Page 193 of 381
4 - 61
ENG
CRANKCASE
EB412743
ASSEMBLING THE CRANKCASE
1. Lubricate:
• crankshaft journal bearings
(with the recommended lubricant)
Recommended lubricant
Engine oil
2. Apply:
• sealant
(onto the crankcase mating surfaces)
NOTE:
Do not allow any sealant to come into
contact with the oil gallery or crankshaft
journal bearings. Do not apply sealant to
within 2 ~ 3 mm (0.08 ~ 0.12 in) of the
crankshaft journal bearings.
3. Install:
• dowel pins
1
Yamaha bond No. 1215
90890-85505
4. Install:
• crankshaft journal lower bearings
(into the lower crankcase)
NOTE:
• Align the projections
a
on the crank-
shaft journal lower bearings with the
notches
b
in the lower crankcase.
• Install each crankshaft journal lower
bearing in its original place.
5. Set the shift drum assembly and trans-
mission gears in the neutral position.
Page 194 of 381
4 - 62
ENG
CRANKCASE
6. Install:
• lower crankcase
1
(onto the upper crankcase
2
)
ACHTUNG:CAUTION:
Before tightening the crankcase bolts,
make sure that the transmission gears
shift correctly when the shift drum
assembly is turned by hand.
7. Install:
• crankcase bolts
NOTE:
• Lubricate the bolt threads with engine
oil.
• Install a washer on bolts
1
~
@
.
• Tighten the bolts in the tightening
sequence cast on the crankcase.
M9
´
105 mm bolts:
1
~
@
M8
´
60 mm bolt:
K
,
L
M6
´
70 mm bolts:
G
,
I
,
O
,
Q
M6
´
64 mm bolts:
F
,
N
M6
´
60 mm bolt:
M
M6
´
55 mm bolts:
A
~
E
M6
´
50 mm bolt:
H
M6
´
45 mm bolts:
J
,
P
,
R
T R..
Bolt
1
~
@
32 Nm (3.2 m • kg, 23 ft • lb)
Bolt
A
~
E
,
G
~
J
,
M
,
O
~
R
12 Nm (1.2 m • kg, 8.7 ft • lb)
Bolt
F
,
N
14 Nm (1.4 m • kg, 10 ft • lb)
Bolt K, L
24 Nm (2.4 m • kg, 17 ft • lb)
Page 195 of 381
ENG
4 - 63
CONNECTING RODS AND PISTONS
EB404001
CONNECTING RODS AND PISTONS
Order Job/Part Q’ty Remarks
Removing the connecting rods and
pistonsRemove the parts in the order listed.
Crankcase Separate.
Refer to “CRANKCASE”.
1 Connecting rod cap 4
2 Big end lower bearing 4
3 Piston pin clip 8
4 Piston pin 4
5 Piston 4
6 Connecting rod 4
7 Big end upper bearing 4
8 Top ring 4
9 2nd ring 4
10 Oil ring 4
For installation, reverse the removal
procedure.
Page 196 of 381
4 - 64
ENGCONNECTING RODS AND PISTONS
EB412131
REMOVING THE CONNECTING RODS AND
PISTONS
The following procedure applies to all of
the connecting rods and pistons.
1. Remove:
• connecting rod cap
• big end bearings
NOTE:
Identify the position of each big end
bearing so that it can be reinstalled in its
original place.
2. Remove:
• piston pin clips 1
• piston pin 2
• piston 3
• connecting rod 4
ACHTUNG:CAUTION:
Do not use a hammer to drive the piston
pin out.
NOTE:
• For reference during installation, put
identification marks on the piston
crown.
• Before removing the piston pin, deburr
the piston pin clip groove and the pis-
ton pin bore area in the piston. If both
areas are deburred and the piston pin
is still difficult to remove, remove it
with the piston pin puller 4.
Piston pin puller
90890-01304
3. Remove:
• top ring
• 2nd ring
• oil ring
NOTE:
To remove a piston ring, open the end
gap with your fingers and lift the other
side of the ring over the piston crown.
