Page 2860 of 3419
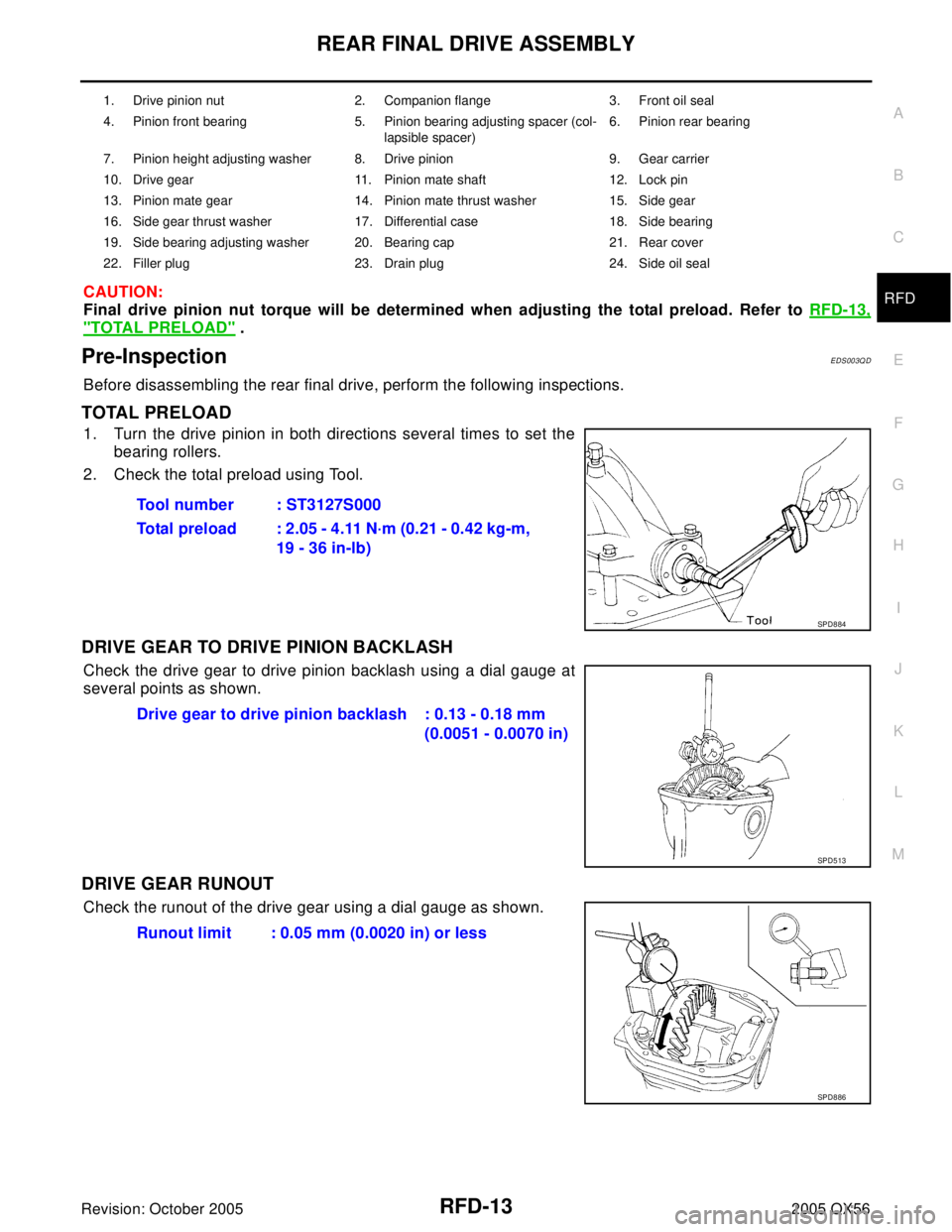
REAR FINAL DRIVE ASSEMBLY
RFD-13
C
E
F
G
H
I
J
K
L
MA
B
RFD
Revision: October 20052005 QX56CAUTION:
Final drive pinion nut torque will be determined when adjusting the total preload. Refer to RFD-13,
"TOTAL PRELOAD" .
