Page 177 of 198
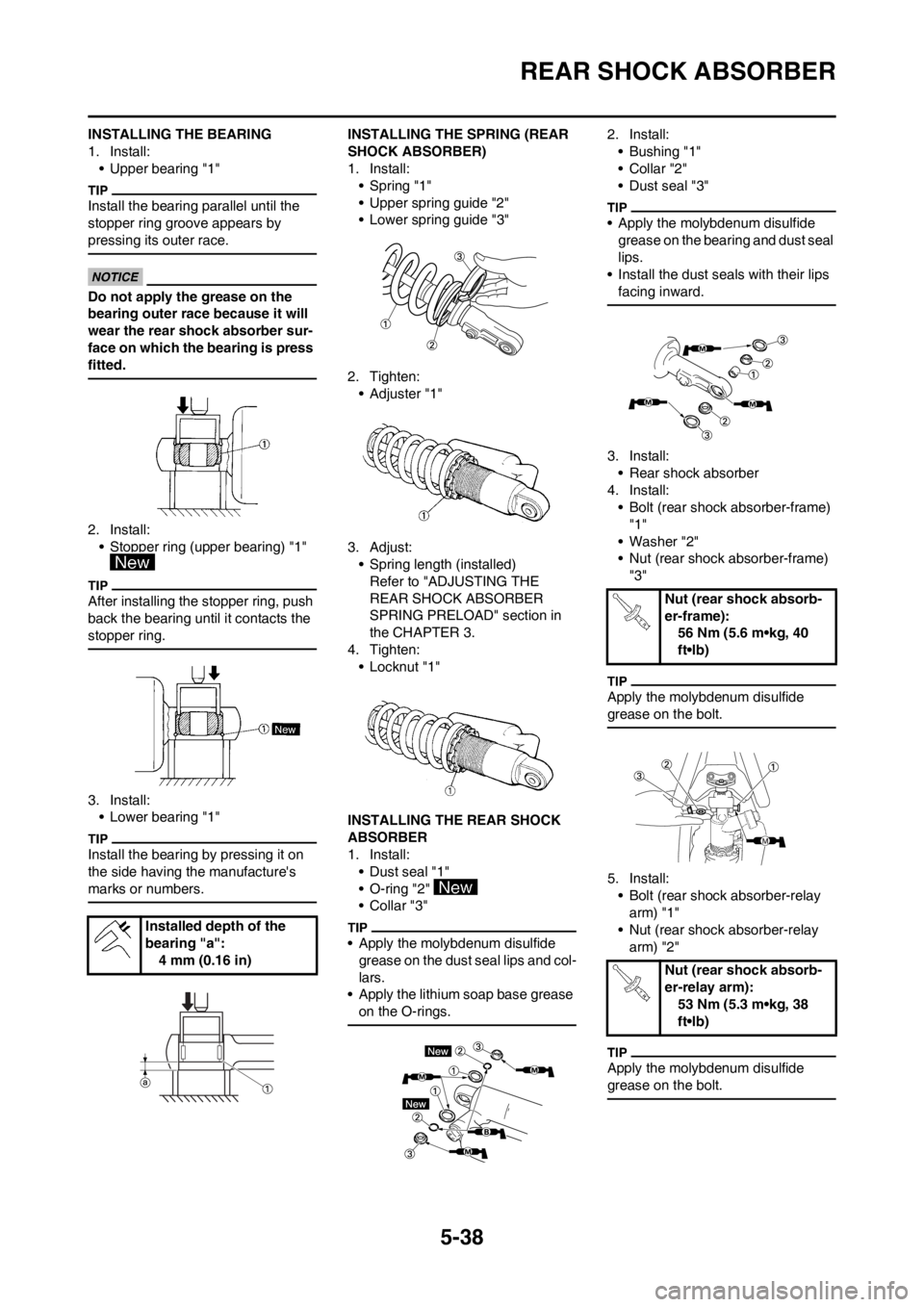
5-38
REAR SHOCK ABSORBER
INSTALLING THE BEARING
1. Install:
• Upper bearing "1"
Install the bearing parallel until the
stopper ring groove appears by
pressing its outer race.
Do not apply the grease on the
bearing outer race because it will
wear the rear shock absorber sur-
face on which the bearing is press
fitted.
2. Install:
• Stopper ring (upper bearing) "1"
After installing the stopper ring, push
back the bearing until it contacts the
stopper ring.
3. Install:
• Lower bearing "1"
Install the bearing by pressing it on
the side having the manufacture's
marks or numbers.
