Page 333 of 557
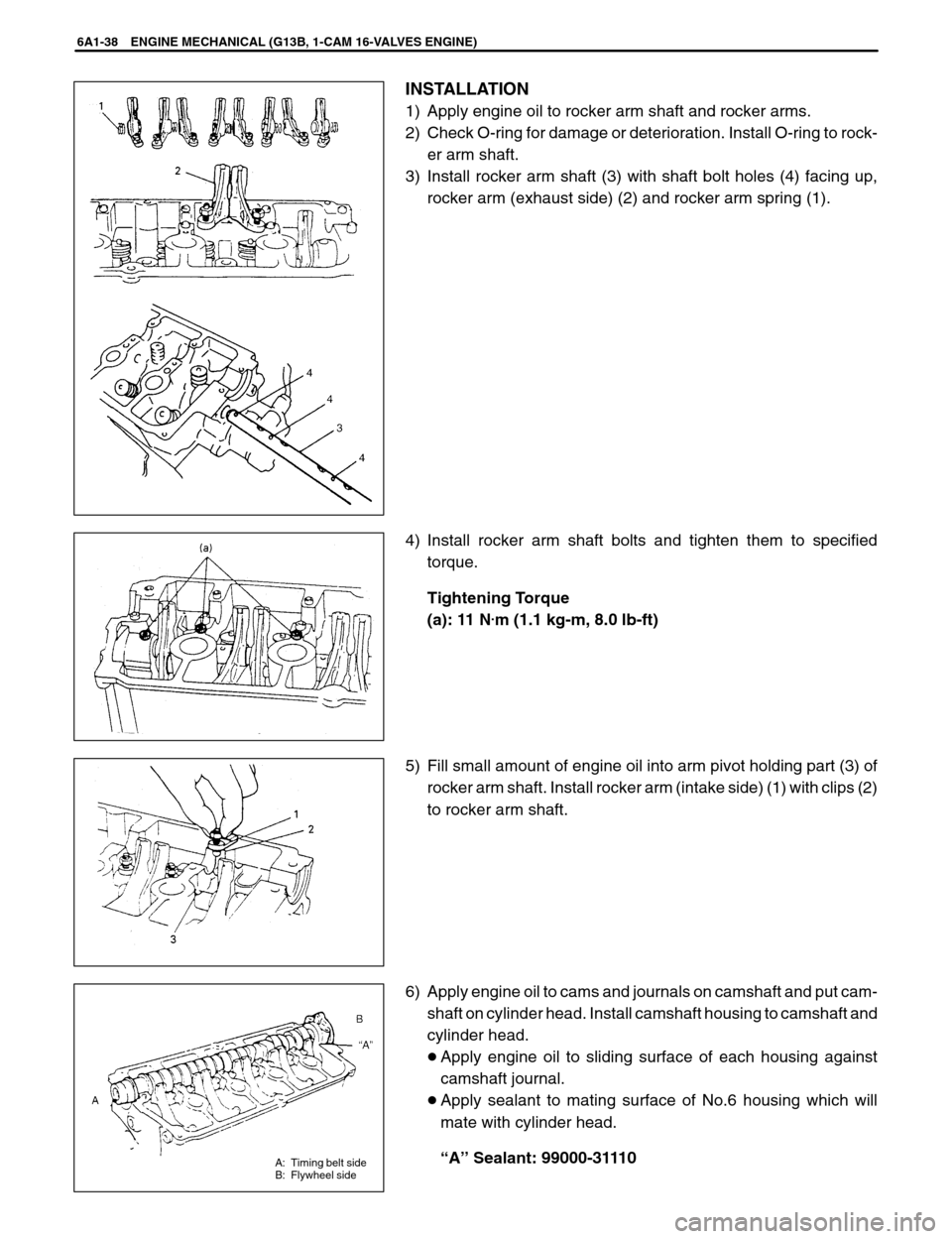
A: Timing belt side
B: Flywheel side
6A1-38 ENGINE MECHANICAL (G13B, 1-CAM 16-VALVES ENGINE)
INSTALLATION
1) Apply engine oil to rocker arm shaft and rocker arms.
