Page 325 of 557
6A1-30 ENGINE MECHANICAL (G13B, 1-CAM 16-VALVES ENGINE)
NOTE:
When installing oil seal (1), press-fit it till its end face is flush
with oil pump case (2) end face.
Check outer and inner rotors, rotor plate, and oil pump case for
excessive wear or damage.
MEASUREMENT
Radial clearance
Check radial clearance between outer rotor (1) and case, using
thickness gauge.
If clearance exceeds its limit, replace outer rotor or case.
Limit on radial clearance between outer rotor and case:
0.200 mm (0.079 in.)
Side clearance
Using straight edge and thickness gauge, measure side clear-
ance.
Limit on side clearance: 0.10 mm (0.0039 in.)
ASSEMBLY
1) Wash, clean and then dry all disassembled parts.
2) Apply thin coat of engine oil to inner (2) and outer rotors (1), oil
seal lip portion, and inside surfaces of oil pump case and plate.
3) Install outer and inner rotors to pump case.
Page 326 of 557
(a)
1. Oil pump
1. No. 1 bolts (short)
2. No. 2 bolts (long)
ENGINE MECHANICAL (G13B, 1-CAM 16-VALVES ENGINE) 6A1-31
4) Install rotor plate. Tighten 5 screw securely.
After installing plate, check to be sure that gears turn smoothly
by hand.
Tightening Torque
(a): 11 N
.m (1.1 kg-m, 8.0 lb-ft)
5) Apply engine oil to guide seal (3) and install guide seal and guide
(2).
INSTALLATION
1) Install two oil pump pins and oil pump gasket to cylinder block.
Use a new gasket.
2) To prevent oil seal lip from being damaged or upturned when
installing oil pump to crankshaft, fit special tool (Oil seal guide)
to crankshaft, and apply engine oil to special tool.
Special Tool
(A): 09926-18210
3) Install oil pump to cylinder block.
As there are 2 types of oil pump bolts, refer to figure for their cor-
rect use and tighten them to specified torque.
Tightening Torque
(a): 11 N
.m (1.1 kg-m, 8.0 lb-ft)
4) Install rubber seal between oil pump and water pump.
Page 327 of 557
