Page 649 of 1463
M162 ENGINE CONTROLS 1F1-79
Accelerator Pedal Sensor Connector(Sensor Side)
Potentiometer 1.
Pin no. 3 :Red
Pin no. 1 :Yellow
Pin no. 5 :Brown
Potentiometer 2.
Pin no. 6 :Violet
Pin no. 4 :Green
Pin no. 2 :White
Accelerator Pedal Sensor Connector(Vehicle Side)
Potentiometer 1.
Pin no. 3 :Red-Black
Pin no. 1 :Blue-Green
Pin no. 5 :Yellow-Green
Potentiometer 2.
Pin no. 6 :Green
Pin no. 4 :Blue-Red
Pin no. 2 :LightGreen
Function
Potentiometer 1, Power Supply(+)
Potentiometer 1, Signal
Potentiometer 2, Ground
Potentiometer 2, Power Supply(+)
Pin no. 3
Pin no. 1
Pin no. 5
Pin no. 6
Pin no. 4
Pin no. 2Potentiometer 2, Signal
Potentiometer 2, Ground
Circuit Diagram
Potentiometer 1.
Potentiometer 2.
Page 686 of 1463
M161 ENGINE CONTROLS 1F2-37
Pin No.Abbreviation Description
21
22
23
24
25
26
27
28
29
30
31
32
33
34
35
36
37
38
39
40
41
42
43
44
45
46
47
48
49
50
51
52
53
54
55
56
57
58
59
60BRS
-
-
-
-
-
KLIKU
-
-
-
GND
SP1+5V
KP
TEV
ML
-
CAN L
CAN H
-
-
-
-
KPI
KLIMA
ETS
-
SP1S
SP2S
BLS
GND
SP2+2.5V
S+B
WA
S-B
KSK
-
AUS
DIAG
V-SIG
TN-SIG Brake switch
-
-
-
-
-
Air conditioning clutch relay
-
-
-
Pedal potentiometer 1 ground
Pedal potentiometer 1 supply
Fuel pump relay
Tank purge valve
Engine fan(High)
-
CAN-Low
CAN-High
-
-
-
-
-
Air conditioning
Electronic traction signal
-
Pedal potentiometer 1 signal
Pedal potentiometer 2 signal
Brake light switch
Pedal potentiometer 2 ground
Pedal potentiometer 2 supply