2) Check O-ring for damage or deterioration. Install O-ring to rock-
er arm shaft.
3) Install rocker arm shaft (3) with shaft bolt holes (4) facing up,
rocker arm (exhaust side) (2) and rocker arm spring (1).
4) Install rocker arm shaft bolts and tighten them to specified
torque.
Tightening Torque
(a): 11 N
.m (1.1 kg-m, 8.0 lb-ft)
5) Fill small amount of engine oil into arm pivot holding part (3) of
rocker arm shaft. Install rocker arm (intake side) (1) with clips (2)
to rocker arm shaft.
6) Apply engine oil to cams and journals on camshaft and put cam-
shaft on cylinder head. Install camshaft housing to camshaft and
cylinder head.
Apply engine oil to sliding surface of each housing against
camshaft journal.
Apply sealant to mating surface of No.6 housing which will
mate with cylinder head.
“A” Sealant: 99000-31110
Page 334 of 557
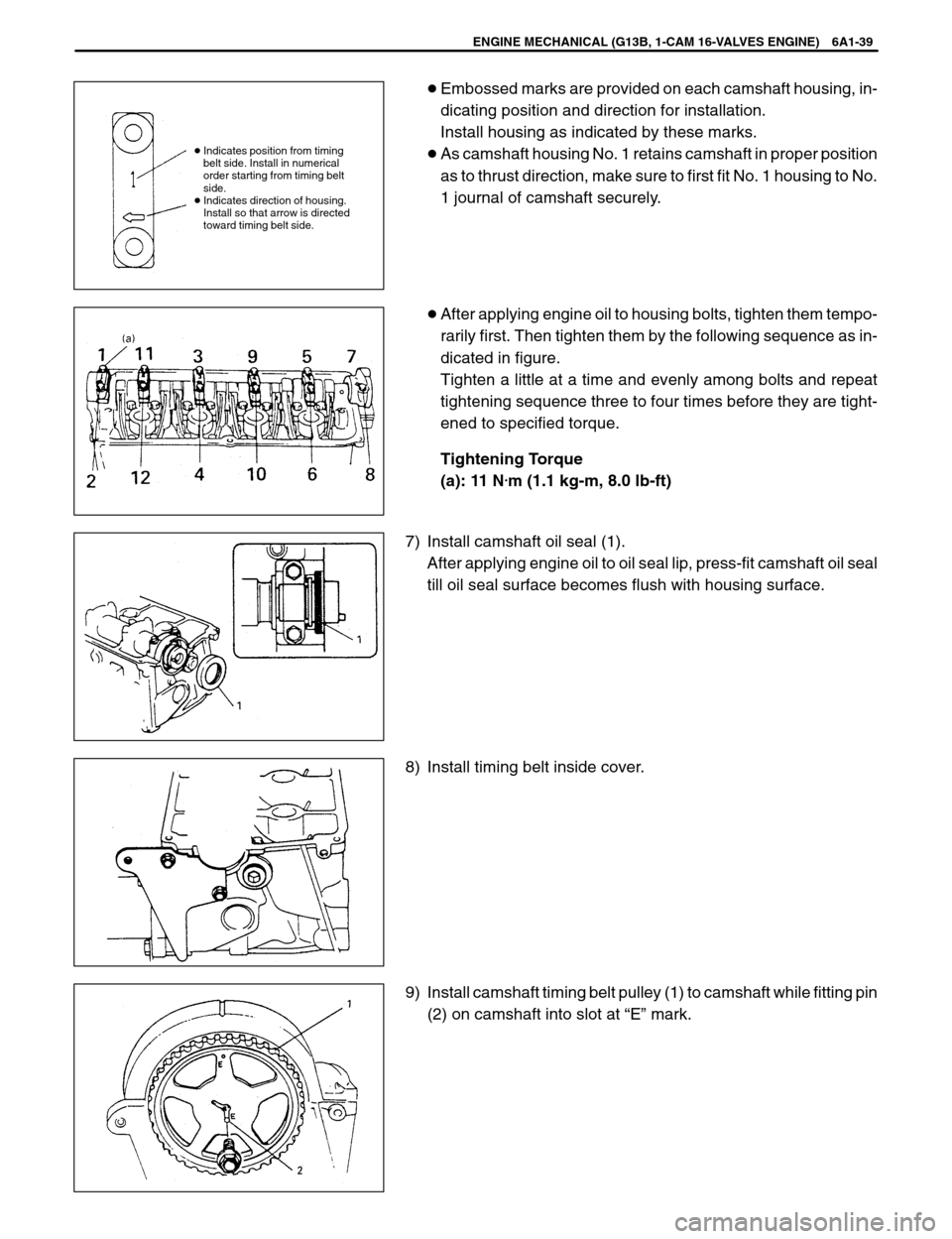
ENGINE MECHANICAL (G13B, 1-CAM 16-VALVES ENGINE) 6A1-39
Indicates position from timing
belt side. Install in numerical
order starting from timing belt
side.
