Page 105 of 128
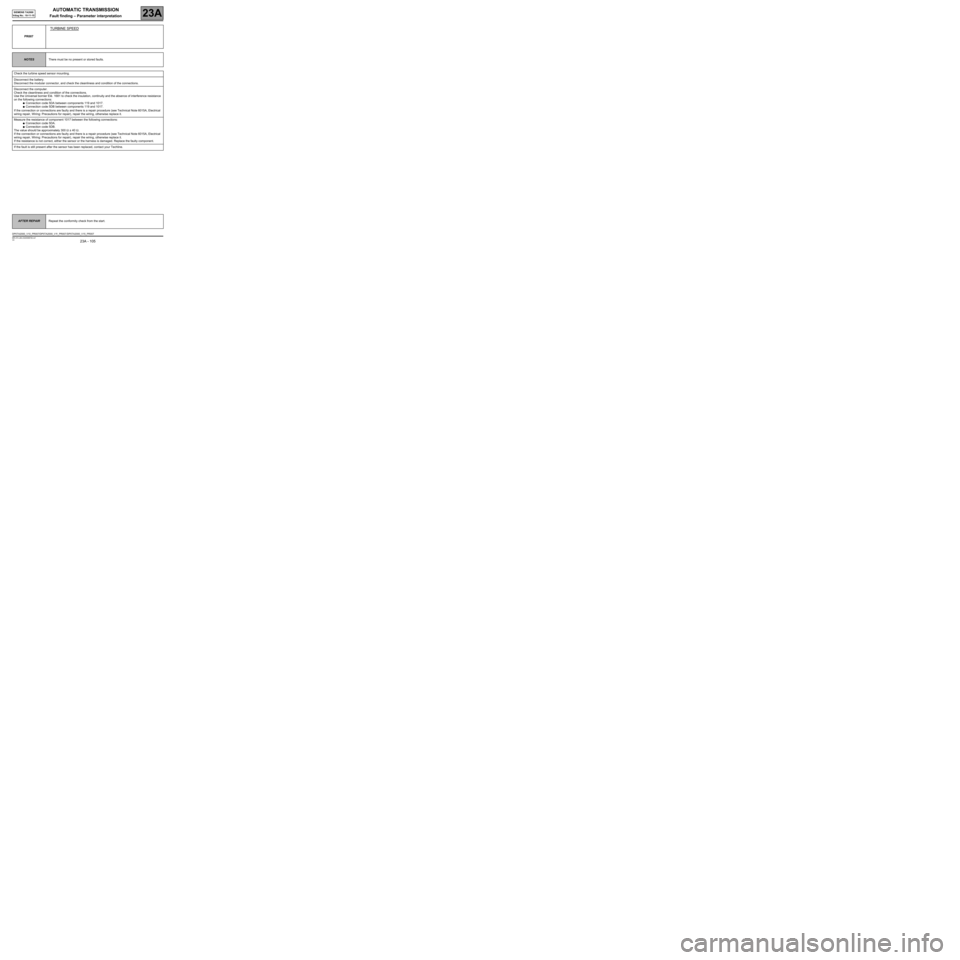
AUTOMATIC TRANSMISSION
Fault finding – Parameter interpretation23A
23A - 105V4 MR-372-J84-23A050$726.mif
SIEMENS TA2000
Vdiag No.: 10-11-15
PR007
TURBINE SPEED
NOTESThere must be no present or stored faults.
Check the turbine speed sensor mounting.
Disconnect the battery.
Disconnect the modular connector, and check the cleanliness and condition of the connections.
Disconnect the computer.
Check the cleanliness and condition of the connections.
Use the Universal bornier Elé. 1681 to check the insulation, continuity and the absence of interference resistance
on the following connections:
●Connection code 5DA between components 119 and 1017.
●Connection code 5DB between components 119 and 1017.