Cruise accelerate/Set
Cruise resume
Cruise decelerate/Set
Cruise safety contact switch
-
Cruise off switch
Diagnostics(K-Line)
Vehicle speed signal
Engine speed signal
Page 690 of 1463
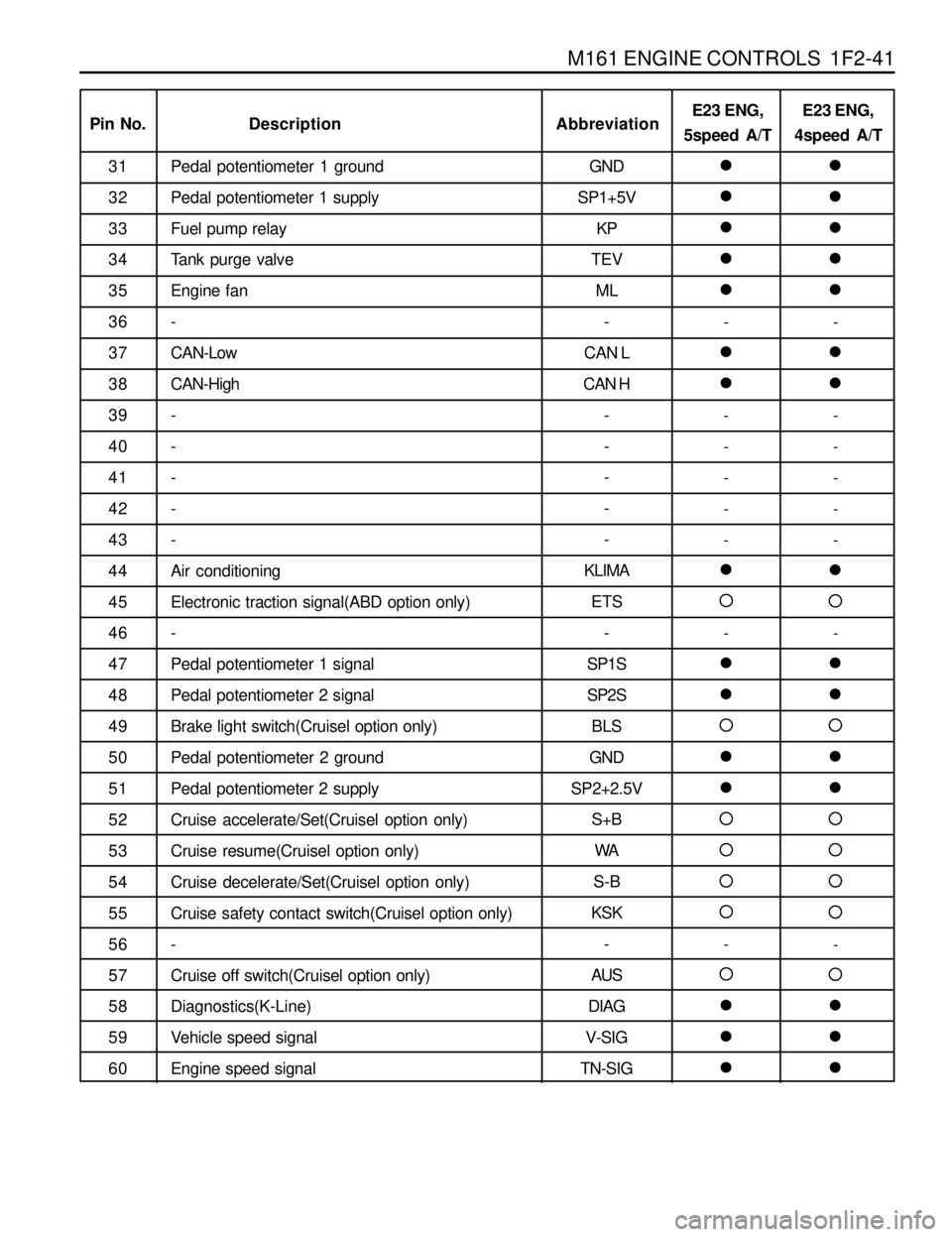
M161 ENGINE CONTROLS 1F2-41
Pin No.Abbreviation Description
Pedal potentiometer 1 ground
Pedal potentiometer 1 supply
Fuel pump relay
Tank purge valve
Engine fan
-
CAN-Low
CAN-High
-
-
-
-
-
Air conditioning
Electronic traction signal(ABD option only)
-
Pedal potentiometer 1 signal
Pedal potentiometer 2 signal
Brake light switch(Cruisel option only)
Pedal potentiometer 2 ground
Pedal potentiometer 2 supply
Cruise accelerate/Set(Cruisel option only)
Cruise resume(Cruisel option only)
Cruise decelerate/Set(Cruisel option only)
Cruise safety contact switch(Cruisel option only)
-
Cruise off switch(Cruisel option only)
Diagnostics(K-Line)
Vehicle speed signal
Engine speed signal31
32
33
34
35
36
37
38
39
40
41
42
43
44
45
46
47
48
49
50
51
52
53
54
55
56
57
58
59
60GND
SP1+5V
KP
TEV
ML
-
CAN L
CAN H
-
-
-
-
-
KLIMA
ETS
-
SP1S
SP2S
BLS
GND
SP2+2.5V
S+B
WA
S-B
KSK
-
AUS
DIAG
V-SIG
TN-SIGl
l
l
l
l
-
l
l
-
-
-
-
-
l
¡
-
l
l
¡
l
l
¡
¡
¡
¡
-
¡
l
l
ll
l
l
l
l
-
l
l
-
-
-
-
-
l
¡
-
l
l
¡
l
l
¡
¡
¡
¡
-
¡
l
l
l
E23 ENG,
4speed A/T E23 ENG,
5speed A/T
Page 695 of 1463
1F2-46 M161 ENGINE CONTROLS
3. Disconnect the vacuum hose.
4. Disconnect the circlip and remove the fuel pressure
regulator.
