Page 1540 of 5135
I35662
EAU
AU2 ºVOICEº switch
S15
±
DIAGNOSTICS NAVIGATION SYSTEM
05±1495
AVENSIS REPAIR MANUAL (RM1018E)
INSPECTION PROCEDURE
1INSPECT STEERING WHEEL ASSY(BEEP SOUND)
(a)Check the switch (Beep sound).
(1)Press steering pad switch LH to check that the beep sound is produced.
OKGo to step 3
NG
2INSPECT STEERING WHEEL ASSY(AU2, EAU)
(a)Remove the horn button assy(See page 50±9).
(b)Check continuity between the terminals at each condi- tion, as shown in the chart.
Tester connectionConditionSpecified condition
AU2 ± EAUDo not switch positionApprox. 100 k
AU2 ± EAUVOICE switch: pushApprox. 3.1 k
NGREPLACE STEERING WHEEL ASSY
(See page 50±9)
OK
3 CHECK TALK BACK
(a) Check whether the system performs talk back or not. Standard: The system performs talk back.
OK SYSTEM OK
NG
Page 1740 of 5135
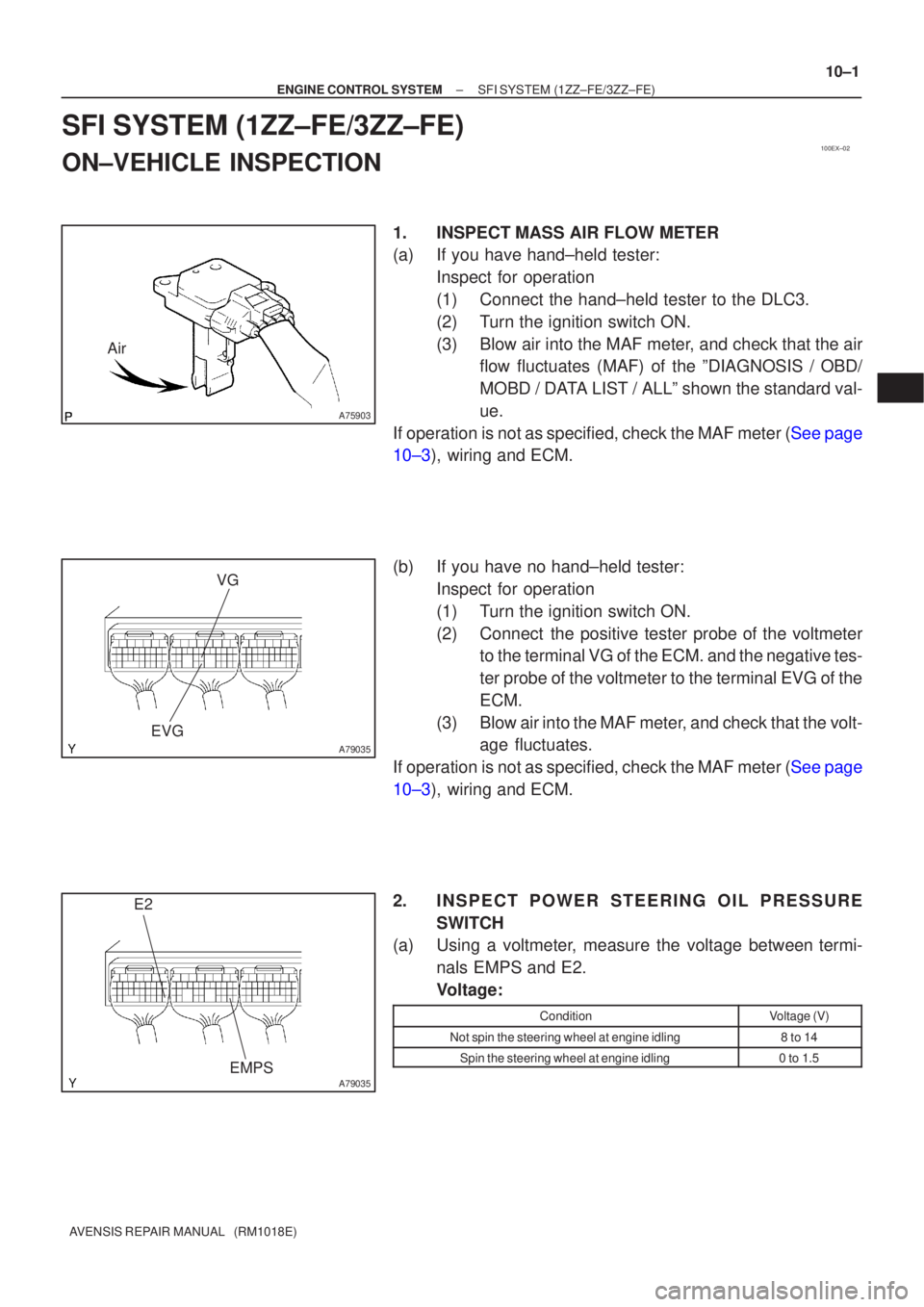
100EX±02
A75903
Air
A79035
VG
EVG
A79035
E2
EMPS
±
ENGINE CONTROL SYSTEM SFI SYSTEM(1ZZ±FE/3ZZ±FE)
10±1
AVENSIS REPAIR MANUAL (RM1018E)
SFI SYSTEM(1ZZ±FE/3ZZ±FE)
ON±VEHICLE INSPECTION
1.INSPECTMASS AIR FLOW METER
(a)If you have hand±held tester:
Inspect for operation
(1)Connect the hand±held tester to the DLC3.
