Page 67 of 751
02-36
Torque change curve of engine and drive shaft
Compression stroke Combustion stroke
Small changes from engine (k):
Damper increases the torque changes to clutchLarge changes from engine (j):
Damper decreases the torque changes to
transaxle by absorbing the impact
3) Operation
Compensating the irregular operation of engine: The secondary flywheel operates almost evenly so
does not cause gear noises
The mass of the primary flywheel is less than conventional flywheel so the engine irregularity
increases more (less pulsation absorbing effect).
Transaxle protection function: Reduces the torsional vibration to powertrain (transaxle) by reducing
the irregularity of engine. -
-
-
Page 68 of 751
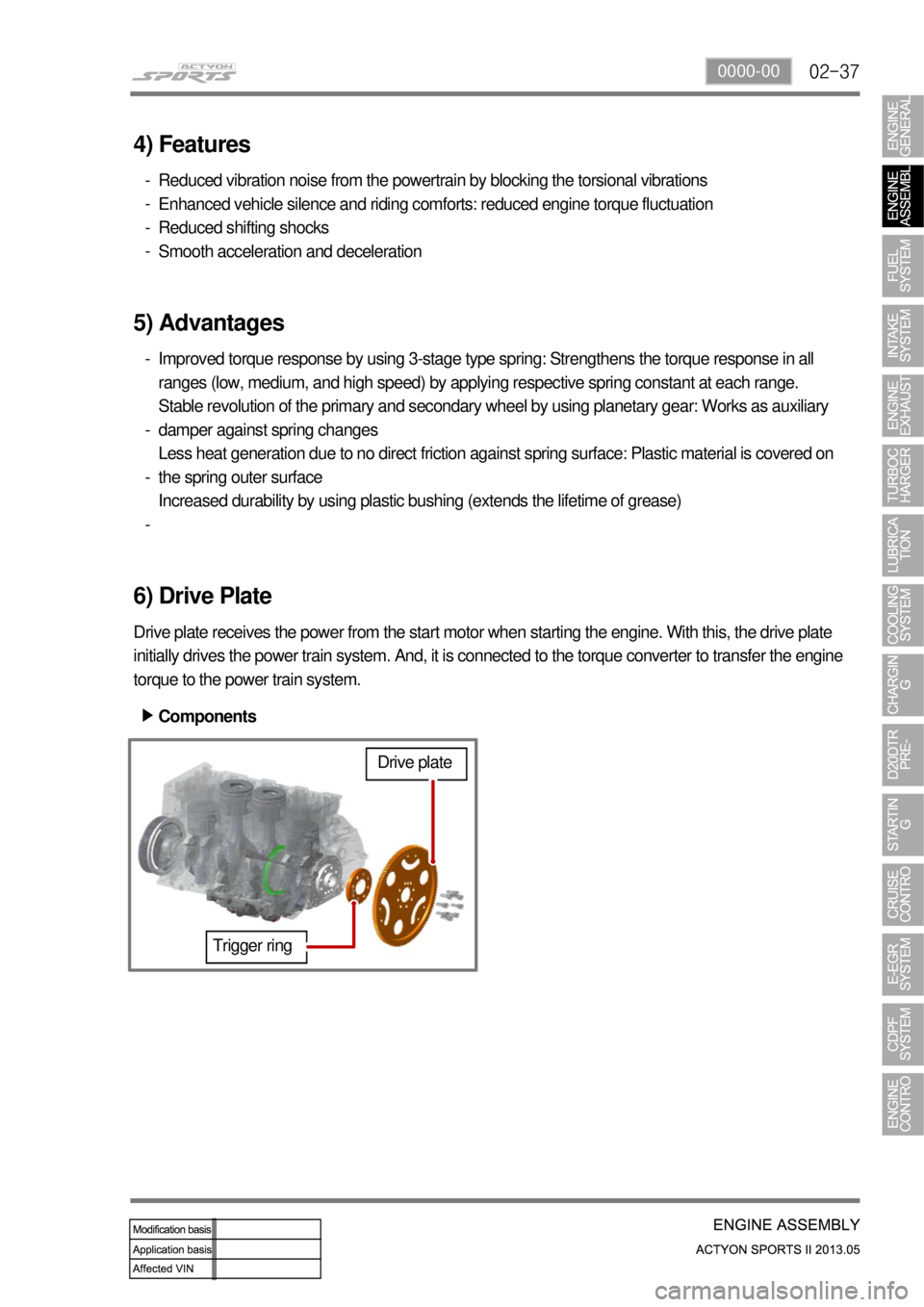
02-370000-00
4) Features
Reduced vibration noise from the powertrain by blocking the torsional vibrations
Enhanced vehicle silence and riding comforts: reduced engine torque fluctuation
Reduced shifting shocks
Smooth acceleration and deceleration -
-
-
-
5) Advantages
Improved torque response by using 3-stage type spring: Strengthens the torque response in all
ranges (low, medium, and high speed) by applying respective spring constant at each range.