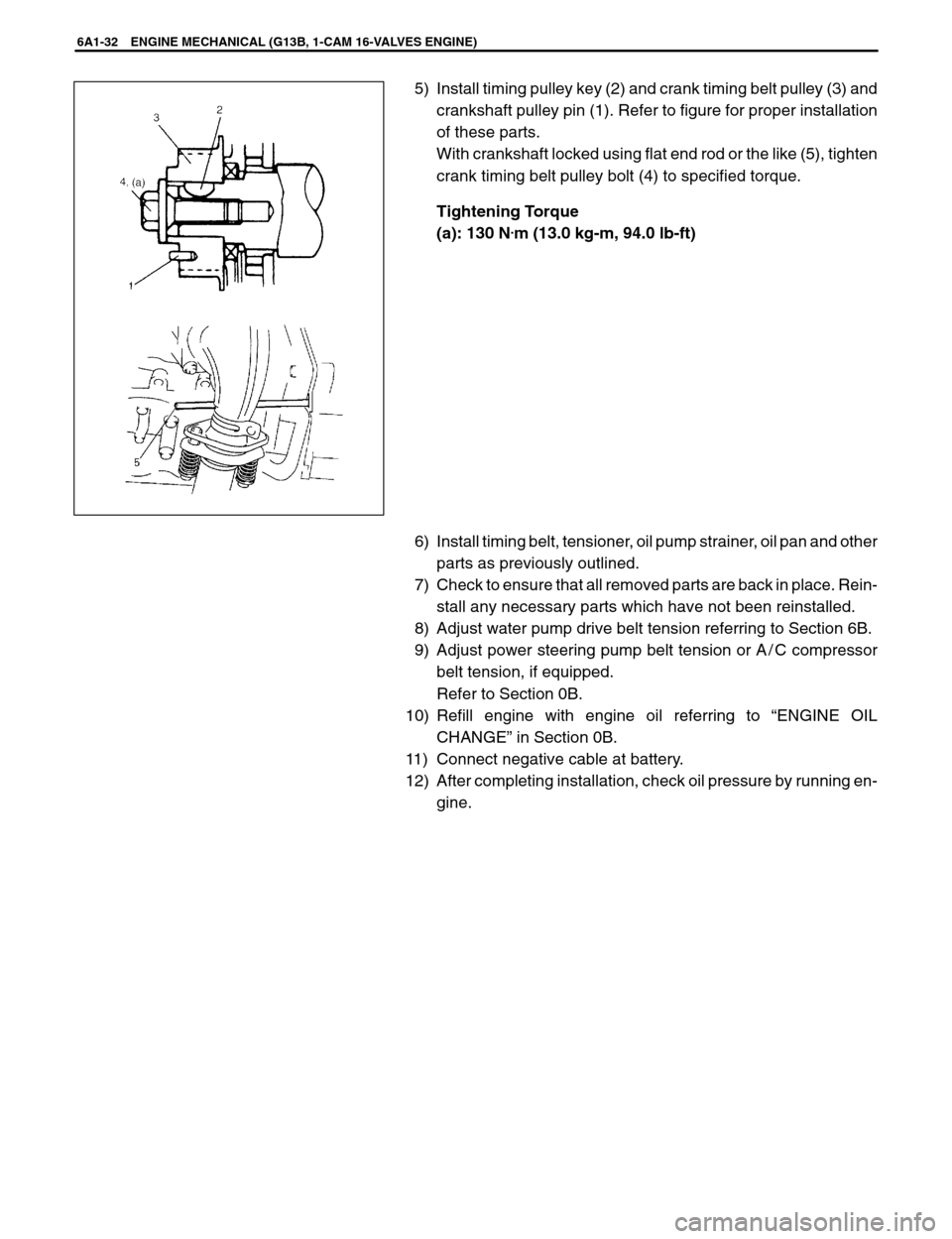
6A1-32 ENGINE MECHANICAL (G13B, 1-CAM 16-VALVES ENGINE)
5) Install timing pulley key (2) and crank timing belt pulley (3) and
crankshaft pulley pin (1). Refer to figure for proper installation
of these parts.
With crankshaft locked using flat end rod or the like (5), tighten
crank timing belt pulley bolt (4) to specified torque.
Tightening Torque
(a): 130 N
.m (13.0 kg-m, 94.0 lb-ft)
6) Install timing belt, tensioner, oil pump strainer, oil pan and other
parts as previously outlined.
7) Check to ensure that all removed parts are back in place. Rein-
stall any necessary parts which have not been reinstalled.
8) Adjust water pump drive belt tension referring to Section 6B.
9) Adjust power steering pump belt tension or A / C compressor
belt tension, if equipped.
Refer to Section 0B.
10) Refill engine with engine oil referring to “ENGINE OIL
CHANGE” in Section 0B.
11) Connect negative cable at battery.
12) After completing installation, check oil pressure by running en-
gine.
Page 328 of 557
1. Camshaft
2. Camshaft oil seal
3. Rocker arm shaft
4. O-ring
5. Rocker shaft bolt
6. Rocker arm (IN)
7. Rocker arm No.1 (EX)
8. Rocker arm No.2 (EX)
9. Valve adjusting screw
10. Valve adjusting screw
11. Clip
12. Lock nut
13. Rocker arm spring
: Tightening Torque : Do not reuse
: Apply engine oil to sliding
: surfaces of each part.
ENGINE MECHANICAL (G13B, 1-CAM 16-VALVES ENGINE) 6A1-33
ROCKER ARMS, ROCKER ARM SHAFT AND CAMSHAFT
REMOVAL
1) Disconnect negative cable at battery.
2) Remove timing belt as previously outlined and remove camshaft
timing belt pulley (1) by using special tool.
Special Tool
(A): 09917-68221
3) Remove cylinder head cover as previously outlined.
Page 329 of 557
1. Oil plug
6A1-34 ENGINE MECHANICAL (G13B, 1-CAM 16-VALVES ENGINE)
4) Disconnect CMP sensor coupler from CMP sensor.
5) Remove CMP sensor case (1) from cylinder head.
