Page 2981 of 3383
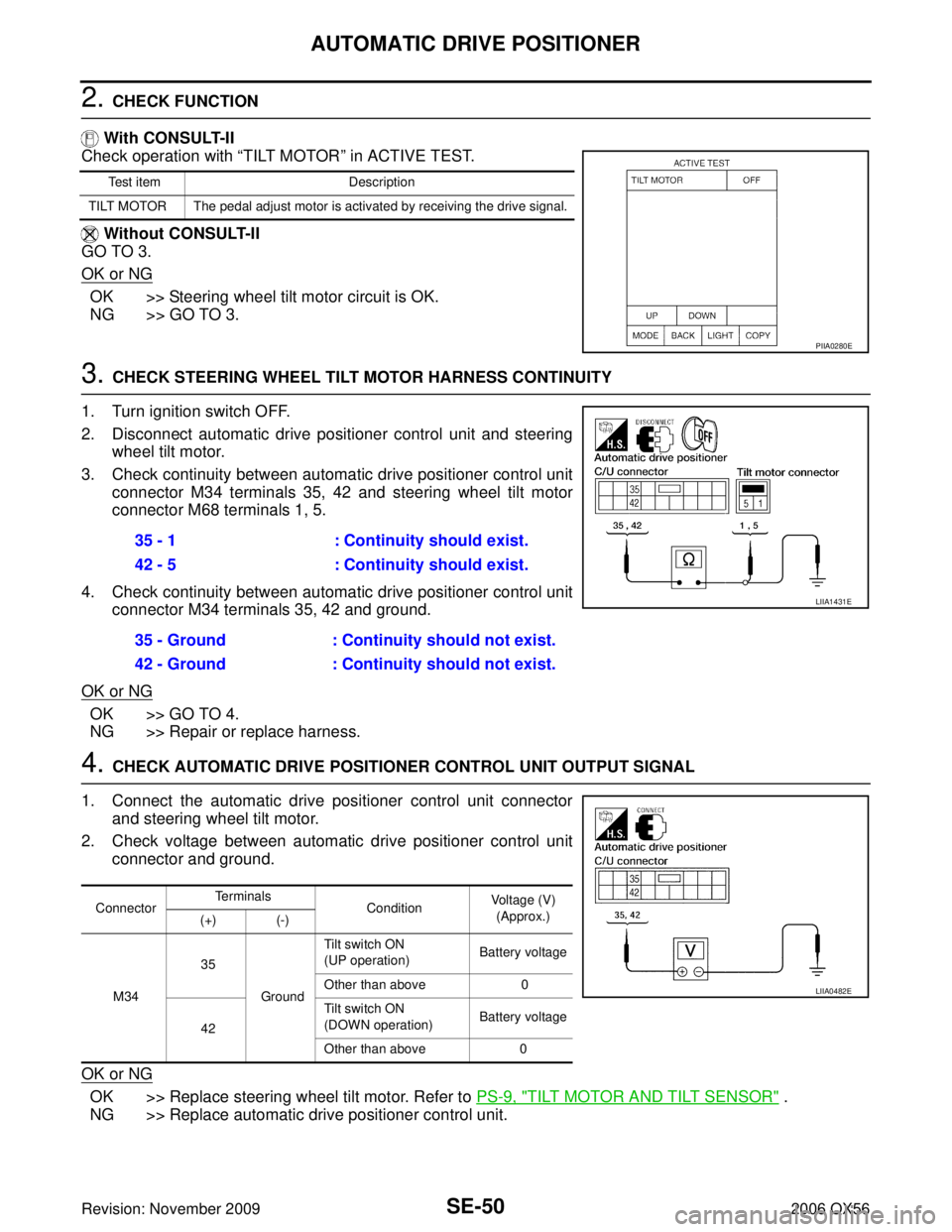
SE-50
AUTOMATIC DRIVE POSITIONER
Revision: November 20092006 QX56
2. CHECK FUNCTION
With CONSULT-II
Check operation with “TILT MOTOR” in ACTIVE TEST.
Without CONSULT-II
GO TO 3.
OK or NG
OK >> Steering wheel tilt motor circuit is OK.
NG >> GO TO 3.
3. CHECK STEERING WHEEL TILT MOTOR HARNESS CONTINUITY
1. Turn ignition switch OFF.
2. Disconnect automatic drive positioner control unit and steering wheel tilt motor.
3. Check continuity between automatic drive positioner control unit connector M34 terminals 35, 42 and steering wheel tilt motor
connector M68 terminals 1, 5.
