Page 2621 of 3383
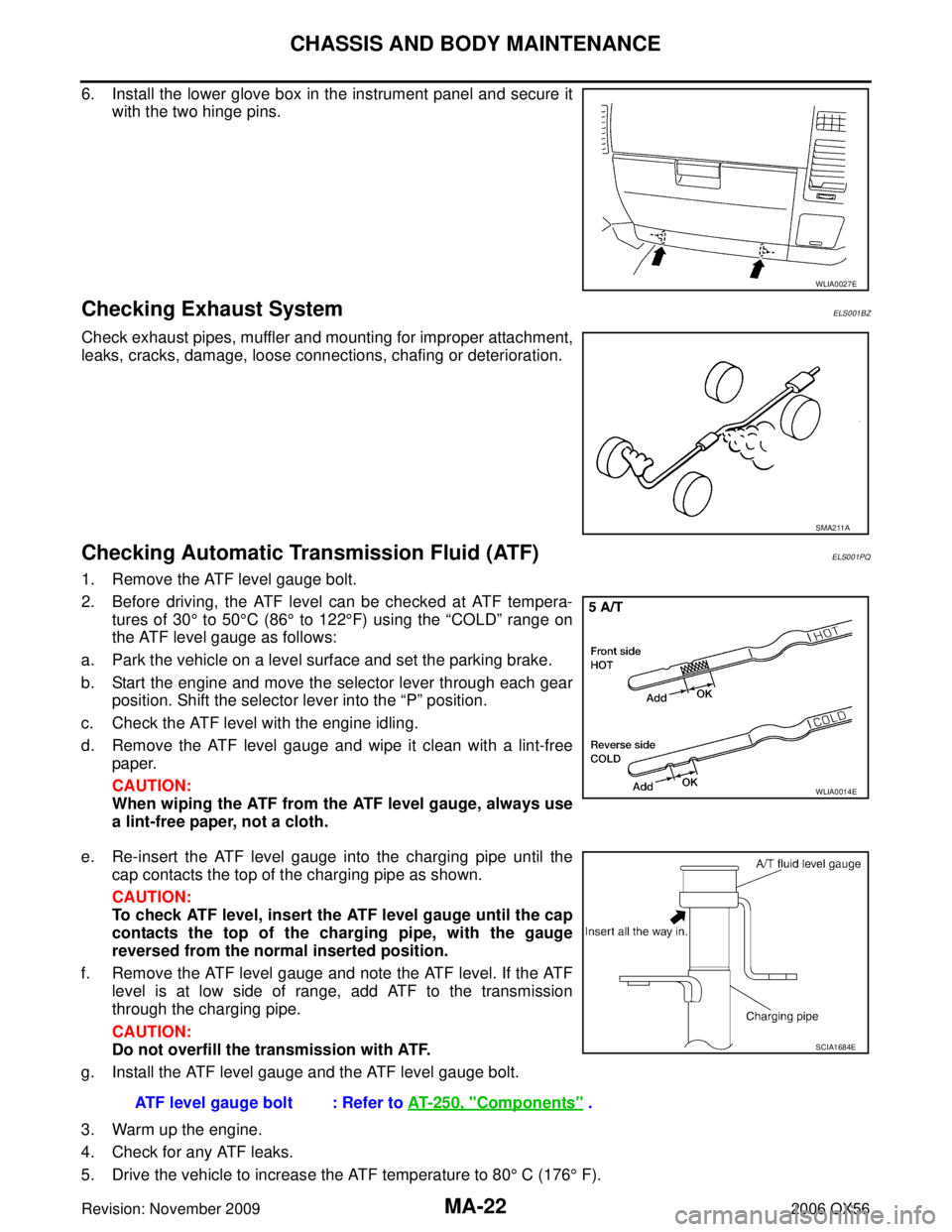
MA-22
CHASSIS AND BODY MAINTENANCE
Revision: November 20092006 QX56
6. Install the lower glove box in the instrument panel and secure it
with the two hinge pins.
Checking Exhaust SystemELS001BZ
Check exhaust pipes, muffler and mounting for improper attachment,
leaks, cracks, damage, loose connections, chafing or deterioration.
