Page 4187 of 4647
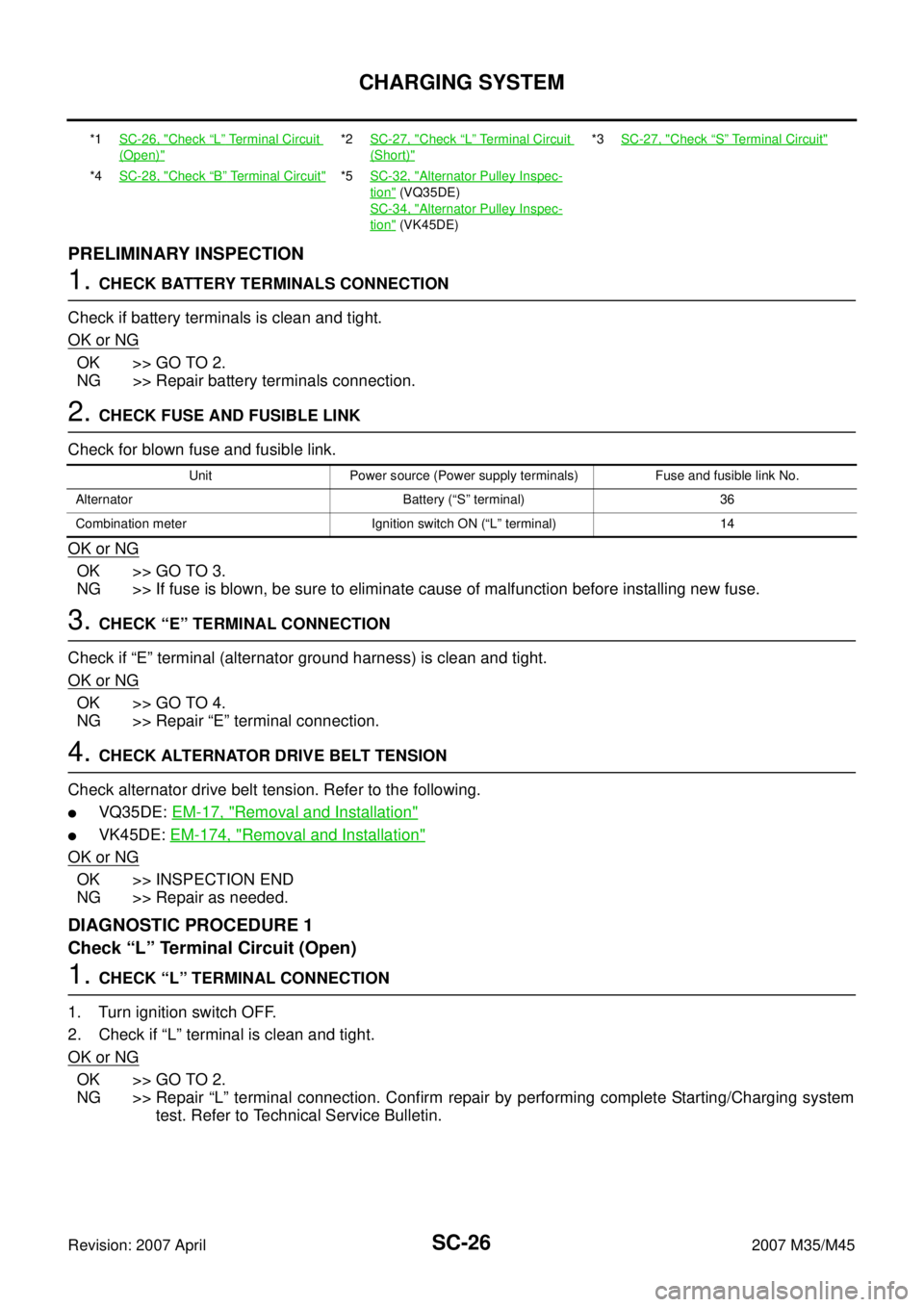
SC-26
CHARGING SYSTEM
Revision: 2007 April2007 M35/M45
PRELIMINARY INSPECTION
1. CHECK BATTERY TERMINALS CONNECTION
Check if battery terminals is clean and tight.
OK or NG
OK >> GO TO 2.
NG >> Repair battery terminals connection.
2. CHECK FUSE AND FUSIBLE LINK
Check for blown fuse and fusible link.
OK or NG
OK >> GO TO 3.
NG >> If fuse is blown, be sure to eliminate cause of malfunction before installing new fuse.
3. CHECK “E” TERMINAL CONNECTION
Check if “E” terminal (alternator ground harness) is clean and tight.
OK or NG
OK >> GO TO 4.
NG >> Repair “E” terminal connection.
