Page 564 of 715
03-73010-00
1. OVERVIEW
The hydraulic clutch transmits the force required to operate the clutch pedal to the concentric
slave cylinder fitted to the clutch housing as a hydraulic pressure.
(The hydraulic pressure is transmitted in the following order: Clutch pedal - Clutch master cylinder
- Clutch pipe - Clutch damper - Clutch pipe and hose - Concentric slave cylinder - Pressure
plate - Flywheel.)
If a driver depress the clutch pedal, the hydraulic pressure is generated in the master cylinder. It is
transmitted to the concentric slave cylinder through the pipe, resulting in the cylinder being forced
out. At this time, the clutch disc is forced against the cylinder by pushing the cover. This, in turn,
remove the flywheel from the pressure plate. As a consequence, the power from the engine will be
cut off and the gear change can be carried out.
Page 566 of 715
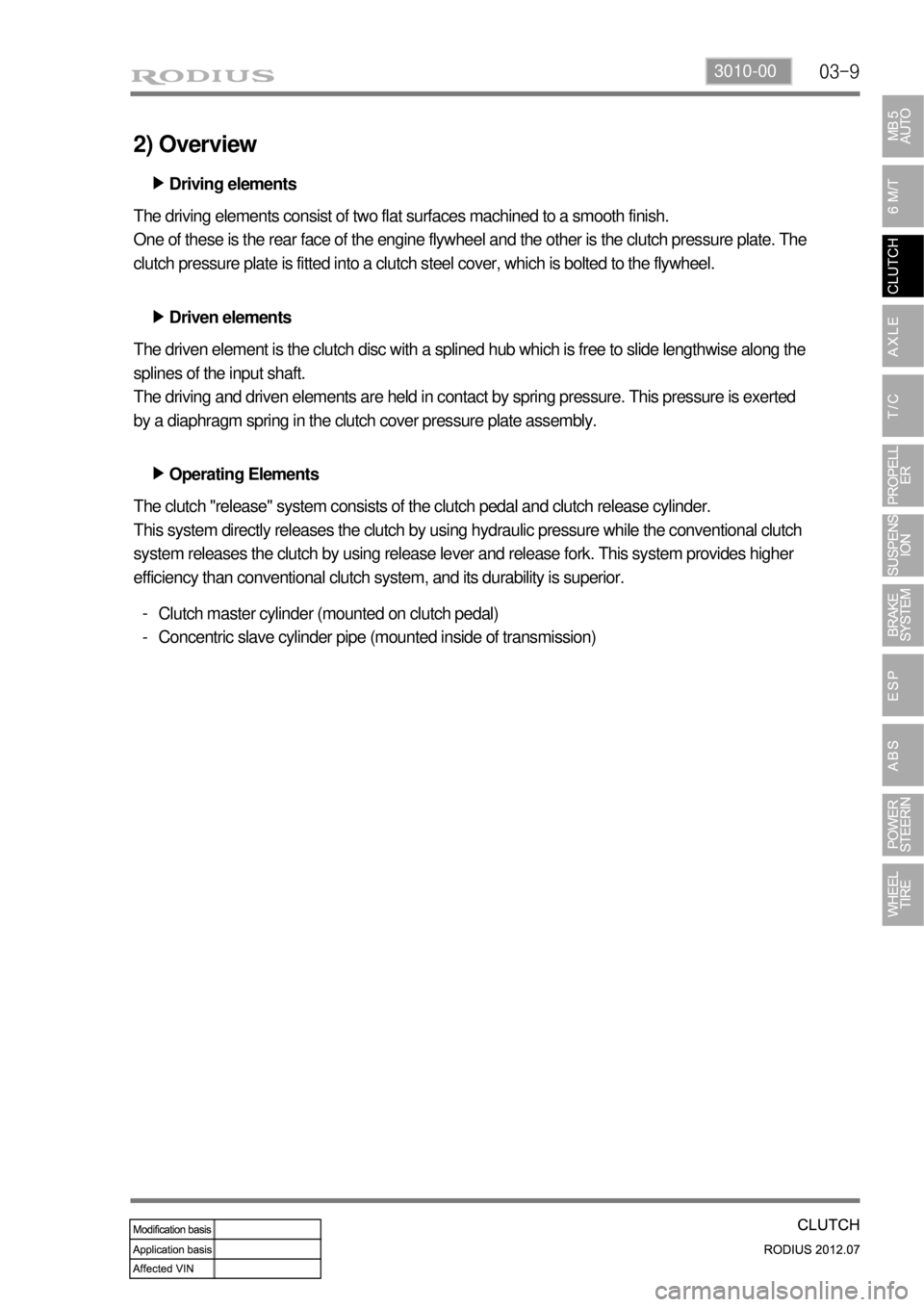
03-93010-00
2) Overview
Driving elements ▶
The driving elements consist of two flat surfaces machined to a smooth finish.
