Page 89 of 558
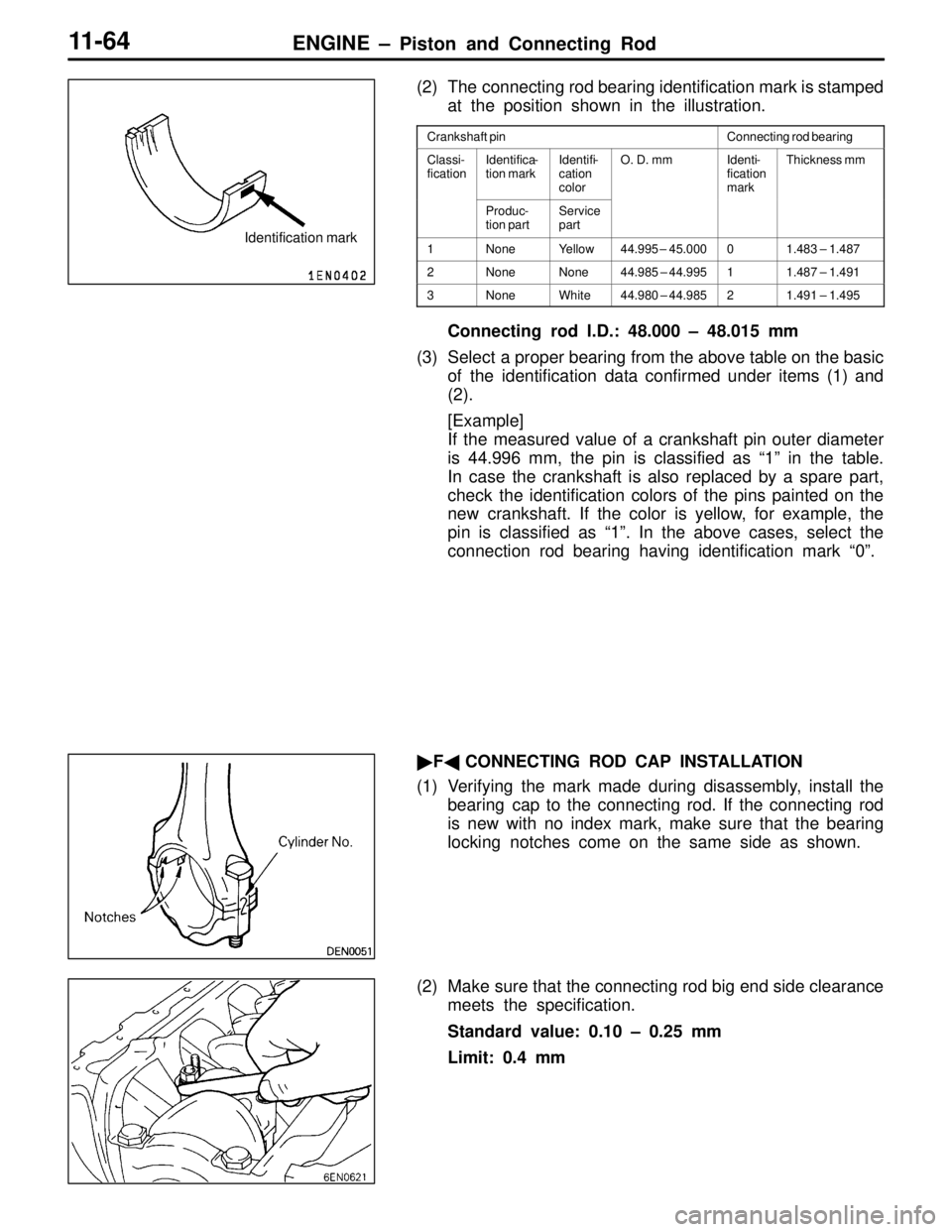
ENGINE – Piston and Connecting Rod11-64
(2) The connecting rod bearing identification mark is stamped
at the position shown in the illustration.
Crankshaft pinConnecting rod bearing
Classi-
ficationIdentifica-
tion markIdentifi-
cation
colorO. D. mmIdenti-
fication
markThickness mm
Produc-
tion partService
part
1NoneYellow44.995 – 45.00001.483 – 1.487
2NoneNone44.985 – 44.99511.487 – 1.491
3NoneWhite44.980 – 44.98521.491 – 1.495
Connecting rod I.D.: 48.000 – 48.015 mm
(3) Select a proper bearing from the above table on the basic
of the identification data confirmed under items (1) and
(2).
[Example]
If the measured value of a crankshaft pin outer diameter
is 44.996 mm, the pin is classified as “1” in the table.