Place a container or rag under CMP sensor case, for a small
amount of oil flows out during removal of case.
6) After loosening all valve adjusting screw lock nuts (2), turn ad-
justing screws (1) back all the way to allow all rocker arms (3) to
move freely.
7) Remove camshaft housing and camshaft.
NOTE:
To remove camshaft housing bolts, loosen them in such or-
der as indicated in figure, a little at a time.
8) Remove timing belt inside cover (2).
9) Remove intake rocker arm (1) with clip (2) from rocker arm shaft
(3).
NOTE:
Do not bend clip when removing intake rocker arm.
Page 330 of 557
EX IN
2. Rocker arm shaft
ENGINE MECHANICAL (G13B, 1-CAM 16-VALVES ENGINE) 6A1-35
10) Remove rocker arm shaft bolts (1).
11) Remove exhaust rocker arms (1) and rocker arm spring (2) by
pulling out rocker arm shaft to battery side after removing bat-
tery.
INSPECTION
Adjusting Screw and Rocker Arm
If tip of adjusting screw (1) is badly worn, replace it.
Rocker arm (2) must be replaced if its cam-riding face (3) is badly
worn.
Rocker Arm Shaft Runout
Using “V” blocks and dial gauge, check runout. If runout exceeds
its limit, replace rocker arm shaft.
Runout limit: 0.10 mm (0.004 in.)
Page 331 of 557

6A1-36 ENGINE MECHANICAL (G13B, 1-CAM 16-VALVES ENGINE)
Rocker Arm-to-Rocker Arm Shaft Clearance
Using a micrometer and a bore gauge, measure rocker shaft dia.
and rocker arm l.D.
Difference between two readings is arm-to-shaft clearance on
which a limit is specified.
If limit is exceeded, replace shaft or arm, or both.
Item
StandardLimit
Rocker arm l.D.15.996 – 16.014 mm
(0.629 – 0.630 in.)———
Rocker arm shaft dia.15.969 – 15.984 mm
(0.6287 – 0.6293 in.)———
Arm-to-shaft clearance0.012 – 0.045 mm
(0.0005 – 0.0018 in.)0.09 mm
(0.0035 in.)
Cam Wear
Using a micrometer, measured height of cam. If measured height
is below limit, replace camshaft.
Cam height
StandardLimit
Intake cam36.184 – 36.344 mm
(1.4246 – 1.4309 in.)36.084 mm
(1.4206 in.)
Exhaust cam35.900 – 36.060 mm
(1.4134 – 1.4197 in.)35.800 mm
(1.4094 in.)
Camshaft Runout
Hold camshaft between two “V” blocks, and measure runout by us-
ing a dial gauge.
If runout exceeds the limit, replace camshaft.
Runout limit: 0.10 mm (0.0039 in.)
Camshaft Journal Wear
Check camshaft journals and camshaft housings for pitting,
scratches, wear or damage.
If any malcondition is found, replace camshaft or cylinder head with
housing. Never replace cylinder head without replacing housing.
