Page 302 of 557
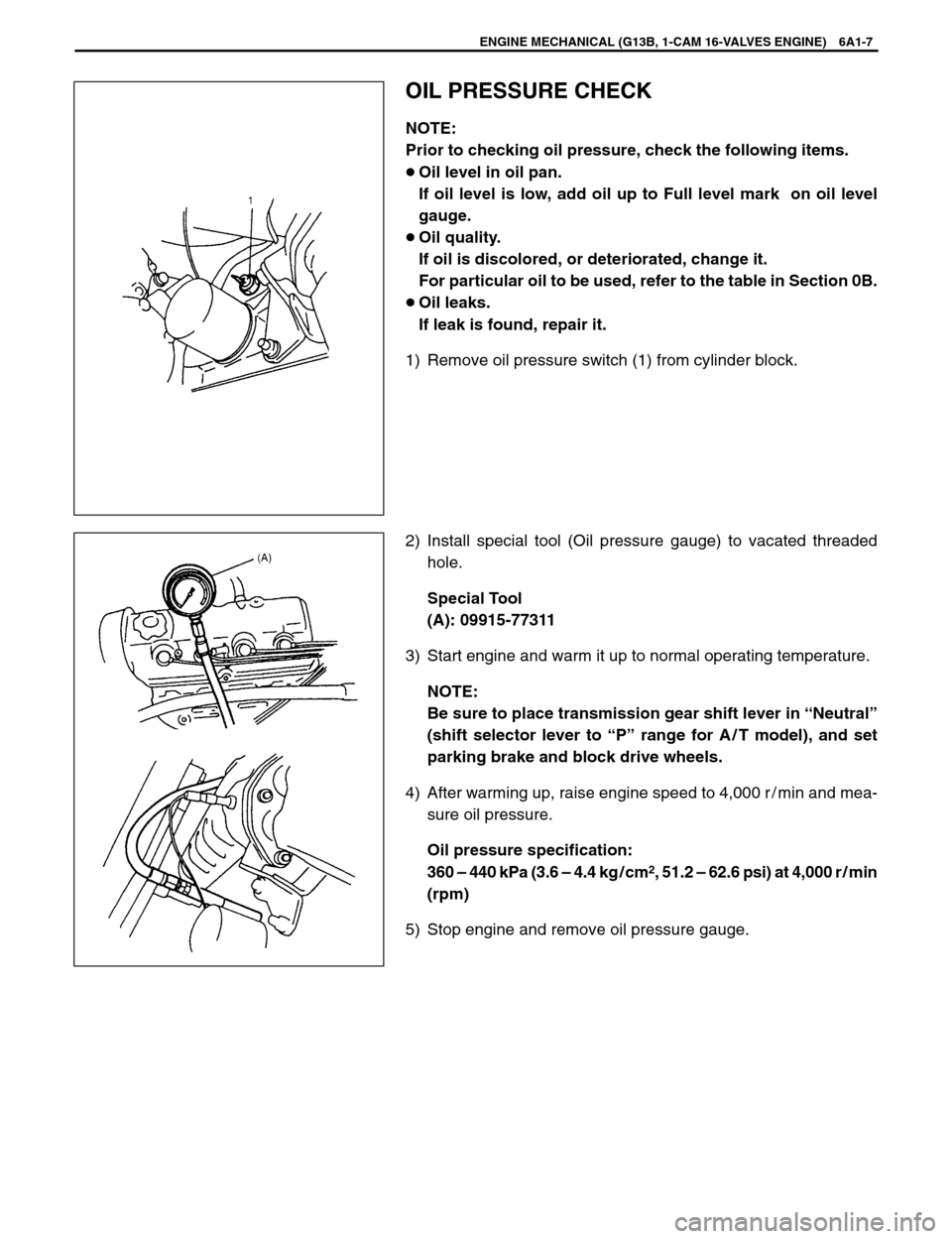
ENGINE MECHANICAL (G13B, 1-CAM 16-VALVES ENGINE) 6A1-7
OIL PRESSURE CHECK
NOTE:
Prior to checking oil pressure, check the following items.
