Page 835 of 1556

Downloaded from www.Manualslib.com manuals search engine Manual Transmission/Transaxle: 5B-23
12) To seat countershaft left bearing outer race (2) to
bearing cone, tap cup by using special tool and
plastic hammer.
Special tool
(A): 09913–70123
13) Before selecting shim, keep pushing outer race with
the power of 100 N (10.0 kgf) and turn countershaft
(2) 10 time or more.
14) Put a shim (3) on bearing outer race (4) provisionally,
place straight edge (1) over it and compress it by
hand through straight edge, and then measure “a”
(Clearance between case surface (5) and straight
edge) by using feeler gauge (6).
Clearance between case surface and straight
edge
“a”: 0.08 – 0.12 mm (0.0032 – 0.0047 in.)15) By repeating step 14), select a suitable shim which
adjusts clearance “a” to specification and put it on
bearing outer race.
NOTE
Insert 0.1 mm (0.004 in.) feeler to know
whether or not a shim fulfills specification
quickly.
Available countershaft 5th gear shim thickness
1. Input shaft
I5RW0A520025-01
0.55 mm
(0.021 in.)0.7 mm
(0.027 in.)0.85 mm
(0.033 in.)1.0 mm
(0.039 in.)
0.6 mm
(0.023 in.)0.75 mm
(0.029 in.)0.9 mm
(0.035 in.)1.05 mm
(0.041 in.)
0.65 mm
(0.025 in.)0.8 mm
(0.031 in.)0.95 mm
(0.037 in.)1.1 mm
(0.043 in.)
2. Countershaft
I7RW01520012-01
Page 836 of 1556
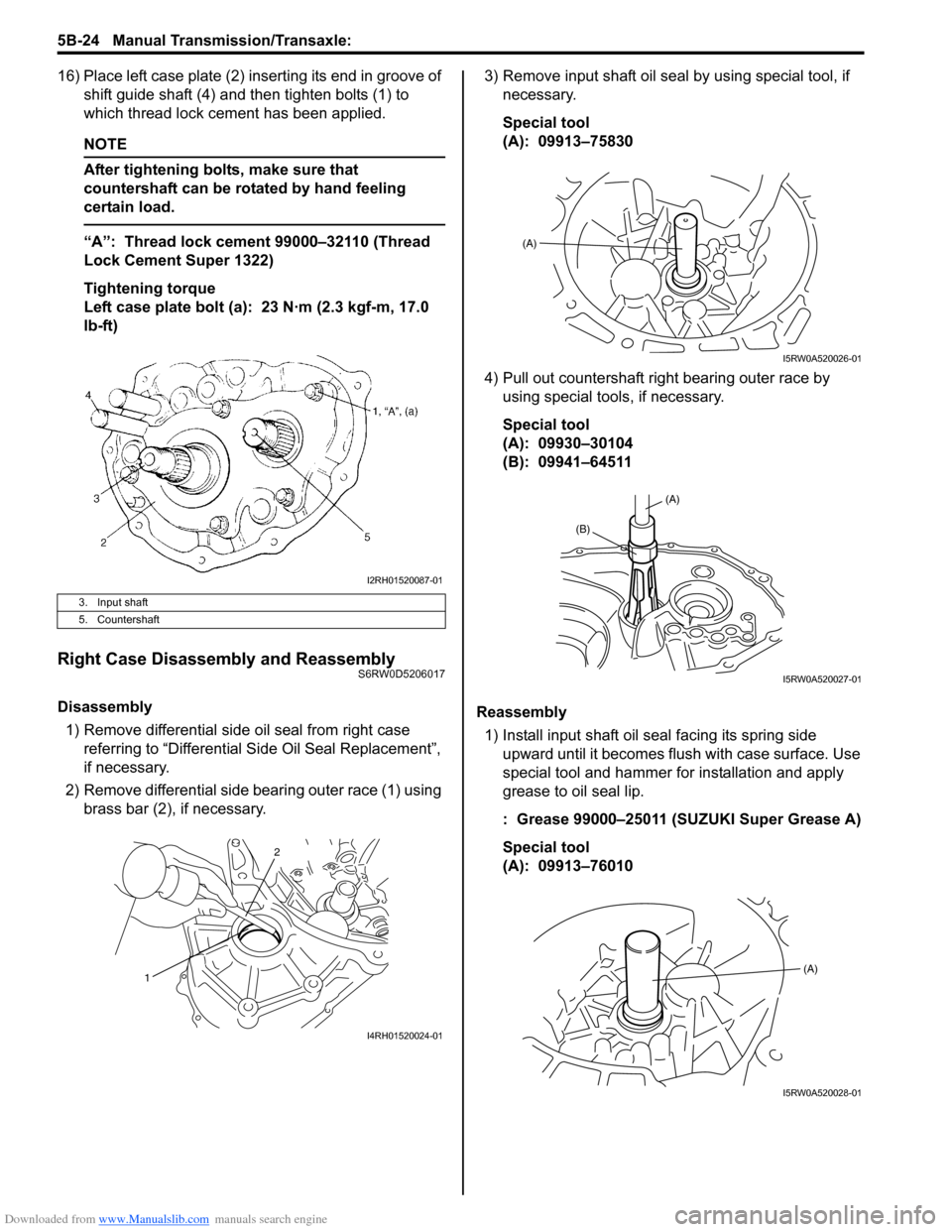
Downloaded from www.Manualslib.com manuals search engine 5B-24 Manual Transmission/Transaxle:
16) Place left case plate (2) inserting its end in groove of
shift guide shaft (4) and then tighten bolts (1) to
which thread lock cement has been applied.