(2)Turn the ignition switch ON.
(3)Blow air into the MAF meter, and check that the airflow fluctuates (MAF) of the ºDIAGNOSIS / OBD/
MOBD / DATA LIST / ALLº shown the standard val-
ue.
If operation is not as specified, check the MAF meter (See page
10±3), wiring and ECM.
(b)If you have no hand±held tester: Inspect for operation
(1)Turn the ignition switch ON.
(2)Connect the positive tester probe of the voltmeterto the terminal VG of the ECM. and the negative tes-
ter probe of the voltmeter to the terminal EVG of the
ECM.
(3)Blow air into the MAF meter, and check that the volt- age fluctuates.
If operation is not as specified, check the MAF meter (See page
10±3), wiring and ECM.
2. INSPECT POWER STEERING OIL PRESSURE SWITCH
(a) Using a voltmeter, measure the voltage between termi-
nals EMPS and E2.
Voltage:
ConditionVoltage (V)
Not spin the steering wheel at engine idling8 to 14
Spin the steering wheel at engine idling0 to 1.5
Page 1756 of 5135
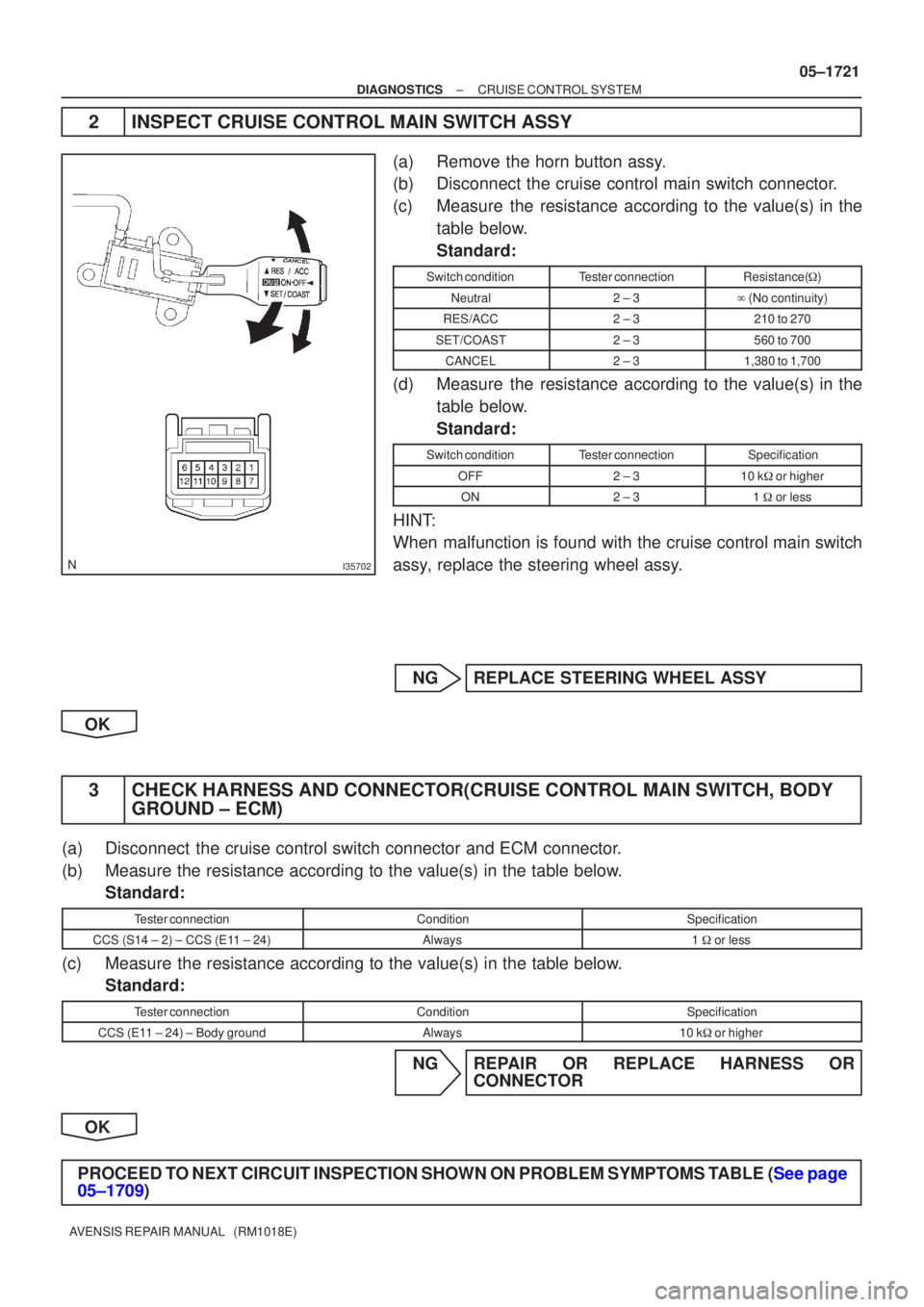
I35702
±
DIAGNOSTICS CRUISE CONTROL SYSTEM
05±1721
AVENSIS REPAIR MANUAL (RM1018E)
2INSPECT CRUISE CONTROL MAIN SWITCH ASSY
(a)Remove the horn button assy.