If the connection or connections are faulty and there is a repair procedure (see Technical Note 6015A, Electrical
wiring repair, Wiring: Precautions for repair), repair the wiring, otherwise replace it.
Measure the resistance of component 1017 between the following connections:
●Connection code 5DA.
●Connection code 5DB.
The value should be approximately 300 Ω ± 40 Ω.
If the connection or connections are faulty and there is a repair procedure (see Technical Note 6015A, Electrical
wiring repair, Wiring: Precautions for repair), repair the wiring, otherwise replace it.
If the resistance is not correct, either the sensor or the harness is damaged. Replace the faulty component.
If the fault is still present after the sensor has been replaced, contact your Techline.
AFTER REPAIRRepeat the conformity check from the start.
DP0TA2000_V10_PR007/DP0TA2000_V11_PR007 /DP0TA2000_V15_PR007
Page 106 of 128
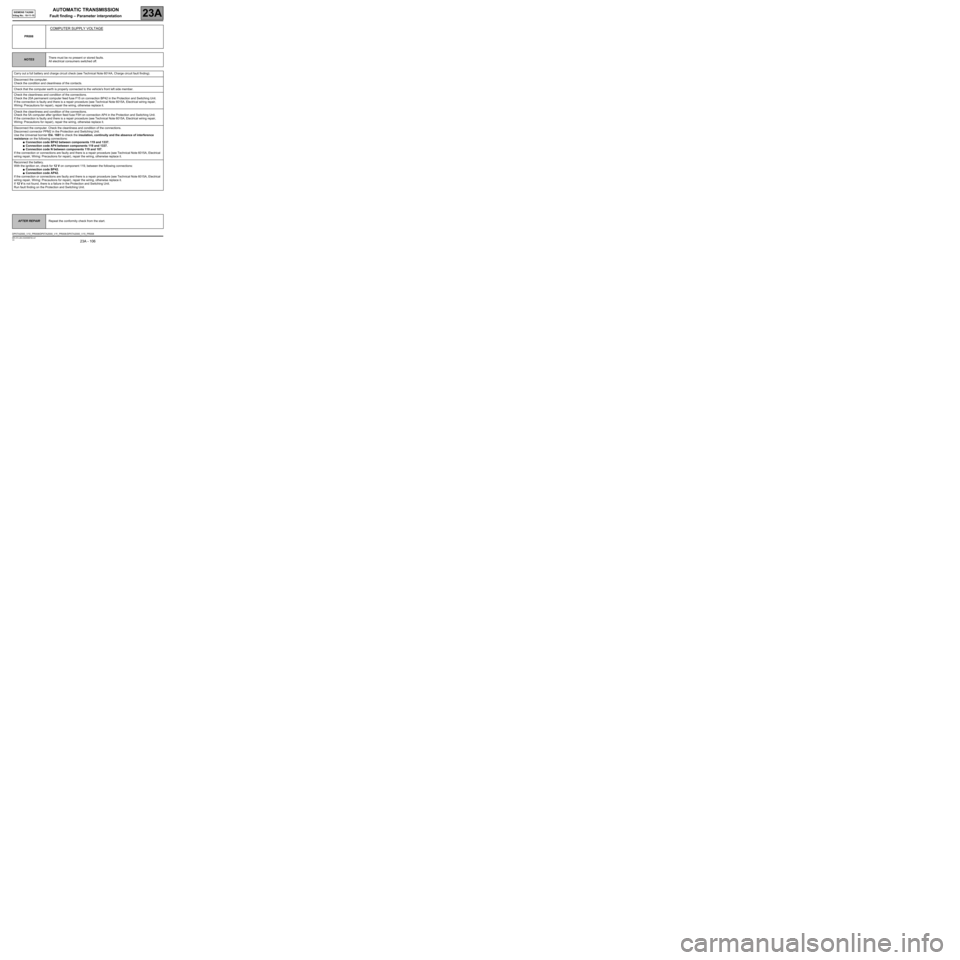
AUTOMATIC TRANSMISSION
Fault finding – Parameter interpretation23A
23A - 106V4 MR-372-J84-23A050$726.mif
SIEMENS TA2000
Vdiag No.: 10-11-15
PR008
COMPUTER SUPPLY VOLTAGE
NOTESThere must be no present or stored faults.
