Page 291 of 557
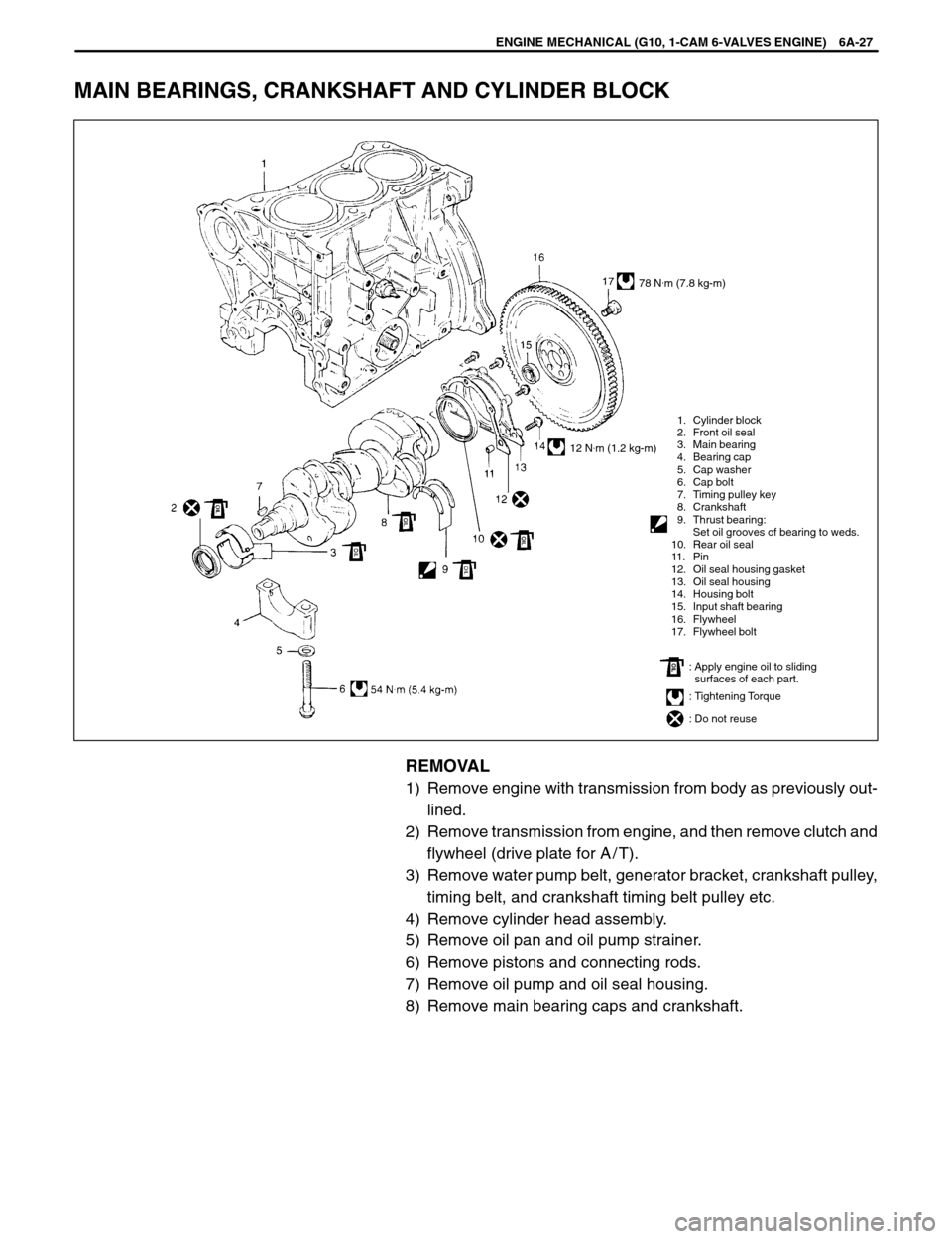
1. Cylinder block
2. Front oil seal
3. Main bearing
4. Bearing cap
5. Cap washer
6. Cap bolt
7. Timing pulley key
8. Crankshaft
9. Thrust bearing:
Set oil grooves of bearing to weds.
10. Rear oil seal
11. Pin
12. Oil seal housing gasket
13. Oil seal housing
14. Housing bolt
15. Input shaft bearing
16. Flywheel
17. Flywheel bolt
: Tightening Torque
: Do not reuse
: Apply engine oil to sliding
: surfaces of each part.
78 N.m (7.8 kg-m)
12 N
.m (1.2 kg-m)
ENGINE MECHANICAL (G10, 1-CAM 6-VALVES ENGINE) 6A-27
MAIN BEARINGS, CRANKSHAFT AND CYLINDER BLOCK
REMOVAL
1) Remove engine with transmission from body as previously out-
lined.
