Page 494 of 2490
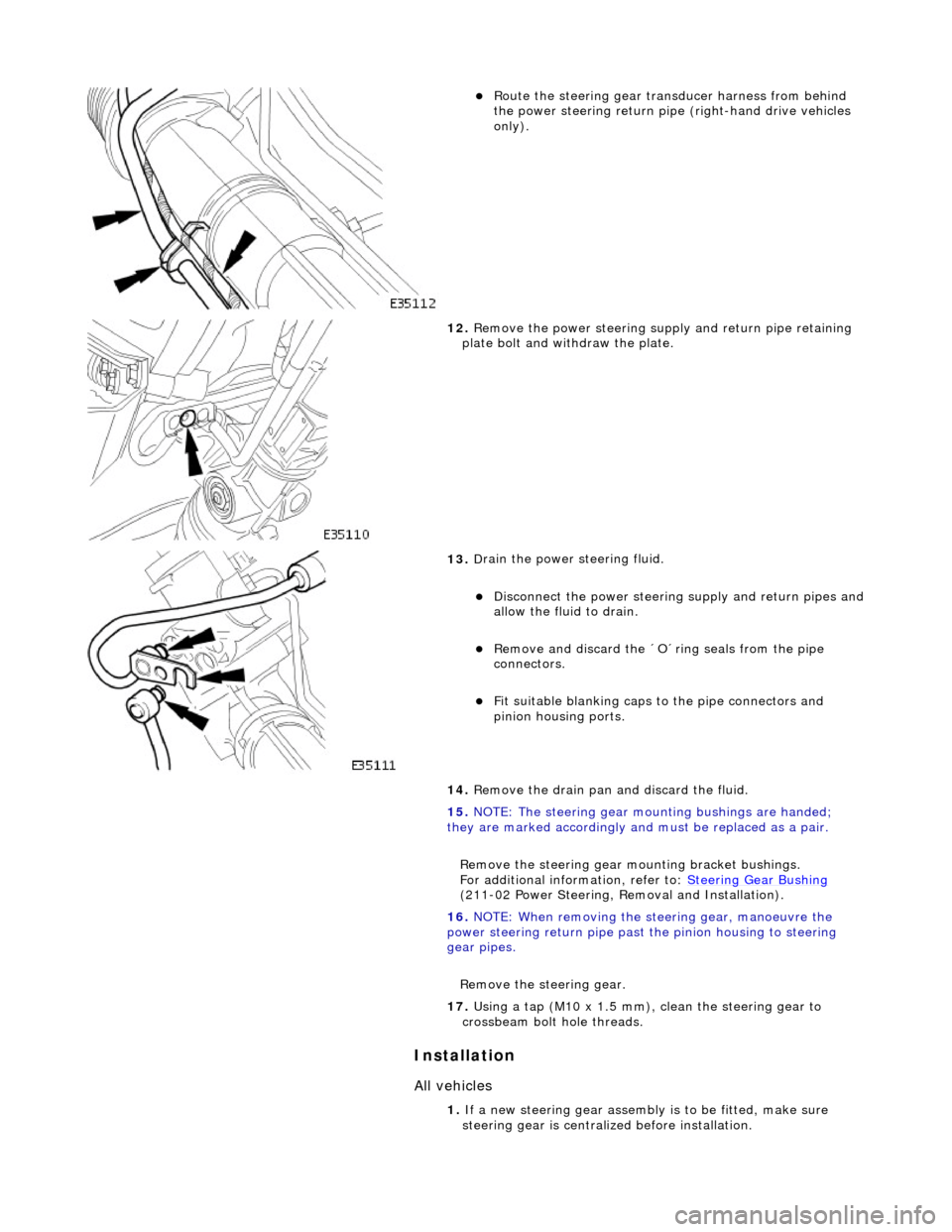
In
stallation
All vehicles
Route t
he steering gear transducer harness from behind
the power steering return pipe (right-hand drive vehicles
only).
12 . Remove the
power steering supply and return pipe retaining
plate bolt and with draw the plate.
13 . D
rain the power steering fluid.
Di
sc
onnect the power steering
supply and return pipes and
allow the fluid to drain.
