Page 281 of 828
12-10
4) Recovery of Set Speed (RESUME)
Even if the cruise control is cancelled, the previous set cruise speed can be recovered by pulling
up the cruise control lever when the current vehicle speed is over 36 km/h without an acceleration
intervention. But if you turn off the ignition switch, the memorized set speed is cleared and you
cannot recover the previous set speed.
But the driver should know the previous set speed to react to the changed vehicle speed
properly. If the vehicle speed increases abruptly, depress the brake pedal to adjust the vehicle
speed properly.
Page 283 of 828
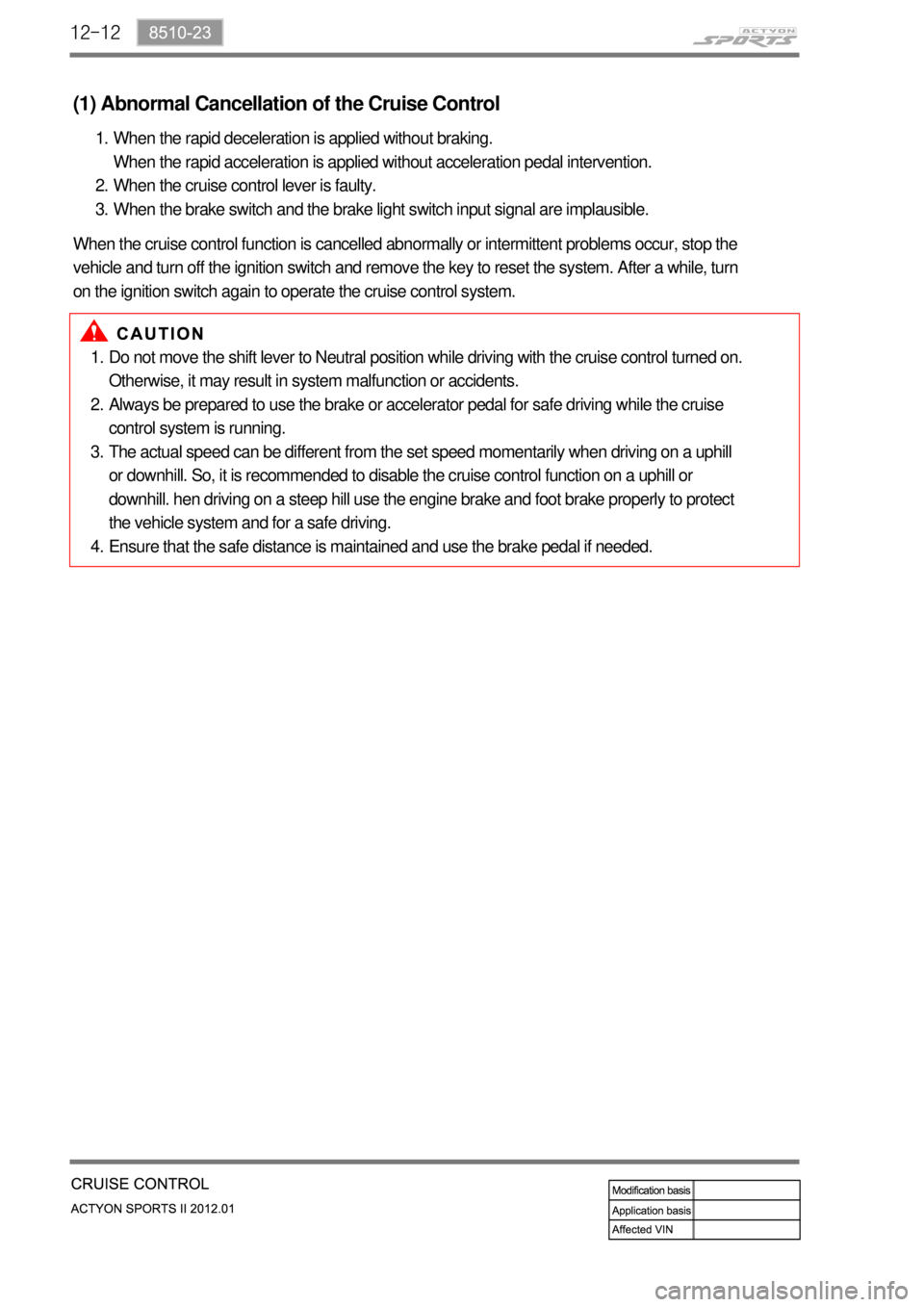
12-12
Do not move the shift lever to Neutral position while driving with the cruise control turned on.