Stable revolution of the primary and secondary wheel by using planetary gear: Works as auxiliary
damper against spring changes
Less heat generation due to no direct friction against spring surface: Plastic material is covered on
the spring outer surface
Increased durability by using plastic bushing (extends the lifetime of grease) -
-
-
-
6) Drive Plate
Drive plate receives the power from the start motor when starting the engine. With this, the drive plate
initially drives the power train system. And, it is connected to the torque converter to transfer the engine
torque to the power train system.
Trigger ring
Drive plate
Components ▶
Page 125 of 751
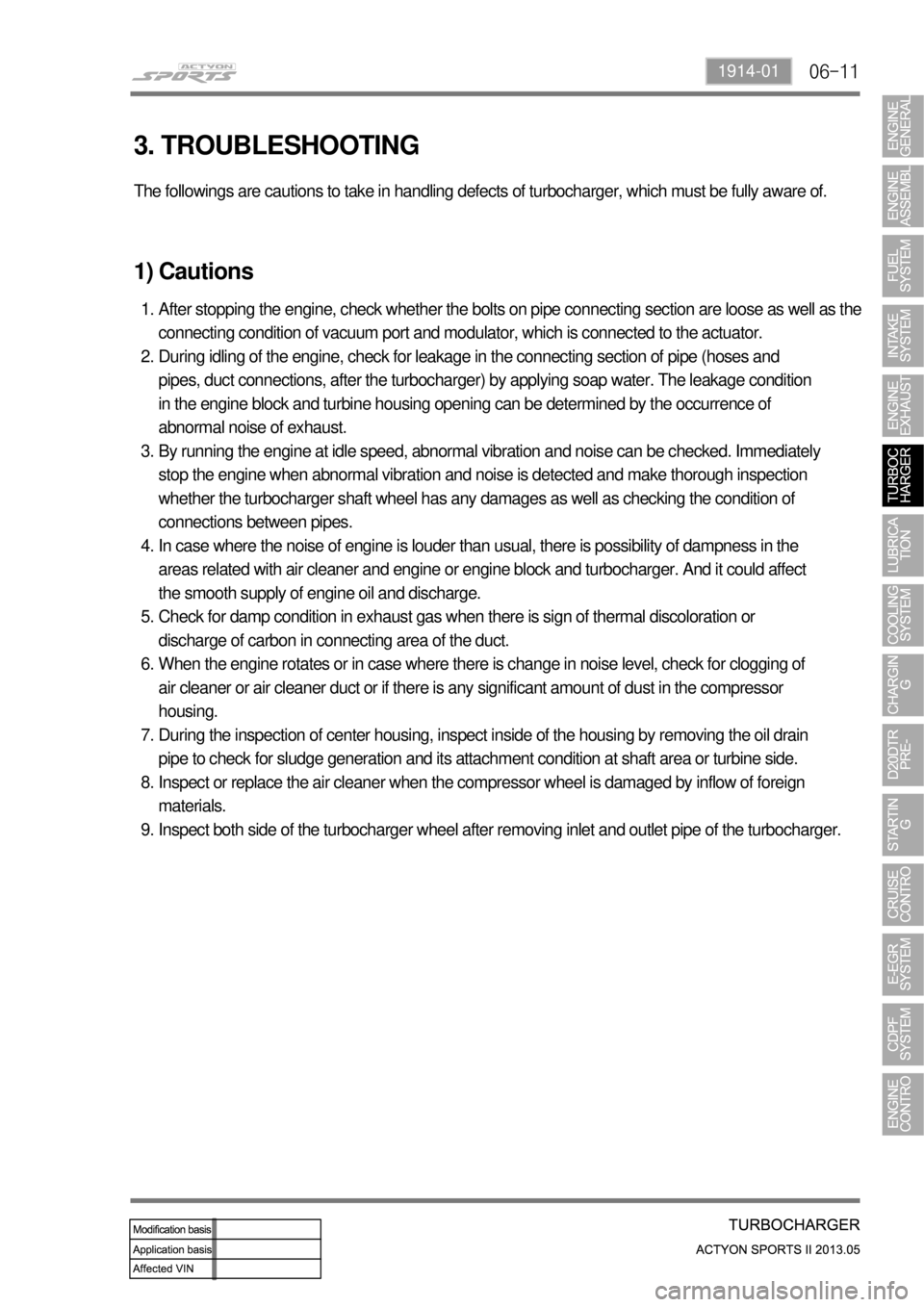
06-111914-01
3. TROUBLESHOOTING
The followings are cautions to take in handling defects of turbocharger, which must be fully aware of.
1) Cautions
After stopping the engine, check whether the bolts on pipe connecting section are loose as well as the
connecting condition of vacuum port and modulator, which is connected to the actuator.
During idling of the engine, check for leakage in the connecting section of pipe (hoses and
pipes, duct connections, after the turbocharger) by applying soap water. The leakage condition
in the engine block and turbine housing opening can be determined by the occurrence of
abnormal noise of exhaust.
By running the engine at idle speed, abnormal vibration and noise can be checked. Immediately
stop the engine when abnormal vibration and noise is detected and make thorough inspection
whether the turbocharger shaft wheel has any damages as well as checking the condition of
connections between pipes.
In case where the noise of engine is louder than usual, there is possibility of dampness in the
areas related with air cleaner and engine or engine block and turbocharger. And it could affect
the smooth supply of engine oil and discharge.
Check for damp condition in exhaust gas when there is sign of thermal discoloration or
discharge of carbon in connecting area of the duct.
When the engine rotates or in case where there is change in noise level, check for clogging of
air cleaner or air cleaner duct or if there is any significant amount of dust in the compressor
housing.
During the inspection of center housing, inspect inside of the housing by removing the oil drain
pipe to check for sludge generation and its attachment condition at shaft area or turbine side.
Inspect or replace the air cleaner when the compressor wheel is damaged by inflow of foreign
materials.
Inspect both side of the turbocharger wheel after removing inlet and outlet pipe of the turbocharger. 1.
2.
3.
4.
5.
6.
7.
8.
9.