Remove an d discard the ´O´ring seals from the
pipe
connectors.
Fi t su
itable blanking caps
to the pipe connectors and
pinion housing ports.
14. Remove the drain pan and discard the fluid.
15. NOTE: The steering gear mounting bushings are handed;
they are marked accordingly and must be replaced as a pair.
Remove the steering gear mo unting bracket bushings.
For additional information, refer to: Steering Gear Bushing
( 21
1-02 Power Steering, Removal and Installation).
16. NOTE: When removing the steering gear, manoeuvre the
power steering return pipe past the pinion housing to steering
gear pipes.
Remove the steering gear.
17. Using a tap (M10 x 1.5 mm), clean the steering gear to
crossbeam bolt hole threads.
1. If a new steering gear assembly is to be fitted, make sure
steering gear is centrali zed before installation.
Page 510 of 2490
The lower steeri ng col
umn:
Is a han
ded assembly
.
Incorporates
a col
umn to toeboard seal
which comprises a rolling element having two, low friction, PTFE rings. The
rolling element locates in a rubber b oot which seals to the toeboard.
Has a lowe
r universal joint connecting the
lower column to the steering rack.
Has an upper un
iversal joint connecting
the lower column to the upper column.
Has a NVH damper in
corporated into
the upper universal joint assembly.
May be installed in an
y orientation on the universal joint splines.
R
e
quires no setting or adjustment.
Has no s
e
rviceable components.
It is essential to disconnect the lower column from the steer ing rack before removing the engine or front suspension
crossbeam.
It e
m
Par
t
Number
De
scr
iption
1-Boot
2-Uni
v
ersal joint to upper column
3-Lower steeri
ng col
umn shaft
4-R
e
taining bolts
5-Uni
v
ersal joint to steering rack
Lower Steering Column
Page 516 of 2490