In case the crankshaft is also replaced by a spare part,
check the identification colors of the pins painted on the
new crankshaft. If the color is yellow, for example, the
pin is classified as “1”. In the above cases, select the
connection rod bearing having identification mark “0”.
FCONNECTING ROD CAP INSTALLATION
(1) Verifying the mark made during disassembly, install the
bearing cap to the connecting rod. If the connecting rod
is new with no index mark, make sure that the bearing
locking notches come on the same side as shown.
(2) Make sure that the connecting rod big end side clearance
meets the specification.
Standard value: 0.10 – 0.25 mm
Limit: 0.4 mm
Identification mark
Page 90 of 558
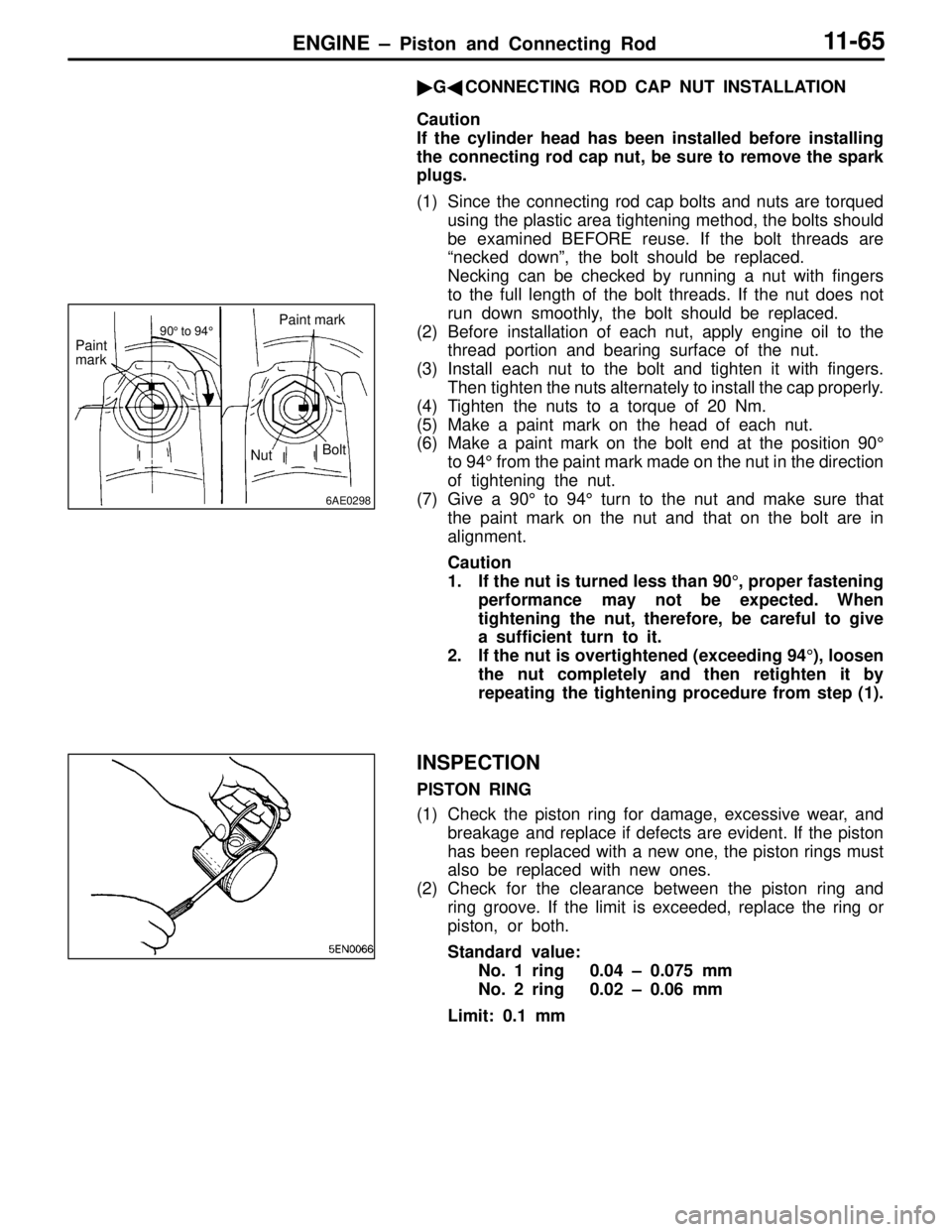
ENGINE – Piston and Connecting Rod11-65
GCONNECTING ROD CAP NUT INSTALLATION
Caution
If the cylinder head has been installed before installing
the connecting rod cap nut, be sure to remove the spark
plugs.
(1) Since the connecting rod cap bolts and nuts are torqued
using the plastic area tightening method, the bolts should
be examined BEFORE reuse. If the bolt threads are
“necked down”, the bolt should be replaced.