(b)Disconnect the cruise control main switch connector.
(c)Measure the resistance according to the value(s) in the
table below.
Standard:
Switch conditionTester connectionResistance( )
Neutral2 ± 3 (No continuity)
RES/ACC2 ± 3210 to 270
SET/COAST2 ± 3560 to 700
CANCEL2 ± 31,380 to 1,700
(d)Measure the resistance according to the value(s) in the
table below.
Standard:
Switch conditionTester connectionSpecification
OFF2 ± 310 k or higher
ON2 ± 31 or less
HINT:
When malfunction is found with the cruise control main switch
assy, replace the steering wheel assy.
NGREPLACE STEERING WHEEL ASSY
OK
3CHECK HARNESS AND CONNECTOR(CRUISE CONTROL MAIN SWITCH, BODY GROUND ± ECM)
(a)Disconnect the cruise control switch connector and ECM connector.
(b)Measure the resistance according to the value(s) in the table below.
Standard:
Tester connectionConditionSpecification
CCS (S14 ± 2) ± CCS (E11 ± 24)Always1 or less
(c)Measure the resistance according to the value(s) in the table below.
Standard:
Tester connectionConditionSpecification
CCS (E11 ± 24) ± Body groundAlways10 k or higher
NGREPAIR OR REPLACE HARNESS OR
CONNECTOR
OK
PROCEED TO NEXT CIRCUIT INSPECTION SHOWN ON PROBLEM SYMPTOMS TABLE (See page
05±1709)
Page 1792 of 5135
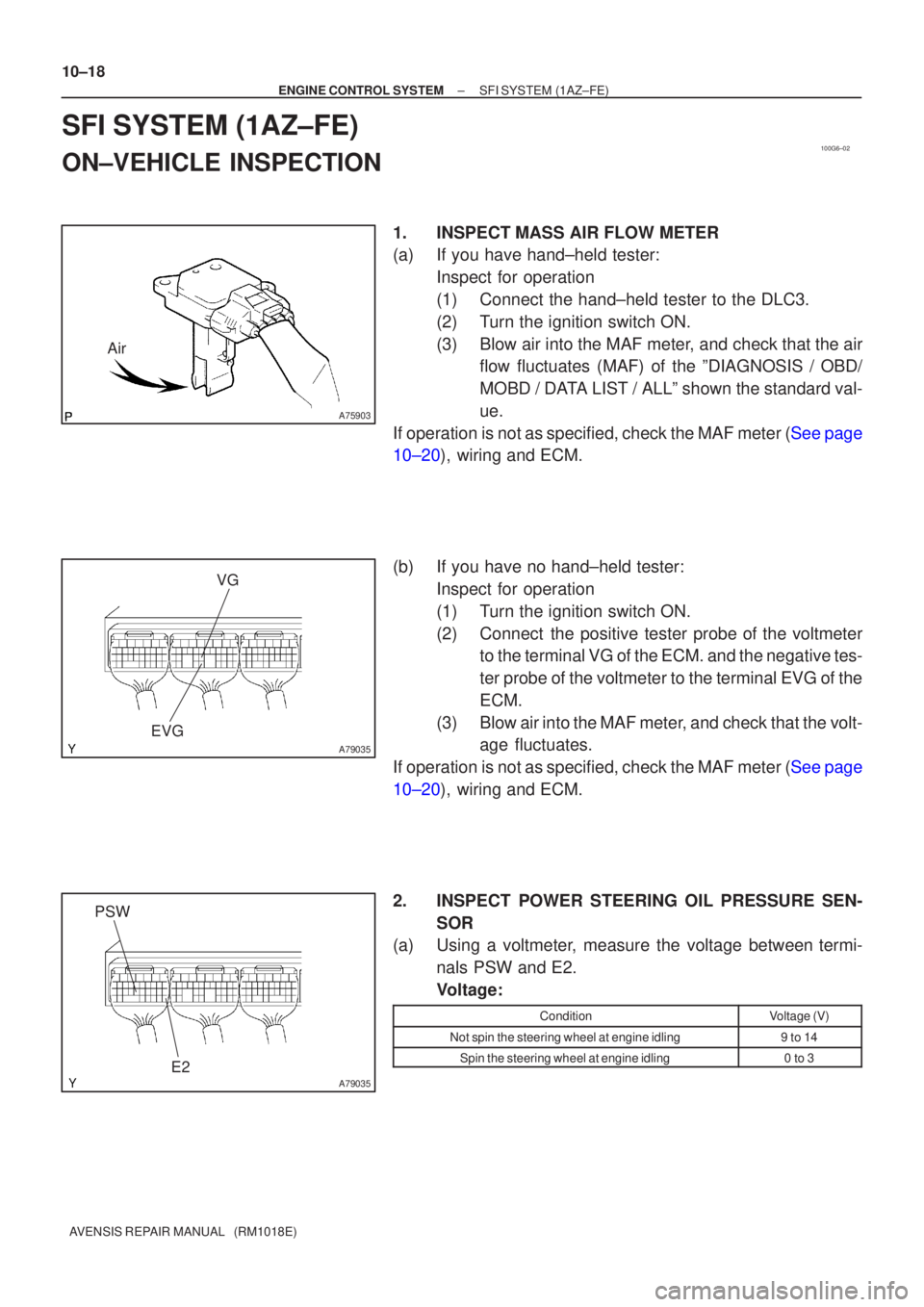
100G6±02
A75903
Air
A79035
VG
EVG
A79035E2
PSW
10±18
±
ENGINE CONTROL SYSTEM SFI SYSTEM(1AZ±FE)
AVENSIS REPAIR MANUAL (RM1018E)
SFI SYSTEM(1AZ±FE)
ON±VEHICLE INSPECTION
1.INSPECTMASS AIR FLOW METER
(a)If you have hand±held tester: Inspect for operation
(1)Connect the hand±held tester to the DLC3.
(2)Turn the ignition switch ON.
(3)Blow air into the MAF meter, and check that the airflow fluctuates (MAF) of the ºDIAGNOSIS / OBD/