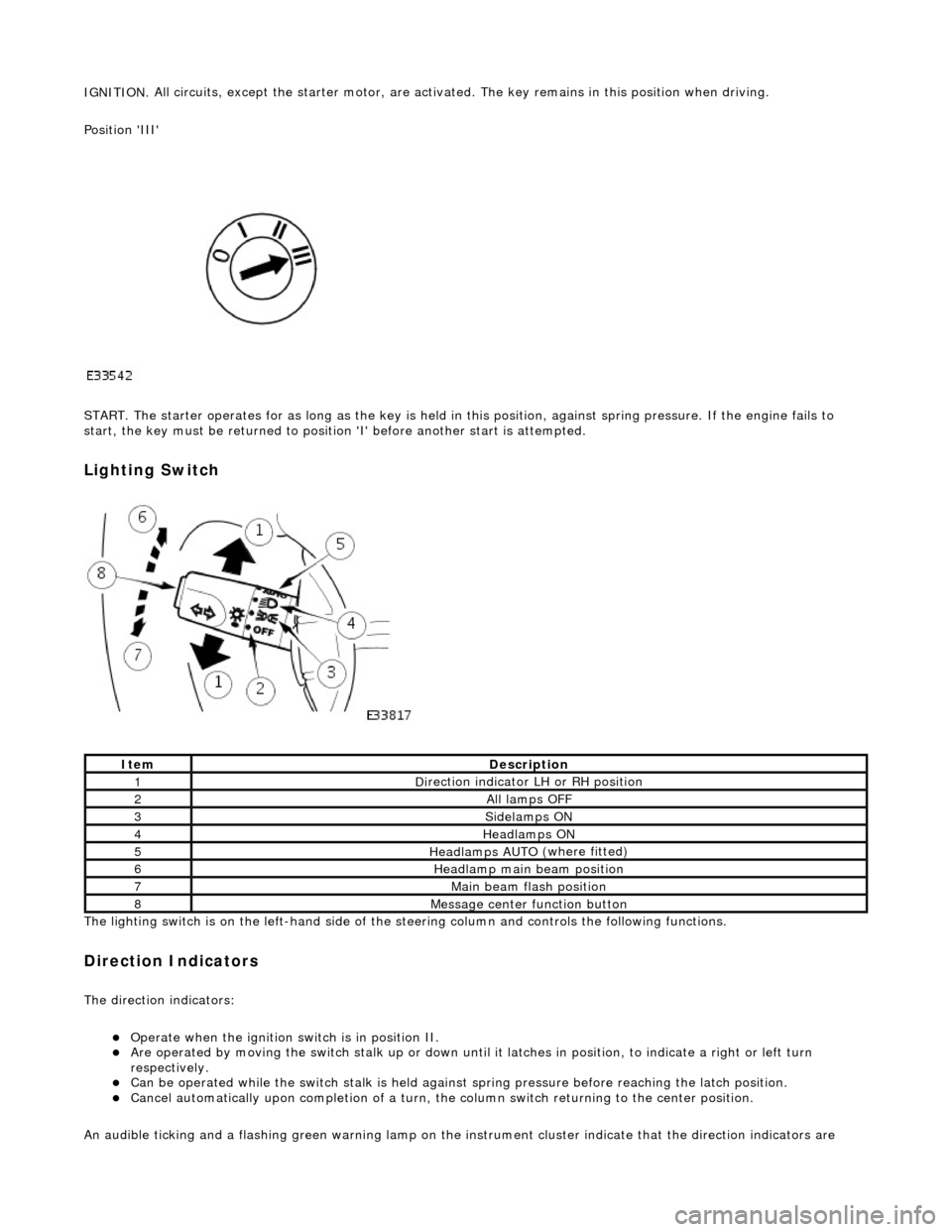
IGNITION.
All circuits, except the star
ter motor, are activated. The key rema ins in this position when driving.
Position 'III'
START. The starter operates for as long as the key is held in this position, ag ainst spring pressure. If the engine fails to
start, the key must be returned to position 'I' befo re another start is attempted.
Lighting Switch
The li
ghting switch is on the left-h
and side of the steering column and controls the following functions.
Direction Indicators
The direction in
dicators:
Operate
when the ignition switch is in position II.
Are operat
ed by movi
ng the switch stalk up or down until it latches in position, to in
dicate a right or left turn
respectively.
Can be o p
erated while the switch stalk is held against
spring pressure before reaching the latch position.
Cancel
automatically upon completion of a turn, the
column switch returning to the center position.
An audible ticking and a flashing green warning lamp on the in strument cluster indicate that the direction indicators are
Ite
m
De
scr
iption
1D
i
rection indicator LH or RH position
2All lamps OFF
3Side
lamps ON
4Headlamps ON
5Headlamps AUT O
(where fitted)
6He
adlam
p main beam position
7Mai
n
beam flash position
8M
e
ssage center function button
Page 517 of 2490
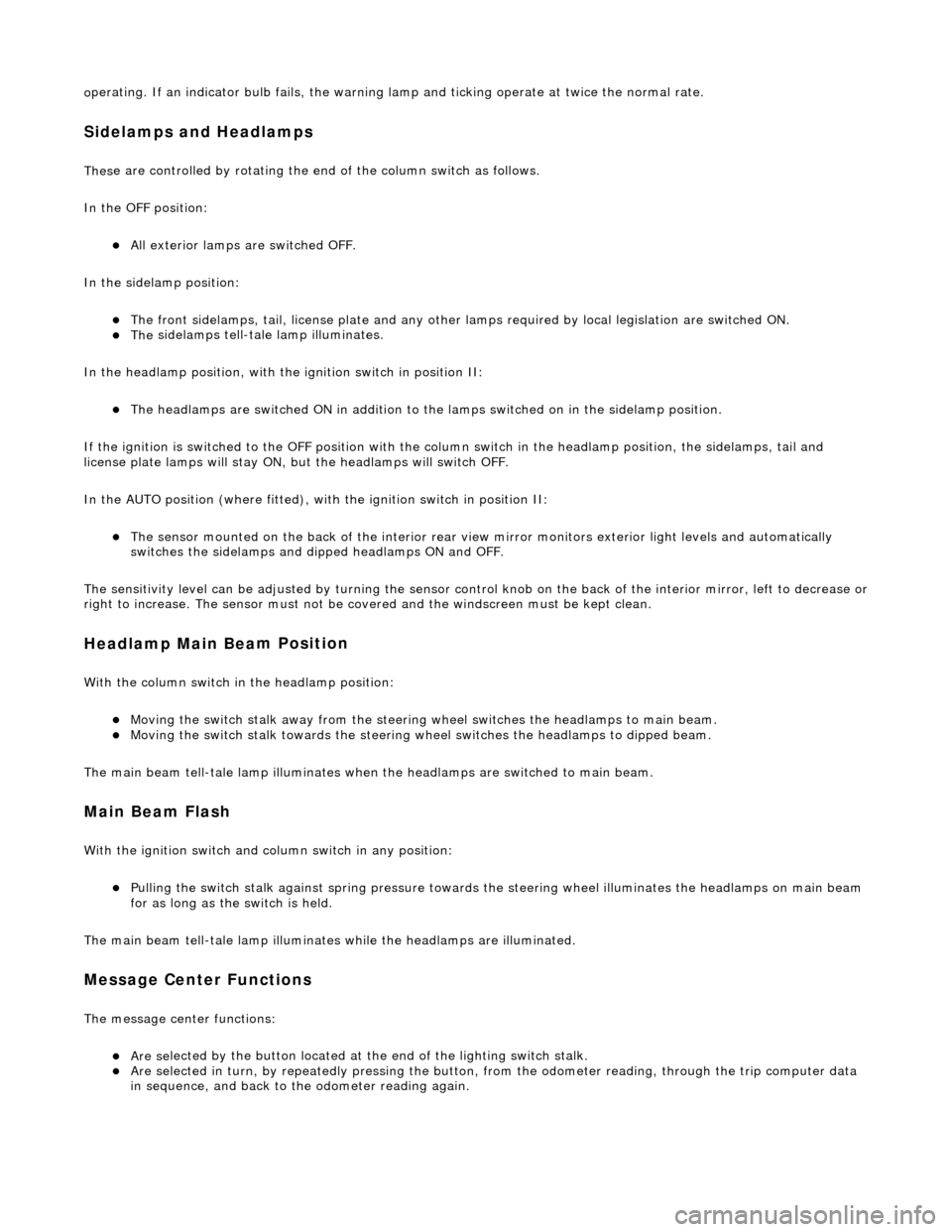
o
perating. If an indicator bulb fails, the warning
lamp and ticking operate at twice the normal rate.
Sidelam
ps and Headlamps
Thes
e are controlled by rotating the end of the column switch as follows.
In the OFF position:
All
exterior lamps are switched OFF.
In the sidelamp position:
The front
sidelamps, tail, license plate and any other la
mps required by local legislation are switched ON.
The
sidelamps tell-tale lamp illuminates.