Necking can be checked by running a nut with fingers
to the full length of the bolt threads. If the nut does not
run down smoothly, the bolt should be replaced.
(2) Before installation of each nut, apply engine oil to the
thread portion and bearing surface of the nut.
(3) Install each nut to the bolt and tighten it with fingers.
Then tighten the nuts alternately to install the cap properly.
(4) Tighten the nuts to a torque of 20 Nm.
(5) Make a paint mark on the head of each nut.
(6) Make a paint mark on the bolt end at the position 90°
to 94° from the paint mark made on the nut in the direction
of tightening the nut.
(7) Give a 90° to 94° turn to the nut and make sure that
the paint mark on the nut and that on the bolt are in
alignment.
Caution
1. If the nut is turned less than 90°, proper fastening
performance may not be expected. When
tightening the nut, therefore, be careful to give
a sufficient turn to it.
2. If the nut is overtightened (exceeding 94°), loosen
the nut completely and then retighten it by
repeating the tightening procedure from step (1).
INSPECTION
PISTON RING
(1) Check the piston ring for damage, excessive wear, and
breakage and replace if defects are evident. If the piston
has been replaced with a new one, the piston rings must
also be replaced with new ones.
(2) Check for the clearance between the piston ring and
ring groove. If the limit is exceeded, replace the ring or
piston, or both.
Standard value:
No. 1 ring 0.04 – 0.075 mm
No. 2 ring 0.02 – 0.06 mm
Limit: 0.1 mm
6AE0298
90° to 94°Paint mark
Paint
mark
NutBolt
Page 92 of 558
ENGINE – Crankshaft and Flywheel11-67
CRANKSHAFT AND FLYWHEEL
REMOVAL AND INSTALLATION
Apply engine oil to all
