Page 29 of 3383
![INFINITI QX56 2006 Factory Service Manual ACS-16
[ICC]
LASER BEAM AIMING ADJUSTMENT
Revision: November 20092006 QX56
The area is not suitable for the adjustment work.
ICC sensor is not clean.
8. After the CONSULT-II displays “ADJUST THE INFINITI QX56 2006 Factory Service Manual ACS-16
[ICC]
LASER BEAM AIMING ADJUSTMENT
Revision: November 20092006 QX56
The area is not suitable for the adjustment work.
ICC sensor is not clean.
8. After the CONSULT-II displays “ADJUST THE](/manual-img/42/57028/w960_57028-28.png)
ACS-16
[ICC]
LASER BEAM AIMING ADJUSTMENT
Revision: November 20092006 QX56
The area is not suitable for the adjustment work.
ICC sensor is not clean.
8. After the CONSULT-II displays “ADJUST THE VERTICAL OF
LASER BEAM AIMING” turn the vertical adjusting screw until
“U/D CORRECT ” value is set in the range of ±4.
CAUTION:
Turn the screw slowly. The value on the CONSULT-II is
slower than the actual movement of the ICC sensor. Wait 2
seconds between each adjustment. Also, during adjust-
ment work, do not block the ICC sensor lens with your hand
or body. In that case, there are times when aiming cannot
be conducted correctly.
NOTE:
Turning the screw clockwise raises the ICC sensor and counter-
clockwise lowers the ICC sensor.
9. When “U/D CORRECT ” value indicates ± 4, confirm that the value remains within ±4 for at least 2 seconds
while nothing is touching the ICC sensor.
When “COMPLETED THE VERTICAL AIMING OF LASER
BEAM ” appears on screen, touch “END ”.
CAUTION:
Be sure that the margin of “U/D CORRECT” is within ±4
when the ICC sensor unit is untouched.
10. Confirm that “ADJUSTING AUTOMATIC HORIZONTAL LASER