In the headlamp position, with the ignition switch in position II:
The h
eadlamps are switched ON in addition to the lamps switched on in the sidelamp position.
If the ignition is switched to the OFF position with the column switch in the headlamp position, the sidelamps, tail and
license plate lamps will stay ON, but the headlamps will switch OFF.
In the AUTO position (where fitted), with the ignition switch in position II:
Th
e sensor mounted on the back of the interior rear view
mirror monitors exterior light levels and automatically
switches the sidelamps and di pped headlamps ON and OFF.
The sensitivity level can be adjusted by turn ing the sensor control knob on the back of the interior mirror, left to decrease or
right to increase. The sensor must not be covered and the windscreen must be kept clean.
Headlamp Main Bea
m Position
Wi
th the column switch in
the headlamp position:
Movin
g the switch stalk away fro
m the steering wheel switches the headlamps to main beam.
Movin
g the switch stalk towards the steering wheel switches the headlamps to dipped beam.
The main beam tell-tale lamp illuminates when the headlamps are switched to main beam.
Ma
in Beam Flash
Wi
th the ignition switch and column switch in any position:
Pulling the
switch stalk agains
t spring pressure towards th e steering wheel illuminates the headlamps on main beam
for as long as the switch is held.
The main beam tell-tale lamp illuminates while the headlamps are illuminated.
M
essage Center Functions
T
he message center functions:
Are se
lected by the button located at the end of the lighting switch stalk.
Are se
lected in turn, by repeatedly pressing the button,
from the odometer reading, through the trip computer data
in sequence, and back to th e odometer reading again.