4. CHECK ALTERNATOR DRIVE BELT TENSION
Check alternator drive belt tension. Refer to the following.
VQ35DE: EM-17, "Removal and Installation"
VK45DE: EM-174, "Removal and Installation"
OK or NG
OK >> INSPECTION END
NG >> Repair as needed.
DIAGNOSTIC PROCEDURE 1
Check “L” Terminal Circuit (Open)
1. CHECK “L” TERMINAL CONNECTION
1. Turn ignition switch OFF.
2. Check if “L” terminal is clean and tight.
OK or NG
OK >> GO TO 2.
NG >> Repair “L” terminal connection. Confirm repair by performing complete Starting/Charging system
test. Refer to Technical Service Bulletin.
*1SC-26, "Check “L” Terminal Circuit
(Open)"
*2SC-27, "Check “L” Terminal Circuit
(Short)"
*3SC-27, "Check “S” Terminal Circuit"
*4SC-28, "Check “B” Terminal Circuit"*5SC-32, "Alternator Pulley Inspec-
tion" (VQ35DE)
SC-34, "
Alternator Pulley Inspec-
tion" (VK45DE)
Unit Power source (Power supply terminals) Fuse and fusible link No.
Alternator Battery (“S” terminal) 36
Combination meter Ignition switch ON (“L” terminal) 14
Page 4188 of 4647
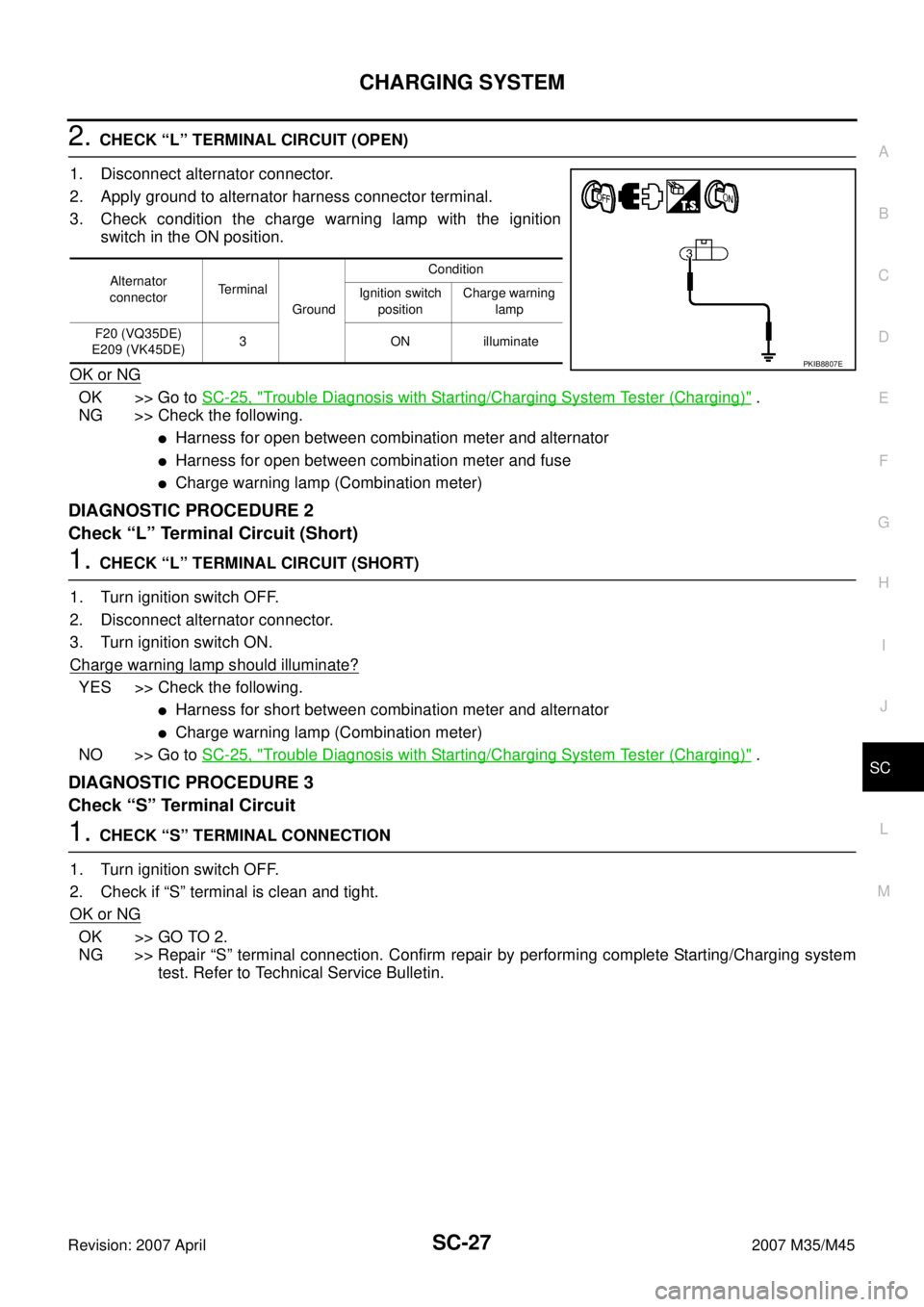
CHARGING SYSTEM
SC-27
C
D
E
F
G
H
I
J
L
MA
B
SC
Revision: 2007 April2007 M35/M45
2. CHECK “L” TERMINAL CIRCUIT (OPEN)
1. Disconnect alternator connector.
2. Apply ground to alternator harness connector terminal.
3. Check condition the charge warning lamp with the ignition
switch in the ON position.
OK or NG
OK >> Go to SC-25, "Trouble Diagnosis with Starting/Charging System Tester (Charging)" .
NG >> Check the following.
Harness for open between combination meter and alternator
Harness for open between combination meter and fuse