Indicates direction of housing.
Install so that arrow is directed
toward timing belt side.
Embossed marks are provided on each camshaft housing, in-
dicating position and direction for installation.
Install housing as indicated by these marks.
As camshaft housing No. 1 retains camshaft in proper position
as to thrust direction, make sure to first fit No. 1 housing to No.
1 journal of camshaft securely.
After applying engine oil to housing bolts, tighten them tempo-
rarily first. Then tighten them by the following sequence as in-
dicated in figure.
Tighten a little at a time and evenly among bolts and repeat
tightening sequence three to four times before they are tight-
ened to specified torque.
Tightening Torque
(a): 11 N
.m (1.1 kg-m, 8.0 lb-ft)
7) Install camshaft oil seal (1).
After applying engine oil to oil seal lip, press-fit camshaft oil seal
till oil seal surface becomes flush with housing surface.
8) Install timing belt inside cover.
9) Install camshaft timing belt pulley (1) to camshaft while fitting pin
(2) on camshaft into slot at “E” mark.
Page 335 of 557
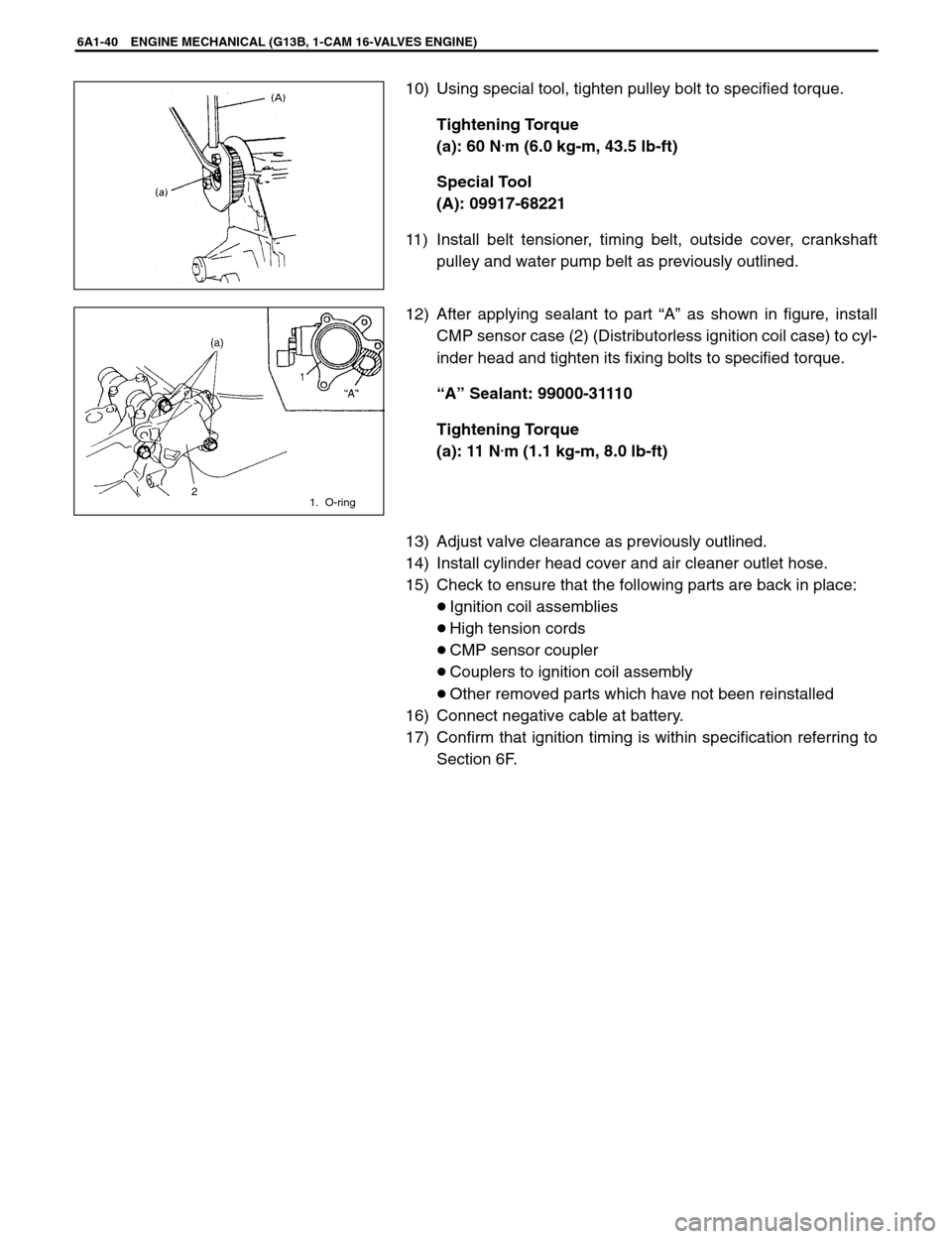
6A1-40 ENGINE MECHANICAL (G13B, 1-CAM 16-VALVES ENGINE)
1. O-ring2
10) Using special tool, tighten pulley bolt to specified torque.
Tightening Torque
(a): 60 N
.m (6.0 kg-m, 43.5 lb-ft)
Special Tool
(A): 09917-68221
11) Install belt tensioner, timing belt, outside cover, crankshaft
pulley and water pump belt as previously outlined.
12) After applying sealant to part “A” as shown in figure, install
CMP sensor case (2) (Distributorless ignition coil case) to cyl-
