Page 48 of 558
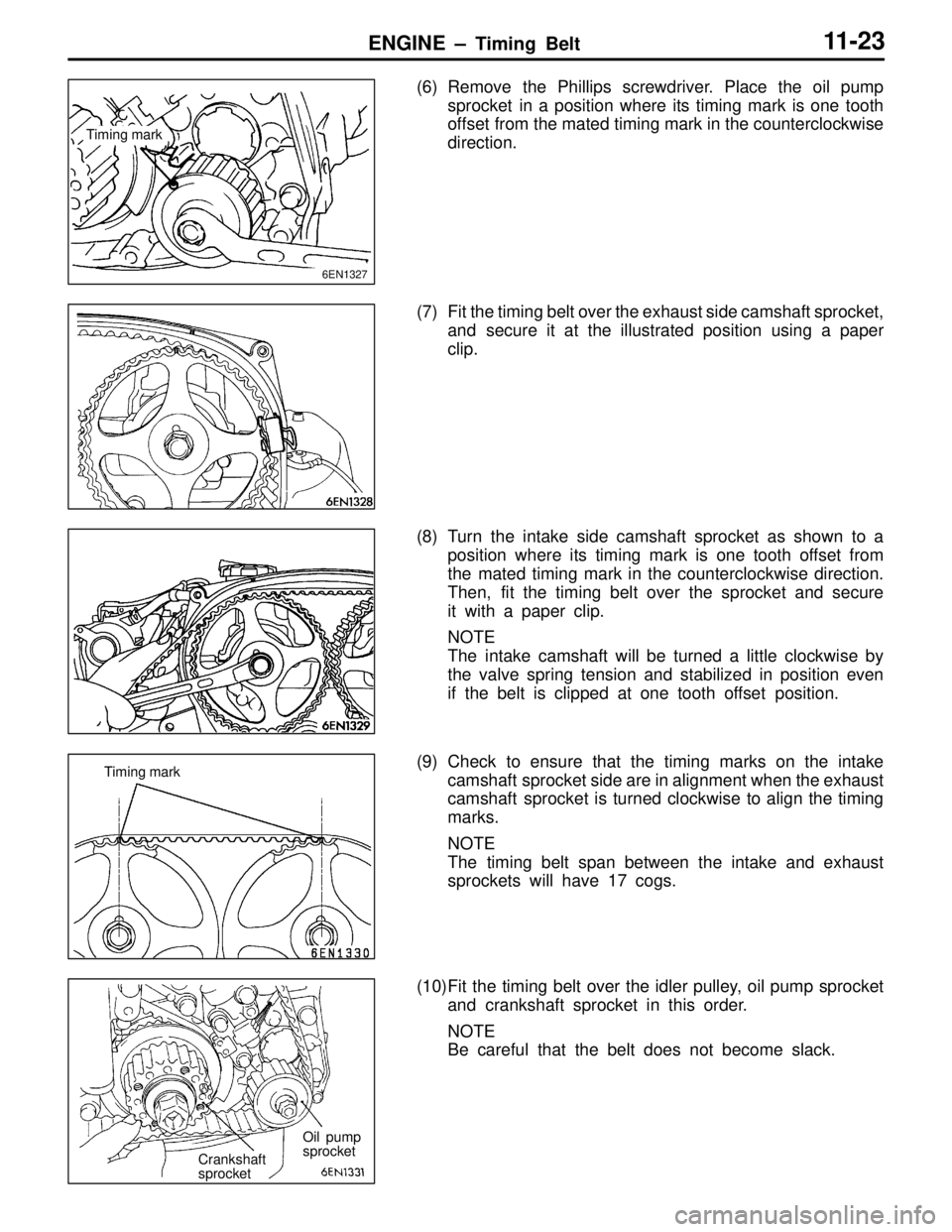
ENGINE – Timing Belt11-23
(6) Remove the Phillips screwdriver. Place the oil pump
sprocket in a position where its timing mark is one tooth
offset from the mated timing mark in the counterclockwise
direction.
