Page 173 of 557
ENGINE GENERAL INFORMATION AND DIAGNOSIS (SFI FOR G13) 6-1-17
DTC
NO.DETECTING ITEMDETECTING CONDITION
(DTC will set when detecting:)MIL
P0705Transmission Range Sensor Circuit
Malfunction
P0720Output Speed Sensor Circuit Malfunction
P0751Shift Solenoid A
Performance or Stuck Off
Refer to Section 7B
P0753Shift Solenoid A Circuit
P0756Shift Solenoid B
Performance or Stuck Off
P0758Shift Solenoid B Circuit
P1620
(No.84)ECU code not registered
P1621
(No.83)NO ECU code transmitted from
Immobilizer Control Module
Refer to Section 8GP1622
(No.82)Fault in ECM
Refer to Section 8G
P1623
(No.81)ECU code not matched
Note:
With the generic scan tool, only star () marked data in the above table can not be read.
Page 176 of 557
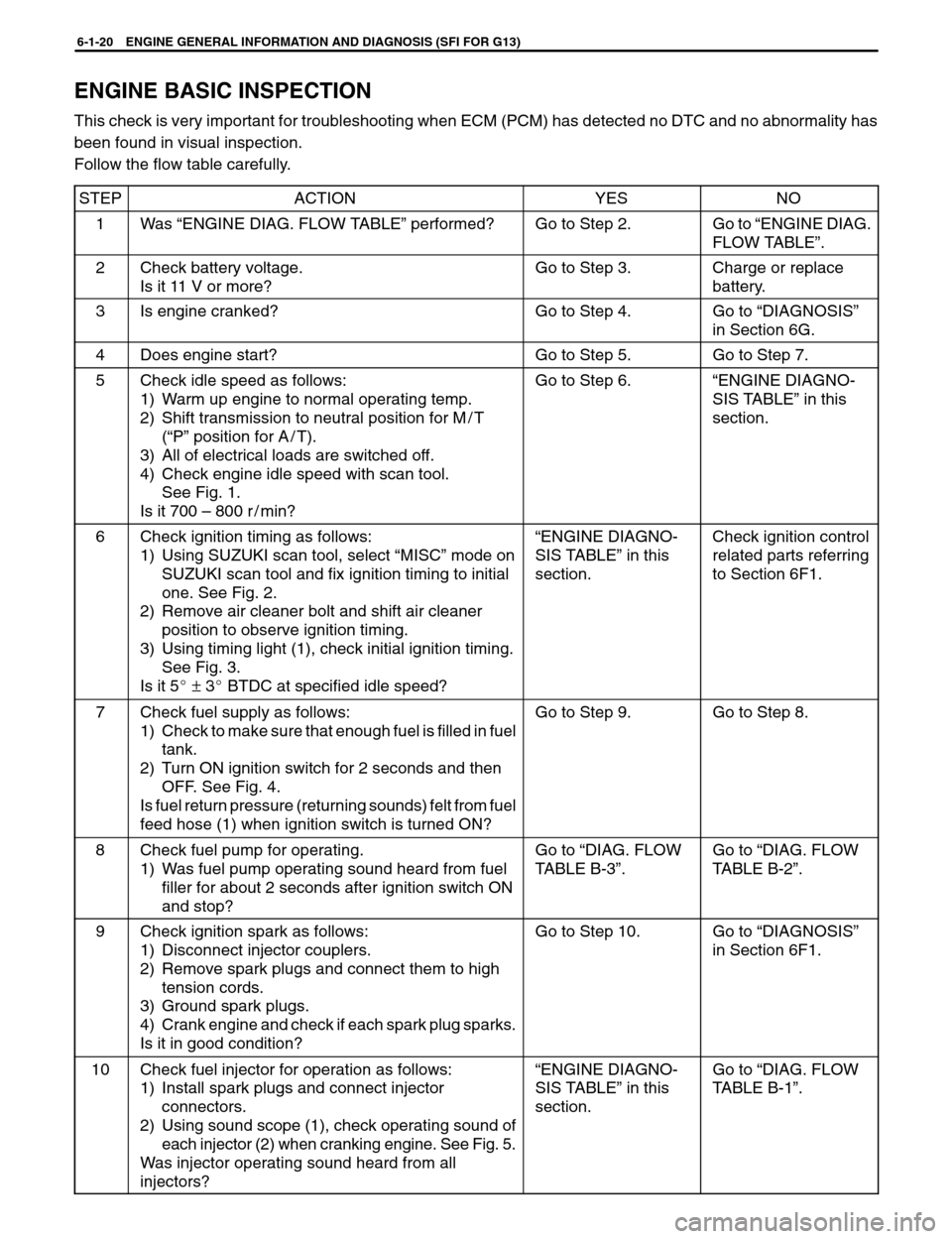
6-1-20 ENGINE GENERAL INFORMATION AND DIAGNOSIS (SFI FOR G13)
ENGINE BASIC INSPECTION
This check is very important for troubleshooting when ECM (PCM) has detected no DTC and no abnormality has
been found in visual inspection.