Otherwise, it may result in system malfunction or accidents.
Always be prepared to use the brake or accelerator pedal for safe driving while the cruise
control system is running.
The actual speed can be different from the set speed momentarily when driving on a uphill
or downhill. So, it is recommended to disable the cruise control function on a uphill or
downhill. hen driving on a steep hill use the engine brake and foot brake properly to protect
the vehicle system and for a safe driving.
Ensure that the safe distance is maintained and use the brake pedal if needed. 1.
2.
3.
4.
(1) Abnormal Cancellation of the Cruise Control
When the rapid deceleration is applied without braking.
When the rapid acceleration is applied without acceleration pedal intervention.
When the cruise control lever is faulty.
When the brake switch and the brake light switch input signal are implausible. 1.
2.
3.
When the cruise control function is cancelled abnormally or intermittent problems occur, stop the
vehicle and turn off the ignition switch and remove the key to reset the system. After a while, turn
on the ignition switch again to operate the cruise control system.
Page 312 of 828
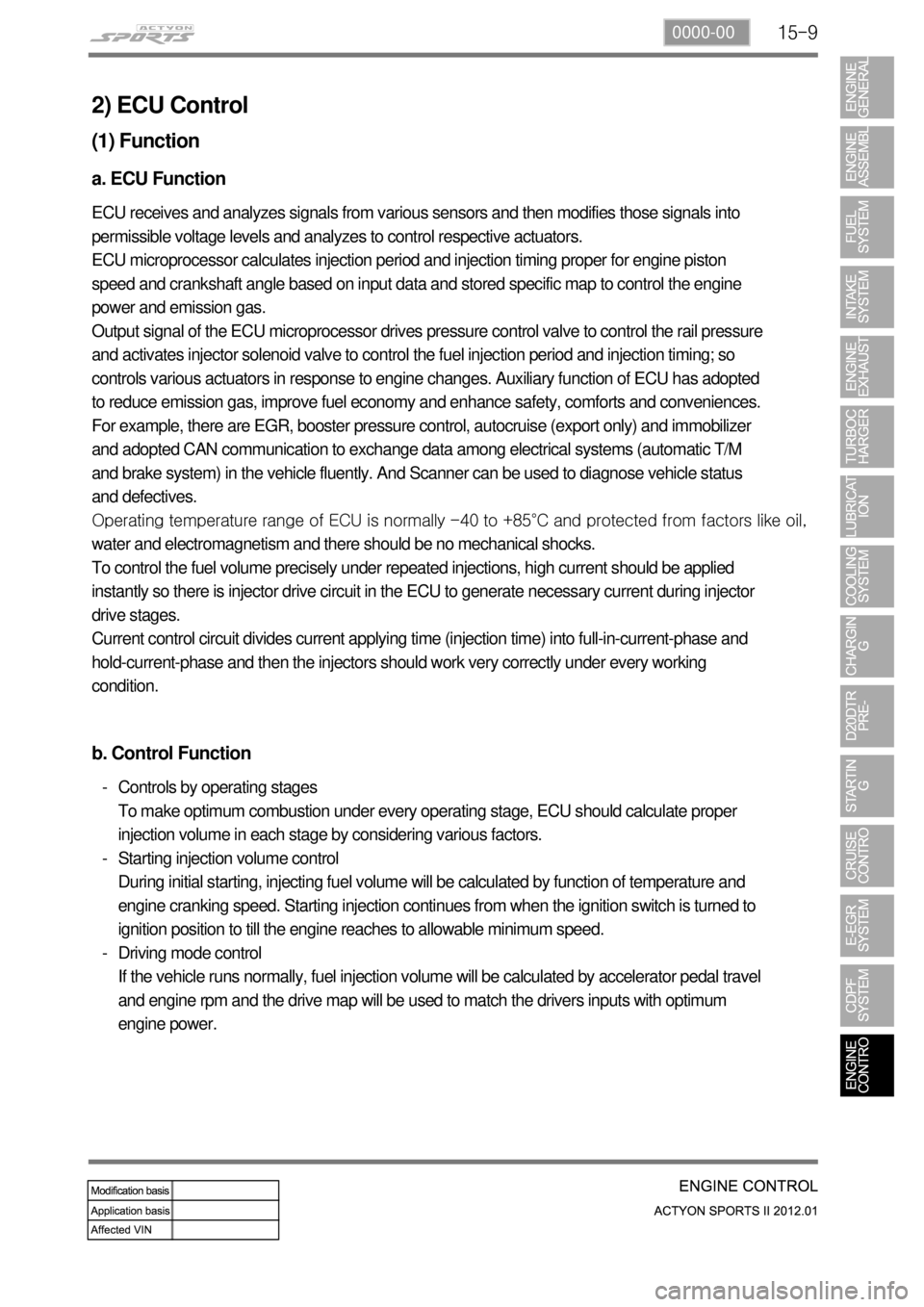
15-90000-00
2) ECU Control
(1) Function
a. ECU Function
ECU receives and analyzes signals from various sensors and then modifies those signals into
permissible voltage levels and analyzes to control respective actuators.
ECU microprocessor calculates injection period and injection timing proper for engine piston
speed and crankshaft angle based on input data and stored specific map to control the engine
power and emission gas.
Output signal of the ECU microprocessor drives pressure control valve to control the rail pressure
and activates injector solenoid valve to control the fuel injection period and injection timing; so
controls various actuators in response to engine changes. Auxiliary function of ECU has adopted
to reduce emission gas, improve fuel economy and enhance safety, comforts and conveniences.
For example, there are EGR, booster pressure control, autocruise (export only) and immobilizer
and adopted CAN communication to exchange data among electrical systems (automatic T/M
and brake system) in the vehicle fluently. And Scanner can be used to diagnose vehicle status
and defectives.