Charge warning lamp (Combination meter)
DIAGNOSTIC PROCEDURE 2
Check “L” Terminal Circuit (Short)
1. CHECK “L” TERMINAL CIRCUIT (SHORT)
1. Turn ignition switch OFF.
2. Disconnect alternator connector.
3. Turn ignition switch ON.
Charge warning lamp should illuminate?
YES >> Check the following.
Harness for short between combination meter and alternator
Charge warning lamp (Combination meter)
NO >> Go to SC-25, "
Trouble Diagnosis with Starting/Charging System Tester (Charging)" .
DIAGNOSTIC PROCEDURE 3
Check “S” Terminal Circuit
1. CHECK “S” TERMINAL CONNECTION
1. Turn ignition switch OFF.
2. Check if “S” terminal is clean and tight.
OK or NG
OK >> GO TO 2.
NG >> Repair “S” terminal connection. Confirm repair by performing complete Starting/Charging system
test. Refer to Technical Service Bulletin.
Alternator
connectorTerminal
GroundCondition
Ignition switch
positionCharge warning
lamp
F20 (VQ35DE)
E209 (VK45DE)3 ON illuminate
PKIB8807E
Page 4189 of 4647
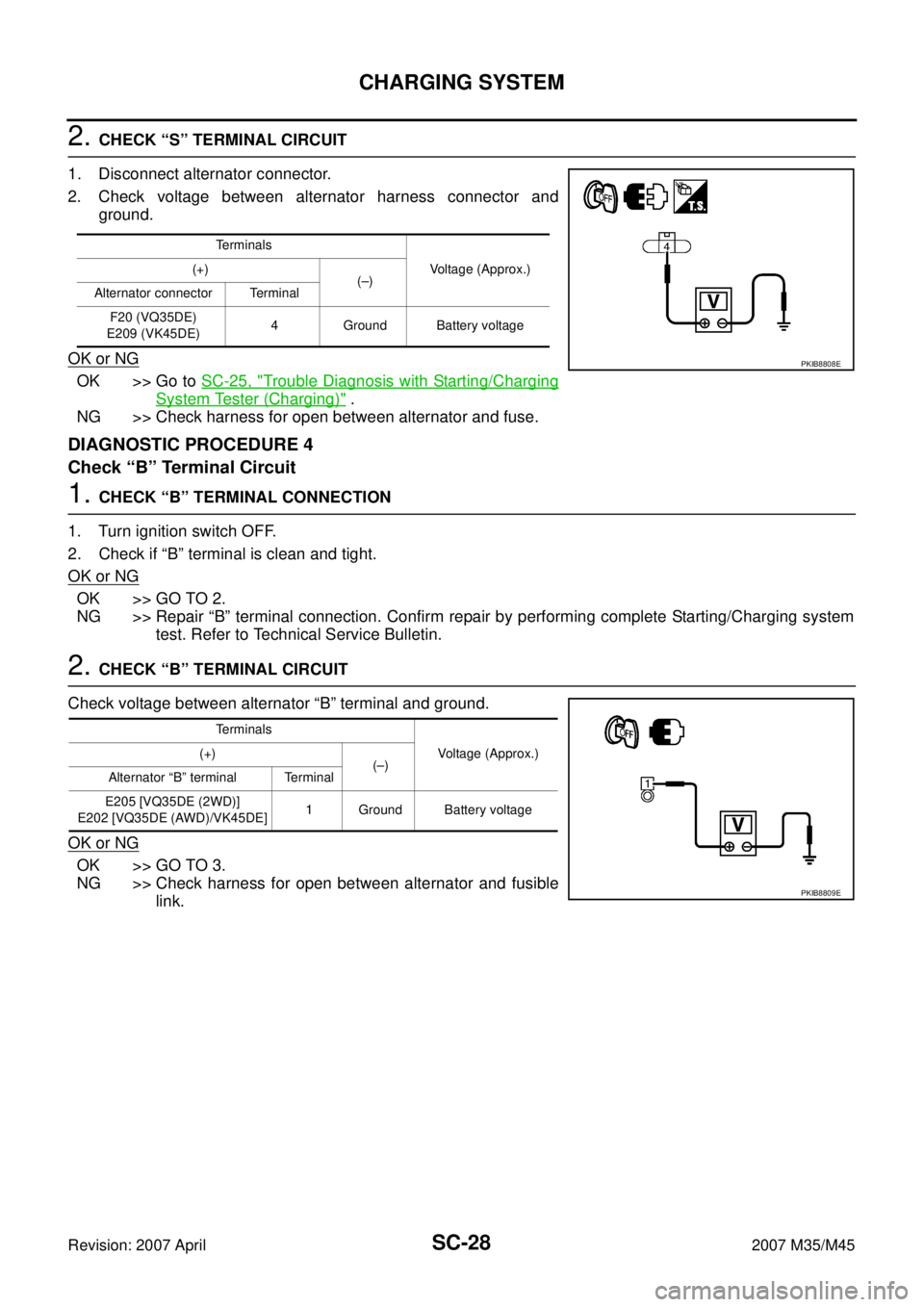
SC-28
CHARGING SYSTEM
Revision: 2007 April2007 M35/M45
2. CHECK “S” TERMINAL CIRCUIT
1. Disconnect alternator connector.
2. Check voltage between alternator harness connector and
ground.
OK or NG
OK >> Go to SC-25, "Trouble Diagnosis with Starting/Charging
System Tester (Charging)" .
NG >> Check harness for open between alternator and fuse.
DIAGNOSTIC PROCEDURE 4
Check “B” Terminal Circuit
1. CHECK “B” TERMINAL CONNECTION
1. Turn ignition switch OFF.
2. Check if “B” terminal is clean and tight.
OK or NG
OK >> GO TO 2.
NG >> Repair “B” terminal connection. Confirm repair by performing complete Starting/Charging system