2) Remove transmission from engine, and then remove clutch and
flywheel (drive plate for A / T).
3) Remove water pump belt, generator bracket, crankshaft pulley,
timing belt, and crankshaft timing belt pulley etc.
4) Remove cylinder head assembly.
5) Remove oil pan and oil pump strainer.
6) Remove pistons and connecting rods.
7) Remove oil pump and oil seal housing.
8) Remove main bearing caps and crankshaft.
Page 293 of 557
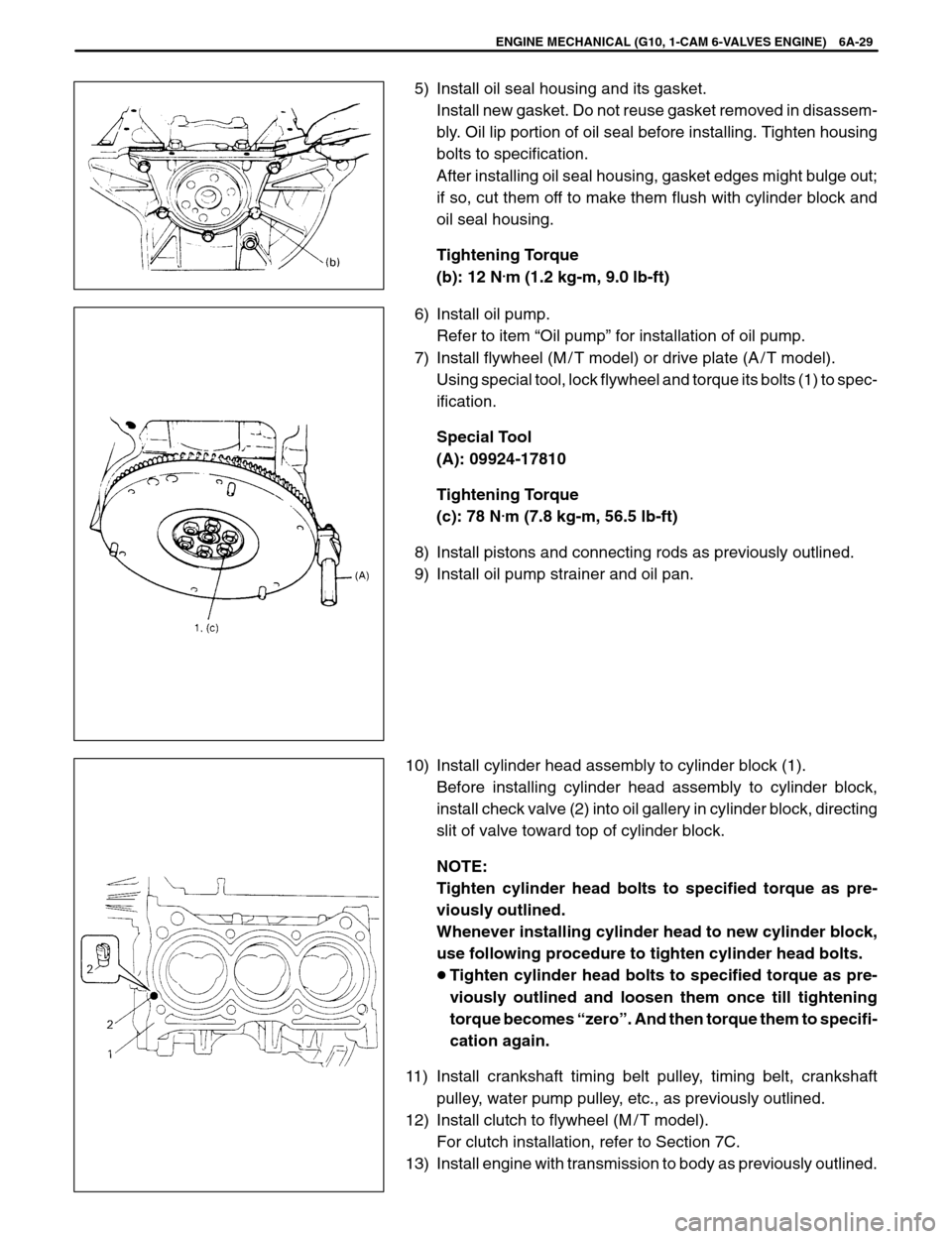
ENGINE MECHANICAL (G10, 1-CAM 6-VALVES ENGINE) 6A-29
5) Install oil seal housing and its gasket.
Install new gasket. Do not reuse gasket removed in disassem-
bly. Oil lip portion of oil seal before installing. Tighten housing
bolts to specification.
After installing oil seal housing, gasket edges might bulge out;
if so, cut them off to make them flush with cylinder block and
oil seal housing.