inder head and tighten its fixing bolts to specified torque.
“A” Sealant: 99000-31110
Tightening Torque
(a): 11 N
.m (1.1 kg-m, 8.0 lb-ft)
13) Adjust valve clearance as previously outlined.
14) Install cylinder head cover and air cleaner outlet hose.
15) Check to ensure that the following parts are back in place:
Ignition coil assemblies
High tension cords
CMP sensor coupler
Couplers to ignition coil assembly
Other removed parts which have not been reinstalled
16) Connect negative cable at battery.
17) Confirm that ignition timing is within specification referring to
Section 6F.
Page 336 of 557
: Do not reuse
1. Valve cotters
2. Valve spring retainer
3. Valve spring:
be sure to position
spring in place with its
bottom end (small-pitch
end) facing the bottom
(valve spring seat side).
4. Valve stem seal
5. Valve spring seat
6. Exhaust valve
7. Intake valve
8. Cylinder head bolt
9. Camshaft housing bolt10. Camshaft housing:
Apply sealant to mating surface of
No.1 and No.6 housings.
11. Valve guide
12. Oil venturi plug
13. Cylinder head gasket:
“TOP” mark provided on gasket comes to
crankshaft pulley side, facing up
(toward cylinder head side).
14. Dowel pin
: Tightening Torque
: Apply engine oil to sliding
: surfaces of each part.
3.5 N.m (0.35 kg-m)
ENGINE MECHANICAL (G13B, 1-CAM 16-VALVES ENGINE) 6A1-41
VALVES AND CYLINDER HEAD
REMOVAL
1) Relieve fuel pressure according to procedure described in Sec-
tion 6.
2) Disconnect negative cable at battery.
3) Drain cooling system.
4) Remove air cleaner outlet hose as previously outlined.
