Page 489 of 698
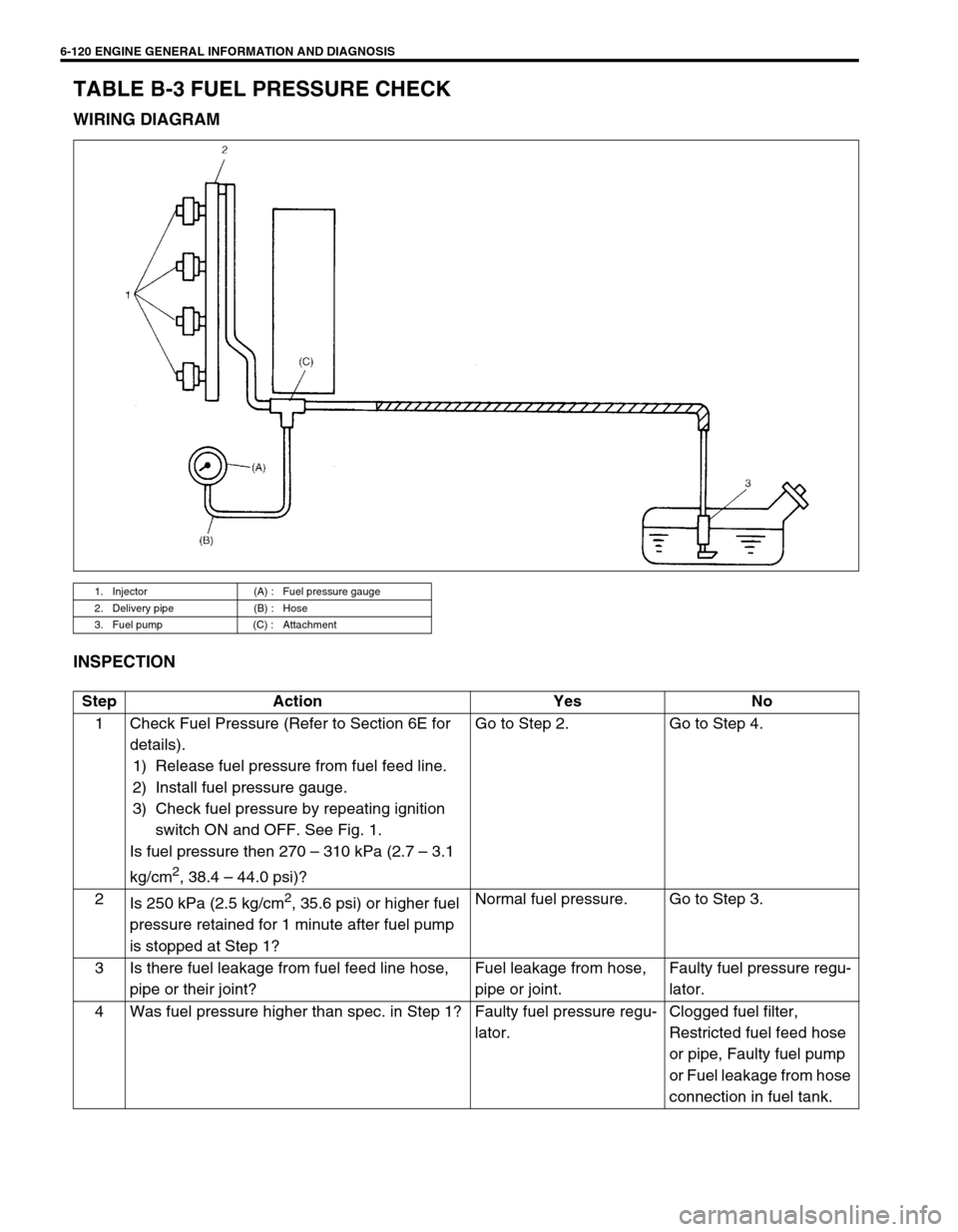
6-120 ENGINE GENERAL INFORMATION AND DIAGNOSIS
TABLE B-3 FUEL PRESSURE CHECK
WIRING DIAGRAM
INSPECTION
1. Injector (A) : Fuel pressure gauge
2. Delivery pipe (B) : Hose
3. Fuel pump (C) : Attachment
Step Action Yes No
1 Check Fuel Pressure (Refer to Section 6E for
details).
1) Release fuel pressure from fuel feed line.
2) Install fuel pressure gauge.