All electrical consumers switched off.
Carry out a full battery and charge circuit check (see Technical Note 6014A, Charge circuit fault finding).
Disconnect the computer.
Check the condition and cleanliness of the contacts.
Check that the computer earth is properly connected to the vehicle's front left side member.
Check the cleanliness and condition of the connections.
Check the 20A permanent computer feed fuse F15 on connection BP42 in the Protection and Switching Unit.
If the connection is faulty and there is a repair procedure (see Technical Note 6015A, Electrical wiring repair,
Wiring: Precautions for repair), repair the wiring, otherwise replace it.
Check the cleanliness and condition of the connections.
Check the 5A computer after ignition feed fuse F5H on connection AP4 in the Protection and Switching Unit.
If the connection is faulty and there is a repair procedure (see Technical Note 6015A, Electrical wiring repair,
Wiring: Precautions for repair), repair the wiring, otherwise replace it.
Disconnect the computer. Check the cleanliness and condition of the connections.
Disconnect connector PPM2 in the Protection and Switching Unit.
Use the Universal bornier Elé. 1681 to check the insulation, continuity and the absence of interference
resistance on the following connections:
●Connection code BP42 between components 119 and 1337.
●Connection code AP4 between components 119 and 1337.
●Connection code N between components 119 and 107.
If the connection or connections are faulty and there is a repair procedure (see Technical Note 6015A, Electrical
wiring repair, Wiring: Precautions for repair), repair the wiring, otherwise replace it.
Reconnect the battery.
With the ignition on, check for 12 V on component 119, between the following connections:
●Connection code BP42.
●Connection code AP42.
If the connection or connections are faulty and there is a repair procedure (see Technical Note 6015A, Electrical
wiring repair, Wiring: Precautions for repair), repair the wiring, otherwise replace it.
If 12 V is not found, there is a failure in the Protection and Switching Unit.
Run fault finding on the Protection and Switching Unit.
AFTER REPAIRRepeat the conformity check from the start.
DP0TA2000_V10_PR008/DP0TA2000_V11_PR008 /DP0TA2000_V15_PR008
