Page 2669 of 4210
![INFINITI QX56 2010 Factory Service Manual LAN
MAIN LINE BETWEEN 4WD AND ABS CIRCUITLAN-71
< COMPONENT DIAGNOSIS > [CAN]
C
D
E
F
G H
I
J
K L
B A
O P
N
MAIN LINE BETWEEN 4WD AND ABS CIRCUIT
Diagnosis ProcedureINFOID:0000000005152915
1.CHECK HAR INFINITI QX56 2010 Factory Service Manual LAN
MAIN LINE BETWEEN 4WD AND ABS CIRCUITLAN-71
< COMPONENT DIAGNOSIS > [CAN]
C
D
E
F
G H
I
J
K L
B A
O P
N
MAIN LINE BETWEEN 4WD AND ABS CIRCUIT
Diagnosis ProcedureINFOID:0000000005152915
1.CHECK HAR](/manual-img/42/57032/w960_57032-2668.png)
LAN
MAIN LINE BETWEEN 4WD AND ABS CIRCUITLAN-71
< COMPONENT DIAGNOSIS > [CAN]
C
D
E
F
G H
I
J
K L
B A
O P
N
MAIN LINE BETWEEN 4WD AND ABS CIRCUIT
Diagnosis ProcedureINFOID:0000000005152915
1.CHECK HARNESS CONTI
NUITY (OPEN CIRCUIT)
1. Turn the ignition switch OFF.
2. Disconnect the battery cabl e from the negative terminal.
3. Disconnect the following harness connectors.
-ECM
- Transfer control unit
- ABS actuator and electric unit (control unit)
4. Check the continuity between the transfer control unit harness connector and t he ABS actuator and elec-
tric unit (control unit) harness connector.
Is the inspection result normal?
YES (Present error)>>Check the following items again. • Decision of CAN system type.
• Not received CONSULT-III data [SELF-DIAG RESULTS, CAN DIAG SUPPORT MNTR (“ECU
list” included)].
• Procedure for detecting root cause.
YES (Past error)>>Error was detected in the main li ne between the transfer control unit and the ABS actuator
and electric unit (control unit).
NO >> Repair the main line between the transfer cont rol unit and the ABS actuator and electric unit (con-
trol unit).
Transfer control unit harness connector ABS actuator and electric unit (control unit)
harness connector Continuity
Connector No. Terminal No.Connector No. Terminal No.
E142 7
E125 11
E x i s t e d
8 15Existed
Revision: April 20092010 QX56
Page 2670 of 4210
![INFINITI QX56 2010 Factory Service Manual LAN-72
< COMPONENT DIAGNOSIS >[CAN]
ECM BRANCH LINE CIRCUIT
ECM BRANCH LINE CIRCUIT
Diagnosis ProcedureINFOID:0000000005146479
1.CHECK CONNECTOR
1. Turn the ignition switch OFF.
2. Disconnect the batt INFINITI QX56 2010 Factory Service Manual LAN-72
< COMPONENT DIAGNOSIS >[CAN]
ECM BRANCH LINE CIRCUIT
ECM BRANCH LINE CIRCUIT
Diagnosis ProcedureINFOID:0000000005146479
1.CHECK CONNECTOR
1. Turn the ignition switch OFF.
2. Disconnect the batt](/manual-img/42/57032/w960_57032-2669.png)
LAN-72
< COMPONENT DIAGNOSIS >[CAN]
ECM BRANCH LINE CIRCUIT
ECM BRANCH LINE CIRCUIT
Diagnosis ProcedureINFOID:0000000005146479
1.CHECK CONNECTOR
1. Turn the ignition switch OFF.
2. Disconnect the battery cable from the negative terminal.
3. Check the following terminals and connectors fo r damage, bend and loose connection (unit side and con-
nector side).
-ECM
- Harness connector E5
- Harness connector F14
Is the inspection result normal?
YES >> GO TO 2.
NO >> Repair the terminal and connector.
2.CHECK HARNESS FOR OPEN CIRCUIT
1. Disconnect the connector of ECM.
2. Check the resistance between the ECM harness connector terminals.
Is the measurement value within the specification?
YES >> GO TO 3.
NO >> Repair the ECM branch line.
3.CHECK POWER SUPPLY AND GROUND CIRCUIT
Check the power supply and the ground circuit of the ECM. Refer to EC-82, "
Diagnosis Procedure".
