Page 190 of 751
14-6
Excessive overload of CDPF (warning lamp illuminated)
If the vehicle is driven at a speed of 5 to 10 km/h for an extended period of time, the soot
accumulated in the CDPF cannot be burned as the CDPF cannot reach the regeneration
temperature. Then, an excessive amount of soot can be accumulated in the CDPF.
This case is much worse than the simple over-load of the CDPF. To inform this to the driver, the
engine warning lamp comes on and the engine power is decreased to protect the system.
To solve this problem, blow soot between the engine and exhaust system several times and erase
the related DTC. Then, check if the same DTC is regenerated again. If so, check the DTC related to
the differential pressure sensor. 1.
2.
3.
Page 285 of 751
06-52110-01
1. COMPONENT LOCATOR
1. Reserver Tank
2. Deaeration Tube
3. Inlet Hose
6. Clamp
7. Clamp
8. Bolt (M6, 2 piece)
9. Radiator10. Lower Radiator Insulator
11. Plate
12. Clip
13. Upper Radiator Insulator
14. Bracket
15. PWM Electric Fan
Page 295 of 751
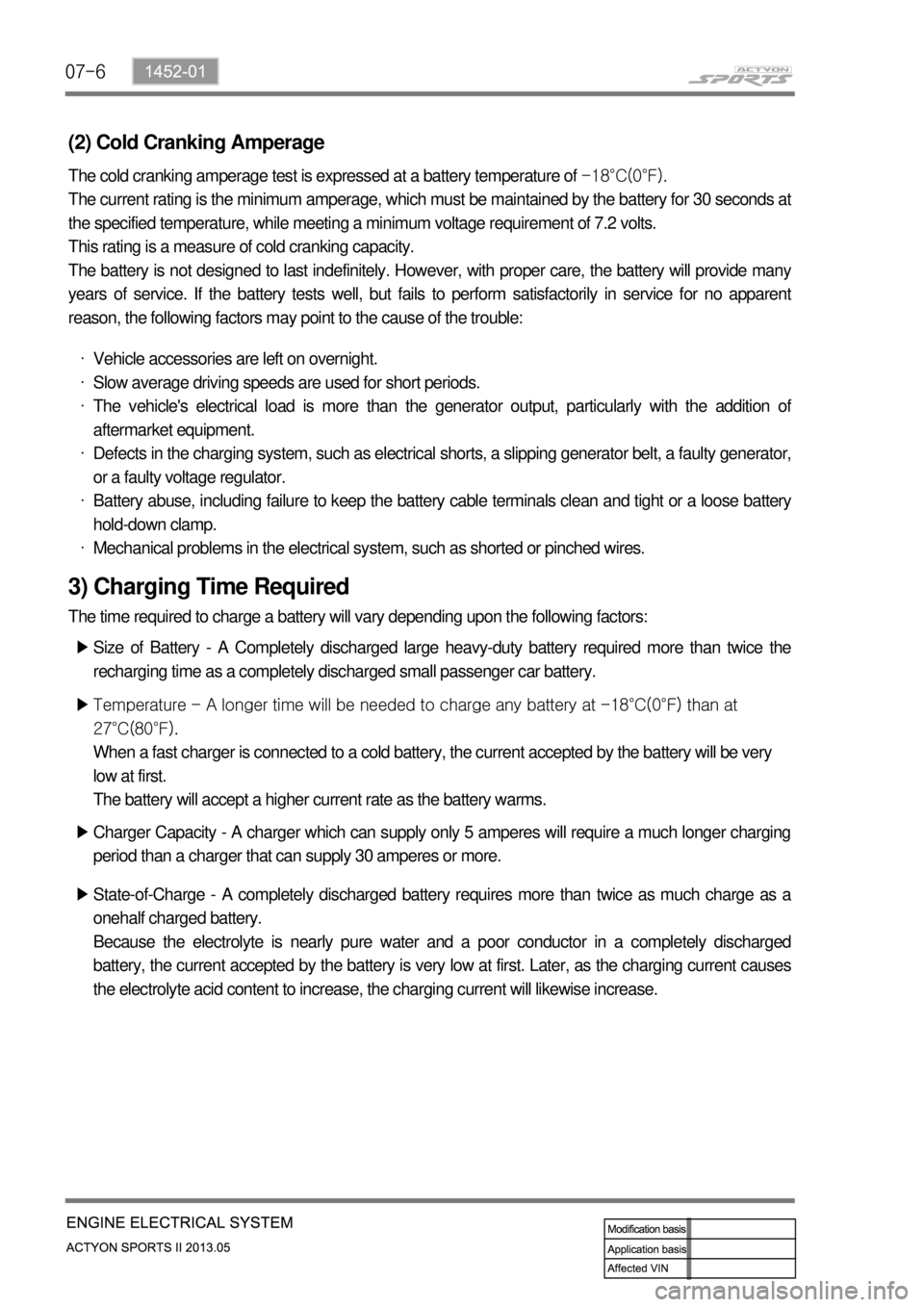
07-6
(2) Cold Cranking Amperage
The cold cranking amperage test is expressed at a battery temperature of -18°C(0°F).
