Page 216 of 557
6-1-60 ENGINE GENERAL INFORMATION AND DIAGNOSIS (SFI FOR G13)
To other sensor
Main
fuseIgnition
switch
Heater
To HO2S-1
heater
DTC P0136 HEATED OXYGEN SENSOR (HO2S) CIRCUIT MALFUNCTION
(SENSOR-2)
CIRCUIT DESCRIPTION
DTC DETECTING CONDITIONPOSSIBLE CAUSE
DTC will set when A or B condition is detected.
A. Max. output voltage of HO2S-2 is lower than specified value or
Min. output voltage is higher than specified value while vehicle
driving.
B. Engine is warmed up and HO2S-2 voltage is 4.5 V or more.
(circuit open)
2 driving cycle detection logic, monitoring once / 1 driving.Exhaust gas leakage
“G” or “R” circuit open or short
Heated oxygen sensor-2 malfunction
Fuel system malfunction
Page 217 of 557
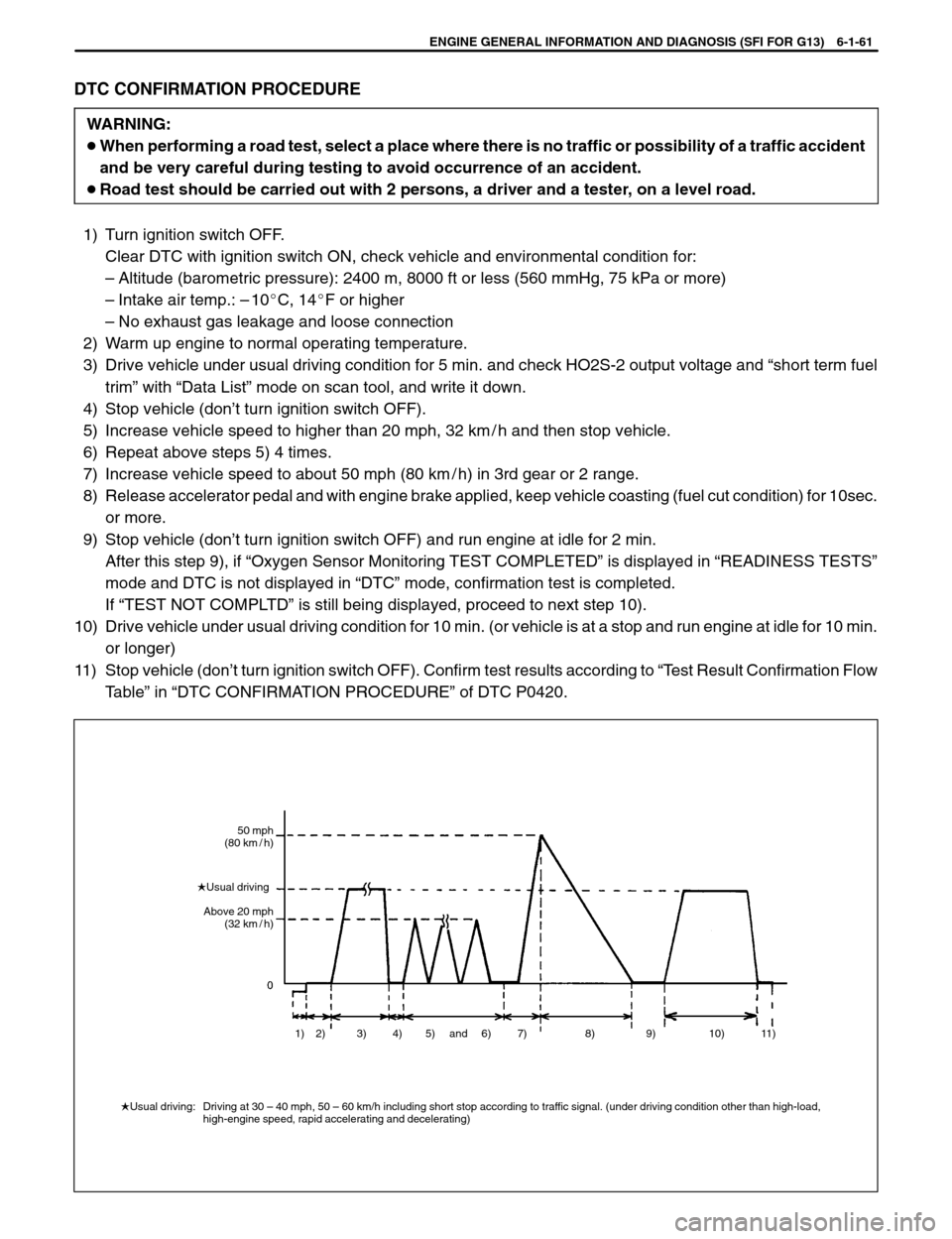
ENGINE GENERAL INFORMATION AND DIAGNOSIS (SFI FOR G13) 6-1-61
Usual driving: Driving at 30 – 40 mph, 50 – 60 km/h including short stop according to traffic signal. (under driving condition other than high-load,
high-engine speed, rapid accelerating and decelerating)1) 2) 3) 4) 5) 6) 7) 8) 9) 10) 11)and 50 mph
(80 km / h)
Above 20 mph
(32 km / h) Usual driving
DTC CONFIRMATION PROCEDURE
WARNING:
When performing a road test, select a place where there is no traffic or possibility of a traffic accident
and be very careful during testing to avoid occurrence of an accident.
