Page 271 of 557
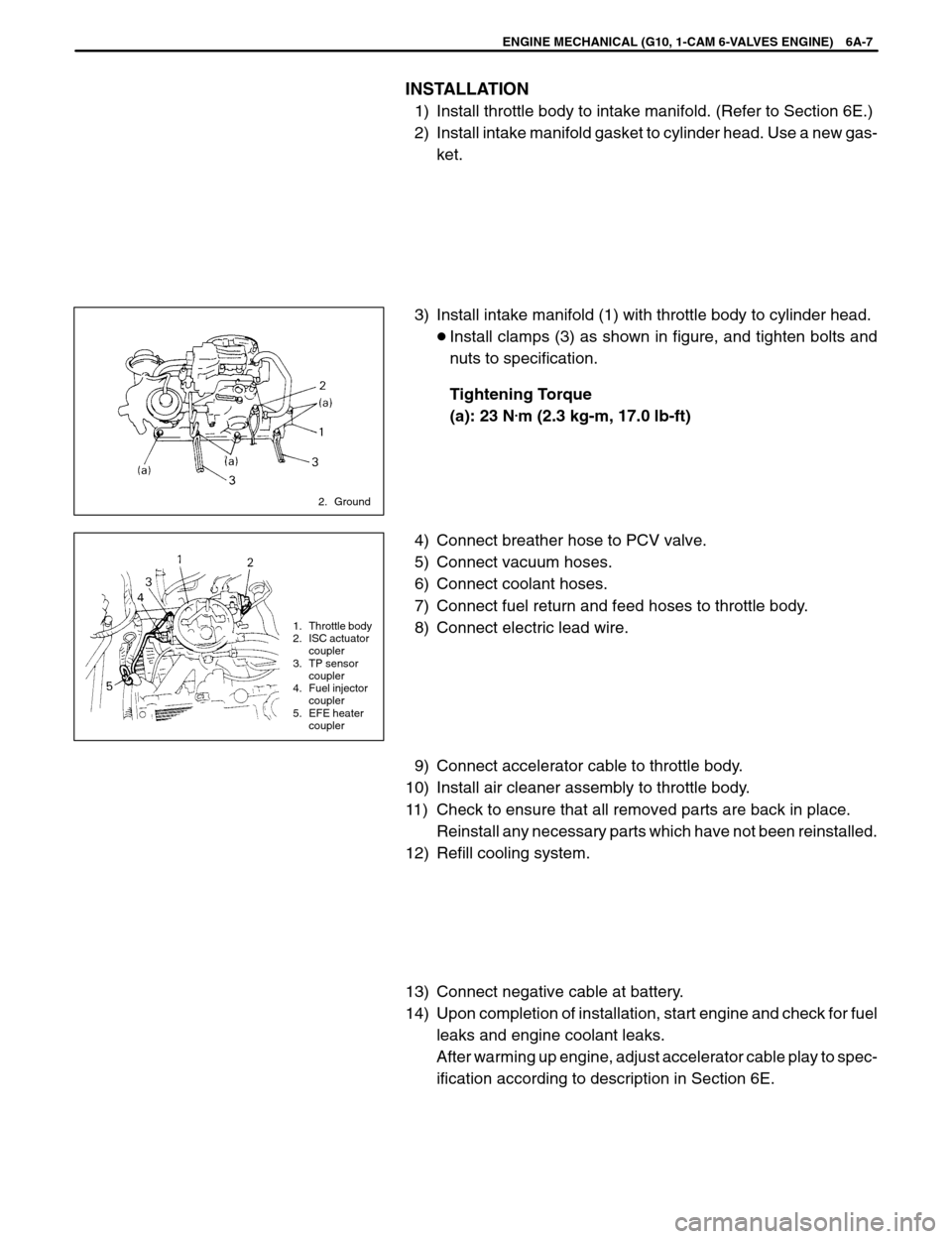
2. Ground
1. Throttle body
2. ISC actuator
coupler
3. TP sensor
coupler
4. Fuel injector
coupler
5. EFE heater
coupler
ENGINE MECHANICAL (G10, 1-CAM 6-VALVES ENGINE) 6A-7
INSTALLATION
1) Install throttle body to intake manifold. (Refer to Section 6E.)
2) Install intake manifold gasket to cylinder head. Use a new gas-
ket.
3) Install intake manifold (1) with throttle body to cylinder head.
Install clamps (3) as shown in figure, and tighten bolts and
nuts to specification.
Tightening Torque
(a): 23 N
.m (2.3 kg-m, 17.0 lb-ft)
4) Connect breather hose to PCV valve.
5) Connect vacuum hoses.
6) Connect coolant hoses.
7) Connect fuel return and feed hoses to throttle body.
8) Connect electric lead wire.
9) Connect accelerator cable to throttle body.
10) Install air cleaner assembly to throttle body.
11) Check to ensure that all removed parts are back in place.
Reinstall any necessary parts which have not been reinstalled.