Tightening Torque
(b): 12 N
.m (1.2 kg-m, 9.0 lb-ft)
6) Install oil pump.
Refer to item “Oil pump” for installation of oil pump.
7) Install flywheel (M / T model) or drive plate (A / T model).
Using special tool, lock flywheel and torque its bolts (1) to spec-
ification.
Special Tool
(A): 09924-17810
Tightening Torque
(c): 78 N
.m (7.8 kg-m, 56.5 lb-ft)
8) Install pistons and connecting rods as previously outlined.
9) Install oil pump strainer and oil pan.
10) Install cylinder head assembly to cylinder block (1).
Before installing cylinder head assembly to cylinder block,
install check valve (2) into oil gallery in cylinder block, directing
slit of valve toward top of cylinder block.
NOTE:
Tighten cylinder head bolts to specified torque as pre-
viously outlined.
Whenever installing cylinder head to new cylinder block,
use following procedure to tighten cylinder head bolts.
Tighten cylinder head bolts to specified torque as pre-
viously outlined and loosen them once till tightening
torque becomes “zero”. And then torque them to specifi-
cation again.
11) Install crankshaft timing belt pulley, timing belt, crankshaft
pulley, water pump pulley, etc., as previously outlined.
12) Install clutch to flywheel (M / T model).
For clutch installation, refer to Section 7C.
13) Install engine with transmission to body as previously outlined.
Page 300 of 557
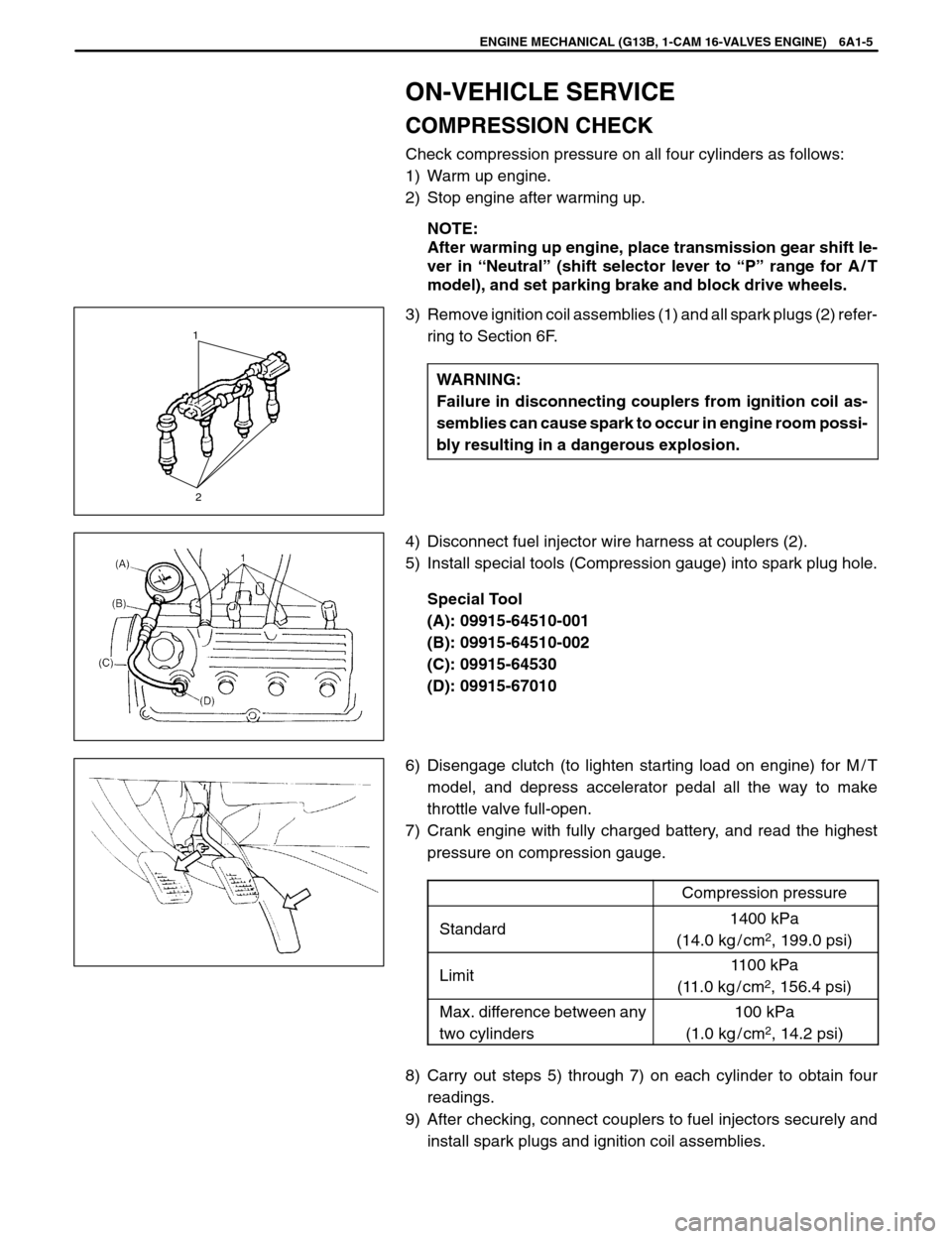
1
2
ENGINE MECHANICAL (G13B, 1-CAM 16-VALVES ENGINE) 6A1-5
ON-VEHICLE SERVICE
COMPRESSION CHECK
Check compression pressure on all four cylinders as follows:
1) Warm up engine.
