Page 257 of 432
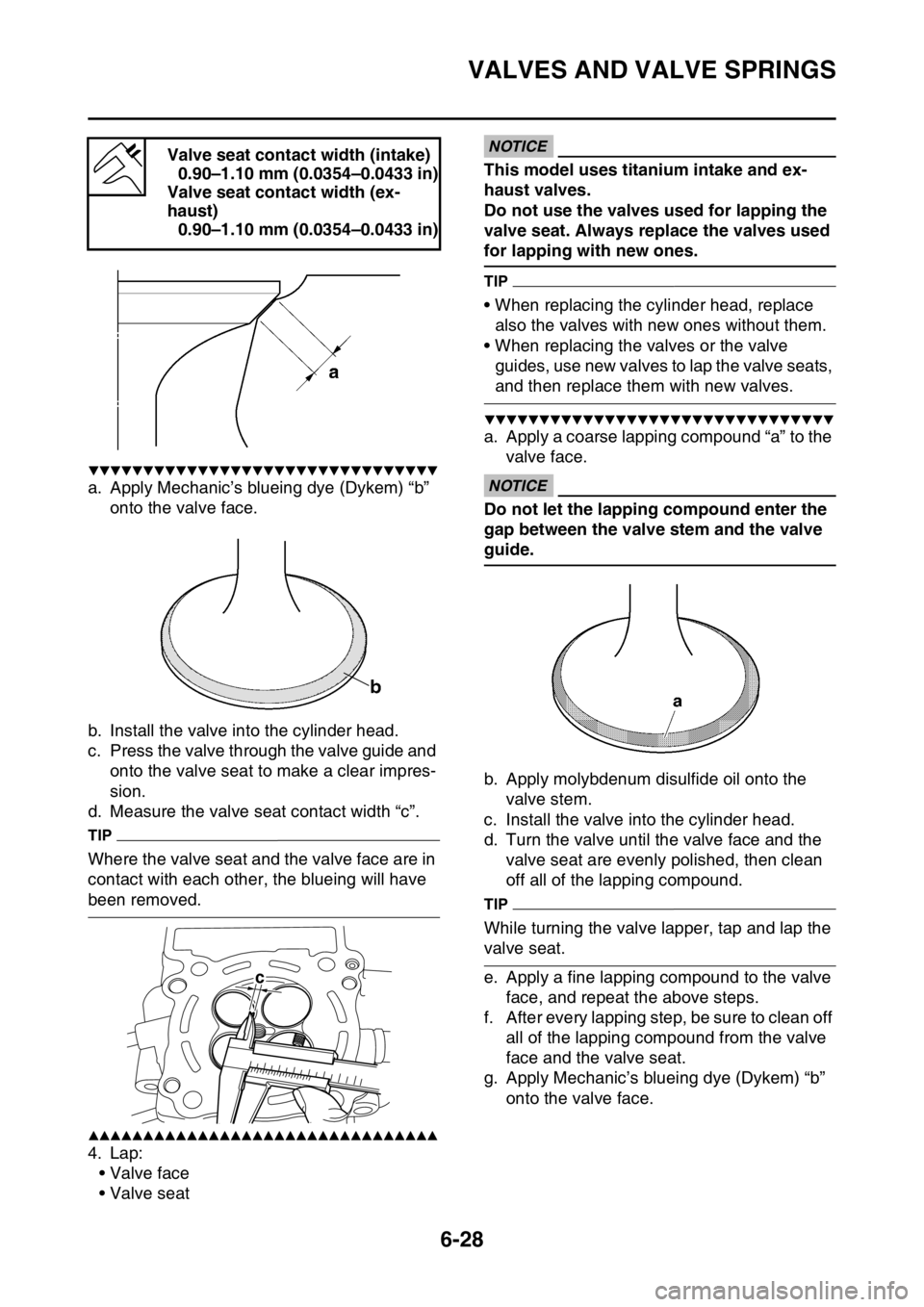
VALVES AND VALVE SPRINGS
6-28
▼▼▼▼▼▼▼▼▼▼▼▼▼▼▼▼▼▼▼▼▼▼▼▼▼▼▼▼▼▼▼▼
a. Apply Mechanic’s blueing dye (Dykem) “b”
onto the valve face.
b. Install the valve into the cylinder head.
c. Press the valve through the valve guide and
onto the valve seat to make a clear impres-
sion.
d. Measure the valve seat contact width “c”.