Page 107 of 128
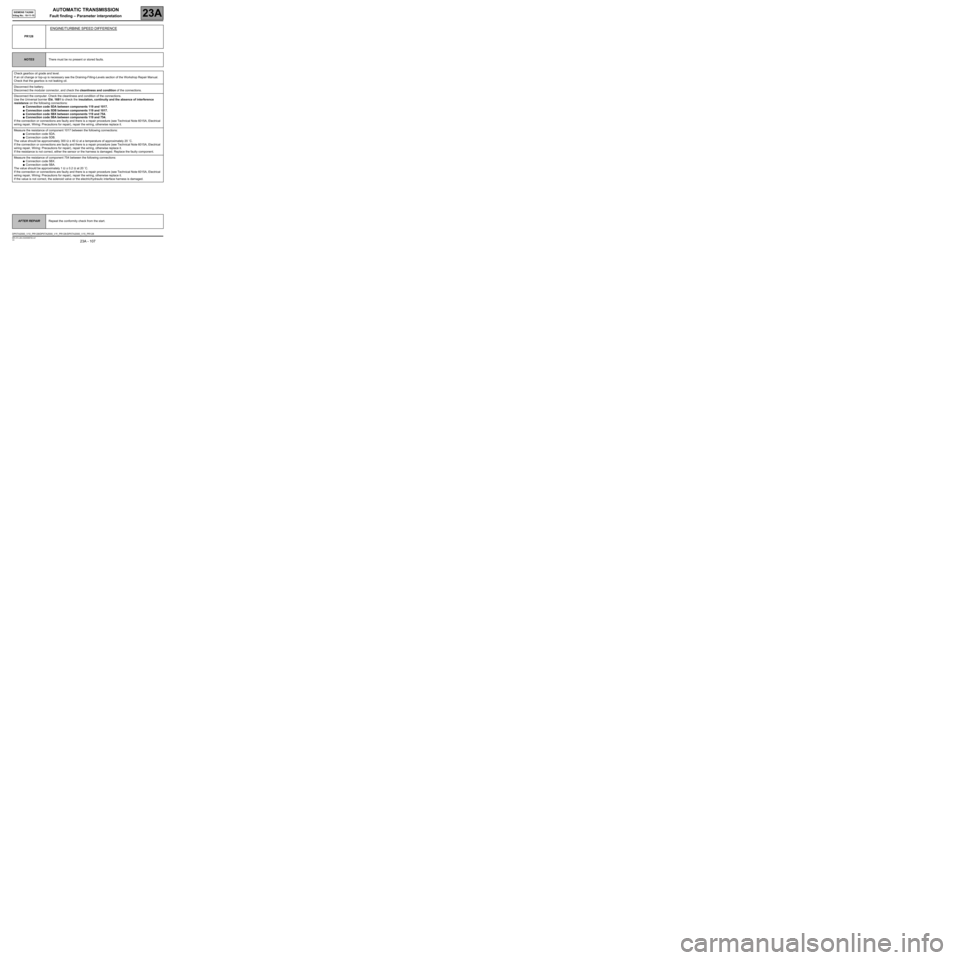
AUTOMATIC TRANSMISSION
Fault finding – Parameter interpretation23A
23A - 107V4 MR-372-J84-23A050$726.mif
SIEMENS TA2000
Vdiag No.: 10-11-15
PR128
ENGINE/TURBINE SPEED DIFFERENCE
NOTESThere must be no present or stored faults.
Check gearbox oil grade and level.
If an oil change or top-up is necessary see the Draining-Filling-Levels section of the Workshop Repair Manual.
Check that the gearbox is not leaking oil.
Disconnect the battery.
Disconnect the modular connector, and check the cleanliness and condition of the connections.
Disconnect the computer. Check the cleanliness and condition of the connections.
Use the Universal bornier Elé. 1681 to check the insulation, continuity and the absence of interference
resistance on the following connections:
●Connection code 5DA between components 119 and 1017.
●Connection code 5DB between components 119 and 1017.
●Connection code 5BX between components 119 and 754.
●Connection code 5BA between components 119 and 754.
If the connection or connections are faulty and there is a repair procedure (see Technical Note 6015A, Electrical
wiring repair, Wiring: Precautions for repair), repair the wiring, otherwise replace it.
Measure the resistance of component 1017 between the following connections:
●Connection code 5DA.
●Connection code 5DB.
The value should be approximately 300 Ω ± 40 Ω at a temperature of approximately 20 ˚C.
If the connection or connections are faulty and there is a repair procedure (see Technical Note 6015A, Electrical
wiring repair, Wiring: Precautions for repair), repair the wiring, otherwise replace it.
If the resistance is not correct, either the sensor or the harness is damaged. Replace the faulty component.
Measure the resistance of component 754 between the following connections:
●Connection code 5BX.
●Connection code 5BA.
The value should be approximately 1 Ω ± 0.2 Ω at 20 ˚C.
If the connection or connections are faulty and there is a repair procedure (see Technical Note 6015A, Electrical
wiring repair, Wiring: Precautions for repair), repair the wiring, otherwise replace it.
If the value is not correct, the solenoid valve or the electric/hydraulic interface harness is damaged.
AFTER REPAIRRepeat the conformity check from the start.
