIESEL INJECTION
Fault finding – Function
Page 13 of 269
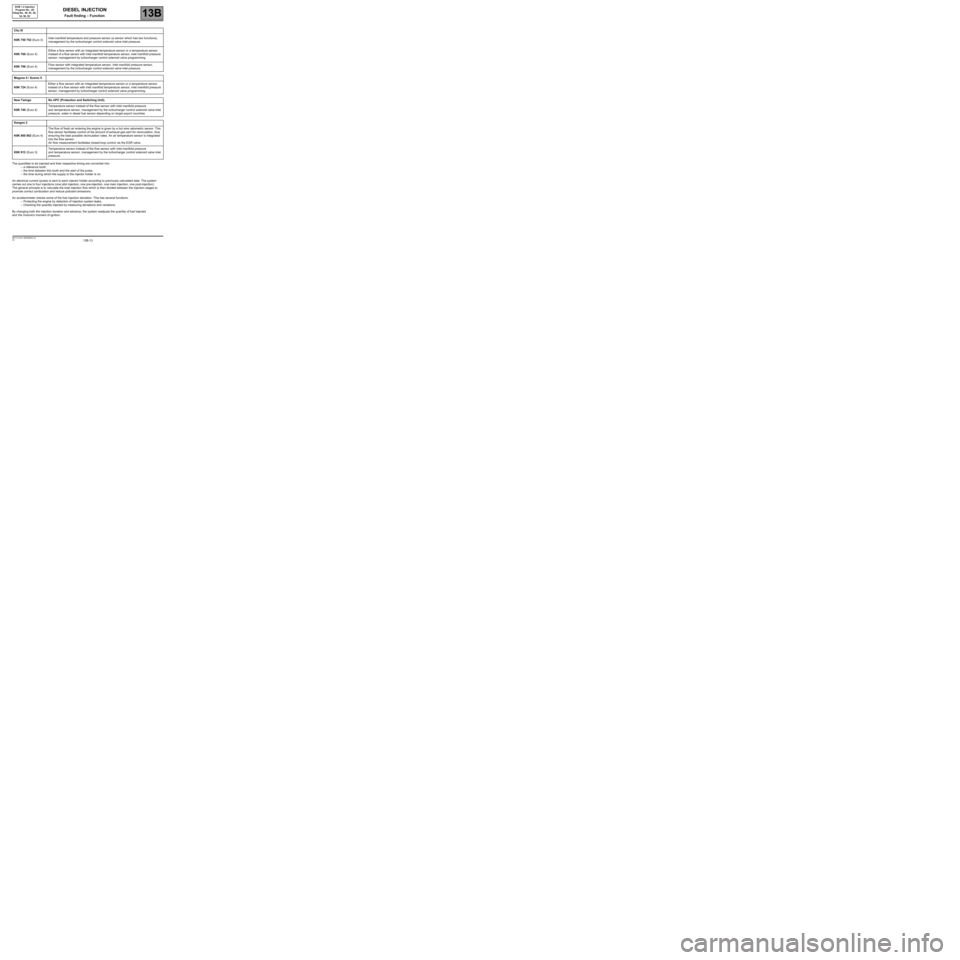
13B-13V6 MR-413-X44-13B000$040.mif
DIESEL INJECTION
Fault finding – Function13B
DCM 1.2 Injection
Program No.: 4D
Vdiag No.: 48, 4C, 50,
54, 58, 5C
The quantities to be injected and their respective timing are converted into:
–a reference tooth,
–the time between this tooth and the start of the pulse,
–the time during which the supply to the injector holder is on.
An electrical current (pulse) is sent to each injector holder according to previously calculated data. The system
carries out one to four injections (one pilot injection, one pre-injection, one main injection, one post-injection).
The general principle is to calculate the total injection flow which is then divided between the injection stages to
promote correct combustion and reduce pollutant emissions.
An accelerometer checks some of the fuel injection deviation. This has several functions:
–Protecting the engine by detection of injection system leaks.
–Checking the quantity injected by measuring deviations and variations.
By changing both the injection duration and advance, the system readjusts the quantity of fuel injected
and the mixture's moment of ignition.Clio III
K9K 750 752 (Euro 3)Inlet manifold temperature and pressure sensor (a sensor which has two functions),
management by the turbocharger control solenoid valve inlet pressure.
K9K 766 (Euro 4)Either a flow sensor with an integrated temperature sensor or a temperature sensor
instead of a flow sensor with inlet manifold temperature sensor, inlet manifold pressure
sensor, management by turbocharger control solenoid valve programming.