<00760097008c00990088009b00900095008e0047009b008c00940097008c00990088009b009c0099008c0047009900880095008e008c00470096008d0047006c006a007c00470090009a0047009500960099009400880093009300a000470054005b005700
47009b009600470052005f005c00b6006a004700880095008b> protected from factors like oil,
water and electromagnetism and there should be no mechanical shocks.
To control the fuel volume precisely under repeated injections, high current should be applied
instantly so there is injector drive circuit in the ECU to generate necessary current during injector
drive stages.
Current control circuit divides current applying time (injection time) into full-in-current-phase and
hold-current-phase and then the injectors should work very correctly under every working
condition.
b. Control Function
Controls by operating stages
To make optimum combustion under every operating stage, ECU should calculate proper
injection volume in each stage by considering various factors.
Starting injection volume control
During initial starting, injecting fuel volume will be calculated by function of temperature and
engine cranking speed. Starting injection continues from when the ignition switch is turned to
ignition position to till the engine reaches to allowable minimum speed.
Driving mode control
If the vehicle runs normally, fuel injection volume will be calculated by accelerator pedal travel
and engine rpm and the drive map will be used to match the drivers inputs with optimum
engine power. -
-
-
Page 314 of 828
15-110000-00
b. Pilot Injection
Injection before main injection. Consists of 1st and 2nd pilot injection, and Pre-injection
Inject a small amount of fuel before main injection to make the combustion smooth. Also, called
as preliminary injection or ignition injection. This helps to reduce Nox, engine noise and vibration,
and to stabilize the idling.
The injected fuel volume is changed and stopped according to the coolant temperature and
intake air volume.
Pilot injection is much earlier than main injection due to higher engine rpm
Too small injection volume (insufficient injection pressure, insufficient fuel injection volume
in main injection, engine braking)
System failure (fuel system, engine control system) -
-
-
Pilot injection
Main injection
Combustion pressure with pilot injection
Combustion pressure without pilot injection 1.
2.
1a.