BEAM AIMING ” is on screen and wait while the horizontal
adjustment is made automatically. (maximum: 10 seconds).
SKIA1221E
WKIA1869E
WKIA2676E
SKIA1224E
Page 319 of 3383
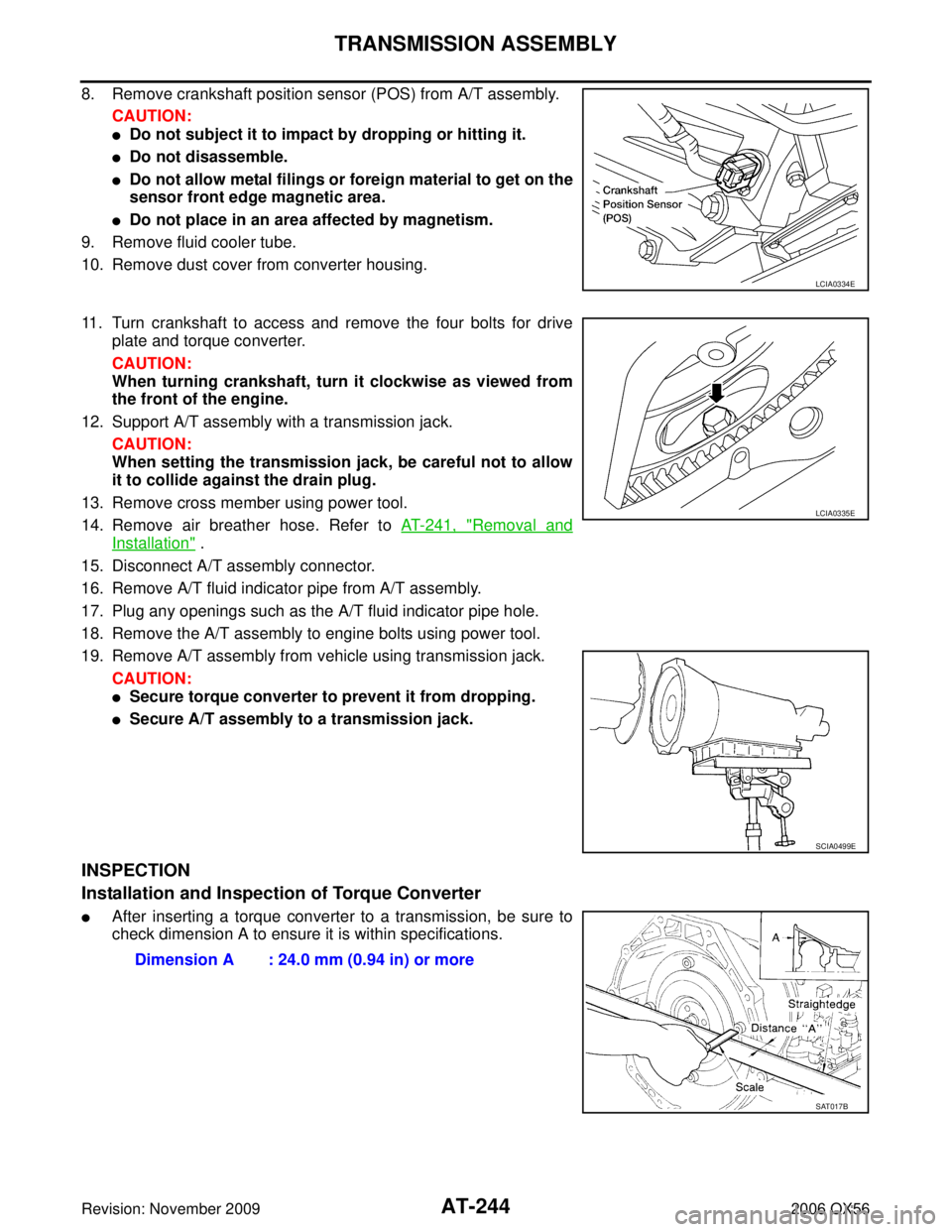
AT-244
TRANSMISSION ASSEMBLY
Revision: November 20092006 QX56
8. Remove crankshaft position sensor (POS) from A/T assembly.
CAUTION:
Do not subject it to impact by dropping or hitting it.
Do not disassemble.
Do not allow metal filings or foreign material to get on the
sensor front edge magnetic area.
Do not place in an area affected by magnetism.
9. Remove fluid cooler tube.
10. Remove dust cover from converter housing.
11. Turn crankshaft to access and remove the four bolts for drive plate and torque converter.
CAUTION:
When turning crankshaft, turn it clockwise as viewed from
the front of the engine.
12. Support A/T assembly with a transmission jack. CAUTION:
When setting the transmission jack, be careful not to allow
it to collide against the drain plug.
13. Remove cross member using power tool.
14. Remove air breather hose. Refer to AT- 2 4 1 , "
Removal and
Installation" .
15. Disconnect A/T assembly connector.
16. Remove A/T fluid indicator pipe from A/T assembly.
17. Plug any openings such as the A/T fluid indicator pipe hole.
18. Remove the A/T assembly to engine bolts using power tool.
19. Remove A/T assembly from vehicle using transmission jack. CAUTION:
Secure torque converter to prevent it from dropping.
Secure A/T assembly to a transmission jack.
INSPECTION
Installation and Inspection of Torque Converter
After inserting a torque converter to a transmission, be sure to
check dimension A to ensure it is within specifications.