Oil level in oil pan.
If oil level is low, add oil up to Full level mark on oil level
gauge.
Oil quality.
If oil is discolored, or deteriorated, change it.
For particular oil to be used, refer to the table in Section 0B.
Oil leaks.
If leak is found, repair it.
1) Remove oil pressure switch (1) from cylinder block.
2) Install special tool (Oil pressure gauge) to vacated threaded
hole.
Special Tool
(A): 09915-77311
3) Start engine and warm it up to normal operating temperature.
NOTE:
Be sure to place transmission gear shift lever in “Neutral”
(shift selector lever to “P” range for A / T model), and set
parking brake and block drive wheels.
4) After warming up, raise engine speed to 4,000 r / min and mea-
sure oil pressure.
Oil pressure specification:
360 – 440 kPa (3.6 – 4.4 kg / cm
2, 51.2 – 62.6 psi) at 4,000 r / min
(rpm)
5) Stop engine and remove oil pressure gauge.
Page 345 of 557

“a”: Valve guide protrusion (11.5 mm)
6A1-50 ENGINE MECHANICAL (G13B, 1-CAM 16-VALVES ENGINE)
ASSEMBLY
1) Before installing valve guide into cylinder head, ream guide hole
with special tool (11 mm reamer) to remove burrs and make it
truly round.
Special Tool
(A): 09916-34542
(B): 09916-38210
2) Install valve guide to cylinder head.
Heat cylinder head uniformly at a temperature of 80 to 100C
(176 to 212F) so that head will not be distorted, and drive new
valve guide into hole with special tools. Drive in new valve guide
until special tool (Valve guide installer) contacts cylinder head.
After installing, make sure that valve guide protrudes by 11.5
mm (0.45 in.) from cylinder head.
Special Tool
(C): 09916-56011
(D): 09916-58210
NOTE:
Do not reuse valve guide once disassembled.
Install new valve guide (Oversize).
Intake and exhaust valve guides are identical.
Valve guide oversize: 0.03 mm (0.0012 in.)
Valve guide protrusion (In and Ex): 11.5 mm (0.45 in.)
3) Ream valve guide bore with special tool (5.5 mm reamer). After
reaming, clean bore.
Special Tool
(A): 09916-34542
(B): 09916-34550
4) Install valve spring seat to cylinder head.
Page 379 of 557
8. Heater inlet hose
9. Heater outlet hose
10. Radiator
11. Oil cooler (A / T only)
12. Engine
13. ECT sensor1. Radiator inlet hose
2. Radiator outlet hose
3. Water intake pipe
4. Thermostat
5. Water pump
6. IAC valve (throttle body)
7. Breather pipe (air cleaner
outlet hose)
6B-2 ENGINE COOLING
GENERAL DESCRIPTION
COOLING SYSTEM CIRCULATION
During engine warm-up (thermostat closed), the water pump discharges coolant into the water jacket chamber
adjacent to No.1 cylinder. Coolant then flows through the cylinder block and the cylinder heat. Coolant then returns
to the water pump through intake manifold, heater inlet hose, heater unit, heater outlet hose, and water intake pipe.
During normal temperatures (thermostat open), coolant takes the same basic route but is now allowed to flow past
the thermostat, the inlet hose and the radiator, and then back to the water pump through the outlet hose and the
water intake pipe.