Checking Automatic Transmission Fluid (ATF)ELS001PQ
1. Remove the ATF level gauge bolt.
2. Before driving, the ATF level can be checked at ATF tempera-tures of 30 ° to 50 °C (86 ° to 122 °F) using the “COLD” range on
the ATF level gauge as follows:
a. Park the vehicle on a level surface and set the parking brake.
b. Start the engine and move the selector lever through each gear position. Shift the selector lever into the “P” position.
c. Check the ATF level with the engine idling.
d. Remove the ATF level gauge and wipe it clean with a lint-free paper.
CAUTION:
When wiping the ATF from the ATF level gauge, always use
a lint-free paper, not a cloth.
e. Re-insert the ATF level gauge into the charging pipe until the cap contacts the top of the charging pipe as shown.
CAUTION:
To check ATF level, insert the ATF level gauge until the cap
contacts the top of the charging pipe, with the gauge
reversed from the normal inserted position.
f. Remove the ATF level gauge and note the ATF level. If the ATF level is at low side of range, add ATF to the transmission
through the charging pipe.
CAUTION:
Do not overfill the transmission with ATF.
g. Install the ATF level gauge and the ATF level gauge bolt.
3. Warm up the engine.
4. Check for any ATF leaks.
5. Drive the vehicle to increase the ATF temperature to 80 ° C (176 ° F).
WLIA0027E
SMA211A
WLIA0014E
ATF level gauge bolt : Refer to AT- 2 5 0 , "Components" .
SCIA1684E
Page 2624 of 3383
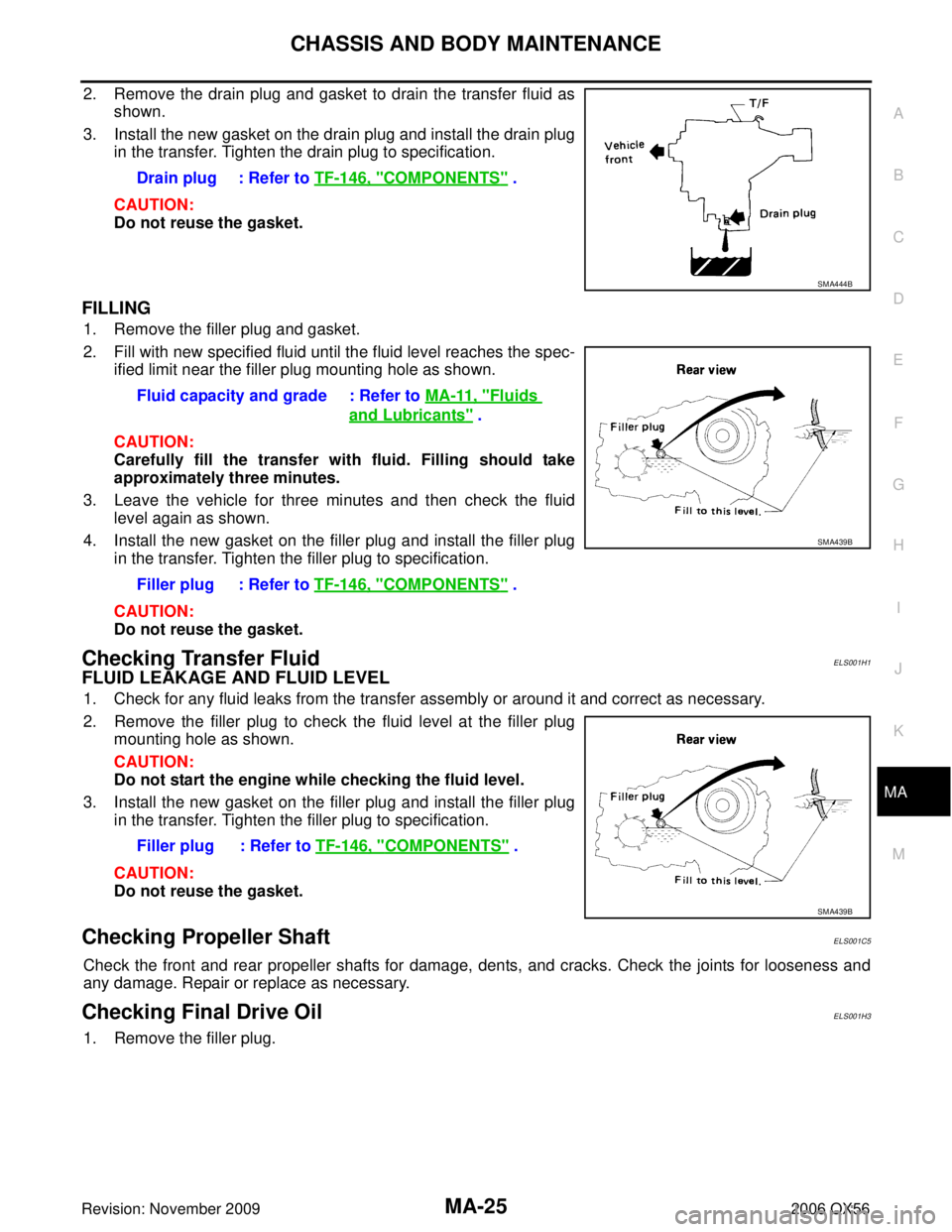
CHASSIS AND BODY MAINTENANCEMA-25
C
DE
F
G H
I
J
K
M A
B
MA
Revision: November 2009 2006 QX56
2. Remove the drain plug and gasket to drain the transfer fluid as
shown.
