Page 497 of 698
![SUZUKI SWIFT 2000 1.G RG413 Service Workshop Manual 6-128 ENGINE GENERAL INFORMATION AND DIAGNOSIS
TABLE B-7 RADIATOR FAN CONTROL SYSTEM CHECK
INSPECTION
1. Radiator fan relay No.1 3. Radiator fan relay No.3 [A] : Case of TYPE A is shown (See NOTE)
2. SUZUKI SWIFT 2000 1.G RG413 Service Workshop Manual 6-128 ENGINE GENERAL INFORMATION AND DIAGNOSIS
TABLE B-7 RADIATOR FAN CONTROL SYSTEM CHECK
INSPECTION
1. Radiator fan relay No.1 3. Radiator fan relay No.3 [A] : Case of TYPE A is shown (See NOTE)
2.](/manual-img/20/7606/w960_7606-496.png)
6-128 ENGINE GENERAL INFORMATION AND DIAGNOSIS
TABLE B-7 RADIATOR FAN CONTROL SYSTEM CHECK
INSPECTION
1. Radiator fan relay No.1 3. Radiator fan relay No.3 [A] : Case of TYPE A is shown (See NOTE)
2. Radiator fan relay No.2 4. Radiator fan [B] : Case of TYPE B is shown (See NOTE)
BATT
80A30A
15A
BLKBLU/WHT
ECM
BLK/ORN
BLK/ORNC42-1
C42-3
L+
L–
H– H+
BLU
C42 (31P) C41 (24P) G02 (17P)1 2 3 4 5 6 7 8 9
10 11 12 13 14 15 16 17 18 19 20 21
22 23 24 25 26 28 27 29 30 315 6
1 2 3 4 5 6 7
11 12
9 10 11 13 12 14 15 16
16 171 2
7 8
13 14 3 4
9 10
15 17 188
19 20 21 22 23 24
C41-18
GRN/RED [B]PPL/YEL [A]
BLK/RED
BLU/WHT
BLU/RED
BLK
BLU
BLU/BLK
PPL/YEL
BLU/REDBLK/YEL
BRN/WHT
1
2
34
G02-3 [A]
C41-9 [B]
NOTE:
For TYPE A and TYPE B, refer to NOTE in “ECM VOLTAGE VALUES TABLE” for applicable model.
Step Action Yes No
1 Check Fan Control System.
1) Connect scan tool to DLC with ignition switch OFF.
2) Start engine and select “DATA LIST” mode on scan
tool.
3) Warm up engine until coolant temp. is 97.5°C, 208°F or
higher and A/C switch turn OFF. (If engine coolant
temp. does not rise, check engine cooling system or
ECT sensor.) See Fig. 1.
Is radiator cooling fan started when engine coolant temp.
reached above temp.?Radiator cooling fan
control system is in
good condition.Go to Step 2.
2 Check Radiator Fan Relay and Its Circuit.
1) Check DTC and pending DTC with scan tool.
Is DTC P0480 displayed?Go to DTC P0480 Diag.
Flow Table.Go to Step 3.
3 Check Radiator Fan Relays.
1) Turn ignition switch OFF and remove radiator cooling
fan relays. (No.1 – No.3)
2) Check for proper connection to relay at terminals “c”
and “d”.
3) If OK, check that there is continuity between “c” and “d”
when battery is connected to terminals “a” and “b”. See
Fig. 2.
Is check result satisfactory?Go to Step 4. Replace radia-
tor fan relay(s).
Page 498 of 698
ENGINE GENERAL INFORMATION AND DIAGNOSIS 6-129
Fig. 1 for Step 1
Fig. 2 for Step 34 Check Radiator Fan.
1) Turn ignition switch OFF.
2) Disconnect cooling fan motor connector.
3) Check for proper connection to motor at “BLU/RED”
and “BLK” terminals.
4) If OK, connect battery to motor and check for operation.
See Fig. 3.
Is it in good condition?“BLU/WHT”, “BLU/
RED” or “BLK” circuit
open.Replace radia-
tor fan motor. Step Action Yes No
[A] : When using SUZUKI scan tool:[ A]
1. Radiator fan No.1
2. Radiator fan No.2
3. Radiator fan No.3
1
1
2
3
2, 3ca
db
Page 499 of 698
6-130 ENGINE GENERAL INFORMATION AND DIAGNOSIS
Fig. 3 for Step 4
SPECIAL TOOL
09912-58441 09912-58431 09912-58490 09912-58421
Pressure gauge Pressure hose 3-way joint & hose Checking tool set
(See NOTE “A”.)
09912-57610 09917-47010 09930-88530 09931-76011
Checking tool plate Vacuum pump gauge Injector test lead Tech 1 A kit
(See NOTE “B”.)
