Page 509 of 698
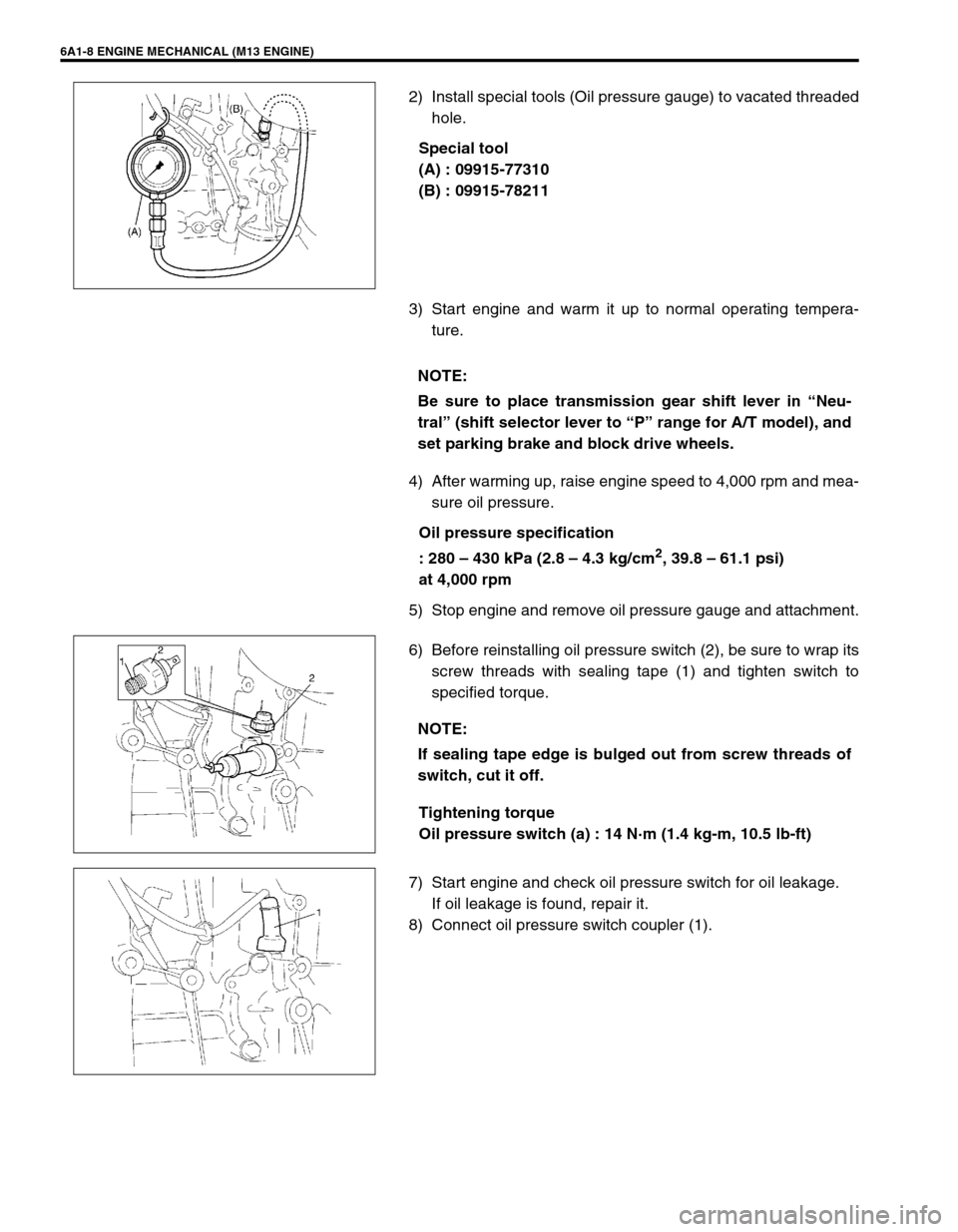
6A1-8 ENGINE MECHANICAL (M13 ENGINE)
2) Install special tools (Oil pressure gauge) to vacated threaded
hole.
Special tool
(A) : 09915-77310
(B) : 09915-78211
3) Start engine and warm it up to normal operating tempera-
ture.
4) After warming up, raise engine speed to 4,000 rpm and mea-
sure oil pressure.
Oil pressure specification
: 280 – 430 kPa (2.8 – 4.3 kg/cm
2, 39.8 – 61.1 psi)
at 4,000 rpm
5) Stop engine and remove oil pressure gauge and attachment.
6) Before reinstalling oil pressure switch (2), be sure to wrap its
screw threads with sealing tape (1) and tighten switch to
specified torque.
Tightening torque
Oil pressure switch (a) : 14 N·m (1.4 kg-m, 10.5 lb-ft)
7) Start engine and check oil pressure switch for oil leakage.
If oil leakage is found, repair it.
8) Connect oil pressure switch coupler (1).
NOTE:
Be sure to place transmission gear shift lever in “Neu-
tral” (shift selector lever to “P” range for A/T model), and
set parking brake and block drive wheels.
NOTE:
If sealing tape edge is bulged out from screw threads of
switch, cut it off.
Page 522 of 698
ENGINE MECHANICAL (M13 ENGINE) 6A1-21
4) Install exhaust manifold cover (1) .
5) Connect heated oxygen sensor coupler (2) and fit coupler to
bracket securely (if equipped).
6) Install heat insulator panel and front bumper with front grille
by referring to Section 9.
7) Connect negative cable at battery.
8) Check exhaust system for exhaust gas leakage.