4. Check continuity between automatic drive positioner control unit connector M34 terminals 35, 42 and ground.
OK or NG
OK >> GO TO 4.
NG >> Repair or replace harness.
4. CHECK AUTOMATIC DRIVE POSITIONER CONTROL UNIT OUTPUT SIGNAL
1. Connect the automatic drive positioner control unit connector and steering wheel tilt motor.
2. Check voltage between automatic drive positioner control unit connector and ground.
OK or NG
OK >> Replace steering wheel tilt motor. Refer to PS-9, "TILT MOTOR AND TILT SENSOR" .
NG >> Replace automatic drive positioner control unit.
Test item Description
TILT MOTOR The pedal adjust motor is activated by receiving the drive signal.
PIIA0280E
35 - 1 : Continuity should exist.
42 - 5 : Continuity should exist.
35 - Ground : Continuity should not exist.
42 - Ground : Continuity should not exist.
LIIA1431E
ConnectorTe r m i n a l s
ConditionVoltage (V)
(Approx.)
(+) (-)
M34 35
Ground Tilt switch ON
(UP operation)
Battery voltage
Other than above 0
42 Tilt switch ON
(DOWN operation)
Battery voltage
Other than above 0
LIIA0482E
Page 2990 of 3383
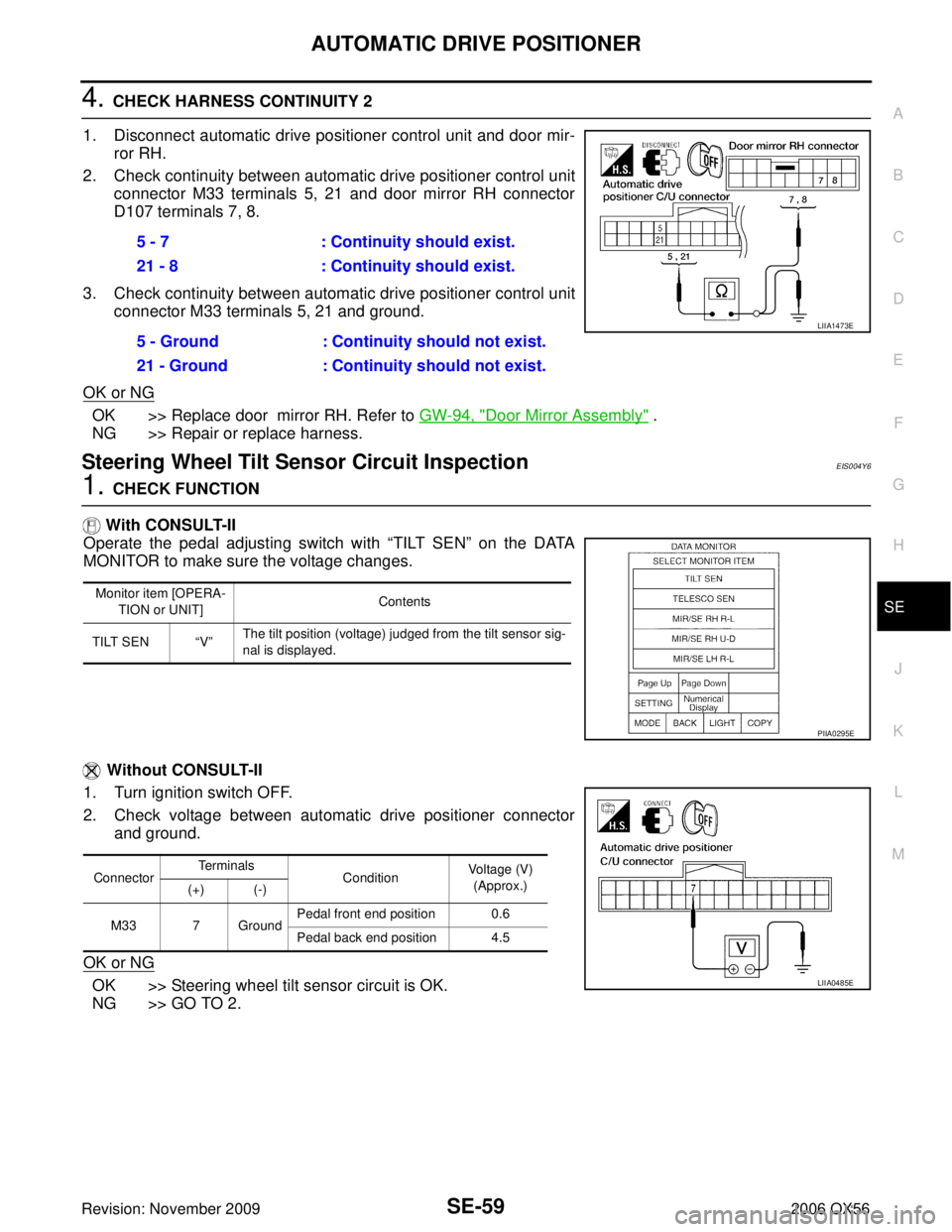
AUTOMATIC DRIVE POSITIONERSE-59
C
DE
F
G H
J
K L
M A
B
SE
Revision: November 2009 2006 QX56
4. CHECK HARNESS CONTINUITY 2
1. Disconnect automatic drive positioner control unit and door mir- ror RH.
2. Check continuity between automatic drive positioner control unit connector M33 terminals 5, 21 and door mirror RH connector
D107 terminals 7, 8.
3. Check continuity between automatic drive positioner control unit connector M33 terminals 5, 21 and ground.
OK or NG
OK >> Replace door mirror RH. Refer to GW-94, "Door Mirror Assembly" .
NG >> Repair or replace harness.