TIP
Where the valve seat and the valve face are in
contact with each other, the blueing will have
been removed.
▲▲▲▲▲▲▲▲▲▲▲▲▲▲▲▲▲▲▲▲▲▲▲▲▲▲▲▲▲▲▲▲
4. Lap:
• Valve face
• Valve seat
ECA
NOTICE
This model uses titanium intake and ex-
haust valves.
Do not use the valves used for lapping the
valve seat. Always replace the valves used
for lapping with new ones.
TIP
• When replacing the cylinder head, replace
also the valves with new ones without them.
• When replacing the valves or the valve
guides, use new valves to lap the valve seats,
and then replace them with new valves.
▼▼▼▼▼▼▼▼▼▼▼▼▼▼▼▼▼▼▼▼▼▼▼▼▼▼▼▼▼▼▼▼
a. Apply a coarse lapping compound “a” to the
valve face.
ECA
NOTICE
Do not let the lapping compound enter the
gap between the valve stem and the valve
guide.
b. Apply molybdenum disulfide oil onto the
valve stem.
c. Install the valve into the cylinder head.
d. Turn the valve until the valve face and the
valve seat are evenly polished, then clean
off all of the lapping compound.
TIP
While turning the valve lapper, tap and lap the
valve seat.
e. Apply a fine lapping compound to the valve