LCIA0334E
LCIA0335E
SCIA0499E
Dimension A : 24.0 mm (0.94 in) or more
SAT017B
Page 320 of 3383
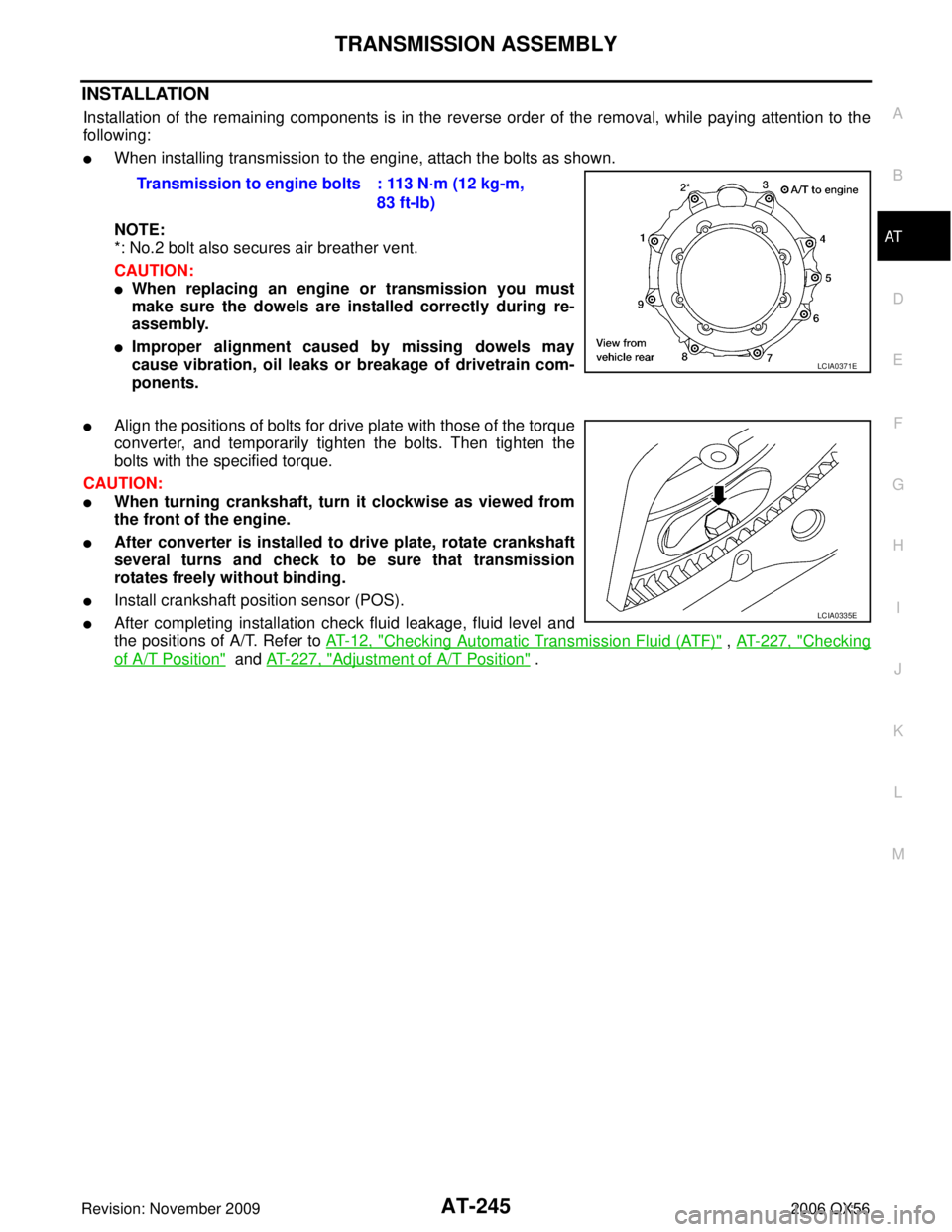
TRANSMISSION ASSEMBLYAT-245
DE
F
G H
I
J
K L
M A
B
AT
Revision: November 2009 2006 QX56
INSTALLATION
Installation of the remaining components is in the reverse order of the removal, while paying attention to the
following:
When installing transmission to the engine, attach the bolts as shown.
NOTE:
*: No.2 bolt also secures air breather vent.