Steering Wheel Tilt Sensor Circuit InspectionEIS004Y6
1. CHECK FUNCTION
With CONSULT-II
Operate the pedal adjusting switch with “TILT SEN” on the DATA
MONITOR to make sure the voltage changes.
Without CONSULT-II
1. Turn ignition switch OFF.
2. Check voltage between automatic drive positioner connector and ground.
OK or NG
OK >> Steering wheel tilt sensor circuit is OK.
NG >> GO TO 2. 5 - 7
: Continuity should exist.
21 - 8 : Continuity should exist.
5 - Ground : Continuity should not exist.
21 - Ground : Continuity should not exist.
LIIA1473E
Monitor item [OPERA-
TION or UNIT] Contents
TILT SEN “V ” The tilt position (voltage) judged from the tilt sensor sig-
nal is displayed.
PIIA0295E
Connector Terminals
ConditionVoltage (V)
(Approx.)
(+) (-)
M33 7 Ground Pedal front end position 0.6
Pedal back end position 4.5
LIIA0485E
Page 2991 of 3383
SE-60
AUTOMATIC DRIVE POSITIONER
Revision: November 20092006 QX56
2. CHECK HARNESS CONTINUITY
1. Disconnect automatic drive positioner control unit and steering wheel tilt sensor.
2. Check continuity between automatic drive positioner connector M33, M34 terminals 7, 33, 41 and steering wheel tilt sensor con-
nector M69 terminals 2, 3, 4.
3. Check continuity between automatic drive positioner control unit connectors M33, M34 terminals 7, 33, 41 and ground.
OK or NG
OK >> Replace steering wheel tilt motor. Refer to PS-9, "TILT
MOTOR AND TILT SENSOR" .
NG >> Repair or replace harness. 7 - 3 : Continuity should exist.
33 - 2 : Continuity should exist.
41 - 4 : Continuity should exist.
7 - Ground : Continuity should not exist.
33 - Ground : Continuity should not exist.
41 - Ground : Continuity should not exist.