face, and repeat the above steps.
f. After every lapping step, be sure to clean off
all of the lapping compound from the valve
face and the valve seat.
g. Apply Mechanic’s blueing dye (Dykem) “b”
onto the valve face. Valve seat contact width (intake)
0.90–1.10 mm (0.0354–0.0433 in)
Valve seat contact width (ex-
haust)
0.90–1.10 mm (0.0354–0.0433 in)
c
Page 258 of 432
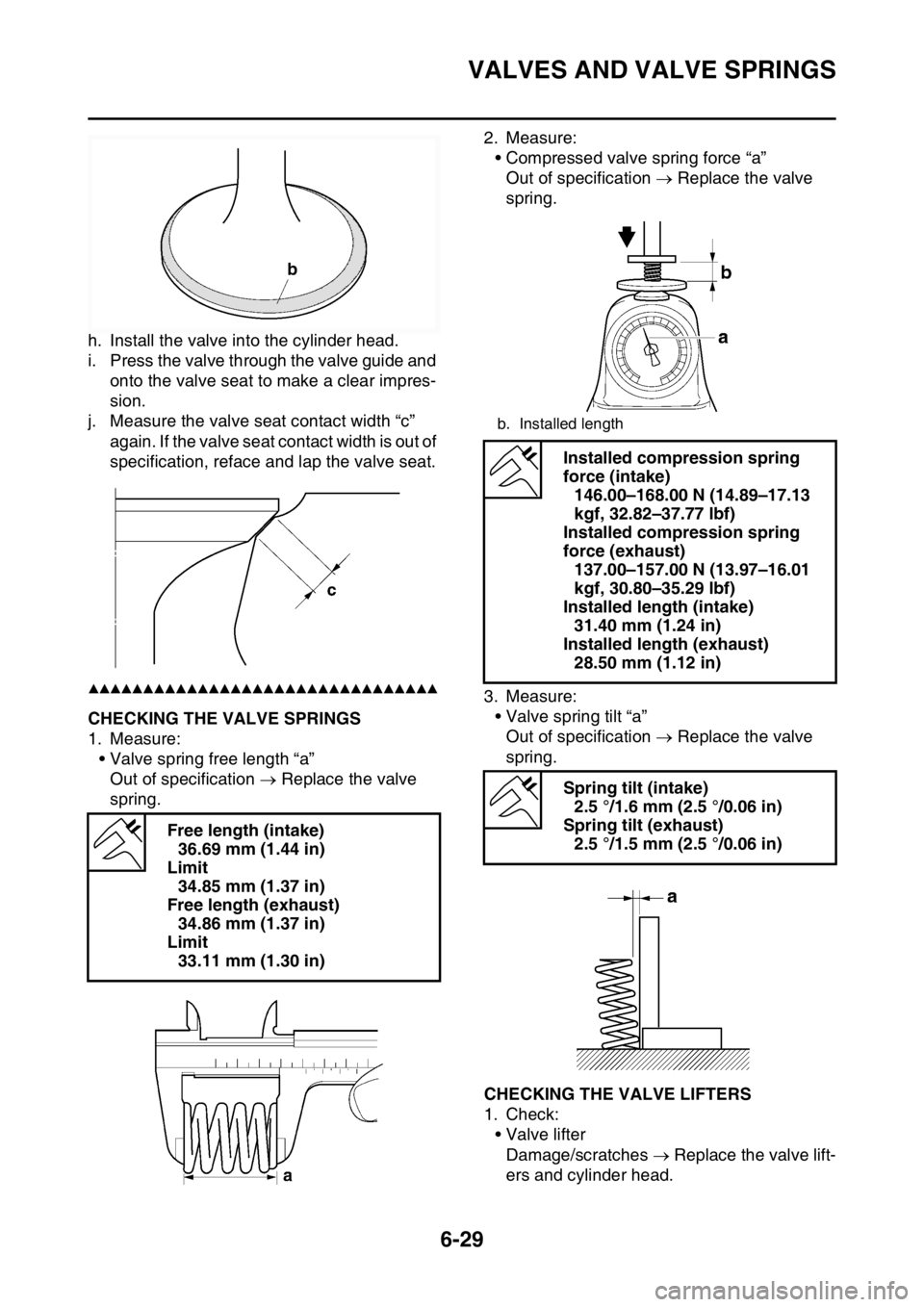
VALVES AND VALVE SPRINGS
6-29
h. Install the valve into the cylinder head.
i. Press the valve through the valve guide and
onto the valve seat to make a clear impres-
sion.
j. Measure the valve seat contact width “c”
again. If the valve seat contact width is out of
specification, reface and lap the valve seat.
▲▲▲▲▲▲▲▲▲▲▲▲▲▲▲▲▲▲▲▲▲▲▲▲▲▲▲▲▲▲▲▲
EAS2GBB253CHECKING THE VALVE SPRINGS
1. Measure:
• Valve spring free length “a”
Out of specification Replace the valve
spring.2. Measure:
• Compressed valve spring force “a”
Out of specification Replace the valve
spring.
3. Measure:
• Valve spring tilt “a”
Out of specification Replace the valve
spring.