Road test should be carried out with 2 persons, a driver and a tester, on a level road.
1) Turn ignition switch OFF.
Clear DTC with ignition switch ON, check vehicle and environmental condition for:
–Altitude (barometric pressure): 2400 m, 8000 ft or less (560 mmHg, 75 kPa or more)
–Intake air temp.: –10C, 14F or higher
–No exhaust gas leakage and loose connection
2) Warm up engine to normal operating temperature.
3) Drive vehicle under usual driving condition for 5 min. and check HO2S-2 output voltage and “short term fuel
trim” with “Data List” mode on scan tool, and write it down.
4) Stop vehicle (don’t turn ignition switch OFF).
5) Increase vehicle speed to higher than 20 mph, 32 km / h and then stop vehicle.
6) Repeat above steps 5) 4 times.
7) Increase vehicle speed to about 50 mph (80 km / h) in 3rd gear or 2 range.
8) Release accelerator pedal and with engine brake applied, keep vehicle coasting (fuel cut condition) for 10sec.
or more.
9) Stop vehicle (don’t turn ignition switch OFF) and run engine at idle for 2 min.
After this step 9), if “Oxygen Sensor Monitoring TEST COMPLETED” is displayed in “READINESS TESTS”
mode and DTC is not displayed in “DTC” mode, confirmation test is completed.
If “TEST NOT COMPLTD” is still being displayed, proceed to next step 10).
10) Drive vehicle under usual driving condition for 10 min. (or vehicle is at a stop and run engine at idle for 10 min.
or longer)
11) Stop vehicle (don’t turn ignition switch OFF). Confirm test results according to “Test Result Confirmation Flow
Table” in “DTC CONFIRMATION PROCEDURE” of DTC P0420.
Page 219 of 557
ENGINE GENERAL INFORMATION AND DIAGNOSIS (SFI FOR G13) 6-1-63
To other sensor
Main
fuseIgnition
switch
Heater
To HO2S-1
heater
DTC P0141 HEATED OXYGEN SENSOR (HO2S) HEATER CIRCUIT
MALFUNCTION (SENSOR-2)
CIRCUIT DESCRIPTION
DTC DETECTING CONDITIONPOSSIBLE CAUSE
DTC will set when A or B condition it met.
A. Low voltage at terminal C02-4 for specified time after engine
start or while engine running at high load.
B. High voltage at terminal C02-4 while engine running under other
than above condition.
2 driving cycle detection logic, continuous monitoring.HO2S-2 heater circuit open or shorted
to ground
ECM (PCM) malfunction
DTC CONFIRMATION PROCEDURE
1) Turn ignition switch OFF once and then ON.
2) Clear DTC, start engine and warm up engine to normal operating temperature.
3) Keep it at 2000 r / min for 2 min.
4) Check pending DTC in “ON BOARD TEST” or “PENDING DTC” mode and DTC in “DTC” mode.