test. Refer to Technical Service Bulletin.
2. CHECK “B” TERMINAL CIRCUIT
Check voltage between alternator “B” terminal and ground.
OK or NG
OK >> GO TO 3.
NG >> Check harness for open between alternator and fusible
link.
Terminals
Voltage (Approx.) (+)
(–)
Alternator connector Terminal
F20 (VQ35DE)
E209 (VK45DE)4 Ground Battery voltage
PKIB8808E
Terminals
Voltage (Approx.) (+)
(–)
Alternator “B” terminal Terminal
E205 [VQ35DE (2WD)]
E202 [VQ35DE (AWD)/VK45DE]1 Ground Battery voltage
PKIB8809E
Page 4210 of 4647
AUTOMATIC DRIVE POSITIONER
SE-11
C
D
E
F
G
H
J
K
L
MA
B
SE
Revision: 2007 April2007 M35/M45
AUTOMATIC DRIVE POSITIONERPFP:28491
Component Parts And Harness Connector LocationNIS0025Q
PIIB6292E
1. Fuse block (J/B) 2. Fuse and fusible link box 3. BCM M1, M2, M3
(View with the glove box assembly
removed)
4. A. Automatic drive positioner control
unit M6, M7
B. Telescopic motor M45
C. Telescopic sensor M44
D. Tilt sensor M37
E. Tilt motor M36
(View with the driver lower panel
removed)5. A. Front lifting motor B209
B. Rear lifting motor B210
C. Driver seat control unit
B204,B205
D. Sliding motor B2076. Seat memory switch D9
7. A. Lumbar support switch B212
B. Reclining switch B213
C. Sliding/Lifting switch B2138. A. ADP steering switch M46
B. Key slot M14
C. Door mirror control switch M959. Reclining motor B208
Page 4230 of 4647
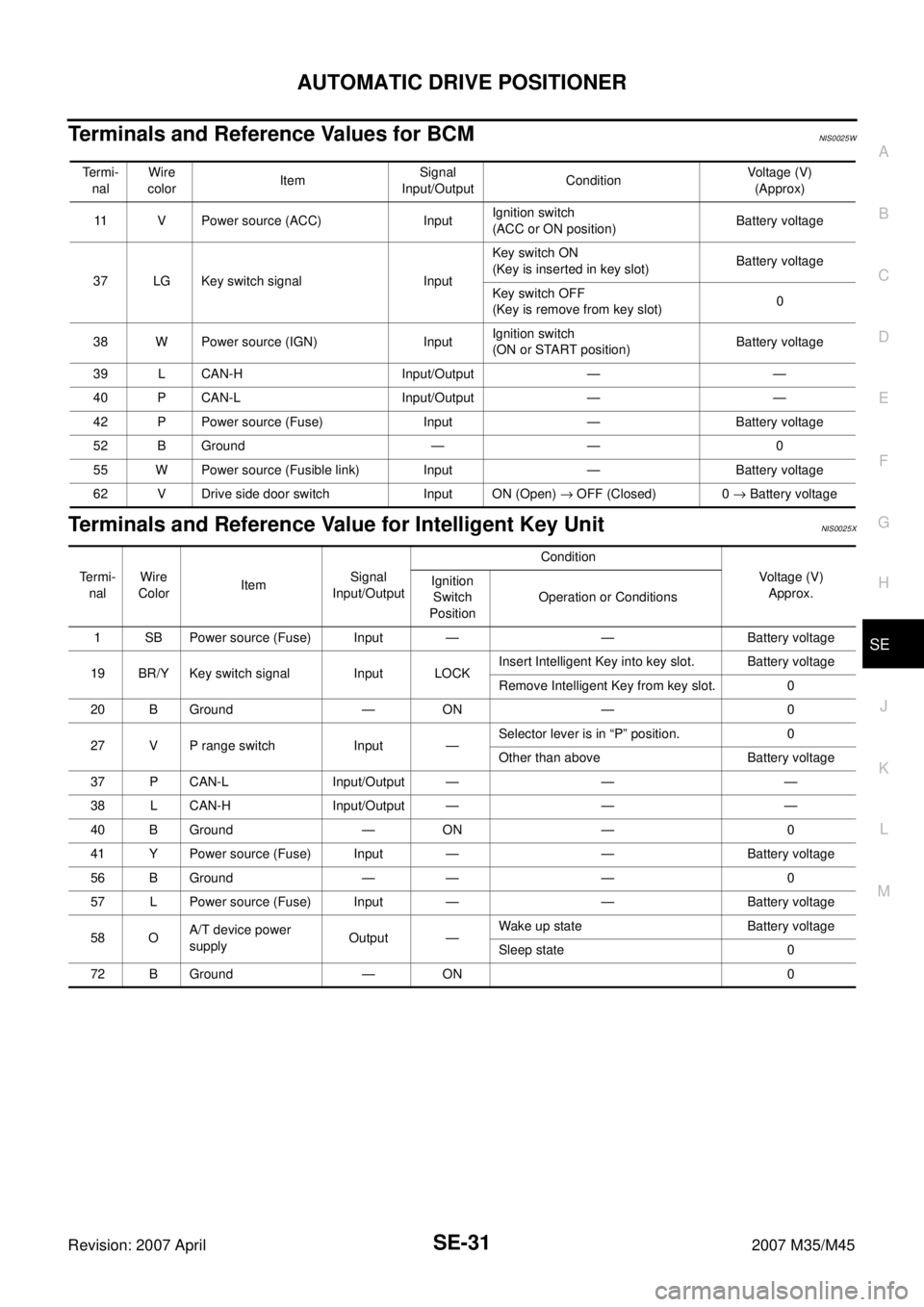
AUTOMATIC DRIVE POSITIONER
SE-31
C
D
E
F
G
H
J
K
L
MA
B
SE
Revision: 2007 April2007 M35/M45
Terminals and Reference Values for BCMNIS0025W
Terminals and Reference Value for Intelligent Key UnitNIS0025X