EAS2GBB254CHECKING THE VALVE LIFTERS
1. Check:
• Valve lifter
Damage/scratches Replace the valve lift-
ers and cylinder head. Free length (intake)
36.69 mm (1.44 in)
Limit
34.85 mm (1.37 in)
Free length (exhaust)
34.86 mm (1.37 in)
Limit
33.11 mm (1.30 in)
b. Installed length
Installed compression spring
force (intake)
146.00–168.00 N (14.89–17.13
kgf, 32.82–37.77 lbf)
Installed compression spring
force (exhaust)
137.00–157.00 N (13.97–16.01
kgf, 30.80–35.29 lbf)
Installed length (intake)
31.40 mm (1.24 in)
Installed length (exhaust)
28.50 mm (1.12 in)
Spring tilt (intake)
2.5 °/1.6 mm (2.5 °/0.06 in)
Spring tilt (exhaust)
2.5 °/1.5 mm (2.5 °/0.06 in)
Page 259 of 432
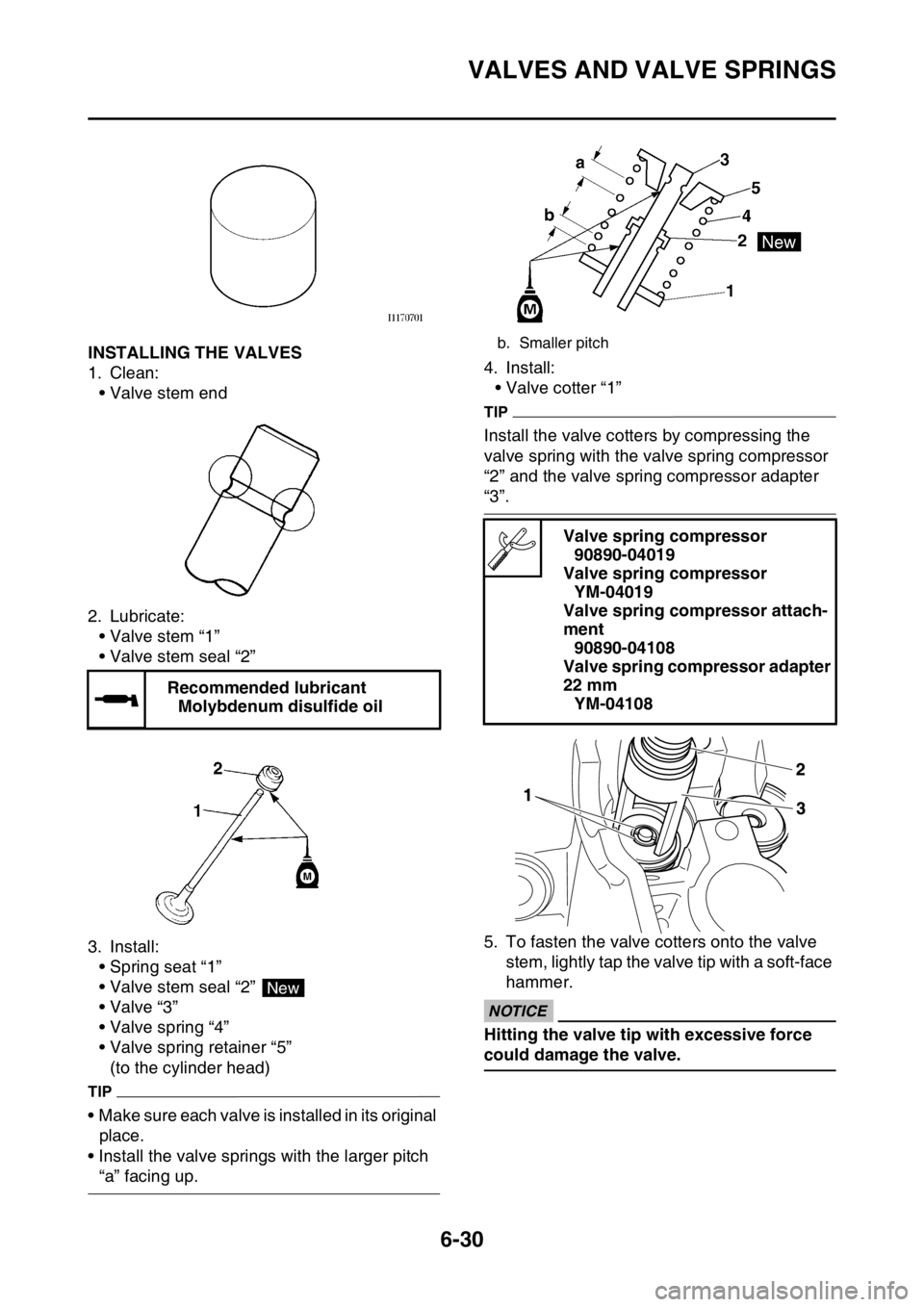
VALVES AND VALVE SPRINGS
6-30
EAS2GBB255INSTALLING THE VALVES
1. Clean:
• Valve stem end
2. Lubricate:
• Valve stem “1”
• Valve stem seal “2”
3. Install:
• Spring seat “1”
• Valve stem seal “2”
•Valve “3”
• Valve spring “4”
• Valve spring retainer “5”
(to the cylinder head)
TIP
• Make sure each valve is installed in its original
place.