12) Refill cooling system.
13) Connect negative cable at battery.
14) Upon completion of installation, start engine and check for fuel
leaks and engine coolant leaks.
After warming up engine, adjust accelerator cable play to spec-
ification according to description in Section 6E.
Page 273 of 557
2. WU-TWC
ENGINE MECHANICAL (G10, 1-CAM 6-VALVES ENGINE) 6A-9
INSTALLATION
1) Install manifold gasket to cylinder head.
Before installing gasket, check it for deterioration or damage,
and replace as necessary.
2) Install exhaust manifold (1).
Tighten manifold bolts and nuts to specified torque.
Tightening Torque
(a): 23 N
.m (2.3 kg-m, 17.0 lb-ft)
3) Install exhaust manifold cover (2).
4) Install pipe seal, and then connect exhaust pipe (1).
Before installing pipe seal, check it for deterioration or damage,
and replace as necessary.
Tighten pipe bolts to specified torque.
Tightening Torque
(c): 43 N
.m (4.3 kg-m, 31.5 lb-ft)
5) Install WU-TWC stiffener (3). (if equipped)
6) Connect heated oxygen sensor coupler.
7) Clamp its wire securely.
8) Connect negative cable at battery.
9) Check exhaust system for exhaust gas leakage.
Page 276 of 557
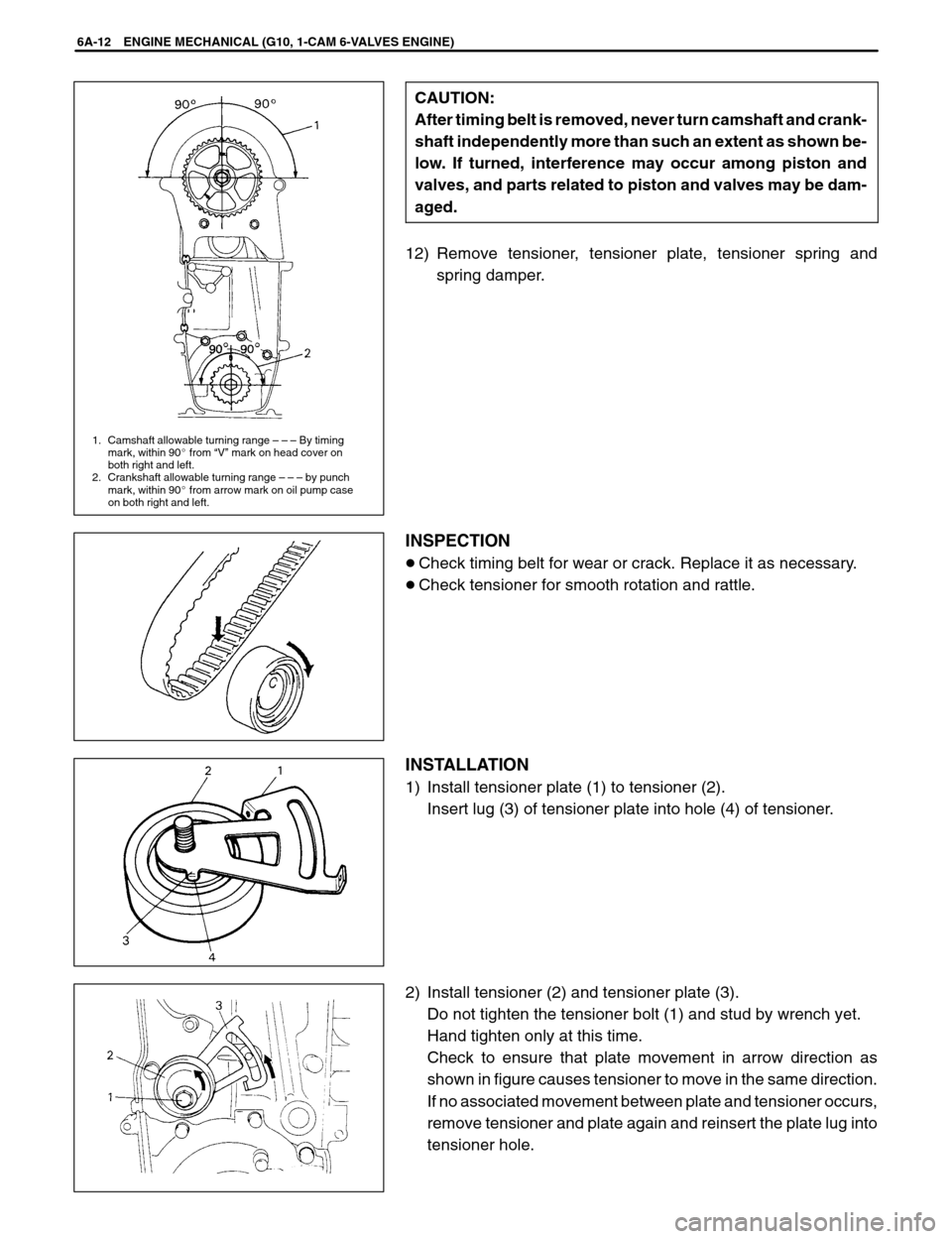
6A-12 ENGINE MECHANICAL (G10, 1-CAM 6-VALVES ENGINE)
1. Camshaft allowable turning range – – – By timing
mark, within 90 from “V” mark on head cover on
both right and left.