(7) Fit the timing belt over the exhaust side camshaft sprocket,
and secure it at the illustrated position using a paper
clip.
(8) Turn the intake side camshaft sprocket as shown to a
position where its timing mark is one tooth offset from
the mated timing mark in the counterclockwise direction.
Then, fit the timing belt over the sprocket and secure
it with a paper clip.
NOTE
The intake camshaft will be turned a little clockwise by
the valve spring tension and stabilized in position even
if the belt is clipped at one tooth offset position.
(9) Check to ensure that the timing marks on the intake
camshaft sprocket side are in alignment when the exhaust
camshaft sprocket is turned clockwise to align the timing
marks.
NOTE
The timing belt span between the intake and exhaust
sprockets will have 17 cogs.
(10)Fit the timing belt over the idler pulley, oil pump sprocket
and crankshaft sprocket in this order.
NOTE
Be careful that the belt does not become slack.
Timing mark
6EN1327
Timing mark
Crankshaft
sprocketOil pump
sprocket
Page 49 of 558
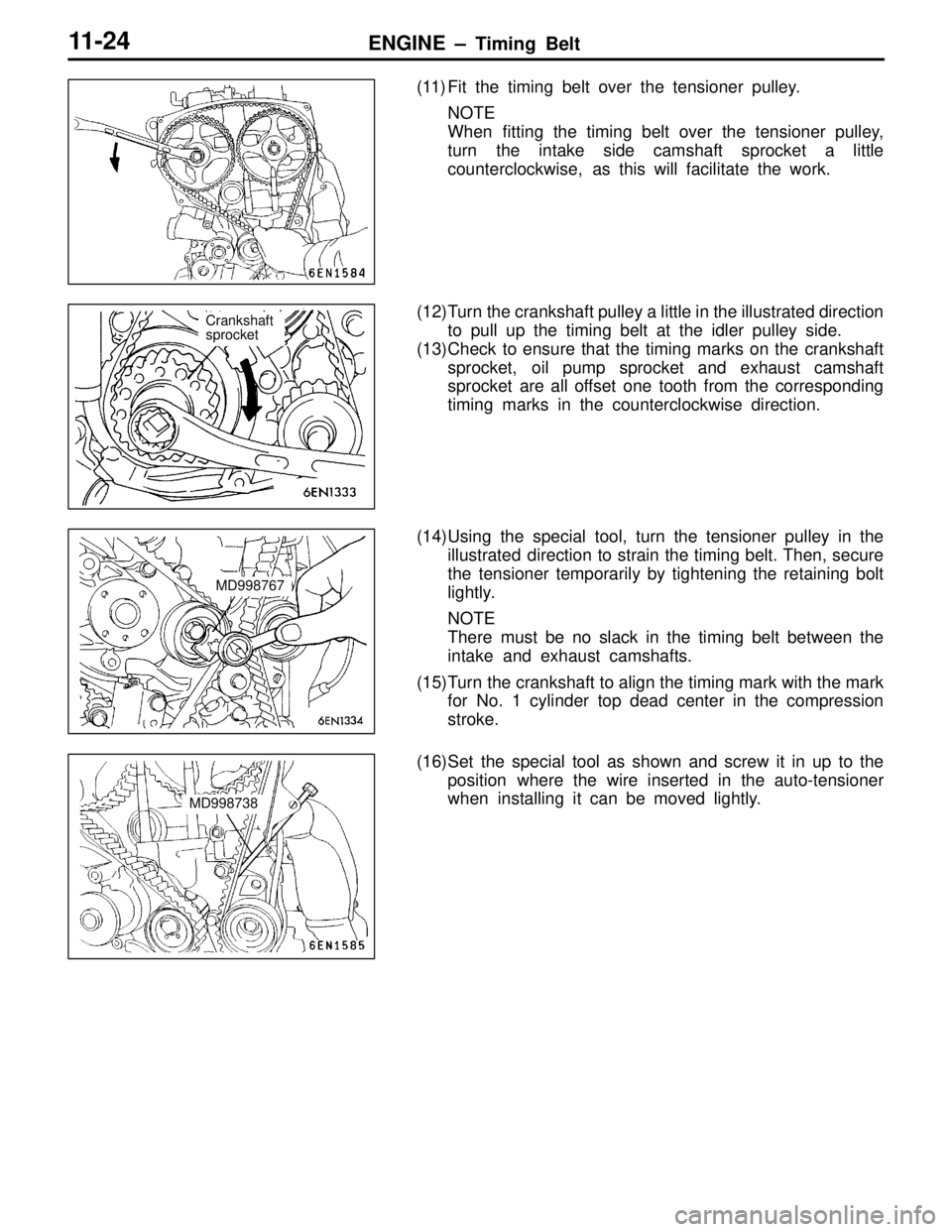
ENGINE – Timing Belt11-24
(11) Fit the timing belt over the tensioner pulley.