Is the inspection result normal?
YES (Present error)>>Replace the ECM. Refer to EC-17, "Procedure After Replacing ECM".
YES (Past error)>>Error was detected in the ECM branch line.
NO >> Repair the power supply and the ground circuit.
ECM harness connector Resistance (Ω)
Connector No. Terminal No.
E16 9486Approx. 108 – 132
Revision: April 20092010 QX56
Page 2685 of 4210
![INFINITI QX56 2010 Factory Service Manual LAN
CAN COMMUNICATION CIRCUITLAN-87
< COMPONENT DIAGNOSIS > [CAN]
C
D
E
F
G H
I
J
K L
B A
O P
N
CAN COMMUNICATION CIRCUIT
Diagnosis ProcedureINFOID:0000000005146494
1.CONNECTOR INSPECTION
1. Turn the INFINITI QX56 2010 Factory Service Manual LAN
CAN COMMUNICATION CIRCUITLAN-87
< COMPONENT DIAGNOSIS > [CAN]
C
D
E
F
G H
I
J
K L
B A
O P
N
CAN COMMUNICATION CIRCUIT
Diagnosis ProcedureINFOID:0000000005146494
1.CONNECTOR INSPECTION
1. Turn the](/manual-img/42/57032/w960_57032-2684.png)
LAN
CAN COMMUNICATION CIRCUITLAN-87
< COMPONENT DIAGNOSIS > [CAN]
C
D
E
F
G H
I
J
K L
B A
O P
N
CAN COMMUNICATION CIRCUIT
Diagnosis ProcedureINFOID:0000000005146494
1.CONNECTOR INSPECTION
1. Turn the ignition switch OFF.
2. Disconnect the battery cabl e from the negative terminal.
3. Disconnect all the unit connectors on CAN communication system.
4. Check terminals and connectors for damage, bend and loose connection.
Is the inspection result normal?
YES >> GO TO 2.
NO >> Repair the terminal and connector.
2.CHECK HARNESS CONTINUI TY (SHORT CIRCUIT)
Check the continuity between the data link connector terminals.
Is the inspection result normal?
YES >> GO TO 3.
NO >> Check the harness and repair the root cause.
3.CHECK HARNESS CONTINUI TY (SHORT CIRCUIT)
Check the continuity between the data link connector and the ground.
Is the inspection result normal?
YES >> GO TO 4.
NO >> Check the harness and repair the root cause.
4.CHECK ECM AND IPDM E/R TERMINATION CIRCUIT
1. Remove the ECM and the IPDM E/R.
2. Check the resistance between the ECM terminals.
3. Check the resistance between the IPDM E/R terminals.
Is the measurement value within the specification?
YES >> GO TO 5.
NO >> Replace the ECM and/or the IPDM E/R.
5.CHECK SYMPTOM
Connect all the connectors. Check if the symptoms descr ibed in the “Symptom (Results from interview with
customer)” are reproduced.
Data link connector Continuity
Connector No. Terminal No.
M22 6 14 Not existed
Data link connector
GroundContinuity
Connector No. Terminal No.
M22 6
Not existed
14 Not existed
ECM
Resistance (Ω)
Te r m i n a l N o .
94 86 Approx. 108 – 132
IPDM E/R Resistance (Ω)
Te r m i n a l N o .
39 40Approx. 108 – 132
LKIA0037E
Revision: April 20092010 QX56
Page 2686 of 4210
![INFINITI QX56 2010 Factory Service Manual LAN-88
< COMPONENT DIAGNOSIS >[CAN]
CAN COMMUNICATION CIRCUIT
Inspection result
Reproduced>>GO TO 6.
Non-reproduced>>Start the diagnosis again. Follow
the trouble diagnosis procedure when past error INFINITI QX56 2010 Factory Service Manual LAN-88
< COMPONENT DIAGNOSIS >[CAN]
CAN COMMUNICATION CIRCUIT
Inspection result
Reproduced>>GO TO 6.
Non-reproduced>>Start the diagnosis again. Follow
the trouble diagnosis procedure when past error](/manual-img/42/57032/w960_57032-2685.png)
LAN-88
< COMPONENT DIAGNOSIS >[CAN]
CAN COMMUNICATION CIRCUIT
Inspection result
Reproduced>>GO TO 6.