CAUTION:
When replacing an engine or transmission you must
make sure the dowels are installed correctly during re-
assembly.
Improper alignment caused by missing dowels may
cause vibration, oil leaks or breakage of drivetrain com-
ponents.
Align the positions of bolts for drive plate with those of the torque
converter, and temporarily tighten the bolts. Then tighten the
bolts with the specified torque.
CAUTION:
When turning crankshaft, turn it clockwise as viewed from
the front of the engine.
After converter is installed to drive plate, rotate crankshaft
several turns and check to be sure that transmission
rotates freely without binding.
Install crankshaft position sensor (POS).
After completing installation check fluid leakage, fluid level and
the positions of A/T. Refer to AT- 1 2 , "
Checking Automatic Transmission Fluid (ATF)" , AT- 2 2 7 , "Checking
of A/T Position" and AT- 2 2 7 , "Adjustment of A/T Position" .
Transmission to engine bolts : 113 N·m (12 kg-m,
83 ft-lb)
LCIA0371E
LCIA0335E
Page 322 of 3383
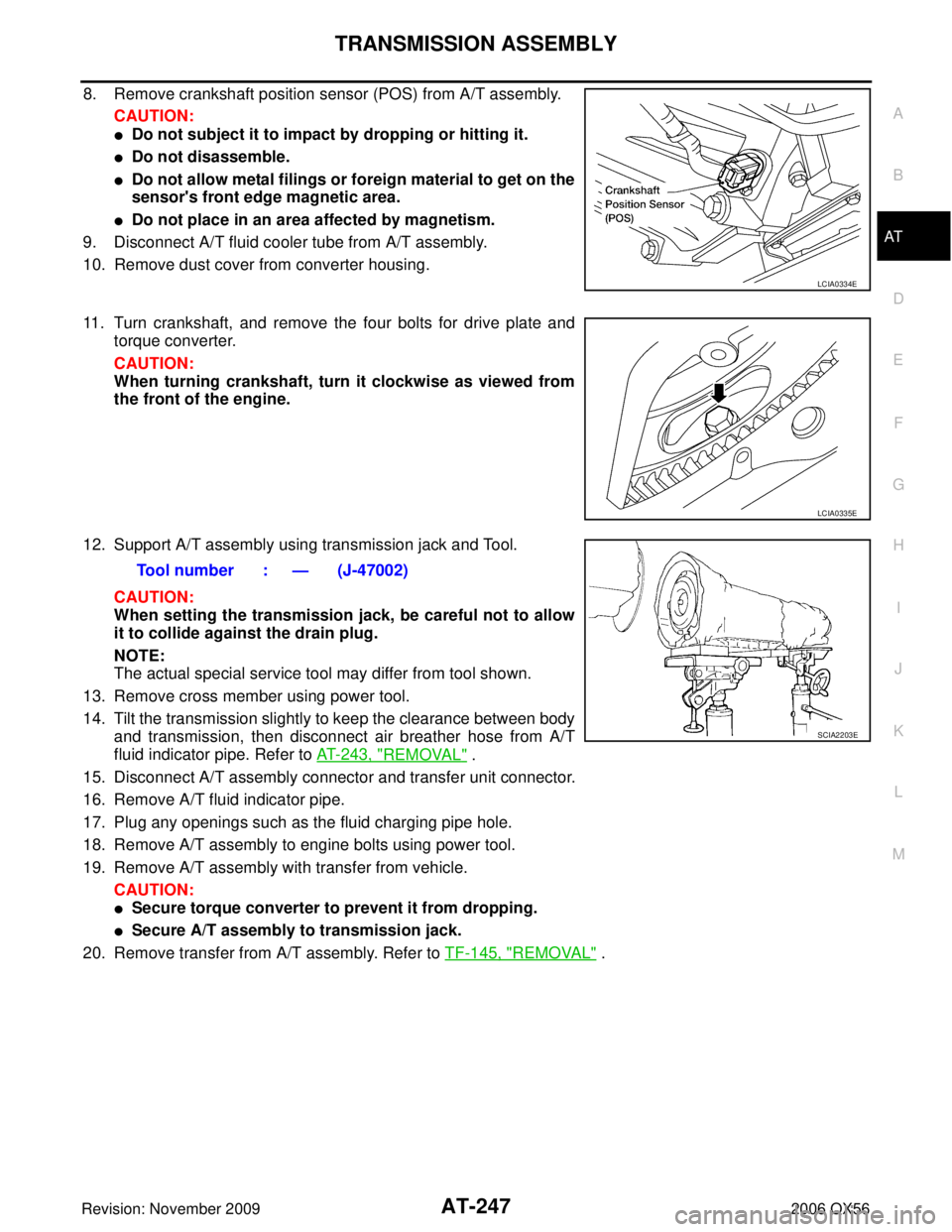
TRANSMISSION ASSEMBLYAT-247
DE
F
G H
I
J
K L
M A
B
AT
Revision: November 2009 2006 QX56
8. Remove crankshaft position sensor (POS) from A/T assembly.
CAUTION:
Do not subject it to impact by dropping or hitting it.
Do not disassemble.
Do not allow metal filings or foreign material to get on the