NOTE
When fitting the timing belt over the tensioner pulley,
turn the intake side camshaft sprocket a little
counterclockwise, as this will facilitate the work.
(12)Turn the crankshaft pulley a little in the illustrated direction
to pull up the timing belt at the idler pulley side.
(13)Check to ensure that the timing marks on the crankshaft
sprocket, oil pump sprocket and exhaust camshaft
sprocket are all offset one tooth from the corresponding
timing marks in the counterclockwise direction.
(14)Using the special tool, turn the tensioner pulley in the
illustrated direction to strain the timing belt. Then, secure
the tensioner temporarily by tightening the retaining bolt
lightly.
NOTE
There must be no slack in the timing belt between the
intake and exhaust camshafts.
(15)Turn the crankshaft to align the timing mark with the mark
for No. 1 cylinder top dead center in the compression
stroke.
(16)Set the special tool as shown and screw it in up to the
position where the wire inserted in the auto-tensioner
when installing it can be moved lightly.
Crankshaft
sprocket
MD998767
MD998738
Page 50 of 558
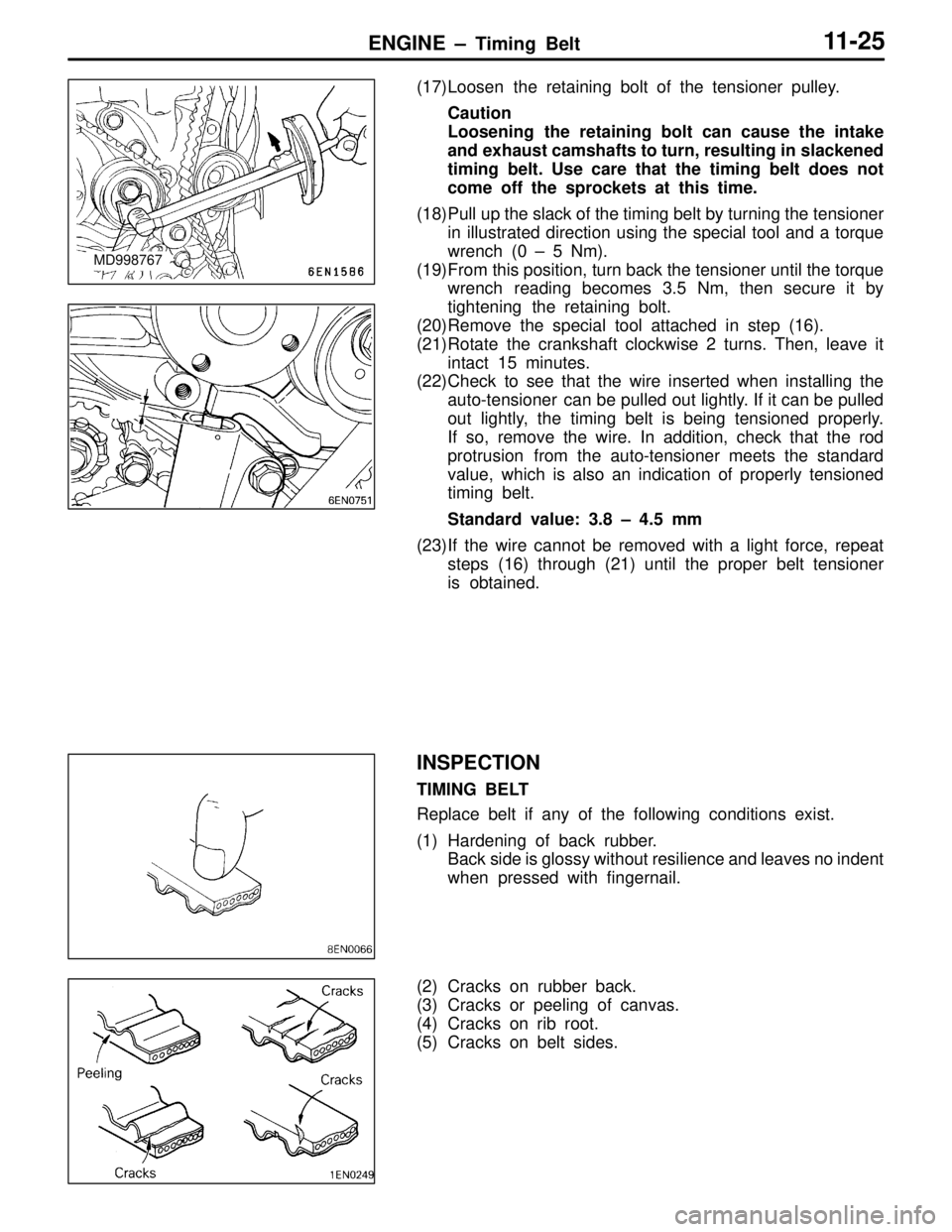
ENGINE – Timing Belt11-25
(17)Loosen the retaining bolt of the tensioner pulley.
Caution
Loosening the retaining bolt can cause the intake
and exhaust camshafts to turn, resulting in slackened
timing belt. Use care that the timing belt does not
come off the sprockets at this time.
(18)Pull up the slack of the timing belt by turning the tensioner
in illustrated direction using the special tool and a torque
wrench (0 – 5 Nm).
(19)From this position, turn back the tensioner until the torque
wrench reading becomes 3.5 Nm, then secure it by
tightening the retaining bolt.
(20)Remove the special tool attached in step (16).