Page 217 of 751
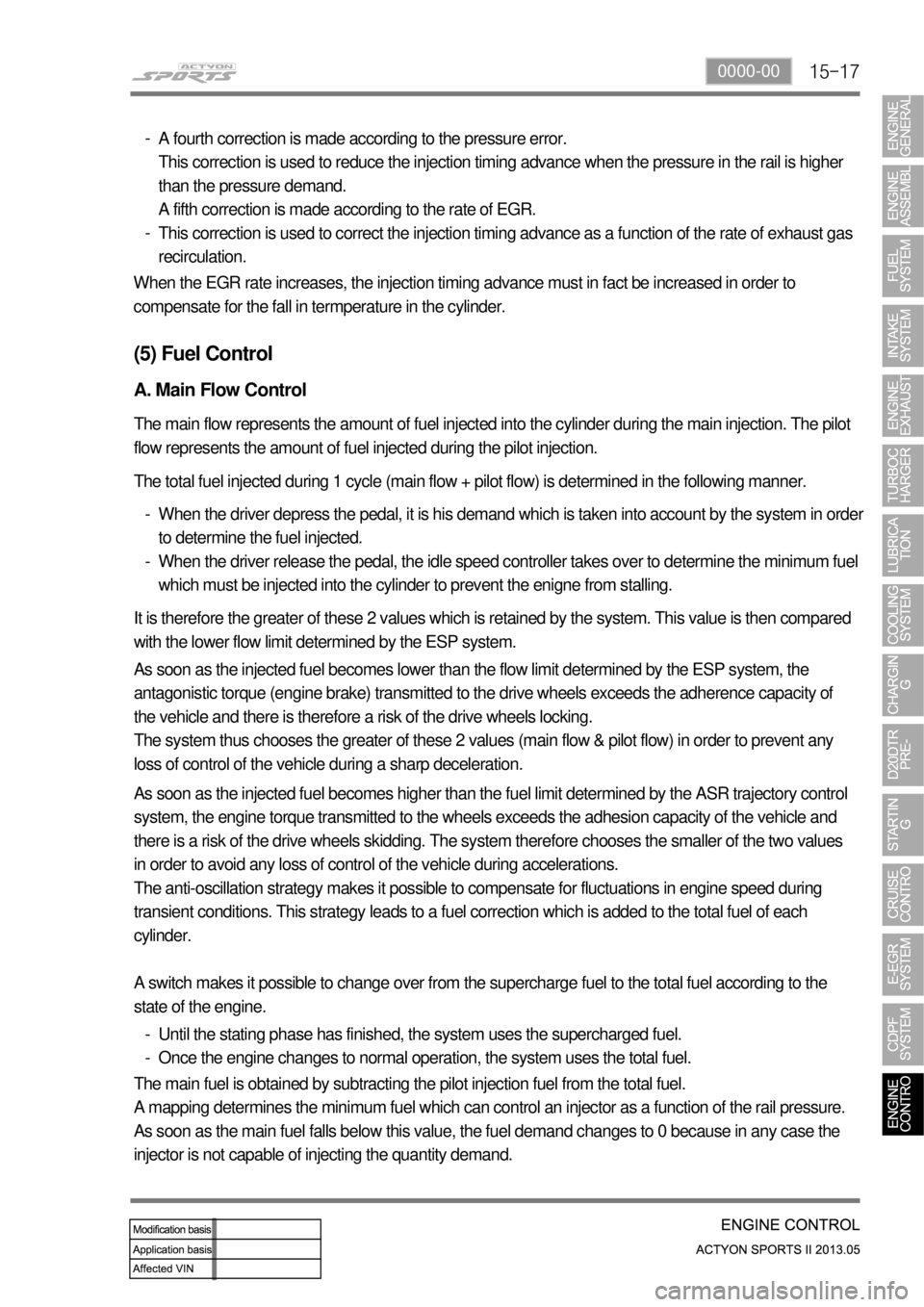
15-170000-00
A fourth correction is made according to the pressure error.
This correction is used to reduce the injection timing advance when the pressure in the rail is higher
than the pressure demand.
A fifth correction is made according to the rate of EGR.
This correction is used to correct the injection timing advance as a function of the rate of exhaust gas
recirculation. -
-
When the EGR rate increases, the injection timing advance must in fact be increased in order to
compensate for the fall in termperature in the cylinder.
A. Main Flow Control
The main flow represents the amount of fuel injected into the cylinder during the main injection. The pilot
flow represents the amount of fuel injected during the pilot injection.
The total fuel injected during 1 cycle (main flow + pilot flow) is determined in the following manner.
When the driver depress the pedal, it is his demand which is taken into account by the system in order
to determine the fuel injected.
