Page 358 of 557
ENGINE MECHANICAL (G13B, 1-CAM 16-VALVES ENGINE) 6A1-63
6) Reverse removal procedure for installation, as previously out-
lined.
7) Adjust water pump drive belt tension referring to Section 6B.
8) Adjust power steering pump belt tension or A / C compressor
belt tension, if equipped.
Refer to Section 0B.
9) Adjust accelerator cable play.
Refer to Section 6E.
10) Check to ensure that all removed parts are back in place. Rein-
stall any necessary parts which have not been reinstalled.
11) Refill engine with engine oil by referring to item “ENGINE OIL
CHANGE” in Section 0B.
12) Refill cooling system referring to Section 6B.
13) Connect negative cable at battery.
14) Check ignition timing referring to Section 6F.
15) Verify that there is no fuel leakage, coolant leakage, oil leakage
and exhaust gas leakage at each connection.
Page 361 of 557
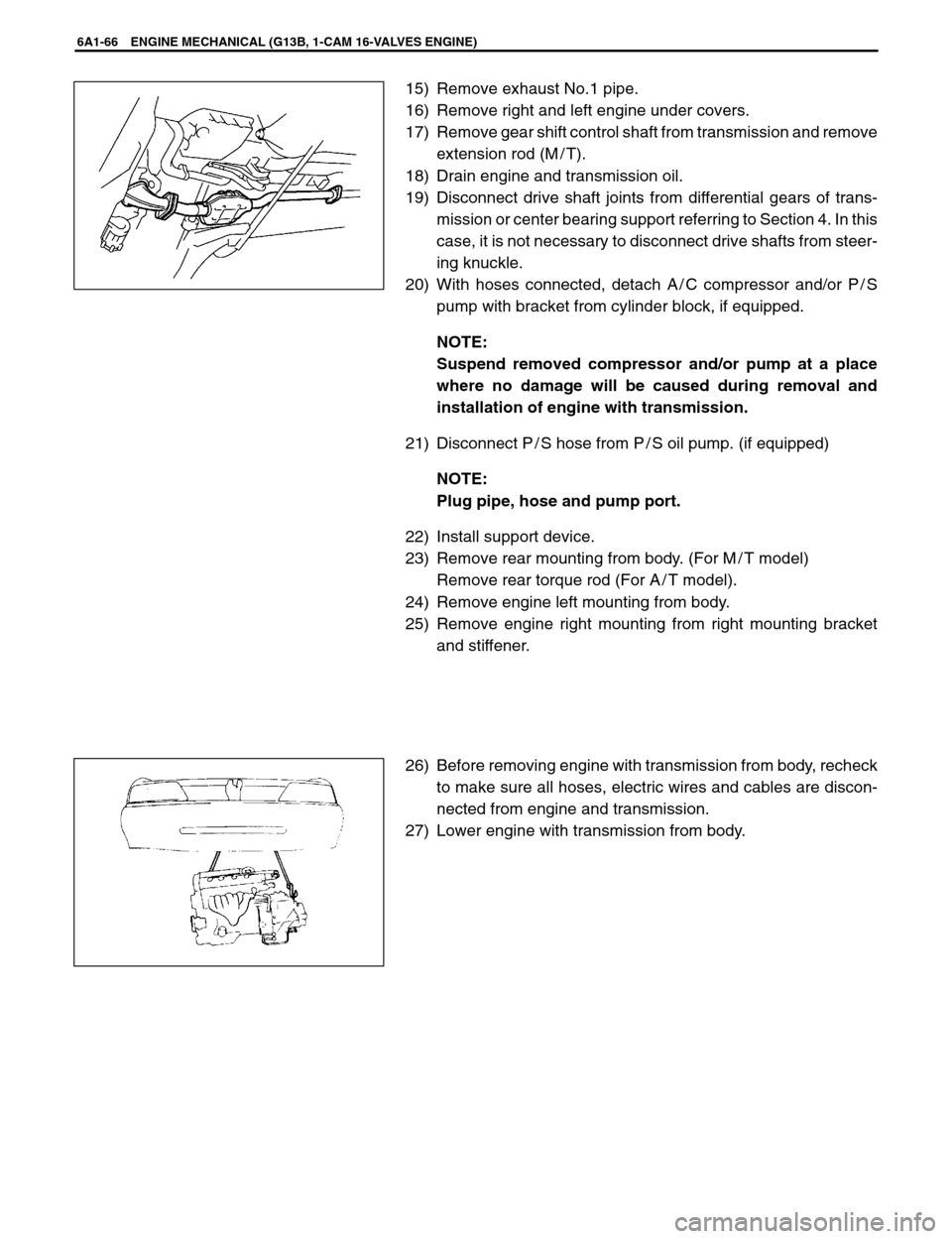
6A1-66 ENGINE MECHANICAL (G13B, 1-CAM 16-VALVES ENGINE)
15) Remove exhaust No.1 pipe.