Non-reproduced>>Start the diagnosis again. Follow
the trouble diagnosis procedure when past error is
detected.
6.CHECK UNIT REPRODUCTION
Perform the reproduction test as per the following procedure for each unit.
1. Turn the ignition switch OFF.
2. Disconnect the battery cable from the negative terminal.
3. Disconnect one of the unit connectors of CAN communication system. NOTE:
ECM and IPDM E/R have a termination circuit. Check other units first.
4. Connect the battery cable to the negative terminal. Check if the symptoms described in the “Symptom
(Results from interview with customer)” are reproduced.
NOTE:
Although unit-related error symptoms occur, do not confuse them with other symptoms.
Inspection result
Reproduced>>Connect the connector. Check other units as per the above procedure.
Non-reproduced>>Replace the unit whose connector was disconnected.
Revision: April 20092010 QX56
Page 2769 of 4210
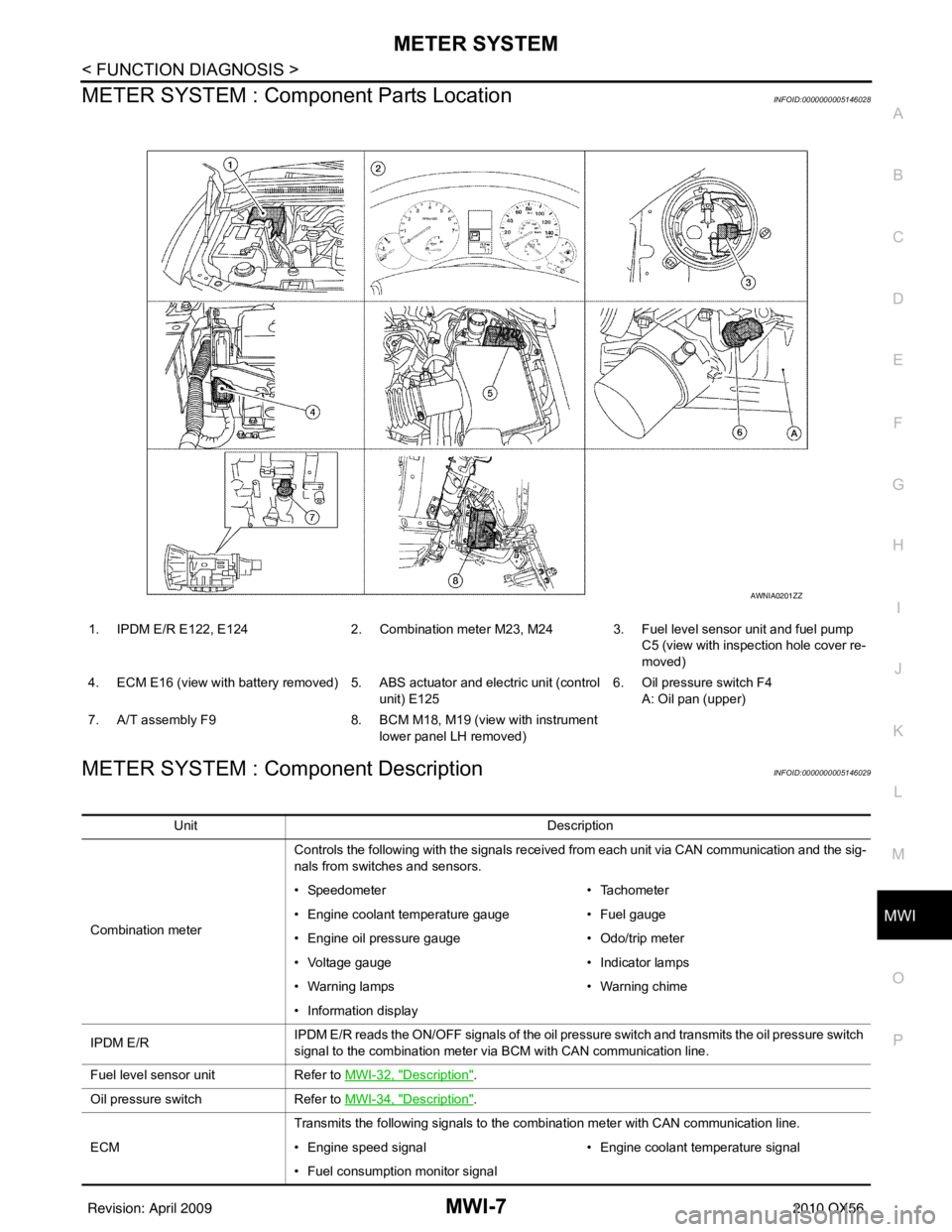
MWI
METER SYSTEMMWI-7
< FUNCTION DIAGNOSIS >
C
DE
F
G H
I
J
K L
M B A
O P
METER SYSTEM : Com ponent Parts LocationINFOID:0000000005146028
METER SYSTEM : Component DescriptionINFOID:0000000005146029
1. IPDM E/R E122, E124 2. Combination meter M23, M24 3. Fuel level sensor unit and fuel pump
C5 (view with inspection hole cover re-
moved)
4. ECM E16 (view with battery removed) 5. ABS actuator and electric unit (control unit) E1256. Oil pressure switch F4
A: Oil pan (upper)
7. A/T assembly F9 8. BCM M18, M19 (view with instrument
lower panel LH removed)
AWNIA0201ZZ
Unit Description
Combination meter Controls the following with the signals received from each unit via CAN communication and the sig-
nals from switches and sensors.
