Page 133 of 698
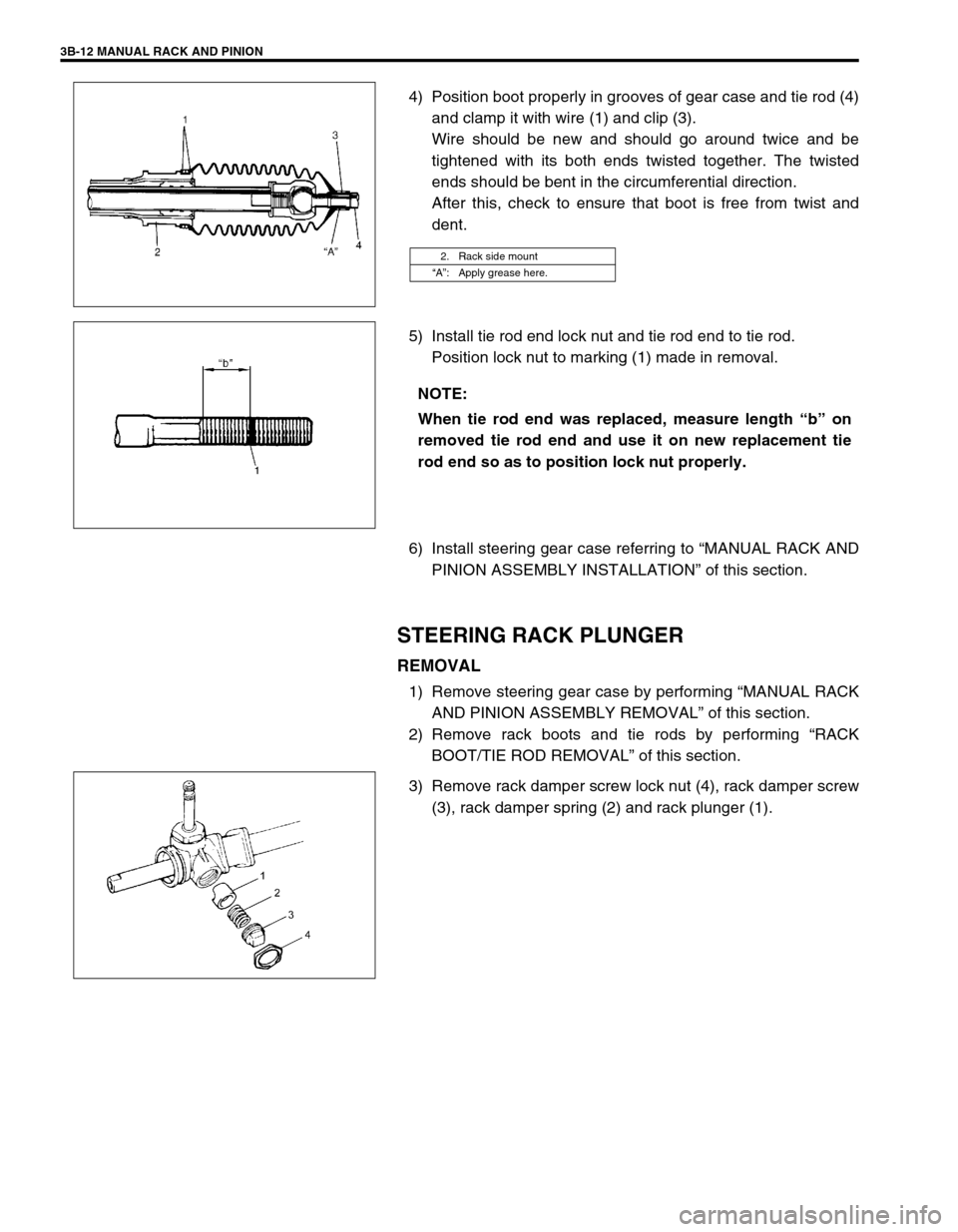
3B-12 MANUAL RACK AND PINION
4) Position boot properly in grooves of gear case and tie rod (4)
and clamp it with wire (1) and clip (3).
Wire should be new and should go around twice and be
tightened with its both ends twisted together. The twisted
ends should be bent in the circumferential direction.