3. Install the new gasket on the drain plug and install the drain plug in the transfer. Tighten the drain plug to specification.
CAUTION:
Do not reuse the gasket.
FILLING
1. Remove the filler plug and gasket.
2. Fill with new specified fluid until the fluid level reaches the spec-ified limit near the filler plug mounting hole as shown.
CAUTION:
Carefully fill the transfer with fluid. Filling should take
approximately three minutes.
3. Leave the vehicle for three minutes and then check the fluid level again as shown.
4. Install the new gasket on the filler plug and install the filler plug in the transfer. Tighten the filler plug to specification.
CAUTION:
Do not reuse the gasket.
Checking Transfer FluidELS001H1
FLUID LEAKAGE AND FLUID LEVEL
1. Check for any fluid leaks from the transfer assembly or around it and correct as necessary.
2. Remove the filler plug to check the fluid level at the filler plugmounting hole as shown.
CAUTION:
Do not start the engine while checking the fluid level.
3. Install the new gasket on the filler plug and install the filler plug in the transfer. Tighten the filler plug to specification.
CAUTION:
Do not reuse the gasket.
Checking Propeller ShaftELS001C5
Check the front and rear propeller shafts for damage, dents, and cracks. Check the joints for looseness and
any damage. Repair or replace as necessary.
Checking Final Drive OilELS001H3
1. Remove the filler plug. Drain plug : Refer to
TF-146, "
COMPONENTS" .
SMA444B
Fluid capacity and grade : Refer to MA-11, "Fluids
and Lubricants" .
Filler plug : Refer to TF-146, "
COMPONENTS" .
SMA439B
Filler plug : Refer to TF-146, "COMPONENTS" .
SMA439B
Page 2627 of 3383
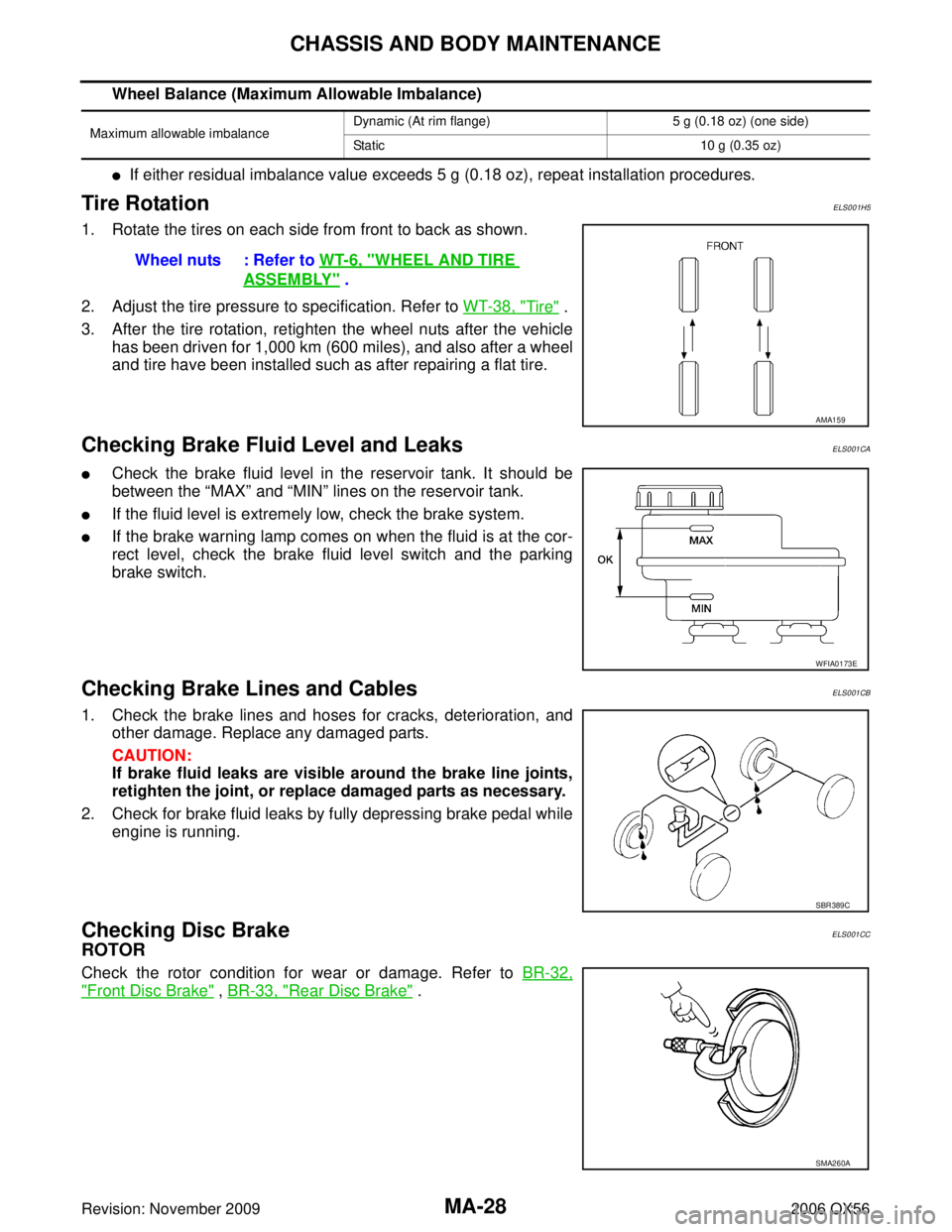
MA-28
CHASSIS AND BODY MAINTENANCE
Revision: November 20092006 QX56
Wheel Balance (Maximum Allowable Imbalance)
If either residual imbalance value exceeds 5 g (0.18 oz), repeat installation procedures.
Tire RotationELS001H5
1. Rotate the tires on each side from front to back as shown.