DP0TA2000_V10_PR128/DP0TA2000_V11_PR128 /DP0TA2000_V15_PR128
Page 108 of 128
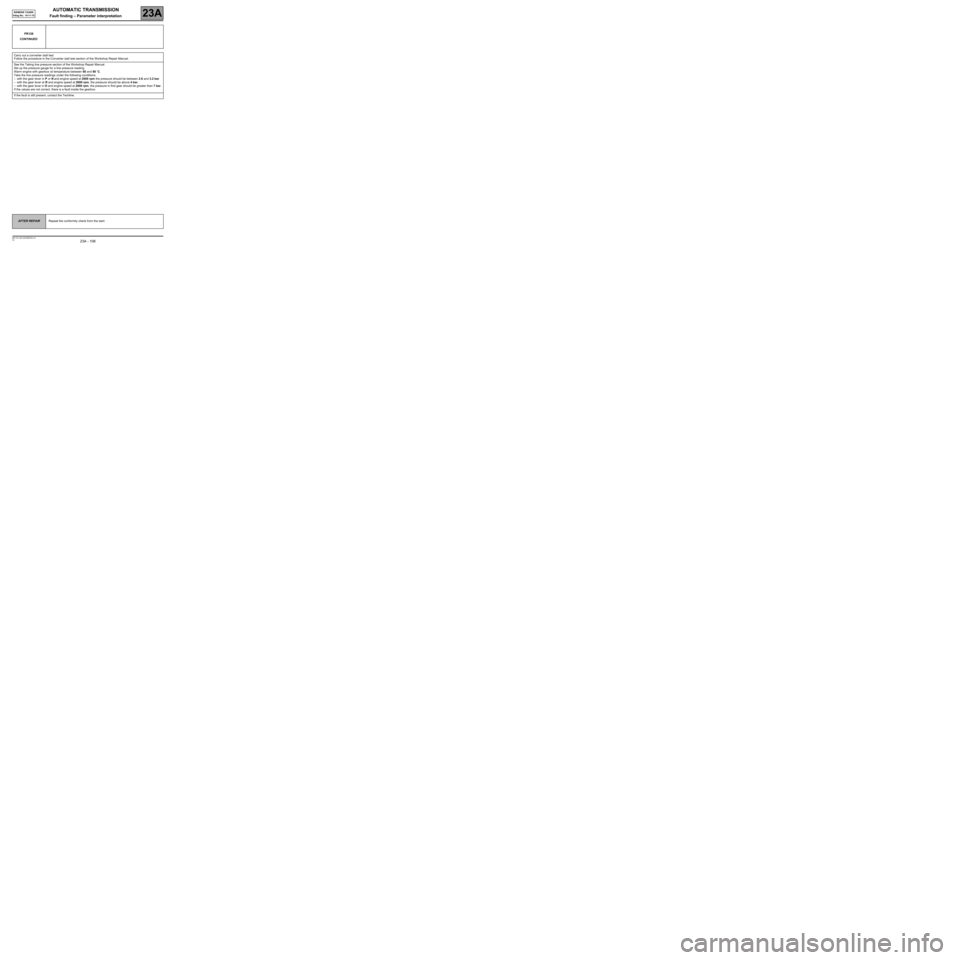
AUTOMATIC TRANSMISSION
Fault finding – Parameter interpretation23A
23A - 108V4 MR-372-J84-23A050$726.mif
SIEMENS TA2000
Vdiag No.: 10-11-15
PR128
CONTINUED
Carry out a converter stall test.
Follow the procedure in the Converter stall test section of the Workshop Repair Manual.
See the Taking line pressure section of the Workshop Repair Manual.
Set up the pressure gauge for a line pressure reading.
Warm engine with gearbox oil temperature between 60 and 80 ˚C.
Take the line pressure readings under the following conditions:
–with the gear lever in P or N and engine speed at 2000 rpm the pressure should be between 2.6 and 3.2 bar.