LIIA1432E
Page 3008 of 3383
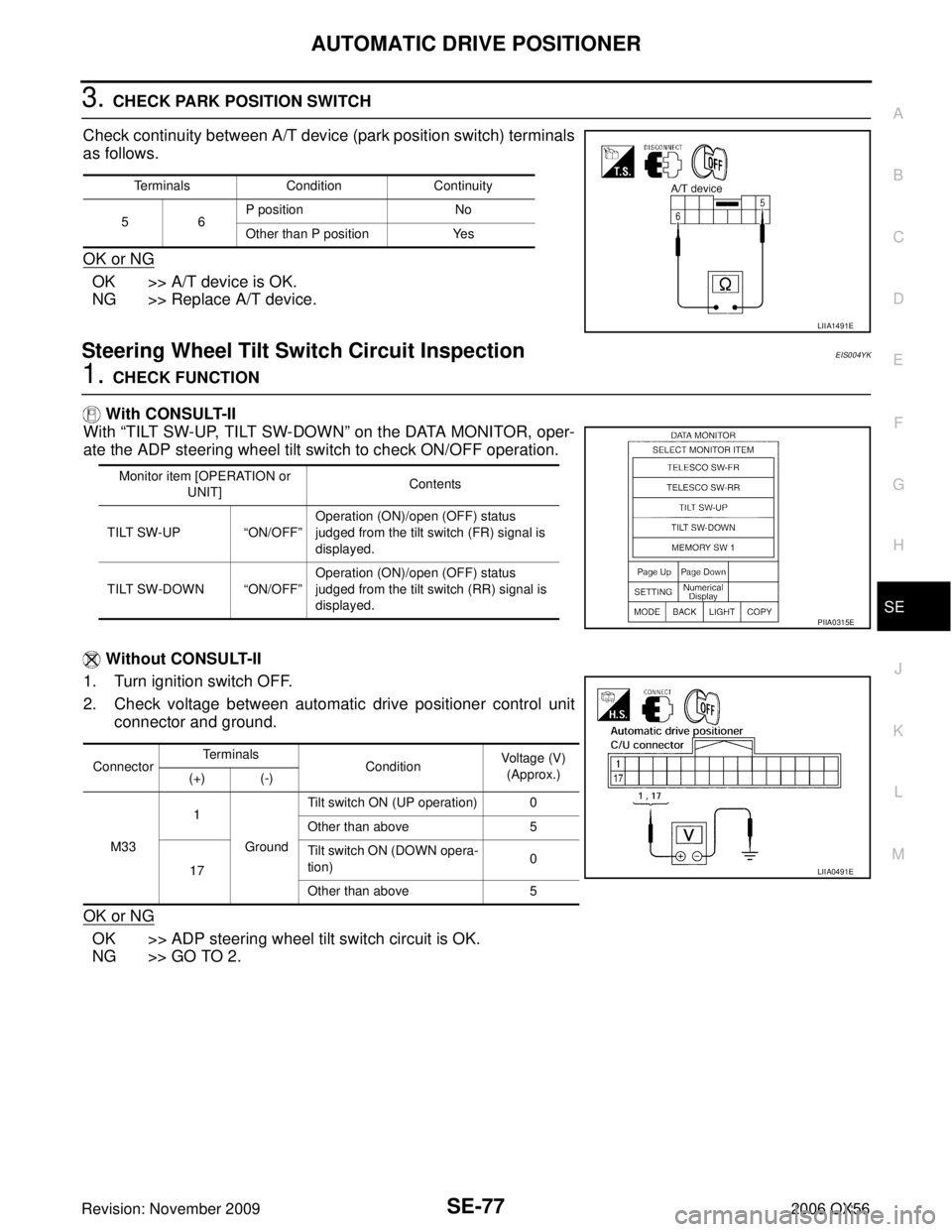
AUTOMATIC DRIVE POSITIONERSE-77
C
DE
F
G H
J
K L
M A
B
SE
Revision: November 2009 2006 QX56
3. CHECK PARK POSITION SWITCH
Check continuity between A/T device (park position switch) terminals
as follows.
OK or NG
OK >> A/T device is OK.
NG >> Replace A/T device.
Steering Wheel Tilt Switch Circuit InspectionEIS004YK
1. CHECK FUNCTION
With CONSULT-II
With “TILT SW-UP, TILT SW-DOWN ” on the DATA MONITOR, oper-
ate the ADP steering wheel tilt switch to check ON/OFF operation.
Without CONSULT-II
1. Turn ignition switch OFF.
2. Check voltage between automatic drive positioner control unit connector and ground.
OK or NG
OK >> ADP steering wheel tilt switch circuit is OK.
NG >> GO TO 2.
Terminals ConditionContinuity
56 P position
No
Other than P position Yes
LIIA1491E
Monitor item [OPERATION or
UNIT] Contents
TILT SW-UP “ON/OFF ”Operation (ON)/open (OFF) status
judged from the tilt switch (FR) signal is
displayed.
TILT SW-DOWN “ON/OFF ”Operation (ON)/open (OFF) status
judged from the tilt switch (RR) signal is
displayed.
PIIA0315E
Connector
Te r m i n a l s
ConditionVoltage (V)
(Approx.)