2b. Stop conditions
Combustion pressure characteristic curve for pilot injection ▶
Page 316 of 828
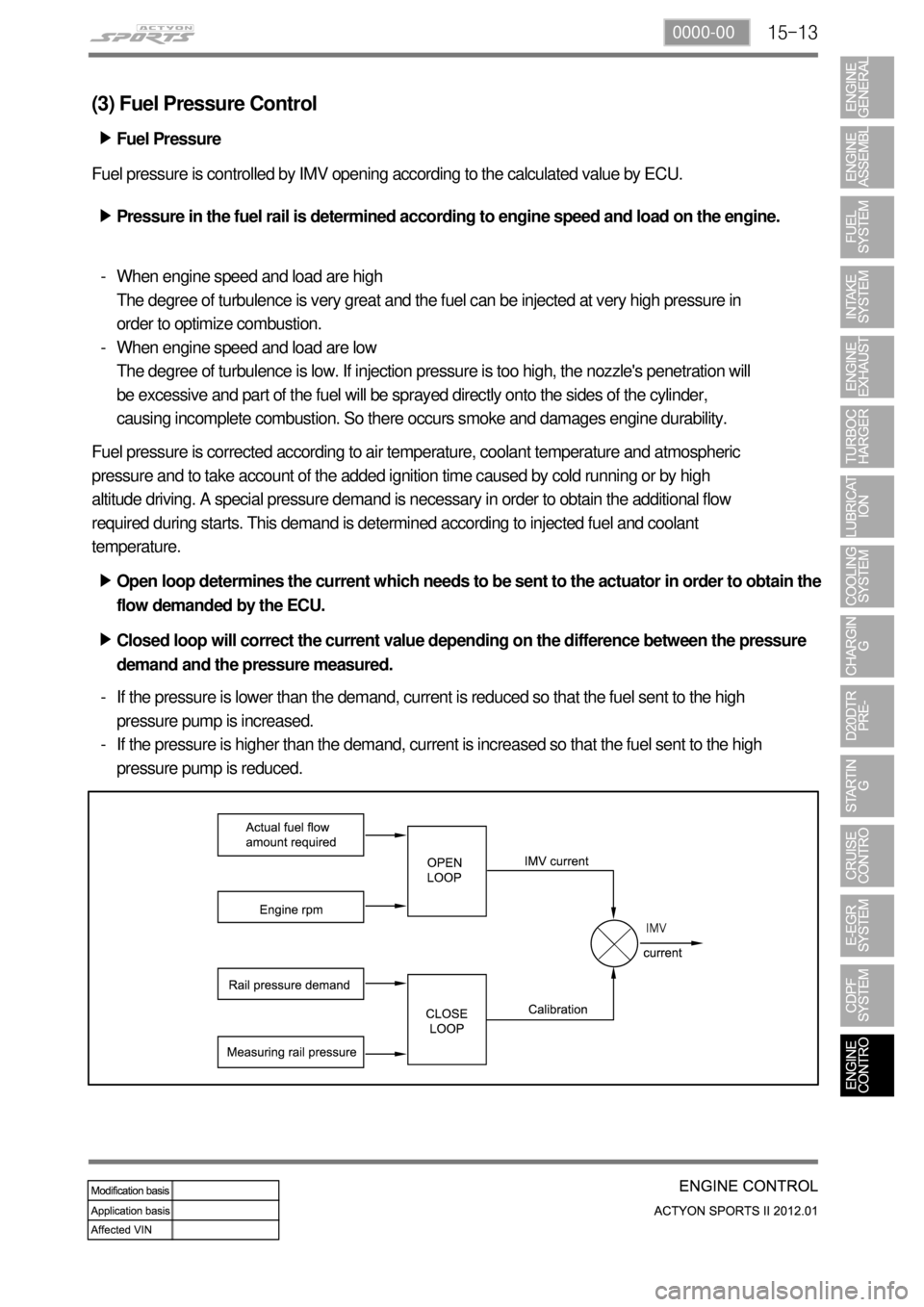
15-130000-00
(3) Fuel Pressure Control
Fuel pressure is controlled by IMV opening according to the calculated value by ECU.
Pressure in the fuel rail is determined according to engine speed and load on the engine. ▶
When engine speed and load are high
The degree of turbulence is very great and the fuel can be injected at very high pressure in
order to optimize combustion.