(21)Rotate the crankshaft clockwise 2 turns. Then, leave it
intact 15 minutes.
(22)Check to see that the wire inserted when installing the
auto-tensioner can be pulled out lightly. If it can be pulled
out lightly, the timing belt is being tensioned properly.
If so, remove the wire. In addition, check that the rod
protrusion from the auto-tensioner meets the standard
value, which is also an indication of properly tensioned
timing belt.
Standard value: 3.8 – 4.5 mm
(23)If the wire cannot be removed with a light force, repeat
steps (16) through (21) until the proper belt tensioner
is obtained.
INSPECTION
TIMING BELT
Replace belt if any of the following conditions exist.
(1) Hardening of back rubber.
Back side is glossy without resilience and leaves no indent
when pressed with fingernail.
(2) Cracks on rubber back.
(3) Cracks or peeling of canvas.
(4) Cracks on rib root.
(5) Cracks on belt sides.
MD998767
Page 51 of 558
ENGINE – Timing Belt11-26
(6) Abnormal wear of belt sides. The sides are normal if
they are sharp as if cut by a knife.
(7) Abnormal wear on teeth.
(8) Missing tooth.
AUTO TENSIONER
(1) Check the auto tensioner for possible leaks and replace
as necessary.
(2) Check the rod end for wear or damage and replace as
necessary.
(3) Measure the rod protrusion. If it is out of specification,
replace the auto tensioner.
Standard value: 12 mm
(4) Press the rod with a force of 98 to 196 N and measure
its protrusion.
(5) If the measured value is 1 mm or more shorter than the
value obtained in step (3), replace the auto tensioner.
12 mm
98 to 196 N
Movement
Page 53 of 558
ENGINE – Fuel and Emission Control Parts11-28
INSTALLATION SERVICE POINTS
AINJECTORS INSTALLATION
(1) Before installing an injector, the rubber O-ring must be
lubricated with a drop of clean engine oil to aid in
installation.