(+) (-)
M33 1
Ground Tilt switch ON (UP operation) 0
Other than above
5
17 Tilt switch ON (DOWN opera-
tion)
0
Other than above 5
LIIA0491E
Page 3009 of 3383
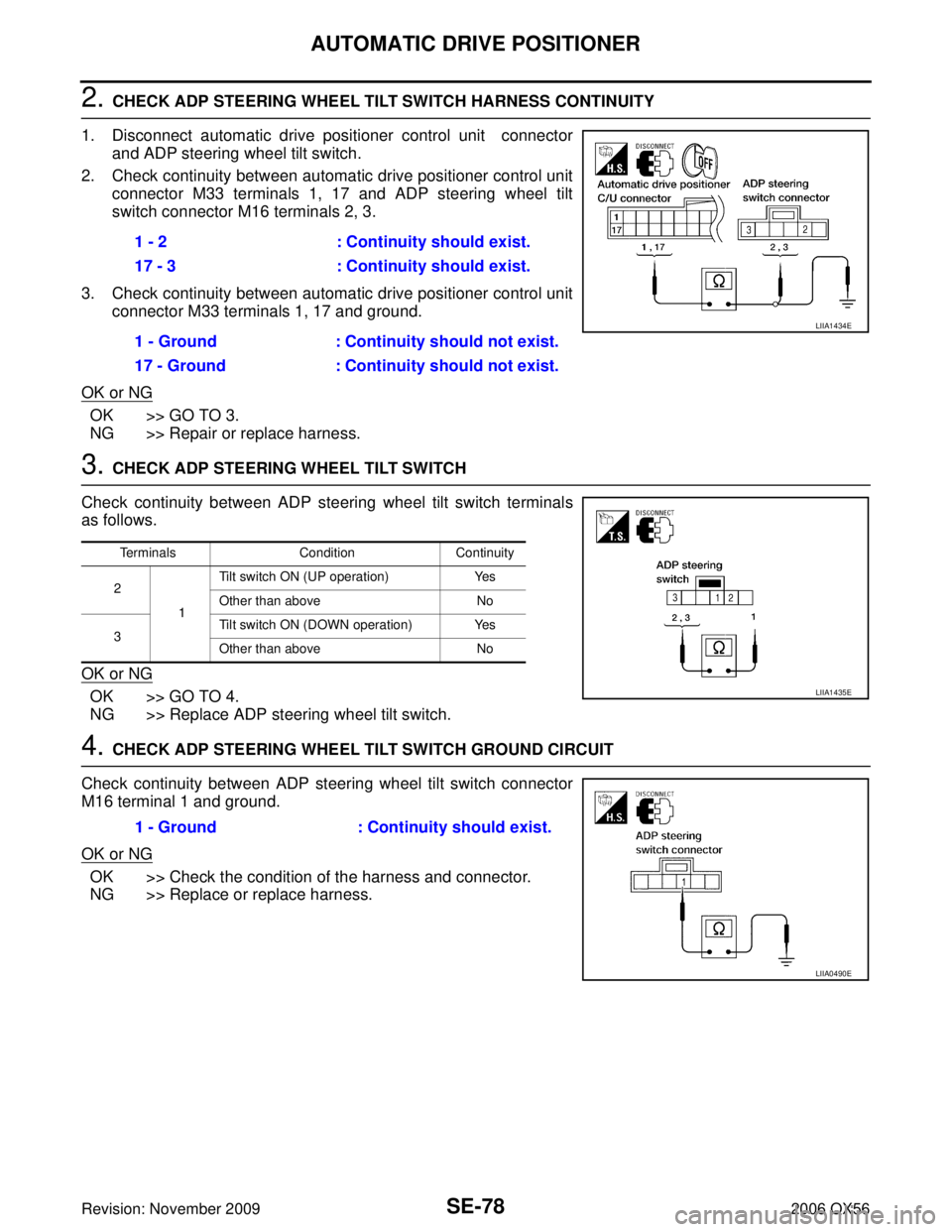
SE-78
AUTOMATIC DRIVE POSITIONER
Revision: November 20092006 QX56
2. CHECK ADP STEERING WHEEL TILT SWITCH HARNESS CONTINUITY
1. Disconnect automatic drive positioner control unit connector and ADP steering wheel tilt switch.
2. Check continuity between automatic drive positioner control unit connector M33 terminals 1, 17 and ADP steering wheel tilt
switch connector M16 terminals 2, 3.
3. Check continuity between automatic drive positioner control unit connector M33 terminals 1, 17 and ground.
OK or NG
OK >> GO TO 3.
NG >> Repair or replace harness.
3. CHECK ADP STEERING WHEEL TILT SWITCH
Check continuity between ADP steering wheel tilt switch terminals
as follows.