Page 521 of 2490
Engine System - General Infor
mation - Engine
Description an
d Operation
The AJ26 power unit is available in 3.2 L and 4.0 L versions, and comprises:
An eight cylinder 9
0 degree 'V' config
uration liquid cooled aluminium cylinder block incorporating 'Nikasil' plated
cylinder bores.
Pi
stons of open-ended skirt design, with
two compression and one oil control ring.
Two al
uminium cylinder heads, each
incorporating two camshafts.
F
our valves per cylinder.
Al
uminium valve lifters and top mounted shims.
Vari
able valve timing (VVT) of the inlet camshafts (4.0 L normally aspirated only).
Camshaft
covers manufactured from Vinylester.
Al
uminium timing cover which accommodat
es the crankshaft front oil seal.
Sin
gle row primary and secondary chains dr
ive the camshafts of each cylinder bank.
An alu
minium bed pl
ate, incorporating iron main bearing supports, which accomm odate the oil pump pick-up,
Page 558 of 2490
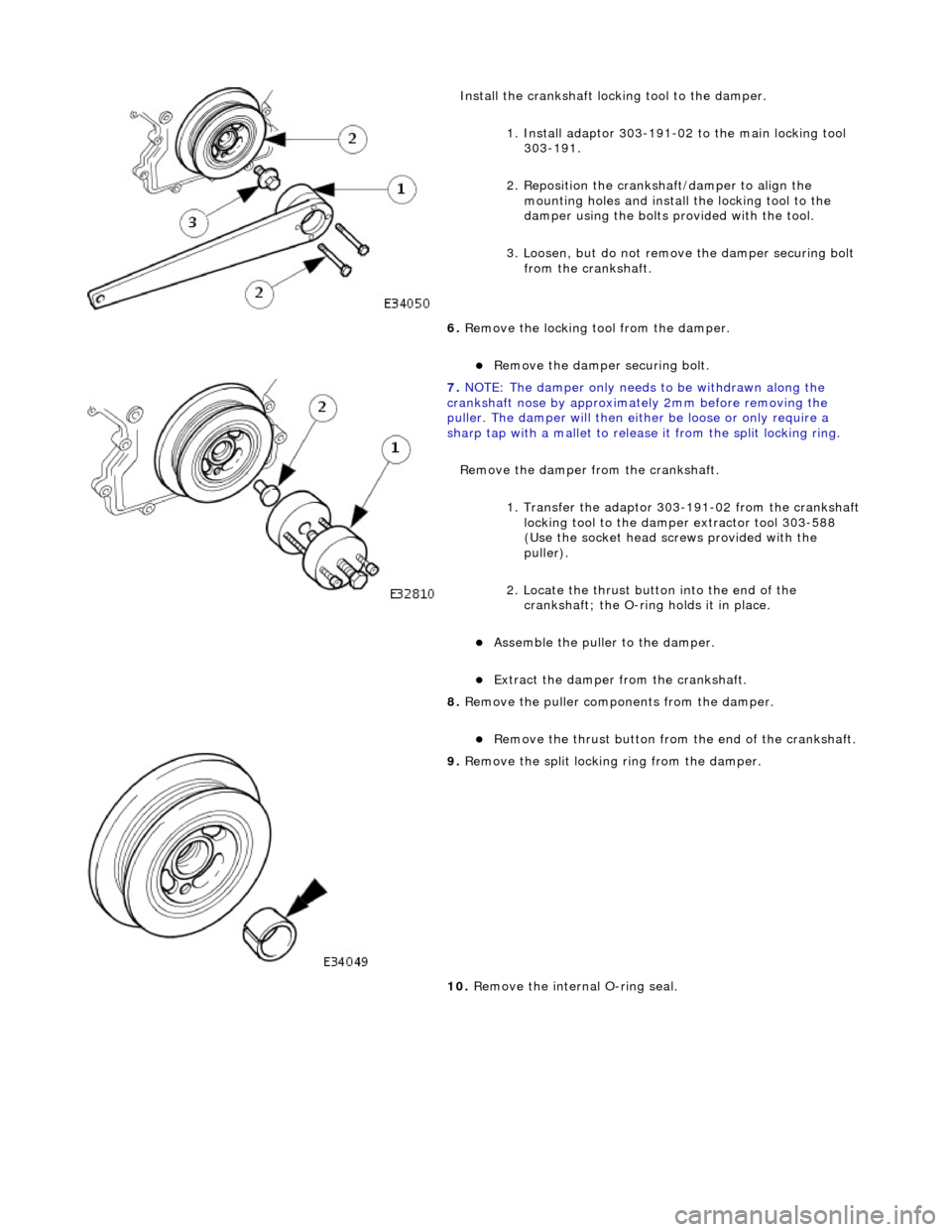
Instal
l the crankshaft locking tool to the damper.