Page 221 of 557
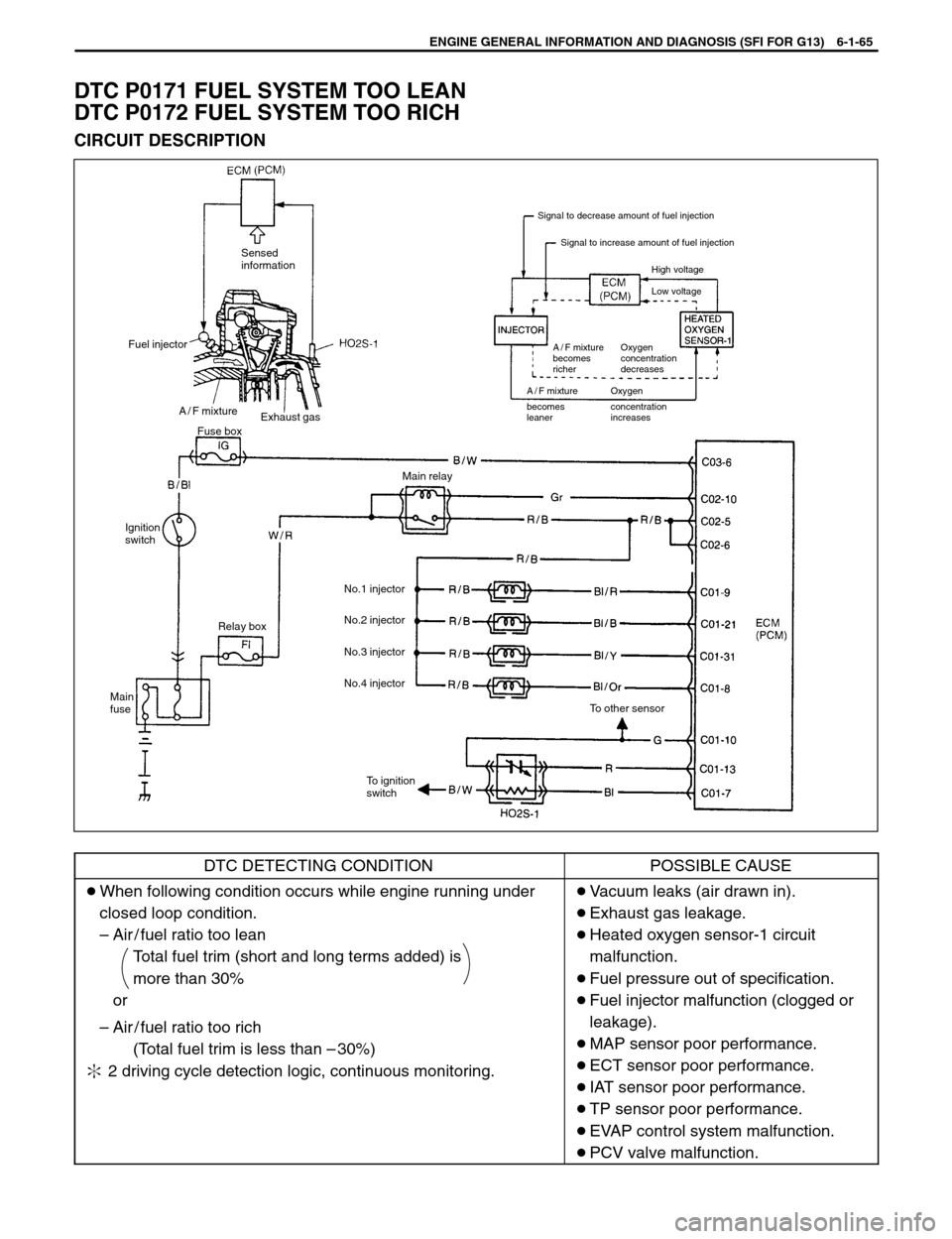
ENGINE GENERAL INFORMATION AND DIAGNOSIS (SFI FOR G13) 6-1-65
Ignition
switch
Main
fuseMain relay
To ignition
switchTo other sensor Relay boxNo.1 injector
No.2 injector
No.3 injector
No.4 injector Fuse box
Signal to decrease amount of fuel injection
Signal to increase amount of fuel injection
High voltage
Low voltage
A / F mixture
becomes
richerOxygen
concentration
decreases
A / F mixture Oxygen
Fuel injectorSensed
information
A / F mixture
Exhaust gas
becomes
leanerconcentration
increases
DTC P0171 FUEL SYSTEM TOO LEAN
DTC P0172 FUEL SYSTEM TOO RICH
CIRCUIT DESCRIPTION
DTC DETECTING CONDITIONPOSSIBLE CAUSE
When following condition occurs while engine running under
closed loop condition.
–Air / fuel ratio too lean
Total fuel trim (short and long terms added) is
more than 30%
or
–Air / fuel ratio too rich
(Total fuel trim is less than –30%)
2 driving cycle detection logic, continuous monitoring.Vacuum leaks (air drawn in).