K9K 768 (Euro 4)Flow sensor with integrated temperature sensor, inlet manifold pressure sensor,
management by the turbocharger control solenoid valve inlet pressure.
Megane II / Scenic II
K9K 724 (Euro 4)Either a flow sensor with an integrated temperature sensor or a temperature sensor
instead of a flow sensor with inlet manifold temperature sensor, inlet manifold pressure
sensor, management by turbocharger control solenoid valve programming.
New Twingo No UPC (Protection and Switching Unit).
K9K 740 (Euro 4)Temperature sensor instead of the flow sensor with inlet manifold pressure
and temperature sensor, management by the turbocharger control solenoid valve inlet
pressure, water in diesel fuel sensor depending on target export countries.
Kangoo 2
K9K 800 802 (Euro 4)The flow of fresh air entering the engine is given by a hot wire ratiometric sensor. This
flow sensor facilitates control of the amount of exhaust gas sent for recirculation, thus
ensuring the best possible recirculation rates. An air temperature sensor is integrated
into the flow sensor.
Air flow measurement facilitates closed-loop control via the EGR valve.
K9K 812 (Euro 3)Temperature sensor instead of the flow sensor with inlet manifold pressure
and temperature sensor, management by the turbocharger control solenoid valve inlet
pressure.
Page 14 of 269
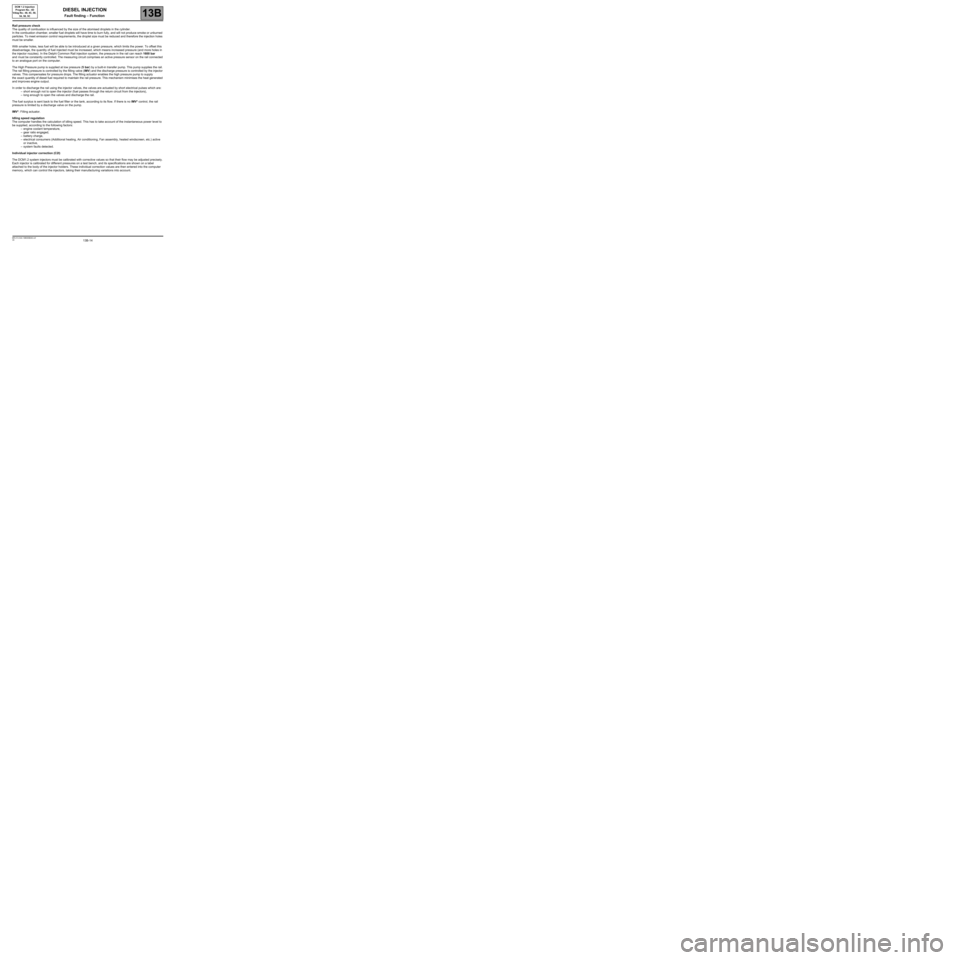
13B-14V6 MR-413-X44-13B000$040.mif
DIESEL INJECTION
Fault finding – Function13B
DCM 1.2 Injection
Program No.: 4D
Vdiag No.: 48, 4C, 50,
54, 58, 5C
Rail pressure check
The quality of combustion is influenced by the size of the atomised droplets in the cylinder.
