Page 368 of 1463
1B3-66 OM600 ENGINE MECHANICAL
18. Remove the timing case cover (19) bolts and then remove
the timing case cover (14).
Notice
Be careful not to damage the cylinder head gasket or oil
pan gasket.
13. Remove the camshaft.
14. Remove the socket bolts(4) in the chain box.
Socket Wrench 115 589 03 07 00
15. Remove the injection pump.
Notice
See the ‘Removal of fuel injection pump’.
16. Remove the oil pan bolts (8, 9) in the area of the timing
case cover (14).
17. Slightly loosen the remaining oil pan bolts.
Page 404 of 1463
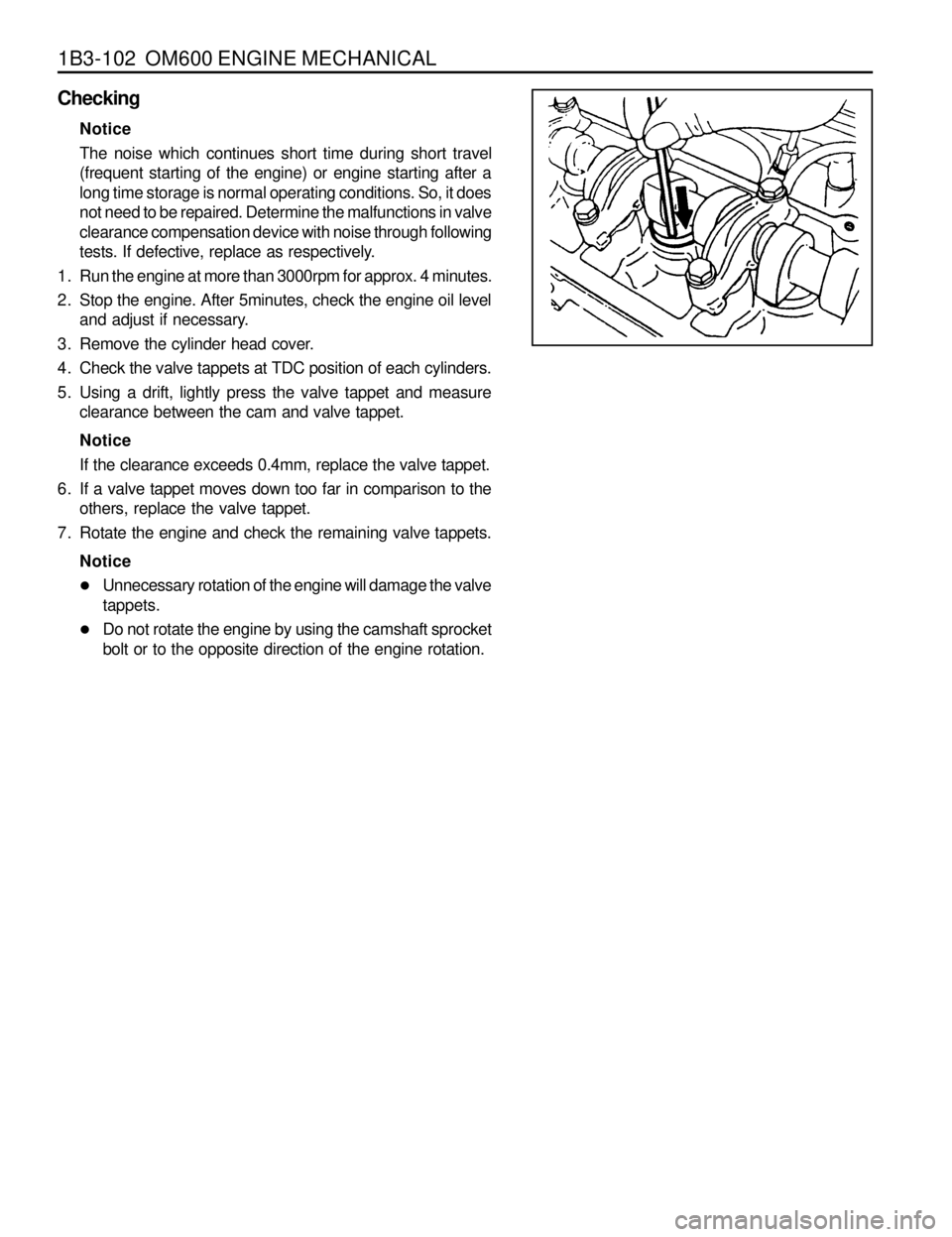
1B3-102 OM600 ENGINE MECHANICAL
Checking
Notice
The noise which continues short time during short travel
(frequent starting of the engine) or engine starting after a
long time storage is normal operating conditions. So, it does
not need to be repaired. Determine the malfunctions in valve
clearance compensation device with noise through following
tests. If defective, replace as respectively.
1. Run the engine at more than 3000rpm for approx. 4 minutes.
2. Stop the engine. After 5minutes, check the engine oil level
and adjust if necessary.
3. Remove the cylinder head cover.
4. Check the valve tappets at TDC position of each cylinders.
5. Using a drift, lightly press the valve tappet and measure
clearance between the cam and valve tappet.