Follow the flow table carefully.
STEP
ACTIONYESNO
1Was “ENGINE DIAG. FLOW TABLE” performed?Go to Step 2.Go to “ENGINE DIAG.
FLOW TABLE”.
2Check battery voltage.
Is it 11 V or more?Go to Step 3.Charge or replace
battery.
3Is engine cranked?Go to Step 4.Go to “DIAGNOSIS”
in Section 6G.
4Does engine start?Go to Step 5.Go to Step 7.
5Check idle speed as follows:
1) Warm up engine to normal operating temp.
2) Shift transmission to neutral position for M / T
(“P” position for A / T).
3) All of electrical loads are switched off.
4) Check engine idle speed with scan tool.
See Fig. 1.
Is it 700 – 800 r / min?Go to Step 6.“ENGINE DIAGNO-
SIS TABLE” in this
section.
6Check ignition timing as follows:
1) Using SUZUKI scan tool, select “MISC” mode on
SUZUKI scan tool and fix ignition timing to initial
one. See Fig. 2.
2) Remove air cleaner bolt and shift air cleaner
position to observe ignition timing.
3) Using timing light (1), check initial ignition timing.
See Fig. 3.
Is it 5 ± 3 BTDC at specified idle speed?“ENGINE DIAGNO-
SIS TABLE” in this
section.Check ignition control
related parts referring
to Section 6F1.
7Check fuel supply as follows:
1) Check to make sure that enough fuel is filled in fuel
tank.
2) Turn ON ignition switch for 2 seconds and then
OFF. See Fig. 4.
Is fuel return pressure (returning sounds) felt from fuel
feed hose (1) when ignition switch is turned ON?Go to Step 9.Go to Step 8.
8Check fuel pump for operating.
1) Was fuel pump operating sound heard from fuel
filler for about 2 seconds after ignition switch ON
and stop?Go to “DIAG. FLOW
TABLE B-3”.Go to “DIAG. FLOW
TABLE B-2”.
9Check ignition spark as follows:
1) Disconnect injector couplers.
2) Remove spark plugs and connect them to high
tension cords.
3) Ground spark plugs.
4) Crank engine and check if each spark plug sparks.
Is it in good condition?Go to Step 10.Go to “DIAGNOSIS”
in Section 6F1.
10Check fuel injector for operation as follows:
1) Install spark plugs and connect injector
connectors.