In the combustion chamber, smaller fuel droplets will have time to burn fully, and will not produce smoke or unburned
particles. To meet emission control requirements, the droplet size must be reduced and therefore the injection holes
must be smaller.
With smaller holes, less fuel will be able to be introduced at a given pressure, which limits the power. To offset this
disadvantage, the quantity of fuel injected must be increased, which means increased pressure (and more holes in
the injector nozzles). In the Delphi Common Rail injection system, the pressure in the rail can reach 1600 bar
and must be constantly controlled. The measuring circuit comprises an active pressure sensor on the rail connected
to an analogue port on the computer.
The High Pressure pump is supplied at low pressure (5 bar) by a built-in transfer pump. This pump supplies the rail.
The rail filling pressure is controlled by the filling valve (IMV) and the discharge pressure is controlled by the injector
valves. This compensates for pressure drops. The filling actuator enables the high pressure pump to supply
the exact quantity of diesel fuel required to maintain the rail pressure. This mechanism minimises the heat generated
and improves engine output.
In order to discharge the rail using the injector valves, the valves are actuated by short electrical pulses which are:
–short enough not to open the injector (fuel passes through the return circuit from the injectors),
–long enough to open the valves and discharge the rail.
The fuel surplus is sent back to the fuel filter or the tank, according to its flow. If there is no IMV* control, the rail
pressure is limited by a discharge valve on the pump.
IMV*: Filling actuator.
Idling speed regulation
The computer handles the calculation of idling speed. This has to take account of the instantaneous power level to
be supplied, according to the following factors:
–engine coolant temperature,
–gear ratio engaged,
–battery charge,
–electrical consumers (Additional heating, Air conditioning, Fan assembly, heated windscreen, etc.) active
or inactive,
–system faults detected.
Individual injector correction (C2I)
The DCM1.2 system injectors must be calibrated with corrective values so that their flow may be adjusted precisely.
Each injector is calibrated for different pressures on a test bench, and its specifications are shown on a label
attached to the body of the injector holders. These individual correction values are then entered into the computer
memory, which can control the injectors, taking their manufacturing variations into account.
Page 15 of 269
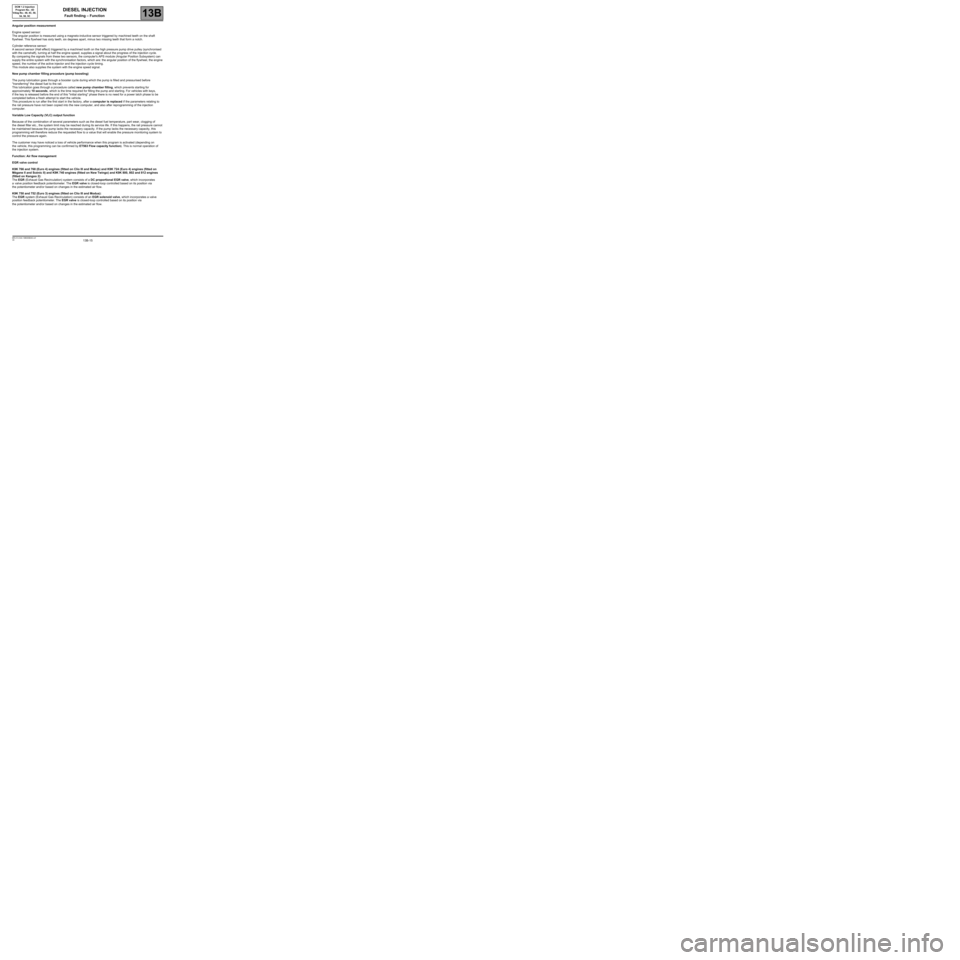
13B-15V6 MR-413-X44-13B000$040.mif
DIESEL INJECTION
Fault finding – Function13B
DCM 1.2 Injection
Program No.: 4D
Vdiag No.: 48, 4C, 50,
54, 58, 5C
Angular position measurement
Engine speed sensor:
The angular position is measured using a magneto-inductive sensor triggered by machined teeth on the shaft
flywheel. This flywheel has sixty teeth, six degrees apart, minus two missing teeth that form a notch.