16) Remove right and left engine under covers.
17) Remove gear shift control shaft from transmission and remove
extension rod (M / T).
18) Drain engine and transmission oil.
19) Disconnect drive shaft joints from differential gears of trans-
mission or center bearing support referring to Section 4. In this
case, it is not necessary to disconnect drive shafts from steer-
ing knuckle.
20) With hoses connected, detach A / C compressor and/or P / S
pump with bracket from cylinder block, if equipped.
NOTE:
Suspend removed compressor and/or pump at a place
where no damage will be caused during removal and
installation of engine with transmission.
21) Disconnect P / S hose from P / S oil pump. (if equipped)
NOTE:
Plug pipe, hose and pump port.
22) Install support device.
23) Remove rear mounting from body. (For M / T model)
Remove rear torque rod (For A / T model).
24) Remove engine left mounting from body.
25) Remove engine right mounting from right mounting bracket
and stiffener.
26) Before removing engine with transmission from body, recheck
to make sure all hoses, electric wires and cables are discon-
nected from engine and transmission.
27) Lower engine with transmission from body.
Page 362 of 557
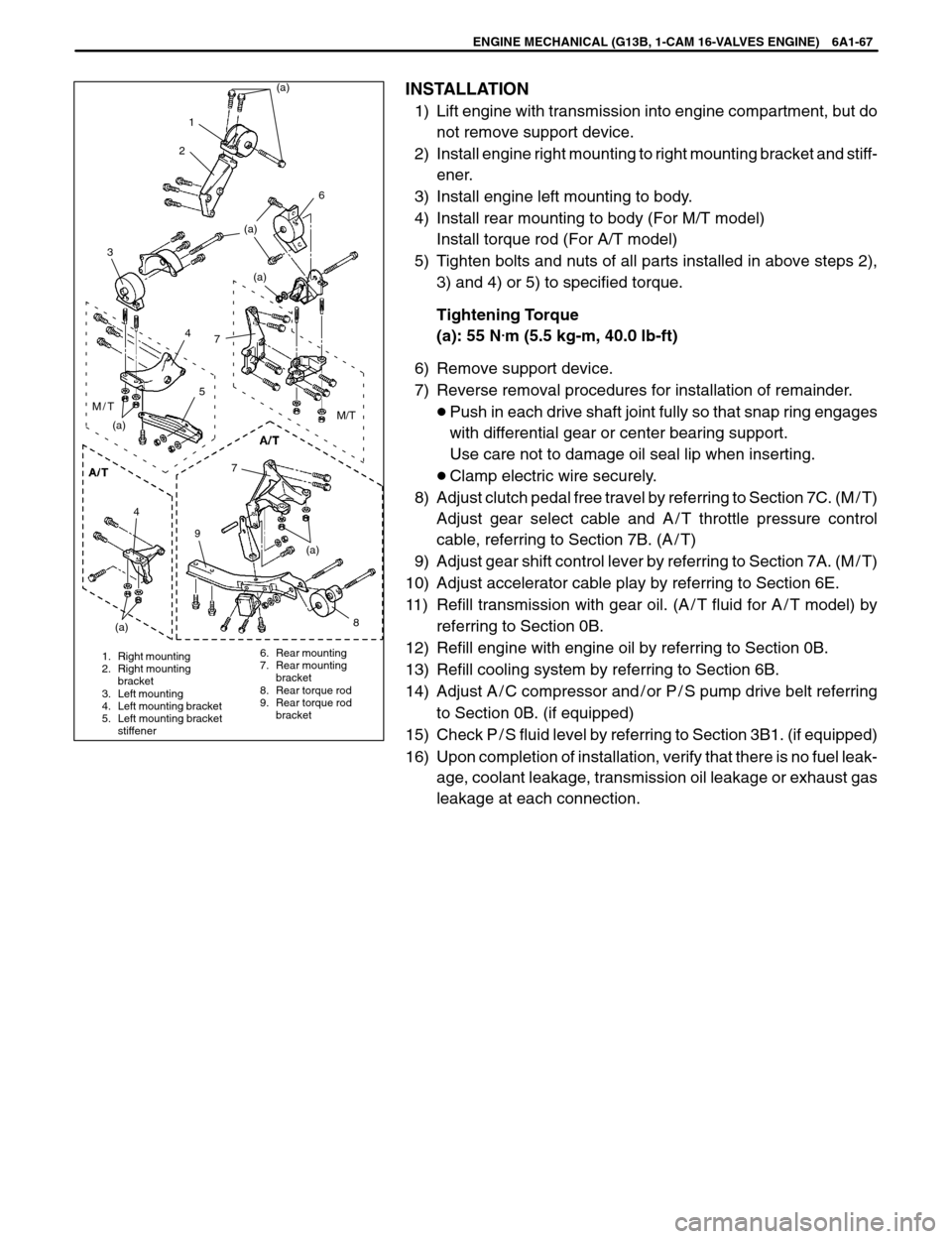
(a)
1
2
3
(a)
(a)
6
74
5
(a)
M/TM/T
9
(a)
4
7
(a)
8
1. Right mounting
2. Right mounting
bracket
3. Left mounting
4. Left mounting bracket
5. Left mounting bracket
stiffener6. Rear mounting
7. Rear mounting
bracket
8. Rear torque rod
9. Rear torque rod
bracket
ENGINE MECHANICAL (G13B, 1-CAM 16-VALVES ENGINE) 6A1-67
INSTALLATION