2) Using sound scope (1), check operating sound of
each injector (2) when cranking engine. See Fig. 5.
Was injector operating sound heard from all
injectors?“ENGINE DIAGNO-
SIS TABLE” in this
section.Go to “DIAG. FLOW
TABLE B-1”.
Page 194 of 557
INFORMATION SENSORS
-1. MAP sensor
-2. TP sensor
-3. IAT sensor
-4. ECT sensor
-5. Heated oxygen sensor-1
5-1. Heated oxygen sensor-2
-6. VSS (A / T)
-7. Transmission range switch (A / T)
-8. Battery
-9. CMP sensor
-10. CKP sensor
-11. Fuel level sensor (gauge) (in fuel tank)
-12. PSP switch
-13. A / C control module (if equipped)
-14. VSS (speedometer) (M / T)OTHERS
A: ECM (PCM)
B: Main relay
C: EVAP canister
D: Data link connector CONTROL DEVICES
a: Fuel injector
b: EVAP canister purge valve
c: Fuel pump relay
d: EGR valve (step motor)
e: Malfunction indicator lamp
f: Ignition coil assembly
g: Radiator fan control relay
h: IAC valve
6-1-38 ENGINE GENERAL INFORMATION AND DIAGNOSIS (SFI FOR G13)
COMPONENT LOCATION
Page 246 of 557
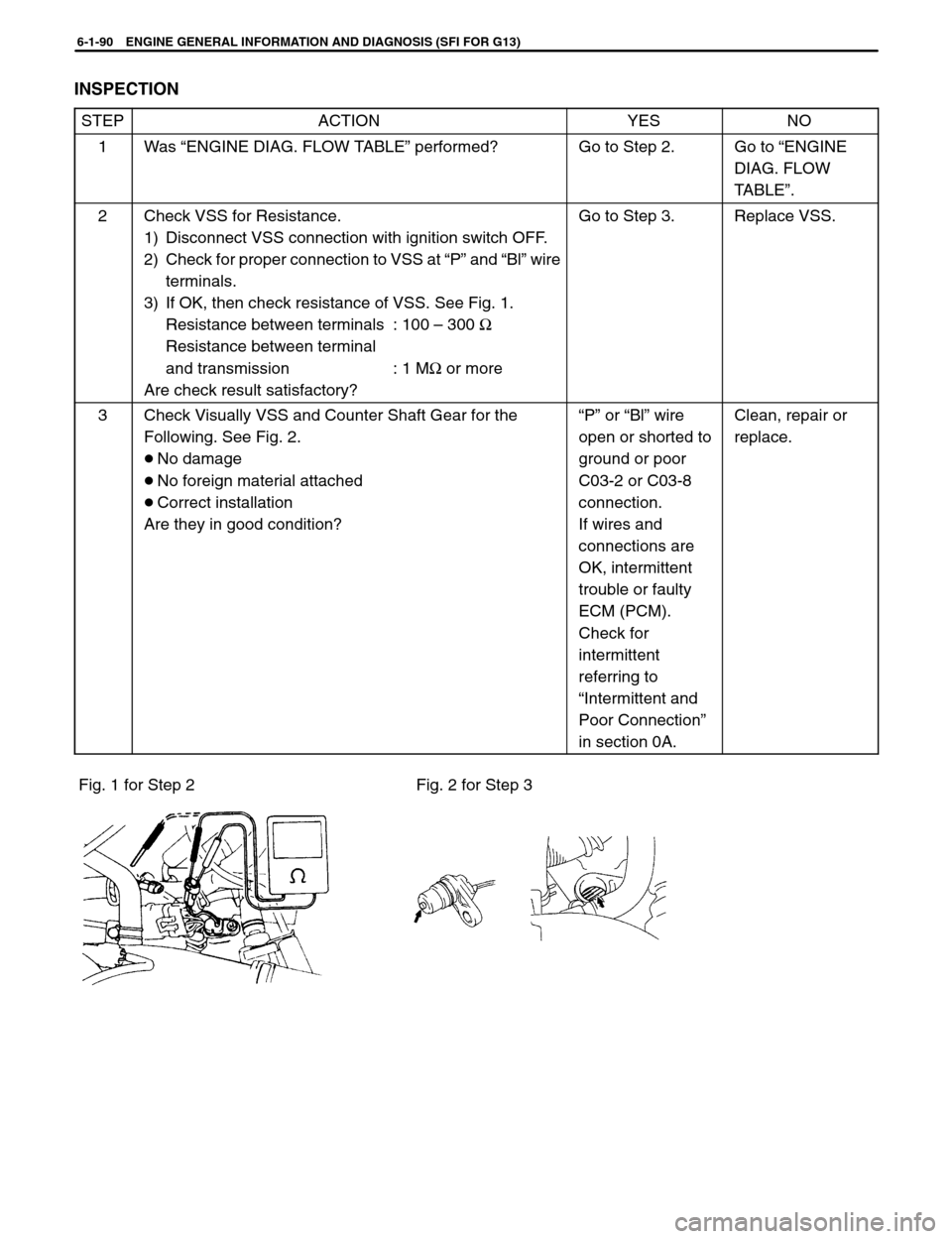
6-1-90 ENGINE GENERAL INFORMATION AND DIAGNOSIS (SFI FOR G13)
Fig. 1 for Step 2 Fig. 2 for Step 3
INSPECTION
STEPACTIONYESNO
1Was “ENGINE DIAG. FLOW TABLE” performed?Go to Step 2.Go to “ENGINE
DIAG. FLOW
TABLE”.
2Check VSS for Resistance.
1) Disconnect VSS connection with ignition switch OFF.
2) Check for proper connection to VSS at “P” and “Bl” wire
terminals.
3) If OK, then check resistance of VSS. See Fig. 1.
Resistance between terminals : 100 – 300 Ω
Resistance between terminal
and transmission : 1 MΩ or more
Are check result satisfactory?Go to Step 3.Replace VSS.
3Check Visually VSS and Counter Shaft Gear for the
Following. See Fig. 2.
No damage
No foreign material attached
Correct installation
Are they in good condition?“P” or “Bl” wire
open or shorted to
ground or poor
C03-2 or C03-8
connection.
If wires and
connections are
OK, intermittent
trouble or faulty
ECM (PCM).
Check for
intermittent
referring to
“Intermittent and
Poor Connection”
in section 0A.Clean, repair or
replace.