NOTE
After tightening bolts, make sure that
countershaft can be rotated by hand feeling
certain load.
“A”: Thread lock cement 99000–32110 (Thread
Lock Cement Super 1322)
Tightening torque
Left case plate bolt (a): 23 N·m (2.3 kgf-m, 17.0
lb-ft)
Right Case Disassembly and ReassemblyS6RW0D5206017
Disassembly
1) Remove differential side oil seal from right case
referring to “Differential Side Oil Seal Replacement”,
if necessary.
2) Remove differential side bearing outer race (1) using
brass bar (2), if necessary.3) Remove input shaft oil seal by using special tool, if
necessary.
Special tool
(A): 09913–75830
4) Pull out countershaft right bearing outer race by
using special tools, if necessary.
Special tool
(A): 09930–30104
(B): 09941–64511
Reassembly
1) Install input shaft oil seal facing its spring side
upward until it becomes flush with case surface. Use
special tool and hammer for installation and apply
grease to oil seal lip.
: Grease 99000–25011 (SUZUKI Super Grease A)
Special tool
(A): 09913–76010
3. Input shaft
5. Countershaft
I2RH01520087-01
2
1
I4RH01520024-01
(A)
I5RW0A520026-01
(A)
(B)
I5RW0A520027-01
(A)
I5RW0A520028-01
Page 837 of 1556
Downloaded from www.Manualslib.com manuals search engine Manual Transmission/Transaxle: 5B-25
2) Install countershaft right bearing outer race (1) by
using special tools and hammer.
Special tool
(A): 09913–75821
(B): 09924–84510–004
3) Install differential side bearing outer race by using
special tool and hammer.
Special tool
(A): 09924–74510
(B): 09925–14520Left Case Disassembly and ReassemblyS6RW0D5206018
Disassembly
1) Removal oil gutter (1), if necessary.
2) Remove oil seal using flat end rod or the like.
3) Remove differential side bearing outer race (1) using
special tools.