INSTALLING THE SPRING (REAR
SHOCK ABSORBER)
1. Install:
• Spring "1"
• Upper spring guide "2"
• Lower spring guide "3"
2. Tighten:
•Adjuster "1"
3. Adjust:
• Spring length (installed)
Refer to "ADJUSTING THE
REAR SHOCK ABSORBER
SPRING PRELOAD" section in
the CHAPTER 3.
4. Tighten:
• Locknut "1"
INSTALLING THE REAR SHOCK
ABSORBER
1. Install:
• Dust seal "1"
• O-ring "2"
• Collar "3"
• Apply the molybdenum disulfide
grease on the dust seal lips and col-
lars.
• Apply the lithium soap base grease
on the O-rings.
2. Install:
• Bushing "1"
•Collar "2"
• Dust seal "3"
• Apply the molybdenum disulfide
grease on the bearing and dust seal
lips.
• Install the dust seals with their lips
facing inward.
3. Install:
• Rear shock absorber
4. Install:
• Bolt (rear shock absorber-frame)
"1"
• Washer "2"
• Nut (rear shock absorber-frame)
"3"
Apply the molybdenum disulfide
grease on the bolt.
5. Install:
• Bolt (rear shock absorber-relay
arm) "1"
• Nut (rear shock absorber-relay
arm) "2"
Apply the molybdenum disulfide
grease on the bolt.
Installed depth of the
bearing "a":
4 mm (0.16 in)
Nut (rear shock absorb-
er-frame):
56 Nm (5.6 m•kg, 40
ft•lb)
Nut (rear shock absorb-
er-relay arm):
53 Nm (5.3 m•kg, 38
ft•lb)
Page 178 of 198
5-39
REAR SHOCK ABSORBER
6. Install:
•Collar "1"
• Rear frame "2"
• Bolt [rear frame (upper)] "3"
• Bolt [rear frame (lower)] "4"
7. Tighten:
• Bolt (air filter joint) "1"Bolt [rear frame (upper)]:
32 Nm (3.2 m•kg, 23
ft•lb)
Bolt [rear frame (lower)]:
32 Nm (3.2 m•kg, 23
ft•lb)
Bolt (air filter joint):
3 Nm (0.3 m•kg, 2.2
ft•lb)
Page 179 of 198
6-1
ELECTRICAL
This section is intended for those who have basic knowledge and skill concerning the servicing of Yamaha motorcycles
(e.g., Yamaha dealers, service engineers, etc.) Those who have little knowledge and skill concerning servicing are request-
ed not to undertake inspection, adjustment, disassembly, or reassembly only by reference to this manual. It may lead to
servicing trouble and mechanical damage.
6
Page 180 of 198
6-2
ELECTRICAL COMPONENTS AND WIRING DIAGRAM
ELECTRICAL
COMPONENTS AND
WIRING DIAGRAM
ELECTRICAL COMPONENTS
1. Engine stop switch
2. Throttle position sensor
3. Neutral switch4. CDI magneto
5. Ignition coil
6. Spark plug7. CDI unit
WIRING DIAGRAM
1. Engine stop switch
2. Throttle position sensor
3. Neutral switch
4. CDI magneto
5. Ignition coil
6. Spark plug
7. CDI unit COLOR CODE
BBlack
Br Brown
GGreen
LBlue
O Orange
PPink
RRed
Sb Sky blue
WWhite
YYellowB/L Black/Blue
B/W Black/White
B/Y Black/Yellow
G/B Green/Black
L/W Blue/White
R/W Red/White
B/WB/W
B/L
B/Y
SbSb
G/B
LYLY
P
B
B
B
B
G
O
WR
P
GW
R
P
B
Br W
W
B/Y G Br
G
RR
OB
Sb Sb
Y
Y
W Y
W
GG B
P P
Br BrRR
O L
B
Sb Y
LL
B/L
B/W
B/W
G/B
B
B
B/L
L
Sb
B/L
G/B
G/B B/Y
B/Y
B/W O
B/W
BrBrP
Page 181 of 198
6-3
IGNITION SYSTEM
IGNITION SYSTEM
INSPECTION STEPS
Use the following steps for checking the possibility of the malfunctioning engine being attributable to ignition system failure
and for checking the spark plug which will not spark.
*marked: Only when the ignition checker is used.
• Remove the following parts before inspection.
1. Seat
2. Fuel tank
• Use the following special tools in this inspection.
Spark gap test Spark→*Clean or replace spark plug.