Cylinder reference sensor:
A second sensor (Hall effect) triggered by a machined tooth on the high pressure pump drive pulley (synchronised
with the camshaft), turning at half the engine speed, supplies a signal about the progress of the injection cycle.
By comparing the signals from these two sensors, the computer's APS module (Angular Position Subsystem) can
supply the entire system with the synchronisation factors, which are: the angular position of the flywheel, the engine
speed, the number of the active injector and the injection cycle timing.
This module also supplies the system with the engine speed signal.
New pump chamber filling procedure (pump boosting)
The pump lubrication goes through a booster cycle during which the pump is filled and pressurised before
"transferring" the diesel fuel to the rail.
This lubrication goes through a procedure called new pump chamber filling, which prevents starting for
approximately 10 seconds, which is the time required for filling the pump and starting. For vehicles with keys,
if the key is released before the end of this "initial starting" phase there is no need for a power latch phase to be
completed before a fresh attempt to start the vehicle.
This procedure is run after the first start in the factory, after a computer is replaced if the parameters relating to
the rail pressure have not been copied into the new computer, and also after reprogramming of the injection
computer.
Variable Low Capacity (VLC) output function
Because of the combination of several parameters such as the diesel fuel temperature, part wear, clogging of
the diesel filter etc., the system limit may be reached during its service life. If this happens, the rail pressure cannot
be maintained because the pump lacks the necessary capacity. If the pump lacks the necessary capacity, this
programming will therefore reduce the requested flow to a value that will enable the pressure monitoring system to
control the pressure again.
The customer may have noticed a loss of vehicle performance when this program is activated (depending on
the vehicle, this programming can be confirmed by ET563 Flow capacity function). This is normal operation of
the injection system.
Function: Air flow management
EGR valve control
K9K 766 and 768 (Euro 4) engines (fitted on Clio III and Modus) and K9K 724 (Euro 4) engines (fitted on
Mégane II and Scénic II) and K9K 740 engines (fitted on New Twingo) and K9K 800, 802 and 812 engines
(fitted on Kangoo 2):
The EGR (Exhaust Gas Recirculation) system consists of a DC proportional EGR valve, which incorporates
a valve position feedback potentiometer. The EGR valve is closed-loop controlled based on its position via
the potentiometer and/or based on changes in the estimated air flow.
K9K 750 and 752 (Euro 3) engines (fitted on Clio III and Modus):
The EGR system (Exhaust Gas Recirculation) consists of an EGR solenoid valve, which incorporates a valve
position feedback potentiometer. The EGR valve is closed-loop controlled based on its position via
the potentiometer and/or based on changes in the estimated air flow.