sensor's front edge magnetic area.
Do not place in an area affected by magnetism.
9. Disconnect A/T fluid cooler tube from A/T assembly.
10. Remove dust cover from converter housing.
11. Turn crankshaft, and remove the four bolts for drive plate and torque converter.
CAUTION:
When turning crankshaft, turn it clockwise as viewed from
the front of the engine.
12. Support A/T assembly using transmission jack and Tool. CAUTION:
When setting the transmission jack, be careful not to allow
it to collide against the drain plug.
NOTE:
The actual special service tool may differ from tool shown.
13. Remove cross member using power tool.
14. Tilt the transmission slightly to keep the clearance between body and transmission, then disconnect air breather hose from A/T
fluid indicator pipe. Refer to AT- 2 4 3 , "
REMOVAL" .
15. Disconnect A/T assembly connector and transfer unit connector.
16. Remove A/T fluid indicator pipe.
17. Plug any openings such as the fluid charging pipe hole.
18. Remove A/T assembly to engine bolts using power tool.
19. Remove A/T assembly with transfer from vehicle. CAUTION:
Secure torque converter to prevent it from dropping.
Secure A/T assembly to transmission jack.
20. Remove transfer from A/T assembly. Refer to TF-145, "
REMOVAL" .
LCIA0334E
LCIA0335E
Tool number : — (J-47002)
