Page 356 of 600
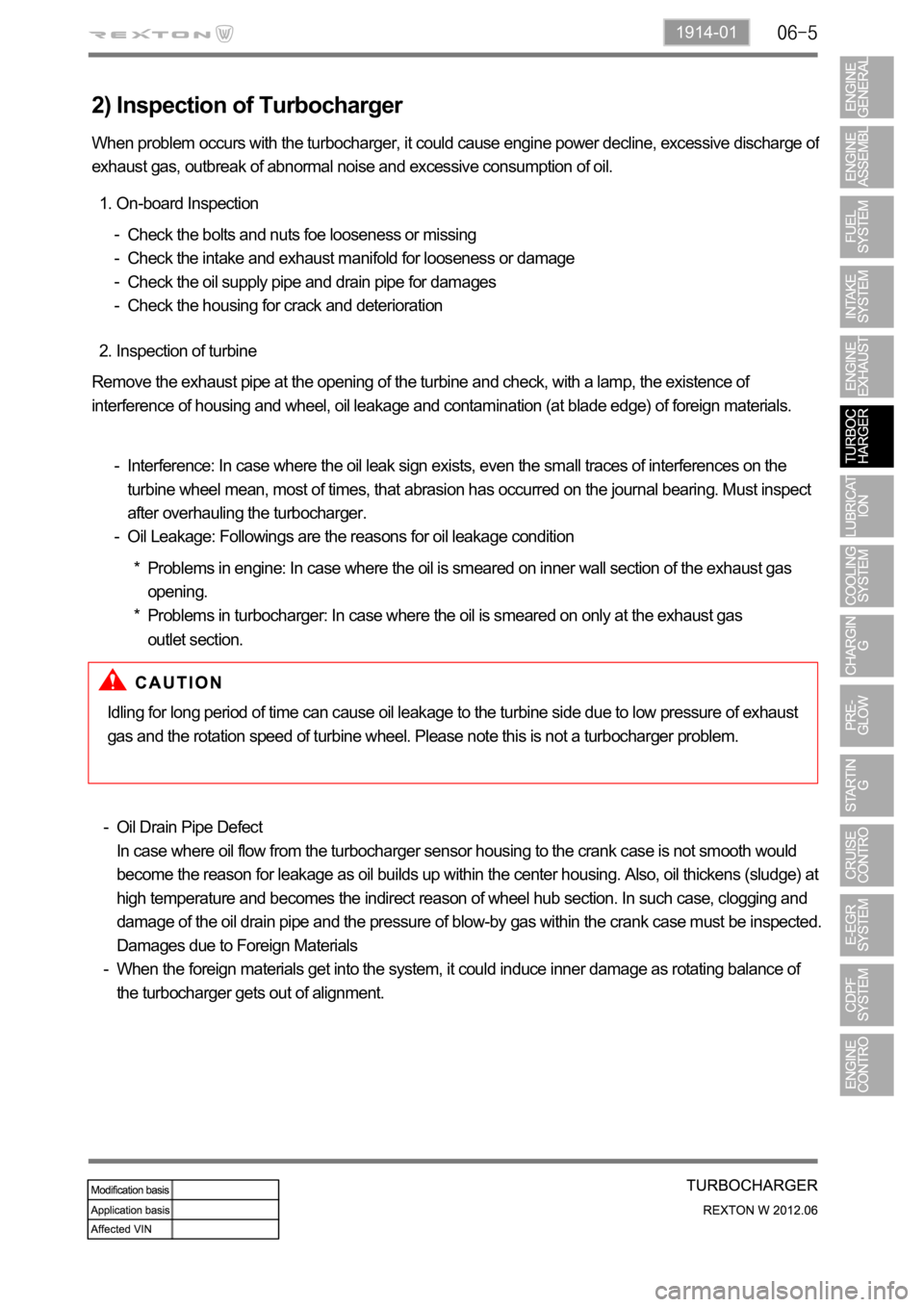
1914-01
2) Inspection of Turbocharger
When problem occurs with the turbocharger, it could cause engine power decline, excessive discharge of
exhaust gas, outbreak of abnormal noise and excessive consumption of oil.
On-board Inspection 1.
Check the bolts and nuts foe looseness or missing
Check the intake and exhaust manifold for looseness or damage
Check the oil supply pipe and drain pipe for damages
Check the housing for crack and deterioration -
-
-
-
Inspection of turbine 2.
Remove the exhaust pipe at the opening of the turbine and check, with a lamp, the existence of
interference of housing and wheel, oil leakage and contamination (at blade edge) of foreign materials.