Pre-InspectionEDS003QD
Before disassembling the rear final drive, perform the following inspections.
TOTAL PRELOAD
1. Turn the drive pinion in both directions several times to set the
bearing rollers.
2. Check the total preload using Tool.
DRIVE GEAR TO DRIVE PINION BACKLASH
Check the drive gear to drive pinion backlash using a dial gauge at
several points as shown.
DRIVE GEAR RUNOUT
Check the runout of the drive gear using a dial gauge as shown.
1. Drive pinion nut 2. Companion flange 3. Front oil seal
4. Pinion front bearing 5. Pinion bearing adjusting spacer (col-
lapsible spacer)6. Pinion rear bearing
7. Pinion height adjusting washer 8. Drive pinion 9. Gear carrier
10. Drive gear 11. Pinion mate shaft 12. Lock pin
13. Pinion mate gear 14. Pinion mate thrust washer 15. Side gear
16. Side gear thrust washer 17. Differential case 18. Side bearing
19. Side bearing adjusting washer 20. Bearing cap 21. Rear cover
22. Filler plug 23. Drain plug 24. Side oil seal
Tool number : ST3127S000
Total preload : 2.05 - 4.11 N·m (0.21 - 0.42 kg-m,
19 - 36 in-lb)
SPD8 84
Drive gear to drive pinion backlash : 0.13 - 0.18 mm
(0.0051 - 0.0070 in)
SPD5 13
Runout limit : 0.05 mm (0.0020 in) or less
SPD8 86
Page 2865 of 3419
RFD-18
REAR FINAL DRIVE ASSEMBLY
Revision: October 20052005 QX56
4. Drive the pinion mate shaft lock pin out from the drive gear side
using a suitable punch.
INSPECTION
Contact Surfaces
1. Clean the disassembled parts in a suitable solvent and blow dry using compressed air.
2. If the following surfaces are burred or scratched, smooth them using an oil stone.
Differential case
Side gear
Pinion mate gear
Pinion mate shaft
Bearing
1. Thoroughly clean the bearing.
2. Check the bearing for wear, scratches, pitting, or flaking.