2) Stop engine after warming up.
NOTE:
After warming up engine, place transmission gear shift le-
ver in “Neutral” (shift selector lever to “P” range for A / T
model), and set parking brake and block drive wheels.
3) Remove ignition coil assemblies (1) and all spark plugs (2) refer-
ring to Section 6F.
WARNING:
Failure in disconnecting couplers from ignition coil as-
semblies can cause spark to occur in engine room possi-
bly resulting in a dangerous explosion.
4) Disconnect fuel injector wire harness at couplers (2).
5) Install special tools (Compression gauge) into spark plug hole.
Special Tool
(A): 09915-64510-001
(B): 09915-64510-002
(C): 09915-64530
(D): 09915-67010
6) Disengage clutch (to lighten starting load on engine) for M / T
model, and depress accelerator pedal all the way to make
throttle valve full-open.
7) Crank engine with fully charged battery, and read the highest
pressure on compression gauge.
Compression pressure
Standard1400 kPa
(14.0 kg / cm
2, 199.0 psi)
Limit1100 kPa
(11.0 kg / cm
2, 156.4 psi)
Max. difference between any
two cylinders100 kPa
(1.0 kg / cm
2, 14.2 psi)
8) Carry out steps 5) through 7) on each cylinder to obtain four
readings.
9) After checking, connect couplers to fuel injectors securely and
install spark plugs and ignition coil assemblies.
Page 301 of 557
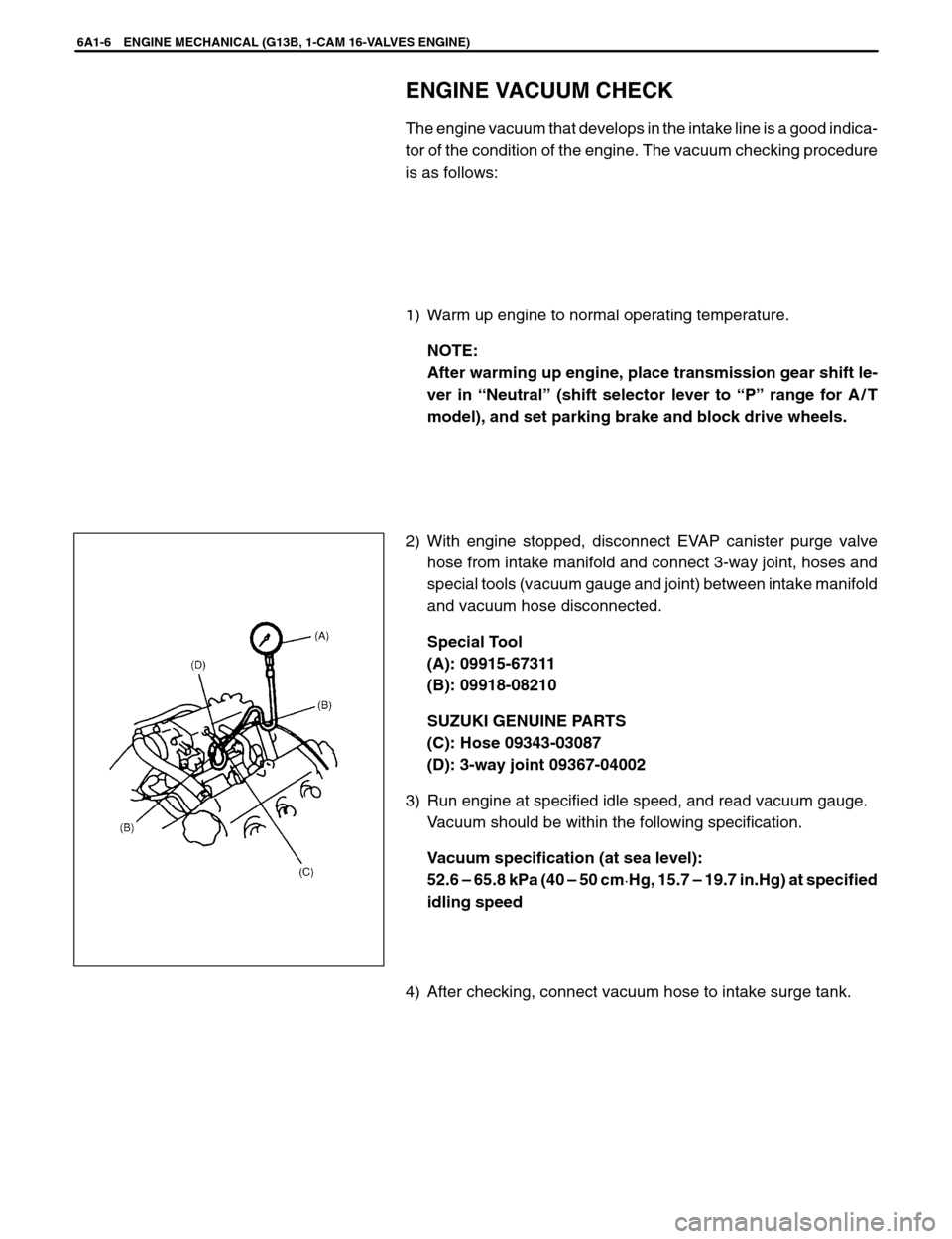
6A1-6 ENGINE MECHANICAL (G13B, 1-CAM 16-VALVES ENGINE)
ENGINE VACUUM CHECK
The engine vacuum that develops in the intake line is a good indica-