MOBD / DATA LIST / ALLº shown the standard val-
ue.
If operation is not as specified, check the MAF meter (See page
10±20), wiring and ECM.
(b)If you have no hand±held tester: Inspect for operation
(1)Turn the ignition switch ON.
(2)Connect the positive tester probe of the voltmeterto the terminal VG of the ECM. and the negative tes-
ter probe of the voltmeter to the terminal EVG of the
ECM.
(3)Blow air into the MAF meter, and check that the volt- age fluctuates.
If operation is not as specified, check the MAF meter (See page
10±20), wiring and ECM.
2. INSPECT POWER STEERING OIL PRESSURE SEN- SOR
(a) Using a voltmeter, measure the voltage between termi-
nals PSW and E2.
Voltage:
ConditionVoltage (V)
Not spin the steering wheel at engine idling9 to 14
Spin the steering wheel at engine idling0 to 3
Page 1831 of 5135
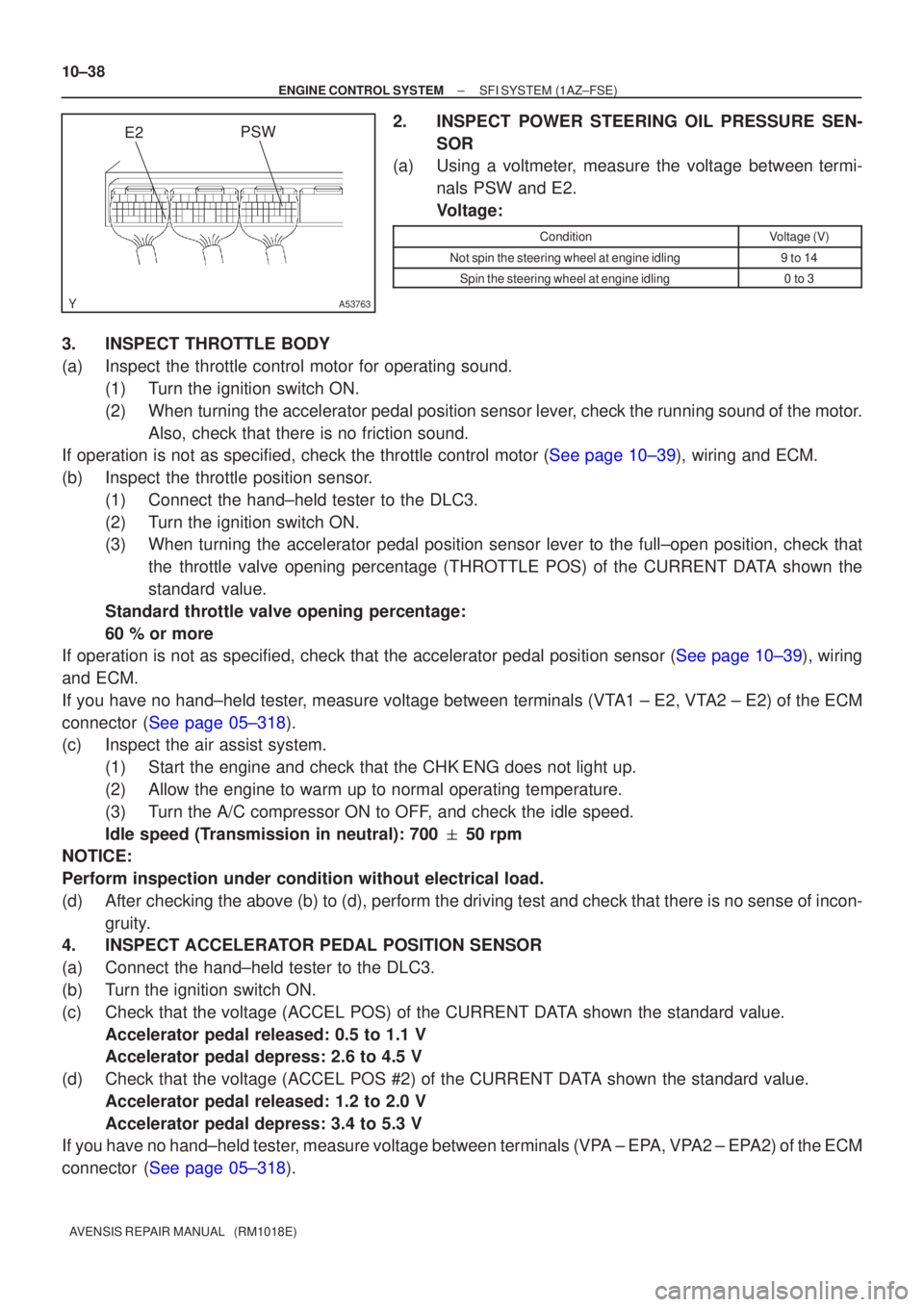
A53763
E2PSW
10±38
±
ENGINE CONTROL SYSTEM SFI SYSTEM(1AZ±FSE)
AVENSIS REPAIR MANUAL (RM1018E)
2.INSPECT POWER STEERING OIL PRESSURE SEN- SOR
(a)Using a voltmeter, measure the voltage between termi-
nals PSW and E2.
Voltage:
ConditionVoltage (V)
Not spin the steering wheel at engine idling9 to 14
Spin the steering wheel at engine idling0 to 3
3.INSPECT THROTTLE BODY
(a)Inspect the throttle control motor for operating sound.(1)Turn the ignition switch ON.
(2)When turning the accelerator pedal position sensor lever, check the running sound of the motor.Also, check that there is no friction sound.
If operation is not as specified, check the throttle control motor (See page 10±39), wiring and ECM.
(b) Inspect the throttle position sensor.