Page 337 of 557
6A1-42 ENGINE MECHANICAL (G13B, 1-CAM 16-VALVES ENGINE)
Ignition coil assembly
Ground wires from
intake manifold
EVAP canister purge
valve
ECT sensorInjectors, TP sensor and
IAC valve wires at the
coupler
Heated oxygen sensor 1
MAP sensor
5) Remove intake manifold rear stiffener (1) and generator adjust
arm reinforcement (2) from intake manifold.
6) Disconnect the following electric wires:
and then release above wire harnesses from clamps.
7) Disconnect the following hoses:
Brake booster hose (1)
EVAP canister purge hose (3) from purge valve
Radiator inlet hose
Heater inlet hose
IAC valve outlet (2)
8) Disconnect fuel feed (2) and return hoses (3) from fuel delivery
pipe (1).
Page 338 of 557
3
2. Breather hose
3. PCV valve4. High-tension cords
5. Ignition coil assembly
6. Ignition coil coupler
A: Camshaft pulley side
B: CMP sensor case side
ENGINE MECHANICAL (G13B, 1-CAM 16-VALVES ENGINE) 6A1-43
9) Remove cylinder head cover (1) as previously outlined.
Loosen all valve lash adjusting screws fully.
10) Remove timing belt and camshaft as previously outlined.
11) Disconnect exhaust pipe from exhaust manifold and remove
exhaust manifold stiffener (if equipped).
12) Loosen cylinder head bolts in such order as indicated in figure
and remove them.
13) Check all around cylinder head for any other parts required to
be removed or disconnected and remove or disconnect what-