2. Adjust the tire pressure to specification. Refer to WT-38, "
Tire" .
3. After the tire rotation, retighten the wheel nuts after the vehicle has been driven for 1,000 km (600 miles), and also after a wheel
and tire have been installed such as after repairing a flat tire.
Checking Brake Fluid Level and LeaksELS001CA
Check the brake fluid level in the reservoir tank. It should be
between the “MAX ” and “MIN” lines on the reservoir tank.
If the fluid level is extremely low, check the brake system.
If the brake warning lamp comes on when the fluid is at the cor-
rect level, check the brake fluid level switch and the parking
brake switch.
Checking Brake Lines and CablesELS001CB
1. Check the brake lines and hoses for cracks, deterioration, and
other damage. Replace any damaged parts.
CAUTION:
If brake fluid leaks are visible around the brake line joints,
retighten the joint, or replace damaged parts as necessary.
2. Check for brake fluid leaks by fully depressing brake pedal while engine is running.
Checking Disc BrakeELS001CC
ROTOR
Check the rotor condition for wear or damage. Refer to BR-32,
"Front Disc Brake" , BR-33, "Rear Disc Brake" .
Maximum allowable imbalance Dynamic (At rim flange)
5 g (0.18 oz) (one side)
Static 10 g (0.35 oz)
Wheel nuts : Refer to WT-6, "WHEEL AND TIRE
ASSEMBLY" .
AMA159
WFIA0173E
SBR389C
SMA260A
Page 2629 of 3383
MA-30
CHASSIS AND BODY MAINTENANCE
Revision: November 20092006 QX56
CHECKING LINES
Check lines for improper attachment, leaks, cracks, damage,
loose connections, chafing, and deterioration.
Checking Axle and Suspension PartsELS001CF
FRONT AND REAR AXLE AND SUSPENSION PARTS
Check front and rear axle and suspension parts for excessive play, cracks, wear or other damage.
Shake each wheel to check for excessive play.
Rotate each wheel to check for abnormal noise.
Check the axle and suspension nuts and bolts for looseness.
Check the strut and shock absorber for oil leakage or other damage.