Special tool
(A): 09942–15511
(B): 09944–96011
I5RW0A520029-02
(A)
(B)
I5RW0A520030-01
I4RH01520028-01
(A)
(B)
1I5RW0A520031-01
Page 838 of 1556
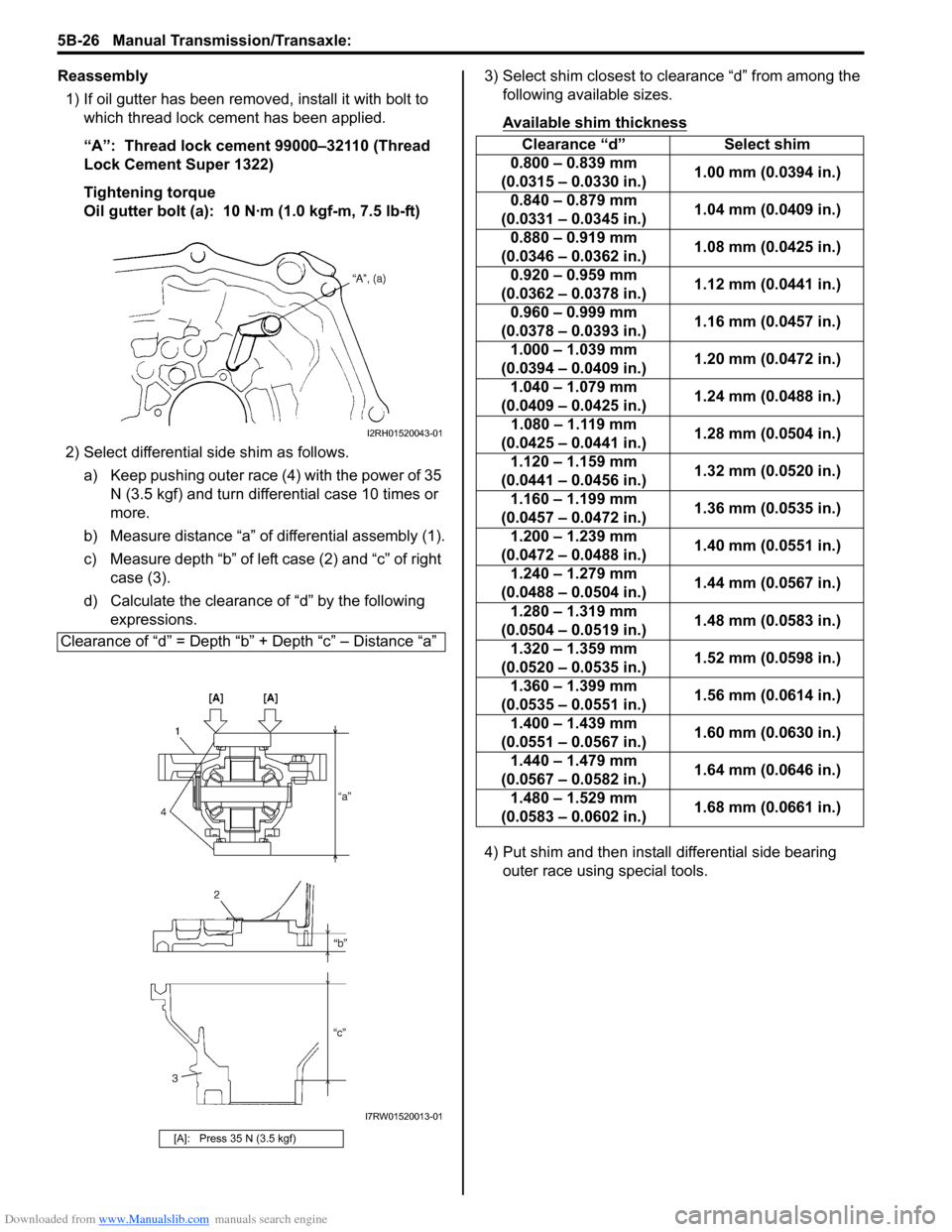
Downloaded from www.Manualslib.com manuals search engine 5B-26 Manual Transmission/Transaxle:
Reassembly
1) If oil gutter has been removed, install it with bolt to
which thread lock cement has been applied.
“A”: Thread lock cement 99000–32110 (Thread
Lock Cement Super 1322)
Tightening torque
Oil gutter bolt (a): 10 N·m (1.0 kgf-m, 7.5 lb-ft)
2) Select differential side shim as follows.
a) Keep pushing outer race (4) with the power of 35
N (3.5 kgf) and turn differential case 10 times or
more.
b) Measure distance “a” of differential assembly (1).
c) Measure depth “b” of left case (2) and “c” of right
case (3).
d) Calculate the clearance of “d” by the following
expressions.3) Select shim closest to clearance “d” from among the
following available sizes.
Available shim thickness
4) Put shim and then install differential side bearing
outer race using special tools. Clearance of “d” = Depth “b” + Depth “c” – Distance “a”
[A]: Press 35 N (3.5 kgf)
I2RH01520043-01
I7RW01520013-01
Clearance “d” Select shim
0.800 – 0.839 mm
(0.0315 – 0.0330 in.)1.00 mm (0.0394 in.)
0.840 – 0.879 mm
(0.0331 – 0.0345 in.)1.04 mm (0.0409 in.)
0.880 – 0.919 mm
(0.0346 – 0.0362 in.)1.08 mm (0.0425 in.)
0.920 – 0.959 mm
(0.0362 – 0.0378 in.)1.12 mm (0.0441 in.)
0.960 – 0.999 mm
(0.0378 – 0.0393 in.)1.16 mm (0.0457 in.)
1.000 – 1.039 mm
(0.0394 – 0.0409 in.)1.20 mm (0.0472 in.)