moving parts before
installation.
1 2
3
4 56
78 910 11 12
13 1415
25 Nm + 9011 Nm132 Nm
9 Nm
11 Nm
32 Nm11 Nm
Removal steps
1. Flywheel bolt
2. Flywheel
3. Rear plate
4. Bell housing cover
E5. Oil seal case
D6. Oil seal
C7. Beam bearing cap bolt
C8. Beam bearing capB9. Crankshaft bearing lower
10. Crankshaft
B11. Crankshaft bearing upper
A12. Crankshaft thrust bearing
13. Check valve
14. Oil jet
15. Cylinder block
Page 94 of 558
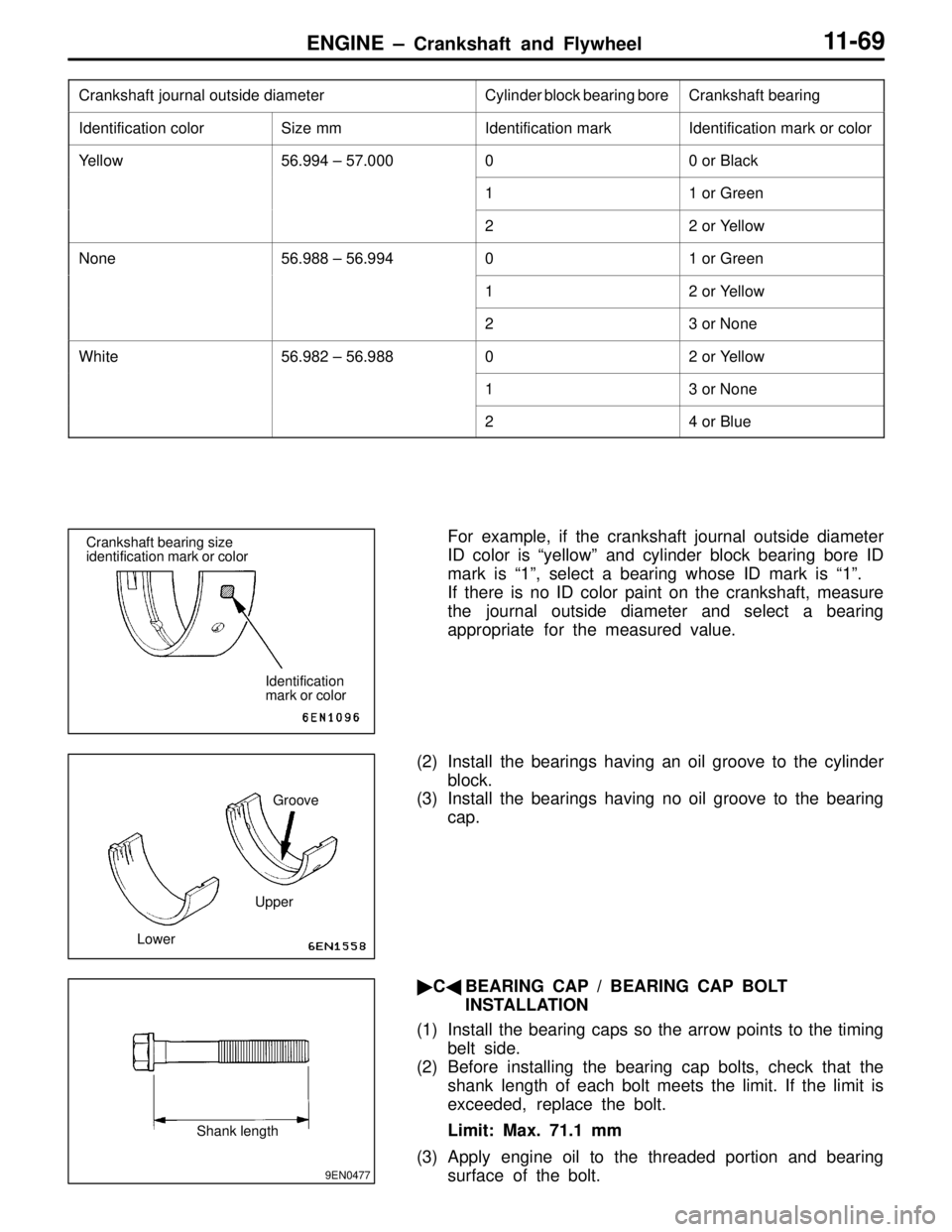
ENGINE – Crankshaft and Flywheel11-69
Crankshaft journal outside diameterCylinder block bearing boreCrankshaft bearing
Identification colorSize mmIdentification markIdentification mark or color
Yellow56.994 – 57.00000 or Black
11 or Green
22 or Yellow
None56.988 – 56.99401 or Green
12 or Yellow
23 or None
White56.982 – 56.98802 or Yellow
13 or None
24 or Blue
For example, if the crankshaft journal outside diameter
ID color is “yellow” and cylinder block bearing bore ID
mark is “1”, select a bearing whose ID mark is “1”.
If there is no ID color paint on the crankshaft, measure
the journal outside diameter and select a bearing
appropriate for the measured value.
(2) Install the bearings having an oil groove to the cylinder
block.
(3) Install the bearings having no oil groove to the bearing
cap.
CBEARING CAP / BEARING CAP BOLT
INSTALLATION
(1) Install the bearing caps so the arrow points to the timing
belt side.
(2) Before installing the bearing cap bolts, check that the
shank length of each bolt meets the limit. If the limit is
exceeded, replace the bolt.
Limit: Max. 71.1 mm
(3) Apply engine oil to the threaded portion and bearing
surface of the bolt.Crankshaft bearing size
identification mark or color
Identification