Check the suspension ball joints for grease leakage and ball joint dust cover for cracks or other damage.
DRIVE SHAFT
Check the boots and drive shaft for cracks, wear, damage, and
grease leakage.
SGIA0506E
SMA525A
SFA901
Page 2634 of 3383
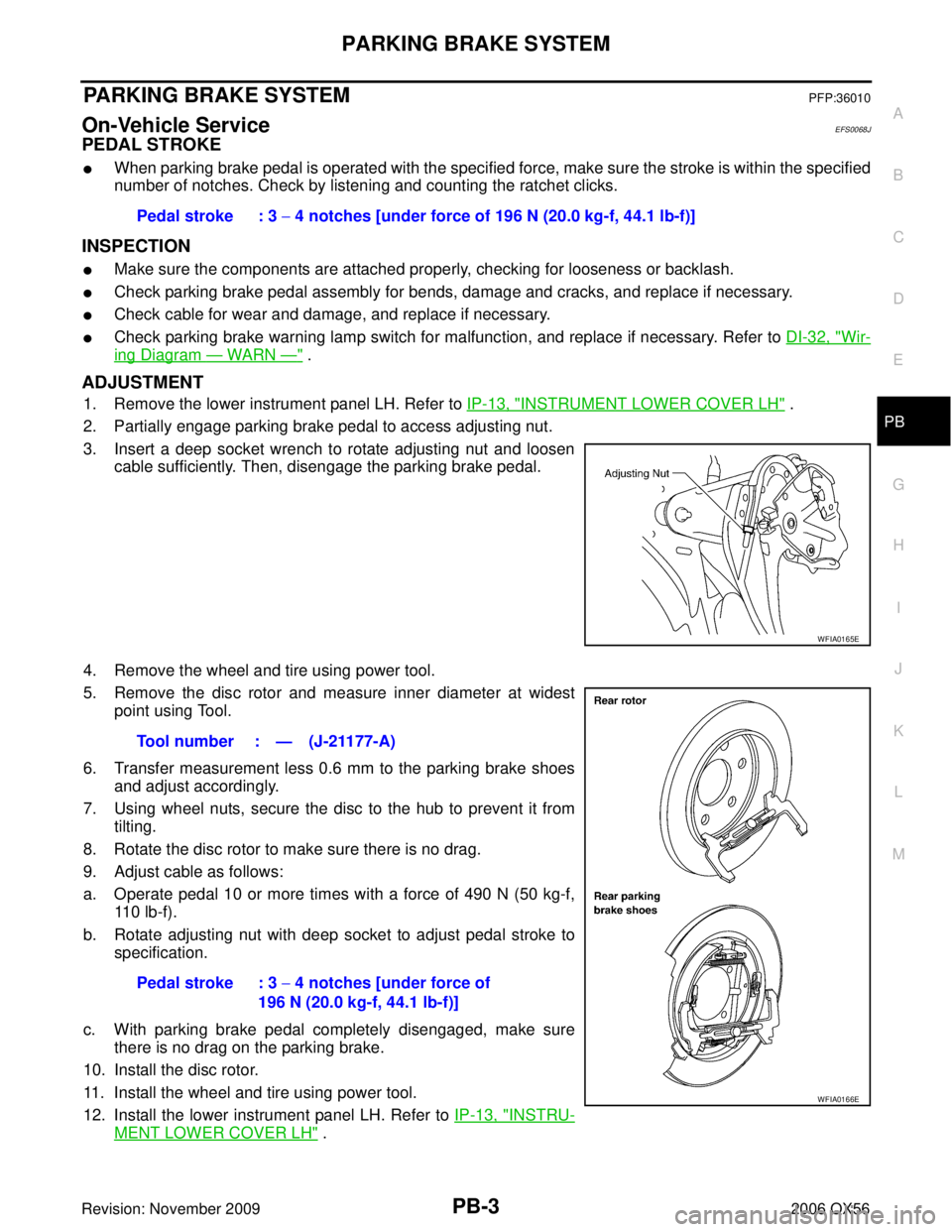
PARKING BRAKE SYSTEMPB-3
C
DE
G H
I
J
K L
M A
B
PB
Revision: November 2009 2006 QX56
PARKING BRAKE SYSTEMPFP:36010
On-Vehicle ServiceEFS0068J
PEDAL STROKE
When parking brake pedal is operated with the specified force, make sure the stroke is within the specified
number of notches. Check by listening and counting the ratchet clicks.