Te r m i -
nal Wire
colorItemSignal
Input/OutputConditionVoltage (V)
(Approx)
11 V Power source (ACC) InputIgnition switch
(ACC or ON position)Battery voltage
37 LG Key switch signal InputKey switch ON
(Key is inserted in key slot)Battery voltage
Key switch OFF
(Key is remove from key slot)0
38 W Power source (IGN) InputIgnition switch
(ON or START position)Battery voltage
39 L CAN-H Input/Output — —
40 P CAN-L Input/Output — —
42 P Power source (Fuse) Input — Battery voltage
52 B Ground — — 0
55 W Power source (Fusible link) Input — Battery voltage
62 V Drive side door switch Input ON (Open) → OFF (Closed) 0 → Battery voltage
Termi-
nalWire
ColorItemSignal
Input/OutputCondition
Voltage (V)
Approx. Ignition
Switch
PositionOperation or Conditions
1 SB Power source (Fuse) Input — — Battery voltage
19 BR/Y Key switch signal Input LOCKInsert Intelligent Key into key slot. Battery voltage
Remove Intelligent Key from key slot. 0
20 B Ground — ON — 0
27 V P range switch Input —Selector lever is in “P” position. 0
Other than above Battery voltage
37 P CAN-L Input/Output — — —
38 L CAN-H Input/Output — — —
40 B Ground — ON — 0
41 Y Power source (Fuse) Input — — Battery voltage
56 B Ground — — — 0
57 L Power source (Fuse) Input — — Battery voltage
58 OA/T device power
supply Output —Wake up state Battery voltage
Sleep state 0
72 B Ground — ON 0
Page 4232 of 4647
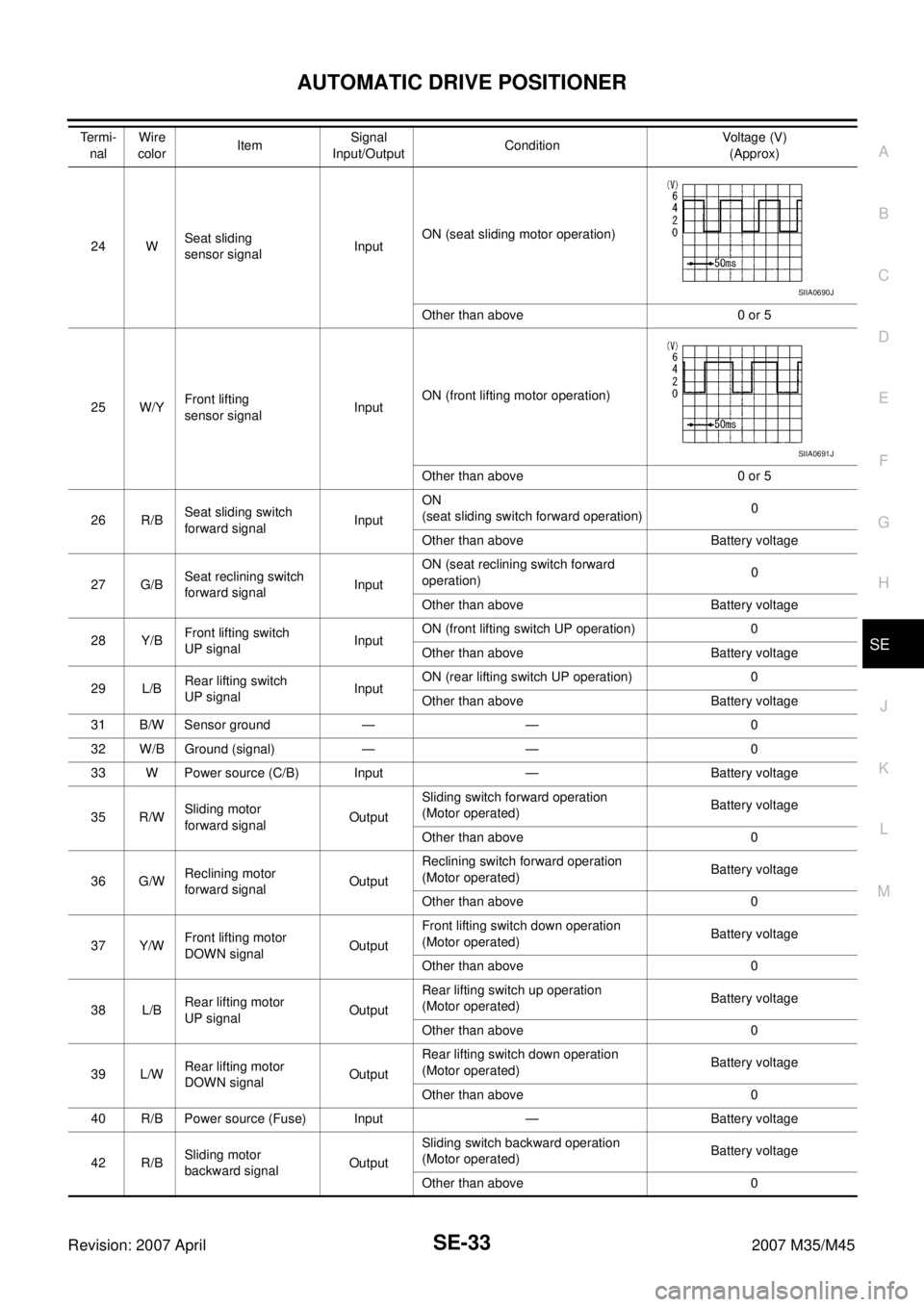
AUTOMATIC DRIVE POSITIONER
SE-33
C
D
E
F
G
H
J
K
L
MA
B
SE
Revision: 2007 April2007 M35/M45
24 WSeat sliding
sensor signalInputON (seat sliding motor operation)
Other than above 0 or 5