One of these is the rear face of the engine flywheel and the other is the clutch pressure plate. The
clutch pressure plate is fitted into a clutch steel cover, which is bolted to the flywheel.
Driven elements ▶
The driven element is the clutch disc with a splined hub which is free to slide lengthwise along the
splines of the input shaft.
The driving and driven elements are held in contact by spring pressure. This pressure is exerted
by a diaphragm spring in the clutch cover pressure plate assembly.
Operating Elements ▶
The clutch "release" system consists of the clutch pedal and clutch release cylinder.
This system directly releases the clutch by using hydraulic pressure while the conventional clutch
system releases the clutch by using release lever and release fork. This system provides higher
efficiency than conventional clutch system, and its durability is superior.
Clutch master cylinder (mounted on clutch pedal)
Concentric slave cylinder pipe (mounted inside of transmission) -
-
Page 568 of 715
03-113010-00
3. DUAL MASS FLYWHEEL (DMF)
The dual mass flywheel (DMF) is of having a mass divided into two halves.
While one mass is connected to the engine crankshaft, which is affected by the mass moment of
inertia of the engine, the other mass is affected by one of the transmission.
The divided dual masses are connected to the coil spring and damping system internally.
The DMF has the following benefits: ▶
Reducing fuel consumption by lowering engine speed
Reducing rattling noise and vehicle vibration in all driving ranges
Reducing synchronization wear
Facilitating gear change
Protecting power train parts by preventing excessive load from being delivered -
-
-
-
-
Primary flywheel
Secondary flywheel
Arc damper spring
Torque limiter
Ring gear 1.
2.
3.
4.
5.
Page 569 of 715
04-34120-01
1. SPECIFICATIONS
Front Axle ▶
Rear Axle ▶
Description Specification
Drive shaft type CV joint
Axle housing type Build up
DifferentialType Conventional type
Gear type Hypoid Gear
Final gear reduction ratioEngine + M/T 3.54
Engine + A/T 4.55
OilCapacity 1.2L
Specification SAE 80W / 90
Description Specification
Axle shaft type Semi-floating
Axle housing type Build up
DifferentialType Conventional type
Gear type Hypoid Gear
Final gear reduction ratioEngine + M/T 3.54
Engine + A/T 4.55
OilCapacity 1.7L
Specification SAE 80W / 90
Page 587 of 715
07-4
3. MAJOR CHANGES
Front Sub Frame
Old New
The engine mounting insulators (A) have been changed according to newly equipped engine
(D20DTR). It improves the durability and NVH.
Front Knuckle Assembly
Old New
The front knuckle assembly has been changed according to new 4WD system (Part-time T/C).
Hub bearingLocking hub
actuator
Page 598 of 715
08-70000-00
Problem Cause Action
Burning smell
around tireToo frequent braking in high driving speed Reduce the use of
foot brake/use
engine brake
properly sed only foot brake during downhill driving
Driving with foot on brake pedal Get off the foot
from pedal
Foreign materials such as dirt or sand in brake system Replace: caliper,
wheel cylinder,
master cylinder,
return spring
Broken return spring in shoe assembly Replace
Incorrectly adjusted parking brake cable Adjust
Incorrect wheel or wheel cover
(generating the heat)Replace
Page 602 of 715
08-114850-03
Let the engine run for 1 to 2 minutes and
stop it. If the brake pedal stroke is
shortened as pumping the brake pedal,
the system is normal. If not, the system is
defective.
Depress the brake pedal several times with
engine off. If the brake goes down when
starting engine with pedal depressed, the
system is normal. If not, the system is
defective. 1.
2.
Depress the brake pedal when the engine
is running. If the pedal height is not
changed for 30 seconds after stopping the
engine, the system is normal. If not, the
system is defective. 3.
If the above three checks are OK, the system
is normal. If any condition is not met, check
the valve, vacuum hose and brake booster.
3) Brake Booster
OK
NG
Engine stopped
Engine running
Page 619 of 715
09-114891-01
(3) ESP Control
The ESP (Electronic Stability Program) has been developed to help a driver avoid danger of losing
control of the vehicle stability due to understeer or oversteer during cornering. The yaw rate sensor,
lateral sensor and longitudinal sensor in the sensor cluster and the steering wheel angle sensor
under the steering column detect the vehicle conditions when the inner or outer wheels are
spinning during oversteer, understeer or cornering. The ESP ECU controls against oversteer or
understeer during cornering by controlling the vehicle stability using input values from these
sensors and applying the braking force to the corresponding wheels independently. The system
also controls the engine power right before the wheel spin synchronized to decelerate the vehicle
automatically in order to maintain the vehicle stable during cornering.