3. Check the tapered roller bearing for smooth rotation. If dam-
aged, replace the outer race and inner race as a set.
ADJUSTMENT OF DIFFERENTIAL CASE
Thrust Washer Selection
1. Install the side gears, pinion mate gears, and thrust washers into
the differential case.
SPD0 25
SPD7 15
SPD5 52
Page 2866 of 3419
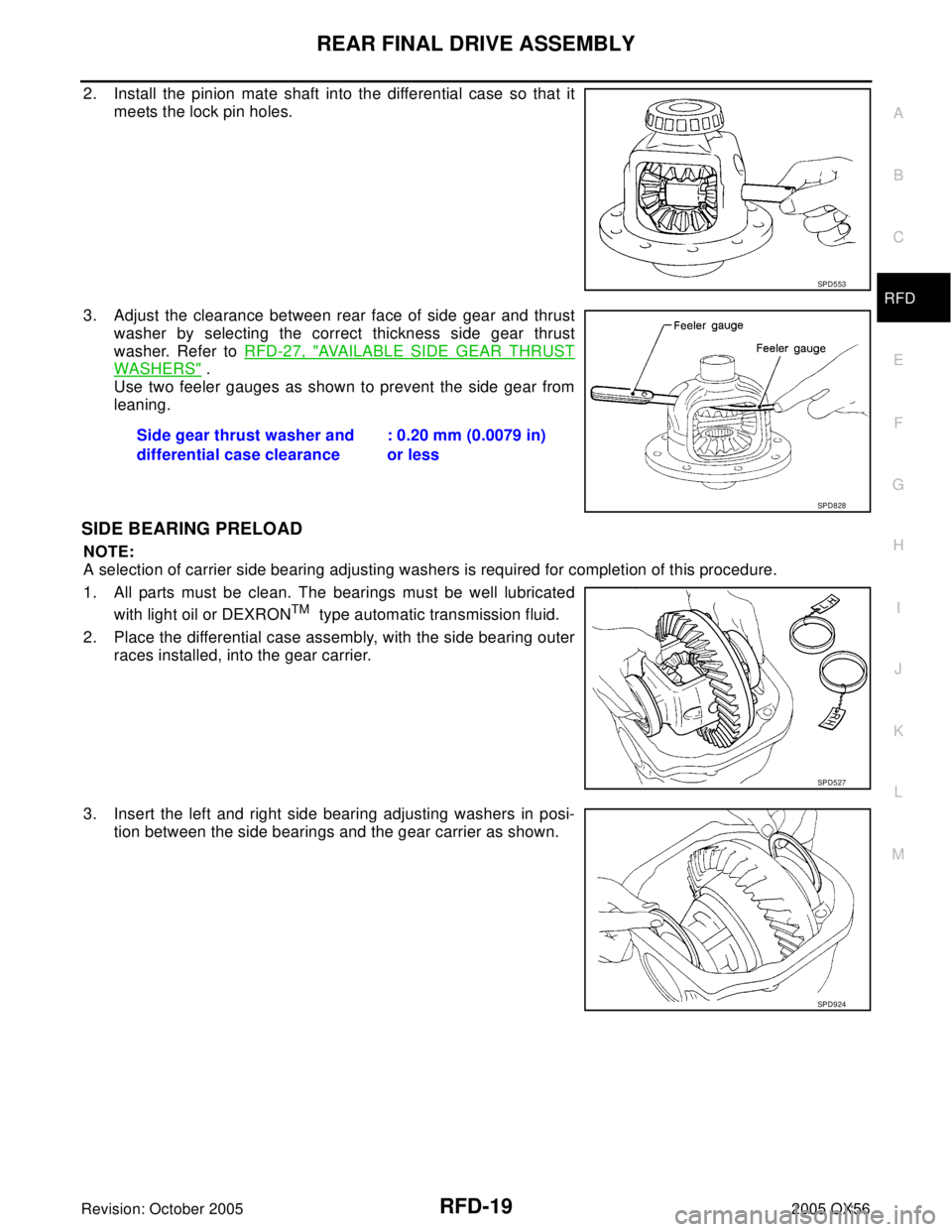
REAR FINAL DRIVE ASSEMBLY
RFD-19
C
E
F
G
H
I
J
K
L
MA
B
RFD
Revision: October 20052005 QX56
2. Install the pinion mate shaft into the differential case so that it
meets the lock pin holes.
3. Adjust the clearance between rear face of side gear and thrust
washer by selecting the correct thickness side gear thrust
washer. Refer to RFD-27, "
AVAILABLE SIDE GEAR THRUST
WASHERS" .
Use two feeler gauges as shown to prevent the side gear from
leaning.
SIDE BEARING PRELOAD
NOTE:
A selection of carrier side bearing adjusting washers is required for completion of this procedure.
1. All parts must be clean. The bearings must be well lubricated
with light oil or DEXRON
TM type automatic transmission fluid.
2. Place the differential case assembly, with the side bearing outer
races installed, into the gear carrier.
3. Insert the left and right side bearing adjusting washers in posi-
tion between the side bearings and the gear carrier as shown.
SPD5 53
Side gear thrust washer and
differential case clearance: 0.20 mm (0.0079 in)
or less
SPD8 28
SPD5 27
SPD9 24
Page 2868 of 3419
REAR FINAL DRIVE ASSEMBLY
RFD-21
C
E
F
G
H
I
J
K
L
MA
B
RFD
Revision: October 20052005 QX56
1. Thoroughly clean the drive gear and drive pinion teeth.
2. Lightly apply a mixture of powdered ferric oxide and oil or the
equivalent. Apply it to 3 or 4 teeth of the drive gear drive side.