1. Install adaptor 303-191-02 to the main locking tool 303-191.
2. Reposition the cranks haft/damper to align the
mounting holes and install the locking tool to the
damper using the bolts provided with the tool.
3. Loosen, but do not remove the damper securing bolt
from the crankshaft.
6. Remove the locking tool from the damper.
Remove
the damper securing bolt.
7. NOTE : Th
e damper only needs to be withdrawn along the
crankshaft nose by approximat ely 2mm before removing the
puller. The damper will then either be loose or only require a
sharp tap with a mallet to release it from the split locking ring.
Remove the damper from the crankshaft.
1. Transfer the adaptor 303 -191-02 from the crankshaft
locking tool to the damper extractor tool 303-588
(Use the socket head screws provided with the
puller).
2. Locate the thrust button into the end of the crankshaft; the O-ring holds it in place.
Ass
emble the puller to the damper.
Ex
trac
t the damper from the crankshaft.
8. Remove the puller components from the damper.
Re
move the thrust button from the end of the crankshaft.
9. Re
move the split locking ring from the damper.
10. Remove the internal O-ring seal.
Page 562 of 2490

5. Re
move the twin fan and motor
assembly for access. Refer to
Operation 26.25.12
6. CAUTIO
N: Under no circumstan
ces should the crankshaft
setting peg 303-531 be used in the following operations, to lock
the crankshaft.
• NOTE: Should extra locking of the crankshaft be required, use a
lever against one torque converte r boss. Remove the plastic mesh
cover from the torque converter housing for access.
Install the crankshaft locking tool to the damper. 1. Install adaptor 303-191-03 to the main locking tool 303-191.
2. Reposition the cranks haft/damper to align the
mounting holes and install the locking tool to the
damper using the bolts provided with the tool.
3. Loosen, but do not remove the damper securing bolt
from the crankshaft.
7. Re
move the locking tool from the damper.
Re
move
the damper securing bolt.
8. NOTE : Th
e damper only needs to be withdrawn along the
crankshaft nose by approximat ely 2mm before removing the
puller. The damper will then either be loose or only require a
sharp tap with a mallet to release it from the split locking ring.
Remove the damper from the crankshaft.
1. Install adaptor 303-191-02 to the damper extractor tool 303-588 (Use the socket head screws provided
with the puller).
2. Locate the thrust button into the end of the crankshaft; the O-ring holds it in place.
Ass
emble the puller to the damper.
Ex
trac
t the damper from the crankshaft.
9. Remove the puller components from the damper.
Re
move the thrust button from the end of the crankshaft.
10 . R
emove the split locking ring from the damper.