(2) Install injector top end. Be careful not to damage O-ring
during installation.
BFUEL PRESSURE REGULATOR INSTALLATION
(1) Apply a small amount of new engine oil to the O-ring.
Insert the fuel pressure regulator into the delivery pipe
being careful not to damage the O-ring.
Caution
Be sure not to let engine oil get into the delivery
pipe.
(2) Check that the fuel pressure regulator turns smoothly.
If it does not turn smoothly, the O-ring may be trapped.
Remove the fuel pressure regulator and check the O-ring
for damage, and then re-insert it into the delivery pipe
and check once again.
CGASKET INSTALLATION
Position the projection as shown in the illustration.
1EN0388
Grommet
O-ring
Projection
Page 63 of 558
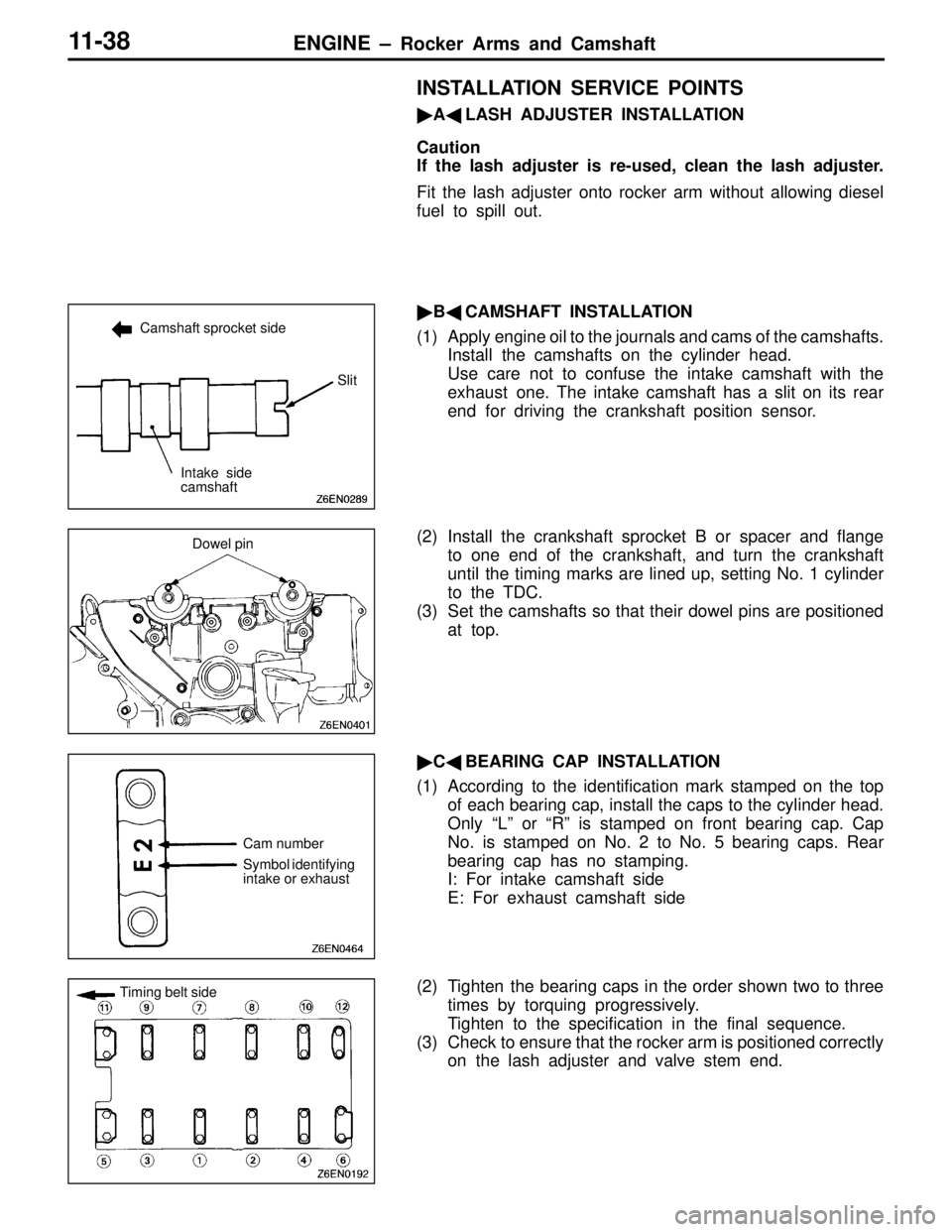
ENGINE – Rocker Arms and Camshaft11-38
INSTALLATION SERVICE POINTS
ALASH ADJUSTER INSTALLATION
Caution
If the lash adjuster is re-used, clean the lash adjuster.