Page 500 of 698
ENGINE GENERAL INFORMATION AND DIAGNOSIS 6-131
09931-76030
Mass storage cartridge 16/14 pin DLC cable
NOTE:
“A” : This kit includes the following items.
1. Tool body & washer, 2. Body plug, 3. Body attachment, 4. Holder, 5. Return hose & clamp,
6. Body attachment-2 & washer, 7. Hose attachment-1, 8. Hose attachment-2
“B” : This kit includes the following items.
1. Storage case, 2. Operator’s manual, 3. Tech 1A, 4. DLC cable, 5. Test lead/probe,
6. Power source cable, 7. DLC cable adaptor, 8. Self–test adaptor
Page 501 of 698
6-132 ENGINE GENERAL INFORMATION AND DIAGNOSIS
Page 502 of 698
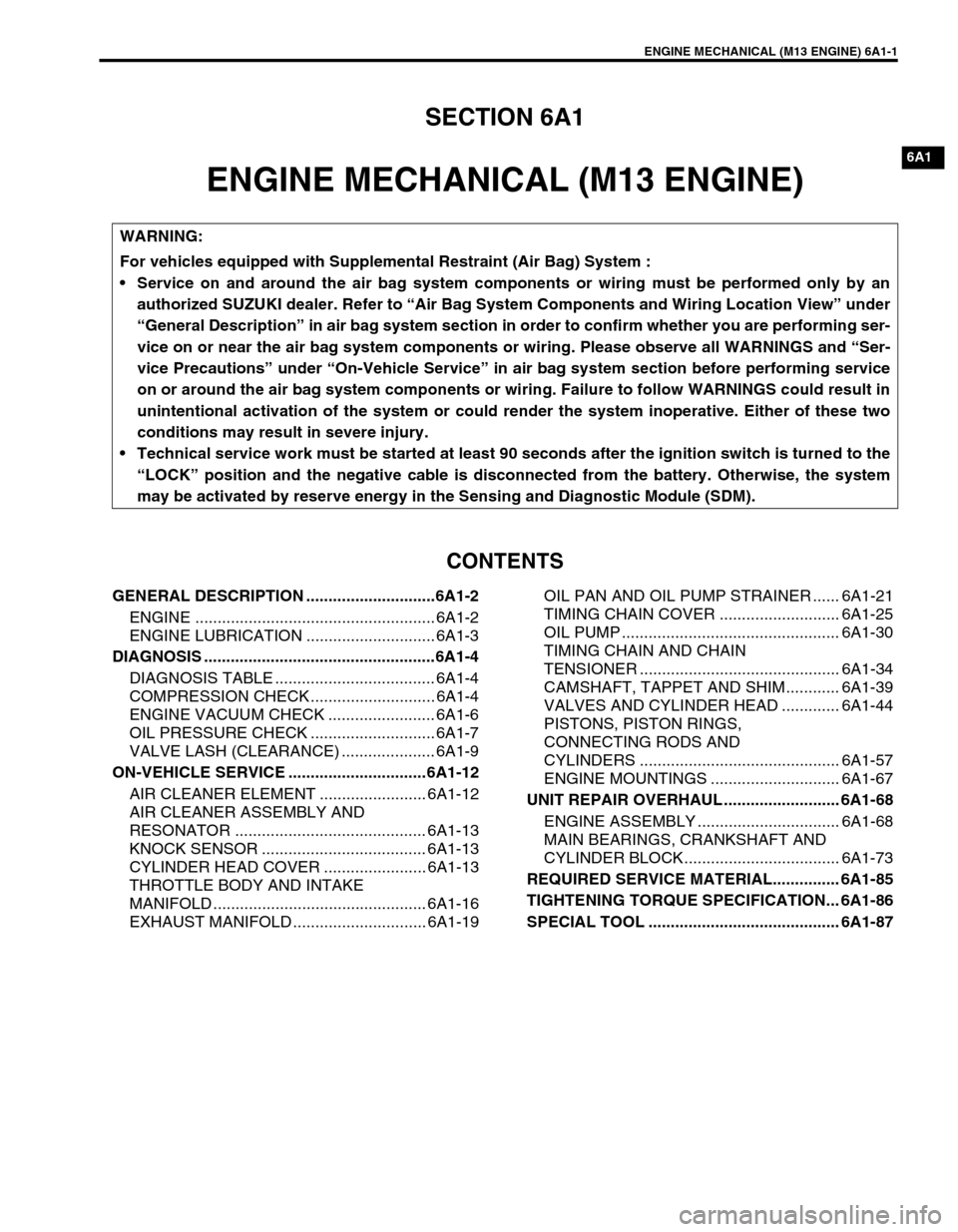
ENGINE MECHANICAL (M13 ENGINE) 6A1-1
6F1
6A1
6G
6H
6K
7A
7A1
7B1
7C1
7D
7E
7F
8A
8B
8C
8D
8E
9
10B
SECTION 6A1
ENGINE MECHANICAL (M13 ENGINE)
CONTENTS
GENERAL DESCRIPTION .............................6A1-2
ENGINE ...................................................... 6A1-2
ENGINE LUBRICATION ............................. 6A1-3
DIAGNOSIS ....................................................6A1-4
DIAGNOSIS TABLE .................................... 6A1-4
COMPRESSION CHECK ............................ 6A1-4
ENGINE VACUUM CHECK ........................ 6A1-6
OIL PRESSURE CHECK ............................ 6A1-7
VALVE LASH (CLEARANCE) ..................... 6A1-9
ON-VEHICLE SERVICE ...............................6A1-12
AIR CLEANER ELEMENT ........................ 6A1-12
AIR CLEANER ASSEMBLY AND
RESONATOR ........................................... 6A1-13
KNOCK SENSOR ..................................... 6A1-13
CYLINDER HEAD COVER ....................... 6A1-13
THROTTLE BODY AND INTAKE
MANIFOLD ................................................ 6A1-16
EXHAUST MANIFOLD .............................. 6A1-19OIL PAN AND OIL PUMP STRAINER ...... 6A1-21
TIMING CHAIN COVER ........................... 6A1-25
OIL PUMP ................................................. 6A1-30
TIMING CHAIN AND CHAIN
TENSIONER ............................................. 6A1-34
CAMSHAFT, TAPPET AND SHIM............ 6A1-39
VALVES AND CYLINDER HEAD ............. 6A1-44
PISTONS, PISTON RINGS,
CONNECTING RODS AND
CYLINDERS ............................................. 6A1-57
ENGINE MOUNTINGS ............................. 6A1-67
UNIT REPAIR OVERHAUL .......................... 6A1-68
ENGINE ASSEMBLY ................................ 6A1-68
MAIN BEARINGS, CRANKSHAFT AND
CYLINDER BLOCK................................... 6A1-73
REQUIRED SERVICE MATERIAL............... 6A1-85