5. Apply the oil to O-ring lightly and then replace it.
6. Installation should follow the removal procedure in the
reverse order.
7. Check for fuel pressure and internal leaks by operating the
engine. 2. Discharge the pressure in fuel supply system by pressing
the service valve.
Removal & Installation Procedure
1. Remove the fuel pressure test connector.
Page 729 of 1463
1F2-80 M161 ENGINE CONTROLS
Accelerator Pedal Sensor Connector(Sensor Side)
Potentiometer 1.
Pin no. 3 :Red
Pin no. 1 :Yellow
Pin no. 5 :Brown
Potentiometer 2.
Pin no. 6 :Violet
Pin no. 4 :Green
Pin no. 2 :White
Accelerator Pedal Sensor Connector(Vehicle Side)
Potentiometer 1.
Pin no. 3 :Red-Black
Pin no. 1 :Blue-Green
Pin no. 5 :Yellow-Green
Potentiometer 2.
Pin no. 6 :Green
Pin no. 4 :Blue-Red
Pin no. 2 :LightGreen
Circuit Diagram
Potentiometer 1.
Potentiometer 2.
Function
Potentiometer 1, Power Supply(+)
Potentiometer 1, Signal
Potentiometer 2, Ground
Potentiometer 2, Power Supply(+) Pin no. 3
Pin no. 1
Pin no. 5
Pin no. 6
Pin no. 4
Pin no. 2Potentiometer 2, Signal
Potentiometer 2, Ground
Page 767 of 1463
1F3-38 OM600 ENGINE CONTROLS
Tools Required
617 589 08 21 00 Position Sensor
Test Procedure
1. Remove the screw plug (5) and seal (4) and collect oil in a
suitable vessel.
2. Install the position sensor (1) into the governor housing of
the injection pump to be the guide pin of the position sensor
facing up.
3. Connect the battery terminal of position sensor (1) to positive
terminal (+) of battery.
Position Sensor 617 589 08 21 00
4. Rotate the crankshaft by hand (in direction of engine rotation)
until the lamp ‘B’ lights up. Rotate the crankshaft carefully
further until both lamps ‘A and B’ come on. In this position,
check the Rl value on the crankshaft vibration damper.
Notice
If only lamp ‘A’ lights up, repeat the test and if out of
specification, adjust start of delivery.
Specification ATDC 14° - 16°
Page 772 of 1463
OM600 ENGINE CONTROLS 1F3-43
Tools Required
617 589 08 21 00 Position Sensor
Adjustment Procedure
1. Position the No. 1 cylinder at ATDC 15°
Notice
Do not rotate the engine in opposite direction of engine
rotation.
2. Remove the bolt (2) at the supporting bracket.
3. Remove the bolt (4).
4. Turn the adjusting screw (1) until both lamps ‘A’ + ‘B’ on
the position sensor light up.
Notice
If the adjustment range is not adequate, remove the injection
pump and reinstall.