tor of the condition of the engine. The vacuum checking procedure
is as follows:
1) Warm up engine to normal operating temperature.
NOTE:
After warming up engine, place transmission gear shift le-
ver in “Neutral” (shift selector lever to “P” range for A / T
model), and set parking brake and block drive wheels.
2) With engine stopped, disconnect EVAP canister purge valve
hose from intake manifold and connect 3-way joint, hoses and
special tools (vacuum gauge and joint) between intake manifold
and vacuum hose disconnected.
Special Tool
(A): 09915-67311
(B): 09918-08210
SUZUKI GENUINE PARTS
(C): Hose 09343-03087
(D): 3-way joint 09367-04002
3) Run engine at specified idle speed, and read vacuum gauge.
Vacuum should be within the following specification.
Vacuum specification (at sea level):
52.6 – 65.8 kPa (40 – 50 cmHg, 15.7 – 19.7 in.Hg) at specified
idling speed
4) After checking, connect vacuum hose to intake surge tank.
Page 302 of 557
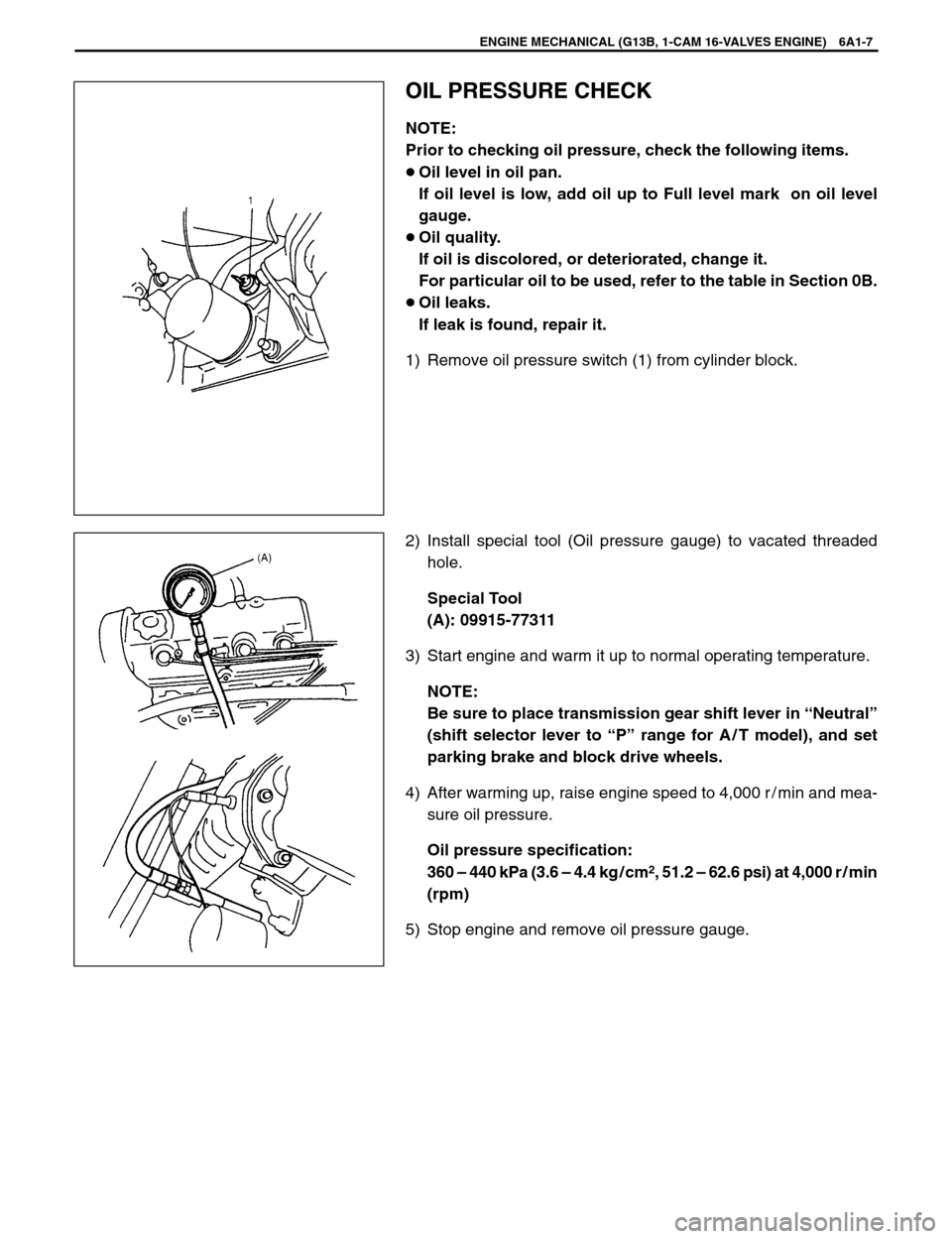
ENGINE MECHANICAL (G13B, 1-CAM 16-VALVES ENGINE) 6A1-7
OIL PRESSURE CHECK
NOTE:
Prior to checking oil pressure, check the following items.
Oil level in oil pan.
If oil level is low, add oil up to Full level mark on oil level
gauge.
Oil quality.
If oil is discolored, or deteriorated, change it.
For particular oil to be used, refer to the table in Section 0B.
Oil leaks.
If leak is found, repair it.
1) Remove oil pressure switch (1) from cylinder block.