1.040 – 1.079 mm
(0.0409 – 0.0425 in.)1.24 mm (0.0488 in.)
1.080 – 1.119 mm
(0.0425 – 0.0441 in.)1.28 mm (0.0504 in.)
1.120 – 1.159 mm
(0.0441 – 0.0456 in.)1.32 mm (0.0520 in.)
1.160 – 1.199 mm
(0.0457 – 0.0472 in.)1.36 mm (0.0535 in.)
1.200 – 1.239 mm
(0.0472 – 0.0488 in.)1.40 mm (0.0551 in.)
1.240 – 1.279 mm
(0.0488 – 0.0504 in.)1.44 mm (0.0567 in.)
1.280 – 1.319 mm
(0.0504 – 0.0519 in.)1.48 mm (0.0583 in.)
1.320 – 1.359 mm
(0.0520 – 0.0535 in.)1.52 mm (0.0598 in.)
1.360 – 1.399 mm
(0.0535 – 0.0551 in.)1.56 mm (0.0614 in.)
1.400 – 1.439 mm
(0.0551 – 0.0567 in.)1.60 mm (0.0630 in.)
1.440 – 1.479 mm
(0.0567 – 0.0582 in.)1.64 mm (0.0646 in.)
1.480 – 1.529 mm
(0.0583 – 0.0602 in.)1.68 mm (0.0661 in.)
Page 839 of 1556
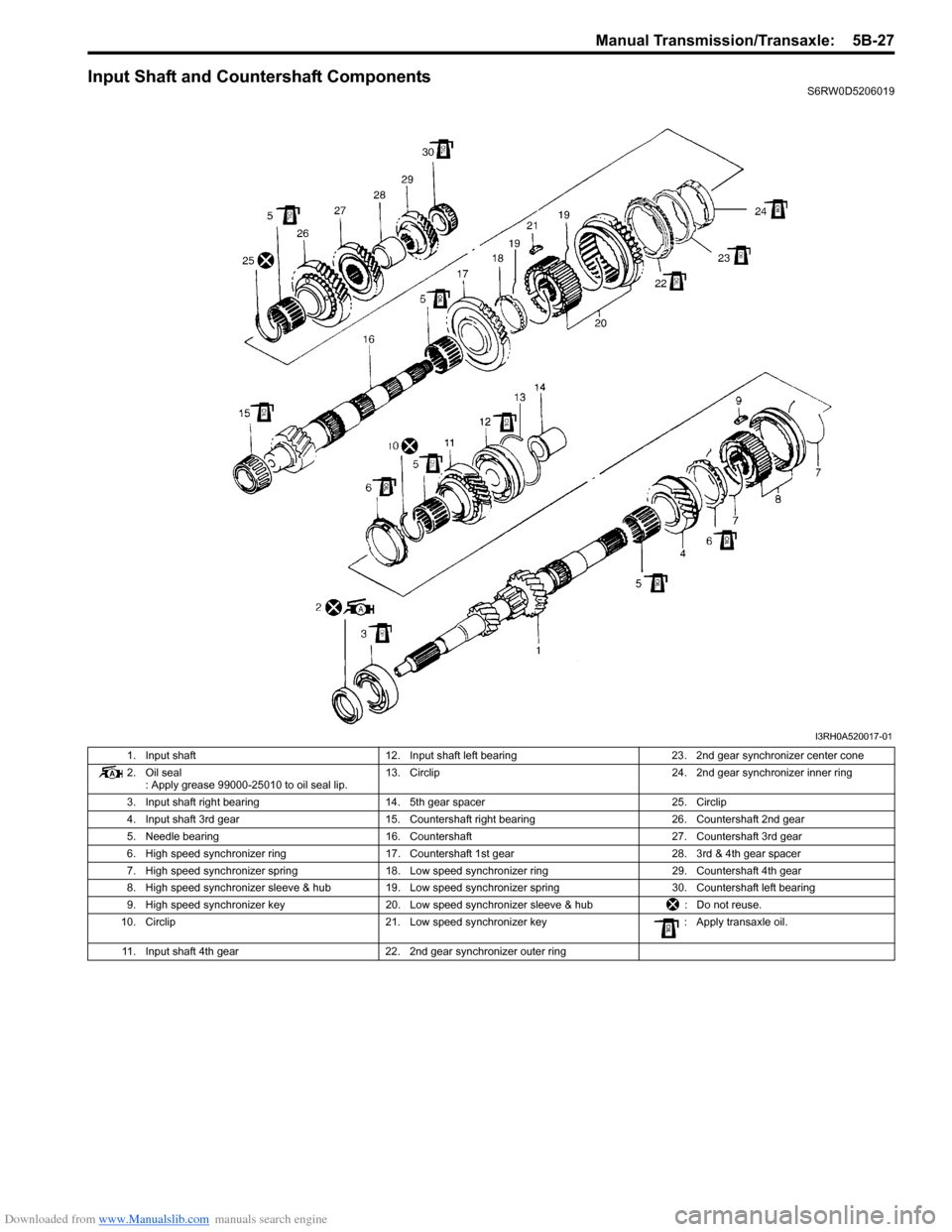
Downloaded from www.Manualslib.com manuals search engine Manual Transmission/Transaxle: 5B-27
Input Shaft and Countershaft ComponentsS6RW0D5206019
I3RH0A520017-01
1. Input shaft 12. Input shaft left bearing 23. 2nd gear synchronizer center cone
2. Oil seal
: Apply grease 99000-25010 to oil seal lip.13. Circlip 24. 2nd gear synchronizer inner ring