Fit the lash adjuster onto rocker arm without allowing diesel
fuel to spill out.
BCAMSHAFT INSTALLATION
(1) Apply engine oil to the journals and cams of the camshafts.
Install the camshafts on the cylinder head.
Use care not to confuse the intake camshaft with the
exhaust one. The intake camshaft has a slit on its rear
end for driving the crankshaft position sensor.
(2) Install the crankshaft sprocket B or spacer and flange
to one end of the crankshaft, and turn the crankshaft
until the timing marks are lined up, setting No. 1 cylinder
to the TDC.
(3) Set the camshafts so that their dowel pins are positioned
at top.
CBEARING CAP INSTALLATION
(1) According to the identification mark stamped on the top
of each bearing cap, install the caps to the cylinder head.
Only “L” or “R” is stamped on front bearing cap. Cap
No. is stamped on No. 2 to No. 5 bearing caps. Rear
bearing cap has no stamping.
I: For intake camshaft side
E: For exhaust camshaft side
(2) Tighten the bearing caps in the order shown two to three
times by torquing progressively.
Tighten to the specification in the final sequence.
(3) Check to ensure that the rocker arm is positioned correctly
on the lash adjuster and valve stem end.
Camshaft sprocket side
Slit
Intake side
camshaft
Dowel pin
Cam number
Symbol identifying
intake or exhaust
Timing belt side
Page 64 of 558
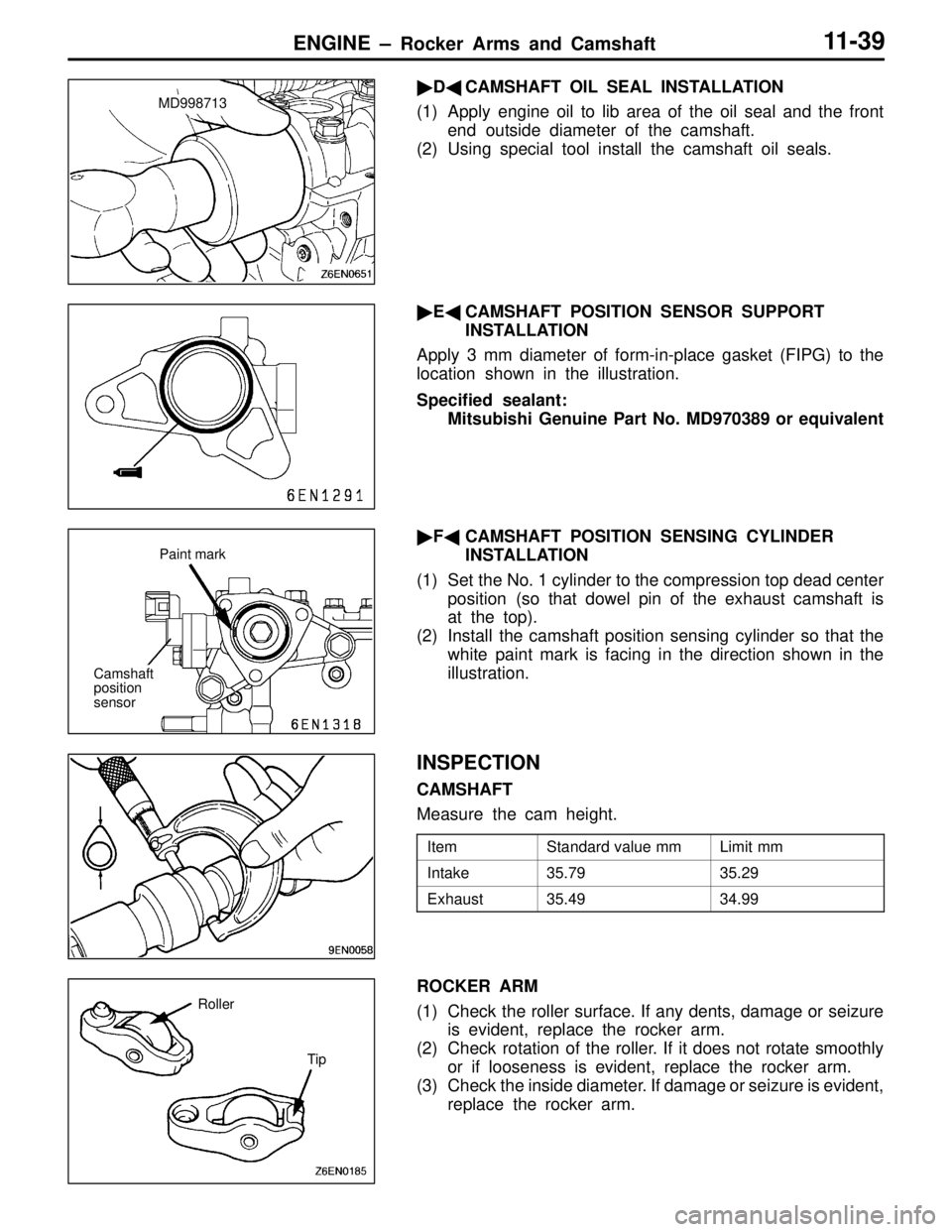
ENGINE – Rocker Arms and Camshaft11-39
DCAMSHAFT OIL SEAL INSTALLATION
(1) Apply engine oil to lib area of the oil seal and the front
end outside diameter of the camshaft.
(2) Using special tool install the camshaft oil seals.
ECAMSHAFT POSITION SENSOR SUPPORT
INSTALLATION