Page 380 of 557
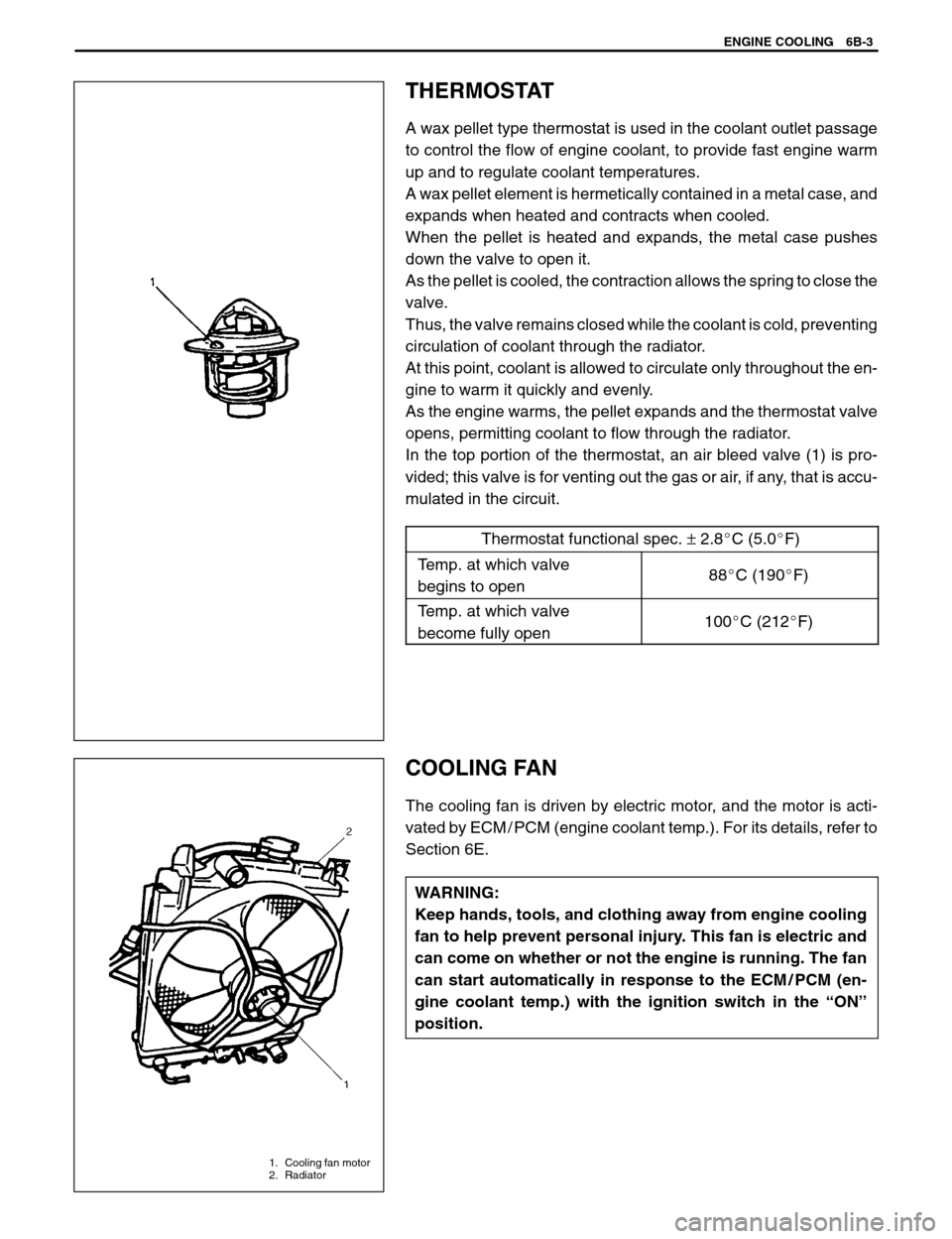
1. Cooling fan motor
2. Radiator
ENGINE COOLING 6B-3
THERMOSTAT
A wax pellet type thermostat is used in the coolant outlet passage
to control the flow of engine coolant, to provide fast engine warm
up and to regulate coolant temperatures.
A wax pellet element is hermetically contained in a metal case, and
expands when heated and contracts when cooled.
When the pellet is heated and expands, the metal case pushes
down the valve to open it.
As the pellet is cooled, the contraction allows the spring to close the
valve.