3) Check fuel pressure by repeating ignition
switch ON and OFF. See Fig. 1.
Is fuel pressure then 270 – 310 kPa (2.7 – 3.1
kg/cm
2, 38.4 – 44.0 psi)?Go to Step 2. Go to Step 4.
2
Is 250 kPa (2.5 kg/cm
2, 35.6 psi) or higher fuel
pressure retained for 1 minute after fuel pump
is stopped at Step 1?Normal fuel pressure. Go to Step 3.
3 Is there fuel leakage from fuel feed line hose,
pipe or their joint?Fuel leakage from hose,
pipe or joint.Faulty fuel pressure regu-
lator.
4 Was fuel pressure higher than spec. in Step 1? Faulty fuel pressure regu-
lator.Clogged fuel filter,
Restricted fuel feed hose
or pipe, Faulty fuel pump
or Fuel leakage from hose
connection in fuel tank.
Page 490 of 698
ENGINE GENERAL INFORMATION AND DIAGNOSIS 6-121
Fig. 1 for Step 1
Special tool
(A) : 09912-58441
(B) : 09912-58490
1. Fuel pressure gauge
2. 3 way joint1, (A)
2, (B)
Page 491 of 698
![SUZUKI SWIFT 2000 1.G RG413 Service Workshop Manual 6-122 ENGINE GENERAL INFORMATION AND DIAGNOSIS
TABLE B-4 IDLE AIR CONTROL SYSTEM CHECK
INSPECTION
1. IAC valve 2. Main relay 3. To TCM
[A] : Case of TYPE A is shown (See NOTE) [B] : Case of TYPE B is SUZUKI SWIFT 2000 1.G RG413 Service Workshop Manual 6-122 ENGINE GENERAL INFORMATION AND DIAGNOSIS
TABLE B-4 IDLE AIR CONTROL SYSTEM CHECK
INSPECTION
1. IAC valve 2. Main relay 3. To TCM
[A] : Case of TYPE A is shown (See NOTE) [B] : Case of TYPE B is](/manual-img/20/7606/w960_7606-490.png)
6-122 ENGINE GENERAL INFORMATION AND DIAGNOSIS
TABLE B-4 IDLE AIR CONTROL SYSTEM CHECK
INSPECTION
1. IAC valve 2. Main relay 3. To TCM
[A] : Case of TYPE A is shown (See NOTE) [B] : Case of TYPE B is shown (See NOTE)
GRN/RED
BLK/YEL
BRN/WHT
BLK/RED
BLK/RED
ECM
C41-10
C41-6
C41-5
C42 (31P) C41 (24P) G02 (17P)1 2 3 4 5 6 7 8 9
10 11 12 13 14 15 16 17 18 19 20 21
22 23 24 25 26 28 27 29 30 315 6
1 2 3 4 5 6 7
11 12
9 10 11 13 12 14 15 16
16 171 2
7 8
13 14 3 4
9 10
15 17 188
19 20 21 22 23 24
3
1
2
C42-6 C41-14 [A]
G02-6 [B]
LT BLU [A]
GRN RED [B]
NOTE:
For TYPE A and TYPE B, refer to NOTE in “ECM VOLTAGE VALUES TABLE” for applicable model.
Step Action Yes No
1 Check engine idle speed and IAC duty referring
to “Idle Speed/IAC Duty Inspection” in Section
6E1.
Is idle speed within specification?Go to Step 2. Go to Step 4.
2 Is IAC duty within specification in Step 1? Go to Step 3. Check for followings :
Vacuum leak
EVAP canister purge con-
trol system
Clog of IAC air passage
Accessory engine load
Closed throttle position
(TP sensor)
Stuck of PCV valve
3 Is engine idle speed kept specified speed even
with headlight ON?System is in good condi-
tion.Check IAC system for
operation referring to Step
2 of DTC P0505 Diag.
Flow Table.
4 Was idle speed higher than specification in
Step 1?Go to Step 5. Go to Step 8.