Exhaust gas leakage.
Heated oxygen sensor-1 circuit
malfunction.
Fuel pressure out of specification.
Fuel injector malfunction (clogged or
leakage).
MAP sensor poor performance.
ECT sensor poor performance.
IAT sensor poor performance.
TP sensor poor performance.
EVAP control system malfunction.
PCV valve malfunction.
Page 237 of 557
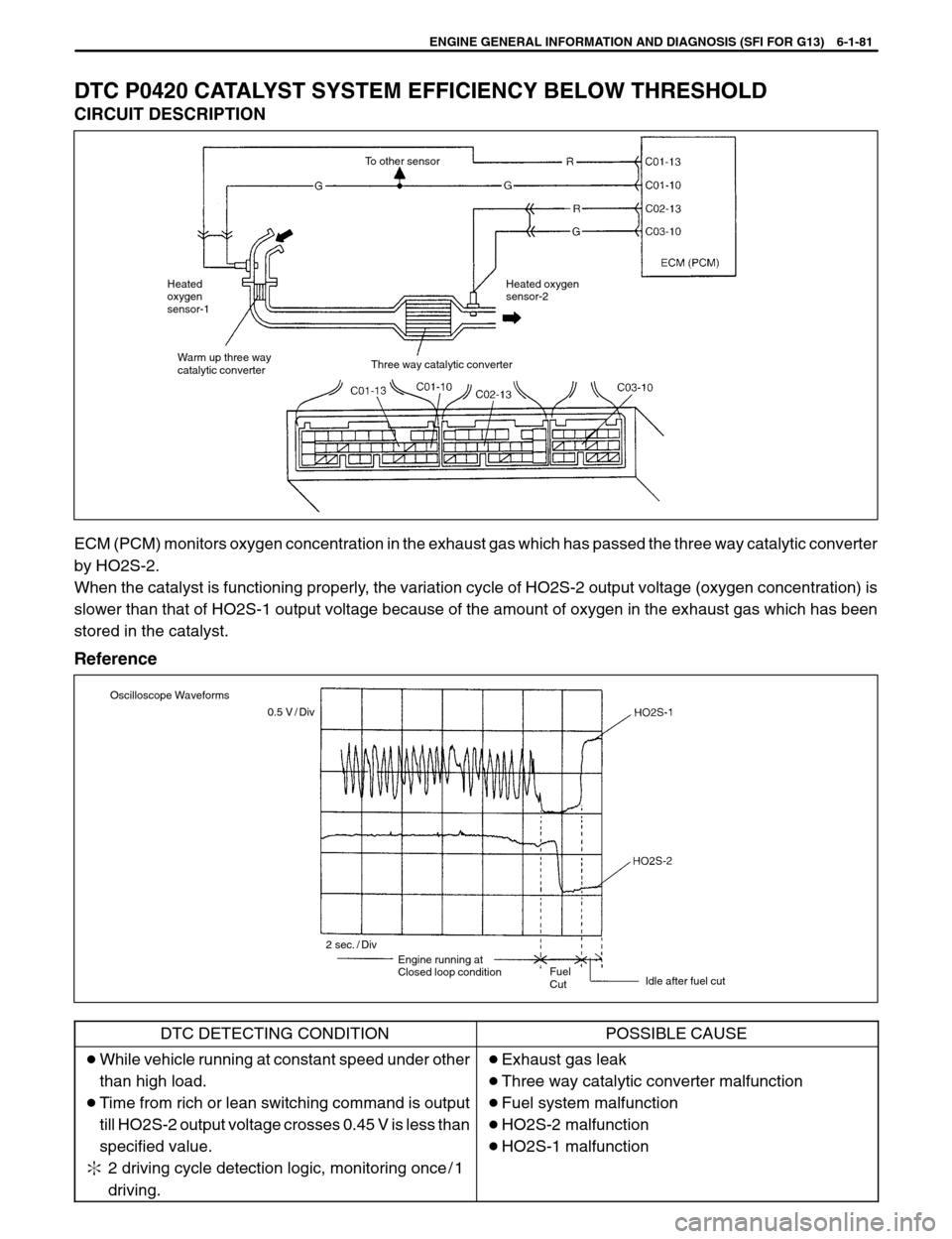
ENGINE GENERAL INFORMATION AND DIAGNOSIS (SFI FOR G13) 6-1-81
Oscilloscope WaveformsHeated
oxygen
sensor-1To other sensor
Heated oxygen
sensor-2
Warm up three way
catalytic converterThree way catalytic converter
Engine running at
Closed loop conditionFuel
CutIdle after fuel cut 0.5 V / Div
2 sec. / Div
DTC P0420 CATALYST SYSTEM EFFICIENCY BELOW THRESHOLD
CIRCUIT DESCRIPTION
ECM (PCM) monitors oxygen concentration in the exhaust gas which has passed the three way catalytic converter
by HO2S-2.