After this, check to ensure that boot is free from twist and
dent.
5) Install tie rod end lock nut and tie rod end to tie rod.
Position lock nut to marking (1) made in removal.
6) Install steering gear case referring to “MANUAL RACK AND
PINION ASSEMBLY INSTALLATION” of this section.
STEERING RACK PLUNGER
REMOVAL
1) Remove steering gear case by performing “MANUAL RACK
AND PINION ASSEMBLY REMOVAL” of this section.
2) Remove rack boots and tie rods by performing “RACK
BOOT/TIE ROD REMOVAL” of this section.
3) Remove rack damper screw lock nut (4), rack damper screw
(3), rack damper spring (2) and rack plunger (1).
2. Rack side mount
“A”: Apply grease here.
NOTE:
When tie rod end was replaced, measure length “b” on
removed tie rod end and use it on new replacement tie
rod end so as to position lock nut properly.
Page 134 of 698
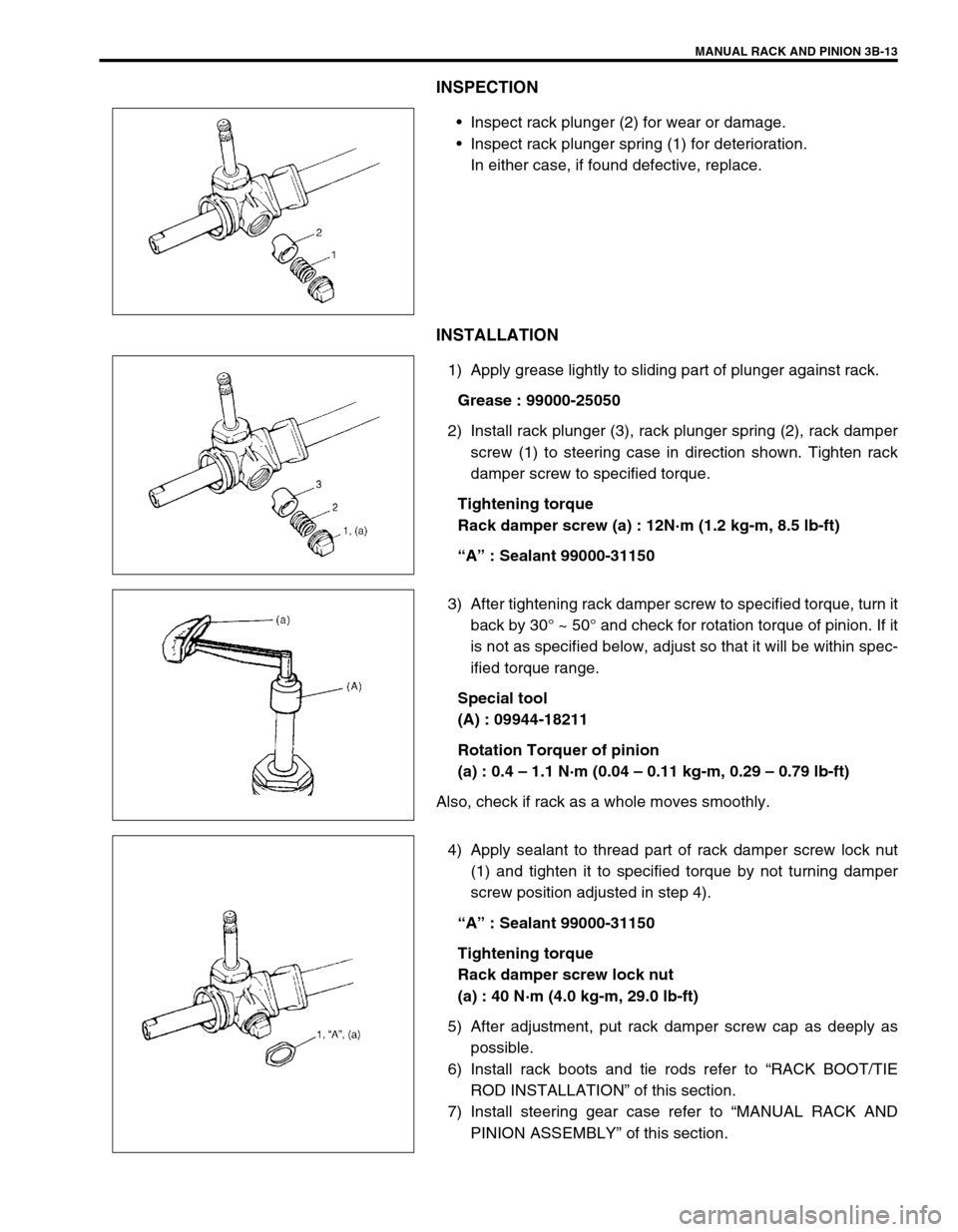
MANUAL RACK AND PINION 3B-13
INSPECTION
Inspect rack plunger (2) for wear or damage.