SCIA2203E
Page 324 of 3383
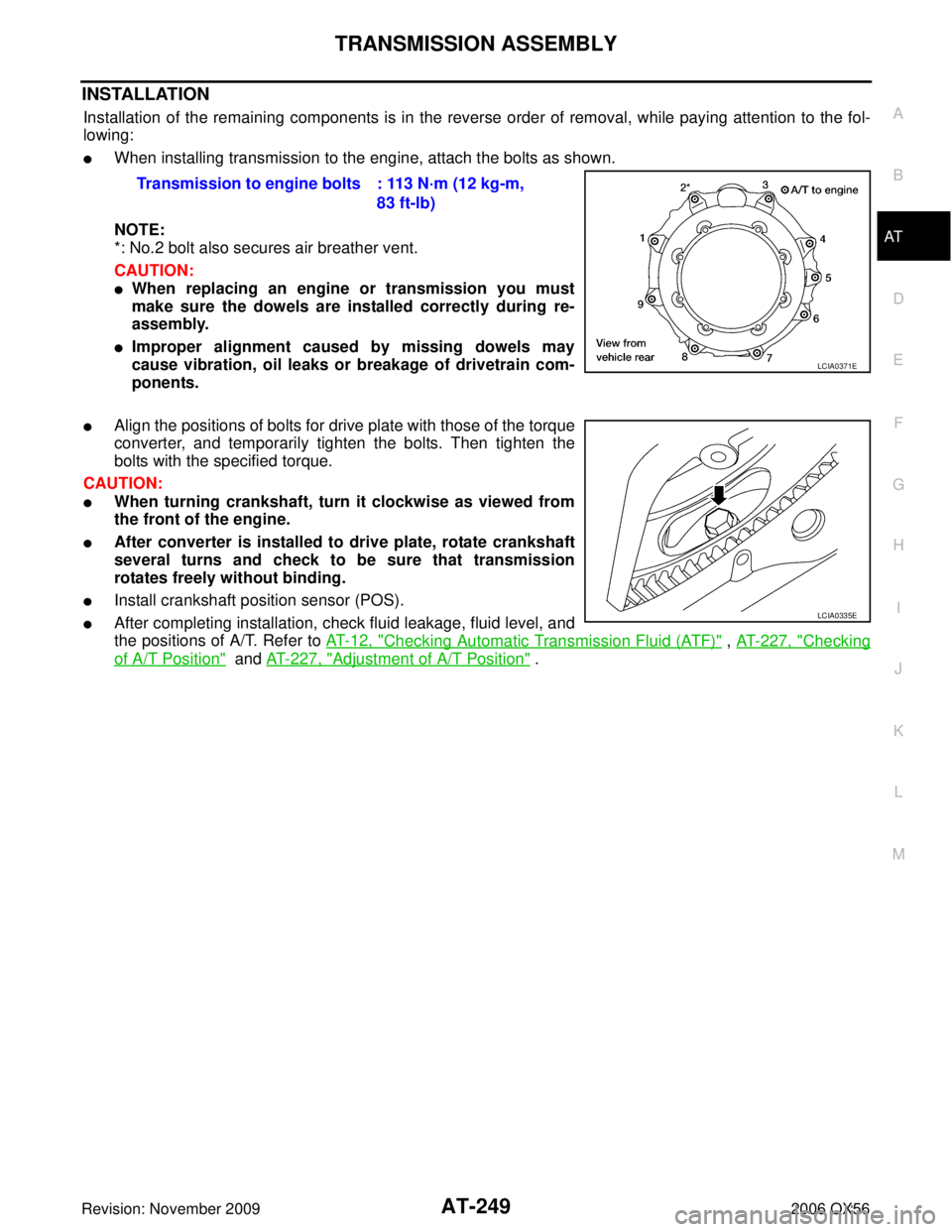
TRANSMISSION ASSEMBLYAT-249
DE
F
G H
I
J
K L
M A
B
AT
Revision: November 2009 2006 QX56
INSTALLATION
Installation of the remaining components is in the reverse order of removal, while paying attention to the fol-
lowing:
When installing transmission to the engine, attach the bolts as shown.
NOTE:
*: No.2 bolt also secures air breather vent.
CAUTION:
When replacing an engine or transmission you must
make sure the dowels are installed correctly during re-
assembly.
Improper alignment caused by missing dowels may
cause vibration, oil leaks or breakage of drivetrain com-
ponents.
Align the positions of bolts for drive plate with those of the torque
converter, and temporarily tighten the bolts. Then tighten the
bolts with the specified torque.
CAUTION:
When turning crankshaft, turn it clockwise as viewed from
the front of the engine.
After converter is installed to drive plate, rotate crankshaft
several turns and check to be sure that transmission
rotates freely without binding.
Install crankshaft position sensor (POS).
After completing installation, check fluid leakage, fluid level, and
the positions of A/T. Refer to AT- 1 2 , "
Checking Automatic Transmission Fluid (ATF)" , AT- 2 2 7 , "Checking
of A/T Position" and AT- 2 2 7 , "Adjustment of A/T Position" .