When engine speed and load are low
The degree of turbulence is low. If injection pressure is too high, the nozzle's penetration will
be excessive and part of the fuel will be sprayed directly onto the sides of the cylinder,
causing incomplete combustion. So there occurs smoke and damages engine durability. -
-
Fuel pressure is corrected according to air temperature, coolant temperature and atmospheric
pressure and to take account of the added ignition time caused by cold running or by high
altitude driving. A special pressure demand is necessary in order to obtain the additional flow
required during starts. This demand is determined according to injected fuel and coolant
temperature.
Open loop determines the current which needs to be sent to the actuator in order to obtain the
flow demanded by the ECU. ▶
Closed loop will correct the current value depending on the difference between the pressure
demand and the pressure measured. ▶
If the pressure is lower than the demand, current is reduced so that the fuel sent to the high
pressure pump is increased.
If the pressure is higher than the demand, current is increased so that the fuel sent to the high
pressure pump is reduced. -
-Fuel Pressure ▶
Page 321 of 828
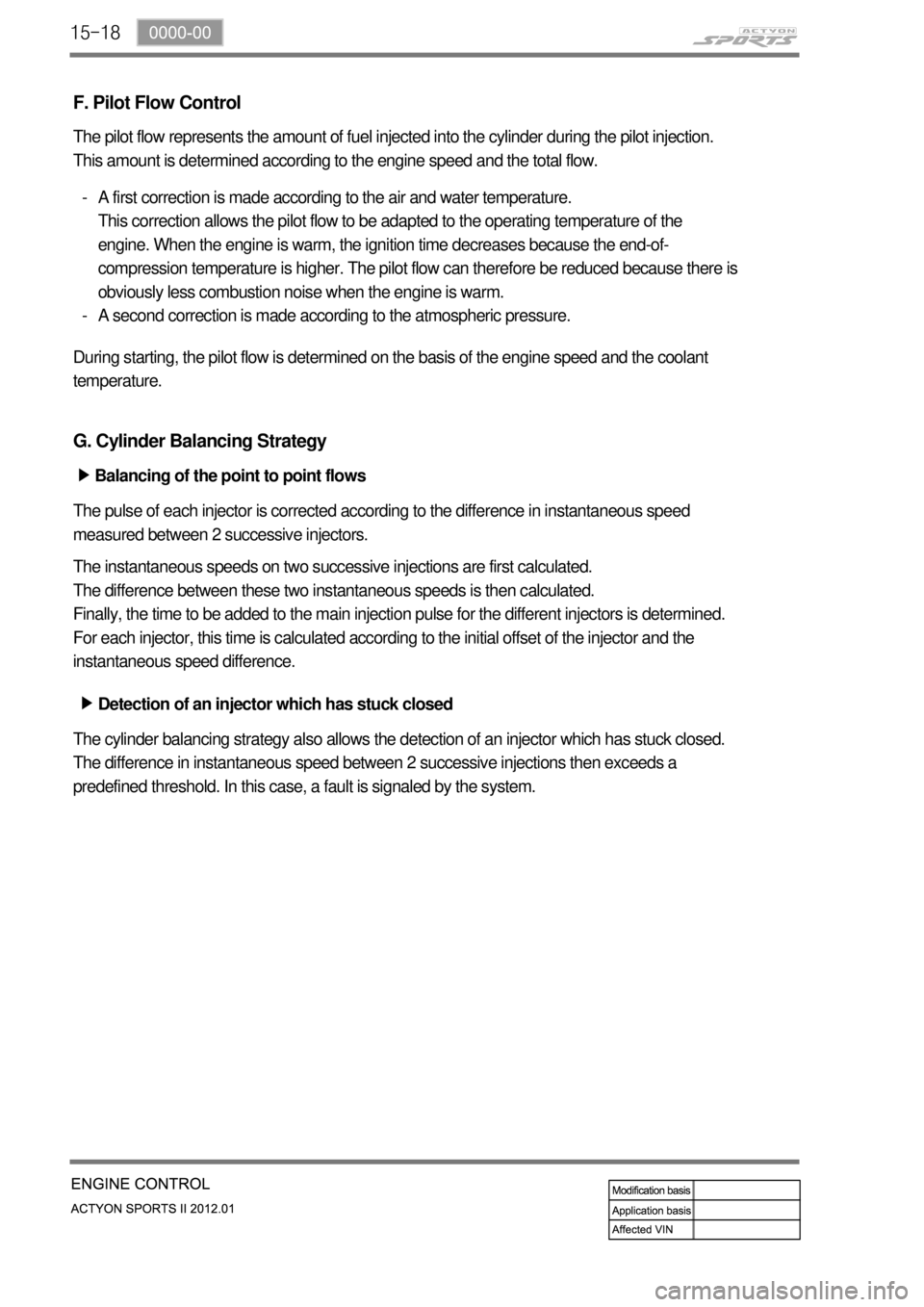
15-18
F. Pilot Flow Control
The pilot flow represents the amount of fuel injected into the cylinder during the pilot injection.