Inspect rack plunger spring (1) for deterioration.
In either case, if found defective, replace.
INSTALLATION
1) Apply grease lightly to sliding part of plunger against rack.
Grease : 99000-25050
2) Install rack plunger (3), rack plunger spring (2), rack damper
screw (1) to steering case in direction shown. Tighten rack
damper screw to specified torque.
Tightening torque
Rack damper screw (a) : 12N·m (1.2 kg-m, 8.5 lb-ft)
“A” : Sealant 99000-31150
3) After tightening rack damper screw to specified torque, turn it
back by 30° ~ 50° and check for rotation torque of pinion. If it
is not as specified below, adjust so that it will be within spec-
ified torque range.
Special tool
(A) : 09944-18211
Rotation Torquer of pinion
(a) : 0.4 – 1.1 N·m (0.04 – 0.11 kg-m, 0.29 – 0.79 lb-ft)
Also, check if rack as a whole moves smoothly.
4) Apply sealant to thread part of rack damper screw lock nut
(1) and tighten it to specified torque by not turning damper
screw position adjusted in step 4).
“A” : Sealant 99000-31150
Tightening torque
Rack damper screw lock nut
(a) : 40 N·m (4.0 kg-m, 29.0 lb-ft)
5) After adjustment, put rack damper screw cap as deeply as
possible.
6) Install rack boots and tie rods refer to “RACK BOOT/TIE
ROD INSTALLATION” of this section.
7) Install steering gear case refer to “MANUAL RACK AND
PINION ASSEMBLY” of this section.
Page 136 of 698
MANUAL RACK AND PINION 3B-15
INSTALLATION
1) Install new oil seal with special tool to pinion bearing plug
(1).
Special tool
(C) : 09925-98210
2) Apply grease to all around pinion teeth (2), pinion needle
bearing, gear case O-ring (4) and gear case oil seal lip (1).
Fill inside of pinion bearing plug (3) with grease.
“A” : Grease 99000-25050
3) Install pinion assembly and after applying sealant to pinion
bearing plug (5) thread as shown.
“B” : Sealant 99000-31150
4) Tighten pinion bearing plug to specified torque.
Tightening torque
Pinion bearing plug (a) : 95 N·m (9.5 kg-m, 69.0 lb-ft)
Special tool
(D) : 09944-26011
5) Install rack plunger in STEERING RACK PLUNGER.
STEERING RACK
REMOVAL
1) Remove steering gear case.
2) Remove boot wires (2) and clips (1).
3) Move both boots toward tie rod end.
Page 138 of 698
MANUAL RACK AND PINION 3B-17
5) Before installing boot to steering rack housing (1), make sure
that rack side mount (2) is positioned as shown. Install tie
rods to rack by performing Steps 1) – 6) in RACK BOOT/TIE
ROD INSTALLATION of this section.
Rack side mount installing position
“a” : 5.1 mm (0.2 in.)
PINION BEARING
REMOVAL
1) Remove rack from steering gear case, referring to STEER-
ING RACK REMOVAL of this section.
2) Remove pinion bearing (1) from gear case with special tools
as shown.
Special tool
(A) : 09921-20200
(B) : 09930-30102
INSTALLATION
1) Apply grease to rollers of pinion bearing.
2) Press-fit pinion bearing (1) into gear case with special tool as
shown.
After press-fitting, make sure that bearing rollers are
installed properly.