Interference: In case where the oil leak sign exists, even the small traces of interferences on the
turbine wheel mean, most of times, that abrasion has occurred on the journal bearing. Must inspect
after overhauling the turbocharger.
Oil Leakage: Followings are the reasons for oil leakage condition -
-
Idling for long period of time can cause oil leakage to the turbine side due to low pressure of exhaust
gas and the rotation speed of turbine wheel. Please note this is not a turbocharger problem.
Oil Drain Pipe Defect
In case where oil flow from the turbocharger sensor housing to the crank case is not smooth would
become the reason for leakage as oil builds up within the center housing. Also, oil thickens (sludge) at
high temperature and becomes the indirect reason of wheel hub section. In such case, clogging and
damage of the oil drain pipe and the pressure of blow-by gas within the crank case must be inspected.
Damages due to Foreign Materials
When the foreign materials get into the system, it could induce inner damage as rotating balance of
the turbocharger gets out of alignment. -
-Problems in engine: In case where the oil is smeared on inner wall section of the exhaust gas
opening.
Problems in turbocharger: In case where the oil is smeared on only at the exhaust gas
outlet section. *
*
Page 357 of 600
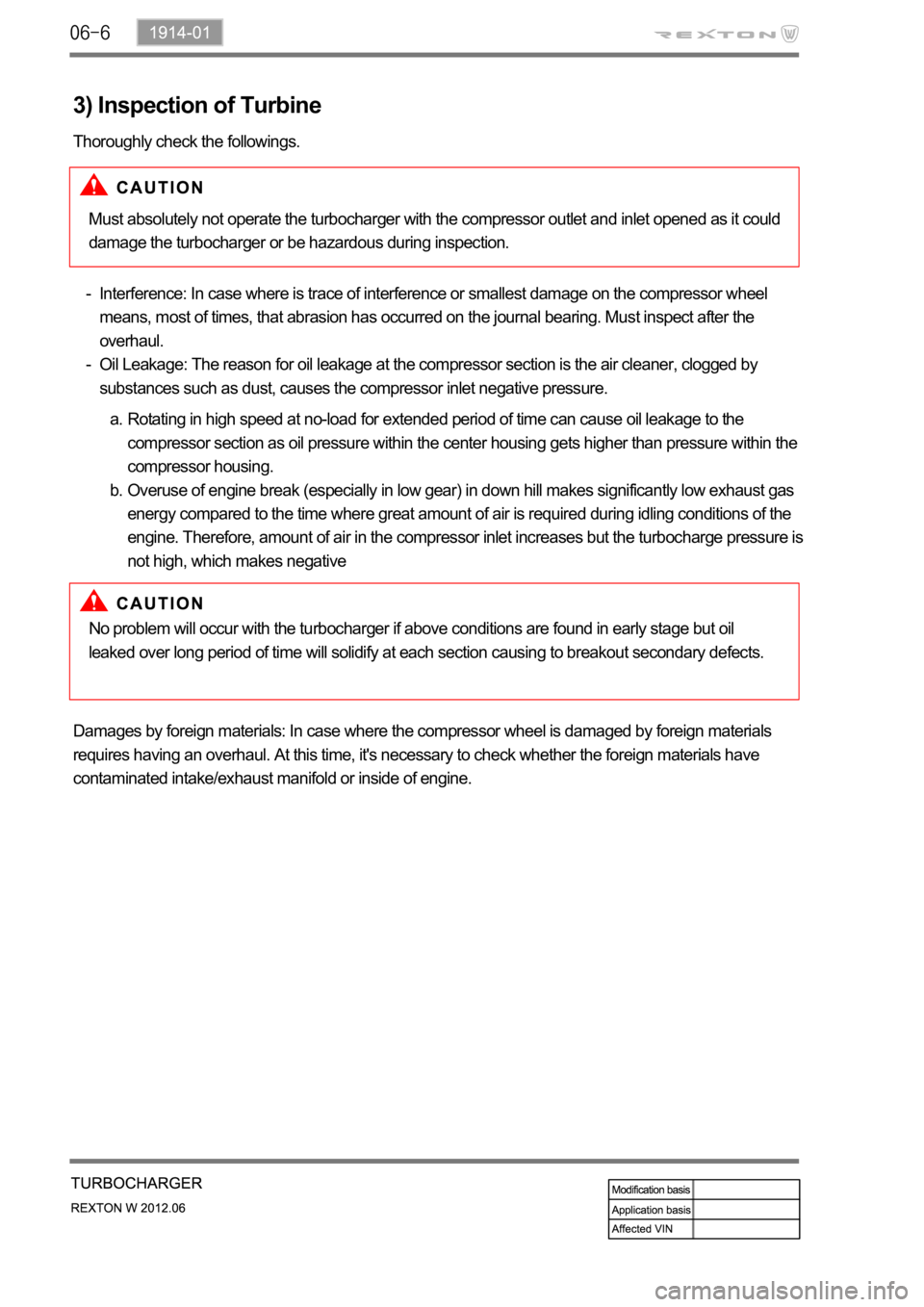
3) Inspection of Turbine
Thoroughly check the followings.