When the driver release the pedal, the idle speed controller takes over to determine the minimum fuel
which must be injected into the cylinder to prevent the enigne from stalling. -
-
It is therefore the greater of these 2 values which is retained by the system. This value is then compared
with the lower flow limit determined by the ESP system.
As soon as the injected fuel becomes lower than the flow limit determined by the ESP system, the
antagonistic torque (engine brake) transmitted to the drive wheels exceeds the adherence capacity of
the vehicle and there is therefore a risk of the drive wheels locking.
The system thus chooses the greater of these 2 values (main flow & pilot flow) in order to prevent any
loss of control of the vehicle during a sharp deceleration.
As soon as the injected fuel becomes higher than the fuel limit determined by the ASR trajectory control
system, the engine torque transmitted to the wheels exceeds the adhesion capacity of the vehicle and
there is a risk of the drive wheels skidding. The system therefore chooses the smaller of the two values
in order to avoid any loss of control of the vehicle during accelerations.
The anti-oscillation strategy makes it possible to compensate for fluctuations in engine speed during
transient conditions. This strategy leads to a fuel correction which is added to the total fuel of each
cylinder.
A switch makes it possible to change over from the supercharge fuel to the total fuel according to the
state of the engine.
Until the stating phase has finished, the system uses the supercharged fuel.
Once the engine changes to normal operation, the system uses the total fuel. -
-
(5) Fuel Control
The main fuel is obtained by subtracting the pilot injection fuel from the total fuel.
A mapping determines the minimum fuel which can control an injector as a function of the rail pressure.
As soon as the main fuel falls below this value, the fuel demand changes to 0 because in any case the
injector is not capable of injecting the quantity demand.
Page 302 of 751
01-38410-02
I/P - LH FUSE / RELAY BOX
- Power supply circuit for HFM sensor added (F30)