Page 197 of 381
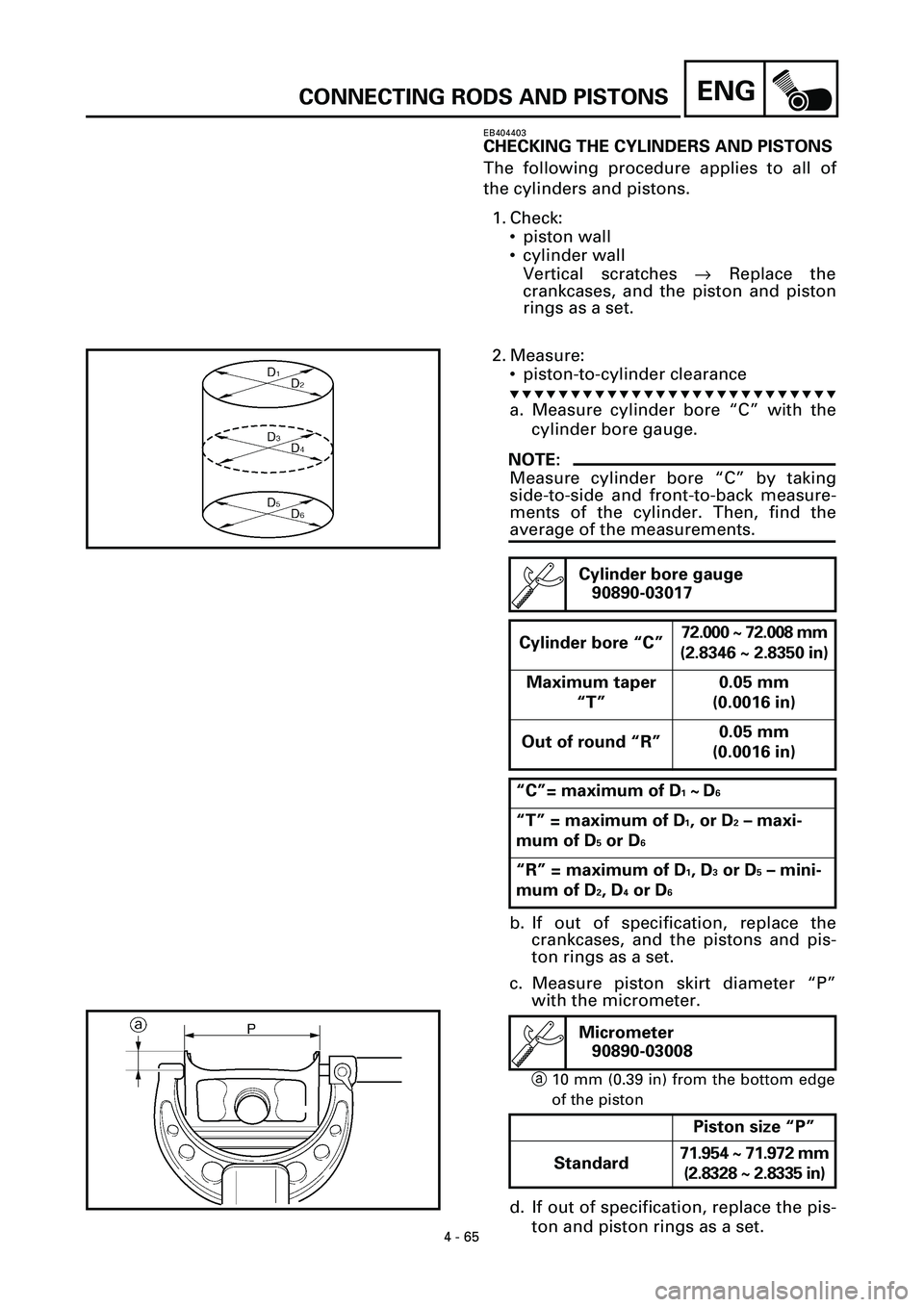
4 - 65
ENGCONNECTING RODS AND PISTONS
EB404403
CHECKING THE CYLINDERS AND PISTONS
The following procedure applies to all of
the cylinders and pistons.
1. Check:
• piston wall
• cylinder wall
Vertical scratches ® Replace the
crankcases, and the piston and piston
rings as a set.
2. Measure:
• piston-to-cylinder clearance
t t t t t t t t t t t t t t t t t t t t t t t t t t t
a. Measure cylinder bore “C” with the
cylinder bore gauge.