2) Install special tool (Oil pressure gauge) to vacated threaded
hole.
Special Tool
(A): 09915-77311
3) Start engine and warm it up to normal operating temperature.
NOTE:
Be sure to place transmission gear shift lever in “Neutral”
(shift selector lever to “P” range for A / T model), and set
parking brake and block drive wheels.
4) After warming up, raise engine speed to 4,000 r / min and mea-
sure oil pressure.
Oil pressure specification:
360 – 440 kPa (3.6 – 4.4 kg / cm
2, 51.2 – 62.6 psi) at 4,000 r / min
(rpm)
5) Stop engine and remove oil pressure gauge.
Page 315 of 557
1.“V” mark on cylinder
head cover
2. Timing mark by “E” on
camshaft timing belt pulley
3. Arrow mark on oil
pump case
4. Punch mark on crankshaft
timing belt pulley
4. Tensioner stud
6. Damper
6
6A1-20 ENGINE MECHANICAL (G13B, 1-CAM 16-VALVES ENGINE)
8) Lock crankshaft inserting flat end rod or the like (2) between fly-
wheel ring gear and transmission case, after removing clutch
housing (torque converter housing for A / T) lower plate.
With crankshaft locked, remove crankshaft timing belt pulley
bolt (3).
9) Remove crankshaft pulley bolts (1).
10) Remove crankshaft pulley (4).
11) Install crankshaft timing belt pulley bolt temporarily to turn
crankshaft.
12) Release harness clamps.
13) Remove timing belt outside cover.
14) For installation of timing belt, align 4 timing marks as shown in
figure by turning crankshaft.
15) Remove timing belt tensioner (3), tensioner plate (2), tensioner
spring (5) and timing belt (1).