1) Lift engine with transmission into engine compartment, but do
not remove support device.
2) Install engine right mounting to right mounting bracket and stiff-
ener.
3) Install engine left mounting to body.
4) Install rear mounting to body (For M/T model)
Install torque rod (For A/T model)
5) Tighten bolts and nuts of all parts installed in above steps 2),
3) and 4) or 5) to specified torque.
Tightening Torque
(a): 55 N
.m (5.5 kg-m, 40.0 lb-ft)
6) Remove support device.
7) Reverse removal procedures for installation of remainder.
Push in each drive shaft joint fully so that snap ring engages
with differential gear or center bearing support.
Use care not to damage oil seal lip when inserting.
Clamp electric wire securely.
8) Adjust clutch pedal free travel by referring to Section 7C. (M / T)
Adjust gear select cable and A / T throttle pressure control
cable, referring to Section 7B. (A / T)
9) Adjust gear shift control lever by referring to Section 7A. (M / T)
10) Adjust accelerator cable play by referring to Section 6E.
11) Refill transmission with gear oil. (A / T fluid for A / T model) by
referring to Section 0B.
12) Refill engine with engine oil by referring to Section 0B.
13) Refill cooling system by referring to Section 6B.
14) Adjust A / C compressor and / or P / S pump drive belt referring
to Section 0B. (if equipped)
15) Check P / S fluid level by referring to Section 3B1. (if equipped)
16) Upon completion of installation, verify that there is no fuel leak-
age, coolant leakage, transmission oil leakage or exhaust gas
leakage at each connection.