INSPECTION
Make sure the components are attached properly, checking for looseness or backlash.
Check parking brake pedal assembly for bends, damage and cracks, and replace if necessary.
Check cable for wear and damage, and replace if necessary.
Check parking brake warning lamp switch for malfunction, and replace if necessary. Refer to DI-32, "Wir-
ing Diagram — WARN —" .
ADJUSTMENT
1. Remove the lower instrument panel LH. Refer to IP-13, "INSTRUMENT LOWER COVER LH" .
2. Partially engage parking brake pedal to access adjusting nut.
3. Insert a deep socket wrench to rotate adjusting nut and loosen cable sufficiently. Then, disengage the parking brake pedal.
4. Remove the wheel and tire using power tool.
5. Remove the disc rotor and measure inner diameter at widest point using Tool.
6. Transfer measurement less 0.6 mm to the parking brake shoes and adjust accordingly.
7. Using wheel nuts, secure the disc to the hub to prevent it from tilting.
8. Rotate the disc rotor to make sure there is no drag.
9. Adjust cable as follows:
a. Operate pedal 10 or more times with a force of 490 N (50 kg-f, 110 lb-f).
b. Rotate adjusting nut with deep socket to adjust pedal stroke to specification.
c. With parking brake pedal completely disengaged, make sure there is no drag on the parking brake.
10. Install the disc rotor.
11. Install the wheel and tire using power tool.
12. Install the lower instrument panel LH. Refer to IP-13, "
INSTRU-
MENT LOWER COVER LH" .
Pedal stroke : 3
− 4 notches [under force of 196 N (20.0 kg-f, 44.1 lb-f)]
WFIA0165E
Tool number : — (J-21177-A)
Pedal stroke : 3 − 4 notches [under force of
196 N (20.0 kg-f, 44.1 lb-f)]
WFIA0166E
Page 2638 of 3383
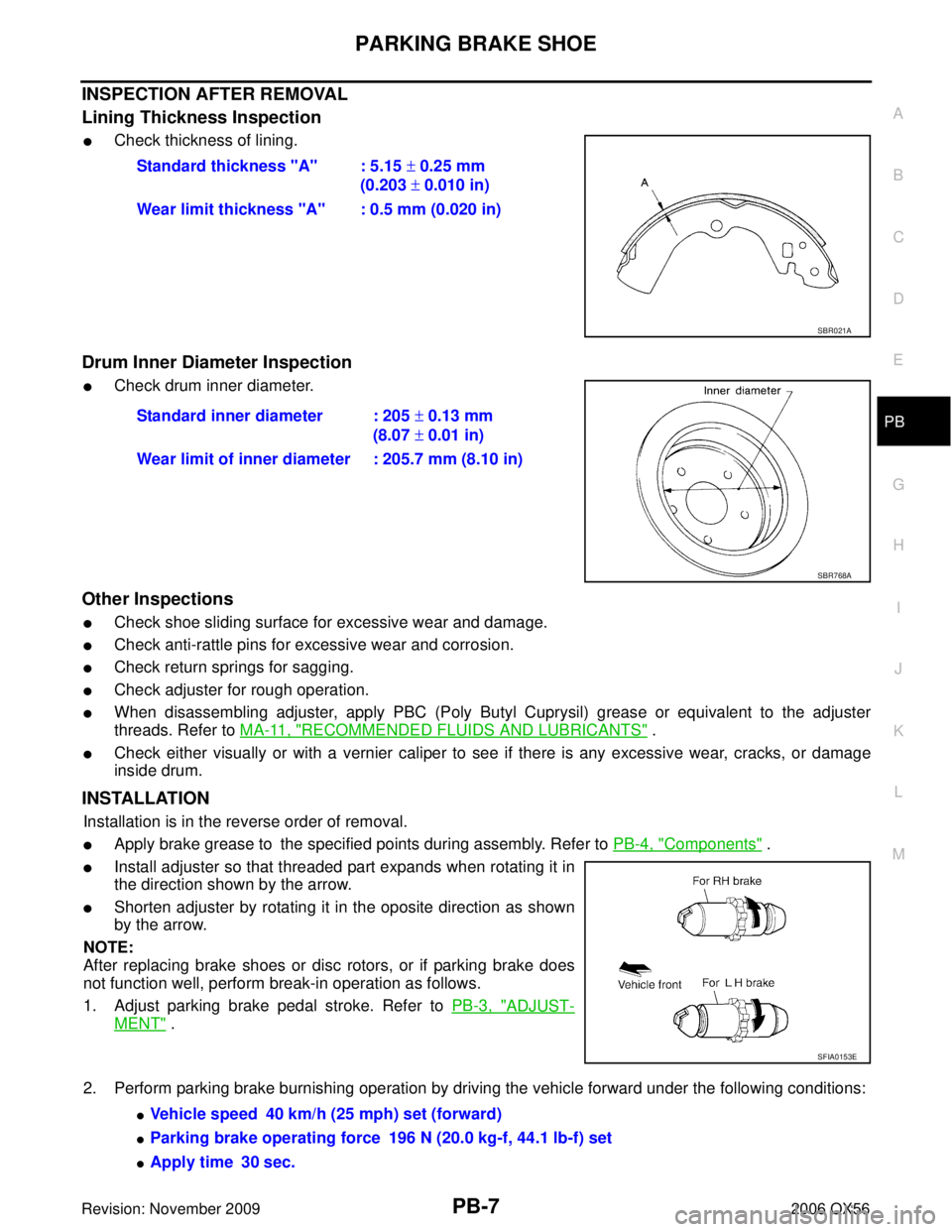
PARKING BRAKE SHOEPB-7
C
DE
G H
I
J
K L
M A
B
PB
Revision: November 2009 2006 QX56
INSPECTION AFTER REMOVAL
Lining Thickness Inspection
Check thickness of lining.
Drum Inner Diameter Inspection
Check drum inner diameter.
Other Inspections
Check shoe sliding surface for excessive wear and damage.