2. Crankshaft allowable turning range – – – by punch
mark, within 90 from arrow mark on oil pump case
on both right and left.
CAUTION:
After timing belt is removed, never turn camshaft and crank-
shaft independently more than such an extent as shown be-
low. If turned, interference may occur among piston and
valves, and parts related to piston and valves may be dam-
aged.
12) Remove tensioner, tensioner plate, tensioner spring and
spring damper.
INSPECTION
Check timing belt for wear or crack. Replace it as necessary.
Check tensioner for smooth rotation and rattle.
INSTALLATION
1) Install tensioner plate (1) to tensioner (2).
Insert lug (3) of tensioner plate into hole (4) of tensioner.
2) Install tensioner (2) and tensioner plate (3).
Do not tighten the tensioner bolt (1) and stud by wrench yet.
Hand tighten only at this time.
Check to ensure that plate movement in arrow direction as
shown in figure causes tensioner to move in the same direction.
If no associated movement between plate and tensioner occurs,
remove tensioner and plate again and reinsert the plate lug into
tensioner hole.
Page 277 of 557
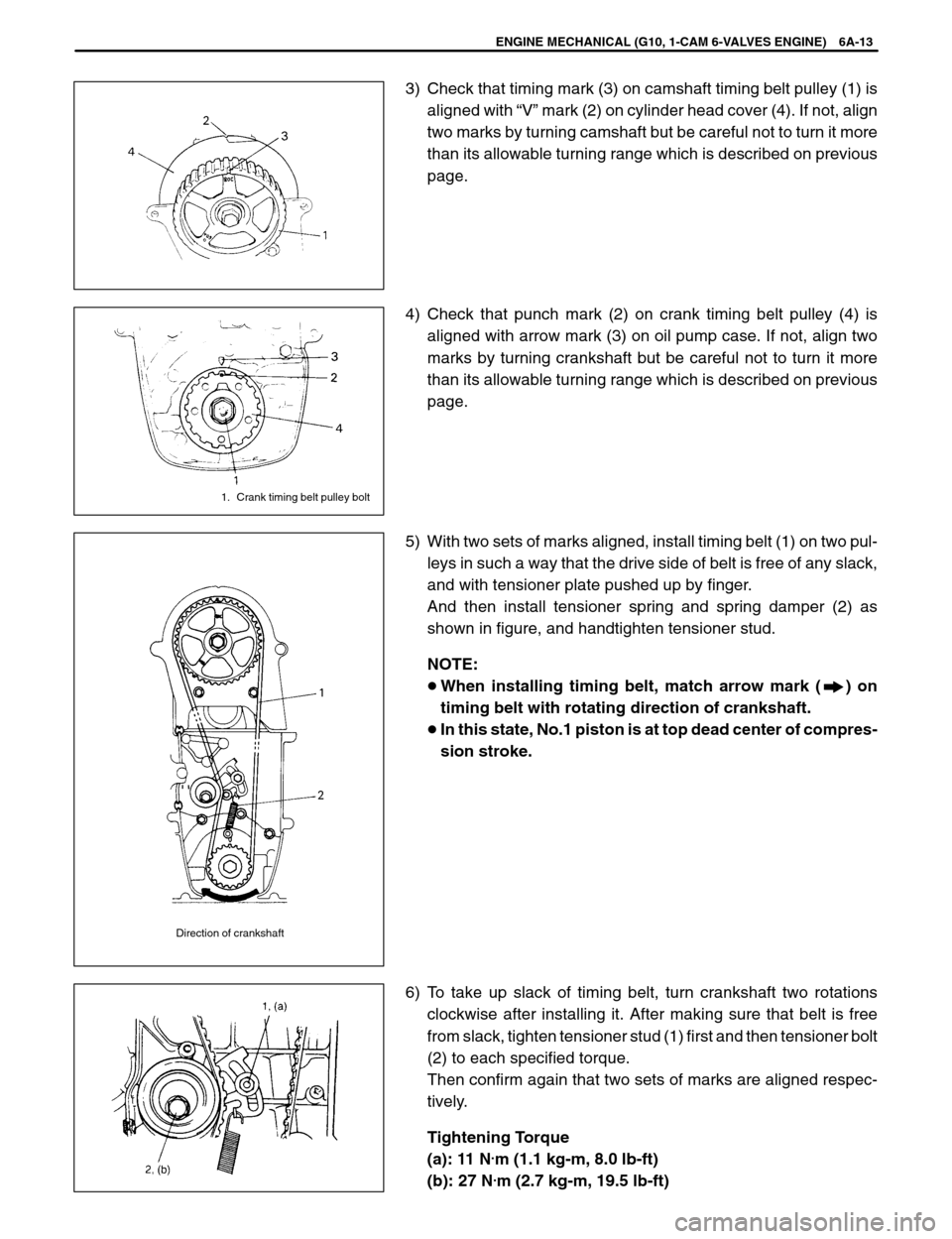
1. Crank timing belt pulley bolt
Direction of crankshaft
ENGINE MECHANICAL (G10, 1-CAM 6-VALVES ENGINE) 6A-13
3) Check that timing mark (3) on camshaft timing belt pulley (1) is
aligned with “V” mark (2) on cylinder head cover (4). If not, align
two marks by turning camshaft but be careful not to turn it more
than its allowable turning range which is described on previous
page.