Page 252 of 557
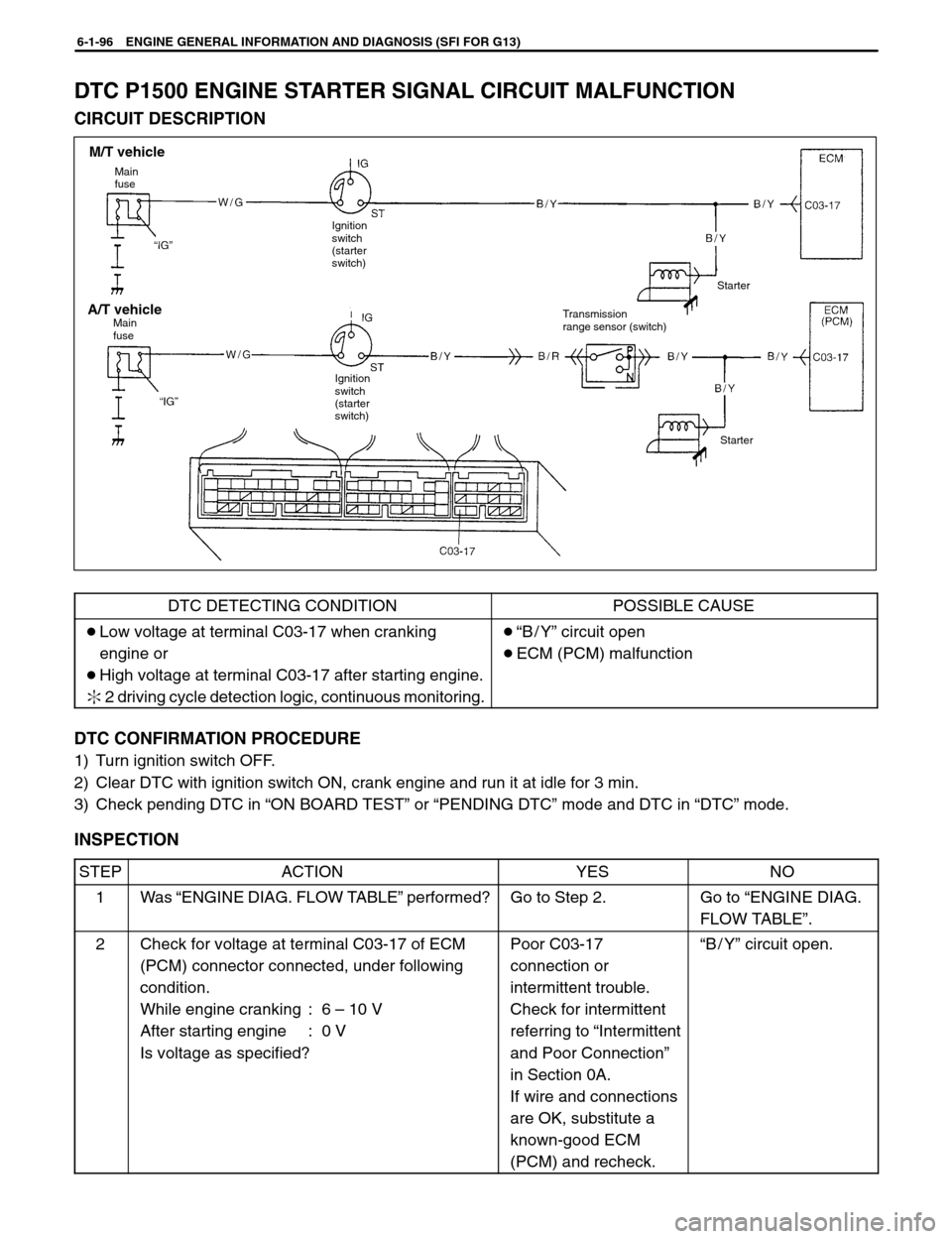
6-1-96 ENGINE GENERAL INFORMATION AND DIAGNOSIS (SFI FOR G13)
Main
fuse
M/T vehicle
A/T vehicle
Ignition
switch
(starter
switch)
Starter
Starter Transmission
range sensor (switch) Main
fuse
Ignition
switch
(starter
switch)
DTC P1500 ENGINE STARTER SIGNAL CIRCUIT MALFUNCTION
CIRCUIT DESCRIPTION
DTC DETECTING CONDITIONPOSSIBLE CAUSE
Low voltage at terminal C03-17 when cranking
engine or
High voltage at terminal C03-17 after starting engine.