Notice
If the clearance exceeds 0.4mm, replace the valve tappet.
6. If a valve tappet moves down too far in comparison to the
others, replace the valve tappet.
7. Rotate the engine and check the remaining valve tappets.
Notice
lUnnecessary rotation of the engine will damage the valve
tappets.
lDo not rotate the engine by using the camshaft sprocket
bolt or to the opposite direction of the engine rotation.
Page 443 of 1463
OM600 ENGINE MECHANICAL 1B3-141
4. Remove the bolt and then remove the camshaft sprocket.
Notice
During removal, be careful not to drop the sprocket with
chain. Remove the chain carefully and then pull out the
sprocket.
5. Remove the chain tensioner.
6. Remove the camshaft bearing cap bolts according to the
removal order.
Notice
Remove the camshaft bearing cap bolts of 1(dark arrow)
first and then remove the bolts of 2 (light arrow) one
revolution in stages until the counter-pressure is released.
In order to avoid damaging the camshaft, it is essential to
adhere to the removal order for the camshaft bearing caps.
OM 662LA
OM 661LA
Page 445 of 1463
OM600 ENGINE MECHANICAL 1B3-143
5. Tighten the camshaft bearing cap bolts acccording to
installation order.
6. Install the camshaft sprocket to be aligned the markings of
the camshaft / camshaft bearing cap (arrow).
Notice
Align the alignment marks on the timing chain and sprocket.
Tightening Torque 25 Nm
Notice
Tighten the No. 1 bolts (light arrow) by one revolution in
stages first and then tighten the No.2 bolts (dark arrow).
OM 661LA OM 662LA
7. Tighten the camshaft sprocket bolt.
Tightening Torque 25Nm + 90°
Page 566 of 1463
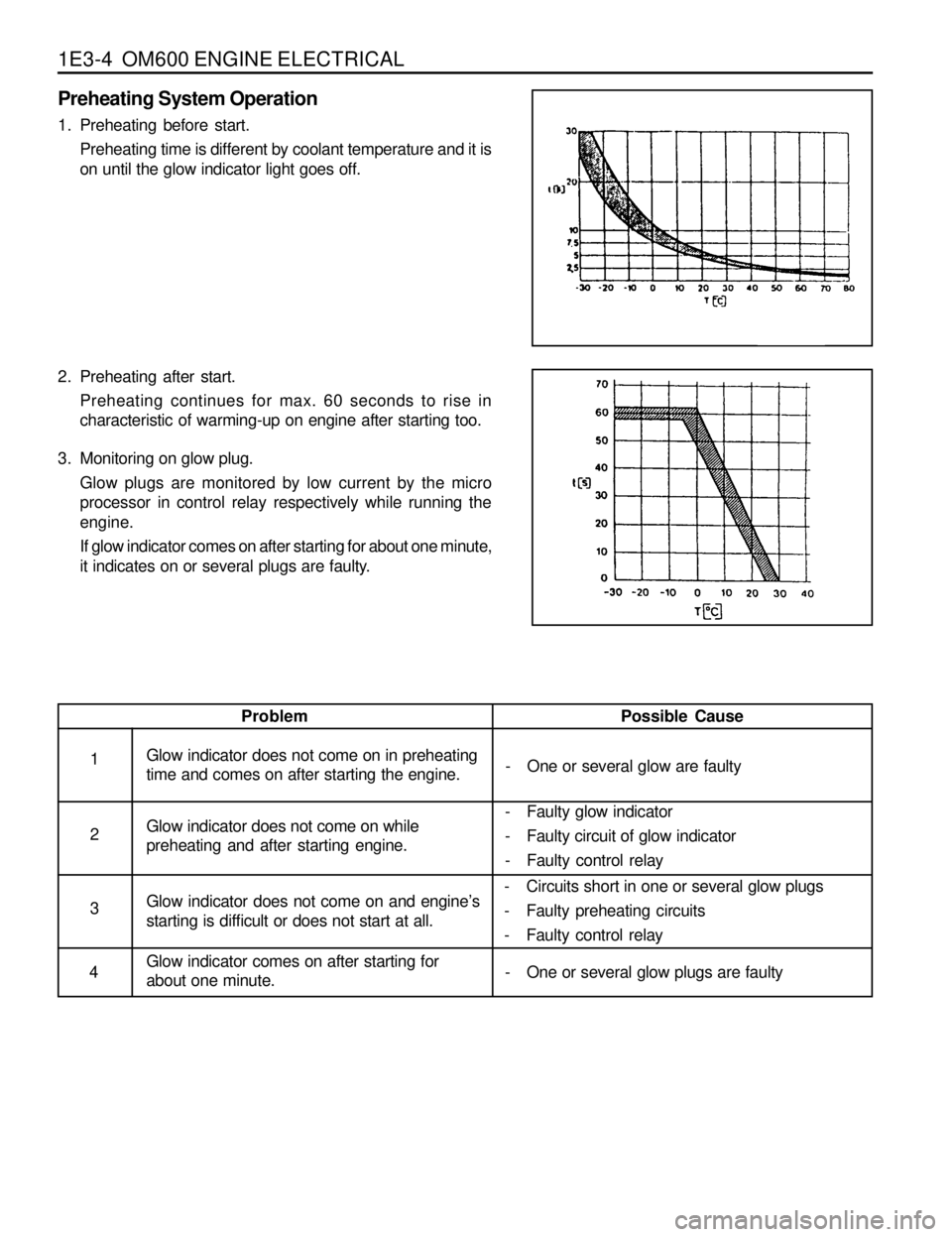
1E3-4 OM600 ENGINE ELECTRICAL
Preheating System Operation
1. Preheating before start.
Preheating time is different by coolant temperature and it is
on until the glow indicator light goes off.