3. Input shaft right bearing 14. 5th gear spacer 25. Circlip
4. Input shaft 3rd gear 15. Countershaft right bearing 26. Countershaft 2nd gear
5. Needle bearing 16. Countershaft 27. Countershaft 3rd gear
6. High speed synchronizer ring 17. Countershaft 1st gear 28. 3rd & 4th gear spacer
7. High speed synchronizer spring 18. Low speed synchronizer ring 29. Countershaft 4th gear
8. High speed synchronizer sleeve & hub 19. Low speed synchronizer spring 30. Countershaft left bearing
9. High speed synchronizer key 20. Low speed synchronizer sleeve & hub : Do not reuse.
10. Circlip 21. Low speed synchronizer key : Apply transaxle oil.
11. Input shaft 4th gear 22. 2nd gear synchronizer outer ring
Page 840 of 1556
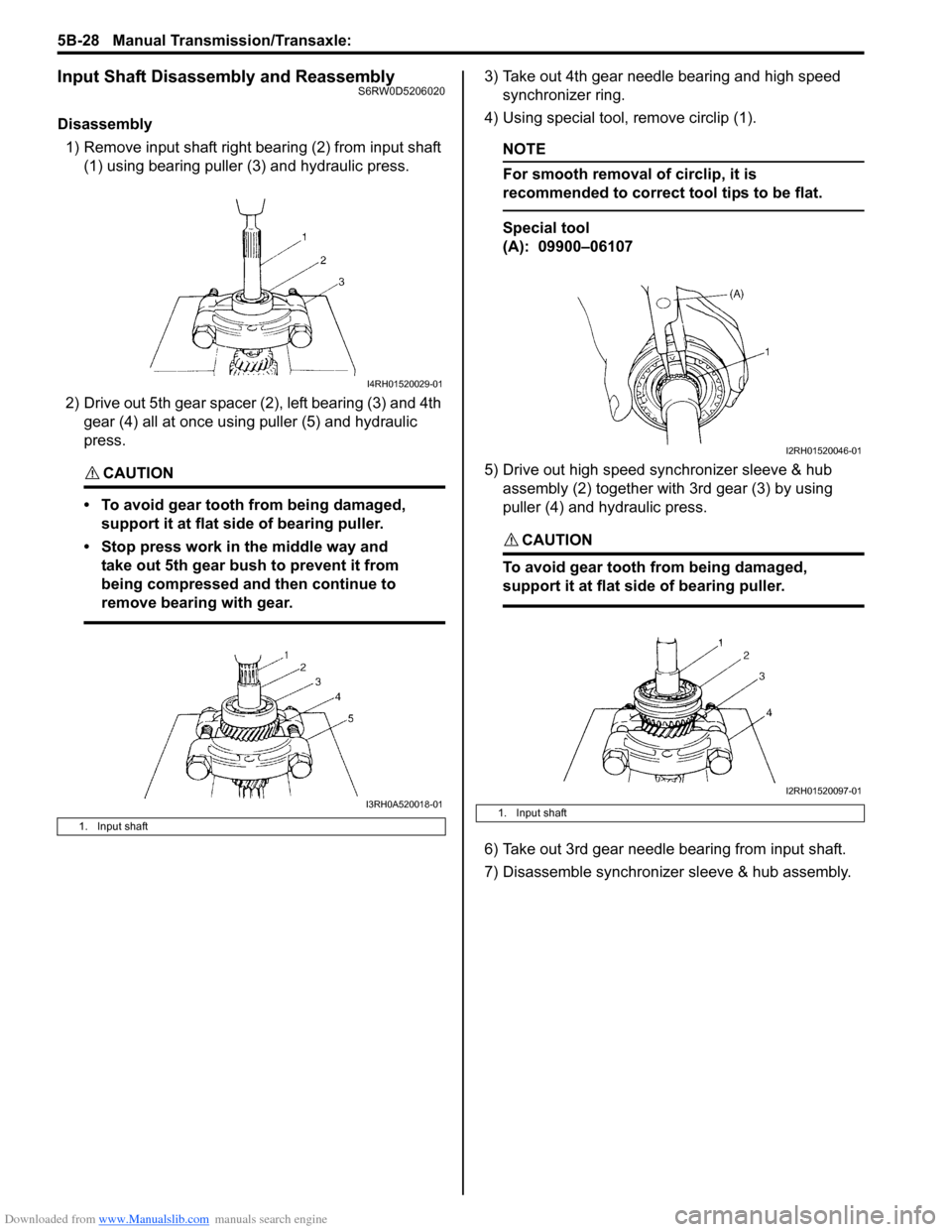
Downloaded from www.Manualslib.com manuals search engine 5B-28 Manual Transmission/Transaxle:
Input Shaft Disassembly and ReassemblyS6RW0D5206020
Disassembly
1) Remove input shaft right bearing (2) from input shaft
(1) using bearing puller (3) and hydraulic press.
2) Drive out 5th gear spacer (2), left bearing (3) and 4th
gear (4) all at once using puller (5) and hydraulic