Thus, the valve remains closed while the coolant is cold, preventing
circulation of coolant through the radiator.
At this point, coolant is allowed to circulate only throughout the en-
gine to warm it quickly and evenly.
As the engine warms, the pellet expands and the thermostat valve
opens, permitting coolant to flow through the radiator.
In the top portion of the thermostat, an air bleed valve (1) is pro-
vided; this valve is for venting out the gas or air, if any, that is accu-
mulated in the circuit.
Thermostat functional spec. ± 2.8C (5.0F)
Temp. at which valve
begins to open88C (190F)
Temp. at which valve
become fully open100C (212F)
COOLING FAN
The cooling fan is driven by electric motor, and the motor is acti-
vated by ECM / PCM (engine coolant temp.). For its details, refer to
Section 6E.
WARNING:
Keep hands, tools, and clothing away from engine cooling
fan to help prevent personal injury. This fan is electric and
can come on whether or not the engine is running. The fan
can start automatically in response to the ECM / PCM (en-
gine coolant temp.) with the ignition switch in the “ON”
position.
Page 382 of 557
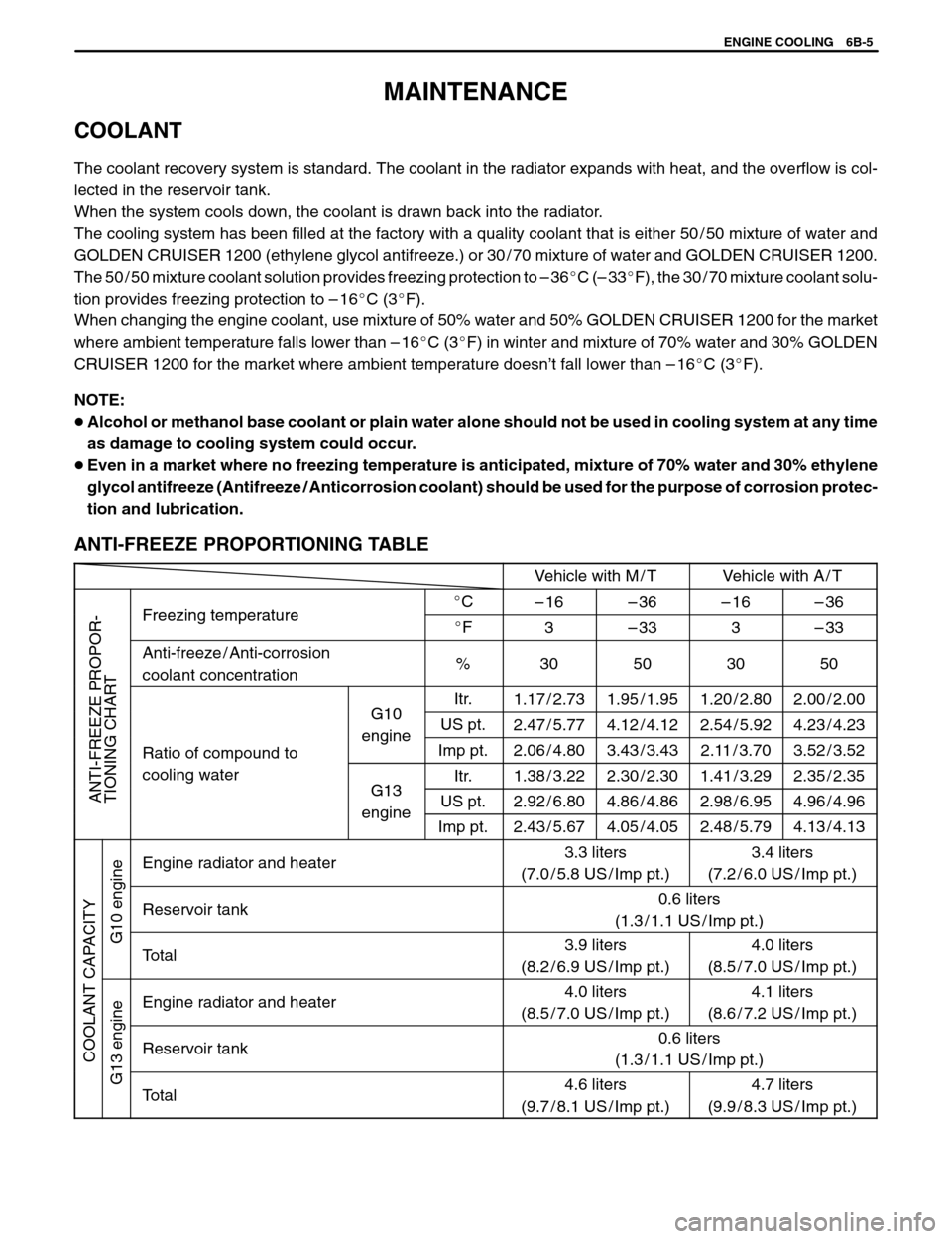
ENGINE COOLING 6B-5
ANTI-FREEZE PROPOR-
TIONING CHART COOLANT CAPACITY
G13 engine G10 engine
MAINTENANCE
COOLANT
The coolant recovery system is standard. The coolant in the radiator expands with heat, and the overflow is col-
lected in the reservoir tank.
When the system cools down, the coolant is drawn back into the radiator.
The cooling system has been filled at the factory with a quality coolant that is either 50 / 50 mixture of water and
GOLDEN CRUISER 1200 (ethylene glycol antifreeze.) or 30 / 70 mixture of water and GOLDEN CRUISER 1200.