OK or NG
OK >> GO TO 4.
NG >> Replace ADP steering wheel tilt switch.
4. CHECK ADP STEERING WHEEL TILT SWITCH GROUND CIRCUIT
Check continuity between ADP steering wheel tilt switch connector
M16 terminal 1 and ground.
OK or NG
OK >> Check the condition of the harness and connector.
NG >> Replace or replace harness. 1 - 2
: Continuity should exist.
17 - 3 : Continuity should exist.
1 - Ground : Continuity should not exist.
17 - Ground : Continuity should not exist.
LIIA1434E
Terminals ConditionContinuity
2 1Tilt switch ON (UP operation)
Yes
Other than above No
3 Tilt switch ON (DOWN operation) Yes
Other than above
No
LIIA1435E
1 - Ground: Continuity should exist.
LIIA0490E
Page 3044 of 3383
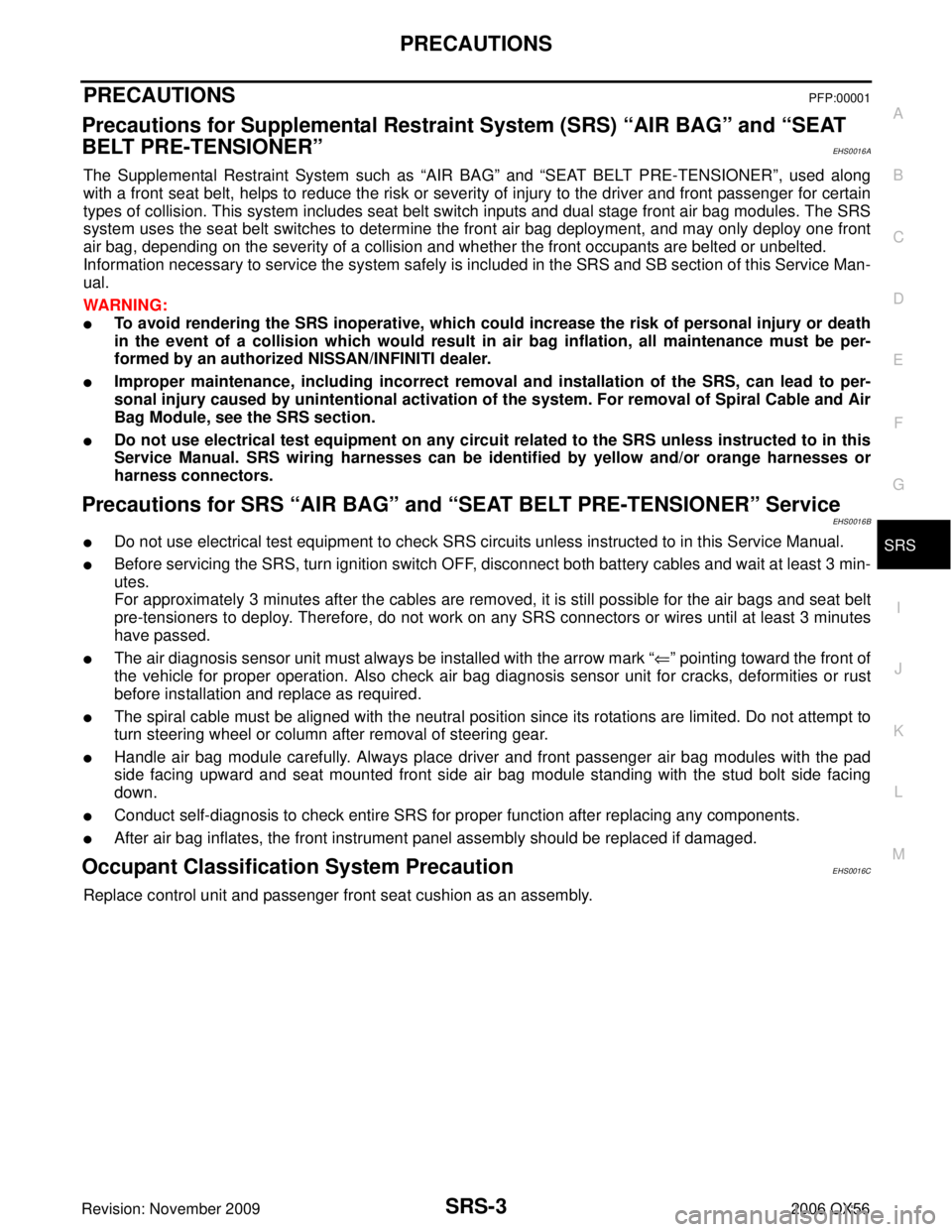
PRECAUTIONSSRS-3
C
DE
F
G
I
J
K L
M A
B
SRS
Revision: November 2009 2006 QX56
PRECAUTIONSPFP:00001
Precautions for Supplemental Restraint System (SRS) “AIR BAG” and “SEAT
BELT PRE-TENSIONER”
EHS0016A
The Supplemental Restraint System such as “AIR BAG” and “SEAT BELT PRE-TENSIONER ”, used along
with a front seat belt, helps to reduce the risk or severity of injury to the driver and front passenger for certain
types of collision. This system includes seat belt switch inputs and dual stage front air bag modules. The SRS
system uses the seat belt switches to determine the front air bag deployment, and may only deploy one front
air bag, depending on the severity of a collision and whether the front occupants are belted or unbelted.