• Install the valve springs with the larger pitch
“a” facing up.4. Install:
• Valve cotter “1”
TIP
Install the valve cotters by compressing the
valve spring with the valve spring compressor
“2” and the valve spring compressor adapter
“3”.
5. To fasten the valve cotters onto the valve
stem, lightly tap the valve tip with a soft-face
hammer.
ECA
NOTICE
Hitting the valve tip with excessive force
could damage the valve. Recommended lubricant
Molybdenum disulfide oil
New
b. Smaller pitch
Valve spring compressor
90890-04019
Valve spring compressor
YM-04019
Valve spring compressor attach-
ment
90890-04108
Valve spring compressor adapter
22 mm
YM-04108
Page 260 of 432
VALVES AND VALVE SPRINGS
6-31
6. Lubricate:
• Adjusting pad “1”
• Valve lifter “2”
7. Install:
• Adjusting pad
• Valve lifter
TIP
• Check that the valve lifter turns smoothly
when rotated with your finger.
• Make sure that the valve lifter and the adjust-
ing pad are reinstalled in their original posi-
tions.
E
1 2
Page 261 of 432
CYLINDER AND PISTON
6-32
EAS2GBB256
CYLINDER AND PISTON
Removing the cylinder and piston
Order Part name Q’ty Remarks
Cylinder headRefer to “CYLINDER HEAD” on page 6-20.
1Cylinder body
1
2Gaskets
1
3Dowel pin
2
4Piston pin clip
2
5Piston pin
1
6Piston
1