The 50 / 50 mixture coolant solution provides freezing protection to – 36C (– 33F), the 30 / 70 mixture coolant solu-
tion provides freezing protection to – 16C (3F).
When changing the engine coolant, use mixture of 50% water and 50% GOLDEN CRUISER 1200 for the market
where ambient temperature falls lower than – 16C (3F) in winter and mixture of 70% water and 30% GOLDEN
CRUISER 1200 for the market where ambient temperature doesn’t fall lower than – 16C (3F).
NOTE:
Alcohol or methanol base coolant or plain water alone should not be used in cooling system at any time
as damage to cooling system could occur.
Even in a market where no freezing temperature is anticipated, mixture of 70% water and 30% ethylene
glycol antifreeze (Antifreeze / Anticorrosion coolant) should be used for the purpose of corrosion protec-
tion and lubrication.
ANTI-FREEZE PROPORTIONING TABLE
Vehicle with M / TVehicle with A / T
Freezing temperatureC–16–36–16–36Freezing temperatureF3–333–33
Anti-freeze / Anti-corrosion
coolant concentration%30503050
G10Itr.1.17 / 2.731.95 / 1.951.20 / 2.802.00 / 2.00G10
engineUS pt.2.47 / 5.774.12 / 4.122.54 / 5.924.23 / 4.23
Ratio of compound to
engineImp pt.2.06 / 4.803.43 / 3.432.11 / 3.703.52 / 3.52
cooling water
G13Itr.1.38 / 3.222.30 / 2.301.41 / 3.292.35 / 2.35G13
engineUS pt.2.92 / 6.804.86 / 4.862.98 / 6.954.96 / 4.96engineImp pt.2.43 / 5.674.05 / 4.052.48 / 5.794.13 / 4.13
Engine radiator and heater3.3 liters
(7.0 / 5.8 US / Imp pt.)3.4 liters
(7.2 / 6.0 US / Imp pt.)
Reservoir tank0.6 liters
(1.3 / 1.1 US / Imp pt.)
Total3.9 liters
(8.2 / 6.9 US / Imp pt.)4.0 liters
(8.5 / 7.0 US / Imp pt.)
Engine radiator and heater4.0 liters
(8.5 / 7.0 US / Imp pt.)4.1 liters
(8.6 / 7.2 US / Imp pt.)