Special tool
(A) : 09943-88211
3) Follow Steps 1) – 5) in STEERING RACK INSTALLATION of
this section to complete installation.
Page 140 of 698

MANUAL RACK AND PINION 3B-19
INSTALLATION
1) Apply grease lightly to entire inner surface of bushing.
2) Press-fit bushing as far into rack housing as shown by using
special tool.
Special tool
(B) : 09943-78210
Bush installing position
“a” : 4.5 – 5.5 mm (0.18 – 0.22 in.)
3) Install snap ring.
4) Follow Steps 1) – 5) in STEERING RACK INSTALLATION of
this section to complete installation.
REQUIRED SERVICE MATERIAL
CAUTION:
Inside of bushing is coated with special coating. As it is
damageable, be sure to use special tool and special care
not to cause damage to inside of bushing when press-fit-
ting it.
MaterialRecommended SUZUKI product
(Part Number)Use
Lithium Grease
(Should be applicable
for –40C° ~ 130°C)SUZUKI SUPER GREASE (E)
(99000-25050)Sliding part of rack against steering housing (All
around rack plunger, rack bushing and rack)
Sliding part against steering pinion
(Oil seal lip, needle bearing)
Steering rack and pinion gear teeth
Filled into pinion bearing cap
Contacting parts of tie-rod and rack side boots
Rack end ball joint
Sealant SUZUKI BOND NO. 1207C
(99000-31150)Rack damper screw nut
Pinion bearing plug thread
Page 254 of 698
FRONT DRIVE SHAFT 4A-1
6F1
6F2
6G
6H
6K
7A
7A1
7B1
7C1
7D
7E
7F
4A
8C
8D
8E
9
10
10A
10B
SECTION 4A
FRONT DRIVE SHAFT
CONTENTS
GENERAL DESCRIPTION .............................. 4A-2
COMPONENT .............................................. 4A-2
DIAGNOSIS ..................................................... 4A-2
DIAGNOSIS TABLE ..................................... 4A-2
DRIVE SHAFT BOOT CHECK ..................... 4A-2ON-VEHICLE SERVICE .................................. 4A-3
DRIVE SHAFT ASSEMBLY ......................... 4A-4
TIGHTENING TORQUE SPECIFICATION.... 4A-16
REQUIRED SERVICE MATERIAL................ 4A-16
SPECIAL TOOL ............................................ 4A-16
Page 255 of 698
4A-2 FRONT DRIVE SHAFT
GENERAL DESCRIPTION
COMPONENT
A constant velocity ball joint is used on the wheel side of front drive shaft. For right side drive shaft of 2WD vehi-
cle, a constant velocity tripod joint on the differential side. For left side drive shaft of every type vehicles and
right side drive shaft of 4WD vehicle, a constant velocity double offset joint is used on the differential or transfer
side. The drive shaft can slide through the tripod joint or the double offset joint in the extension/contraction direc-
tion.
DIAGNOSIS
DIAGNOSIS TABLE
DRIVE SHAFT BOOT CHECK
Inspect drive shaft boot for tear.
If even a small tear is noted, replace with new one. Condition Possible Cause Correction
Abnormal Noise
Worn or breakage drive shaft joint Replace.
Worn or breakage center bearing Replace.