7Piston ring set
1
For installation, reverse the removal proce-
dure.
1
2
3
4
4
5
6
7
10 Nm (1.0 mkgf, 7.2 ftIbf)T.R.
10 Nm (1.0 mkgf, 7.2 ftIbf)T.R.
E
E
New
New
New
LT
E
Page 262 of 432
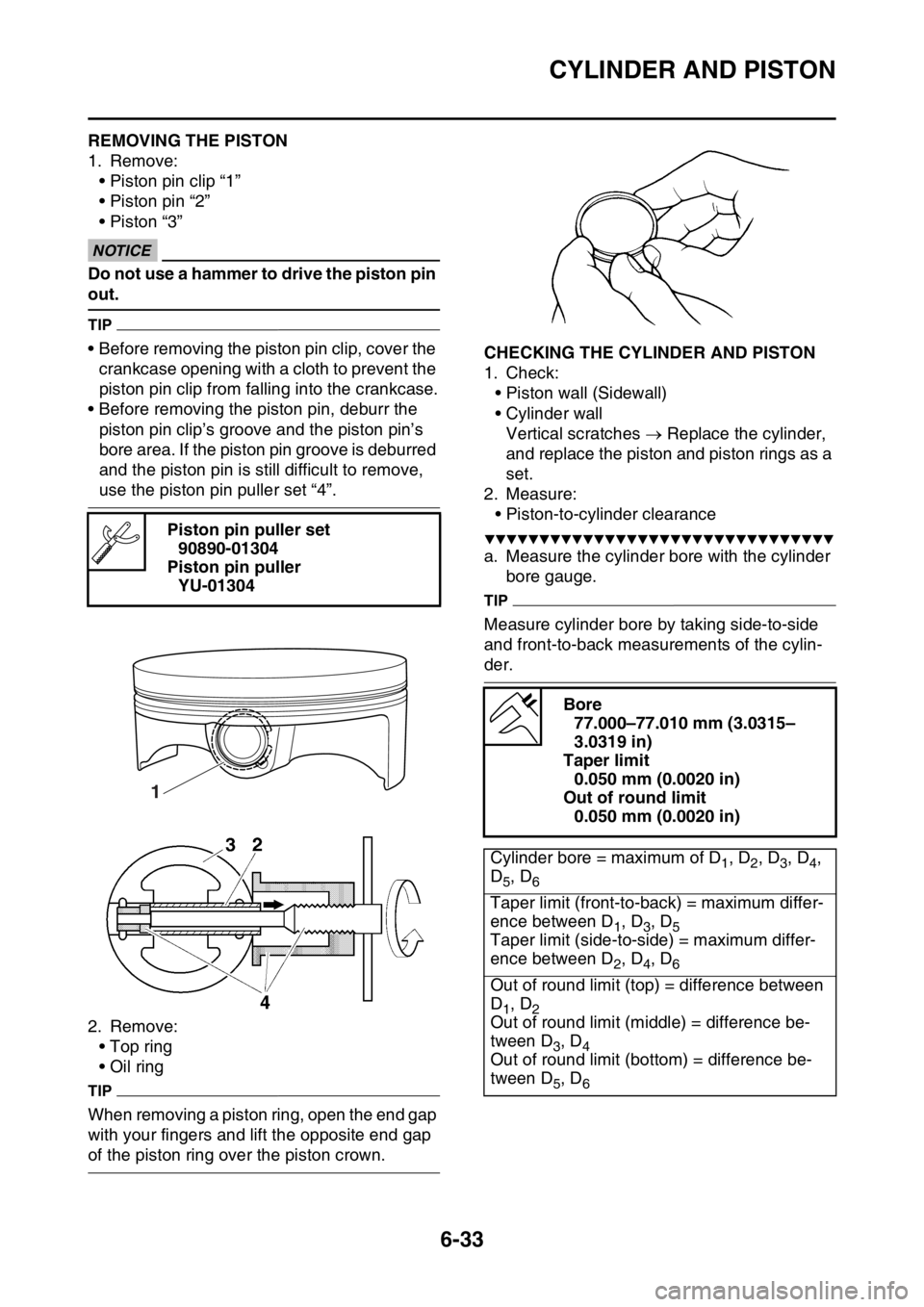
CYLINDER AND PISTON
6-33
EAS2GBB257REMOVING THE PISTON
1. Remove:
• Piston pin clip “1”
• Piston pin “2”
• Piston “3”
ECA
NOTICE
Do not use a hammer to drive the piston pin
out.
TIP
• Before removing the piston pin clip, cover the
crankcase opening with a cloth to prevent the
piston pin clip from falling into the crankcase.
• Before removing the piston pin, deburr the
piston pin clip’s groove and the piston pin’s
bore area. If the piston pin groove is deburred
and the piston pin is still difficult to remove,
use the piston pin puller set “4”.
2. Remove:
• Top ring
• Oil ring
TIP
When removing a piston ring, open the end gap
with your fingers and lift the opposite end gap
of the piston ring over the piston crown.
EAS2GBB258CHECKING THE CYLINDER AND PISTON
1. Check:
• Piston wall (Sidewall)
• Cylinder wall
Vertical scratches Replace the cylinder,
and replace the piston and piston rings as a
set.
2. Measure:
• Piston-to-cylinder clearance
▼▼▼▼▼▼▼▼▼▼▼▼▼▼▼▼▼▼▼▼▼▼▼▼▼▼▼▼▼▼▼▼
a. Measure the cylinder bore with the cylinder
bore gauge.