The current rating is the minimum amperage, which must be maintained by the battery for 30 seconds at
the specified temperature, while meeting a minimum voltage requirement of 7.2 volts.
This rating is a measure of cold cranking capacity.
The battery is not designed to last indefinitely. However, with proper care, the battery will provide many
years of service. If the battery tests well, but fails to perform satisfactorily in service for no apparent
reason, the following factors may point to the cause of the trouble:
Vehicle accessories are left on overnight.
Slow average driving speeds are used for short periods.
The vehicle's electrical load is more than the generator output, particularly with the addition o
f
aftermarket equipment.
Defects in the charging system, such as electrical shorts, a slipping generator belt, a faulty generator,
or a faulty voltage regulator.
Battery abuse, including failure to keep the battery cable terminals clean and tight or a loose battery
hold-down clamp.
Mechanical problems in the electrical system, such as shorted or pinched wires. ·
·
·
·
·
·
3) Charging Time Required
The time required to charge a battery will vary depending upon the following factors:
Size of Battery - A Completely discharged large heavy-duty battery required more than twice the
recharging time as a completely discharged small passenger car battery. ▶
<007b008c00940097008c00990088009b009c0099008c00470054004700680047009300960095008e008c00990047009b00900094008c0047009e00900093009300470089008c00470095008c008c008b008c008b0047009b00960047008a008f0088009900
8e008c00470088009500a0004700890088009b009b008c0099>y at -18°C(0°F) than at
27°C(80°F).
When a fast charger is connected to a cold battery, the current accepted by the battery will be very
low at first.
The battery will accept a higher current rate as the battery warms. ▶
Charger Capacity - A charger which can supply only 5 amperes will require a much longer charging
period than a charger that can supply 30 amperes or more. ▶
State-of-Charge - A completely discharged battery requires more than twice as much charge as a
onehalf charged battery.