Page 492 of 698
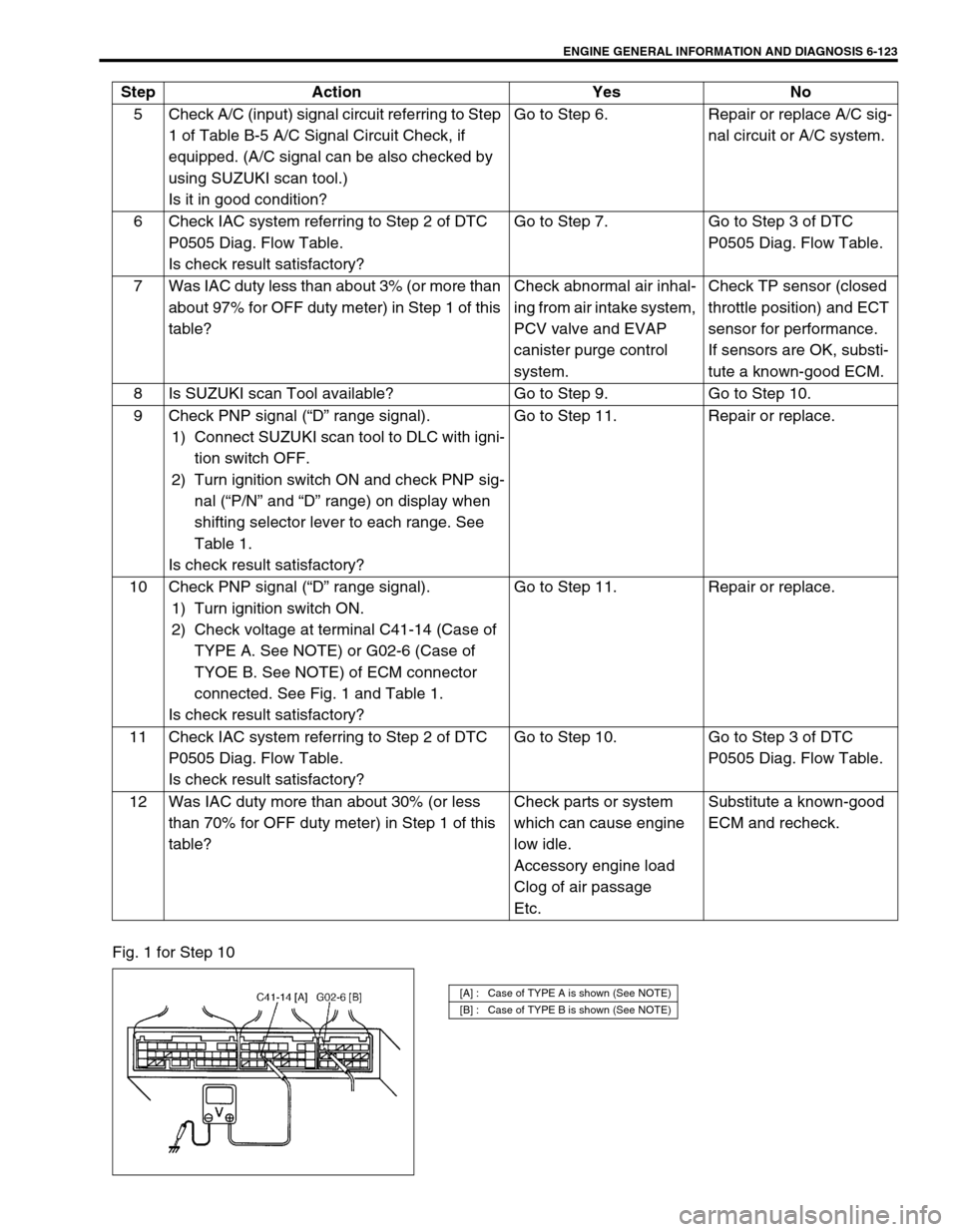
ENGINE GENERAL INFORMATION AND DIAGNOSIS 6-123
Fig. 1 for Step 105 Check A/C (input) signal circuit referring to Step
1 of Table B-5 A/C Signal Circuit Check, if
equipped. (A/C signal can be also checked by
using SUZUKI scan tool.)
Is it in good condition?Go to Step 6. Repair or replace A/C sig-
nal circuit or A/C system.
6 Check IAC system referring to Step 2 of DTC
P0505 Diag. Flow Table.
Is check result satisfactory?Go to Step 7. Go to Step 3 of DTC
P0505 Diag. Flow Table.
7 Was IAC duty less than about 3% (or more than
about 97% for OFF duty meter) in Step 1 of this
table?Check abnormal air inhal-
ing from air intake system,
PCV valve and EVAP
canister purge control
system.Check TP sensor (closed
throttle position) and ECT
sensor for performance.
If sensors are OK, substi-
tute a known-good ECM.