TIP
Measure cylinder bore by taking side-to-side
and front-to-back measurements of the cylin-
der. Piston pin puller set
90890-01304
Piston pin puller
YU-01304
1
Bore
77.000–77.010 mm (3.0315–
3.0319 in)
Taper limit
0.050 mm (0.0020 in)
Out of round limit
0.050 mm (0.0020 in)
Cylinder bore = maximum of D
1, D2, D3, D4,
D
5, D6
Taper limit (front-to-back) = maximum differ-
ence between D
1, D3, D5Taper limit (side-to-side) = maximum differ-
ence between D
2, D4, D6
Out of round limit (top) = difference between
D
1, D2Out of round limit (middle) = difference be-
tween D
3, D4Out of round limit (bottom) = difference be-
tween D
5, D6
Page 263 of 432

CYLINDER AND PISTON
6-34
b. If out of specification, rebore or replace the
cylinder, and replace the piston and the pis-
ton rings as a set.
c. Measure the piston outside diameter “a” at
the measuring point (from piston skirt bot-
tom) “b” with the micrometer.
d. If out of specification, replace the cylinder,
the piston, and the piston rings as a set.
e. Calculate the piston-to-cylinder clearance
with the following formula.
f. If out of specification, replace the cylinder,
the piston, and the piston rings as a set.
▲▲▲▲▲▲▲▲▲▲▲▲▲▲▲▲▲▲▲▲▲▲▲▲▲▲▲▲▲▲▲▲
EAS2GBB259CHECKING THE PISTON RINGS
1. Measure:
• Piston ring side clearance
Out of specification Replace the piston
and piston rings as a set.
TIP
Before measuring the piston ring side clear-
ance, eliminate any carbon deposits from the
piston ring grooves and piston rings.
2. Install:
• Piston rings
TIP
Level the piston ring into the cylinder with the
piston.
3. Measure:
• Piston ring end gap