press.
CAUTION!
• To avoid gear tooth from being damaged,
support it at flat side of bearing puller.
• Stop press work in the middle way and
take out 5th gear bush to prevent it from
being compressed and then continue to
remove bearing with gear.
3) Take out 4th gear needle bearing and high speed
synchronizer ring.
4) Using special tool, remove circlip (1).
NOTE
For smooth removal of circlip, it is
recommended to correct tool tips to be flat.
Special tool
(A): 09900–06107
5) Drive out high speed synchronizer sleeve & hub
assembly (2) together with 3rd gear (3) by using
puller (4) and hydraulic press.
CAUTION!
To avoid gear tooth from being damaged,
support it at flat side of bearing puller.
6) Take out 3rd gear needle bearing from input shaft.
7) Disassemble synchronizer sleeve & hub assembly.
1. Input shaft
I4RH01520029-01
I3RH0A520018-011. Input shaft
I2RH01520046-01
I2RH01520097-01
Page 841 of 1556
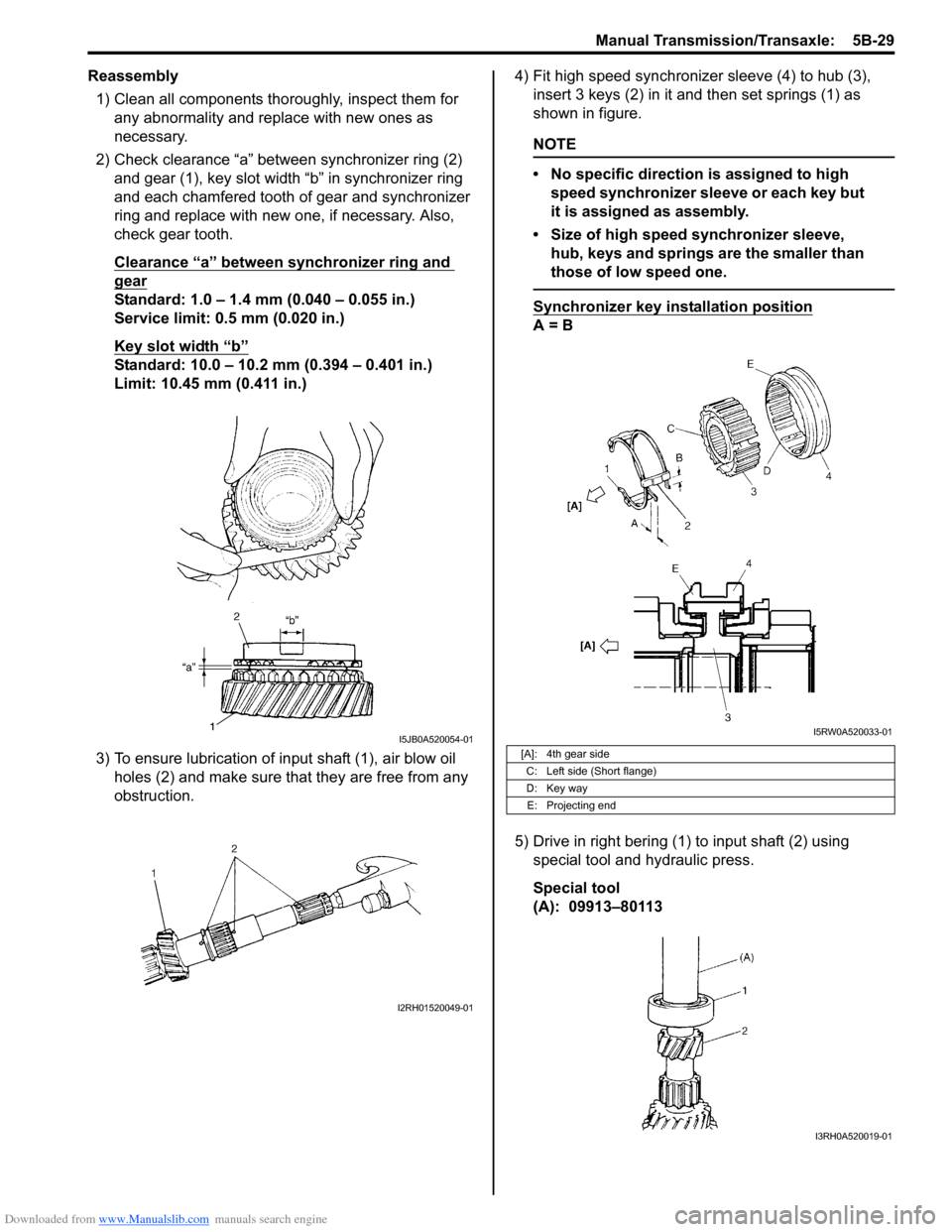
Downloaded from www.Manualslib.com manuals search engine Manual Transmission/Transaxle: 5B-29
Reassembly
1) Clean all components thoroughly, inspect them for
any abnormality and replace with new ones as
necessary.
2) Check clearance “a” between synchronizer ring (2)
and gear (1), key slot width “b” in synchronizer ring
and each chamfered tooth of gear and synchronizer
ring and replace with new one, if necessary. Also,
check gear tooth.
Clearance “a” between synchronizer ring and
gear
Standard: 1.0 – 1.4 mm (0.040 – 0.055 in.)
Service limit: 0.5 mm (0.020 in.)
Key slot width “b”
Standard: 10.0 – 10.2 mm (0.394 – 0.401 in.)
Limit: 10.45 mm (0.411 in.)
3) To ensure lubrication of input shaft (1), air blow oil
holes (2) and make sure that they are free from any
obstruction.4) Fit high speed synchronizer sleeve (4) to hub (3),
insert 3 keys (2) in it and then set springs (1) as
shown in figure.
NOTE
• No specific direction is assigned to high
speed synchronizer sleeve or each key but
it is assigned as assembly.
• Size of high speed synchronizer sleeve,
hub, keys and springs are the smaller than
those of low speed one.
Synchronizer key installation position
A = B
5) Drive in right bering (1) to input shaft (2) using
special tool and hydraulic press.