No spark↓
Check entire ignition system for connection.
(couplers, leads and ignition coil)No good→
Repair or replace.
OK↓
Check engine stop switch. No good→Replace.
OK↓
Check ignition coil. (primary coil and secondary
coil)No good→
Replace.
OK↓
Check CDI magneto. (pickup coil and charging
coil)No good→
Replace.
OK↓
Check neutral switch. No good→Repair or replace.
OK↓
Replace CDI unit.
Dynamic spark tester:
YM-34487
Ignition checker:
90890-06754
Pocket tester:
YU-3112-C/90890-03112
Page 182 of 198
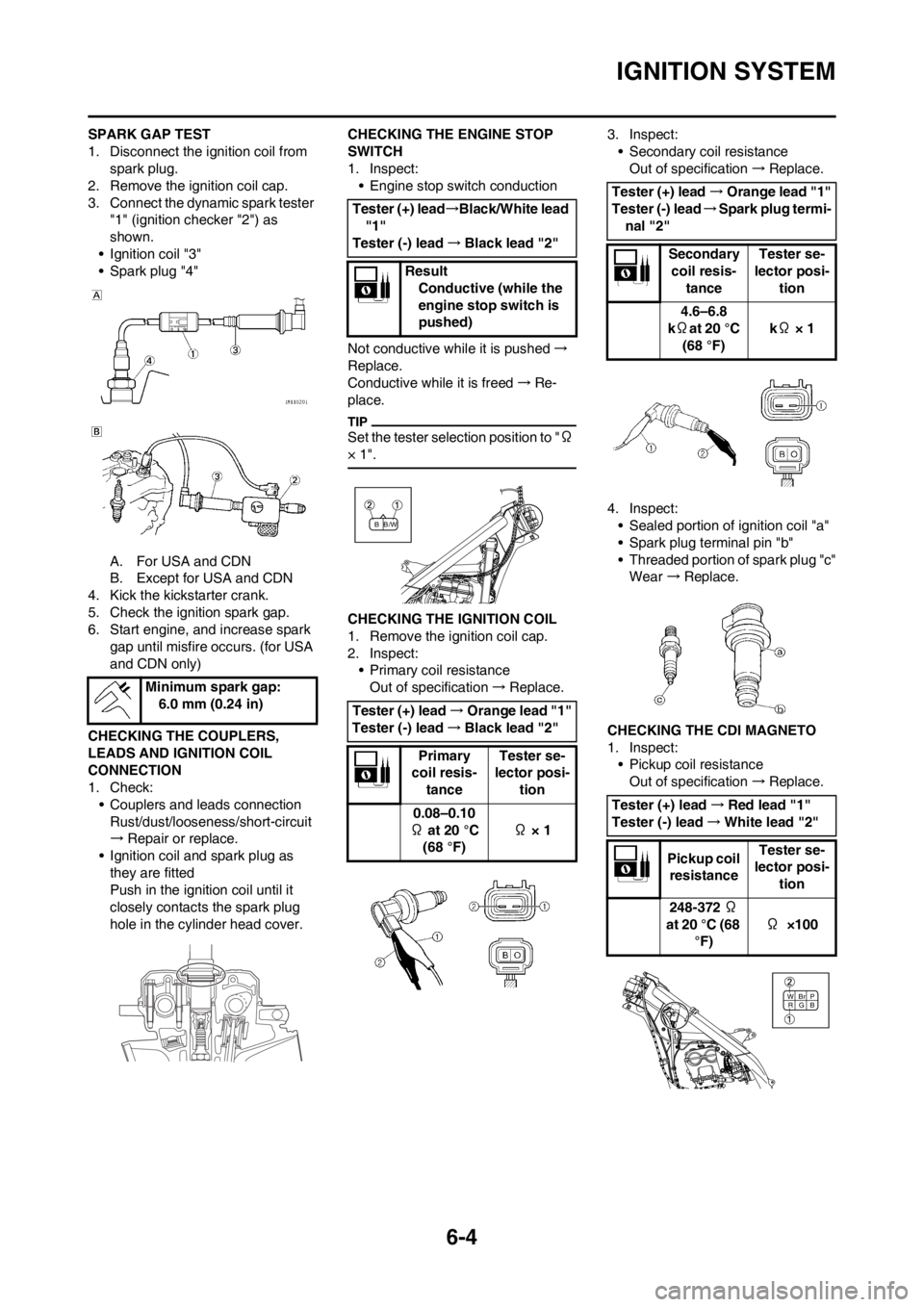
6-4
IGNITION SYSTEM
SPARK GAP TEST
1. Disconnect the ignition coil from
spark plug.