• Speedometer
• Tachometer
• Engine coolant temperature gauge • Fuel gauge
• Engine oil pressure gauge • Odo/trip meter
• Voltage gauge • Indicator lamps
• Warning lamps • Warning chime
• Information display
IPDM E/R IPDM E/R reads the ON/OFF signals of the oil pressure switch and transmits the oil pressure switch
signal to the combination meter via BCM with CAN communication line.
Fuel level sensor unit Refer to MWI-32, "
Description".
Oil pressure switch Refer to MWI-34, "
Description".
ECM Transmits the following signals to the combination meter with CAN communication line.
• Engine speed signal
• Engine coolant temperature signal
• Fuel consumption monitor signal
Revision: April 20092010 QX56
Page 2771 of 4210
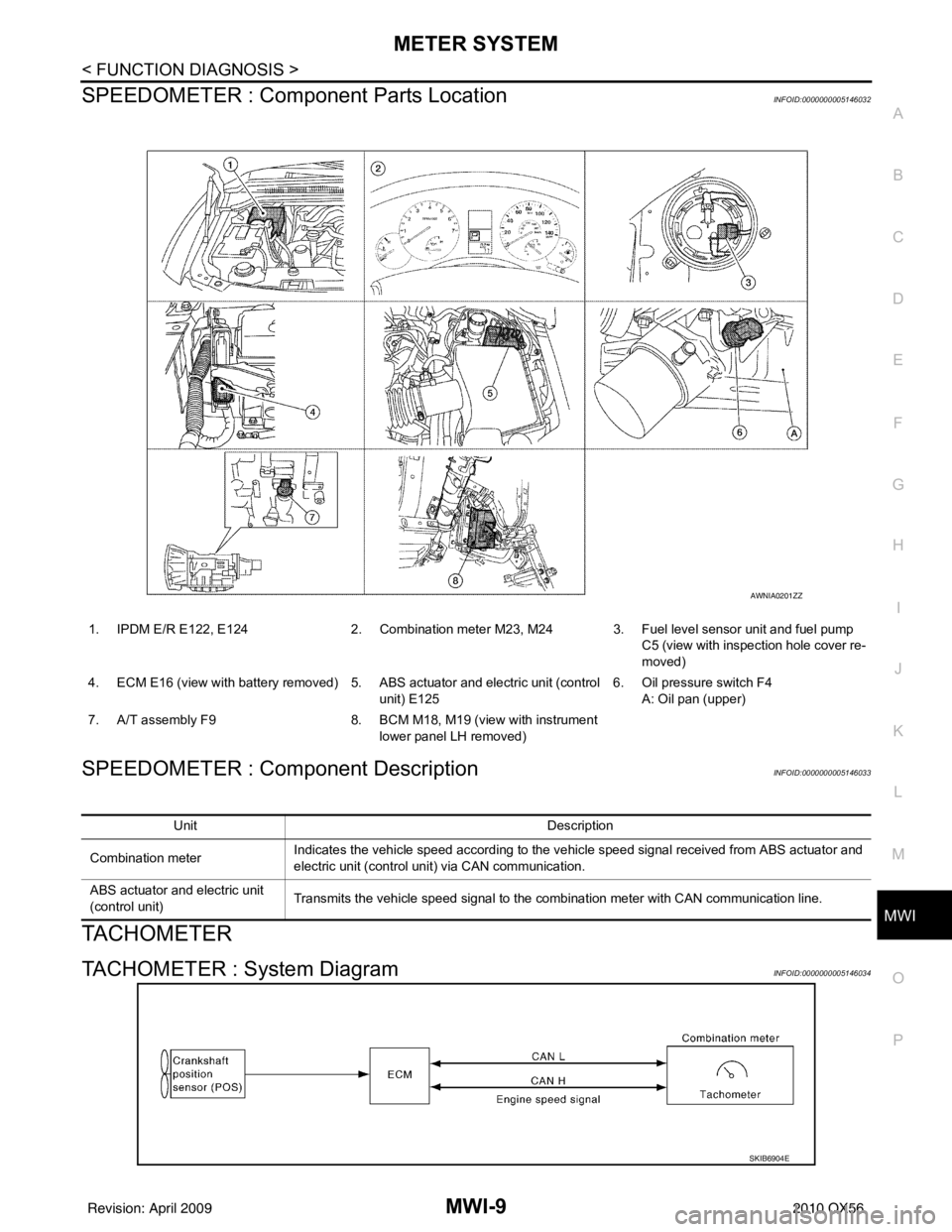
MWI
METER SYSTEMMWI-9
< FUNCTION DIAGNOSIS >
C
DE
F
G H
I
J
K L
M B A
O P
SPEEDOMETER : Compone nt Parts LocationINFOID:0000000005146032
SPEEDOMETER : Component DescriptionINFOID:0000000005146033
TACHOMETER
TACHOMETER : System DiagramINFOID:0000000005146034
1. IPDM E/R E122, E124 2. Combination meter M23, M24 3. Fuel level sensor unit and fuel pump
C5 (view with inspection hole cover re-
moved)
4. ECM E16 (view with battery removed) 5. ABS actuator and electric unit (control unit) E1256. Oil pressure switch F4