25 W/YFront lifting
sensor signalInputON (front lifting motor operation)
Other than above 0 or 5
26 R/BSeat sliding switch
forward signalInputON
(seat sliding switch forward operation)0
Other than above Battery voltage
27 G/BSeat reclining switch
forward signalInputON (seat reclining switch forward
operation)0
Other than above Battery voltage
28 Y/BFront lifting switch
UP signalInputON (front lifting switch UP operation) 0
Other than above Battery voltage
29 L/BRear lifting switch
UP signalInputON (rear lifting switch UP operation) 0
Other than above Battery voltage
31 B/W Sensor ground — — 0
32 W/B Ground (signal) — — 0
33 W Power source (C/B) Input — Battery voltage
35 R/WSliding motor
forward signalOutputSliding switch forward operation
(Motor operated)Battery voltage
Other than above 0
36 G/WReclining motor
forward signalOutputReclining switch forward operation
(Motor operated)Battery voltage
Other than above 0
37 Y/WFront lifting motor
DOWN signalOutputFront lifting switch down operation
(Motor operated)Battery voltage
Other than above 0
38 L/BRear lifting motor
UP signalOutputRear lifting switch up operation
(Motor operated)Battery voltage
Other than above 0
39 L/WRear lifting motor
DOWN signalOutputRear lifting switch down operation
(Motor operated)Battery voltage
Other than above 0
40 R/B Power source (Fuse) Input — Battery voltage
42 R/BSliding motor
backward signalOutputSliding switch backward operation
(Motor operated)Battery voltage
Other than above 0 Te r m i -
nalWire
colorItemSignal
Input/OutputConditionVoltage (V)
(Approx)
SIIA0690J
SIIA0691J
Page 4234 of 4647