Because the electrolyte is nearly pure water and a poor conductor in a completely discharged
battery, the current accepted by the battery is very low at first. Later, as the charging current causes
the electrolyte acid content to increase, the charging current will likewise increase. ▶
Page 297 of 751
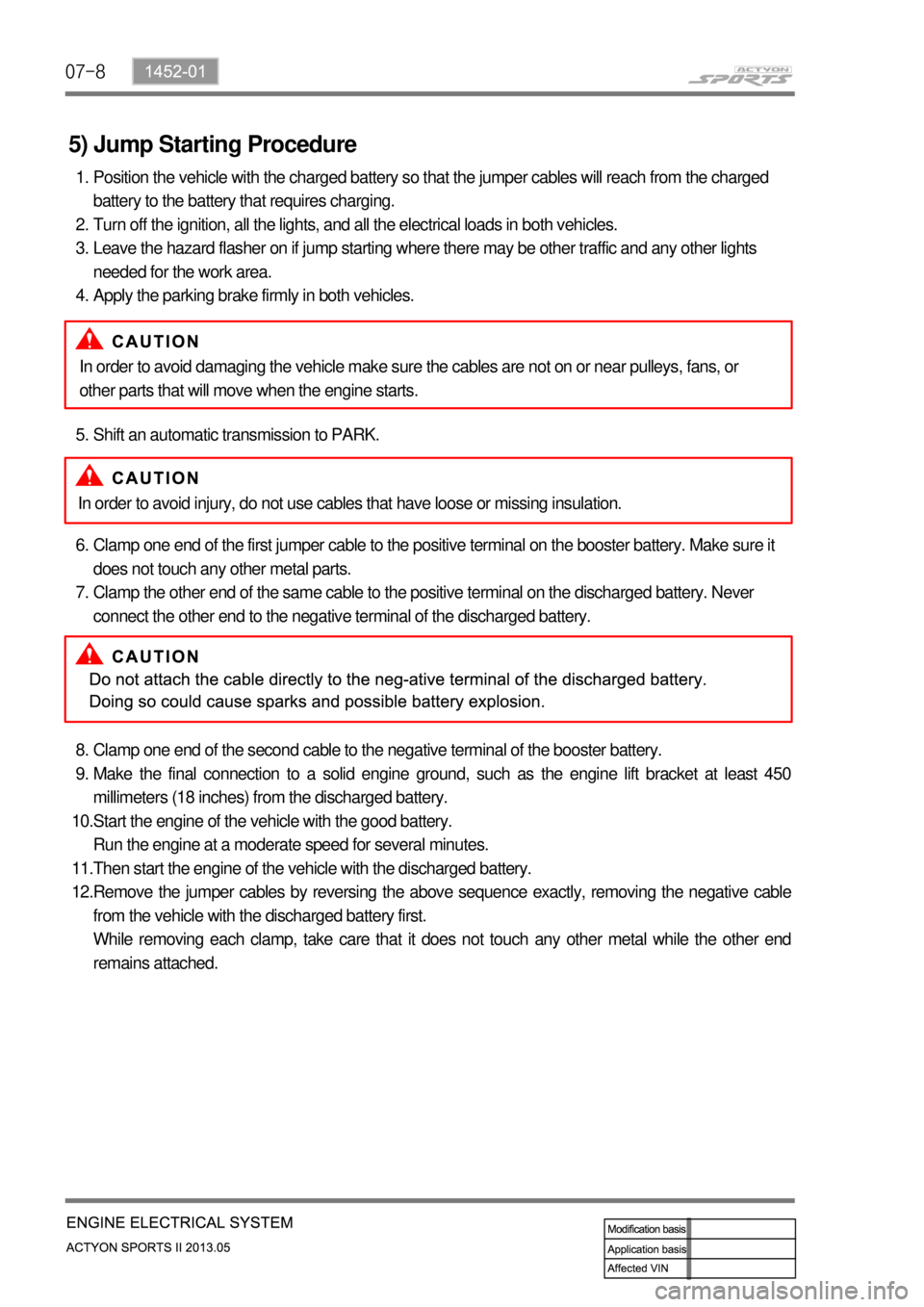
07-8
5) Jump Starting Procedure
Position the vehicle with the charged battery so that the jumper cables will reach from the charged
battery to the battery that requires charging.
Turn off the ignition, all the lights, and all the electrical loads in both vehicles.
Leave the hazard flasher on if jump starting where there may be other traffic and any other lights
needed for the work area.
Apply the parking brake firmly in both vehicles. 1.
2.
3.
4.
Shift an automatic transmission to PARK. 5.
Clamp one end of the first jumper cable to the positive terminal on the booster battery. Make sure it
does not touch any other metal parts.
Clamp the other end of the same cable to the positive terminal on the discharged battery. Never
connect the other end to the negative terminal of the discharged battery. 6.
7.
Clamp one end of the second cable to the negative terminal of the booster battery.
Make the final connection to a solid engine ground, such as the engine lift bracket at least 450
millimeters (18 inches) from the discharged battery.