ever necessary.
14) Remove cylinder head with intake manifold, exhaust manifold
CMP sensor case, using lifting device if necessary.
Page 339 of 557
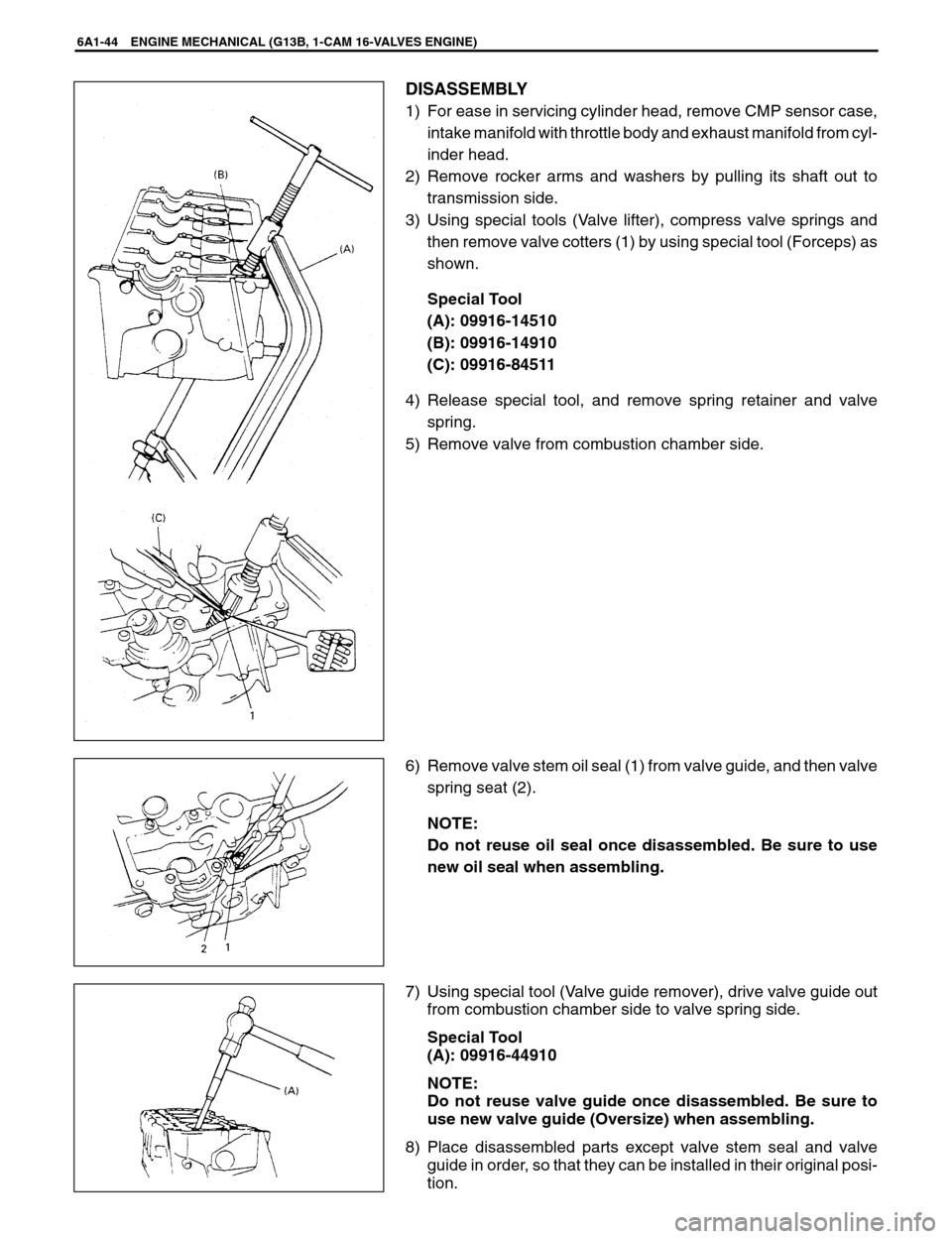
6A1-44 ENGINE MECHANICAL (G13B, 1-CAM 16-VALVES ENGINE)
DISASSEMBLY
1) For ease in servicing cylinder head, remove CMP sensor case,
intake manifold with throttle body and exhaust manifold from cyl-
inder head.
2) Remove rocker arms and washers by pulling its shaft out to
transmission side.
3) Using special tools (Valve lifter), compress valve springs and
then remove valve cotters (1) by using special tool (Forceps) as
shown.
Special Tool
(A): 09916-14510
(B): 09916-14910
(C): 09916-84511
4) Release special tool, and remove spring retainer and valve
spring.
5) Remove valve from combustion chamber side.
6) Remove valve stem oil seal (1) from valve guide, and then valve
spring seat (2).
NOTE:
Do not reuse oil seal once disassembled. Be sure to use
new oil seal when assembling.
7) Using special tool (Valve guide remover), drive valve guide out
from combustion chamber side to valve spring side.
Special Tool
(A): 09916-44910
NOTE:
Do not reuse valve guide once disassembled. Be sure to
use new valve guide (Oversize) when assembling.
8) Place disassembled parts except valve stem seal and valve
guide in order, so that they can be installed in their original posi-