Must absolutely not operate the turbocharger with the compressor outlet and inlet opened as it could
damage the turbocharger or be hazardous during inspection.
Interference: In case where is trace of interference or smallest damage on the compressor wheel
means, most of times, that abrasion has occurred on the journal bearing. Must inspect after the
overhaul.
Oil Leakage: The reason for oil leakage at the compressor section is the air cleaner, clogged by
substances such as dust, causes the compressor inlet negative pressure. -
-
Rotating in high speed at no-load for extended period of time can cause oil leakage to the
compressor section as oil pressure within the center housing gets higher than pressure within the
compressor housing.
Overuse of engine break (especially in low gear) in down hill makes significantly low exhaust gas
energy compared to the time where great amount of air is required during idling conditions of the
engine. Therefore, amount of air in the compressor inlet increases but the turbocharge pressure is
not high, which makes negative a.
b.
No problem will occur with the turbocharger if above conditions are found in early stage but oil
leaked over long period of time will solidify at each section causing to breakout secondary defects.
Damages by foreign materials: In case where the compressor wheel is damaged by foreign materials
requires having an overhaul. At this time, it's necessary to check whether the foreign materials have
contaminated intake/exhaust manifold or inside of engine.
Page 360 of 600
1914-01
Turbine Side: Inflow of foreign materials from engine
Compressor Side: such as air filter, muffler and nut 3.
Page 362 of 600
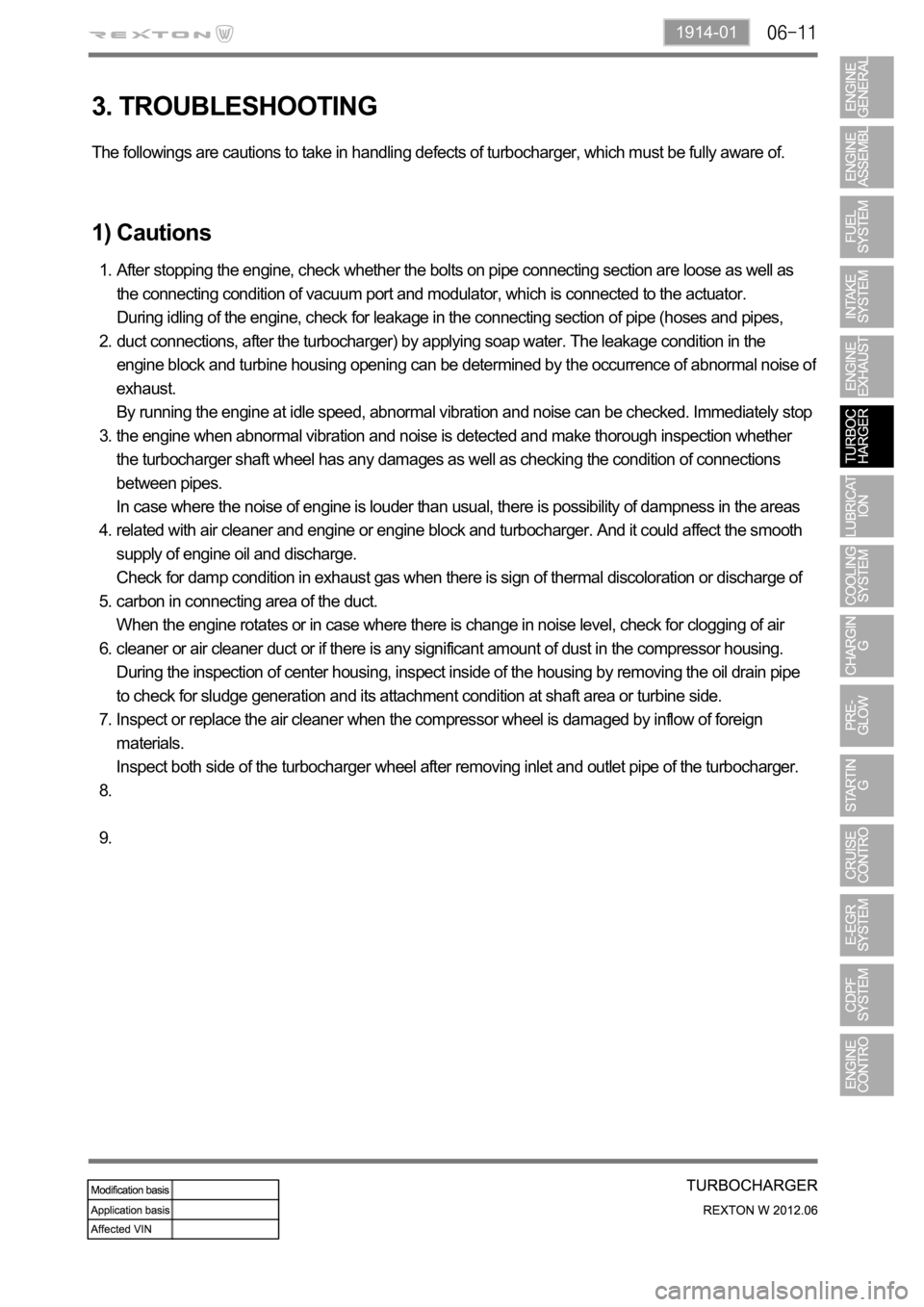
1914-01
3. TROUBLESHOOTING
The followings are cautions to take in handling defects of turbocharger, which must be fully aware of.
1) Cautions
After stopping the engine, check whether the bolts on pipe connecting section are loose as well as