8 Is SUZUKI scan Tool available? Go to Step 9. Go to Step 10.
9 Check PNP signal (“D” range signal).
1) Connect SUZUKI scan tool to DLC with igni-
tion switch OFF.
2) Turn ignition switch ON and check PNP sig-
nal (“P/N” and “D” range) on display when
shifting selector lever to each range. See
Table 1.
Is check result satisfactory?Go to Step 11. Repair or replace.
10 Check PNP signal (“D” range signal).
1) Turn ignition switch ON.
2) Check voltage at terminal C41-14 (Case of
TYPE A. See NOTE) or G02-6 (Case of
TYOE B. See NOTE) of ECM connector
connected. See Fig. 1 and Table 1.
Is check result satisfactory?Go to Step 11. Repair or replace.
11 Check IAC system referring to Step 2 of DTC
P0505 Diag. Flow Table.
Is check result satisfactory?Go to Step 10. Go to Step 3 of DTC
P0505 Diag. Flow Table.
12 Was IAC duty more than about 30% (or less
than 70% for OFF duty meter) in Step 1 of this
table?Check parts or system
which can cause engine
low idle.
Accessory engine load
Clog of air passage
Etc.Substitute a known-good
ECM and recheck. Step Action Yes No
[A] : Case of TYPE A is shown (See NOTE)
[B] : Case of TYPE B is shown (See NOTE)
Page 493 of 698
6-124 ENGINE GENERAL INFORMATION AND DIAGNOSIS
Table 1 for Step 9 and 10
TABLE B-5 A/C SIGNAL CIRCUITS CHECK (VEHICLE WITH A/C)
Scan tool or voltmeter
SUZUKI SCAN TOOL
DISPLAYVOLTAGE AT C41-14
Selector lever
position“P” and “N” range P/N range 10 – 14V
“R”, “D”, “2” and “L” range D range 0 – 1V
1. Blower fan motor 3. A/C switch 5. A/C evaporator temp. sensor
2. Blower fan switch 4. A/C pressure switch 6. A/C compressor clutch
[A] : Case of TYPE A is shown (See NOTE) [B] : Case of TYPE B is shown (See NOTE)
IG2
M
ECM
PNK/BLU
YEL/GRN
PNK/GRN
WHT/BLK
ORN
PNK/BLK
G02-13
C41-16
C41-1
C42 (31P) C41 (24P) G02 (17P)1 2 3 4 5 6 7 8 9
10 11 12 13 14 15 16 17 18 19 20 21
22 23 24 25 26 28 27 29 30 315 6
1 2 3 4 5 6 7
11 12
9 10 11 13 12 14 15 16
16 171 2
7 8
13 14 3 4
9 10
15 17 188
19 20 21 22 23 24
1
234
5
6
C41-18 [A]
C42-30 [B]
G02-14 [A]
G02-1 [B]
G02-14 [B] G02-10 [A]
NOTE:
For TYPE A and TYPE B, refer to NOTE in “ECM VOLTAGE VALUES TABLE” for applicable model.
Page 494 of 698

ENGINE GENERAL INFORMATION AND DIAGNOSIS 6-125
INSPECTION
Fig. 1 for Step 1Step Action Yes No
1 Check evaporator temp. sensor resistance.
1) Disconnect ECM connectors with ignition
switch at OFF position.
2) Check resistance between G02-14 terminal
and G02-10 terminal (Case of TYPE A. See
NOTE) or between G02-1 terminal and
G02-14 terminal (Case of TYPE B. See
NOTE). See Fig. 1.
Is it within specification?
At 0°C 6.3 – 6.9 k
Ω
At 25°C 1.8 – 2.2 k
ΩGo to Step 2. Faulty A/C evaporator
temp. sensor or its circuit.
2 Check A/C switch signal.
1) Check voltage at C41-16 terminal under
each condition given below.
Ignition switch ON A/C switch OFF
: 10 – 14V
Ignition switch ON A/C switch ON
: 0 – 1V
Is check result satisfactory?Go to Step 3.“YEL/GRN” wire open or
short
Poor C41-16 terminal
connection
If wire and connection are
OK, substitute a known-
good ECM and recheck.
Go to Step 3.
3 1) Check voltage at C41-1 terminal under each
condition given below.
While engine running, A/C switch OFF
: 0 V
While engine running, A/C switch ON
: 10 – 14V
Is check result satisfactory?A/C control system cir-
cuits are in good condi-
tion.“PNK/BLK” wire open or
short
Poor C41-1 terminal con-
nection
If wire and connection are
OK, substitute a known-
good ECM and recheck.