(1) Connect the hand±held tester to the DLC3.
(2) Turn the ignition switch ON.
(3) When turning the accelerator pedal position sensor lever to the full±\
open position, check thatthe throttle valve opening percentage (THROTTLE POS) of the CURRENT DATA shown the
standard value.
Standard throttle valve opening percentage:
60 % or more
If operation is not as specified, check that the accelerator pedal positio\
n sensor (See page 10±39), wiring
and ECM.
If you have no hand±held tester, measure voltage between terminals (VTA1 ± E2, VTA2 ± E2) of the ECM
connector (See page 05±318).
(c) Inspect the air assist system.
(1) Start the engine and check that the CHK ENG does not light up.
(2) Allow the engine to warm up to normal operating temperature.
(3) Turn the A/C compressor ON to OFF, and check the idle speed.
Idle speed (Transmission in neutral): 700 50 rpm
NOTICE:
Perform inspection under condition without electrical load.
(d) After checking the above (b) to (d), perform the driving test and check that there is no sense of incon-
gruity.
4. INSPECT ACCELERATOR PEDAL POSITION SENSOR
(a) Connect the hand±held tester to the DLC3.
(b) Turn the ignition switch ON.
(c) Check that the voltage (ACCEL POS) of the CURRENT DATA shown the standard value.
Accelerator pedal released: 0.5 to 1.1 V
Accelerator pedal depress: 2.6 to 4.5 V
(d) Check that the voltage (ACCEL POS #2) of the CURRENT DATA shown the standard value. Accelerator pedal released: 1.2 to 2.0 V
Accelerator pedal depress: 3.4 to 5.3 V
If you have no hand±held tester, measure voltage between terminals (VPA ± EPA, VPA2 ± EPA2) of the ECM
connector (See page 05±318).