When the catalyst is functioning properly, the variation cycle of HO2S-2 output voltage (oxygen concentration) is
slower than that of HO2S-1 output voltage because of the amount of oxygen in the exhaust gas which has been
stored in the catalyst.
Reference
DTC DETECTING CONDITIONPOSSIBLE CAUSE
While vehicle running at constant speed under other
than high load.
Time from rich or lean switching command is output
till HO2S-2 output voltage crosses 0.45 V is less than
specified value.
2 driving cycle detection logic, monitoring once / 1
driving.Exhaust gas leak
Three way catalytic converter malfunction
Fuel system malfunction
HO2S-2 malfunction
HO2S-1 malfunction
Page 267 of 557
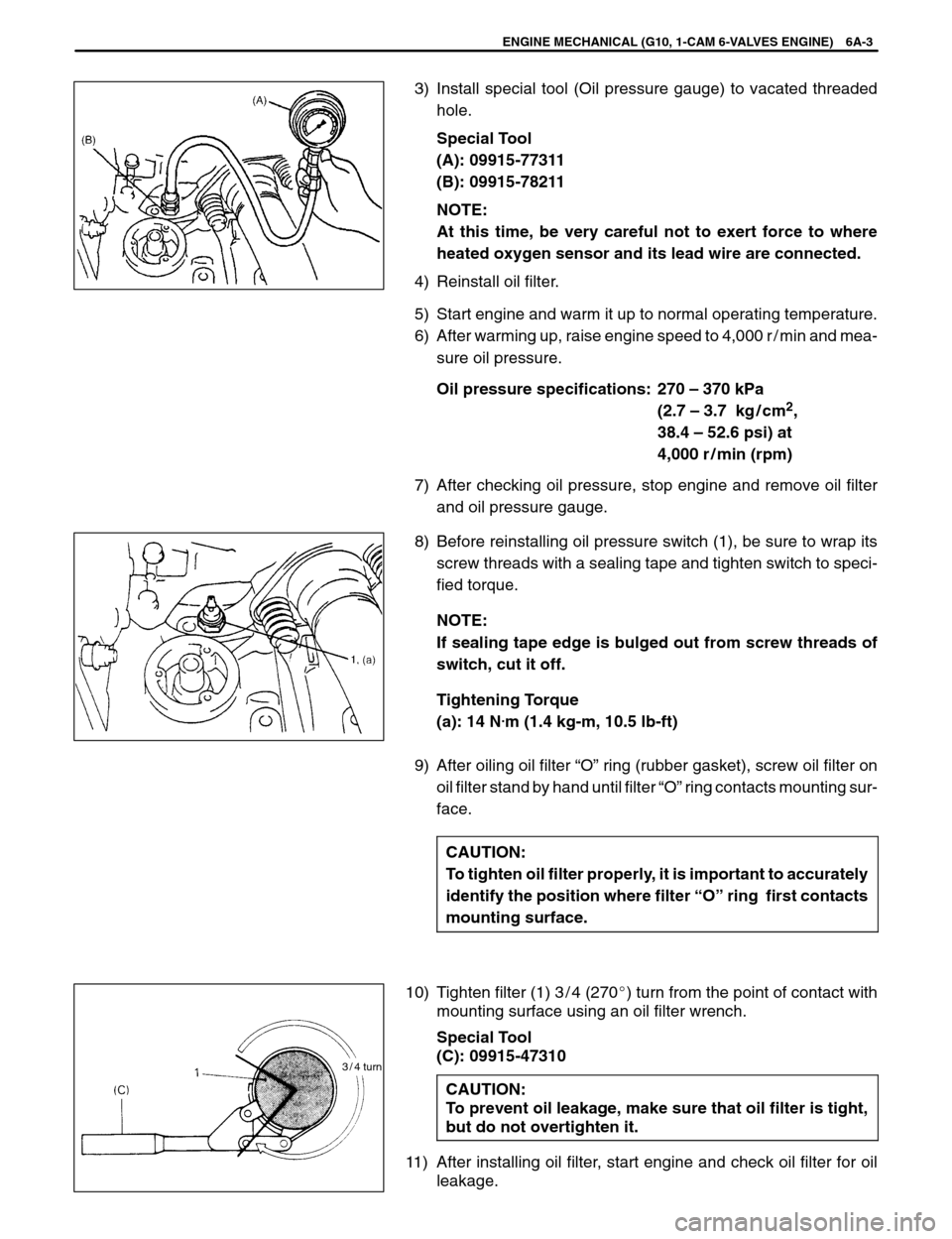
3 / 4 turn
ENGINE MECHANICAL (G10, 1-CAM 6-VALVES ENGINE) 6A-3
3) Install special tool (Oil pressure gauge) to vacated threaded
hole.