A: Oil pan (upper)
7. A/T assembly F9 8. BCM M18, M19 (view with instrument
lower panel LH removed)
AWNIA0201ZZ
Unit Description
Combination meter Indicates the vehicle speed according to the vehicle speed signal received from ABS actuator and
electric unit (control unit) via CAN communication.
ABS actuator and electric unit
(control unit) Transmits the vehicle speed signal to the combination meter with CAN communication line.
SKIB6904E
Revision: April 20092010 QX56
Page 2772 of 4210
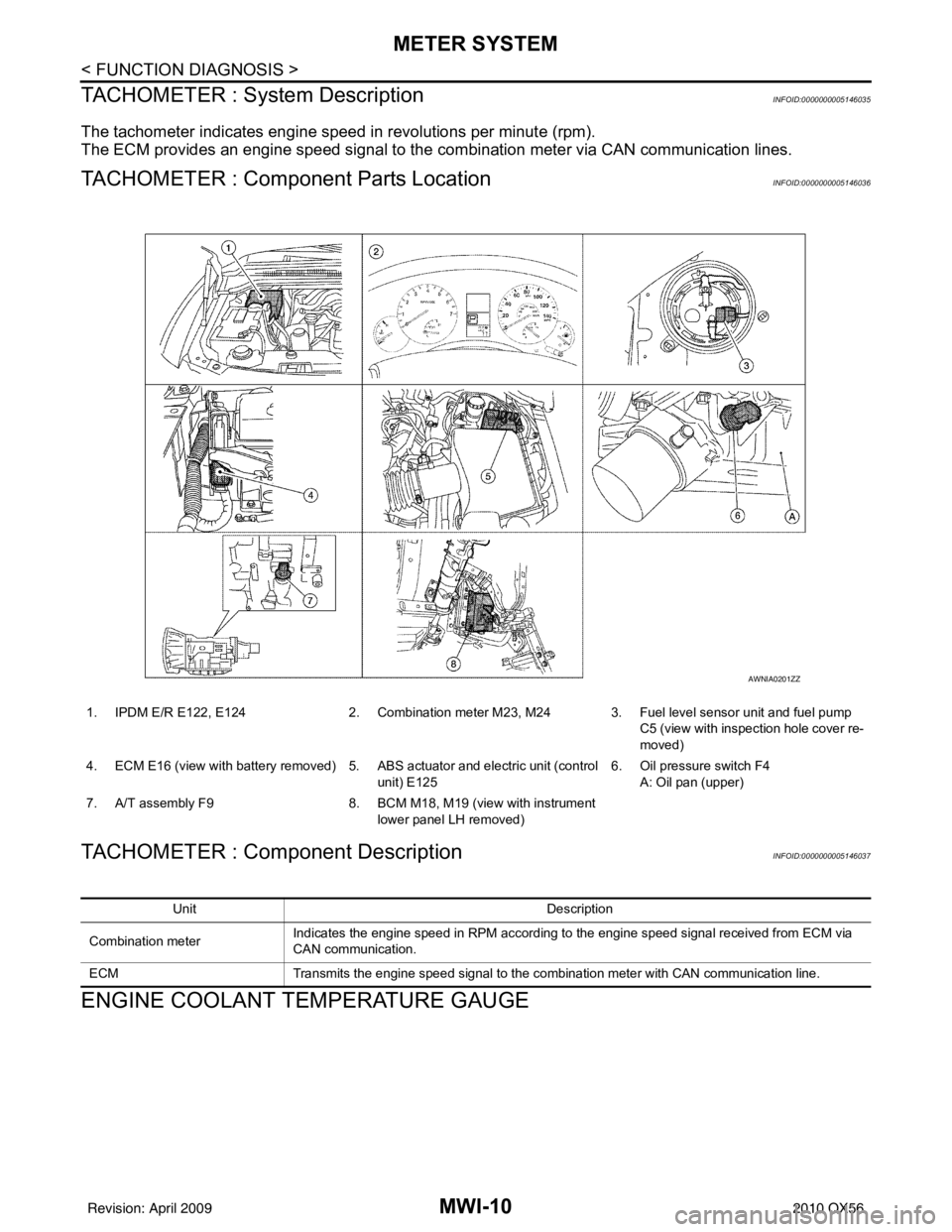
MWI-10
< FUNCTION DIAGNOSIS >
METER SYSTEM
TACHOMETER : System Description
INFOID:0000000005146035
The tachometer indicates engine speed in revolutions per minute (rpm).
The ECM provides an engine speed signal to the co mbination meter via CAN communication lines.
TACHOMETER : Component Parts LocationINFOID:0000000005146036
TACHOMETER : Component DescriptionINFOID:0000000005146037
ENGINE COOLANT TEMPERATURE GAUGE
1. IPDM E/R E122, E1242. Combination meter M23, M24 3. Fuel level sensor unit and fuel pump
C5 (view with inspection hole cover re-
moved)
4. ECM E16 (view with battery removed) 5. ABS actuator and electric unit (control
unit) E125 6. Oil pressure switch F4
A: Oil pan (upper)