3. Use your hand to hold the companion flange steady and rotate
the drive gear in both directions.
4. Check the tooth contact as shown.
ASSEMBLY OF DIFFERENTIAL CASE ASSEMBLY
1. Install the pinion mate shaft lock pin using a suitable punch as
shown.
The lock pin must be flush with the case.
2. Place the differential case on the drive gear.
SPD3 57
SDIA0813E
SDIA1910E
SPD0 30
Page 2869 of 3419
RFD-22
REAR FINAL DRIVE ASSEMBLY
Revision: October 20052005 QX56
3. Apply genuine medium strength locking sealant or equivalent as
shown. Refer to GI-45, "
Recommended Chemical Products and
Sealants" .
Tighten the drive gear bolts in a criss-cross pattern to specifi-
cation.
4. Press-fit the side bearing inner races on the differential case
using Tools.
INSTALLATION OF DRIVE PINION ASSEMBLY
1. Press-fit the pinion front and rear bearing outer races using
Tools.
2. Select pinion height adjusting washer. Refer to RFD-27, "
Drive Pinion Height Adjustment" . Drive gear bolts
Step 1 : 78.5 N·m (8.0 kg-m, 58 ft-lb)
Step 2 : 34° degrees
SPD5 54
Tool number A: KV38100200
B: ST33081000
SPD3 53
Tool number A: ST15310000
B: ST35325000
C: ST30621000
SPD9 92
Page 2890 of 3419
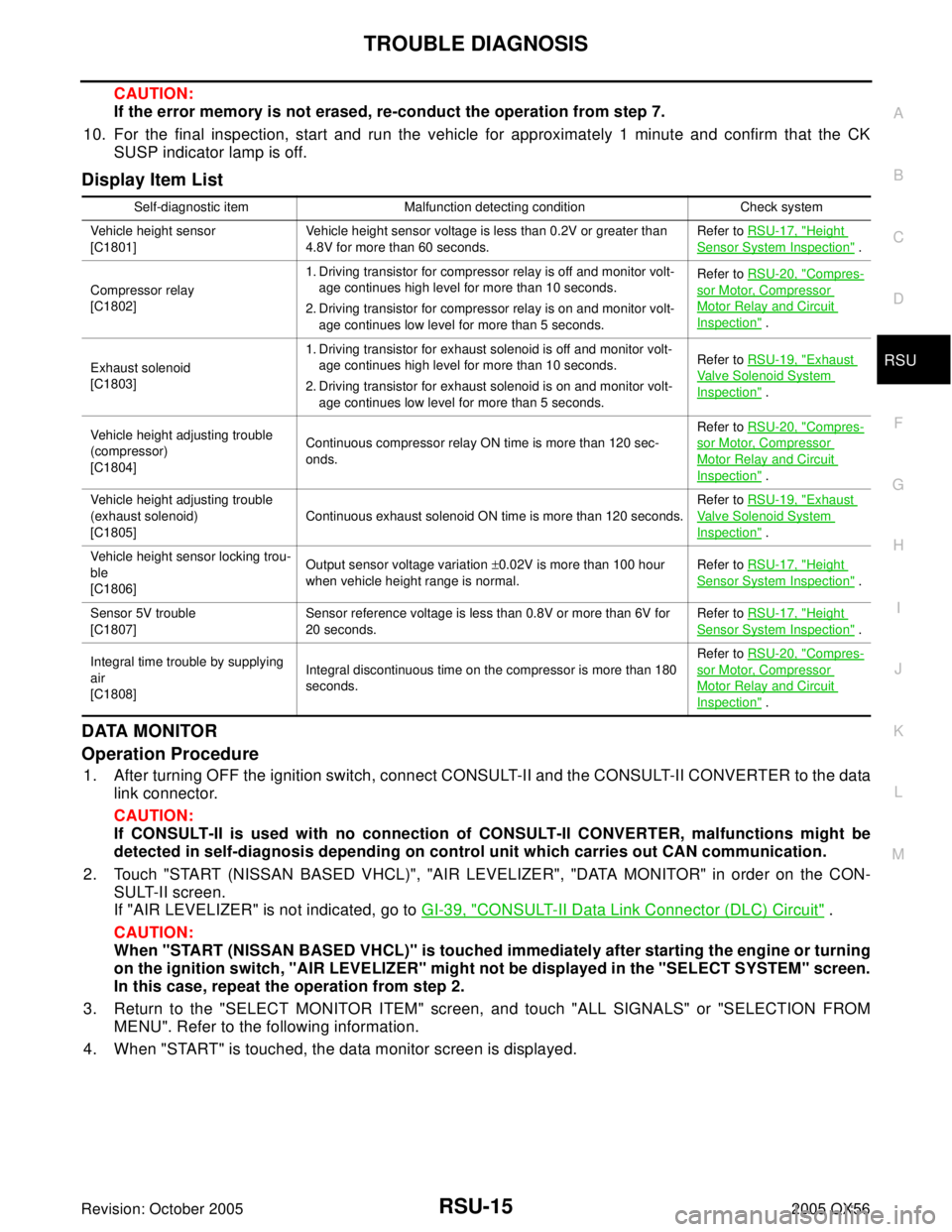
TROUBLE DIAGNOSIS
RSU-15
C
D
F
G
H
I
J
K
L
MA
B
RSU
Revision: October 20052005 QX56
CAUTION:
If the error memory is not erased, re-conduct the operation from step 7.
10. For the final inspection, start and run the vehicle for approximately 1 minute and confirm that the CK
SUSP indicator lamp is off.
Display Item List
DATA MONITOR
Operation Procedure
1. After turning OFF the ignition switch, connect CONSULT-II and the CONSULT-II CONVERTER to the data
link connector.
CAUTION:
If CONSULT-II is used with no connection of CONSULT-II CONVERTER, malfunctions might be