2. Preheating after start.
Preheating continues for max. 60 seconds to rise in
characteristic of warming-up on engine after starting too.
3. Monitoring on glow plug.
Glow plugs are monitored by low current by the micro
processor in control relay respectively while running the
engine.
If glow indicator comes on after starting for about one minute,
it indicates on or several plugs are faulty.
Possible Cause
- One or several glow are faulty Problem
Glow indicator does not come on in preheating
time and comes on after starting the engine.
Glow indicator does not come on while
preheating and after starting engine.
Glow indicator does not come on and engine’s
starting is difficult or does not start at all.
Glow indicator comes on after starting for
about one minute.1
2
3
4- Faulty glow indicator
- Faulty circuit of glow indicator
- Faulty control relay
- Circuits short in one or several glow plugs
- Faulty preheating circuits
- Faulty control relay
- One or several glow plugs are faulty
Page 608 of 1463
1F1-38 M162 ENGINE CONTROLS
Pin No.Abbreciation Decription
21
22
23
24
25
26
27
28
29
30
31
32
33
34
35
36
37
38
39
40
41
42
43
44
45
46
47
48
49
50
51
52
53
54
55
56
57
58
59
60BRS
-
-
-
-
-
KLIKU
-
-
-
GND
SP1+5V
KP
TEV
ML
-
CAN L
CAN H
-
-
-
-
KPI
KLIMA
KLIMA
-
SP1S
SP2S
BLS
GND
SP2+2.5V
S+B
WA
S-B
KSK
-
AUS
DIAG
V-SIG
TN-SIG Brake switch
-
-
-
-
-
Air conditioning clutch relay
-
-
-
Pedal potentiometer 1 ground
Pedal potentiometer 1 supply
Fuel pump relay
Tank purge valve
Engine fan (H1)
-
CAN-Low
CAN-High
-
-
-
-
Clutch switch
Air conditioning
Electronic traction signal
-
Pedal potentiometer 1 signal
Pedal potentiometer 2 signal
Brake light switch
Pedal potentiometer 2 ground
Pedal potentiometer 2 supply
Cruise accelerate/Set
Cruise resume
Cruise decelerate/Set
Cruise safety contact switch
-
Cruise off switch
Diagnostics (k-line)
Vehicle speed signal
Engine speed signal
Page 612 of 1463
1F1-42 M162 ENGINE CONTROLS
Pin No.Description
Pedal potentiometer 1 ground
Pedal potentiometer 1 supply
Fuel pump relay
Tank purge valve
Engine fan
-
CAN-Low
CAN-High
-
-
-
-
Clutch switch
Air conditioning
Electronic traction signal(ABD)
-
Pedal potentiometer 1 signal
Pedal potentiometer 2 signal
Brake light switch
Pedal potentiometer 2 ground
Pedal potentiometer 2 supply
Cruise accelerate/Set
Cruise resume
Cruise decelerate/Set
Cruise safety contact switch
-
Cruise off switch
Diagnostics(K-line)
Vehicle speed signal
Engine speed signal31
32
33
34
35
36
37
38
39
40
41
42
43
44
45
46
47
48
49
50
51
52
53
54
55
56
57
58
59
60GND
SP1+5V
KP
TEV
ML
-
CAN L
CAN H
-
-
-
-
KPL
KLIMA
ETS
-
SP1S
SP2S
BLS
GND
SP2+2.5V
S+B
WA
S-B
KSK
-
AUS
DIAG
V-SIG
TN-SIGl
l
l
l
l
-
l
l
-
-
-
-
¡
l
¡
-
l
l
¡
l
l
¡
¡
¡
¡
-
¡
l
l
ll
l
l
l
l
-
l
l
-
-
-
-
¡
l
¡
-
l
l
¡
l
l
¡
¡
¡
¡
-
¡
l
l
l
Remarks
AbbreviationE32 ENG,
5speed M/T E32 ENG,
4speed A/T
(BTRA)
Page 617 of 1463
M162 ENGINE CONTROLS 1F1-47
3. Disconnect the vacuum hose.
4. Disconnect the circlip and remove the fuel pressure
regulator.
5. Apply the oil to O-ring lightly and then replace it.
6. Installation should follow the removal procedure in the
reverse order.
7. Check for fuel pressure and internal leaks by operating the
engine. 2. Discharge the pressure in fuel supply system by pressing
the service valve.
Removal & Installation Procedure
1. Remove the fuel pressure test connector.