2. Remove the ignition coil cap.
3. Connect the dynamic spark tester
"1" (ignition checker "2") as
shown.
• Ignition coil "3"
• Spark plug "4"
A. For USA and CDN
B. Except for USA and CDN
4. Kick the kickstarter crank.
5. Check the ignition spark gap.
6. Start engine, and increase spark
gap until misfire occurs. (for USA
and CDN only)
CHECKING THE COUPLERS,
LEADS AND IGNITION COIL
CONNECTION
1. Check:
• Couplers and leads connection
Rust/dust/looseness/short-circuit
→Repair or replace.
• Ignition coil and spark plug as
they are fitted
Push in the ignition coil until it
closely contacts the spark plug
hole in the cylinder head cover.CHECKING THE ENGINE STOP
SWITCH
1. Inspect:
• Engine stop switch conduction
Not conductive while it is pushed→
Replace.
Conductive while it is freed→Re-
place.
Set the tester selection position to "Ω
× 1".
CHECKING THE IGNITION COIL
1. Remove the ignition coil cap.
2. Inspect:
• Primary coil resistance
Out of specification→Replace.3. Inspect:
• Secondary coil resistance
Out of specification→Replace.
4. Inspect:
• Sealed portion of ignition coil "a"
• Spark plug terminal pin "b"
• Threaded portion of spark plug "c"
Wear →Replace.
CHECKING THE CDI MAGNETO
1. Inspect:
• Pickup coil resistance
Out of specification→Replace. Minimum spark gap:
6.0 mm (0.24 in)
Tester (+) lead→Black/White lead
"1"
Tester (-) lead→Black lead "2"
Result
Conductive (while the
engine stop switch is
pushed)
Tester (+) lead→Orange lead "1"
Tester (-) lead→Black lead "2"
Primary
coil resis-
tanceTester se-
lector posi-
tion
0.08–0.10
Ω at 20 °C
(68 °F) Ω × 1
/W BB
Tester (+) lead→Orange lead "1"
Tester (-) lead→Spark plug termi-
nal "2"
Secondary
coil resis-
tanceTester se-
lector posi-
tion
4.6–6.8
kΩat 20 °C
(68 °F) kΩ × 1
Tester (+) lead→Red lead "1"
Tester (-) lead→White lead "2"
Pickup coil
resistanceTester se-
lector posi-
tion
248-372 Ω
at 20 °C (68
°F)Ω ×100
B WBr
GP
R
Page 183 of 198
6-5
IGNITION SYSTEM
2. Inspect:
• Charging coil 1 resistance
Out of specification→Replace.
3. Inspect:
• Charging coil 2 resistance
Out of specification→Replace.CHECKING THE NEUTRAL
SWITCH
1. Inspect:
• Neutral switch conduction
Not conductive while it is in neutral→
Replace.
Conductive while it is engaged→Re-
place.
Set the tester selection position to "Ω
× 1".
CHECKING THE CDI UNIT
Check all electrical components. If no
fault is found, replace the CDI unit.
Then check the electrical compo-
nents again. Tester (+) lead→Brown lead "1"
Tester (-) lead→Green lead "2"
Charging
coil 1 resis-
tanceTester se-
lector posi-
tion
720-1,080
Ω at 20 °C
(68 °F)Ω ×100
Tester (+) lead→Pink lead "1"
Tester (-) lead→Black lead "2"
Charging
coil 2 resis-
tanceTester se-
lector posi-
tion
44-66 Ω at
20 °C (68
°F)Ω ×10
B WBr
GP
R
B WBr
GP
R
Tester (+) lead→Sky blue lead "1"
Tester (-) lead→Ground "2"
Result
Conductive (while gear
is in neutral)
Page 184 of 198
6-6
THROTTLE POSITION SENSOR SYSTEM
THROTTLE POSITION SENSOR SYSTEM
INSPECTION STEPS
If the throttle position sensor will not operate, use the following inspection steps.
*marked: Refer to "IGNITION SYSTEM" section.
Use the following special tools in this inspection.
Check entire ignition system for connection. No good→Repair or replace.
OK↓
Check throttle position sensor. (Throttle position
sensor coil)No good→
Replace.
OK↓
*Check CDI magneto. (Charging coil) No good→Replace.
OK↓
Check CDI unit. (Throttle position sensor input
voltage)No good→
Replace.
Pocket tester:
YU-3112-C/90890-03112