detected in self-diagnosis depending on control unit which carries out CAN communication.
2. Touch "START (NISSAN BASED VHCL)", "AIR LEVELIZER", "DATA MONITOR" in order on the CON-
SULT-II screen.
If "AIR LEVELIZER" is not indicated, go to GI-39, "
CONSULT-II Data Link Connector (DLC) Circuit" .
CAUTION:
When "START (NISSAN BASED VHCL)" is touched immediately after starting the engine or turning
on the ignition switch, "AIR LEVELIZER" might not be displayed in the "SELECT SYSTEM" screen.
In this case, repeat the operation from step 2.
3. Return to the "SELECT MONITOR ITEM" screen, and touch "ALL SIGNALS" or "SELECTION FROM
MENU". Refer to the following information.
4. When "START" is touched, the data monitor screen is displayed.
Self-diagnostic item Malfunction detecting condition Check system
Vehicle height sensor
[C1801]Vehicle height sensor voltage is less than 0.2V or greater than
4.8V for more than 60 seconds.Refer to RSU-17, "
Height
Sensor System Inspection" .
Compressor relay
[C1802]1. Driving transistor for compressor relay is off and monitor volt-
age continues high level for more than 10 seconds.
2. Driving transistor for compressor relay is on and monitor volt-
age continues low level for more than 5 seconds.Refer to RSU-20, "
Compres-
sor Motor, Compressor
Motor Relay and Circuit
Inspection" .
Exhaust solenoid
[C1803]1. Driving transistor for exhaust solenoid is off and monitor volt-
age continues high level for more than 10 seconds.
2. Driving transistor for exhaust solenoid is on and monitor volt-
age continues low level for more than 5 seconds.Refer to RSU-19, "
Exhaust
Valve Solenoid System
Inspection" .
Vehicle height adjusting trouble
(compressor)
[C1804]Continuous compressor relay ON time is more than 120 sec-
onds.Refer to RSU-20, "
Compres-
sor Motor, Compressor
Motor Relay and Circuit
Inspection" .