4) Check that punch mark (2) on crank timing belt pulley (4) is
aligned with arrow mark (3) on oil pump case. If not, align two
marks by turning crankshaft but be careful not to turn it more
than its allowable turning range which is described on previous
page.
5) With two sets of marks aligned, install timing belt (1) on two pul-
leys in such a way that the drive side of belt is free of any slack,
and with tensioner plate pushed up by finger.
And then install tensioner spring and spring damper (2) as
shown in figure, and handtighten tensioner stud.
NOTE:
When installing timing belt, match arrow mark (
) on
timing belt with rotating direction of crankshaft.
In this state, No.1 piston is at top dead center of compres-
sion stroke.
6) To take up slack of timing belt, turn crankshaft two rotations
clockwise after installing it. After making sure that belt is free
from slack, tighten tensioner stud (1) first and then tensioner bolt
(2) to each specified torque.
Then confirm again that two sets of marks are aligned respec-
tively.
Tightening Torque
(a): 11 N
.m (1.1 kg-m, 8.0 lb-ft)
(b): 27 N
.m (2.7 kg-m, 19.5 lb-ft)
Page 281 of 557
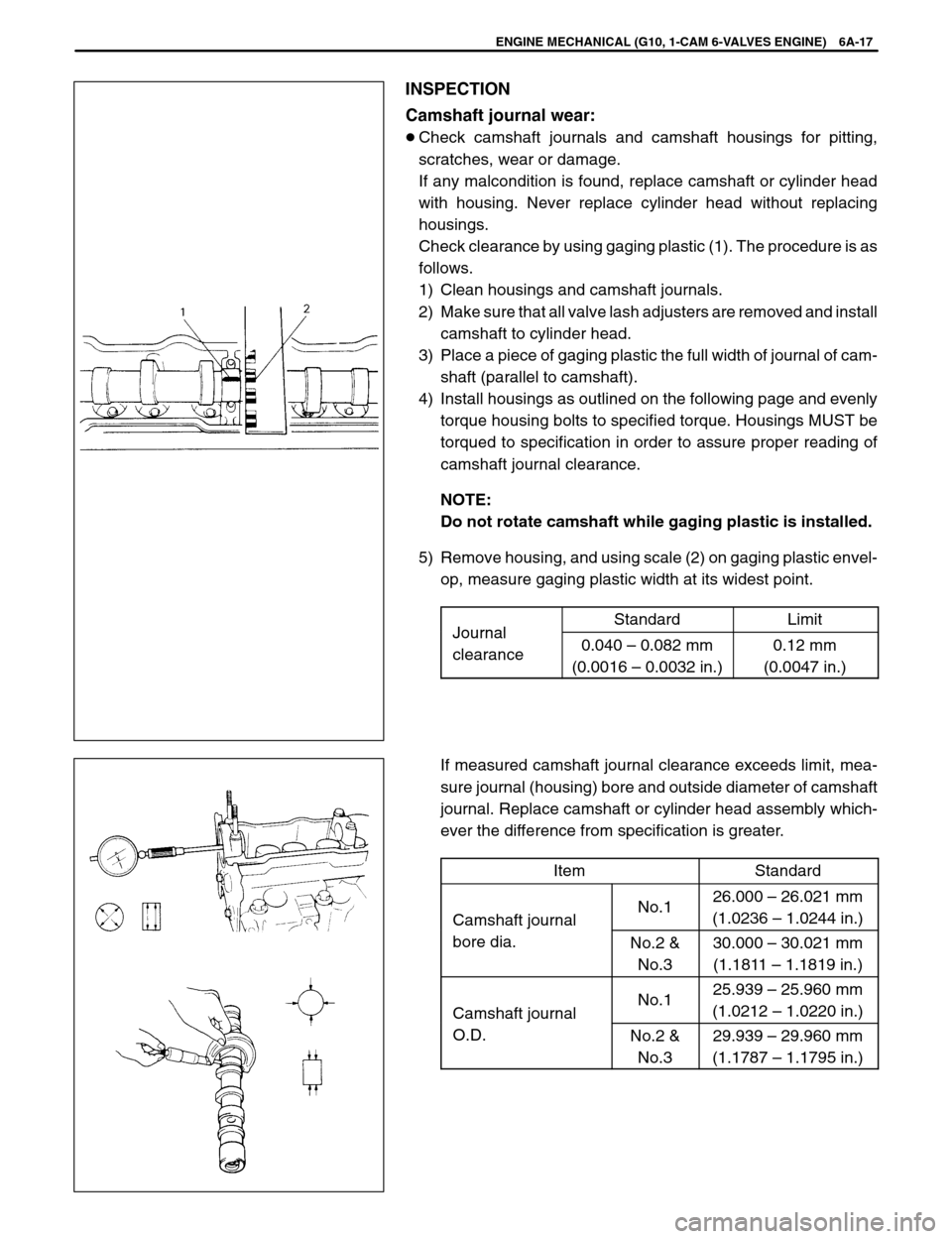
ENGINE MECHANICAL (G10, 1-CAM 6-VALVES ENGINE) 6A-17
INSPECTION
Camshaft journal wear:
Check camshaft journals and camshaft housings for pitting,
scratches, wear or damage.