- Fuse for heated steering wheel added (F32)
1. MAJOR CHANGES
Driver’s interior fuse and relay box assembly changed ▶
F32
F30
Page 412 of 751
06-58610-08
8510-60 Heated steering wheel switch
- Heated steering wheel switch added to outside mirror switch bezel
8510-10 Rear seat warmer switch
- Adopt rear seat warmer switches to rear door LH/RH
2. MAJOR CHANGES
Page 413 of 751
06-6
8510-72 Multifunction switch
- Connector pin and layout changed due to heated steering wheel system adopted
- Mounting appearance changed due to changed steering wheel angle sensor
(wiring route changed) and contact coil (fixing key)
Fixing key
Mounting
groove
Page 415 of 751
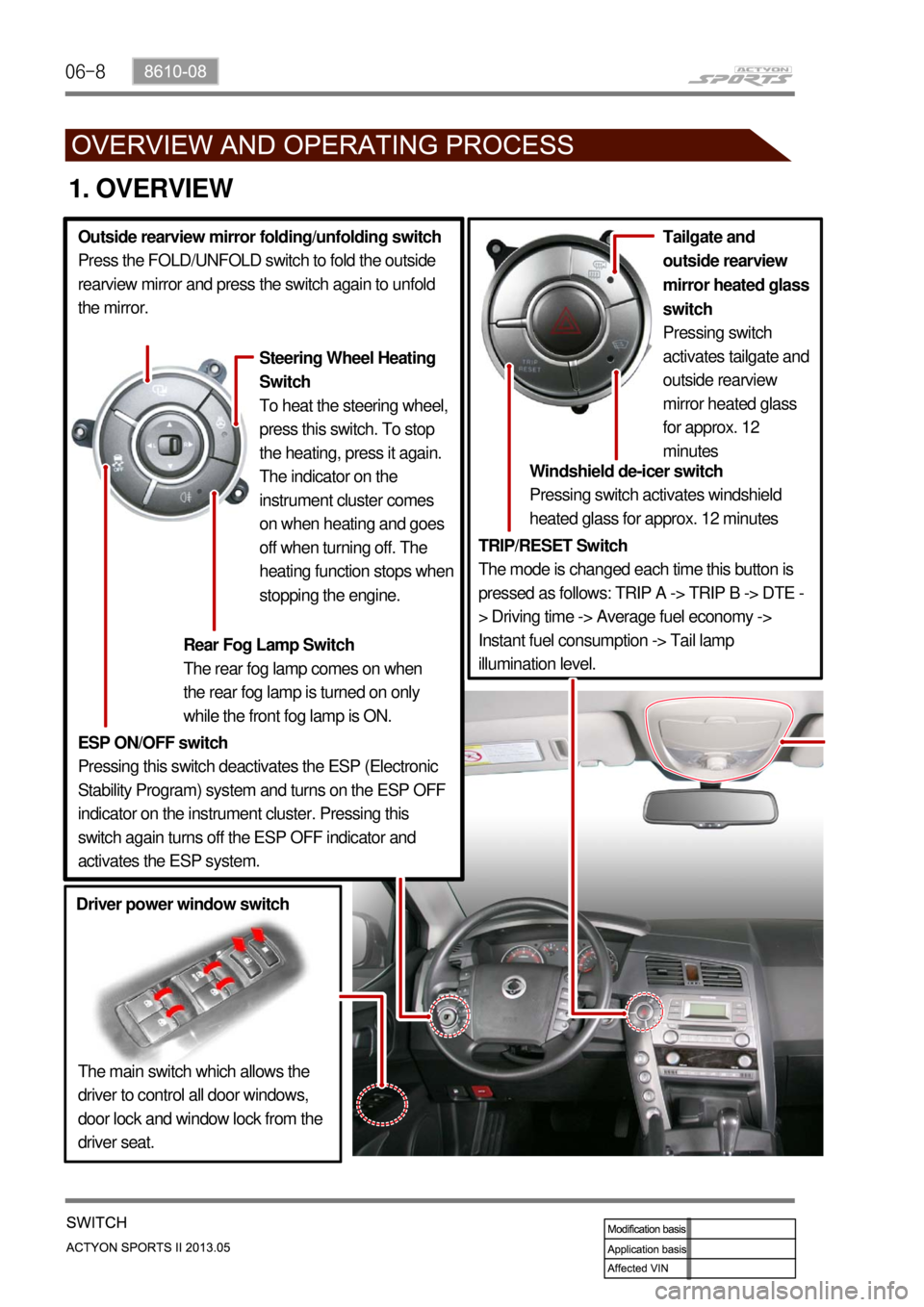
06-8
1. OVERVIEW
TRIP/RESET Switch
The mode is changed each time this button is
pressed as follows: TRIP A -> TRIP B -> DTE -
> Driving time -> Average fuel economy ->
Instant fuel consumption -> Tail lamp
illumination level.Windshield de-icer switch
Pressing switch activates windshield
heated glass for approx. 12 minutes
The main switch which allows the
driver to control all door windows,
door lock and window lock from the
driver seat. Tailgate and
outside rearview
mirror heated glass
switch
Pressing switch
activates tailgate and
outside rearview
mirror heated glass
for approx. 12
minutes
Driver power window switchESP ON/OFF switch
Pressing this switch deactivates the ESP (Electronic
Stability Program) system and turns on the ESP OFF
indicator on the instrument cluster. Pressing this
switch again turns off the ESP OFF indicator and
activates the ESP system. Outside rearview mirror folding/unfolding switch
Press the FOLD/UNFOLD switch to fold the outside
rearview mirror and press the switch again to unfold
the mirror.
Rear Fog Lamp Switch
The rear fog lamp comes on when
the rear fog lamp is turned on only
while the front fog lamp is ON.
Steering Wheel Heating
Switch
To heat the steering wheel,
press this switch. To stop
the heating, press it again.
The indicator on the
instrument cluster comes
on when heating and goes
off when turning off. The
heating function stops when
stopping the engine.