Page 2069 of 5135
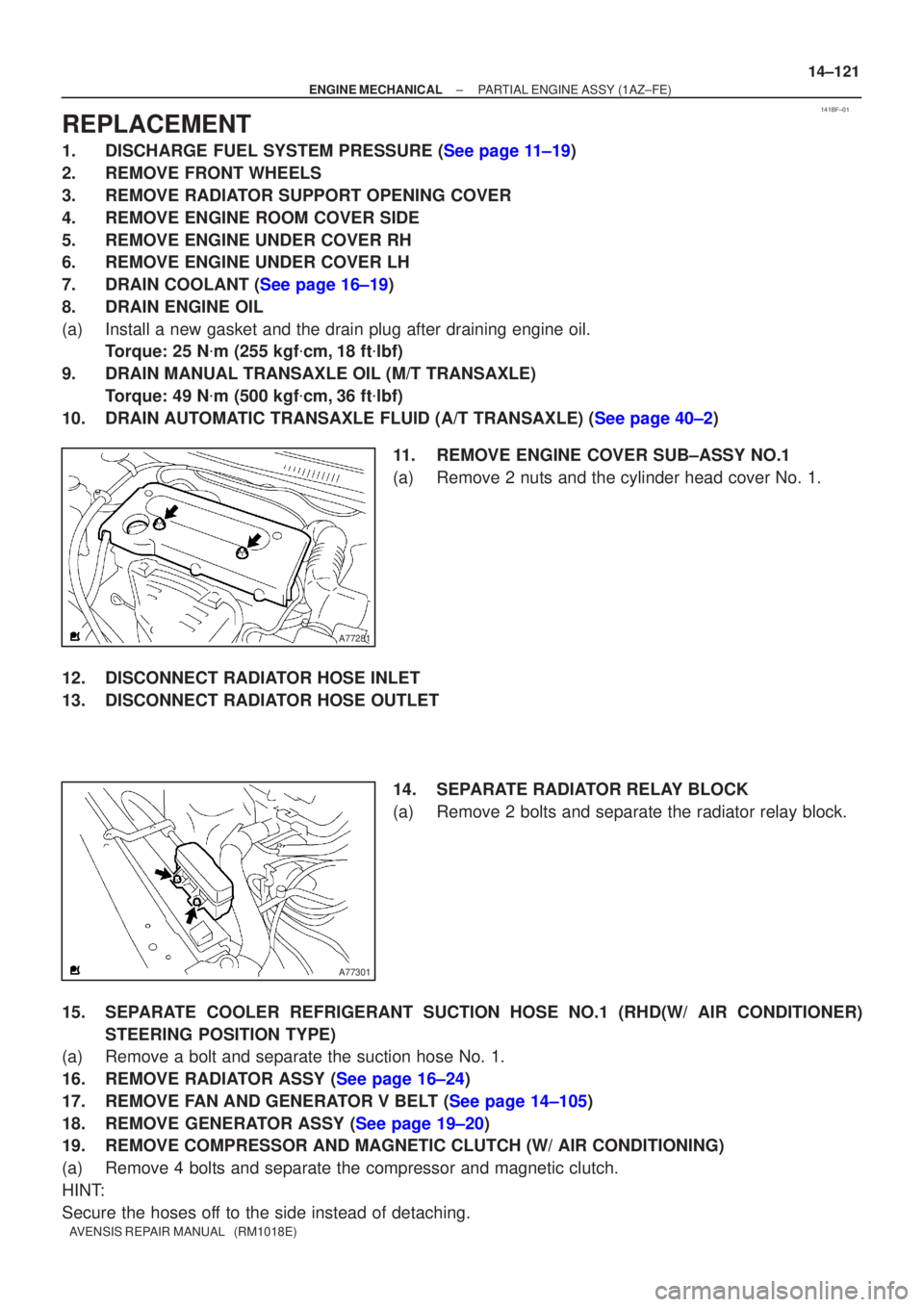
141BF±01
A77281
A77301
±
ENGINE MECHANICAL PARTIAL ENGINE ASSY(1AZ±FE)
14±121
AVENSIS REPAIR MANUAL (RM1018E)
REPLACEMENT
1.DISCHARGE FUEL SYSTEM PRESSURE (See page 11±19)
2.REMOVE FRONT WHEELS
3.REMOVE RADIATOR SUPPORT OPENING COVER
4.REMOVE ENGINE ROOM COVER SIDE
5.REMOVE ENGINE UNDER COVER RH
6.REMOVE ENGINE UNDER COVER LH
7.DRAIN COOLANT (See page 16±19)
8.DRAIN ENGINE OIL
(a)Install a new gasket and the drain plug after draining engine oil.
Torque: 25 N m (255 kgf cm,18 ft lbf)
9.DRAIN MANUAL TRANSAXLE OIL (M/T TRANSAXLE) Torque: 49 N m (500 kgf cm,36 ft lbf)
10.DRAIN AUTOMATIC TRANSAXLE FLUID (A/T TRANSAXLE) (See page 40±2)
11.REMOVE ENGINE COVER SUB±ASSY NO.1
(a)Remove 2 nuts and the cylinder head cover No. 1.
12.DISCONNECT RADIATOR HOSE INLET
13.DISCONNECT RADIATOR HOSE OUTLET 14.SEPARATE RADIATOR RELAY BLOCK
(a)Remove 2 bolts and separate the radiator relay block.