Page 332 of 557
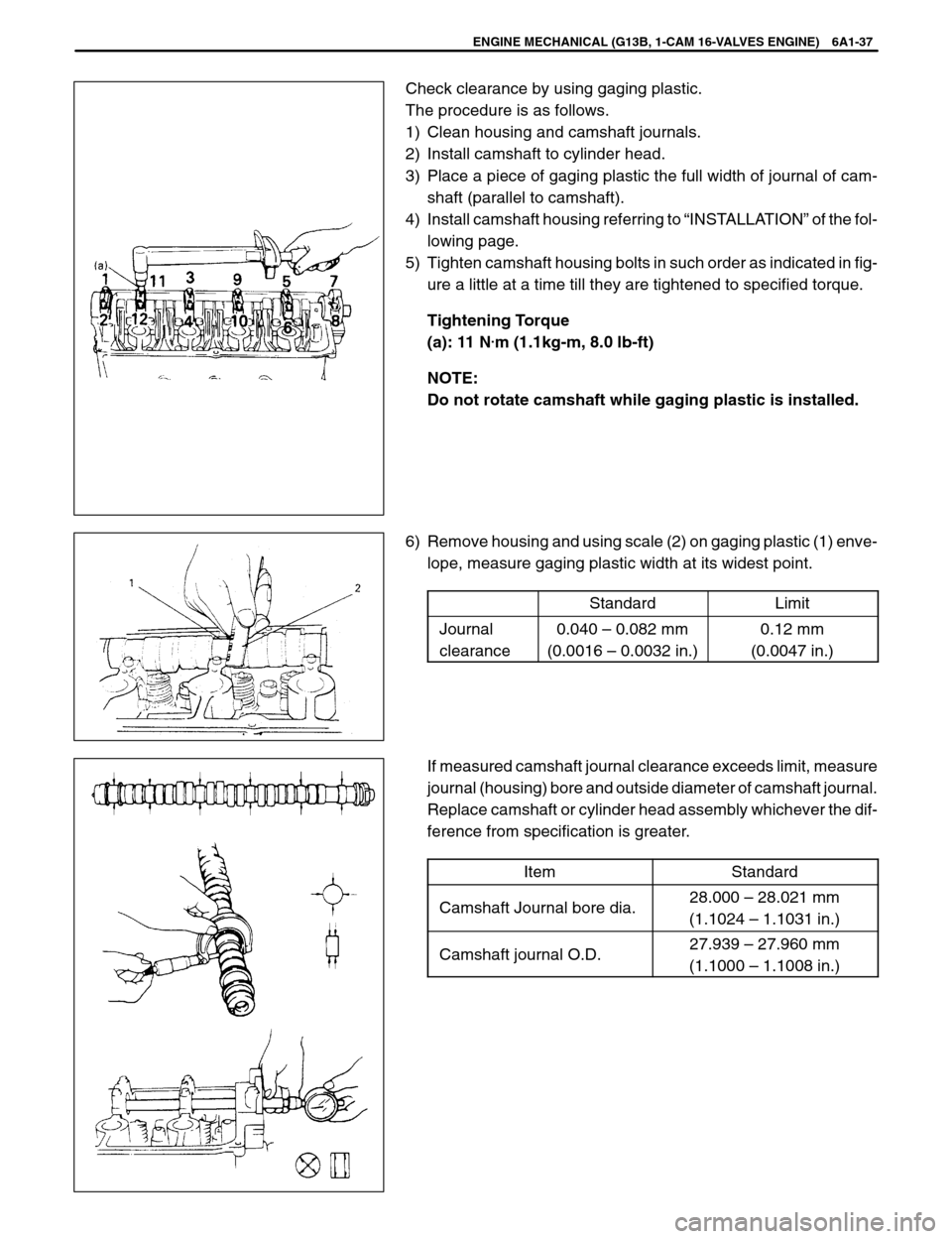
ENGINE MECHANICAL (G13B, 1-CAM 16-VALVES ENGINE) 6A1-37
Check clearance by using gaging plastic.
The procedure is as follows.
1) Clean housing and camshaft journals.
2) Install camshaft to cylinder head.
3) Place a piece of gaging plastic the full width of journal of cam-
shaft (parallel to camshaft).
4) Install camshaft housing referring to “INSTALLATION” of the fol-
lowing page.
5) Tighten camshaft housing bolts in such order as indicated in fig-
ure a little at a time till they are tightened to specified torque.
Tightening Torque
(a): 11 N
.m (1.1kg-m, 8.0 lb-ft)
NOTE:
Do not rotate camshaft while gaging plastic is installed.
6) Remove housing and using scale (2) on gaging plastic (1) enve-
lope, measure gaging plastic width at its widest point.
StandardLimit
Journal
clearance0.040 – 0.082 mm
(0.0016 – 0.0032 in.)0.12 mm
(0.0047 in.)
If measured camshaft journal clearance exceeds limit, measure
journal (housing) bore and outside diameter of camshaft journal.
Replace camshaft or cylinder head assembly whichever the dif-
ference from specification is greater.
Item
Standard
Camshaft Journal bore dia.28.000 – 28.021 mm
(1.1024 – 1.1031 in.)
Camshaft journal O.D.27.939 – 27.960 mm
(1.1000 – 1.1008 in.)