Out of specification Replace the piston
ring.
TIP
The oil ring expander’s end gap cannot be
measured. If the oil ring rail’s gap is excessive,
replace all three oil rings. Diameter
76.955–76.970 mm (3.0297–
3.0303 in)
Measuring point (from piston
skirt bottom)
6.0 mm (0.24 in)
Piston-to-cylinder clearance =
Cylinder bore - Piston diameter
Piston-to-cylinder clearance
0.030–0.055 mm (0.0012–0.0022
in)
Limit
0.15 mm (0.006 in)
b
a
Ring side clearance
0.030–0.065 mm (0.0012–0.0026
in)
Limit
0.115 mm (0.0045 in)
a. 10 mm (0.39 in)
Page 264 of 432
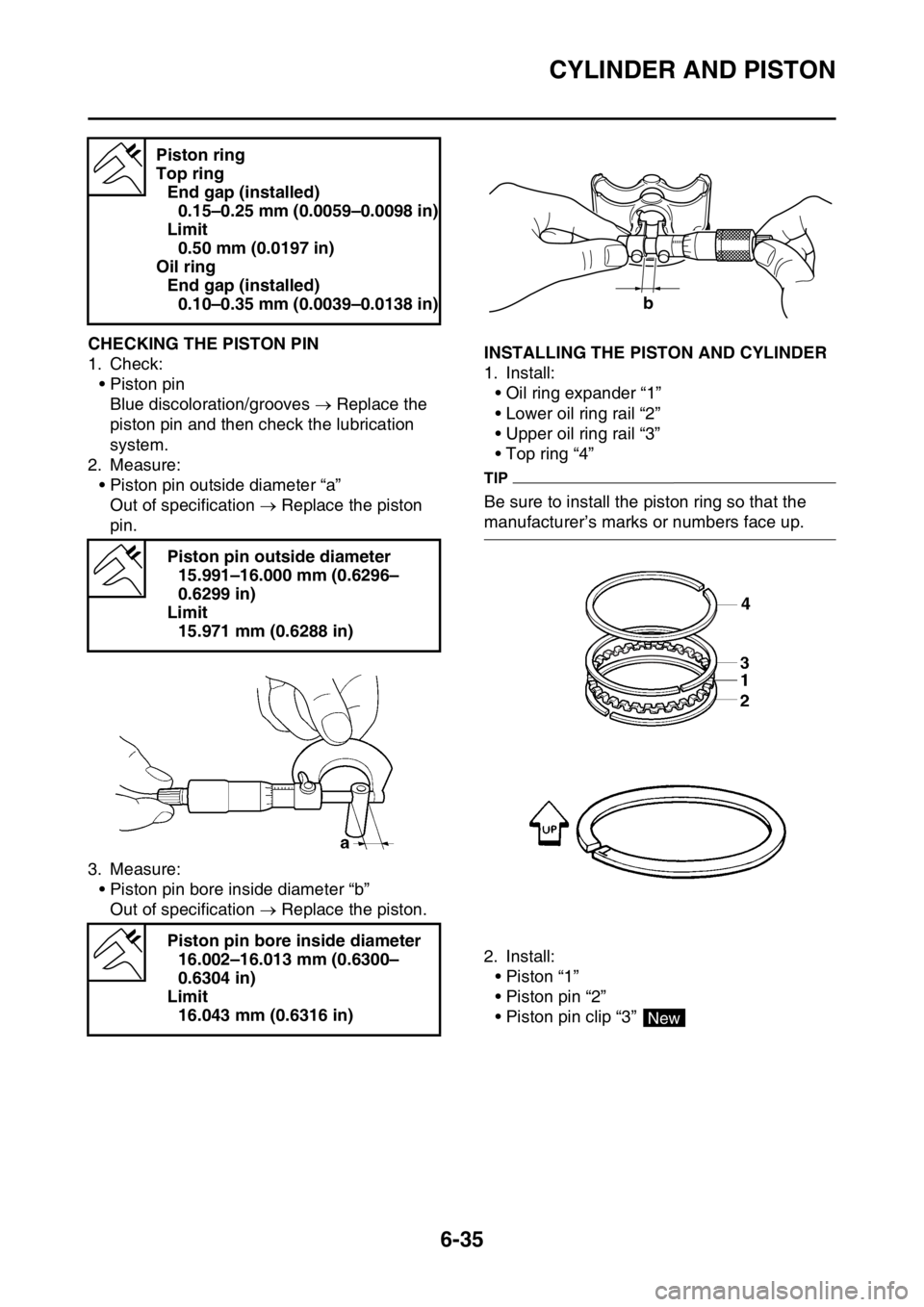
CYLINDER AND PISTON
6-35
EAS2GBB260CHECKING THE PISTON PIN
1. Check:
• Piston pin
Blue discoloration/grooves Replace the
piston pin and then check the lubrication
system.
2. Measure:
• Piston pin outside diameter “a”
Out of specification Replace the piston
pin.
3. Measure:
• Piston pin bore inside diameter “b”
Out of specification Replace the piston.EAS2GBB261INSTALLING THE PISTON AND CYLINDER
1. Install:
• Oil ring expander “1”
• Lower oil ring rail “2”
• Upper oil ring rail “3”
• Top ring “4”
TIP
Be sure to install the piston ring so that the
manufacturer’s marks or numbers face up.
2. Install:
• Piston “1”
• Piston pin “2”
• Piston pin clip “3” Piston ring
Top ring
End gap (installed)
0.15–0.25 mm (0.0059–0.0098 in)
Limit
0.50 mm (0.0197 in)
Oil ring
End gap (installed)
0.10–0.35 mm (0.0039–0.0138 in)
Piston pin outside diameter
15.991–16.000 mm (0.6296–
0.6299 in)
Limit
15.971 mm (0.6288 in)
Piston pin bore inside diameter
16.002–16.013 mm (0.6300–
0.6304 in)
Limit
16.043 mm (0.6316 in)
b
4
New