NOTE:
Measure cylinder bore “C” by taking
side-to-side and front-to-back measure-
ments of the cylinder. Then, find the
average of the measurements.
b. If out of specification, replace the
crankcases, and the pistons and pis-
ton rings as a set.
c. Measure piston skirt diameter “P”
with the micrometer.
a10 mm (0.39 in) from the bottom edge
of the piston
d. If out of specification, replace the pis-
ton and piston rings as a set.
Cylinder bore gauge
90890-03017
Cylinder bore “C”72.000 ~ 72.008 mm
(2.8346 ~ 2.8350 in)
Maximum taper
“T”0.05 mm
(0.0016 in)
Out of round “R”0.05 mm
(0.0016 in)
“C”= maximum of D
1 ~ D6
“T” = maximum of D1, or D2 – maxi-
mum of D
5 or D6
“R” = maximum of D1, D3 or D5 – mini-
mum of D
2, D4 or D6
Micrometer
90890-03008
Piston size “P”
Standard71.954 ~ 71.972 mm
(2.8328 ~ 2.8335 in)
Page 198 of 381
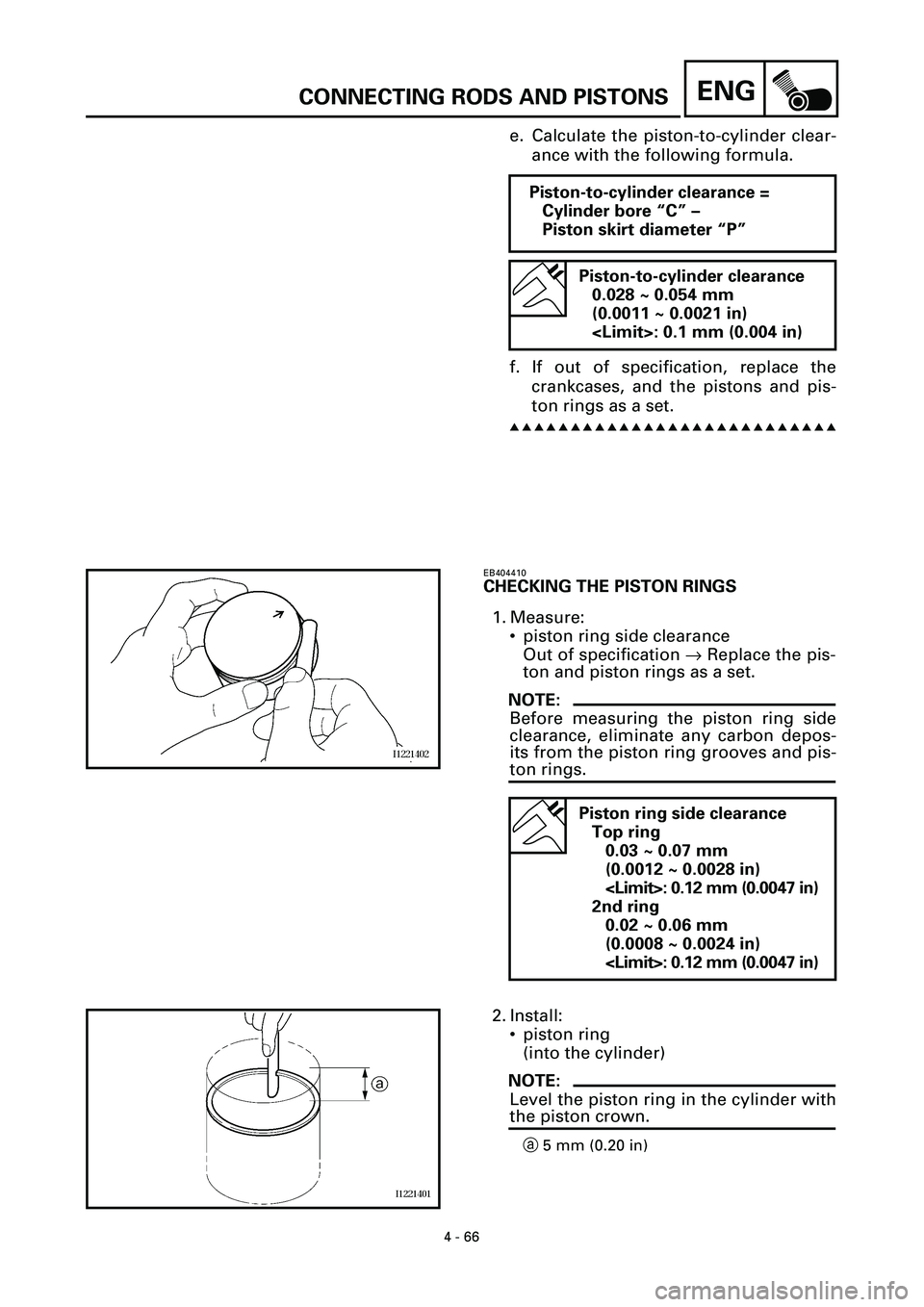
4 - 66
ENGCONNECTING RODS AND PISTONS
e. Calculate the piston-to-cylinder clear-
ance with the following formula.