Start the engine of the vehicle with the good battery.
Run the engine at a moderate speed for several minutes.
Then start the engine of the vehicle with the discharged battery.
Remove the jumper cables by reversing the above sequence exactly, removing the negative cable
from the vehicle with the discharged battery first.
While removing each clamp, take care that it does not touch any other metal while the other end
remains attached. 8.
9.
10.
11.
12.In order to avoid damaging the vehicle make sure the cables are not on or near pulleys, fans, or
other parts that will move when the engine starts.
In order to avoid injury, do not use cables that have loose or missing insulation.
Page 298 of 751
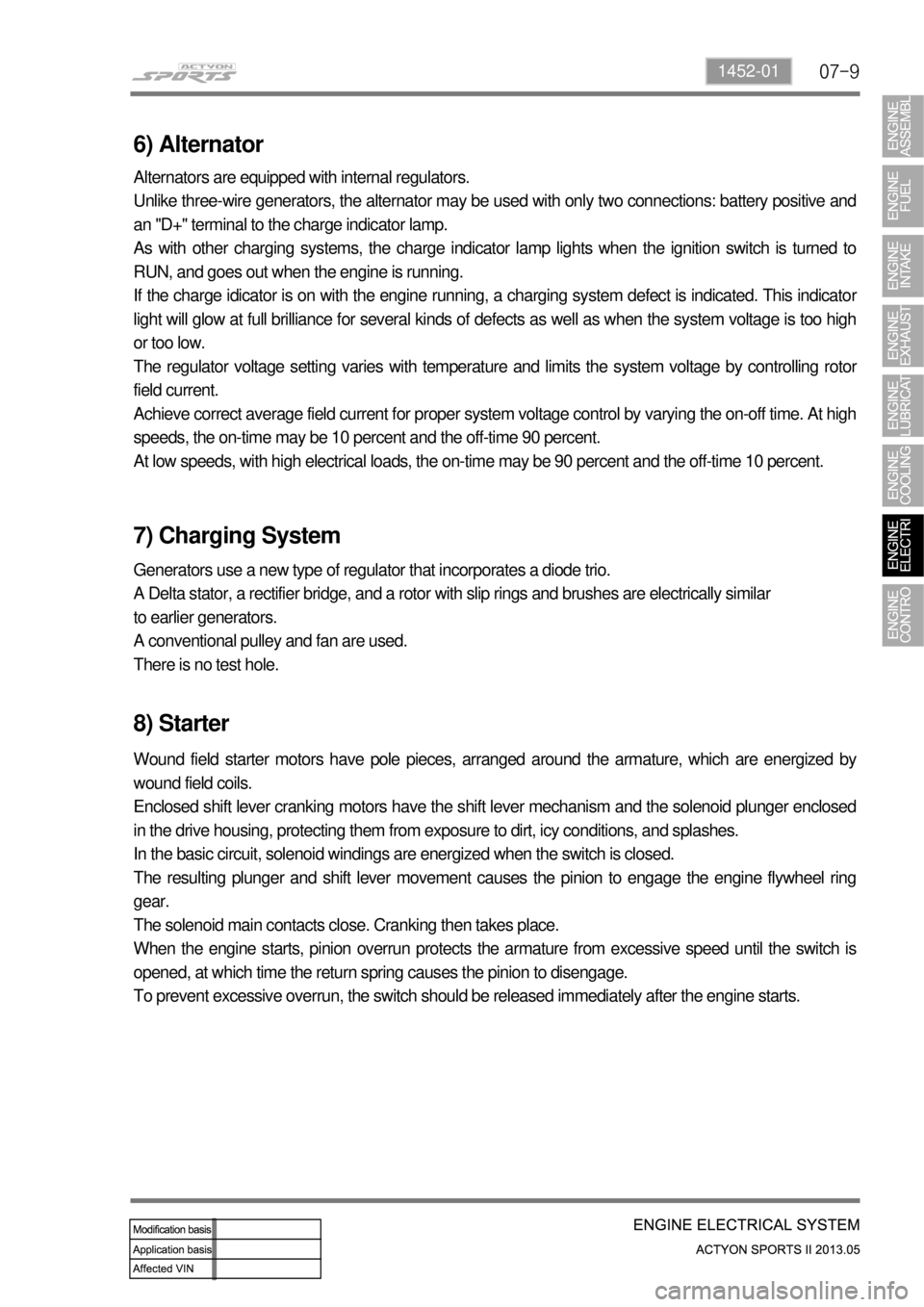
07-91452-01
6) Alternator
Alternators are equipped with internal regulators.