Reservoir tank0.6 liters
(1.3 / 1.1 US / Imp pt.)
Total4.6 liters
(9.7 / 8.1 US / Imp pt.)4.7 liters
(9.9 / 8.3 US / Imp pt.)
Page 384 of 557
1. Radiator hose
2. Clamp
ENGINE COOLING 6B-7
ON-VEHICLE SERVICE
WARNING:
Check to make sure that engine coolant temperature is
cold before removing any part of cooling system.
Also be sure to disconnect negative cord from battery ter-
minal before removing any part.
COOLING WATER PIPES OR HOSES
REMOVAL
1) Drain cooling system.
2) To remove these pipes or hoses, loosen screw on each pipe or
hose clip and pull hose end off.
INSTALLATION
Install removed parts in reverse order of removal procedure, noting
the following.
Tighten each clamp bolt securely.
Refill cooling system with proper coolant, referring to description
on COOLANT of MAINTENANCE.
THERMOSTAT
REMOVAL
1) Disconnect negative cable at battery.
2) Drain cooling system and tighten drain plug.
3) Disconnect thermostat cap (1) from thermostat case (2).
Page 385 of 557
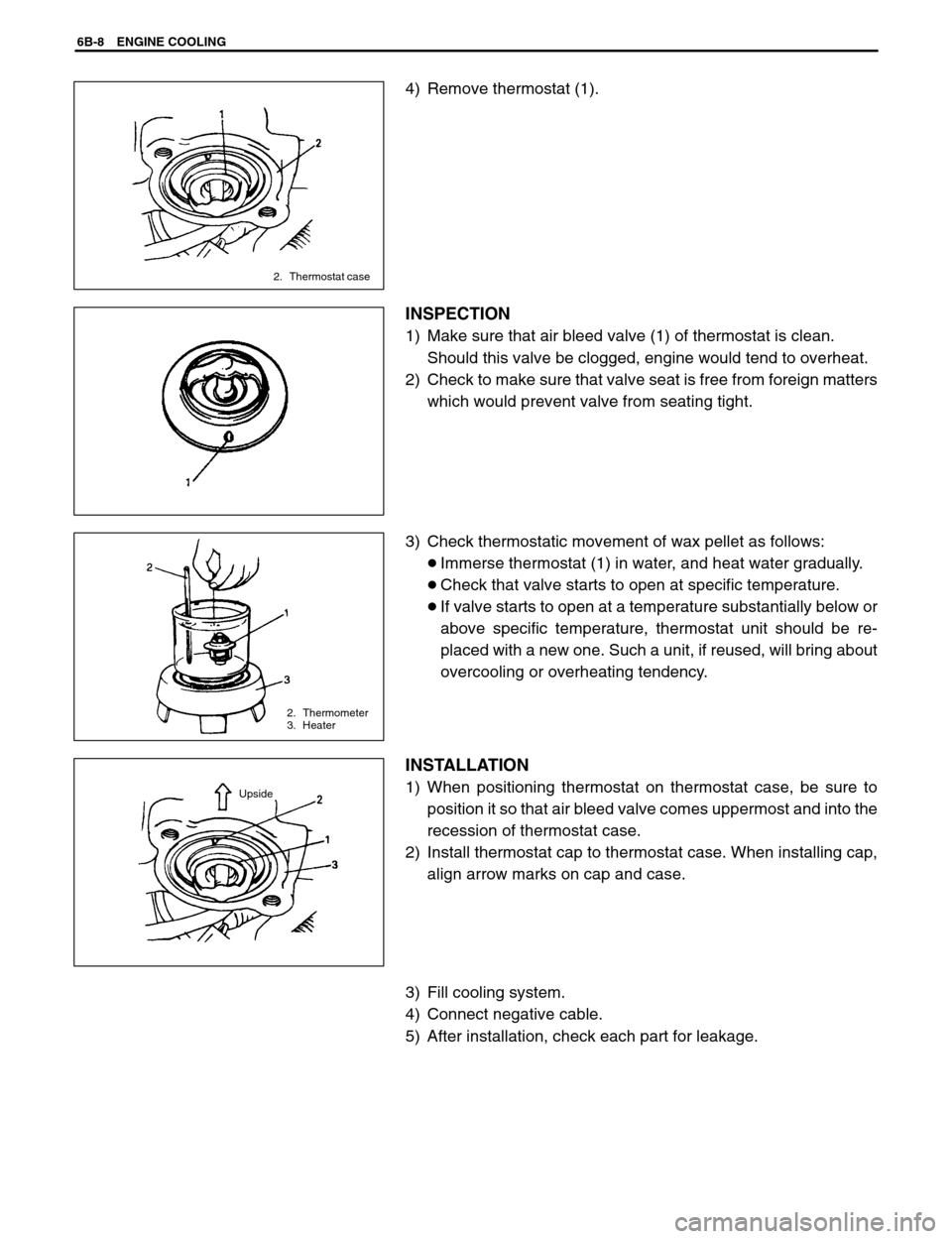
2. Thermostat case
2. Thermometer
3. Heater
Upside
6B-8 ENGINE COOLING
4) Remove thermostat (1).
INSPECTION
1) Make sure that air bleed valve (1) of thermostat is clean.
Should this valve be clogged, engine would tend to overheat.
2) Check to make sure that valve seat is free from foreign matters
which would prevent valve from seating tight.