–with the gear lever at R and engine speed at 2000 rpm, the pressure should be above 4 bar.
–with the gear lever in D and engine speed at 2000 rpm, the pressure in first gear should be greater than 7 bar.
If the values are not correct, there is a fault inside the gearbox.
If the fault is still present, contact the Techline.
AFTER REPAIRRepeat the conformity check from the start.
Page 109 of 128
AUTOMATIC TRANSMISSION
Fault finding – Parameter interpretation23A
23A - 109V4 MR-372-J84-23A050$726.mif
SIEMENS TA2000
Vdiag No.: 10-11-15
PR135
STANDARD PEDAL POSITION
NOTESThere must be no present or stored faults.
Run a multiplex network test (see 88B, Multiplex).
If parameter PR135 Standard pedal position is absent, refer to the interpretation of the parameter (see 17B,
Petrol injection or 13B, Diesel injection).
AFTER REPAIRRepeat the conformity check from the start.
DP0TA2000_V10_PR135/DP0TA2000_V11_PR135 /DP0TA2000_V15_PR135
Page 110 of 128
AUTOMATIC TRANSMISSION
Fault finding – Parameter interpretation23A
23A - 110V4 MR-372-J84-23A050$726.mif
SIEMENS TA2000
Vdiag No.: 10-11-15
PR138
REFERENCE PRESSURE
NOTESThere must be no present or stored faults.
The reference pressure is determined by the automatic transmission computer.
Check the pressure setting on the diagnostic tool:
–engine not running: pressure reading 21 bar.
–engine at idle speed (~ 700 rpm) and selector lever at D or R: pressure reading ~ 2.7 bar.
–engine speed ~ 1400 rpm and gear lever at D or R: pressure reading ~ 8.9 bar.
AFTER REPAIRRepeat the conformity check from the start.
DP0TA2000_V10_PR138/DP0TA2000_V11_PR138 /DP0TA2000_V15_PR138
Page 111 of 128
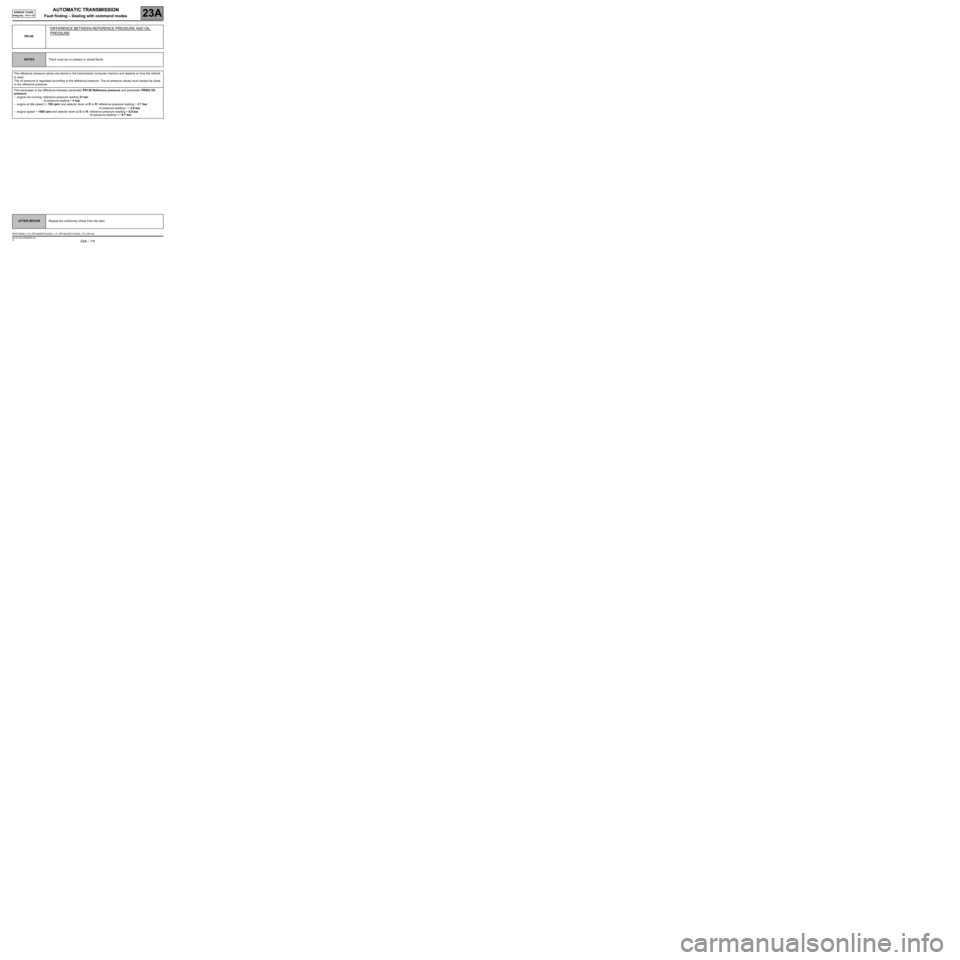
AUTOMATIC TRANSMISSION
Fault finding – Dealing with command modes23A
23A - 111V4 MR-372-J84-23A050$792.mif
SIEMENS TA2000
Vdiag No.: 10-11-15AUTOMATIC TRANSMISSION
Fault finding – Dealing with command modes
PR146
DIFFERENCE BETWEEN REFERENCE PRESSURE AND OIL
PRESSURE
NOTESThere must be no present or stored faults.
The reference pressure values are stored in the transmission computer memory and depend on how the vehicle
is used.
The oil pressure is regulated according to the reference pressure. The oil pressure values must always be close