Position Sensor 617 589 08 21 00
5. After adjusting, retighten all the bolt to the specified torque.
To the right
To the leftStart of delivery retarded
Start of delivery advanced
Page 833 of 1463
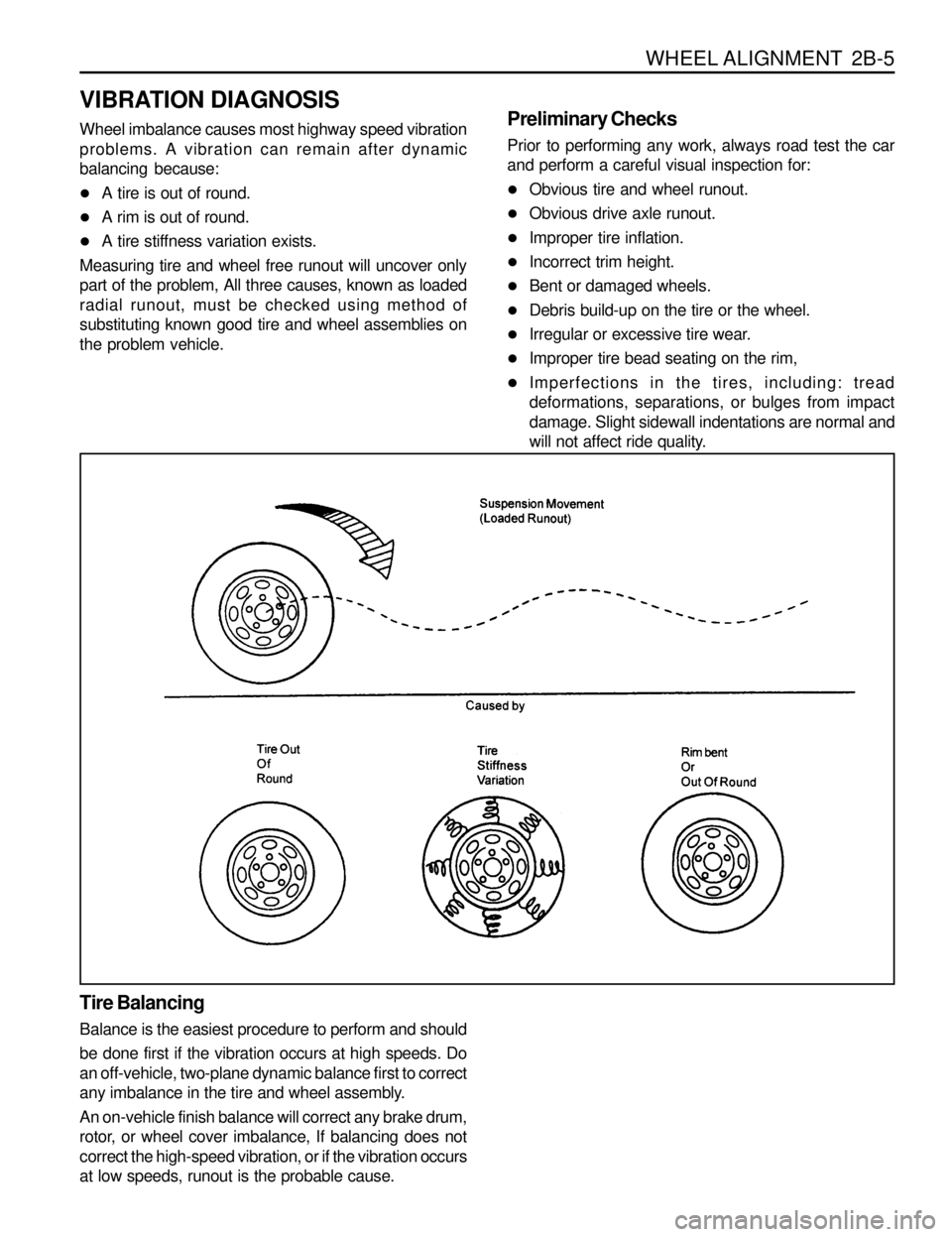
WHEEL ALIGNMENT 2B-5
VIBRATION DIAGNOSIS
Wheel imbalance causes most highway speed vibration
problems. A vibration can remain after dynamic
balancing because:
lA tire is out of round.
lA rim is out of round.
lA tire stiffness variation exists.
Measuring tire and wheel free runout will uncover only
part of the problem, All three causes, known as loaded
radial runout, must be checked using method of
substituting known good tire and wheel assemblies on
the problem vehicle.
Preliminary Checks
Prior to performing any work, always road test the car
and perform a careful visual inspection for:
lObvious tire and wheel runout.
lObvious drive axle runout.
lImproper tire inflation.
lIncorrect trim height.
lBent or damaged wheels.
lDebris build-up on the tire or the wheel.
lIrregular or excessive tire wear.
lImproper tire bead seating on the rim,
lImperfections in the tires, including: tread
deformations, separations, or bulges from impact
damage. Slight sidewall indentations are normal and
will not affect ride quality.
Tire Balancing
Balance is the easiest procedure to perform and should
be done first if the vibration occurs at high speeds. Do
an off-vehicle, two-plane dynamic balance first to correct
any imbalance in the tire and wheel assembly.
An on-vehicle finish balance will correct any brake drum,
rotor, or wheel cover imbalance, If balancing does not
correct the high-speed vibration, or if the vibration occurs
at low speeds, runout is the probable cause.