If any malcondition is found, replace camshaft or cylinder head
with housing. Never replace cylinder head without replacing
housings.
Check clearance by using gaging plastic (1). The procedure is as
follows.
1) Clean housings and camshaft journals.
2) Make sure that all valve lash adjusters are removed and install
camshaft to cylinder head.
3) Place a piece of gaging plastic the full width of journal of cam-
shaft (parallel to camshaft).
4) Install housings as outlined on the following page and evenly
torque housing bolts to specified torque. Housings MUST be
torqued to specification in order to assure proper reading of
camshaft journal clearance.
NOTE:
Do not rotate camshaft while gaging plastic is installed.
5) Remove housing, and using scale (2) on gaging plastic envel-
op, measure gaging plastic width at its widest point.
JournalStandardLimitJournal
clearance0.040 – 0.082 mm
(0.0016 – 0.0032 in.)0.12 mm
(0.0047 in.)
If measured camshaft journal clearance exceeds limit, mea-
sure journal (housing) bore and outside diameter of camshaft
journal. Replace camshaft or cylinder head assembly which-
ever the difference from specification is greater.
Item
Standard
Camshaft journalNo.126.000 – 26.021 mm
(1.0236 – 1.0244 in.)
j
bore dia.No.2 &
No.330.000 – 30.021 mm
(1.1811 – 1.1819 in.)
Camshaft journalNo.125.939 – 25.960 mm
(1.0212 – 1.0220 in.)
j
O.D.No.2 &
No.329.939 – 29.960 mm
(1.1787 – 1.1795 in.)
Page 282 of 557
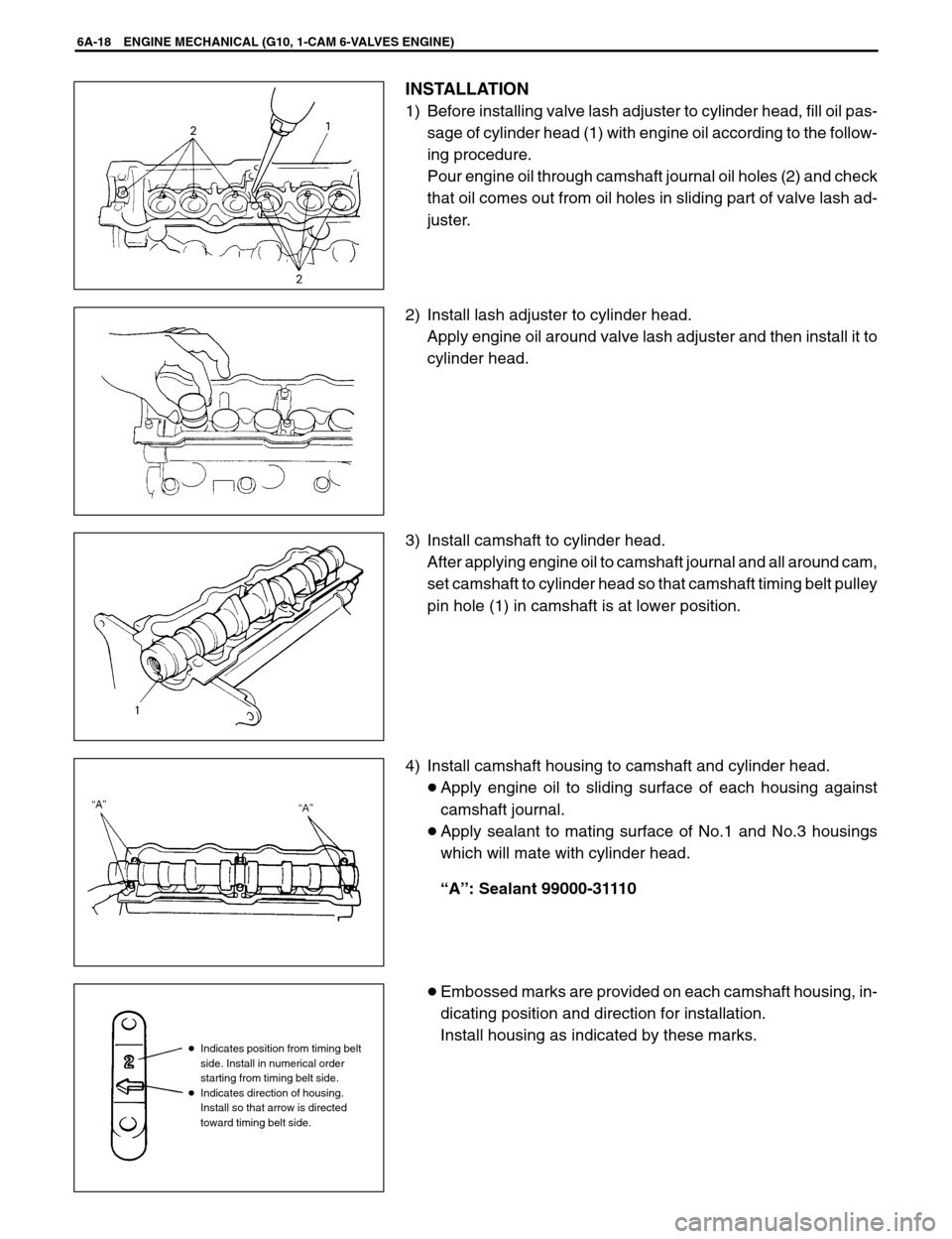
Indicates position from timing belt
side. Install in numerical order
starting from timing belt side.
Indicates direction of housing.
Install so that arrow is directed
toward timing belt side.
6A-18 ENGINE MECHANICAL (G10, 1-CAM 6-VALVES ENGINE)
INSTALLATION
1) Before installing valve lash adjuster to cylinder head, fill oil pas-