mark or color
UpperGroove
Lower
9EN0477
Shank length
Page 96 of 558
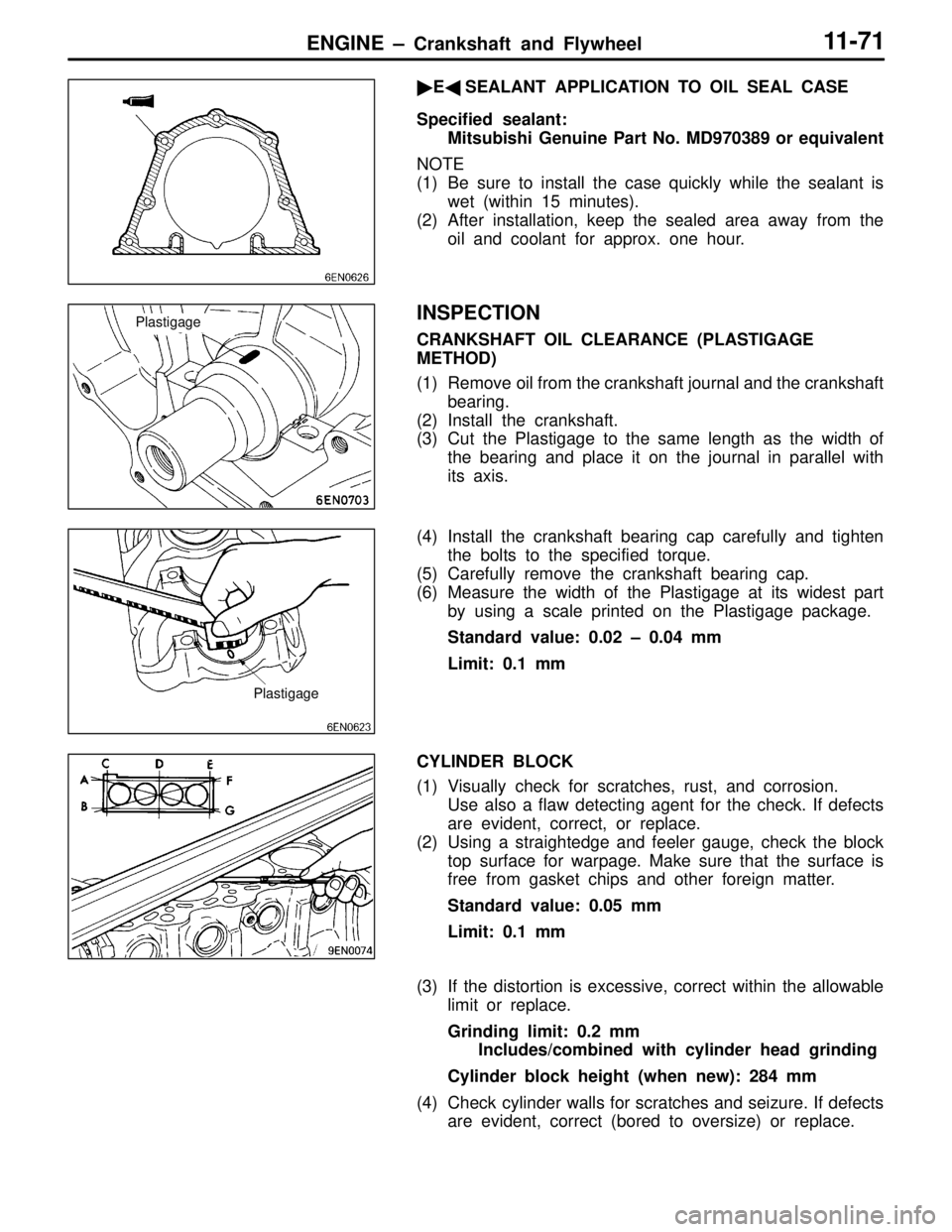
ENGINE – Crankshaft and Flywheel11-71
ESEALANT APPLICATION TO OIL SEAL CASE
Specified sealant:
Mitsubishi Genuine Part No. MD970389 or equivalent
NOTE
(1) Be sure to install the case quickly while the sealant is
wet (within 15 minutes).
(2) After installation, keep the sealed area away from the
oil and coolant for approx. one hour.
INSPECTION
CRANKSHAFT OIL CLEARANCE (PLASTIGAGE
METHOD)
(1) Remove oil from the crankshaft journal and the crankshaft
bearing.
(2) Install the crankshaft.
(3) Cut the Plastigage to the same length as the width of
the bearing and place it on the journal in parallel with
its axis.
(4) Install the crankshaft bearing cap carefully and tighten
the bolts to the specified torque.
(5) Carefully remove the crankshaft bearing cap.
(6) Measure the width of the Plastigage at its widest part
by using a scale printed on the Plastigage package.
Standard value: 0.02 – 0.04 mm
Limit: 0.1 mm
CYLINDER BLOCK
(1) Visually check for scratches, rust, and corrosion.
Use also a flaw detecting agent for the check. If defects
are evident, correct, or replace.
(2) Using a straightedge and feeler gauge, check the block
top surface for warpage. Make sure that the surface is
free from gasket chips and other foreign matter.
Standard value: 0.05 mm
Limit: 0.1 mm
(3) If the distortion is excessive, correct within the allowable
limit or replace.
Grinding limit: 0.2 mm
Includes/combined with cylinder head grinding
Cylinder block height (when new): 284 mm
(4) Check cylinder walls for scratches and seizure. If defects
are evident, correct (bored to oversize) or replace.