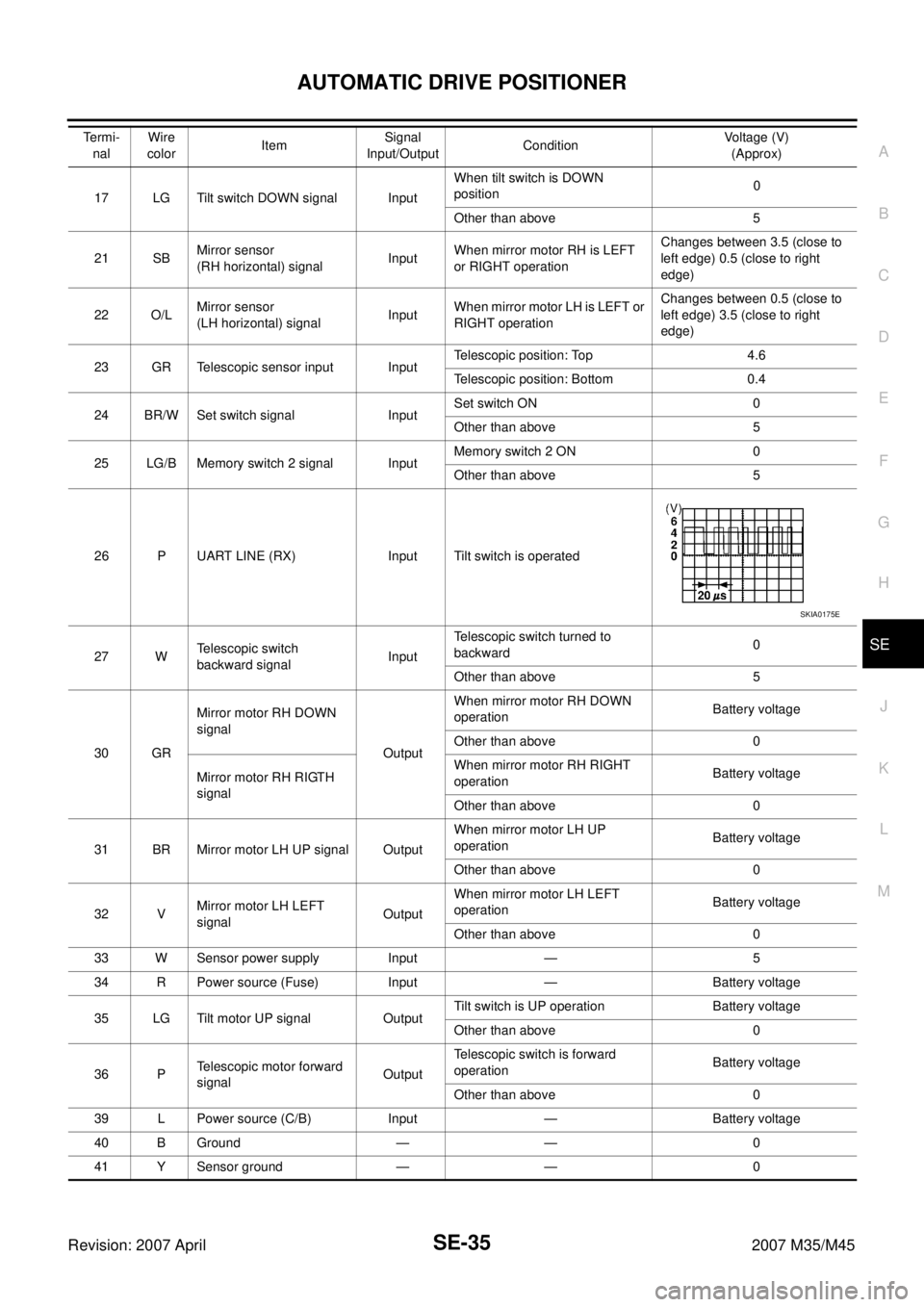
AUTOMATIC DRIVE POSITIONER
SE-35
C
D
E
F
G
H
J
K
L
MA
B
SE
Revision: 2007 April2007 M35/M45
17 LG Tilt switch DOWN signal InputWhen tilt switch is DOWN
position0
Other than above 5
21 SBMirror sensor
(RH horizontal) signalInputWhen mirror motor RH is LEFT
or RIGHT operationChanges between 3.5 (close to
left edge) 0.5 (close to right
edge)
22 O/LMirror sensor
(LH horizontal) signalInputWhen mirror motor LH is LEFT or
RIGHT operationChanges between 0.5 (close to
left edge) 3.5 (close to right
edge)
23 GR Telescopic sensor input InputTelescopic position: Top 4.6
Telescopic position: Bottom 0.4
24 BR/W Set switch signal InputSet switch ON 0
Other than above 5
25 LG/B Memory switch 2 signal InputMemory switch 2 ON 0
Other than above 5
26 P UART LINE (RX) Input Tilt switch is operated
27 WTelescopic switch
backward signalInputTelescopic switch turned to
backward0
Other than above 5
30 GRMirror motor RH DOWN
signal
OutputWhen mirror motor RH DOWN
operationBattery voltage
Other than above 0
Mirror motor RH RIGTH
signalWhen mirror motor RH RIGHT
operationBattery voltage
Other than above 0
31 BR Mirror motor LH UP signal OutputWhen mirror motor LH UP
operationBattery voltage
Other than above 0
32 VMirror motor LH LEFT
signalOutputWhen mirror motor LH LEFT
operationBattery voltage
Other than above 0
33 W Sensor power supply Input — 5
34 R Power source (Fuse) Input — Battery voltage
35 LG Tilt motor UP signal OutputTilt switch is UP operation Battery voltage
Other than above 0
36 PTelescopic motor forward
signalOutputTelescopic switch is forward
operationBattery voltage