Transmission to engine bolts : 113 N·m (12 kg-m,
83 ft-lb)
LCIA0371E
LCIA0335E
Page 339 of 3383
AT-264
DISASSEMBLY
Revision: November 20092006 QX56
DISASSEMBLYPFP:31020
DisassemblyECS00EQ7
CAUTION:
Do not disassemble parts behind drum support. Refer to AT- 1 7 , "
Cross-Sectional View (2WD models)"
or AT- 1 8 , "Cross-Sectional View (4WD models)" .
1. Drain ATF through drain plug.
2. Remove torque converter by holding it firmly and turing while pulling straight out.
3. Check torque converter one-way clutch using check tool as shown.
a. Insert check tool into the groove of bearing support built into one-way clutch outer race.
b. While holding bearing support with check tool, rotate one- way clutch spline using suitable tool.
c. Check that inner race rotates clockwise only. If not, replace torque converter assembly.
4. Remove converter housing from transmission case. CAUTION:
Be careful not to scratch converter housing.
SCIA5010E
SCIA3171E
SCIA5171E
Page 414 of 3383
PRECAUTIONSATC-13
C
DE
F
G H
I
K L
M A
B
AT C
Revision: November 2009 2006 QX56
SERVICE COUPLERS
Never attempt to connect HFC-134a (R-134a) service couplers to a
CFC-12 (R-12) A/C system. The HFC-134a (R-134a) couplers will
not properly connect to the CFC-12 (R-12) system. If an improper
connection is attempted, discharging and contamination may occur.
REFRIGERANT WEIGHT SCALE
Verify that no refrigerant other than HFC134a (R-134a) and specified
oils have been used with the scale. If the scale controls refrigerant
flow electronically, the hose fitting must be 1/2”-16 ACME.
CHARGING CYLINDER
Using a charging cylinder is not recommended. Refrigerant may be vented into air from cylinder's top valve
when filling the cylinder with refrigerant. Also, the accuracy of the cylinder is generally less than that of an