Plastigage
Plastigage
Page 97 of 558
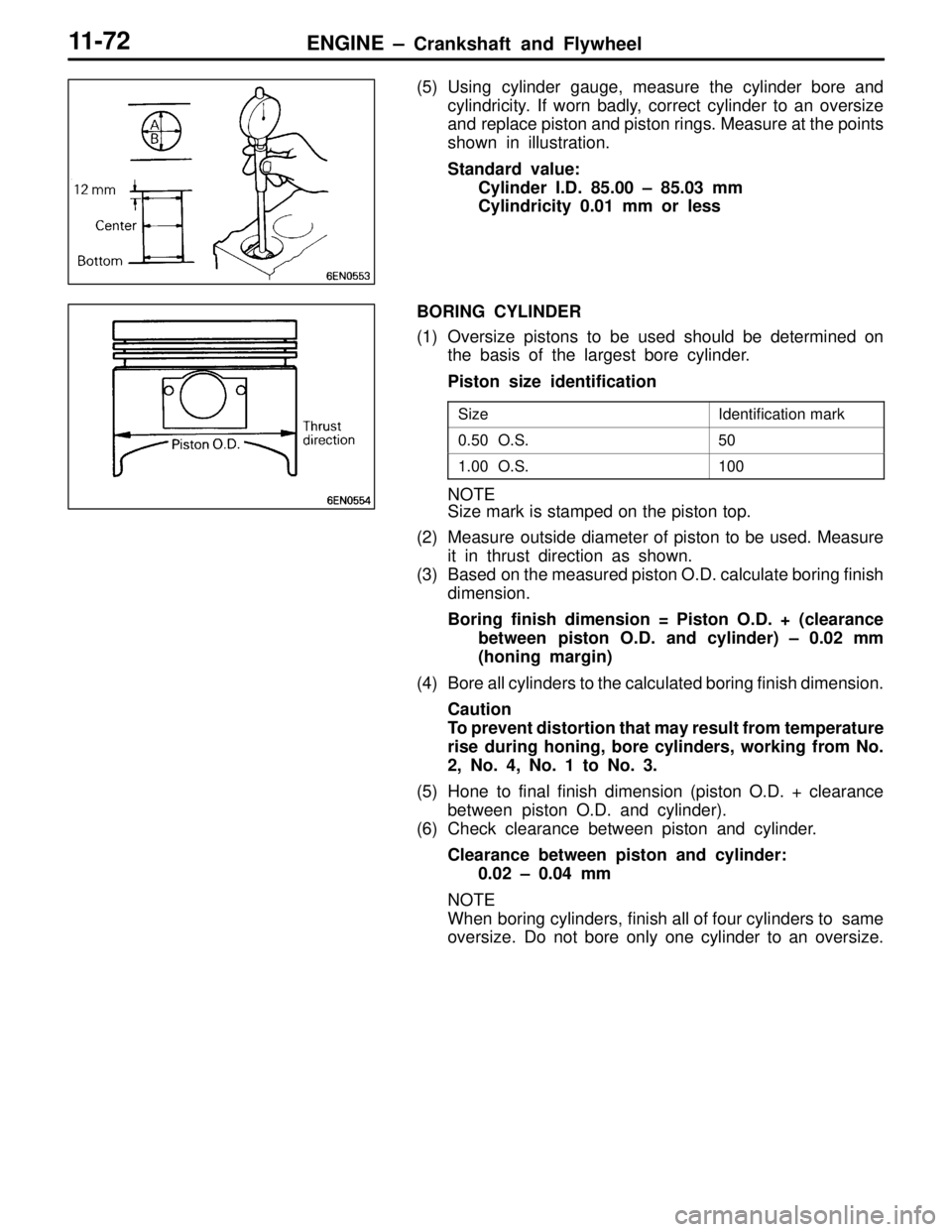
ENGINE – Crankshaft and Flywheel11-72
(5) Using cylinder gauge, measure the cylinder bore and
cylindricity. If worn badly, correct cylinder to an oversize
and replace piston and piston rings. Measure at the points
shown in illustration.
Standard value:
Cylinder I.D. 85.00 – 85.03 mm
Cylindricity 0.01 mm or less
BORING CYLINDER
(1) Oversize pistons to be used should be determined on
the basis of the largest bore cylinder.
Piston size identification
SizeIdentification mark
0.50 O.S.50
1.00 O.S.100
NOTE
Size mark is stamped on the piston top.
(2) Measure outside diameter of piston to be used. Measure
it in thrust direction as shown.
(3) Based on the measured piston O.D. calculate boring finish
dimension.
Boring finish dimension = Piston O.D. + (clearance
between piston O.D. and cylinder) – 0.02 mm
(honing margin)
(4) Bore all cylinders to the calculated boring finish dimension.
Caution
To prevent distortion that may result from temperature
rise during honing, bore cylinders, working from No.
2, No. 4, No. 1 to No. 3.
(5) Hone to final finish dimension (piston O.D. + clearance
between piston O.D. and cylinder).
(6) Check clearance between piston and cylinder.
Clearance between piston and cylinder:
0.02 – 0.04 mm
NOTE
When boring cylinders, finish all of four cylinders to same
oversize. Do not bore only one cylinder to an oversize.