f. If out of specification, replace the
crankcases, and the pistons and pis-
ton rings as a set.
s s s s s s s s s s s s s s s s s s s s s s s s s s s
Piston-to-cylinder clearance =
Cylinder bore “C” –
Piston skirt diameter “P”
Piston-to-cylinder clearance
0.028 ~ 0.054 mm
(0.0011 ~ 0.0021 in)
: 0.1 mm (0.004 in)
EB404410
CHECKING THE PISTON RINGS
1. Measure:
• piston ring side clearance
Out of specification ® Replace the pis-
ton and piston rings as a set.
NOTE:
Before measuring the piston ring side
clearance, eliminate any carbon depos-
its from the piston ring grooves and pis-
ton rings.
Piston ring side clearance
Top ring
0.03 ~ 0.07 mm
(0.0012 ~ 0.0028 in)
: 0.12 mm (0.0047 in)
2nd ring
0.02 ~ 0.06 mm
(0.0008 ~ 0.0024 in)
: 0.12 mm (0.0047 in)
2. Install:
• piston ring
(into the cylinder)
NOTE:
Level the piston ring in the cylinder with
the piston crown.
a5 mm (0.20 in)
Page 199 of 381
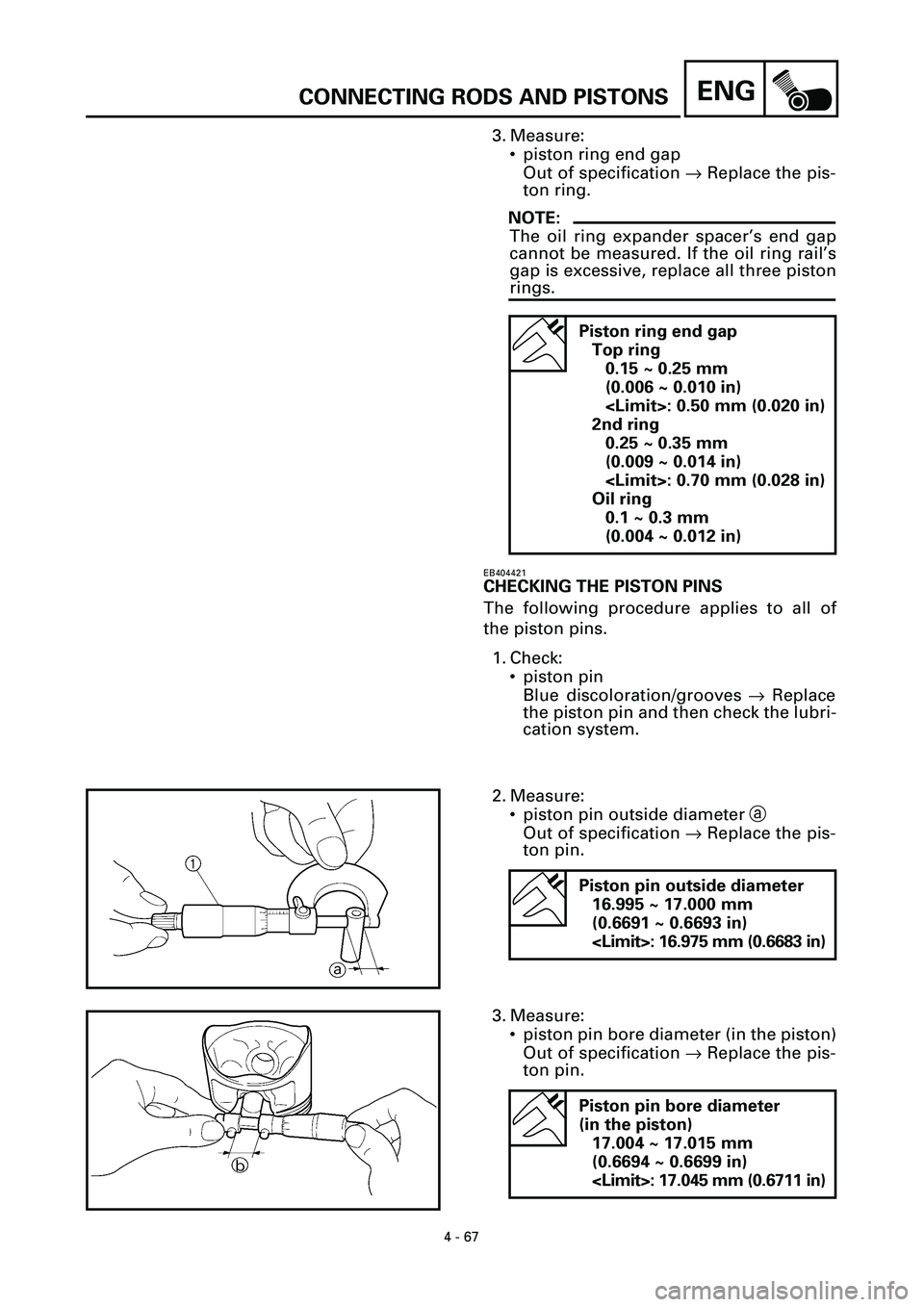
4 - 67
ENGCONNECTING RODS AND PISTONS
3. Measure:
• piston ring end gap
Out of specification ® Replace the pis-
ton ring.
NOTE:
The oil ring expander spacer’s end gap