2 driving cycle detection logic, continuous monitoring.“B/Y” circuit open
ECM (PCM) malfunction
DTC CONFIRMATION PROCEDURE
1) Turn ignition switch OFF.
2) Clear DTC with ignition switch ON, crank engine and run it at idle for 3 min.
3) Check pending DTC in “ON BOARD TEST” or “PENDING DTC” mode and DTC in “DTC” mode.
INSPECTION
STEPACTIONYESNO
1Was “ENGINE DIAG. FLOW TABLE” performed?Go to Step 2.Go to “ENGINE DIAG.
FLOW TABLE”.
2Check for voltage at terminal C03-17 of ECM
(PCM) connector connected, under following
condition.
While engine cranking : 6 – 10 V
After starting engine : 0 V
Is voltage as specified?Poor C03-17
connection or
intermittent trouble.
Check for intermittent
referring to “Intermittent
and Poor Connection”
in Section 0A.
If wire and connections
are OK, substitute a
known-good ECM
(PCM) and recheck.“B/Y” circuit open.
Page 288 of 557
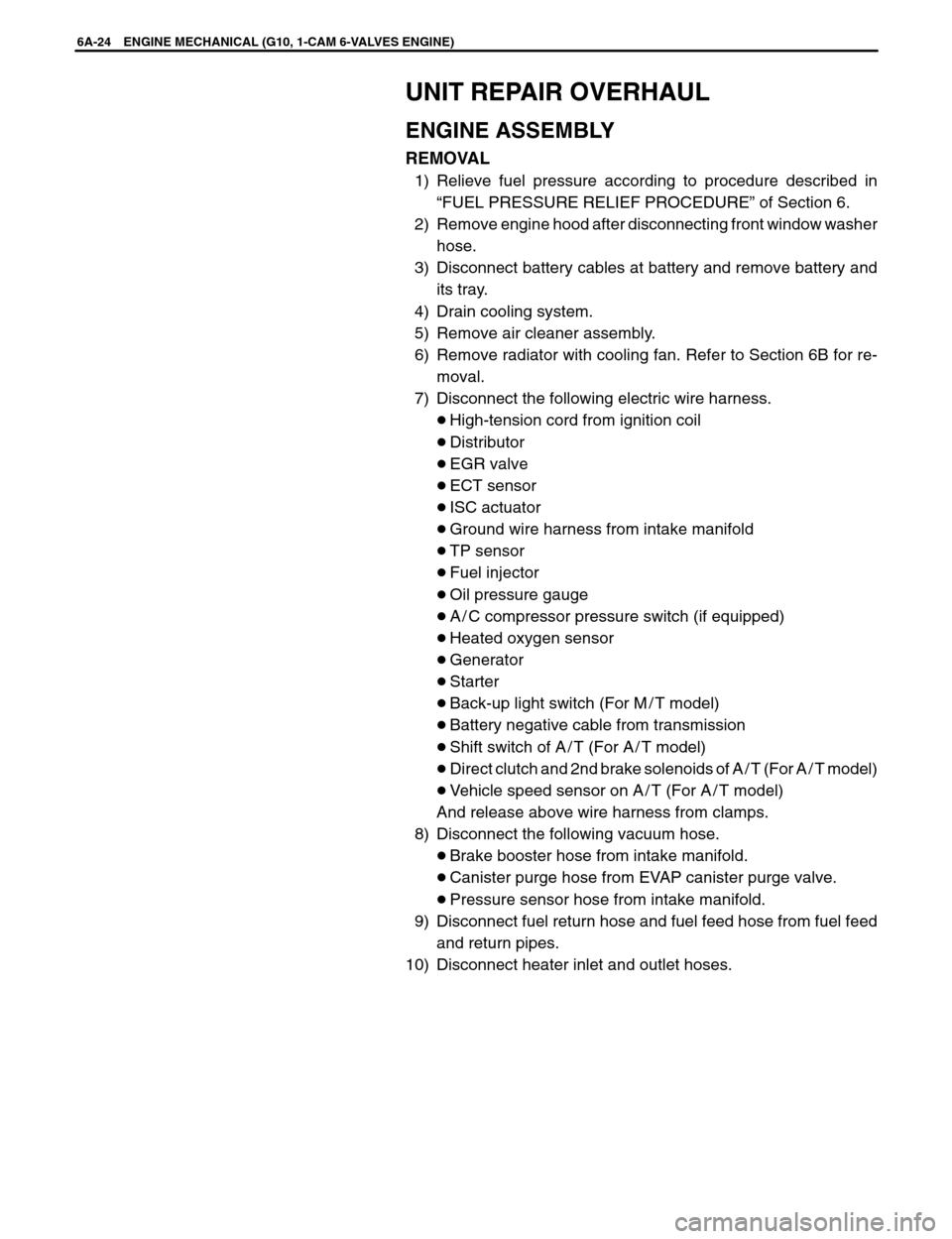
6A-24 ENGINE MECHANICAL (G10, 1-CAM 6-VALVES ENGINE)
UNIT REPAIR OVERHAUL
ENGINE ASSEMBLY
REMOVAL
1) Relieve fuel pressure according to procedure described in
“FUEL PRESSURE RELIEF PROCEDURE” of Section 6.