Page 99 of 558
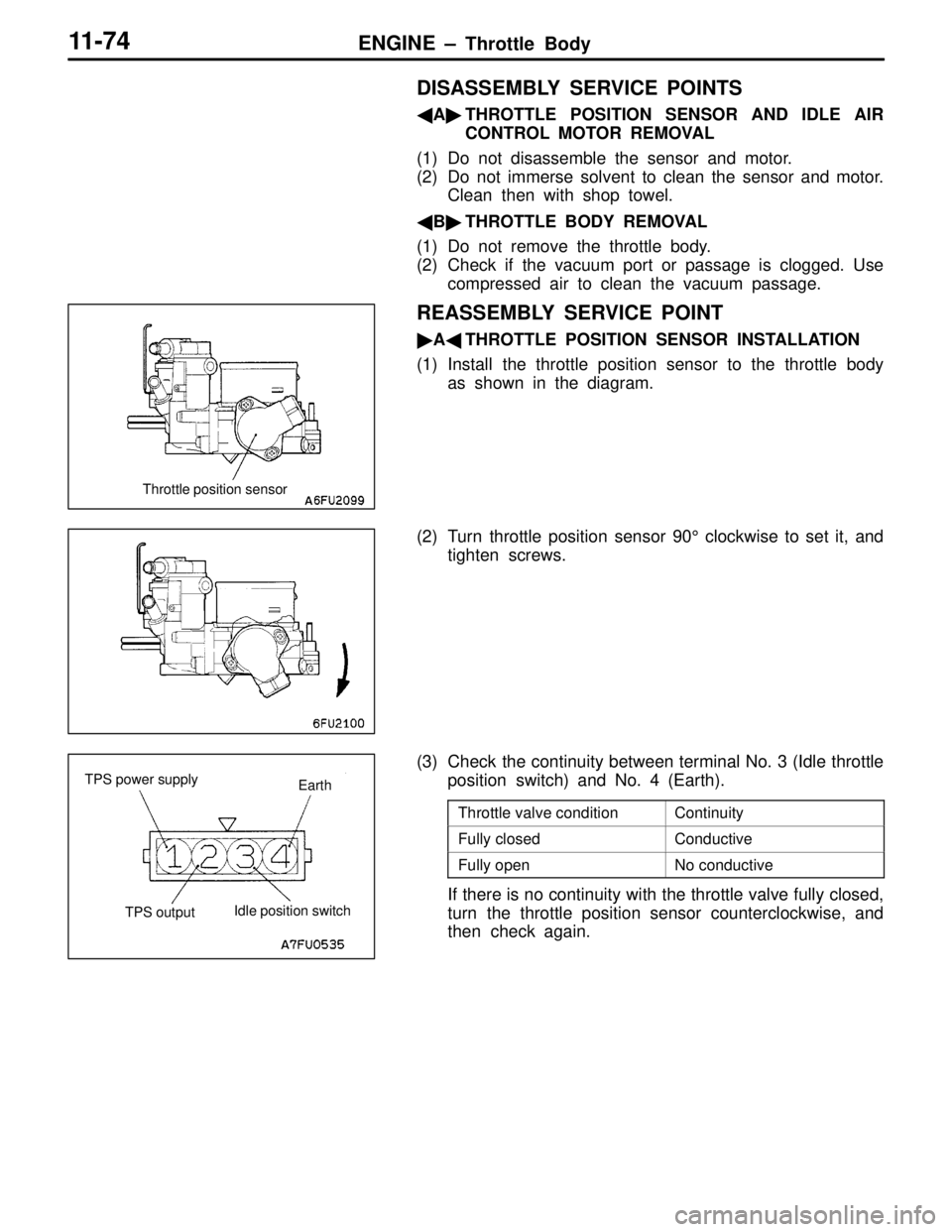
ENGINE – Throttle Body11-74
DISASSEMBLY SERVICE POINTS
ATHROTTLE POSITION SENSOR AND IDLE AIR
CONTROL MOTOR REMOVAL
(1) Do not disassemble the sensor and motor.
(2) Do not immerse solvent to clean the sensor and motor.
Clean then with shop towel.
BTHROTTLE BODY REMOVAL
(1) Do not remove the throttle body.
(2) Check if the vacuum port or passage is clogged. Use
compressed air to clean the vacuum passage.
REASSEMBLY SERVICE POINT
ATHROTTLE POSITION SENSOR INSTALLATION
(1) Install the throttle position sensor to the throttle body
as shown in the diagram.
(2) Turn throttle position sensor 90° clockwise to set it, and
tighten screws.
(3) Check the continuity between terminal No. 3 (Idle throttle
position switch) and No. 4 (Earth).
Throttle valve conditionContinuity
Fully closedConductive
Fully openNo conductive
If there is no continuity with the throttle valve fully closed,
turn the throttle position sensor counterclockwise, and
then check again.