Page 377 of 557
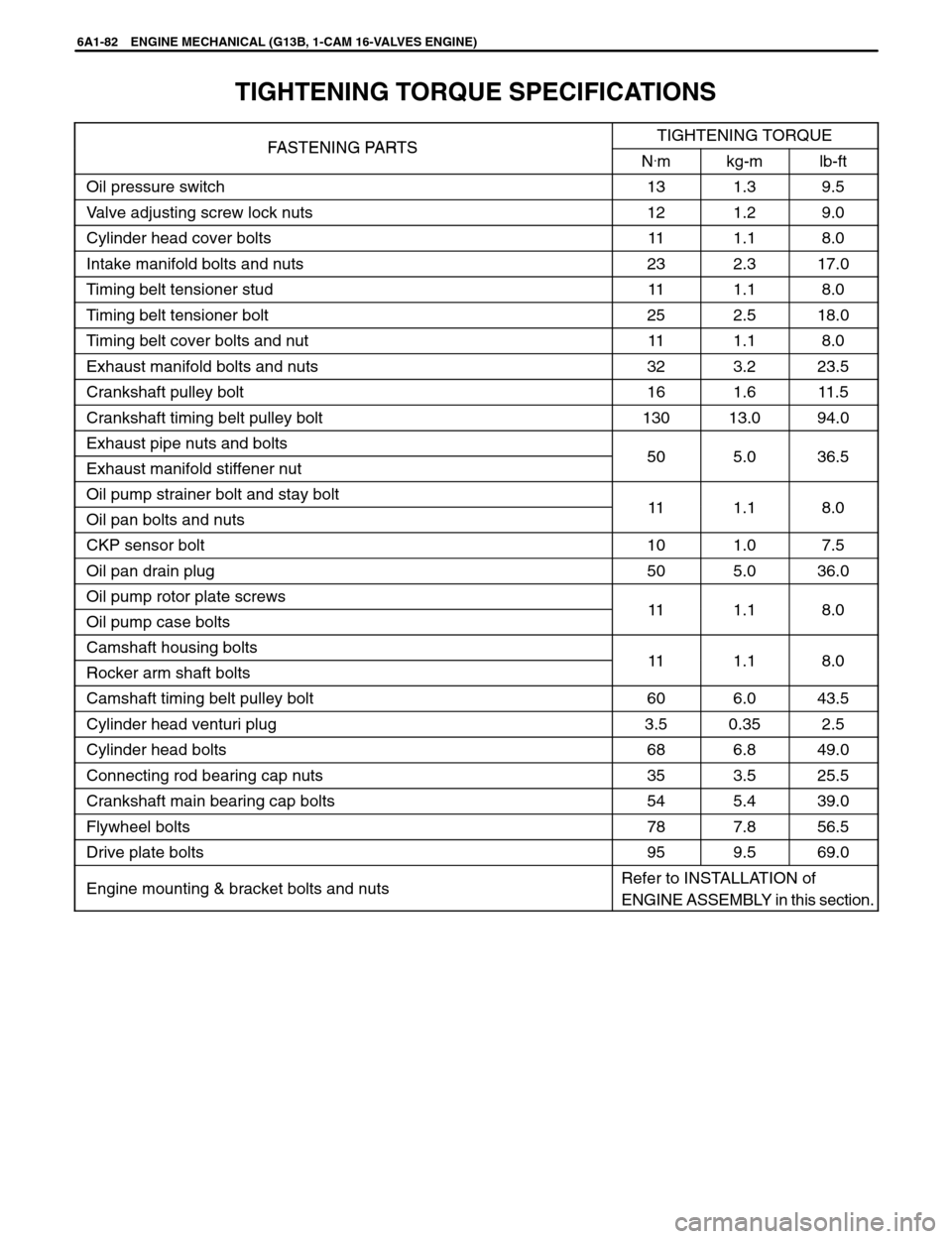
6A1-82 ENGINE MECHANICAL (G13B, 1-CAM 16-VALVES ENGINE)
TIGHTENING TORQUE SPECIFICATIONS
FASTENING PARTSTIGHTENING TORQUEFASTENING PA R T SN.mkg-mlb-ft
Oil pressure switch131.39.5
Valve adjusting screw lock nuts121.29.0
Cylinder head cover bolts111.18.0
Intake manifold bolts and nuts232.317.0
Timing belt tensioner stud111.18.0
Timing belt tensioner bolt252.518.0
Timing belt cover bolts and nut111.18.0
Exhaust manifold bolts and nuts323.223.5
Crankshaft pulley bolt161.611.5
Crankshaft timing belt pulley bolt13013.094.0
Exhaust pipe nuts and bolts505036 5Exhaust manifold stiffener nut505.036.5
Oil pump strainer bolt and stay bolt111180Oil pan bolts and nuts111.18.0
CKP sensor bolt101.07.5
Oil pan drain plug505.036.0
Oil pump rotor plate screws111180Oil pump case bolts111.18.0
Camshaft housing bolts111180Rocker arm shaft bolts111.18.0
Camshaft timing belt pulley bolt606.043.5
Cylinder head venturi plug3.50.352.5
Cylinder head bolts686.849.0
Connecting rod bearing cap nuts353.525.5
Crankshaft main bearing cap bolts545.439.0
Flywheel bolts787.856.5
Drive plate bolts959.569.0
Engine mounting & bracket bolts and nutsRefer to INSTALLATION of
ENGINE ASSEMBLY in this section.