to the reference pressure.
This parameter is the difference between parameter PR138 Reference pressure and parameter PR003 Oil
pressure.
–engine not running: reference pressure reading 21 bar.
oil pressure reading = 0 bar.
–engine at idle speed (~ 700 rpm) and selector lever at D or R: reference pressure reading ~ 2.7 bar.
oil pressure reading = ~ 2.6 bar.
–engine speed ~ 1400 rpm and selector lever at D or R: reference pressure reading ~ 8.9 bar.
oil pressure reading = ~ 8.7 bar.
AFTER REPAIRRepeat the conformity check from the start.
DP0TA2000_V10_PR146/DP0TA2000_V11_PR146 /DP0TA2000_V15_PR146
MR-372-J84-23A050$792.mif
Page 112 of 128

AUTOMATIC TRANSMISSION
Fault finding – Dealing with command modes23A
23A - 112V4 MR-372-J84-23A050$792.mif
SIEMENS TA2000
Vdiag No.: 10-11-15
COMMANDS AND CLEARING:
Before using these clearing commands, engine and vehicle speeds must be zero and the selector lever must be in
position P or N.
AC024 Sequential control of the actuators
This command activates sequence solenoid valves EVS1 to EVS6 simultaneously to check that they
operate correctly.
RZ004 Fault memory
This command clears present and stored faults from the automatic transmission computer.
RZ005 Self-adapting programs
This command enables the self-adapting programming to be cleared from the automatic transmission
computer, after reprogramming or after gearbox components have been replaced.
After running this command, carry out a road test with the vehicle before returning it to the customer.
This is because the automatic gearbox may malfunction during the time taken for the self-adapting
programs to reinstall.
RZ006 Converter lockup self-adapting program
This command clears the self-adapting programs associated with the converter.
After running this command, carry out a road test with the vehicle before returning it to the customer.
This is because, after the command, the automatic gearbox may malfunction during the time taken
for the self-adapting programs associated with the converter to reinstall.
RZ007 OBD memory
This command clears the computer's OBD memory.
AFTER REPAIRRepeat the conformity check from the start.