Vehicle height adjusting trouble
(exhaust solenoid)
[C1805]Continuous exhaust solenoid ON time is more than 120 seconds.Refer to RSU-19, "
Exhaust
Valve Solenoid System
Inspection" .
Vehicle height sensor locking trou-
ble
[C1806]Output sensor voltage variation ±0.02V is more than 100 hour
when vehicle height range is normal.Refer to RSU-17, "
Height
Sensor System Inspection" .
Sensor 5V trouble
[C1807]Sensor reference voltage is less than 0.8V or more than 6V for
20 seconds.Refer to RSU-17, "
Height
Sensor System Inspection" .
Integral time trouble by supplying
air
[C1808]Integral discontinuous time on the compressor is more than 180
seconds.Refer to RSU-20, "
Compres-
sor Motor, Compressor
Motor Relay and Circuit
Inspection" .
Page 2907 of 3419
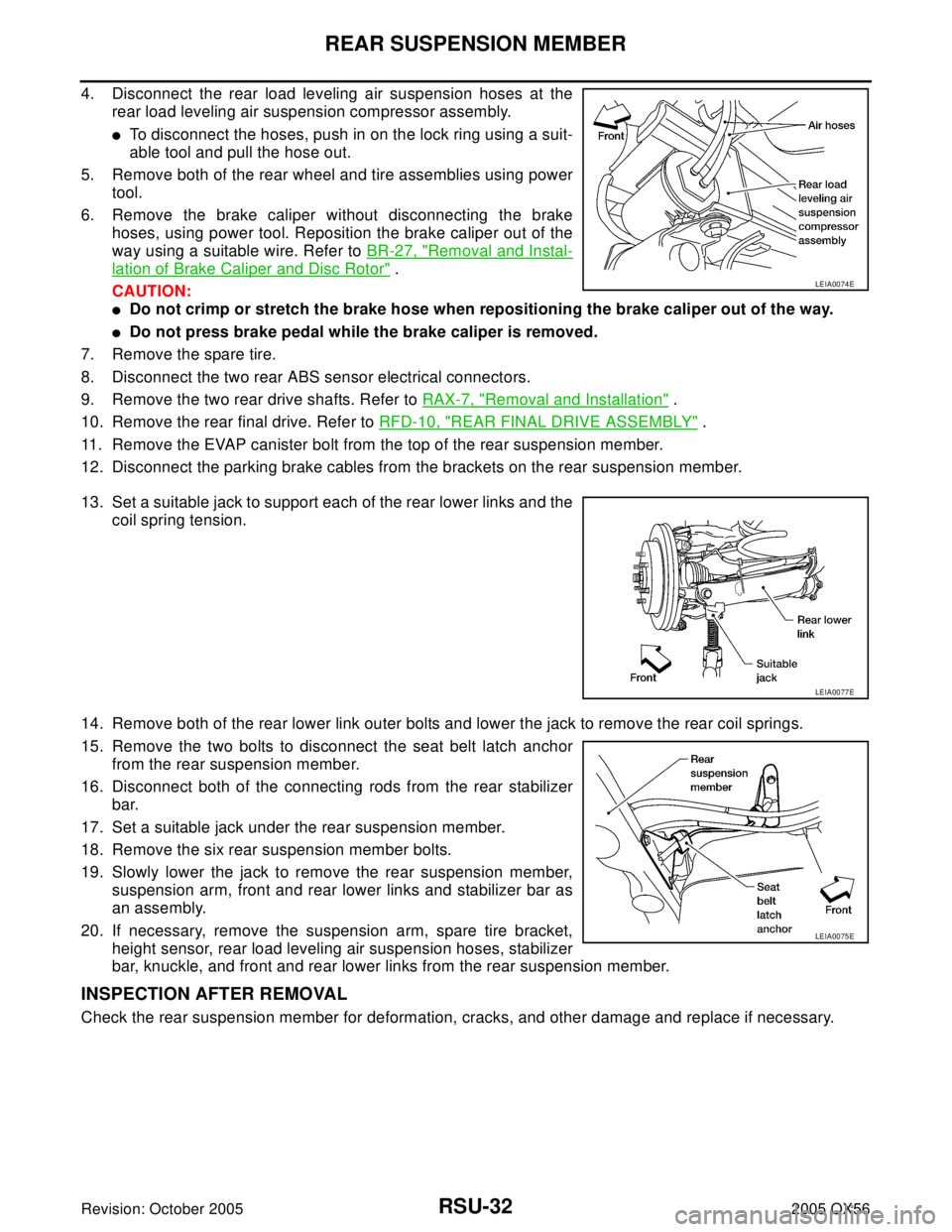
RSU-32
REAR SUSPENSION MEMBER
Revision: October 20052005 QX56
4. Disconnect the rear load leveling air suspension hoses at the
rear load leveling air suspension compressor assembly.