Page 394 of 557
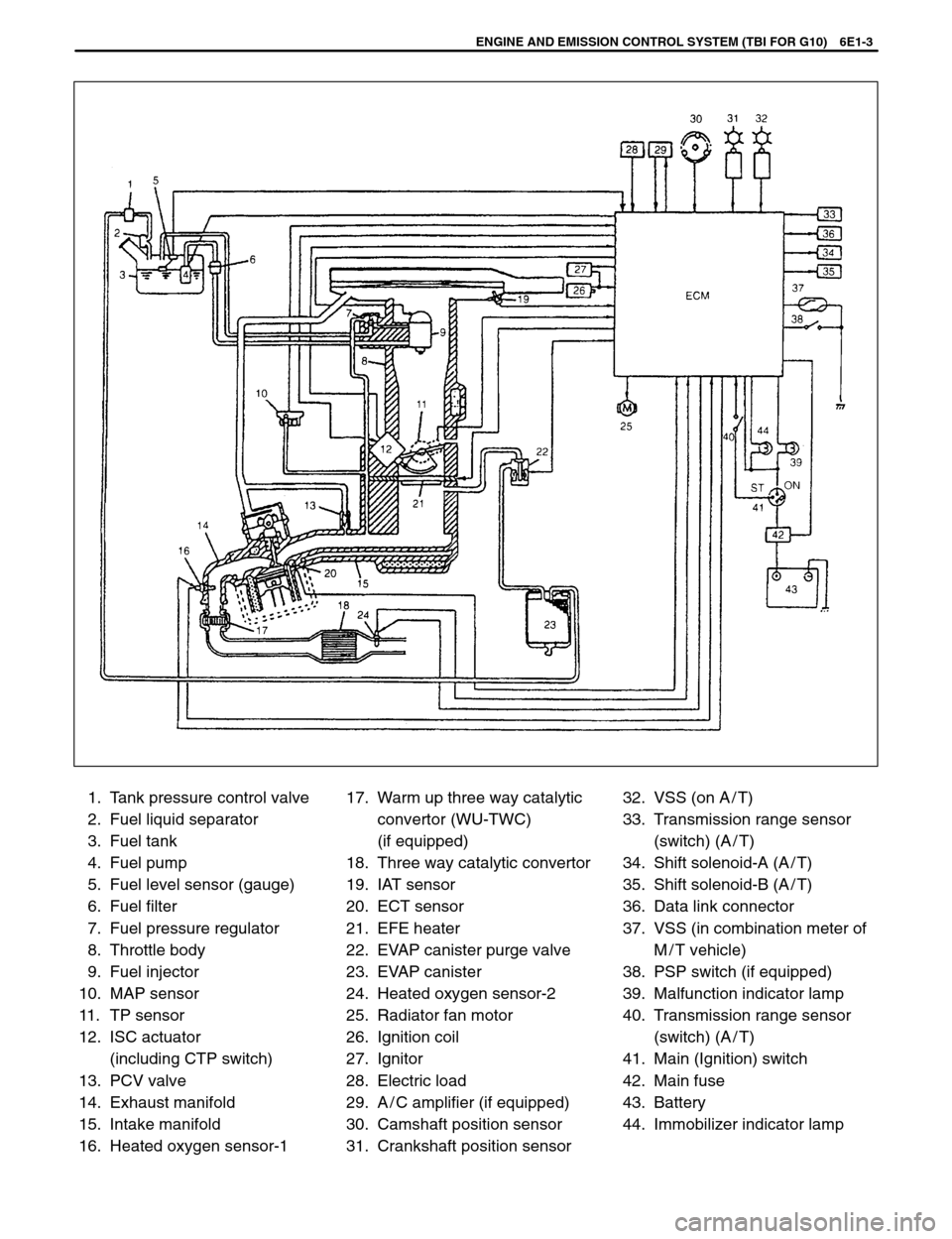
ENGINE AND EMISSION CONTROL SYSTEM (TBI FOR G10) 6E1-3
1. Tank pressure control valve
2. Fuel liquid separator
3. Fuel tank
4. Fuel pump
5. Fuel level sensor (gauge)
6. Fuel filter
7. Fuel pressure regulator
8. Throttle body
9. Fuel injector
10. MAP sensor
11. TP sensor
12. ISC actuator
(including CTP switch)
13. PCV valve
14. Exhaust manifold
15. Intake manifold
16. Heated oxygen sensor-117. Warm up three way catalytic
convertor (WU-TWC)
(if equipped)
18. Three way catalytic convertor
19. IAT sensor
20. ECT sensor
21. EFE heater
22. EVAP canister purge valve
23. EVAP canister
24. Heated oxygen sensor-2
25. Radiator fan motor
26. Ignition coil
27. Ignitor
28. Electric load
29. A / C amplifier (if equipped)