Page 16 of 269
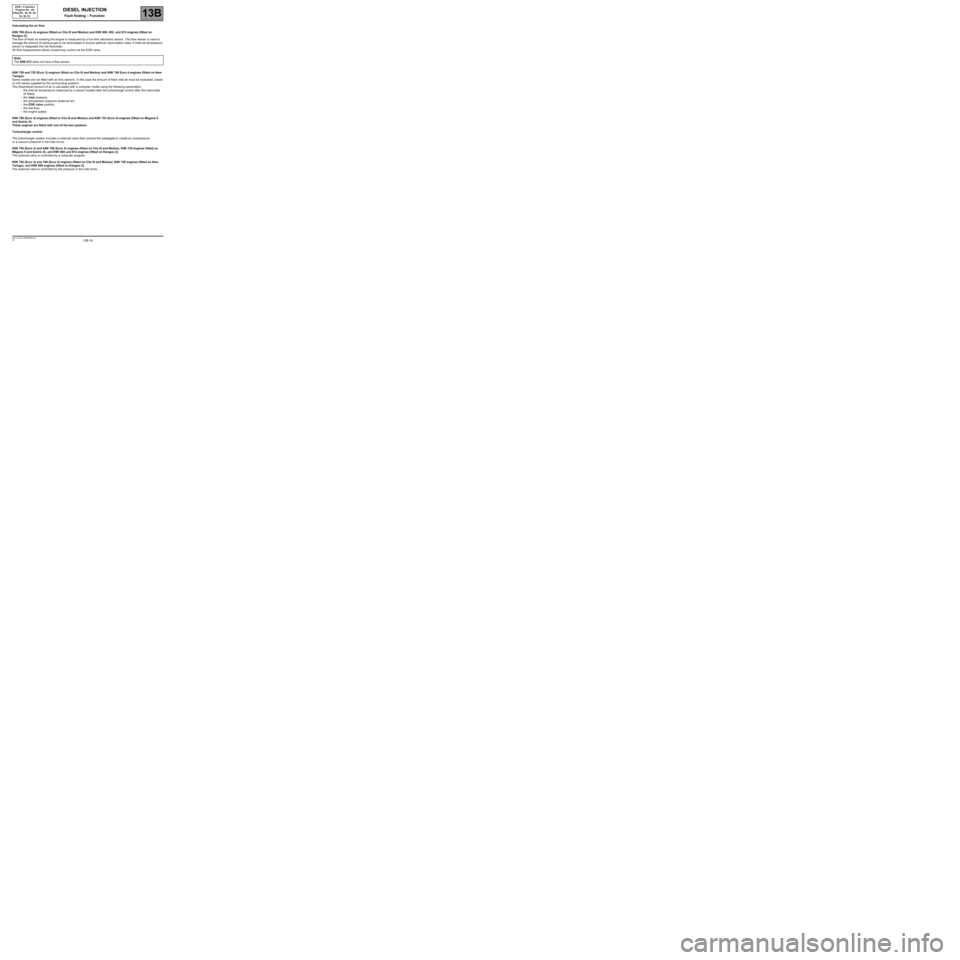
13B-16V6 MR-413-X44-13B000$040.mif
DIESEL INJECTION
Fault finding – Function13B
DCM 1.2 Injection
Program No.: 4D
Vdiag No.: 48, 4C, 50,
54, 58, 5C
Calculating the air flow
K9K 768 (Euro 4) engines (fitted on Clio III and Modus) and K9K 800, 802, and 812 engines (fitted on
Kangoo 2):
The flow of fresh air entering the engine is measured by a hot wire ratiometric sensor. This flow sensor is used to
manage the amount of exhaust gas to be recirculated to ensure optimum recirculation rates. A fresh air temperature
sensor is integrated into the flowmeter.
Air flow measurement allows closed-loop control via the EGR valve.
K9K 750 and 752 (Euro 3) engines (fitted on Clio III and Modus) and K9K 740 Euro 4 engines (fitted on New
Twingo):
Some models are not fitted with air flow sensors. In this case the amount of fresh inlet air must be evaluated, based
on the values supplied by the surrounding systems.
The (theoretical) amount of air is calculated with a computer model using the following parameters:
–the inlet air temperature measured by a sensor located after the turbocharger and/or after the intercooler
(if fitted),
–the inlet pressure,
–the atmospheric pressure (external air),
–the EGR valve position,
–the fuel flow,
–the engine speed.
K9K 766 (Euro 4) engines (fitted to Clio III and Modus) and K9K 724 (Euro 4) engines (fitted on Mégane II
and Scénic II):
These engines are fitted with one of the two systems.
Turbocharger control
The turbocharger system includes a solenoid valve that controls the wastegate to create an overpressure
or a vacuum pressure in the inlet circuit.
K9K 750 (Euro 3) and K9K 766 (Euro 4) engines (fitted on Clio III and Modus), K9K 724 engines (fitted on
Mégane II and Scénic II), and K9K 802 and 812 engines (fitted on Kangoo 2):
The solenoid valve is controlled by a computer program.
K9K 752 (Euro 3) and 768 (Euro 4) engines (fitted on Clio III and Modus), K9K 740 engines (fitted on New
Twingo), and K9K 800 engines (fitted on Kangoo 2):
The solenoid valve is controlled by the pressure in the inlet ducts.Note:
The K9K 812 does not have a flow sensor.