Other than above 0
39 L Power source (C/B) Input — Battery voltage
40 B Ground — — 0
41 Y Sensor ground — — 0 Te r m i -
nal Wire
colorItemSignal
Input/OutputConditionVoltage (V)
(Approx)
SKIA0175E
Page 4241 of 4647

SE-42
AUTOMATIC DRIVE POSITIONER
Revision: 2007 April2007 M35/M45
CAN Communication Inspection Using CONSULT-II (Self-Diagnosis)NIS00263
1. SELF-DIAGNOSTIC RESULT CHECK
CAUTION:
If CONSULT-II is used with no connection of CONSULT-II CONVERTER, malfunctions might be
detected in self-diagnosis depending on control unit which carry out CAN communication.
1. Connect to CONSULT-II, and select “AUTO DRIVE POS.” on the “SELECT DIAG SYSTEM” screen.
2. Select “SELF-DIAG RESULTS” on “SELECT DIAG MODE” screen.
3. Check display content in self-diagnostic results.
Contents displayed
No malfunction>>Inspection End.
Malfunction in CAN communication system>>After printing the monitor items, go to “CAN System”. Refer to
LAN-50, "
CAN System Specification Chart" .
Check BCM Power Supply and Ground CircuitNIS00264
1. CHECK FUSE
Check if any of the following fuses in the BCM are blown.
NOTE:
Refer to SE-11, "
Component Parts And Harness Connector Location" .
OK or NG
OK >> GO TO 2.
NG >> If fuse is blown, be sure to eliminate cause of malfunction before installing new fuse. Refer to PG-
3, "POWER SUPPLY ROUTING CIRCUIT" .
CONSULT-II display code Diagnosis item
U1000INITIAL DIAG
TRANSMIT DIAG
BCM/SEC
METER/M&A
TCM
Unit Power source Fuse No.
BCMBattery power supplyF (50A)
Battery power supply 21 (10A)
Ignition switch ON or STRAT signal 1 (15A)
Ignition switch ACC or ON signal 6 (10A)