Apply 3 mm diameter of form-in-place gasket (FIPG) to the
location shown in the illustration.
Specified sealant:
Mitsubishi Genuine Part No. MD970389 or equivalent
FCAMSHAFT POSITION SENSING CYLINDER
INSTALLATION
(1) Set the No. 1 cylinder to the compression top dead center
position (so that dowel pin of the exhaust camshaft is
at the top).
(2) Install the camshaft position sensing cylinder so that the
white paint mark is facing in the direction shown in the
illustration.
INSPECTION
CAMSHAFT
Measure the cam height.
ItemStandard value mmLimit mm
Intake35.7935.29
Exhaust35.4934.99
ROCKER ARM
(1) Check the roller surface. If any dents, damage or seizure
is evident, replace the rocker arm.
(2) Check rotation of the roller. If it does not rotate smoothly
or if looseness is evident, replace the rocker arm.
(3) Check the inside diameter. If damage or seizure is evident,
replace the rocker arm.
MD998713
Camshaft
position
sensorPaint mark
Roller
Tip
Page 67 of 558
ENGINE – Rocker Arms and Camshaft11-42
(9) Remove the lash adjuster from the container, then stand
the lash adjuster with its plunger at the top. Push the
plunger firmly and check that it does not move. Also,
check that the lash adjuster’s height matches that of a
new lash adjuster.
NOTE
If lash adjuster contracts, perform the operations (7)
through (9) again to fill it with diesel fuel completely.
Replace the lash adjuster if it still contracts after performing
these steps.
(10)Stand the lash adjuster upright to prevent diesel fuel from
spilling out. Do not allow the lash adjuster to become
contaminated by dirt or other foreign matter. Fit the lash
adjuster onto the engine as soon as possible.