7. A/T assembly F9 8. BCM M18, M19 (view with instrument
lower panel LH removed)
AWNIA0201ZZ
Unit Description
Combination meter Indicates the engine speed in RPM according to the engine speed signal received from ECM via
CAN communication.
ECM Transmits the engine speed signal to the combination meter with CAN communication line.
Revision: April 20092010 QX56
Page 2773 of 4210
MWI
METER SYSTEMMWI-11
< FUNCTION DIAGNOSIS >
C
DE
F
G H
I
J
K L
M B A
O P
ENGINE COOLANT TEMPERATURE GAUGE : System DiagramINFOID:0000000005146038
ENGINE COOLANT TEMPERATURE GAUGE : System DescriptionINFOID:0000000005146039
The engine coolant temperature gauge indicates the engine coolant temperature.
The ECM provides an engine coolant temperature signal to the combination meter via CAN communication
lines.
ENGINE COOLANT TEMPERATURE GA UGE : Component Parts Location
INFOID:0000000005146040
SKIB6905E
1. IPDM E/R E122, E124 2. Combination meter M23, M24 3. Fuel level sensor unit and fuel pump
C5 (view with inspection hole cover re-
moved)
4. ECM E16 (view with battery removed) 5. ABS actuator and electric unit (control unit) E1256. Oil pressure switch F4
A: Oil pan (upper)
7. A/T assembly F9 8. BCM M18, M19 (view with instrument
lower panel LH removed)
AWNIA0201ZZ
Revision: April 20092010 QX56