sage of cylinder head (1) with engine oil according to the follow-
ing procedure.
Pour engine oil through camshaft journal oil holes (2) and check
that oil comes out from oil holes in sliding part of valve lash ad-
juster.
2) Install lash adjuster to cylinder head.
Apply engine oil around valve lash adjuster and then install it to
cylinder head.
3) Install camshaft to cylinder head.
After applying engine oil to camshaft journal and all around cam,
set camshaft to cylinder head so that camshaft timing belt pulley
pin hole (1) in camshaft is at lower position.
4) Install camshaft housing to camshaft and cylinder head.
Apply engine oil to sliding surface of each housing against
camshaft journal.
Apply sealant to mating surface of No.1 and No.3 housings
which will mate with cylinder head.
“A”: Sealant 99000-31110
Embossed marks are provided on each camshaft housing, in-
dicating position and direction for installation.
Install housing as indicated by these marks.
Page 284 of 557
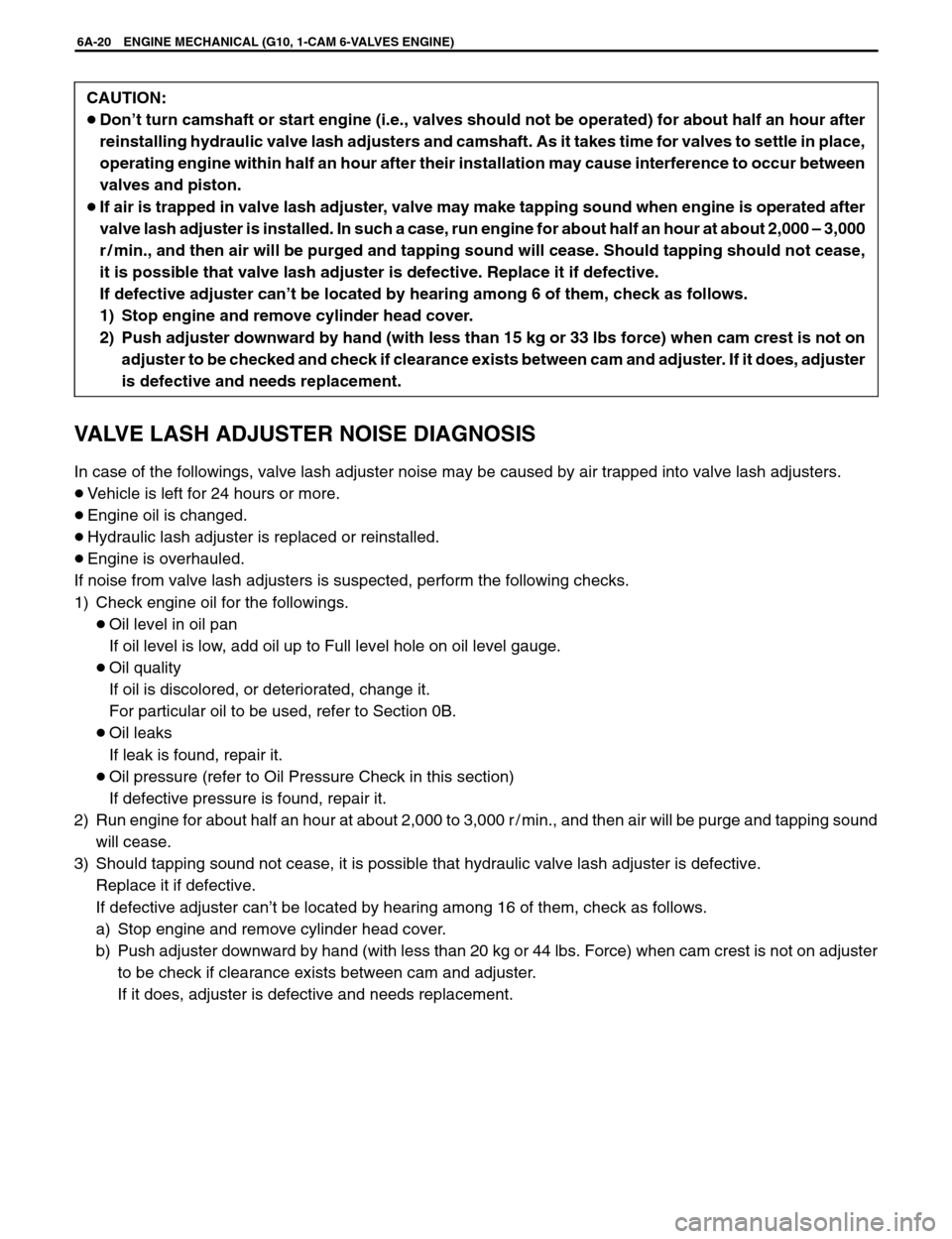
6A-20 ENGINE MECHANICAL (G10, 1-CAM 6-VALVES ENGINE)
CAUTION:
Don’t turn camshaft or start engine (i.e., valves should not be operated) for about half an hour after
reinstalling hydraulic valve lash adjusters and camshaft. As it takes time for valves to settle in place,
operating engine within half an hour after their installation may cause interference to occur between
valves and piston.
If air is trapped in valve lash adjuster, valve may make tapping sound when engine is operated after
valve lash adjuster is installed. In such a case, run engine for about half an hour at about 2,000 – 3,000
r / min., and then air will be purged and tapping sound will cease. Should tapping should not cease,