Page 323 of 557
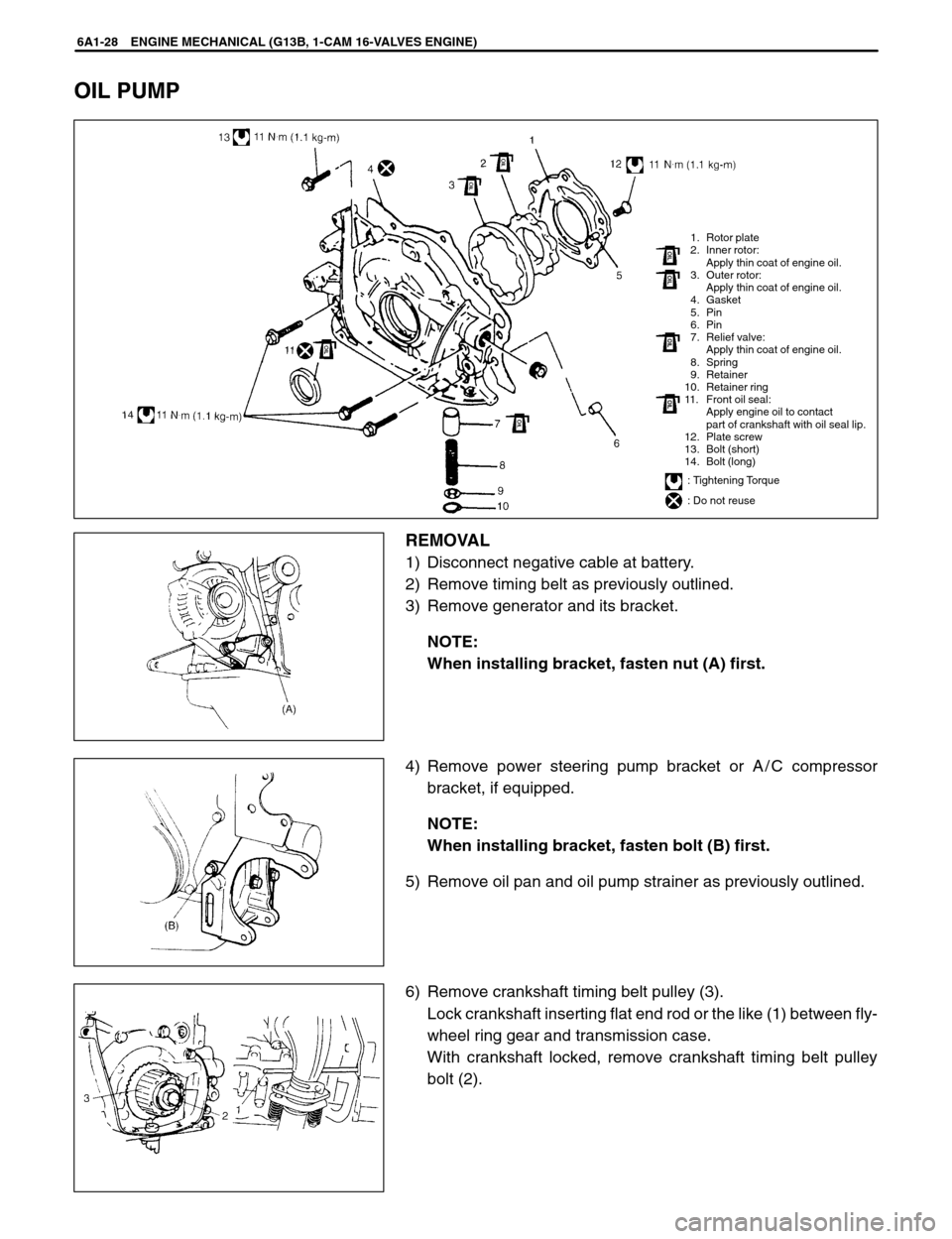
1. Rotor plate
2. Inner rotor:
Apply thin coat of engine oil.
3. Outer rotor:
Apply thin coat of engine oil.
4. Gasket
5. Pin
6. Pin
7. Relief valve:
Apply thin coat of engine oil.
8. Spring
9. Retainer
10. Retainer ring
11. Front oil seal:
Apply engine oil to contact
part of crankshaft with oil seal lip.
12. Plate screw
13. Bolt (short)
14. Bolt (long)
: Tightening Torque
: Do not reuse
6A1-28 ENGINE MECHANICAL (G13B, 1-CAM 16-VALVES ENGINE)
OIL PUMP
REMOVAL
1) Disconnect negative cable at battery.
2) Remove timing belt as previously outlined.
3) Remove generator and its bracket.
NOTE:
When installing bracket, fasten nut (A) first.
4) Remove power steering pump bracket or A / C compressor
bracket, if equipped.
NOTE:
When installing bracket, fasten bolt (B) first.
5) Remove oil pan and oil pump strainer as previously outlined.
6) Remove crankshaft timing belt pulley (3).
Lock crankshaft inserting flat end rod or the like (1) between fly-
wheel ring gear and transmission case.
With crankshaft locked, remove crankshaft timing belt pulley
bolt (2).