15.SEPARATE COOLER REFRIGERANT SUCTION HOSE NO.1 (RHD(W/ AIR CONDITIONER) STEERING POSITION TYPE)
(a)Remove a bolt and separate the suction hose No. 1.
16.REMOVE RADIATOR ASSY (See page 16±24)
17.REMOVE FAN AND GENERATOR V BELT (See page 14±105)
18.REMOVE GENERATOR ASSY (See page 19±20)
19. REMOVE COMPRESSOR AND MAGNETIC CLUTCH (W/ AIR CONDITIONING)
(a) Remove 4 bolts and separate the compressor and magnetic clutch.
HINT:
Secure the hoses off to the side instead of detaching.
Page 2082 of 5135
14±134
±
ENGINE MECHANICAL PARTIAL ENGINE ASSY(1AZ±FE)
AVENSIS REPAIR MANUAL (RM1018E)
155.INSTALL RADIATOR ASSY (See page 16±24)
156.INSTALL RADIATOR RELAY BLOCK Torque: 5.0 N m (51 kgf cm,44 in. lbf)
157.INSTALL ENGINE COVER SUB±ASSY NO.1 Torque: 7.0 N m (71 kgf cm,62 in. lbf)
158.ADD MANUAL TRANSAXLE OIL (M/T TRANSAXLE)
159.ADD AUTOMATIC TRANSAXLE FLUID (A/T TRANSAXLE)
160.ADD ENGINE OIL
161.ADD COOLANT (See page 16±19)
162. ADD POWER STEERING FLUID
163. BLEED POWER STEERING FLUID
164. CHECK FOR ENGINE OIL LEAKS
165.CHECK FOR ENGINE COOLANT LEAKS (See page 16±13)
166.CHECK FOR FUEL LEAKS (See page 11±15)
167. INSTALL FRONT WHEELS Torque: 103 N m (1,050 kgf cm, 76 ft lbf)
168.ADJUST FRONT WHEEL ALIGNMENT (See page 26±6)
169.INSPECT CHECK IDLE SPEED AND IGNITION TIMING (See page 14±101)
170.INSPECT CO/HC (See page 14±101)
171. CHECK ABS SPEED SENSOR SIGNAL
Page 2152 of 5135
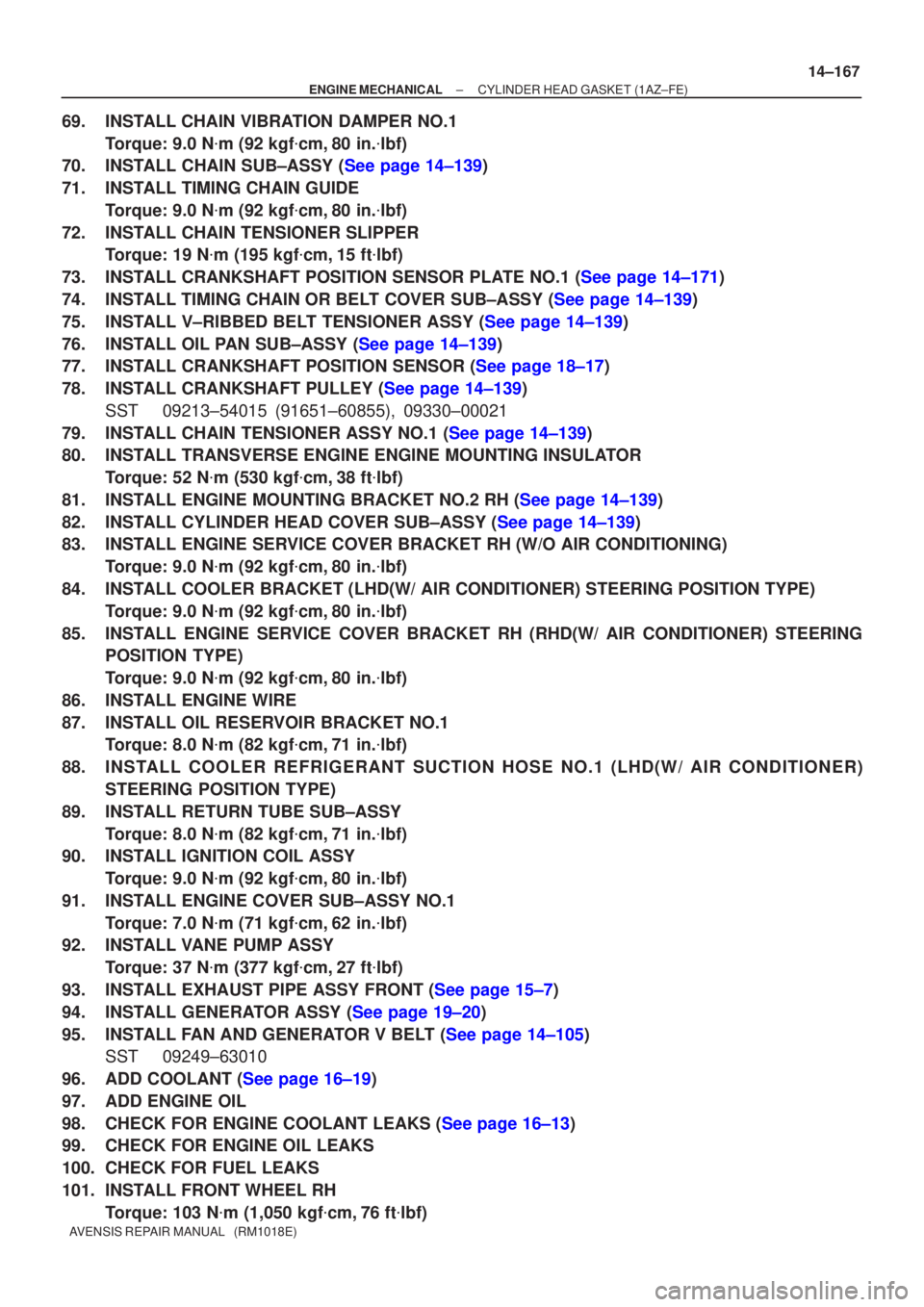
±
ENGINE MECHANICAL CYLINDER HEAD GASKET(1AZ±FE)
14±167
AVENSIS REPAIR MANUAL (RM1018E)
69.INSTALL CHAIN VIBRATION DAMPER NO.1
Torque: 9.0 N m (92 kgf cm,80 in. lbf)
70.INSTALL CHAIN SUB±ASSY (See page 14±139)
71.INSTALL TIMING CHAIN GUIDE
Torque: 9.0 N m (92 kgf cm,80 in. lbf)
72.INSTALL CHAIN TENSIONER SLIPPER Torque: 19 N m (195 kgf cm,15 ft lbf)
73.INSTALL CRANKSHAFT POSITION SENSOR PLATE NO.1 (See page 14±171)