Unlike three-wire generators, the alternator may be used with only two connections: battery positive and
an "D+" terminal to the charge indicator lamp.
As with other charging systems, the charge indicator lamp lights when the ignition switch is turned to
RUN, and goes out when the engine is running.
If the charge idicator is on with the engine running, a charging system defect is indicated. This indicato
r
light will glow at full brilliance for several kinds of defects as well as when the system voltage is too high
or too low.
The regulator voltage setting varies with temperature and limits the system voltage by controlling roto
r
field current.
Achieve correct average field current for proper system voltage control by varying the on-off time. At high
speeds, the on-time may be 10 percent and the off-time 90 percent.
At low speeds, with high electrical loads, the on-time may be 90 percent and the off-time 10 percent.
7) Charging System
Generators use a new type of regulator that incorporates a diode trio.
A Delta stator, a rectifier bridge, and a rotor with slip rings and brushes are electrically similar
to earlier generators.
A conventional pulley and fan are used.
There is no test hole.
8) Starter
Wound field starter motors have pole pieces, arranged around the armature, which are energized by
wound field coils.
Enclosed shift lever cranking motors have the shift lever mechanism and the solenoid plunger enclosed
in the drive housing, protecting them from exposure to dirt, icy conditions, and splashes.
In the basic circuit, solenoid windings are energized when the switch is closed.
The resulting plunger and shift lever movement causes the pinion to engage the engine flywheel ring
gear.
The solenoid main contacts close. Cranking then takes place.
When the engine starts, pinion overrun protects the armature from excessive speed until the switch is
opened, at which time the return spring causes the pinion to disengage.
To prevent excessive overrun, the switch should be released immediately after the engine starts.
Page 304 of 751
01-58410-02
ICM
Interior Fuse & Relay
Box (RH)
2. MOUNTING LOCATION
In engine compartment ▶
In vehicle ▶
Fuse & Relay Box In Engine
Compartment
1. OVERVIEW
The ICM (Integrated Control Module) mounted to the back of the STICS is integrated with the door
lock/unlock relay, windshield de-icer relay and turn signal lamp relay. There are four fuse & relay units.
Interior Fuse & Relay
Box (LH)Mounting Location of
ICM
Page 308 of 751
01-98410-02
5. OPERATING PROCESS OF ICM BOX
The following relays are integrated into the ICM (Integrated Control Module) box.
Door lock/unlock relay
Windshield de-icer relay
Turn signal lamp relay -
-
-
1) Overview
2) Mounting Location
Door lock/
unlock relay
Turn signal lamp relay
Windshield
de-icer relay
Inner view of ICM PCB
PAS buzzer
Chime
ICM box
STICS
The relays in the ICM box cannot be replaced respectively; so if the any of the components on
the PCB are defective, they should be replaced as an assembly.
Page 311 of 751
01-12
(3) Turn signal lamp (Hazard warning lamp operation)
The B+ power supplied through the No. F66 interior fuse on the right-hand of the engine compartment is
on standby on the No. 30 and 86 hazard warning lamp relay terminals via the ICM No. 18 terminal.
The STICS activates and/or controls the hazard warning lamp relay using the No. A26 terminal
depending on the operating conditions. The activated relay supplies the No. 87 and 87a terminals with
the power, which is on standby on the No. 30 hazard warning lamp relay terminal.
The supplied power flows to the corresponding circuit via the No. 7 and 16 ICM terminals.