To disconnect the hoses, push in on the lock ring using a suit-
able tool and pull the hose out.
5. Remove both of the rear wheel and tire assemblies using power
tool.
6. Remove the brake caliper without disconnecting the brake
hoses, using power tool. Reposition the brake caliper out of the
way using a suitable wire. Refer to BR-27, "
Removal and Instal-
lation of Brake Caliper and Disc Rotor" .
CAUTION:
Do not crimp or stretch the brake hose when repositioning the brake caliper out of the way.
Do not press brake pedal while the brake caliper is removed.
7. Remove the spare tire.
8. Disconnect the two rear ABS sensor electrical connectors.
9. Remove the two rear drive shafts. Refer to RAX-7, "
Removal and Installation" .
10. Remove the rear final drive. Refer to RFD-10, "
REAR FINAL DRIVE ASSEMBLY" .
11. Remove the EVAP canister bolt from the top of the rear suspension member.
12. Disconnect the parking brake cables from the brackets on the rear suspension member.
13. Set a suitable jack to support each of the rear lower links and the
coil spring tension.
14. Remove both of the rear lower link outer bolts and lower the jack to remove the rear coil springs.
15. Remove the two bolts to disconnect the seat belt latch anchor
from the rear suspension member.
16. Disconnect both of the connecting rods from the rear stabilizer
bar.
17. Set a suitable jack under the rear suspension member.
18. Remove the six rear suspension member bolts.
19. Slowly lower the jack to remove the rear suspension member,
suspension arm, front and rear lower links and stabilizer bar as
an assembly.
20. If necessary, remove the suspension arm, spare tire bracket,
height sensor, rear load leveling air suspension hoses, stabilizer
bar, knuckle, and front and rear lower links from the rear suspension member.
INSPECTION AFTER REMOVAL
Check the rear suspension member for deformation, cracks, and other damage and replace if necessary.