11. Remove the internal O-ring seal.
Page 594 of 2490
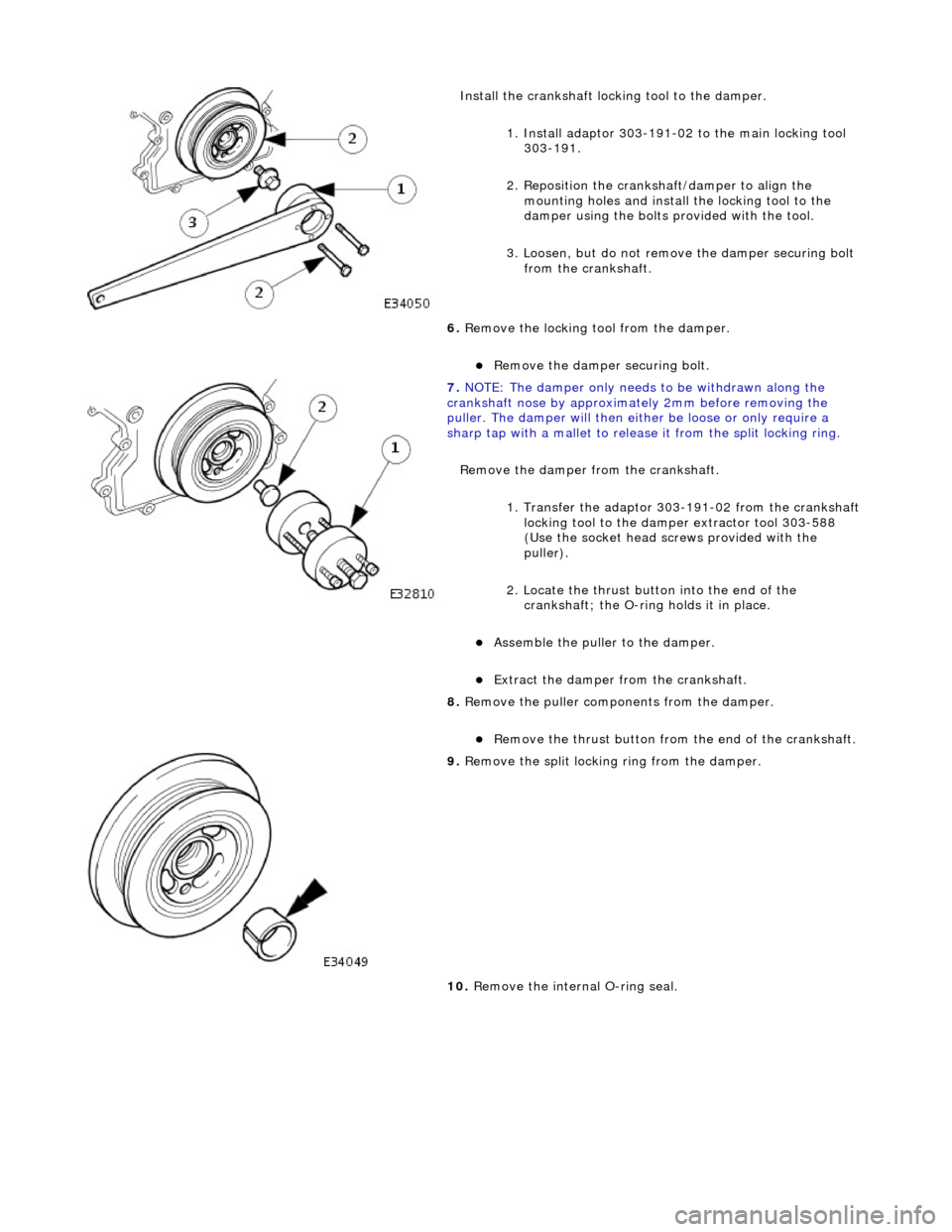
Instal
l the crankshaft locking tool to the damper.
1. Install adaptor 303-191-02 to the main locking tool 303-191.
2. Reposition the cranks haft/damper to align the
mounting holes and install the locking tool to the
damper using the bolts provided with the tool.
3. Loosen, but do not remove the damper securing bolt
from the crankshaft.
6. Remove the locking tool from the damper.
Remove
the damper securing bolt.
7. NOTE : Th
e damper only needs to be withdrawn along the
crankshaft nose by approximat ely 2mm before removing the
puller. The damper will then either be loose or only require a
sharp tap with a mallet to release it from the split locking ring.
Remove the damper from the crankshaft.
1. Transfer the adaptor 303 -191-02 from the crankshaft
locking tool to the damper extractor tool 303-588
(Use the socket head screws provided with the
puller).
2. Locate the thrust button into the end of the crankshaft; the O-ring holds it in place.
Ass
emble the puller to the damper.
Ex
trac
t the damper from the crankshaft.
8. Remove the puller components from the damper.
Re
move the thrust button from the end of the crankshaft.
9. Re
move the split locking ring from the damper.
10. Remove the internal O-ring seal.