electronic scale or of quality recycle/recharge equipment.
Shut-off valve rotationA/C service valve
Clockwise Open
Counterclockwise Close
RHA273D
RHA274D
Page 455 of 3383
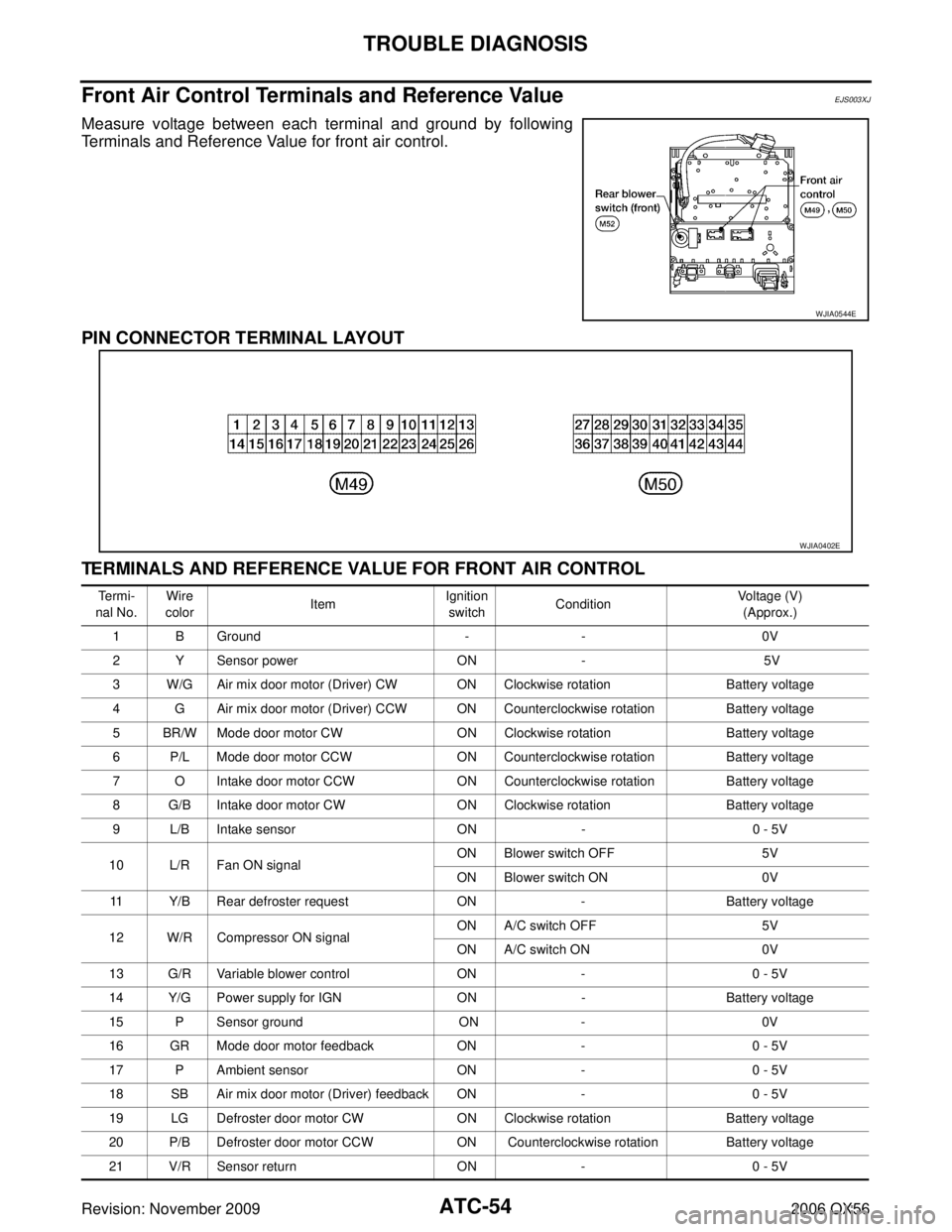
ATC-54
TROUBLE DIAGNOSIS
Revision: November 20092006 QX56
Front Air Control Terminals and Reference ValueEJS003XJ
Measure voltage between each terminal and ground by following
Terminals and Reference Value for front air control.
PIN CONNECTOR TERMINAL LAYOUT
TERMINALS AND REFERENCE VALUE FOR FRONT AIR CONTROL
WJIA0544E
WJIA0402E
Te r m i -
nal No. Wire
color ItemIgnition
switch Condition Voltage (V)
(Approx.)
1 B Ground -- 0V
2 Y Sensor power ON- 5V
3 W/G Air mix door motor (Driver) CW ON Clockwise rotation Battery voltage
4 G Air mix door motor (Driver) CCW ON Counterclockwise rotation Battery voltage
5 BR/W Mode door motor CW ON Clockwise rotationBattery voltage
6 P/L Mode door motor CCW ON Counterclockwise rotationBattery voltage
7 O Intake door motor CCW ON Counterclockwise rotationBattery voltage
8 G/B Intake door motor CW ON Clockwise rotationBattery voltage
9 L/B Intake sensor ON- 0 - 5V
10 L/R Fan ON signal ON Blower switch OFF
5V
ON Blower switch ON 0V
11 Y/B Rear defroster request ON- Battery voltage
12 W/R Compressor ON signal ON A/C switch OFF
5V
ON A/C switch ON 0V
13 G/R Variable blower control ON- 0 - 5V
14 Y/G Power supply for IGN ON- Battery voltage
15 P Sensor ground ON- 0V
16 GR Mode door motor feedback ON- 0 - 5V
17 P Ambient sensor ON- 0 - 5V
18 SB Air mix door motor (Driver) feedback ON -0 - 5V
19 LG Defroster door motor CW ON Clockwise rotationBattery voltage
20 P/B Defroster door motor CCW ON Counterclockwise rotationBattery voltage
21 V/R Sensor return ON- 0 - 5V