Information necessary to service the system safely is included in the SRS and SB section of this Service Man-
ual.
WARNING:
To avoid rendering the SRS inoperative, which could increase the risk of personal injury or death
in the event of a collision which would result in air bag inflation, all maintenance must be per-
formed by an authorized NISSAN/INFINITI dealer.
Improper maintenance, including incorrect removal and installation of the SRS, can lead to per-
sonal injury caused by unintentional activation of the system. For removal of Spiral Cable and Air
Bag Module, see the SRS section.
Do not use electrical test equipment on any circuit related to the SRS unless instructed to in this
Service Manual. SRS wiring harnesses can be identified by yellow and/or orange harnesses or
harness connectors.
Precautions for SRS “AIR BAG” and “SEAT BELT PRE-TENSIONER” ServiceEHS0016B
Do not use electrical test equipment to check SRS circuits unless instructed to in this Service Manual.
Before servicing the SRS, turn ignition switch OFF, disconnect both battery cables and wait at least 3 min-
utes.
For approximately 3 minutes after the cables are removed, it is still possible for the air bags and seat belt
pre-tensioners to deploy. Therefore, do not work on any SRS connectors or wires until at least 3 minutes
have passed.
The air diagnosis sensor unit must always be installed with the arrow mark “⇐” pointing toward the front of
the vehicle for proper operation. Also check air bag diagnosis sensor unit for cracks, deformities or rust
before installation and replace as required.
The spiral cable must be aligned with the neutral position since its rotations are limited. Do not attempt to
turn steering wheel or column after removal of steering gear.
Handle air bag module carefully. Always place driver and front passenger air bag modules with the pad
side facing upward and seat mounted front side air bag module standing with the stud bolt side facing
down.
Conduct self-diagnosis to check entire SRS for proper function after replacing any components.
After air bag inflates, the front instrument panel assembly should be replaced if damaged.
Occupant Classification System PrecautionEHS0016C
Replace control unit and passenger front seat cushion as an assembly.
Page 3045 of 3383
SRS-4
PREPARATION
Revision: November 20092006 QX56
PREPARATIONPFP:00002
Special Service ToolsEHS0016E
The actual shapes of Kent-Moore tools may differ from those of special service tools illustrated here.
Commercial Service ToolsEHS0016F
Tool number
(Kent-Moore No.)
Tool nameDescription
—
(J-42057)
Air bag lock master key set Removing and installing air bag lock
LRS210
Tool name
(Kent-Moore No.)