cannot be measured. If the oil ring rail’s
gap is excessive, replace all three piston
rings.
Piston ring end gap
Top ring
0.15 ~ 0.25 mm
(0.006 ~ 0.010 in)
: 0.50 mm (0.020 in)
2nd ring
0.25 ~ 0.35 mm
(0.009 ~ 0.014 in)
: 0.70 mm (0.028 in)
Oil ring
0.1 ~ 0.3 mm
(0.004 ~ 0.012 in)
EB404421
CHECKING THE PISTON PINS
The following procedure applies to all of
the piston pins.
1. Check:
• piston pin
Blue discoloration/grooves ® Replace
the piston pin and then check the lubri-
cation system.
2. Measure:
• piston pin outside diameter a
Out of specification ® Replace the pis-
ton pin.
Piston pin outside diameter
16.995 ~ 17.000 mm
(0.6691 ~ 0.6693 in)
: 16.975 mm (0.6683 in)
3. Measure:
• piston pin bore diameter (in the piston)
Out of specification ® Replace the pis-
ton pin.
Piston pin bore diameter
(in the piston)
17.004 ~ 17.015 mm
(0.6694 ~ 0.6699 in)
: 17.045 mm (0.6711 in)
Page 200 of 381
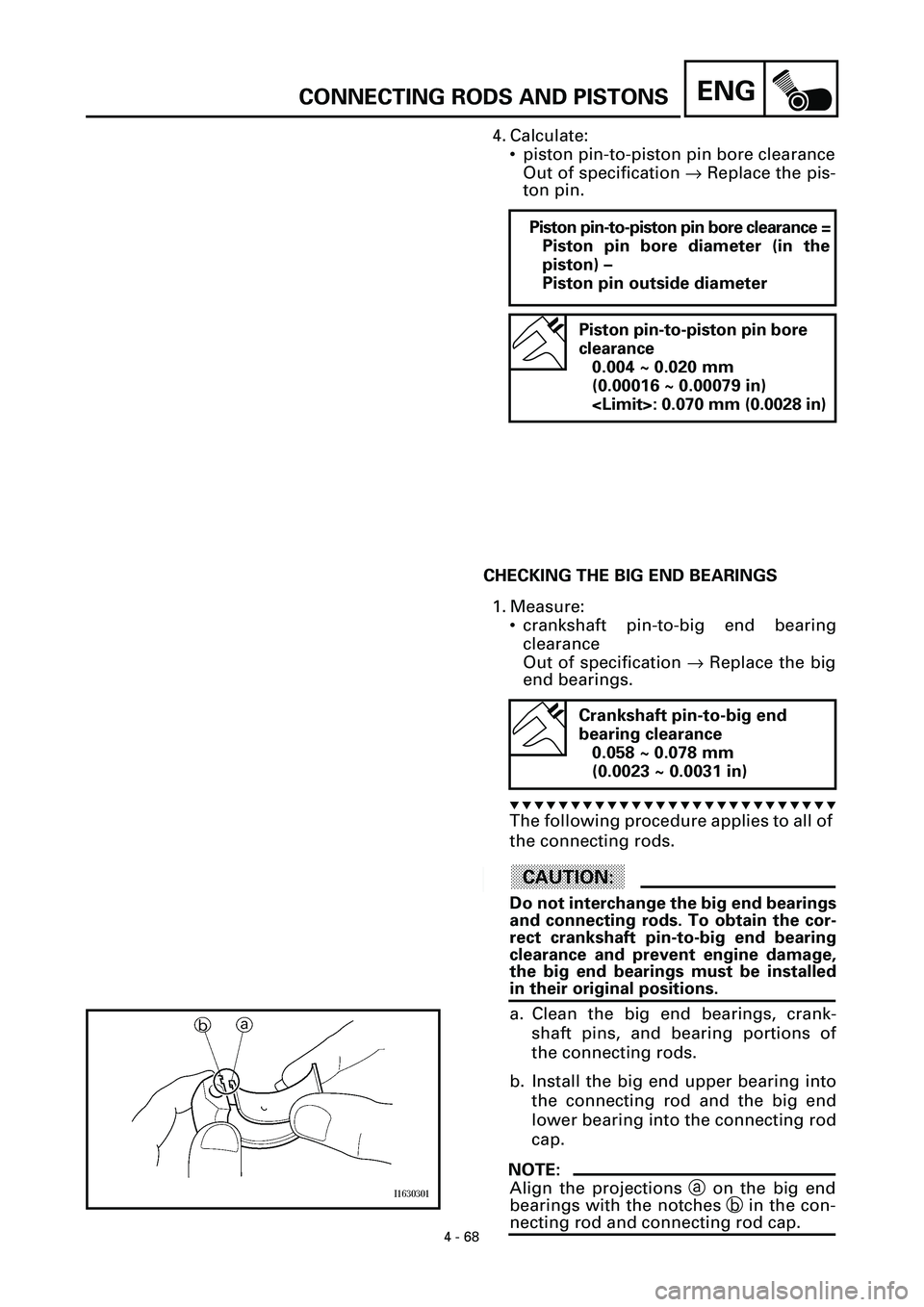
4 - 68
ENGCONNECTING RODS AND PISTONS
4. Calculate:
• piston pin-to-piston pin bore clearance
Out of specification ® Replace the pis-
ton pin.
Piston pin-to-piston pin bore clearance =
Piston pin bore diameter (in the
piston) –
Piston pin outside diameter
Piston pin-to-piston pin bore
clearance
0.004 ~ 0.020 mm
(0.00016 ~ 0.00079 in)
: 0.070 mm (0.0028 in)
CHECKING THE BIG END BEARINGS
1. Measure:
• crankshaft pin-to-big end bearing
clearance
Out of specification ® Replace the big
end bearings.
t t t t t t t t t t t t t t t t t t t t t t t t t t t
The following procedure applies to all of
the connecting rods.
ACHTUNG:CAUTION:
Do not interchange the big end bearings
and connecting rods. To obtain the cor-
rect crankshaft pin-to-big end bearing
clearance and prevent engine damage,
the big end bearings must be installed
in their original positions.
a. Clean the big end bearings, crank-
shaft pins, and bearing portions of
the connecting rods.
b. Install the big end upper bearing into
the connecting rod and the big end
lower bearing into the connecting rod
cap.
NOTE:
Align the projections a on the big end
bearings with the notches b in the con-
necting rod and connecting rod cap.
Crankshaft pin-to-big end
bearing clearance
0.058 ~ 0.078 mm
(0.0023 ~ 0.0031 in)