Check anti-rattle pins for excessive wear and corrosion.
Check return springs for sagging.
Check adjuster for rough operation.
When disassembling adjuster, apply PBC (Poly Butyl Cuprysil) grease or equivalent to the adjuster
threads. Refer to MA-11, "
RECOMMENDED FLUIDS AND LUBRICANTS" .
Check either visually or with a vernier caliper to see if there is any excessive wear, cracks, or damage
inside drum.
INSTALLATION
Installation is in the reverse order of removal.
Apply brake grease to the specified points during assembly. Refer to PB-4, "Components" .
Install adjuster so that threaded part expands when rotating it in
the direction shown by the arrow.
Shorten adjuster by rotating it in the oposite direction as shown
by the arrow.
NOTE:
After replacing brake shoes or disc rotors, or if parking brake does
not function well, perform break-in operation as follows.
1. Adjust parking brake pedal stroke. Refer to PB-3, "
ADJUST-
MENT" .
2. Perform parking brake burnishing operation by driving the vehicle forward under the following conditions: Standard thickness "A" : 5.15
± 0.25 mm
(0.203 ± 0.010 in)
Wear limit thickness "A" : 0.5 mm (0.020 in)
SBR021A
Standard inner diameter : 205 ± 0.13 mm
(8.07 ± 0.01 in)
Wear limit of inner diameter : 205.7 mm (8.10 in)
SBR768A
SFIA0153E
Vehicle speed 40 km/h (25 mph) set (forward)
Parking brake operating force 196 N (20.0 kg-f, 44.1 lb-f) set
Apply time 30 sec.
Page 2710 of 3383
HARNESS CONNECTORPG-69
C
DE
F
G H
I
J
L
M A
B
PG
Revision: November 2009 2006 QX56
HARNESS CONNECTOR (SLIDE-LOCKING TYPE)
A new style slide-locking type connector is used on certain systems and components, especially those
related to OBD.
The slide-locking type connectors help prevent incomplete locking and accidental looseness or discon-
nection.
The slide-locking type connectors are disconnected by pushing or pulling the slider. Refer to the illustra-
tion below.
CAUTION:
Do not pull the harness or wires when disconnecting the connector.
Be careful not to damage the connector support bracket when disconnecting the connector.