Description
Steering wheel puller
(J-1859A) Removing steering wheel
Steering wheel puller legs
(J-42578) Removing steering wheel
LHIA0043E
LHIA0044E
Page 3087 of 3383
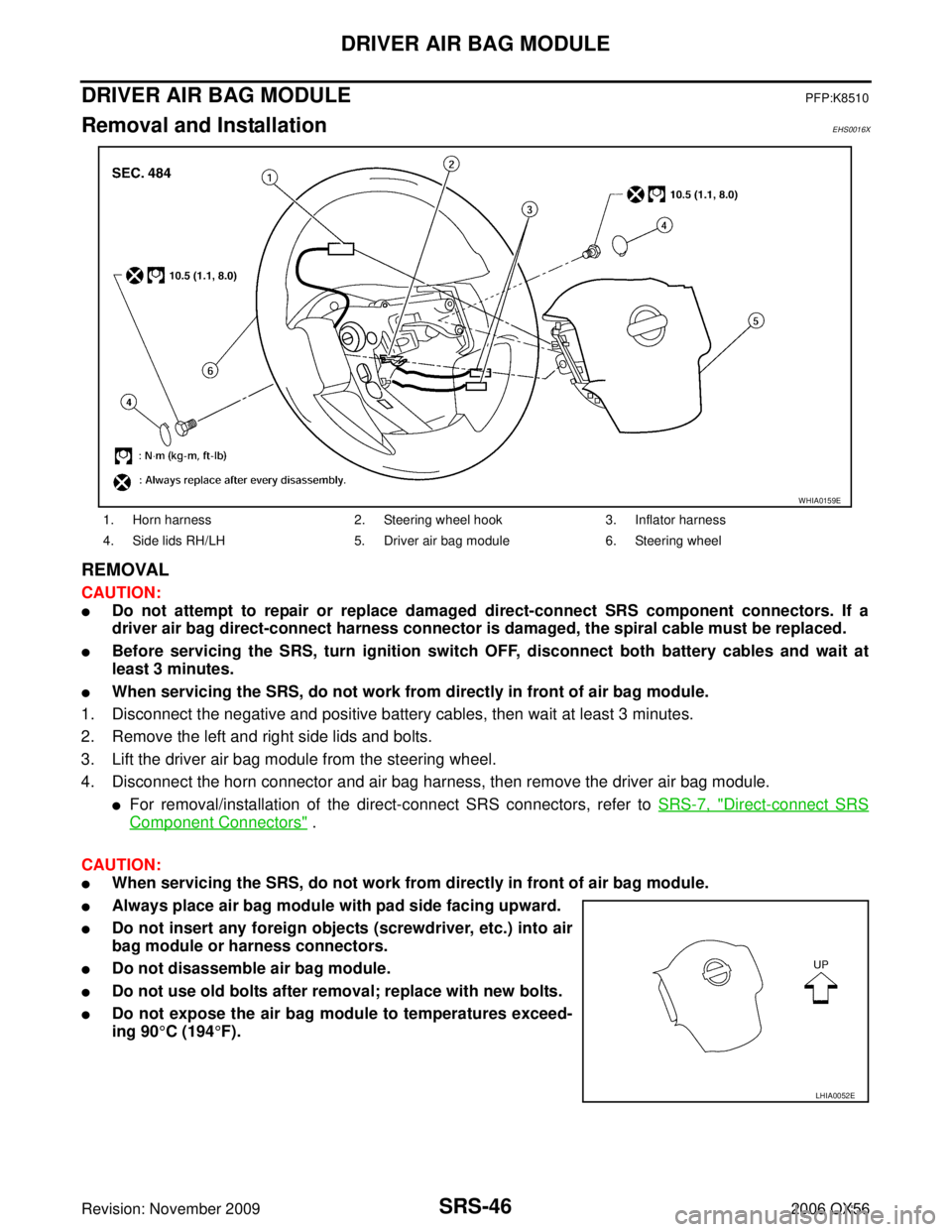
SRS-46
DRIVER AIR BAG MODULE
Revision: November 20092006 QX56
DRIVER AIR BAG MODULEPFP:K8510
Removal and InstallationEHS0016X
REMOVAL
CAUTION:
Do not attempt to repair or replace damaged direct-connect SRS component connectors. If a
driver air bag direct-connect harness connector is damaged, the spiral cable must be replaced.
Before servicing the SRS, turn ignition switch OFF, disconnect both battery cables and wait at
least 3 minutes.
When servicing the SRS, do not work from directly in front of air bag module.
1. Disconnect the negative and positive battery cables, then wait at least 3 minutes.
2. Remove the left and right side lids and bolts.
3. Lift the driver air bag module from the steering wheel.
4. Disconnect the horn connector and air bag harness, then remove the driver air bag module.
For removal/installation of the direct-connect SRS connectors, refer to SRS-7, "Direct-connect SRS
Component Connectors" .
CAUTION:
When servicing the SRS, do not work from directly in front of air bag module.
Always place air bag module with pad side facing upward.
Do not insert any foreign objects (screwdriver, etc.) into air
bag module or harness connectors.
Do not disassemble air bag module.
Do not use old bolts after removal; replace with new bolts.
Do not expose the air bag module to temperatures exceed-
ing 90 °C (194 °F).
1. Horn harness 2. Steering wheel hook 3. Inflator harness
4. Side lids RH/LH 5. Driver air bag module 6. Steering wheel
WHIA0159E
LHIA0052E