Special tool
(A): 09913–80113
I5JB0A520054-01
I2RH01520049-01
[A]: 4th gear side
C: Left side (Short flange)
D: Key way
E: Projecting end
I5RW0A520033-01
I3RH0A520019-01
Page 842 of 1556
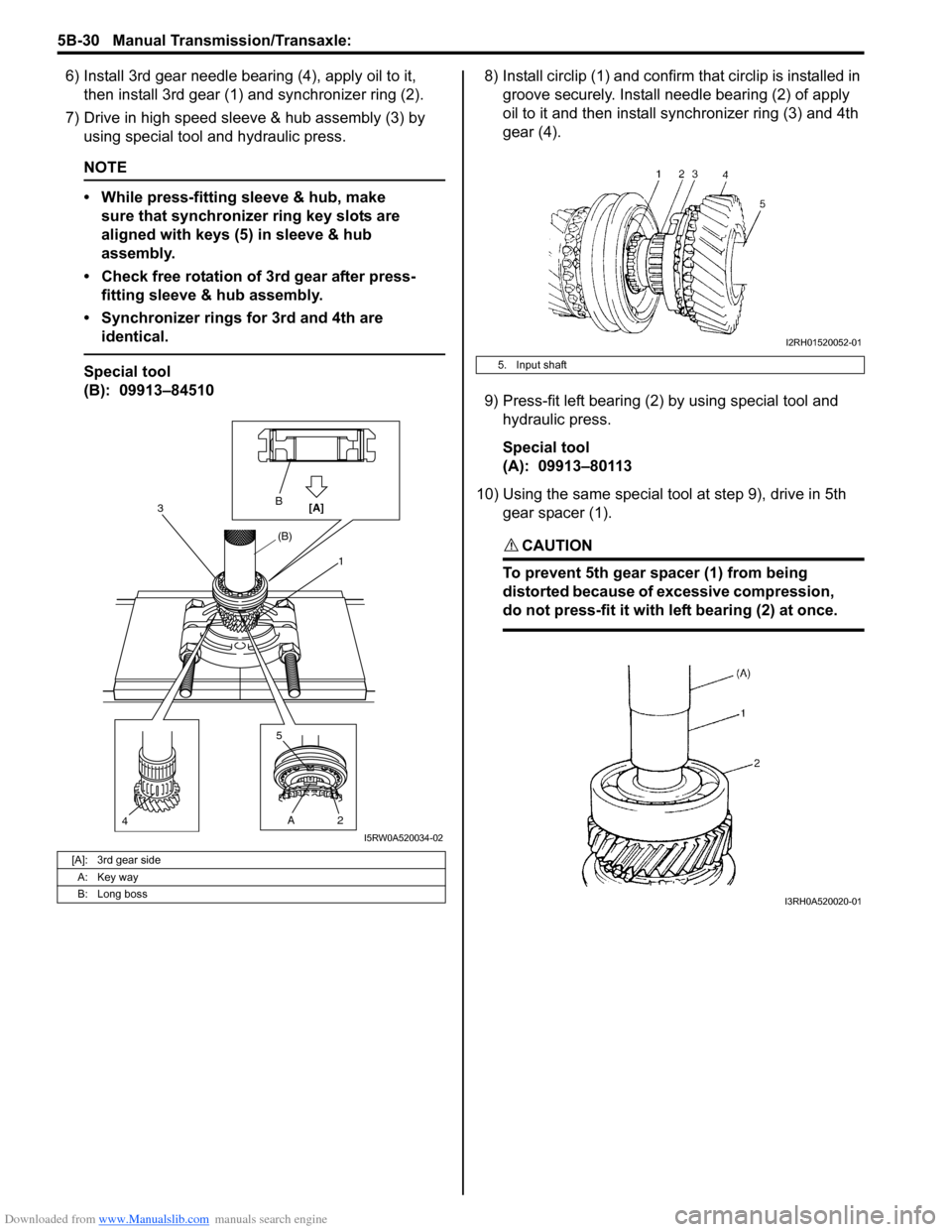
Downloaded from www.Manualslib.com manuals search engine 5B-30 Manual Transmission/Transaxle:
6) Install 3rd gear needle bearing (4), apply oil to it,
then install 3rd gear (1) and synchronizer ring (2).
7) Drive in high speed sleeve & hub assembly (3) by
using special tool and hydraulic press.
NOTE
• While press-fitting sleeve & hub, make
sure that synchronizer ring key slots are
aligned with keys (5) in sleeve & hub
assembly.
• Check free rotation of 3rd gear after press-
fitting sleeve & hub assembly.
• Synchronizer rings for 3rd and 4th are
identical.
Special tool
(B): 09913–845108) Install circlip (1) and confirm that circlip is installed in
groove securely. Install needle bearing (2) of apply
oil to it and then install synchronizer ring (3) and 4th
gear (4).
9) Press-fit left bearing (2) by using special tool and
hydraulic press.
Special tool
(A): 09913–80113
10) Using the same special tool at step 9), drive in 5th
gear spacer (1).
CAUTION!
To prevent 5th gear spacer (1) from being
distorted because of excessive compression,
do not press-fit it with left bearing (2) at once.
[A]: 3rd gear side
A: Key way
B: Long boss
B
[A]3
(B)
4A 5
21
I5RW0A520034-02
5. Input shaft
I2RH01520052-01
I3RH0A520020-01