2) Remove engine hood after disconnecting front window washer
hose.
3) Disconnect battery cables at battery and remove battery and
its tray.
4) Drain cooling system.
5) Remove air cleaner assembly.
6) Remove radiator with cooling fan. Refer to Section 6B for re-
moval.
7) Disconnect the following electric wire harness.
High-tension cord from ignition coil
Distributor
EGR valve
ECT sensor
ISC actuator
Ground wire harness from intake manifold
TP sensor
Fuel injector
Oil pressure gauge
A / C compressor pressure switch (if equipped)
Heated oxygen sensor
Generator
Starter
Back-up light switch (For M / T model)
Battery negative cable from transmission
Shift switch of A / T (For A / T model)
Direct clutch and 2nd brake solenoids of A / T (For A / T model)
Vehicle speed sensor on A / T (For A / T model)
And release above wire harness from clamps.
8) Disconnect the following vacuum hose.
Brake booster hose from intake manifold.
Canister purge hose from EVAP canister purge valve.
Pressure sensor hose from intake manifold.
9) Disconnect fuel return hose and fuel feed hose from fuel feed
and return pipes.
10) Disconnect heater inlet and outlet hoses.
Page 289 of 557
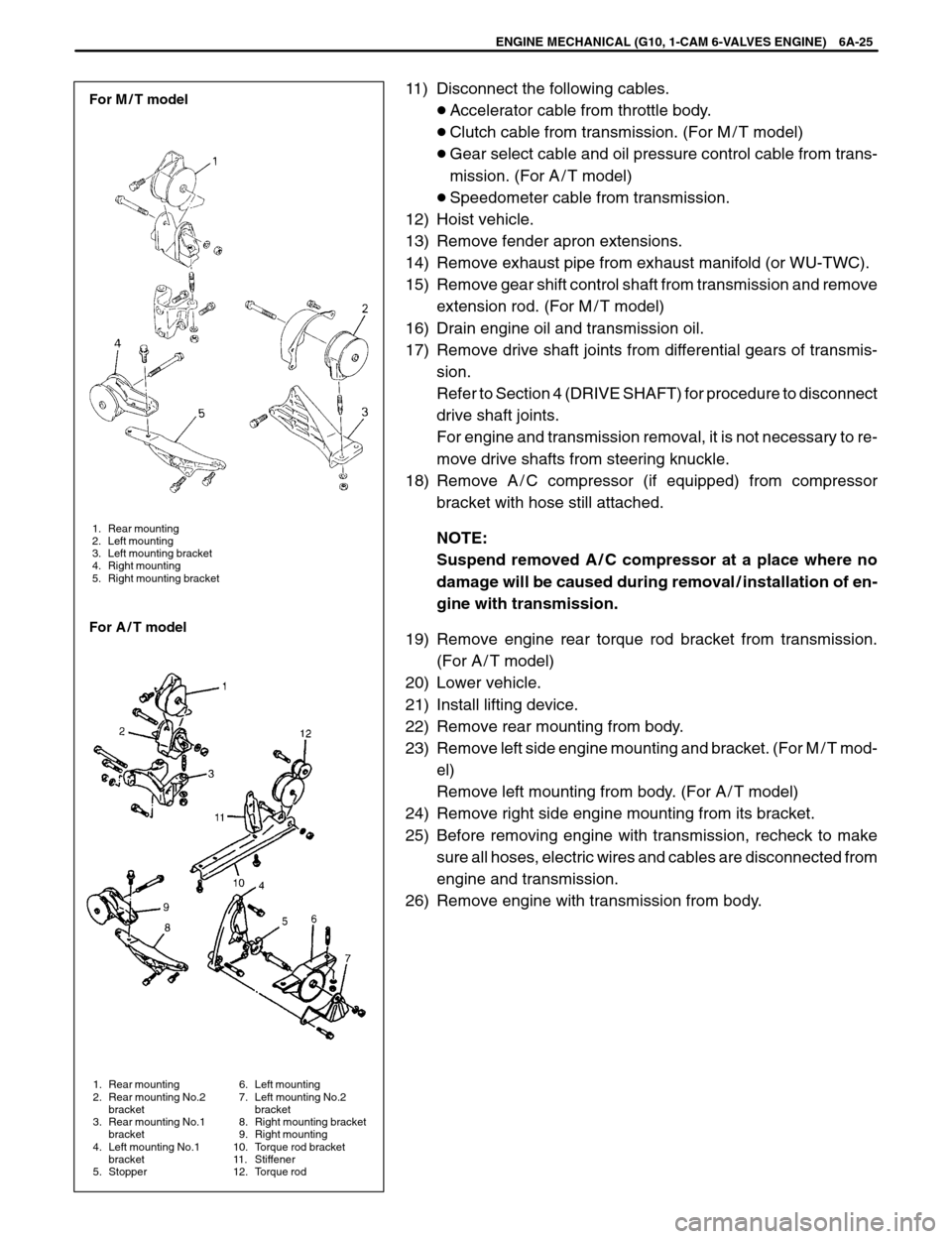
1. Rear mounting
2. Left mounting
3. Left mounting bracket
4. Right mounting
5. Right mounting bracket
For M / T model
For A / T model
1. Rear mounting
2. Rear mounting No.2
bracket
3. Rear mounting No.1
bracket
4. Left mounting No.1
bracket
5. Stopper6. Left mounting
7. Left mounting No.2
bracket
8. Right mounting bracket
9. Right mounting
10. Torque rod bracket
11. Stiffener
12. Torque rod
ENGINE MECHANICAL (G10, 1-CAM 6-VALVES ENGINE) 6A-25
11) Disconnect the following cables.
Accelerator cable from throttle body.
Clutch cable from transmission. (For M / T model)