Throttle position sensor
Earth TPS power supply
TPS outputIdle position switch
Page 102 of 558
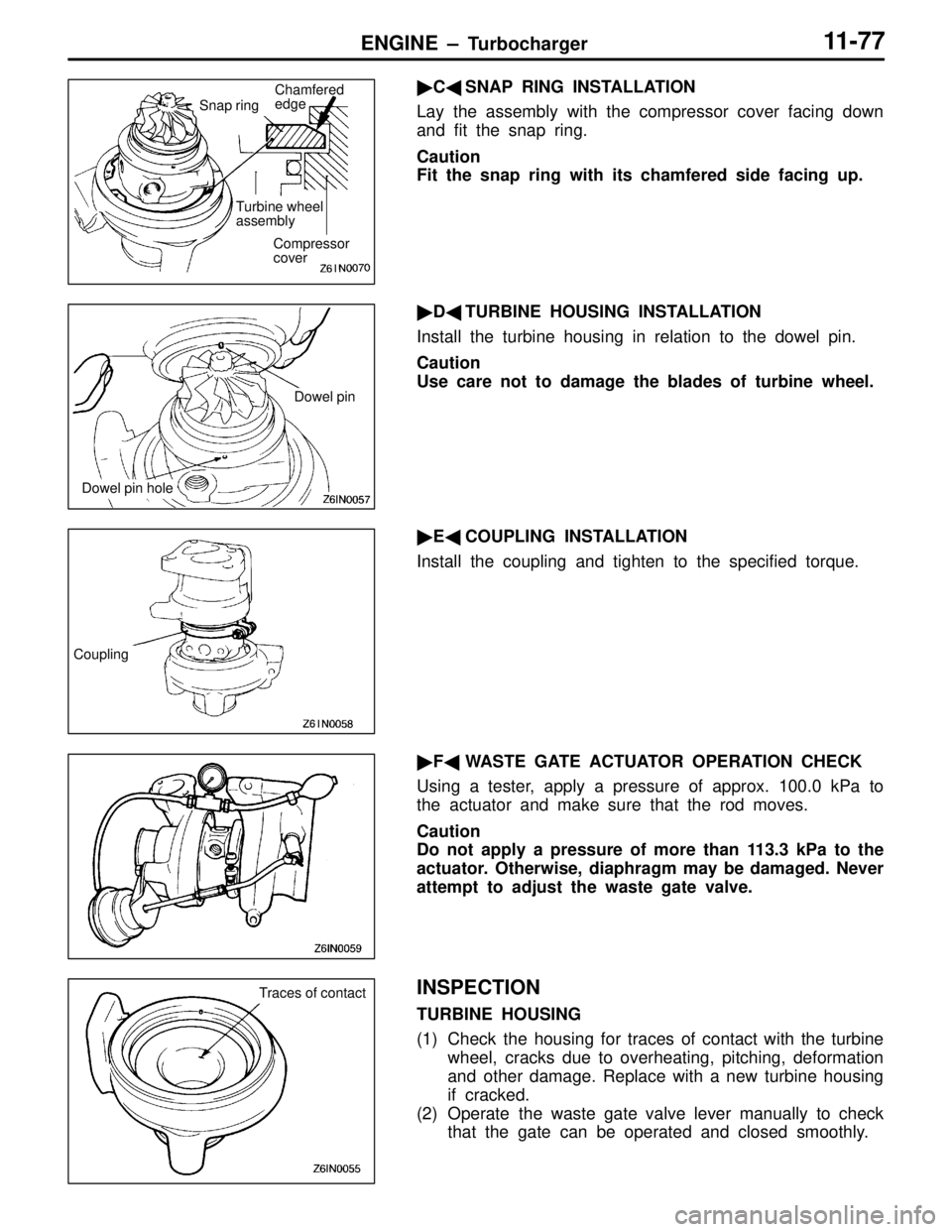
ENGINE – Turbocharger11-77
CSNAP RING INSTALLATION
Lay the assembly with the compressor cover facing down
and fit the snap ring.
Caution
Fit the snap ring with its chamfered side facing up.
DTURBINE HOUSING INSTALLATION
Install the turbine housing in relation to the dowel pin.
Caution
Use care not to damage the blades of turbine wheel.
ECOUPLING INSTALLATION
Install the coupling and tighten to the specified torque.
FWASTE GATE ACTUATOR OPERATION CHECK
Using a tester, apply a pressure of approx. 100.0 kPa to
the actuator and make sure that the rod moves.
Caution
Do not apply a pressure of more than 113.3 kPa to the
actuator. Otherwise, diaphragm may be damaged. Never
attempt to adjust the waste gate valve.
INSPECTION
TURBINE HOUSING
(1) Check the housing for traces of contact with the turbine
wheel, cracks due to overheating, pitching, deformation
and other damage. Replace with a new turbine housing
if cracked.
(2) Operate the waste gate valve lever manually to check
that the gate can be operated and closed smoothly.
Compressor
cover
Turbine wheel
assembly
Chamfered
edge
Snap ring
Dowel pin
Dowel pin hole
Coupling
Traces of contact