it is possible that valve lash adjuster is defective. Replace it if defective.
If defective adjuster can’t be located by hearing among 6 of them, check as follows.
1) Stop engine and remove cylinder head cover.
2) Push adjuster downward by hand (with less than 15 kg or 33 lbs force) when cam crest is not on
adjuster to be checked and check if clearance exists between cam and adjuster. If it does, adjuster
is defective and needs replacement.
VALVE LASH ADJUSTER NOISE DIAGNOSIS
In case of the followings, valve lash adjuster noise may be caused by air trapped into valve lash adjusters.
Vehicle is left for 24 hours or more.
Engine oil is changed.
Hydraulic lash adjuster is replaced or reinstalled.
Engine is overhauled.
If noise from valve lash adjusters is suspected, perform the following checks.
1) Check engine oil for the followings.
Oil level in oil pan
If oil level is low, add oil up to Full level hole on oil level gauge.
Oil quality
If oil is discolored, or deteriorated, change it.
For particular oil to be used, refer to Section 0B.
Oil leaks
If leak is found, repair it.
Oil pressure (refer to Oil Pressure Check in this section)
If defective pressure is found, repair it.
2) Run engine for about half an hour at about 2,000 to 3,000 r / min., and then air will be purge and tapping sound
will cease.
3) Should tapping sound not cease, it is possible that hydraulic valve lash adjuster is defective.
Replace it if defective.
If defective adjuster can’t be located by hearing among 16 of them, check as follows.
a) Stop engine and remove cylinder head cover.
b) Push adjuster downward by hand (with less than 20 kg or 44 lbs. Force) when cam crest is not on adjuster
to be check if clearance exists between cam and adjuster.
If it does, adjuster is defective and needs replacement.