Page 339 of 557
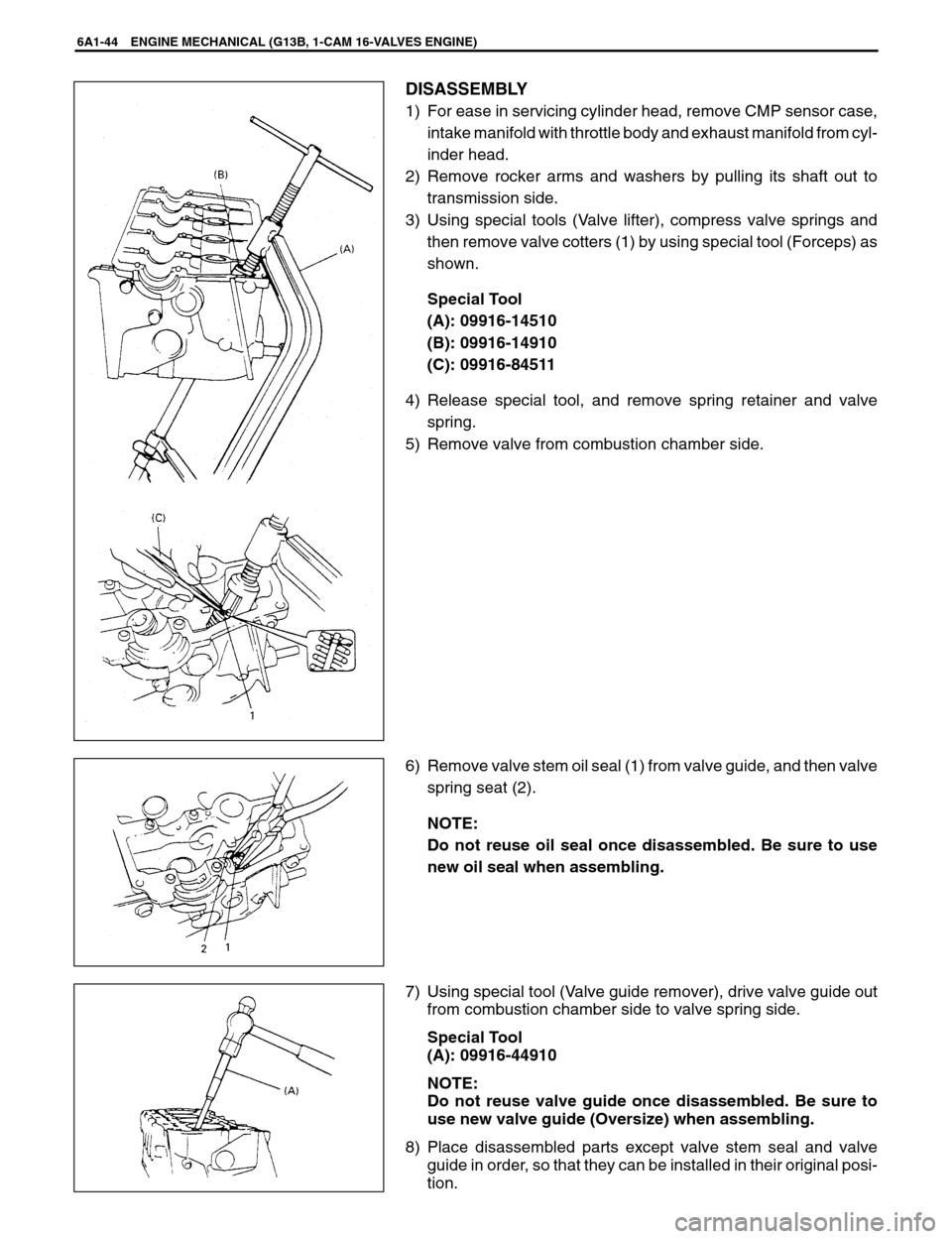
6A1-44 ENGINE MECHANICAL (G13B, 1-CAM 16-VALVES ENGINE)
DISASSEMBLY
1) For ease in servicing cylinder head, remove CMP sensor case,
intake manifold with throttle body and exhaust manifold from cyl-
inder head.
2) Remove rocker arms and washers by pulling its shaft out to
transmission side.
3) Using special tools (Valve lifter), compress valve springs and
then remove valve cotters (1) by using special tool (Forceps) as
shown.
Special Tool
(A): 09916-14510
(B): 09916-14910
(C): 09916-84511
4) Release special tool, and remove spring retainer and valve
spring.
5) Remove valve from combustion chamber side.
6) Remove valve stem oil seal (1) from valve guide, and then valve
spring seat (2).
NOTE:
Do not reuse oil seal once disassembled. Be sure to use
new oil seal when assembling.
7) Using special tool (Valve guide remover), drive valve guide out
from combustion chamber side to valve spring side.
Special Tool
(A): 09916-44910
NOTE:
Do not reuse valve guide once disassembled. Be sure to
use new valve guide (Oversize) when assembling.
8) Place disassembled parts except valve stem seal and valve
guide in order, so that they can be installed in their original posi-
tion.