NOTE:
When A/C evaporator thermistor temp. is below 2.5°C (36.5°F), A/C remain OFF (C41-1 terminal volt-
age become 0 – 1 V). This condition is not abnormal.
Page 495 of 698
![SUZUKI SWIFT 2000 1.G RG413 Service Workshop Manual 6-126 ENGINE GENERAL INFORMATION AND DIAGNOSIS
TABLE B-6 ELECTRIC LOAD SIGNAL CIRCUIT CHECK
INSPECTION
1. Blower fan motor 3. Rear defogger 5. To A/C switch
2. Blower fan switch 4. Position lamp
[A] : SUZUKI SWIFT 2000 1.G RG413 Service Workshop Manual 6-126 ENGINE GENERAL INFORMATION AND DIAGNOSIS
TABLE B-6 ELECTRIC LOAD SIGNAL CIRCUIT CHECK
INSPECTION
1. Blower fan motor 3. Rear defogger 5. To A/C switch
2. Blower fan switch 4. Position lamp
[A] :](/manual-img/20/7606/w960_7606-494.png)
6-126 ENGINE GENERAL INFORMATION AND DIAGNOSIS
TABLE B-6 ELECTRIC LOAD SIGNAL CIRCUIT CHECK
INSPECTION
1. Blower fan motor 3. Rear defogger 5. To A/C switch
2. Blower fan switch 4. Position lamp
[A] : Case of TYPE A is shown (See NOTE) [B] : Case of TYPE B is shown (See NOTE)
IG2
M
ECM
PNK/BLUG02-13
C42 (31P) C41 (24P) G02 (17P)1 2 3 4 5 6 7 8 9
10 11 12 13 14 15 16 17 18 19 20 21
22 23 24 25 26 28 27 29 30 315 6
1 2 3 4 5 6 7
11 12
9 10 11 13 12 14 15 16
16 171 2
7 8
13 14 3 4
9 10
15 17 188
19 20 21 22 23 24
RED/BLK [A]
IG11
+BB
43 25 1
C42-17 [A]
C41-17 [B] RED/YEL [B]
NOTE:
For TYPE A and TYPE B, refer to NOTE in “ECM VOLTAGE VALUES TABLE” for applicable model.
Step Action Yes No
1 Is SUZUKI scan tool available? Go to Step 2. Go to Step 3.
2 Check Electric Load Signal Circuit.
1) Connect SUZUKI scan tool to DLC with igni-
tion switch OFF.
2) Start engine and select “DATA LIST” mode
on scan tool.
3) Check electric load signal under following
each condition. See Fig. 1 and Table 1.
Is check result satisfactory?Electric load signal circuit
is in good condition.“RED/BLK” (Case of
TYPE A. See NOTE) or
C41-17 (Case of TYPE B.
See NOTE) and/or “PNK/
BLU” circuit open or short,
Electric load diodes mal-
function or Each electric
load circuit malfunction.
3 Check Electric Load Signal Circuit.
1) Turn ignition switch ON.
2) Check voltage at each terminals C42-17
(Case of TYPE A. See NOTE) or C41-17
(Case of TYPE B. See NOTE) and G02-13
of ECM connector connected, under above
each condition. See Fig. 2 and Table 1.
Is each voltage as specified?Electric load signal circuit
is in good condition.“RED/BLK” (Case of
TYPE A. See NOTE) or
C41-17 (Case of TYPE B.
See NOTE) and/or “PNK/
BLU” circuit open or short,
Electric load diodes mal-
function or Each electric
load circuit malfunction.
Page 496 of 698
ENGINE GENERAL INFORMATION AND DIAGNOSIS 6-127
Fig. 1 for Step 2
Fig. 2 for Step 3
Table 1 for Step 2 and 3
[A] : When using SUZUKI scan tool:
[ A]
[A] : When not using SUZUKI scan tool:
[a] : Case of TYPE A is shown (See NOTE)
[b] : Case of TYPE B is shown (See NOTE)
Scan tool or voltmeter
SUZUKI
SCAN TOOLVOLTAGE
AT C42-17VOLTAGE
AT G02-13
Ignition switch ON, Small
light, heater blower fan and
rear defogger all turnedOFF OFF 0V 10 – 14V
ON ON 10 – 14V 0V