TIGHTENING TORQUE SPECIFICATION... 6A1-86
SPECIAL TOOL ........................................... 6A1-87
WARNING:
For vehicles equipped with Supplemental Restraint (Air Bag) System :
Service on and around the air bag system components or wiring must be performed only by an
authorized SUZUKI dealer. Refer to “Air Bag System Components and Wiring Location View” under
“General Description” in air bag system section in order to confirm whether you are performing ser-
vice on or near the air bag system components or wiring. Please observe all WARNINGS and “Ser-
vice Precautions” under “On-Vehicle Service” in air bag system section before performing service
on or around the air bag system components or wiring. Failure to follow WARNINGS could result in
unintentional activation of the system or could render the system inoperative. Either of these two
conditions may result in severe injury.
Technical service work must be started at least 90 seconds after the ignition switch is turned to the
“LOCK” position and the negative cable is disconnected from the battery. Otherwise, the system
may be activated by reserve energy in the Sensing and Diagnostic Module (SDM).
Page 503 of 698
6A1-2 ENGINE MECHANICAL (M13 ENGINE)
GENERAL DESCRIPTION
ENGINE
The engine is water-cooled, in line 4 cylinders, 4 stroke cycle gasoline unit with its DOHC (Double overhead
camshaft) valve mechanism arranged for “V” type valve configuration and 16 valves (4 valves/one cylinder). The
double overhead camshaft is mounted over the cylinder head; it is driven from crankshaft through timing chain,
and no push rods are provided in the valve train system.
Page 504 of 698
ENGINE MECHANICAL (M13 ENGINE) 6A1-3
ENGINE LUBRICATION
The oil pump is of a trochoid type, and mounted on the crankshaft. Oil is drawn up through the oil pump strainer
and passed through the pump to the oil filter.
The filtered oil flows into 2 paths in cylinder block.
In one path, oil reaches the crankshaft journal bearings. Oil from the crankshaft journal bearings is supplied to
the connecting rod bearings by means of intersecting passages drilled in the crankshaft, and then injected from
the big end of connecting rod to lubricate piston, rings, and cylinder wall.
In other path oil goes up to the cylinder head and lubricates valves and camshafts, etc., after passing through
the internal oilway of camshafts.
An oil relief valve is provided on the oil pump. This valve starts relieving oil pressure when the pressure exceeds
about 400 kPa (4.0 kg/cm
2, 56.9 psi).