30. Camshaft position sensor
31. Crankshaft position sensor32. VSS (on A / T)
33. Transmission range sensor
(switch) (A / T)
34. Shift solenoid-A (A / T)
35. Shift solenoid-B (A / T)
36. Data link connector
37. VSS (in combination meter of
M / T vehicle)
38. PSP switch (if equipped)
39. Malfunction indicator lamp
40. Transmission range sensor
(switch) (A / T)
41. Main (Ignition) switch
42. Main fuse
43. Battery
44. Immobilizer indicator lamp
Page 414 of 557
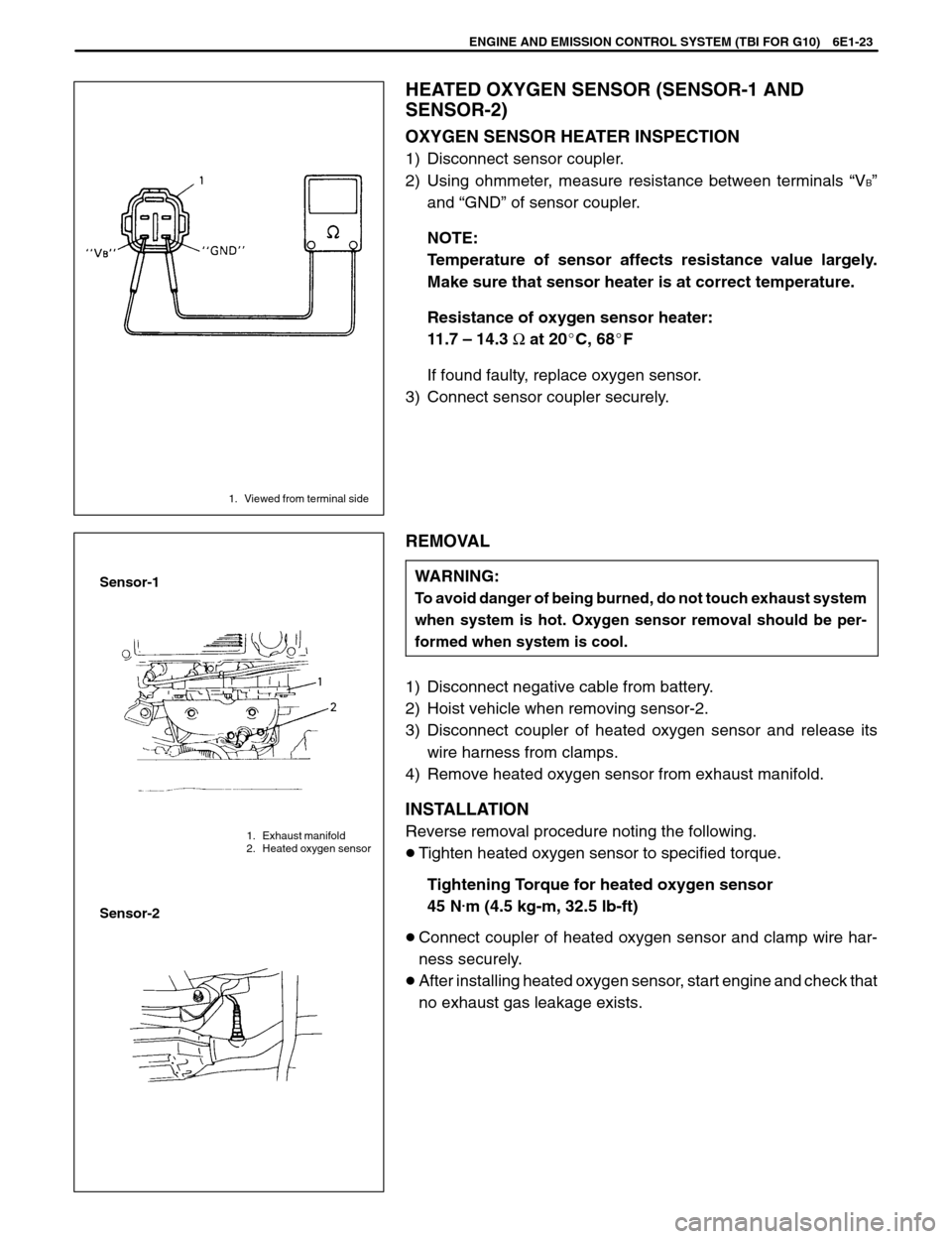
ENGINE AND EMISSION CONTROL SYSTEM (TBI FOR G10) 6E1-23
1. Viewed from terminal side
1. Exhaust manifold
2. Heated oxygen sensor
Sensor-1
Sensor-2
HEATED OXYGEN SENSOR (SENSOR-1 AND
SENSOR-2)
OXYGEN SENSOR HEATER INSPECTION
1) Disconnect sensor coupler.