This amount is determined according to the engine speed and the total flow.
A first correction is made according to the air and water temperature.
This correction allows the pilot flow to be adapted to the operating temperature of the
engine. When the engine is warm, the ignition time decreases because the end-of-
compression temperature is higher. The pilot flow can therefore be reduced because there is
obviously less combustion noise when the engine is warm.
A second correction is made according to the atmospheric pressure. -
-
During starting, the pilot flow is determined on the basis of the engine speed and the coolant
temperature.
G. Cylinder Balancing Strategy
Balancing of the point to point flows ▶
The pulse of each injector is corrected according to the difference in instantaneous speed
measured between 2 successive injectors.
The instantaneous speeds on two successive injections are first calculated.
The difference between these two instantaneous speeds is then calculated.
Finally, the time to be added to the main injection pulse for the different injectors is determined.
For each injector, this time is calculated according to the initial offset of the injector and the
instantaneous speed difference.
Detection of an injector which has stuck closed ▶
The cylinder balancing strategy also allows the detection of an injector which has stuck closed.
The difference in instantaneous speed between 2 successive injections then exceeds a
predefined threshold. In this case, a fault is signaled by the system.
Page 329 of 828
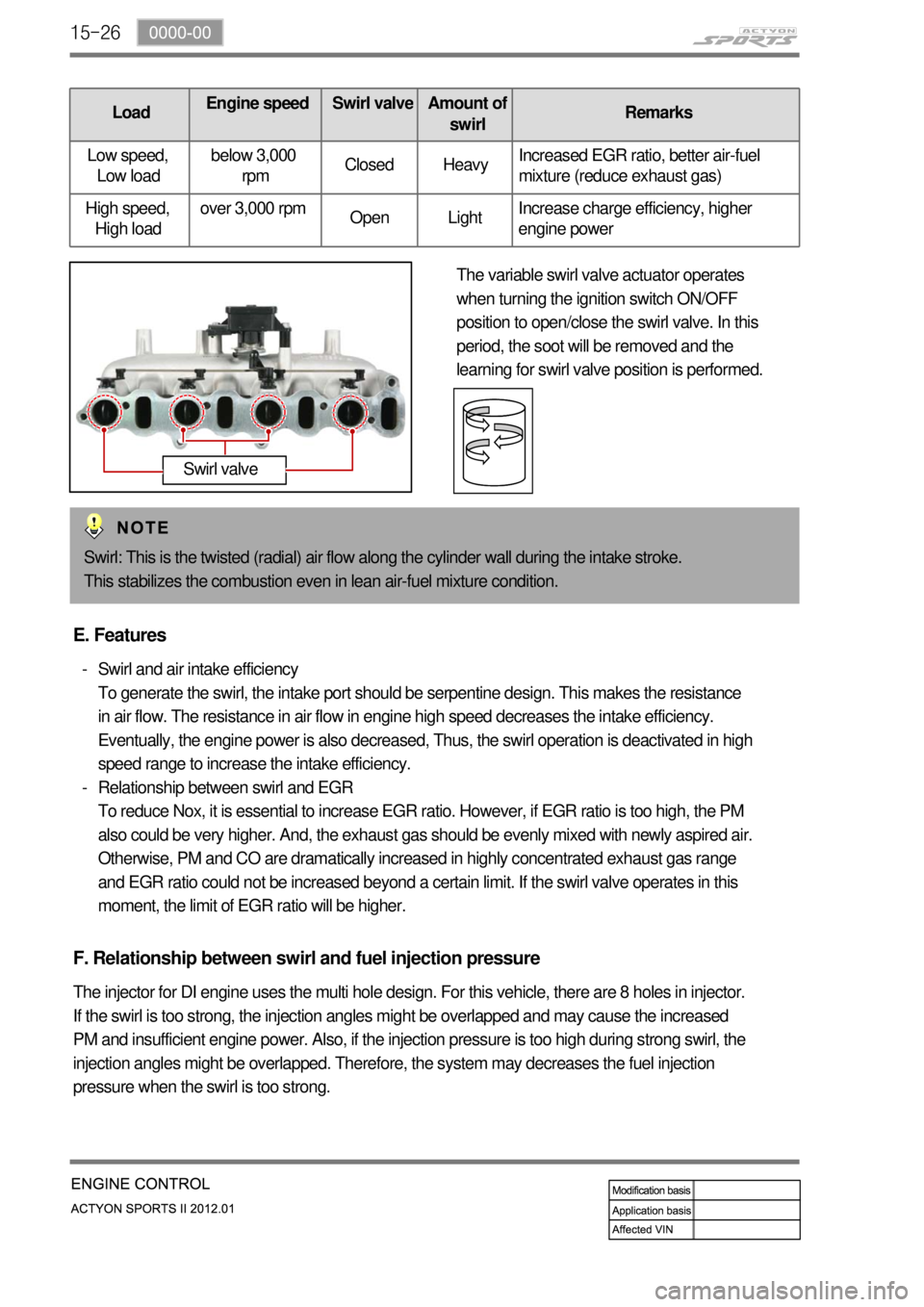
15-26
LoadEngine speed Swirl valveAmount of
swirlRemarks
Low speed,
Low loadbelow 3,000
rpmClosed HeavyIncreased EGR ratio, better air-fuel
mixture (reduce exhaust gas)
High speed,
High loadover 3,000 rpm
Open LightIncrease charge efficiency, higher
engine power
The variable swirl valve actuator operates
when turning the ignition switch ON/OFF
position to open/close the swirl valve. In this
period, the soot will be removed and the
learning for swirl valve position is performed.
Swirl: This is the twisted (radial) air flow along the cylinder wall during the intake stroke.