74.INSTALL TIMING CHAIN OR BELT COVER SUB±ASSY (See page 14±139)
75.INSTALL V±RIBBED BELT TENSIONER ASSY (See page 14±139)
76.INSTALL OIL PAN SUB±ASSY (See page 14±139)
77.INSTALL CRANKSHAFT POSITION SENSOR (See page 18±17)
78.INSTALL CRANKSHAFT PULLEY (See page 14±139) SST09213±54015 (91651±60855), 09330±00021
79.INSTALL CHAIN TENSIONER ASSY NO.1 (See page 14±139)
80.INSTALL TRANSVERSE ENGINE ENGINE MOUNTING INSULATOR Torque: 52 N m (530 kgf cm,38 ft lbf)
81.INSTALL ENGINE MOUNTING BRACKET NO.2 RH (See page 14±139)
82.INSTALL CYLINDER HEAD COVER SUB±ASSY (See page 14±139)
83.INSTALL ENGINE SERVICE COVER BRACKET RH (W/O AIR CONDITIONING) Torque: 9.0 N m (92 kgf cm,80 in. lbf)
84.INSTALL COOLER BRACKET (LHD(W/ AIR CONDITIONER) STEERING POSITION TYPE) Torque: 9.0 N m (92 kgf cm,80 in. lbf)
85.INSTALL ENGINE SERVICE COVER BRACKET RH (RHD(W/ AIR CONDITIONER) STEERING POSITION TYPE)
Torque: 9.0 N m (92 kgf cm,80 in. lbf)
86.INSTALL ENGINE WIRE
87.INSTALL OIL RESERVOIR BRACKET NO.1 Torque: 8.0 N m (82 kgf cm,71 in. lbf)
88.IN STALL COOL ER REFRIGERANT SUCTION HOSE NO.1 (LHD(W/ AIR CONDITION ER)
STEERING POSITION TYPE)
89.INSTALL RETURN TUBE SUB±ASSY Torque: 8.0 N m (82 kgf cm,71 in. lbf)
90.INSTALL IGNITION COIL ASSY
Torque: 9.0 N m (92 kgf cm,80 in. lbf)
91.INSTALL ENGINE COVER SUB±ASSY NO.1 Torque: 7.0 N m (71 kgf cm,62 in. lbf)
92.INSTALL VANE PUMP ASSY
Torque: 37 N m (377 kgf cm,27 ft lbf)
93.INSTALL EXHAUST PIPE ASSY FRONT (See page 15±7)
94.INSTALL GENERATOR ASSY (See page 19±20)
95.INSTALL FAN AND GENERATOR V BELT (See page 14±105) SST 09249±63010
96.ADD COOLANT (See page 16±19)
97. ADD ENGINE OIL
98.CHECK FOR ENGINE COOLANT LEAKS (See page 16±13)
99. CHECK FOR ENGINE OIL LEAKS
100. CHECK FOR FUEL LEAKS
101. INSTALL FRONT WHEEL RH Torque: 103 N m (1,050 kgf cm, 76 ft lbf)