[Example]
AEL299C
Page 2723 of 3383
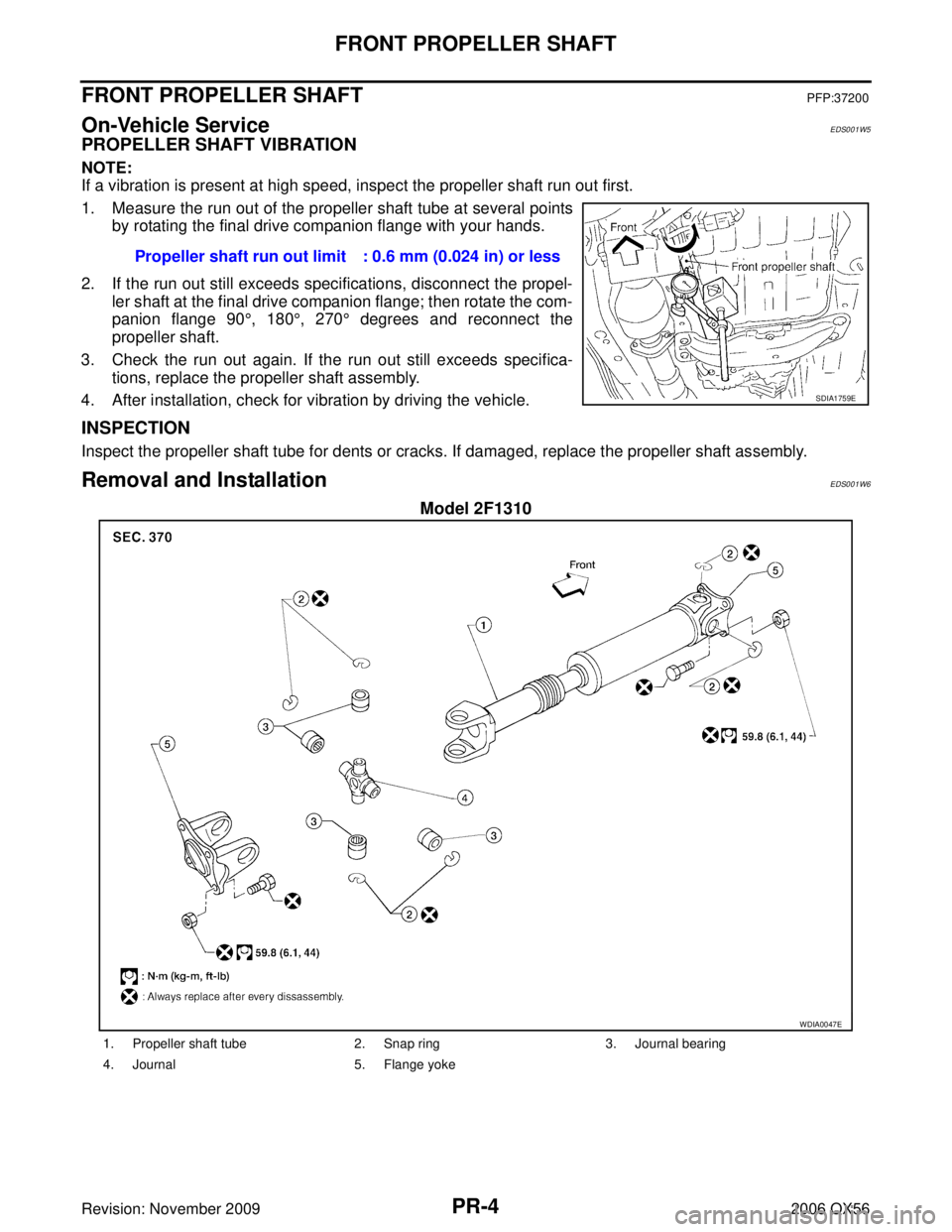
PR-4
FRONT PROPELLER SHAFT
Revision: November 20092006 QX56
FRONT PROPELLER SHAFTPFP:37200
On-Vehicle ServiceEDS001W5
PROPELLER SHAFT VIBRATION
NOTE:
If a vibration is present at high speed, inspect the propeller shaft run out first.
1. Measure the run out of the propeller shaft tube at several points
by rotating the final drive companion flange with your hands.
2. If the run out still exceeds specifications, disconnect the propel- ler shaft at the final drive companion flange; then rotate the com-
panion flange 90 °, 180 °, 270 ° degrees and reconnect the
propeller shaft.
3. Check the run out again. If the run out still exceeds specifica- tions, replace the propeller shaft assembly.
4. After installation, check for vibration by driving the vehicle.
INSPECTION
Inspect the propeller shaft tube for dents or cracks. If damaged, replace the propeller shaft assembly.
Removal and InstallationEDS001W6
Model 2F1310
Propeller shaft run out limit : 0.6 mm (0.024 in) or less
SDIA1759E
WDIA0047E
1. Propeller shaft tube 2. Snap ring 3. Journal bearing
4. Journal 5. Flange yoke