LEIA0074E
LEIA0077E
LEIA0075E
Page 2908 of 3419
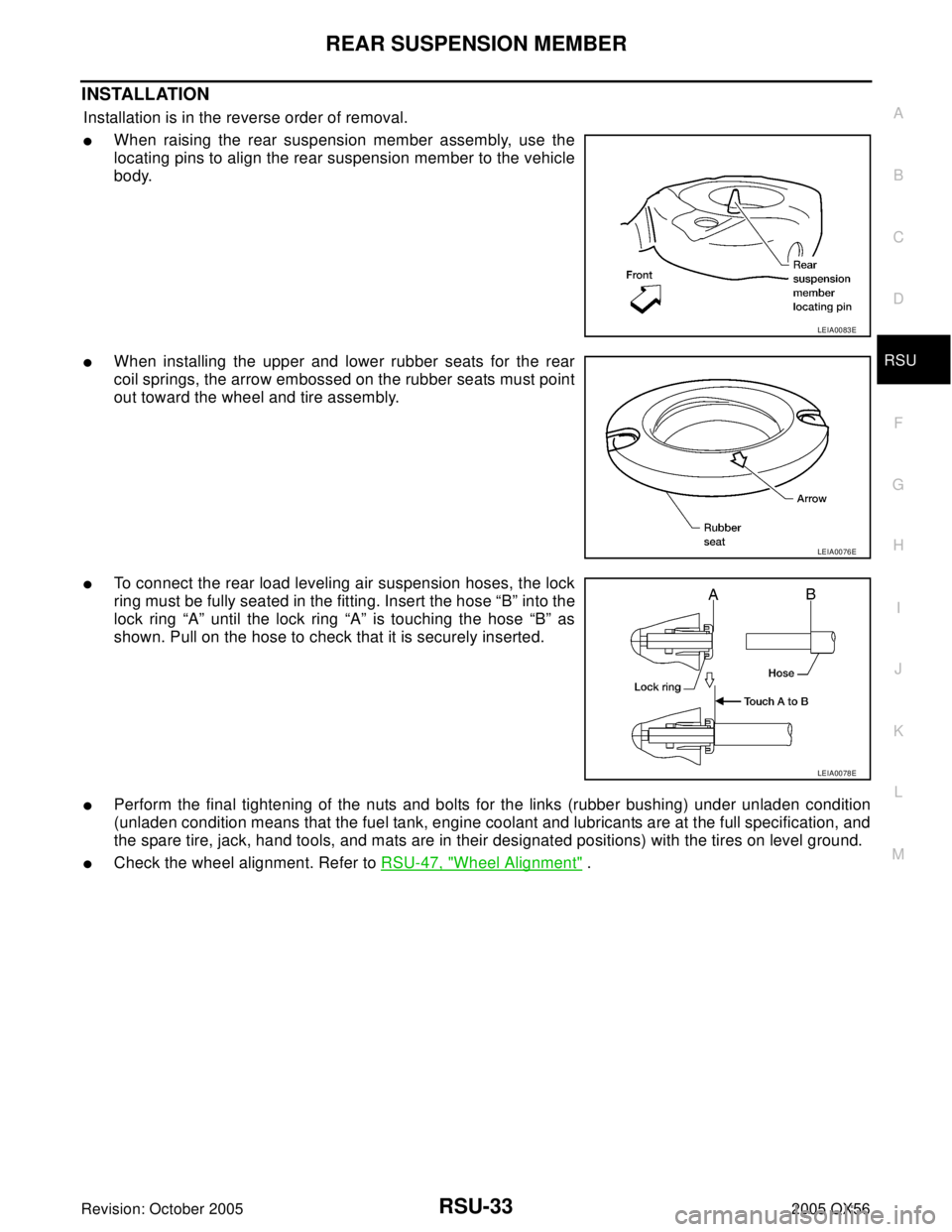
REAR SUSPENSION MEMBER
RSU-33
C
D
F
G
H
I
J
K
L
MA
B
RSU
Revision: October 20052005 QX56
INSTALLATION
Installation is in the reverse order of removal.
When raising the rear suspension member assembly, use the
locating pins to align the rear suspension member to the vehicle
body.
When installing the upper and lower rubber seats for the rear
coil springs, the arrow embossed on the rubber seats must point
out toward the wheel and tire assembly.
To connect the rear load leveling air suspension hoses, the lock
ring must be fully seated in the fitting. Insert the hose “B” into the
lock ring “A” until the lock ring “A” is touching the hose “B” as
shown. Pull on the hose to check that it is securely inserted.
Perform the final tightening of the nuts and bolts for the links (rubber bushing) under unladen condition
(unladen condition means that the fuel tank, engine coolant and lubricants are at the full specification, and
the spare tire, jack, hand tools, and mats are in their designated positions) with the tires on level ground.
Check the wheel alignment. Refer to RSU-47, "Wheel Alignment" .
LEIA0083E
LEIA0076E
LEIA0078E