3) Check thermostatic movement of wax pellet as follows:
Immerse thermostat (1) in water, and heat water gradually.
Check that valve starts to open at specific temperature.
If valve starts to open at a temperature substantially below or
above specific temperature, thermostat unit should be re-
placed with a new one. Such a unit, if reused, will bring about
overcooling or overheating tendency.
INSTALLATION
1) When positioning thermostat on thermostat case, be sure to
position it so that air bleed valve comes uppermost and into the
recession of thermostat case.
2) Install thermostat cap to thermostat case. When installing cap,
align arrow marks on cap and case.
3) Fill cooling system.
4) Connect negative cable.
5) After installation, check each part for leakage.
Page 399 of 557
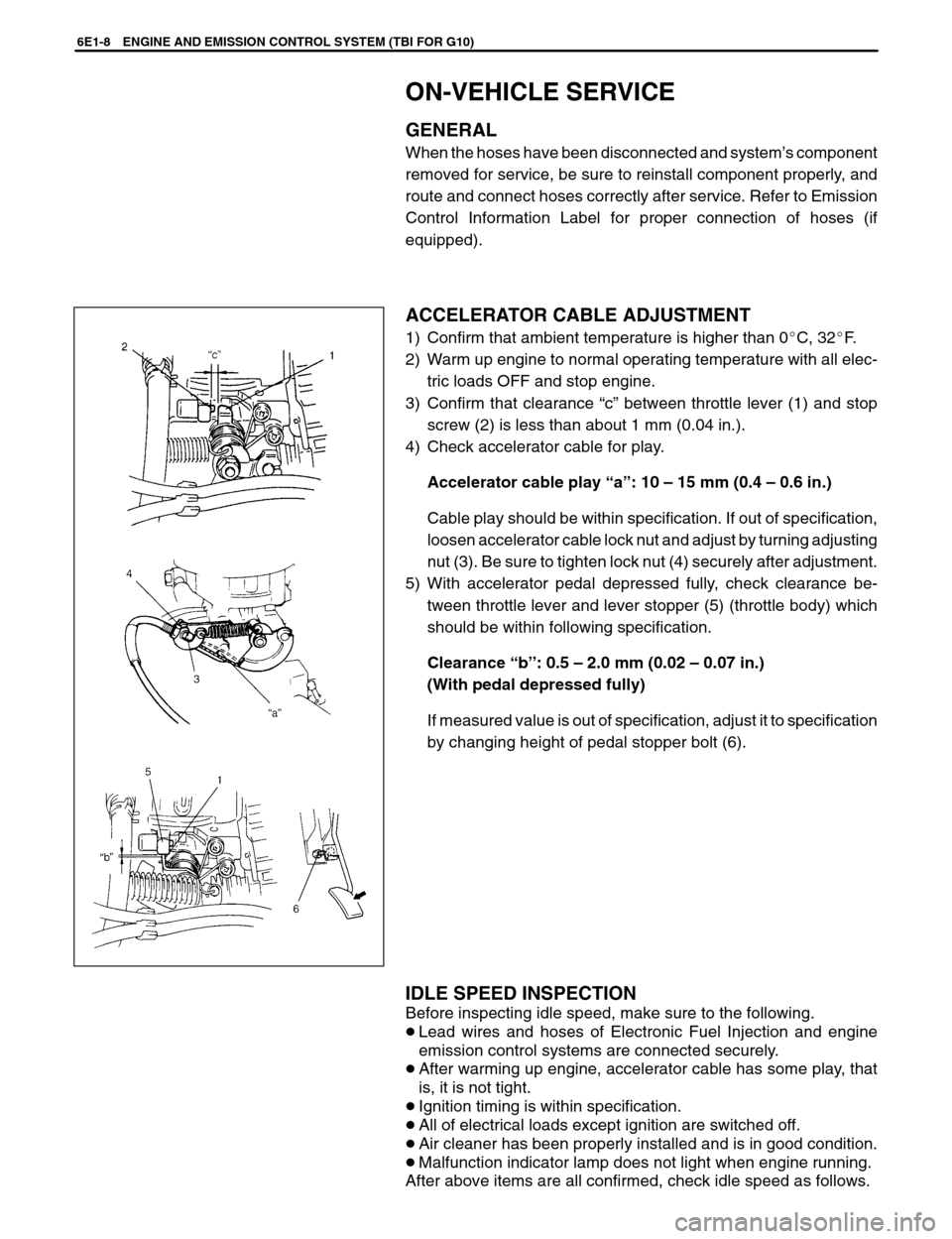
6E1-8 ENGINE AND EMISSION CONTROL SYSTEM (TBI FOR G10)
ON-VEHICLE SERVICE
GENERAL
When the hoses have been disconnected and system’s component
removed for service, be sure to reinstall component properly, and
route and connect hoses correctly after service. Refer to Emission
Control Information Label for proper connection of hoses (if
equipped).
ACCELERATOR CABLE ADJUSTMENT
1) Confirm that ambient temperature is higher than 0C, 32F.
2) Warm up engine to normal operating temperature with all elec-
tric loads OFF and stop engine.
3) Confirm that clearance “c” between throttle lever (1) and stop
screw (2) is less than about 1 mm (0.04 in.).
4) Check accelerator cable for play.
Accelerator cable play “a”: 10 – 15 mm (0.4 – 0.6 in.)
Cable play should be within specification. If out of specification,
loosen accelerator cable lock nut and adjust by turning adjusting
nut (3). Be sure to tighten lock nut (4) securely after adjustment.
5) With accelerator pedal depressed fully, check clearance be-
tween throttle lever and lever stopper (5) (throttle body) which
should be within following specification.
Clearance “b”: 0.5 – 2.0 mm (0.02 – 0.07 in.)
(With pedal depressed fully)
If measured value is out of specification, adjust it to specification
by changing height of pedal stopper bolt (6).
IDLE SPEED INSPECTION
Before inspecting idle speed, make sure to the following.
Lead wires and hoses of Electronic Fuel Injection and engine
emission control systems are connected securely.
After warming up engine, accelerator cable has some play, that
is, it is not tight.
Ignition timing is within specification.
All of electrical loads except ignition are switched off.
Air cleaner has been properly installed and is in good condition.
Malfunction indicator lamp does not light when engine running.
After above items are all confirmed, check idle speed as follows.