2) Using ohmmeter, measure resistance between terminals “V
B”
and “GND” of sensor coupler.
NOTE:
Temperature of sensor affects resistance value largely.
Make sure that sensor heater is at correct temperature.
Resistance of oxygen sensor heater:
11.7 – 14.3 Ω at 20C, 68F
If found faulty, replace oxygen sensor.
3) Connect sensor coupler securely.
REMOVAL
WARNING:
To avoid danger of being burned, do not touch exhaust system
when system is hot. Oxygen sensor removal should be per-
formed when system is cool.
1) Disconnect negative cable from battery.
2) Hoist vehicle when removing sensor-2.
3) Disconnect coupler of heated oxygen sensor and release its
wire harness from clamps.
4) Remove heated oxygen sensor from exhaust manifold.
INSTALLATION
Reverse removal procedure noting the following.
Tighten heated oxygen sensor to specified torque.
Tightening Torque for heated oxygen sensor
45 N
.m (4.5 kg-m, 32.5 lb-ft)
Connect coupler of heated oxygen sensor and clamp wire har-
ness securely.
After installing heated oxygen sensor, start engine and check that
no exhaust gas leakage exists.
Page 459 of 557
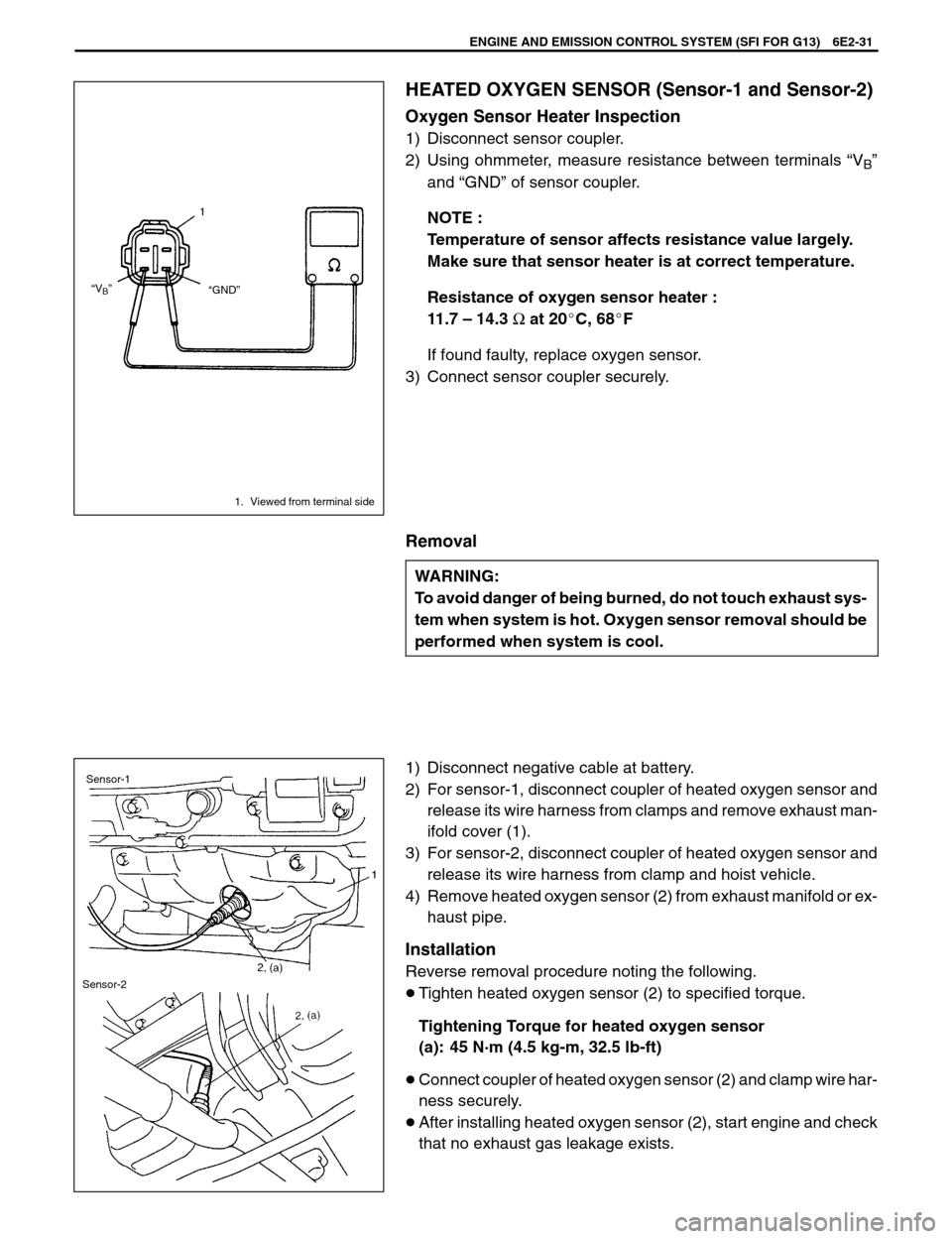
ENGINE AND EMISSION CONTROL SYSTEM (SFI FOR G13) 6E2-31
1. Viewed from terminal side
Sensor-1
Sensor-2
“VB”
“GND”
HEATED OXYGEN SENSOR (Sensor-1 and Sensor-2)
Oxygen Sensor Heater Inspection
1) Disconnect sensor coupler.
2) Using ohmmeter, measure resistance between terminals “V
B”
and “GND” of sensor coupler.
NOTE :
Temperature of sensor affects resistance value largely.
Make sure that sensor heater is at correct temperature.
Resistance of oxygen sensor heater :