tion.
Page 340 of 557
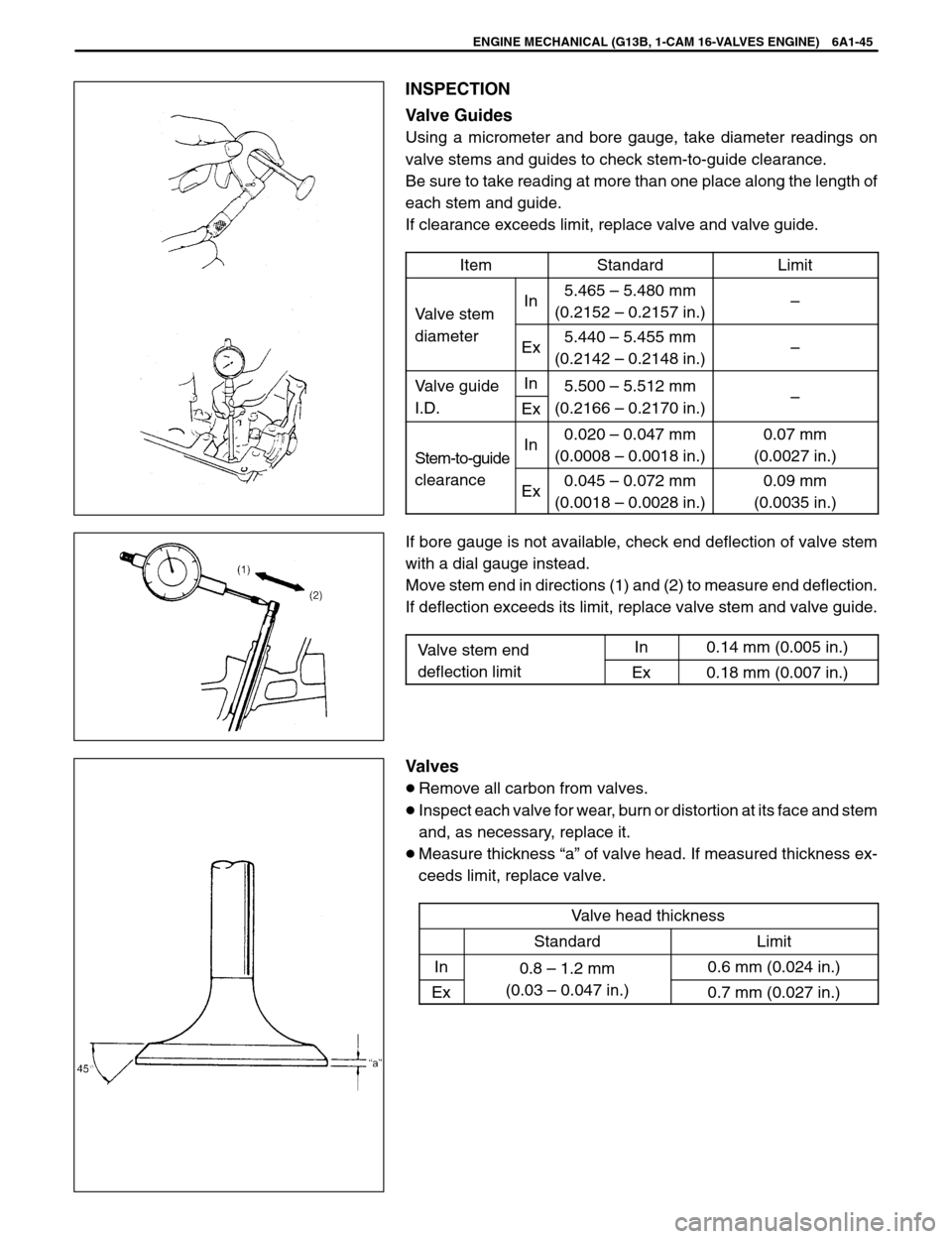
ENGINE MECHANICAL (G13B, 1-CAM 16-VALVES ENGINE) 6A1-45
INSPECTION
Valve Guides
Using a micrometer and bore gauge, take diameter readings on
valve stems and guides to check stem-to-guide clearance.
Be sure to take reading at more than one place along the length of
each stem and guide.
If clearance exceeds limit, replace valve and valve guide.
Item
StandardLimit
Valve stemIn5.465 – 5.480 mm
(0.2152 – 0.2157 in.)–
diameterEx5.440 – 5.455 mm
(0.2142 – 0.2148 in.)–
Valve guideIn5.500 – 5.512 mmg
I.D.Ex(0.2166 – 0.2170 in.)–
Stem-to-guideIn0.020 – 0.047 mm
(0.0008 – 0.0018 in.)0.07 mm
(0.0027 in.)
g
clearanceEx0.045 – 0.072 mm
(0.0018 – 0.0028 in.)0.09 mm
(0.0035 in.)
If bore gauge is not available, check end deflection of valve stem
with a dial gauge instead.
Move stem end in directions (1) and (2) to measure end deflection.
If deflection exceeds its limit, replace valve stem and valve guide.
Valve stem end
In0.14 mm (0.005 in.)
deflection limitEx0.18 mm (0.007 in.)
Valves
Remove all carbon from valves.
Inspect each valve for wear, burn or distortion at its face and stem
and, as necessary, replace it.
Measure thickness “a” of valve head. If measured thickness ex-
ceeds limit, replace valve.
Valve head thickness
StandardLimit
In0.8 – 1.2 mm0.6 mm (0.024 in.)
Ex(0.03 – 0.047 in.)0.7 mm (0.027 in.)