Page 256 of 698
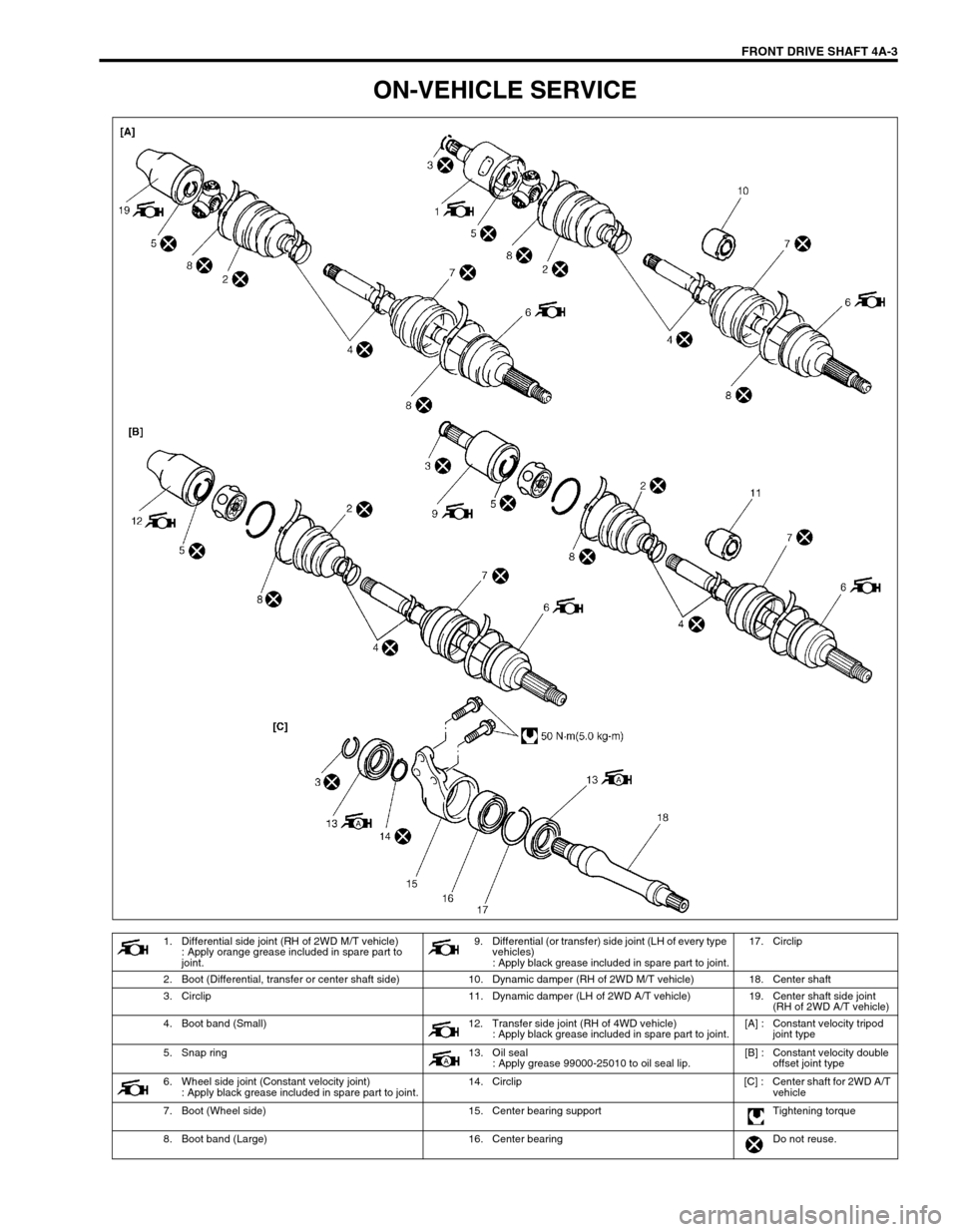
FRONT DRIVE SHAFT 4A-3
ON-VEHICLE SERVICE
1. Differential side joint (RH of 2WD M/T vehicle)
: Apply orange grease included in spare part to
joint.9. Differential (or transfer) side joint (LH of every type
vehicles)
: Apply black grease included in spare part to joint.17. Circlip
2. Boot (Differential, transfer or center shaft side) 10. Dynamic damper (RH of 2WD M/T vehicle) 18. Center shaft
3. Circlip 11. Dynamic damper (LH of 2WD A/T vehicle) 19. Center shaft side joint
(RH of 2WD A/T vehicle)
4. Boot band (Small) 12. Transfer side joint (RH of 4WD vehicle)
: Apply black grease included in spare part to joint.[A] : Constant velocity tripod
joint type
5. Snap ring 13. Oil seal
: Apply grease 99000-25010 to oil seal lip.[B] : Constant velocity double
offset joint type
6. Wheel side joint (Constant velocity joint)
: Apply black grease included in spare part to joint.14. Circlip [C] : Center shaft for 2WD A/T
vehicle
7. Boot (Wheel side) 15. Center bearing support Tightening torque
8. Boot band (Large) 16. Center bearing Do not reuse.