Special Tool
(A): 09915-77311
(B): 09915-78211
NOTE:
At this time, be very careful not to exert force to where
heated oxygen sensor and its lead wire are connected.
4) Reinstall oil filter.
5) Start engine and warm it up to normal operating temperature.
6) After warming up, raise engine speed to 4,000 r / min and mea-
sure oil pressure.
Oil pressure specifications: 270 – 370 kPa
(2.7 – 3.7 kg / cm
2,
38.4 – 52.6 psi) at
4,000 r / min (rpm)
7) After checking oil pressure, stop engine and remove oil filter
and oil pressure gauge.
8) Before reinstalling oil pressure switch (1), be sure to wrap its
screw threads with a sealing tape and tighten switch to speci-
fied torque.
NOTE:
If sealing tape edge is bulged out from screw threads of
switch, cut it off.
Tightening Torque
(a): 14 N
.m (1.4 kg-m, 10.5 lb-ft)
9) After oiling oil filter “O” ring (rubber gasket), screw oil filter on
oil filter stand by hand until filter “O” ring contacts mounting sur-
face.
CAUTION:
To tighten oil filter properly, it is important to accurately
identify the position where filter “O” ring first contacts
mounting surface.
10) Tighten filter (1) 3 / 4 (270) turn from the point of contact with
mounting surface using an oil filter wrench.
Special Tool
(C): 09915-47310
CAUTION:
To prevent oil leakage, make sure that oil filter is tight,
but do not overtighten it.
11) After installing oil filter, start engine and check oil filter for oil
leakage.
Page 272 of 557
1. Exhaust manifold
2. Gasket
3. Cover
4. Heated oxygen sensor
5. Pipe seal
6. Exhaust pipe
7. WU-TWC (if equipped)
8. Exhaust pipe bolt : Tightening Torque
: Do not reuse
6A-8 ENGINE MECHANICAL (G10, 1-CAM 6-VALVES ENGINE)
EXHAUST MANIFOLD
WARNING:
To avoid danger of being burned, do not service exhaust
system while it is still hot.
Service should be performed after system cools down.
REMOVAL
1) Disconnect negative cable at battery.
2) Disconnect heated oxygen sensor coupler.
Release its wire from clamps.
3) Disconnect exhaust pipe (1) from exhaust manifold (or WU-
TWC (2)).
4) Remove WU-TWC stiffener (3). (if equipped)
5) Remove exhaust manifold cover (2). (for vehicle with WU-TWC)
6) Remove exhaust manifold (1) with WU-TWC (if equipped) and
its gasket from cylinder head.
Page 273 of 557
2. WU-TWC
ENGINE MECHANICAL (G10, 1-CAM 6-VALVES ENGINE) 6A-9
INSTALLATION
1) Install manifold gasket to cylinder head.
Before installing gasket, check it for deterioration or damage,
and replace as necessary.
2) Install exhaust manifold (1).
Tighten manifold bolts and nuts to specified torque.
Tightening Torque
(a): 23 N
.m (2.3 kg-m, 17.0 lb-ft)
3) Install exhaust manifold cover (2).
4) Install pipe seal, and then connect exhaust pipe (1).
Before installing pipe seal, check it for deterioration or damage,
and replace as necessary.
Tighten pipe bolts to specified torque.
Tightening Torque
(c): 43 N
.m (4.3 kg-m, 31.5 lb-ft)
5) Install WU-TWC stiffener (3). (if equipped)
6) Connect heated oxygen sensor coupler.
7) Clamp its wire securely.
8) Connect negative cable at battery.
9) Check exhaust system for exhaust gas leakage.