the connecting condition of vacuum port and modulator, which is connected to the actuator.
During idling of the engine, check for leakage in the connecting section of pipe (hoses and pipes,
duct connections, after the turbocharger) by applying soap water. The leakage condition in the
engine block and turbine housing opening can be determined by the occurrence of abnormal noise o
f
exhaust.
By running the engine at idle speed, abnormal vibration and noise can be checked. Immediately stop
the engine when abnormal vibration and noise is detected and make thorough inspection whether
the turbocharger shaft wheel has any damages as well as checking the condition of connections
between pipes.
In case where the noise of engine is louder than usual, there is possibility of dampness in the areas
related with air cleaner and engine or engine block and turbocharger. And it could affect the smooth
supply of engine oil and discharge.
Check for damp condition in exhaust gas when there is sign of thermal discoloration or discharge of
carbon in connecting area of the duct.
When the engine rotates or in case where there is change in noise level, check for clogging of air
cleaner or air cleaner duct or if there is any significant amount of dust in the compressor housing.
During the inspection of center housing, inspect inside of the housing by removing the oil drain pipe
to check for sludge generation and its attachment condition at shaft area or turbine side.
Inspect or replace the air cleaner when the compressor wheel is damaged by inflow of foreign
materials.
Inspect both side of the turbocharger wheel after removing inlet and outlet pipe of the turbocharger. 1.
2.
3.
4.
5.
6.
7.
8.
9.
Page 368 of 600
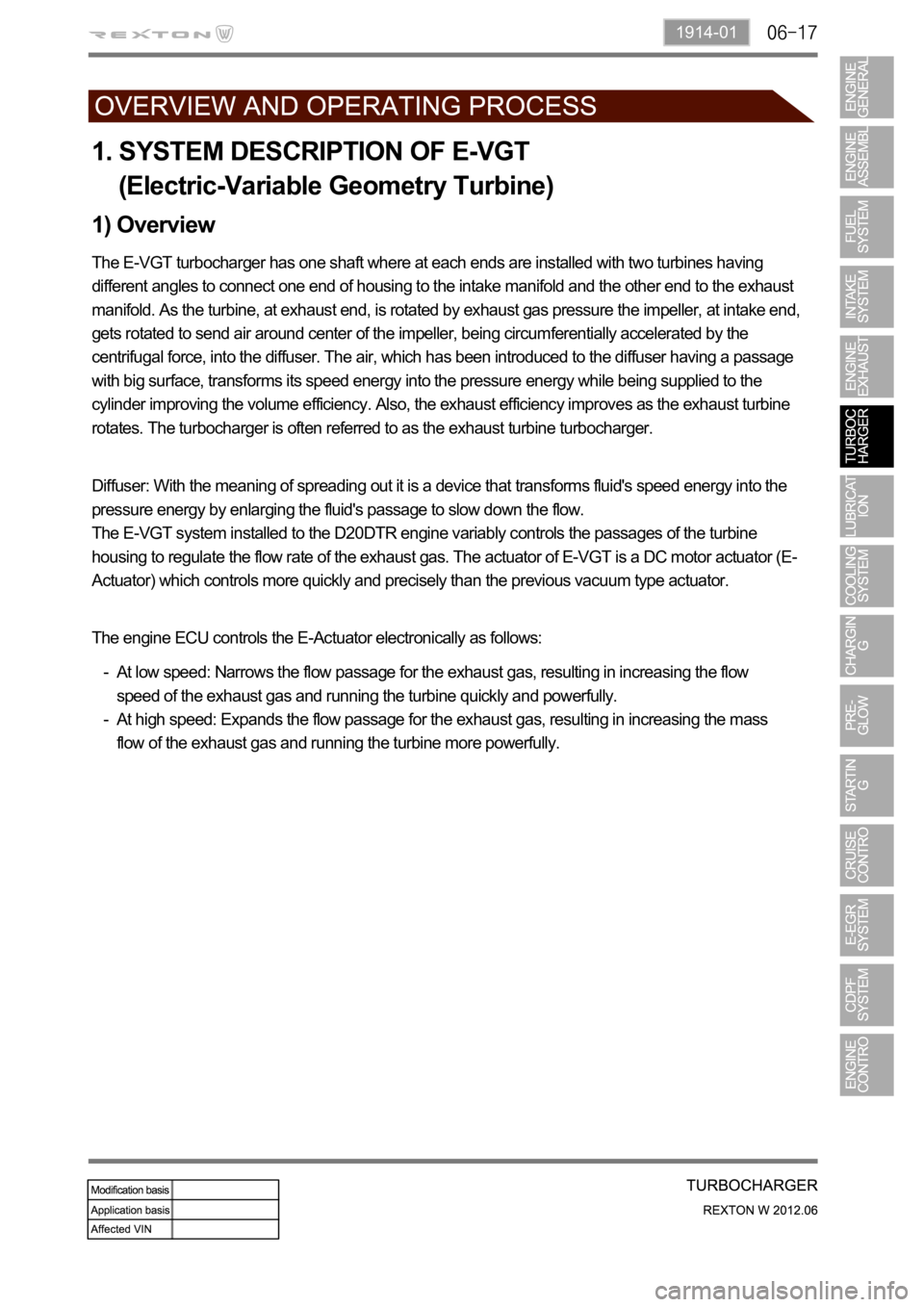
1914-01
1. SYSTEM DESCRIPTION OF E-VGT
(Electric-Variable Geometry Turbine)
The E-VGT turbocharger has one shaft where at each ends are installed with two turbines having