OIL PAN AND OIL PUMP STRAINER
REMOVAL
1) Disconnect negative cable at battery.
2) Disconnect heated oxygen sensor coupler and detach it from
its stay.
3) Remove oil level gauge.
[A] : Sealant application amount 3. O-ring 8. Oil pan nut
“a” : 3 mm (0.12 in.) 4. Gasket 9. Oil pan bolt
“b” : 2 mm (0.08 in.) 5. Drain plug Tightening torque
1. Oil pan
: Apply sealant 99000-31150 to mating surface.6. Strainer bolt Do not reuse.
2. Strainer 7. Bracket bolt
Page 528 of 698
ENGINE MECHANICAL (M13 ENGINE) 6A1-27
11) Support engine with supporting device (1).
12) Remove engine right side mounting (2) with bracket from
timing chain cover and body.
13) Remove timing chain cover (1).
CLEAN
Clean sealing surface on timing chain cover, cylinder block
and cylinder head.
Remove oil, old sealant and dust from sealing surface.
INSPECTION
Check oil seal (1) lip for fault or other damage.
Replace as necessary.
Special tool
(A) : 09913-75520
NOTE:
When installing new oil seal, tap it in until its surface is
flash with edge of timing chain cover (2).
To install oil seal, use special tool (Bearing installer).
Page 529 of 698
6A1-28 ENGINE MECHANICAL (M13 ENGINE)
INSTALLATION
Reverse removal procedure to install timing chain cover, noting
the following points.
1) Apply sealant “A” to mating surface of cylinder and cylinder
head and “B” to mating surface of timing chain cover as
shown in figure.
“A” : Sealant 99000-31140
“B” : Sealant 99000-31150
Sealant amount for timing chain cover
Width “a” : 3 mm, 0.12 in.
Height “b” : 2 mm, 0.08 in.
2) Apply engine oil to oil seal lip, then install timing chain cover
(1).
Tighten bolts and nut to specified torque.
Tightening torque
Timing chain cover bolts (a) : 23 N·m (2.3 kg-m, 17.0 lb-ft)
3) Install engine right mounting (1) with bracket to timing chain
cover and body.
Tighten bolts to specified torque.
Tightening torque
Engine mounting bolt (a) : 75 N·m (7.5 kg-m, 54.5 lb-ft)
Engine mounting bracket bolt
(b) : 55 N·m (5.5 kg-m, 40.0 lb-ft)
4) Remove support device (2).
NOTE:
Before installing timing chain cover, check that pin is
securely fitted.
Page 532 of 698
ENGINE MECHANICAL (M13 ENGINE) 6A1-31
2) Remove outer rotor (1) and inner rotor (2).
3) Remove relief valve (1), spring (2) and retainer (3) by remov-
ing circlip (4).
INSPECTION
Check oil seal lip for fault or other damage. Replace as nec-
essary.
Special tool
(A) : 09913-75520
NOTE:
When installing new oil seal (1), press-fit it till its end face
is flush with oil pump case (2) end face.
Page 533 of 698
6A1-32 ENGINE MECHANICAL (M13 ENGINE)
Check outer (1) and inner rotors (2), rotor plate, and oil pump
case for excessive wear or damage.
Check relief valve (1) for excessive wear or damage and
operates smoothly.
MEASUREMENT
Radial Clearance
Check radial clearance between outer rotor (1) and case (2),
using thickness gauge (3).
If clearance exceeds its limit, replace outer rotor or case.
Limit on radial clearance between outer rotor and
case for oil pump
: 0.310 mm (0.0122 in.)
Side Clearance
Using straight edge (1) and thickness gauge (2), measure side
clearance.
Limit on side clearance for oil pump inner rotor
: 0.15 mm (0.0059 in.)
Page 534 of 698
ENGINE MECHANICAL (M13 ENGINE) 6A1-33
ASSEMBLY
1) Wash, clean and then dry all disassembled parts.
2) Apply thin coat of engine oil to inner and outer rotors, oil seal
lip portion, and inside surfaces of oil pump case and plate.
3) Install outer (1) and inner rotors (2) to oil pump case.
4) Install relief valve component (1) to rotor plate (2).
5) Install rotor plate and tighten all bolts to specified torque.
After installing plate, check to be sure that rotors turn
smoothly by hand (0.3 N·m (0.03 kg-m, 0.25 lb-ft) torque or
below).
Tightening torque
Oil pump rotor plate bolts (a) : 11 N·m (1.1 kg-m, 8.0 lb-ft)
INSTALLATION
For installation referring to “TIMING CHAIN COVER”.
Page 538 of 698
ENGINE MECHANICAL (M13 ENGINE) 6A1-37
5) Apply engine oil to sliding surface of timing chain No.1 guide
(1) and install it as shown in figure.
Tighten guide bolts to specified torque.
Tightening torque
Timing chain No.1 guide bolt
(a) : 9 N·m (0.9 kg-m, 6.5 lb-ft)
6) Apply engine oil to sliding surface of chain tensioner (1) and
install chain tensioner and spacer.
Tighten tensioner bolt to specified torque
Tightening torque
Timing chain tensioner bolt
(a) : 22 N·m (2.2 kg-m, 16.0 lb-ft)
7) Check that match marks (1) on intake and exhaust camshaft
timing sprockets are in match with making timing chain (2)
and match mark on crankshaft timing sprocket (3) are in with
marking timing chain(4).
8) Screw in plunger (1) by turning body (2) in arrow direction
and install a retainer (3) (wire) to hold plunger in place.