Gear select cable and oil pressure control cable from trans-
mission. (For A / T model)
Speedometer cable from transmission.
12) Hoist vehicle.
13) Remove fender apron extensions.
14) Remove exhaust pipe from exhaust manifold (or WU-TWC).
15) Remove gear shift control shaft from transmission and remove
extension rod. (For M / T model)
16) Drain engine oil and transmission oil.
17) Remove drive shaft joints from differential gears of transmis-
sion.
Refer to Section 4 (DRIVE SHAFT) for procedure to disconnect
drive shaft joints.
For engine and transmission removal, it is not necessary to re-
move drive shafts from steering knuckle.
18) Remove A / C compressor (if equipped) from compressor
bracket with hose still attached.
NOTE:
Suspend removed A / C compressor at a place where no
damage will be caused during removal / installation of en-
gine with transmission.
19) Remove engine rear torque rod bracket from transmission.
(For A / T model)
20) Lower vehicle.
21) Install lifting device.
22) Remove rear mounting from body.
23) Remove left side engine mounting and bracket. (For M / T mod-
el)
Remove left mounting from body. (For A / T model)
24) Remove right side engine mounting from its bracket.
25) Before removing engine with transmission, recheck to make
sure all hoses, electric wires and cables are disconnected from
engine and transmission.
26) Remove engine with transmission from body.
Page 290 of 557
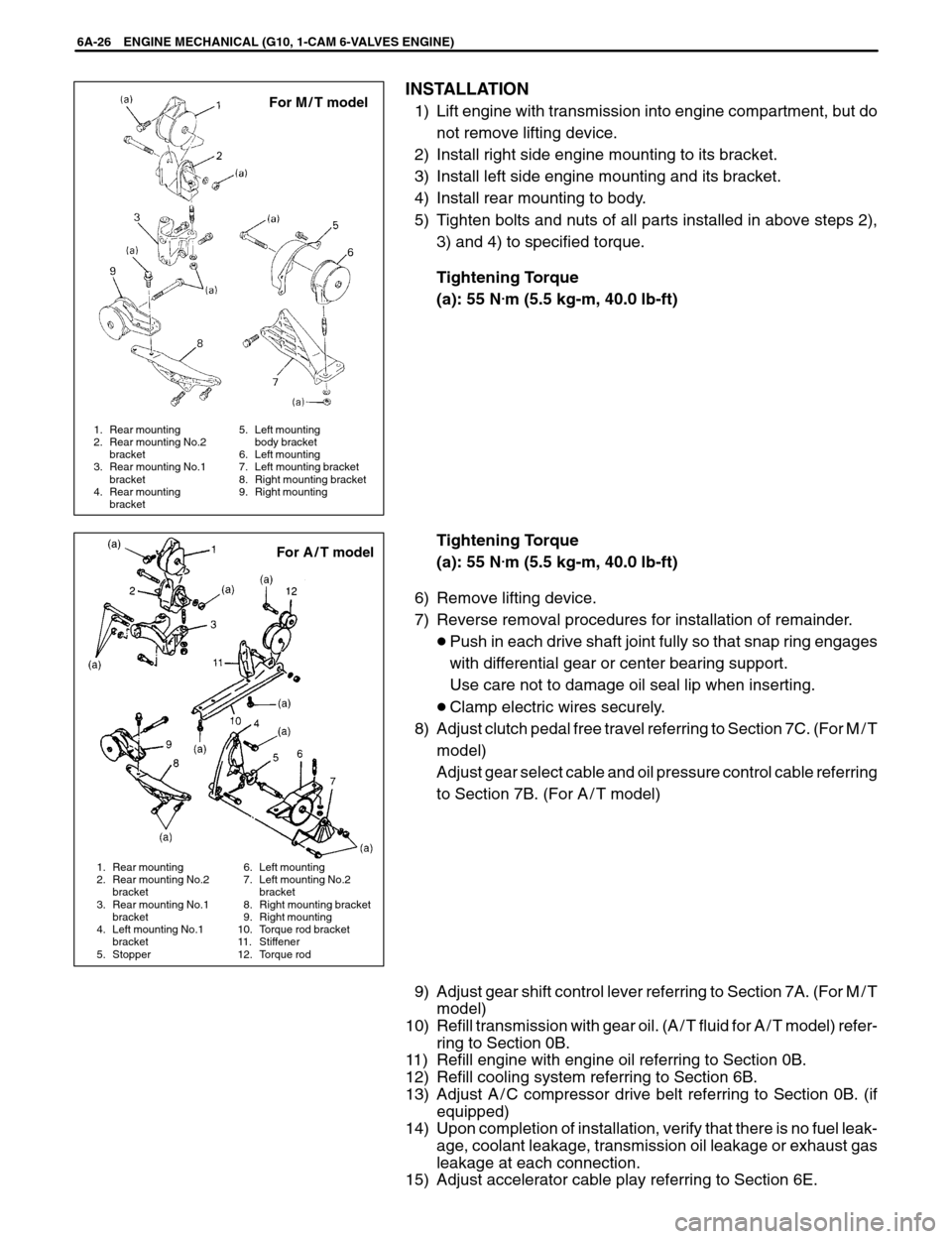
1. Rear mounting
2. Rear mounting No.2
bracket
3. Rear mounting No.1
bracket
4. Rear mounting
bracket5. Left mounting
body bracket
6. Left mounting
7. Left mounting bracket
8. Right mounting bracket
9. Right mounting
For M / T model
For A / T model
1. Rear mounting
2. Rear mounting No.2