This stabilizes the combustion even in lean air-fuel mixture condition.
Swirl valve
E. Features
Swirl and air intake efficiency
To generate the swirl, the intake port should be serpentine design. This makes the resistance
in air flow. The resistance in air flow in engine high speed decreases the intake efficiency.
Eventually, the engine power is also decreased, Thus, the swirl operation is deactivated in high
speed range to increase the intake efficiency.
Relationship between swirl and EGR
To reduce Nox, it is essential to increase EGR ratio. However, if EGR ratio is too high, the PM
also could be very higher. And, the exhaust gas should be evenly mixed with newly aspired air.
Otherwise, PM and CO are dramatically increased in highly concentrated exhaust gas range
and EGR ratio could not be increased beyond a certain limit. If the swirl valve operates in this
moment, the limit of EGR ratio will be higher. -
-
F. Relationship between swirl and fuel injection pressure
The injector for DI engine uses the multi hole design. For this vehicle, there are 8 holes in injector.
If the swirl is too strong, the injection angles might be overlapped and may cause the increased
PM and insufficient engine power. Also, if the injection pressure is too high during strong swirl, the
injection angles might be overlapped. Therefore, the system may decreases the fuel injection
pressure when the swirl is too strong.
Page 346 of 828
15-430000-00
(14) Immobilizer control
A. Overview
The Immobilizer System provides an additional theft deterrent to the vehicle in which it is installed
and prevents it from being started by unauthorized persons. The transponder integrated in the key
and the engine control unit have the same code. When the ignition key with the integrated
transponder is turned to the ON position, the ECU (Engine Control Unit) checks the crypto code
of the key and, if correct, allows the vehicle to start the engine.
For details, refer to Chapter "Immobilizer".
B. Components
Basic components (ignition key system) ▶
D20DTR ECUImmobilizer antennaInstrument cluster
Immobilizer keyStart motor