Page 285 of 557
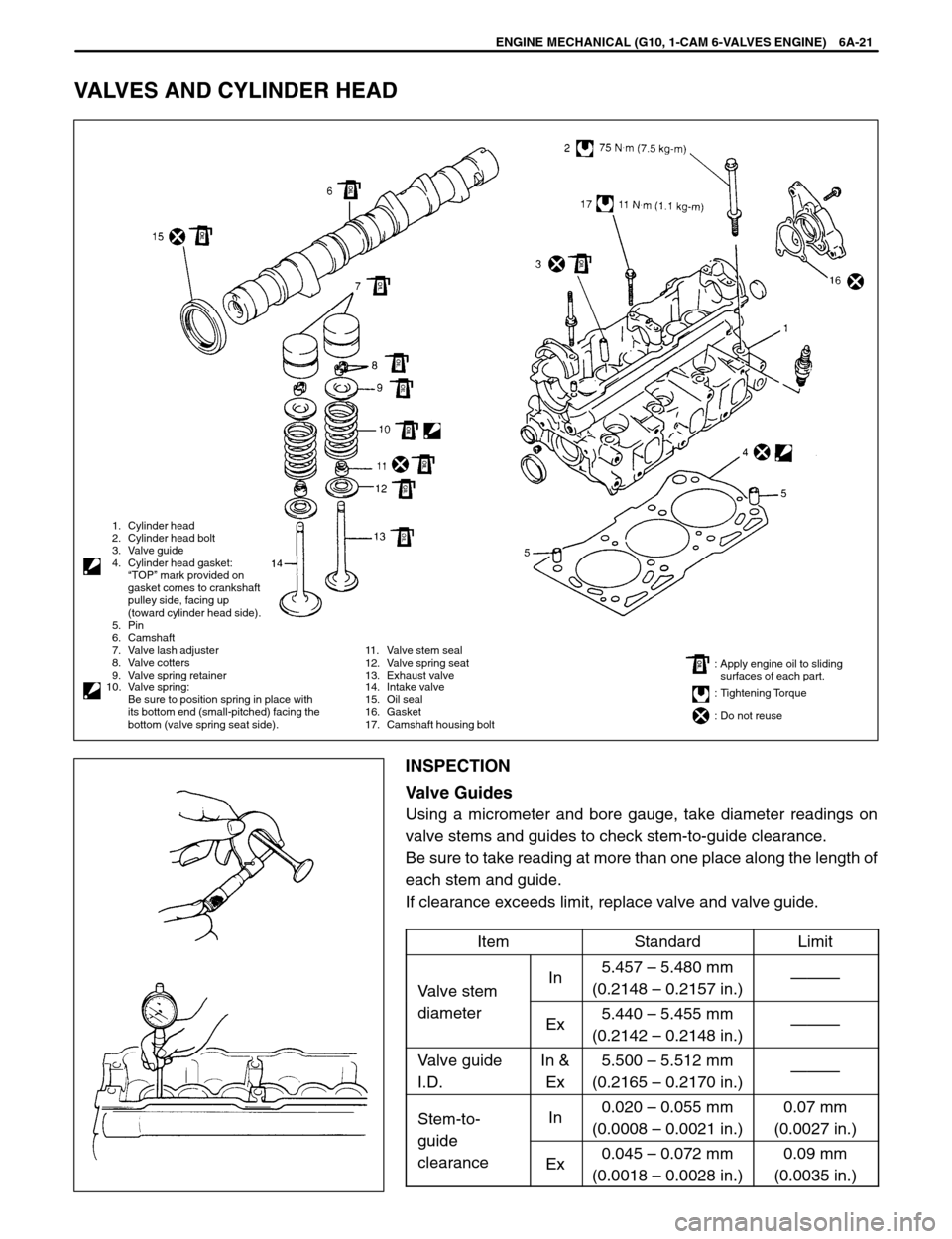
1. Cylinder head
2. Cylinder head bolt
3. Valve guide
4. Cylinder head gasket:
“TOP” mark provided on
gasket comes to crankshaft
pulley side, facing up
(toward cylinder head side).
5. Pin
6. Camshaft
7. Valve lash adjuster
8. Valve cotters
9. Valve spring retainer
10. Valve spring:
Be sure to position spring in place with
its bottom end (small-pitched) facing the
bottom (valve spring seat side).11. Valve stem seal
12. Valve spring seat
13. Exhaust valve
14. Intake valve
15. Oil seal
16. Gasket
17. Camshaft housing bolt: Tightening Torque
: Do not reuse
: Apply engine oil to sliding
: surfaces of each part.
ENGINE MECHANICAL (G10, 1-CAM 6-VALVES ENGINE) 6A-21
VALVES AND CYLINDER HEAD
INSPECTION
Valve Guides
Using a micrometer and bore gauge, take diameter readings on
valve stems and guides to check stem-to-guide clearance.
Be sure to take reading at more than one place along the length of
each stem and guide.
If clearance exceeds limit, replace valve and valve guide.
Item
StandardLimit
Valve stemIn5.457 – 5.480 mm
(0.2148 – 0.2157 in.)———
diameterEx5.440 – 5.455 mm
(0.2142 – 0.2148 in.)———
Valve guide
I.D.In &
Ex5.500 – 5.512 mm
(0.2165 – 0.2170 in.)———
Stem-to-
guide
In0.020 – 0.055 mm
(0.0008 – 0.0021 in.)0.07 mm
(0.0027 in.)
guide
clearanceEx0.045 – 0.072 mm
(0.0018 – 0.0028 in.)0.09 mm
(0.0035 in.)