11.7 – 14.3 Ω at 20C, 68F
If found faulty, replace oxygen sensor.
3) Connect sensor coupler securely.
Removal
WARNING:
To avoid danger of being burned, do not touch exhaust sys-
tem when system is hot. Oxygen sensor removal should be
performed when system is cool.
1) Disconnect negative cable at battery.
2) For sensor-1, disconnect coupler of heated oxygen sensor and
release its wire harness from clamps and remove exhaust man-
ifold cover (1).
3) For sensor-2, disconnect coupler of heated oxygen sensor and
release its wire harness from clamp and hoist vehicle.
4) Remove heated oxygen sensor (2) from exhaust manifold or ex-
haust pipe.
Installation
Reverse removal procedure noting the following.
Tighten heated oxygen sensor (2) to specified torque.
Tightening Torque for heated oxygen sensor
(a): 45 N·m (4.5 kg-m, 32.5 lb-ft)
Connect coupler of heated oxygen sensor (2) and clamp wire har-
ness securely.
After installing heated oxygen sensor (2), start engine and check
that no exhaust gas leakage exists.
Page 489 of 557
6K
1. Exhaust manifold
2. Seal
3. WU-TWC
4. Exhaust pipe
5. Muffler
6. Muffler mounting
7. Gasket
8. Heated oxygen sensor : Tightening Torque : Do not reuse
[For 1.0 2WD H / B model]
EXHAUST SYSTEM 6K-1
SECTION 6K
EXHAUST SYSTEM
NOTE:
For the descriptions (items) not found in this section, refer to the same section of Service Manual men-
tioned in FOREWORD of this manual.
CONTENTS
ON-VEHICLE SERVICE6K-1 . . . . . . . . . . . . . . . . . . . . . . . . . . . . . . . . . . . . . . . . . . . . . . . . . . . . . . . . . . . . . . . . . . . .
ON-VEHICLE SERVICE