bracket
3. Rear mounting No.1
bracket
4. Left mounting No.1
bracket
5. Stopper6. Left mounting
7. Left mounting No.2
bracket
8. Right mounting bracket
9. Right mounting
10. Torque rod bracket
11. Stiffener
12. Torque rod
6A-26 ENGINE MECHANICAL (G10, 1-CAM 6-VALVES ENGINE)
INSTALLATION
1) Lift engine with transmission into engine compartment, but do
not remove lifting device.
2) Install right side engine mounting to its bracket.
3) Install left side engine mounting and its bracket.
4) Install rear mounting to body.
5) Tighten bolts and nuts of all parts installed in above steps 2),
3) and 4) to specified torque.
Tightening Torque
(a): 55 N
.m (5.5 kg-m, 40.0 lb-ft)
Tightening Torque
(a): 55 N
.m (5.5 kg-m, 40.0 lb-ft)
6) Remove lifting device.
7) Reverse removal procedures for installation of remainder.
Push in each drive shaft joint fully so that snap ring engages
with differential gear or center bearing support.
Use care not to damage oil seal lip when inserting.
Clamp electric wires securely.
8) Adjust clutch pedal free travel referring to Section 7C. (For M / T
model)
Adjust gear select cable and oil pressure control cable referring
to Section 7B. (For A / T model)
9) Adjust gear shift control lever referring to Section 7A. (For M / T
model)
10) Refill transmission with gear oil. (A / T fluid for A / T model) refer-
ring to Section 0B.
11) Refill engine with engine oil referring to Section 0B.
12) Refill cooling system referring to Section 6B.
13) Adjust A / C compressor drive belt referring to Section 0B. (if
equipped)
14) Upon completion of installation, verify that there is no fuel leak-
age, coolant leakage, transmission oil leakage or exhaust gas
leakage at each connection.
15) Adjust accelerator cable play referring to Section 6E.