different angles to connect one end of housing to the intake manifold and the other end to the exhaust
manifold. As the turbine, at exhaust end, is rotated by exhaust gas pressure the impeller, at intake end,
gets rotated to send air around center of the impeller, being circumferentially accelerated by the
centrifugal force, into the diffuser. The air, which has been introduced to the diffuser having a passage
with big surface, transforms its speed energy into the pressure energy while being supplied to the
cylinder improving the volume efficiency. Also, the exhaust efficiency improves as the exhaust turbine
rotates. The turbocharger is often referred to as the exhaust turbine turbocharger.
1) Overview
Diffuser: With the meaning of spreading out it is a device that transforms fluid's speed energy into the
pressure energy by enlarging the fluid's passage to slow down the flow.
The E-VGT system installed to the D20DTR engine variably controls the passages of the turbine
housing to regulate the flow rate of the exhaust gas. The actuator of E-VGT is a DC motor actuator (E-
Actuator) which controls more quickly and precisely than the previous vacuum type actuator.
The engine ECU controls the E-Actuator electronically as follows:
At low speed: Narrows the flow passage for the exhaust gas, resulting in increasing the flow
speed of the exhaust gas and running the turbine quickly and powerfully.
At high speed: Expands the flow passage for the exhaust gas, resulting in increasing the mass
flow of the exhaust gas and running the turbine more powerfully. -
-
Page 370 of 600
1914-01
E-VGT turbocharger
Improves engine power
2. COMPONENTS
Engine ECU (D20DTR)
E-VGT duty controlAccelerator pedal position
sensor
Transfers driver's will to
accelerate to ECU
Atmospheric pressure, RPM
signal
HFM sensor
Improves the engine powerCoolant temperature sensor
Operates the VGT according to
engine warm-upT-MAP sensor
Booster pressure and
temperature
Page 372 of 600
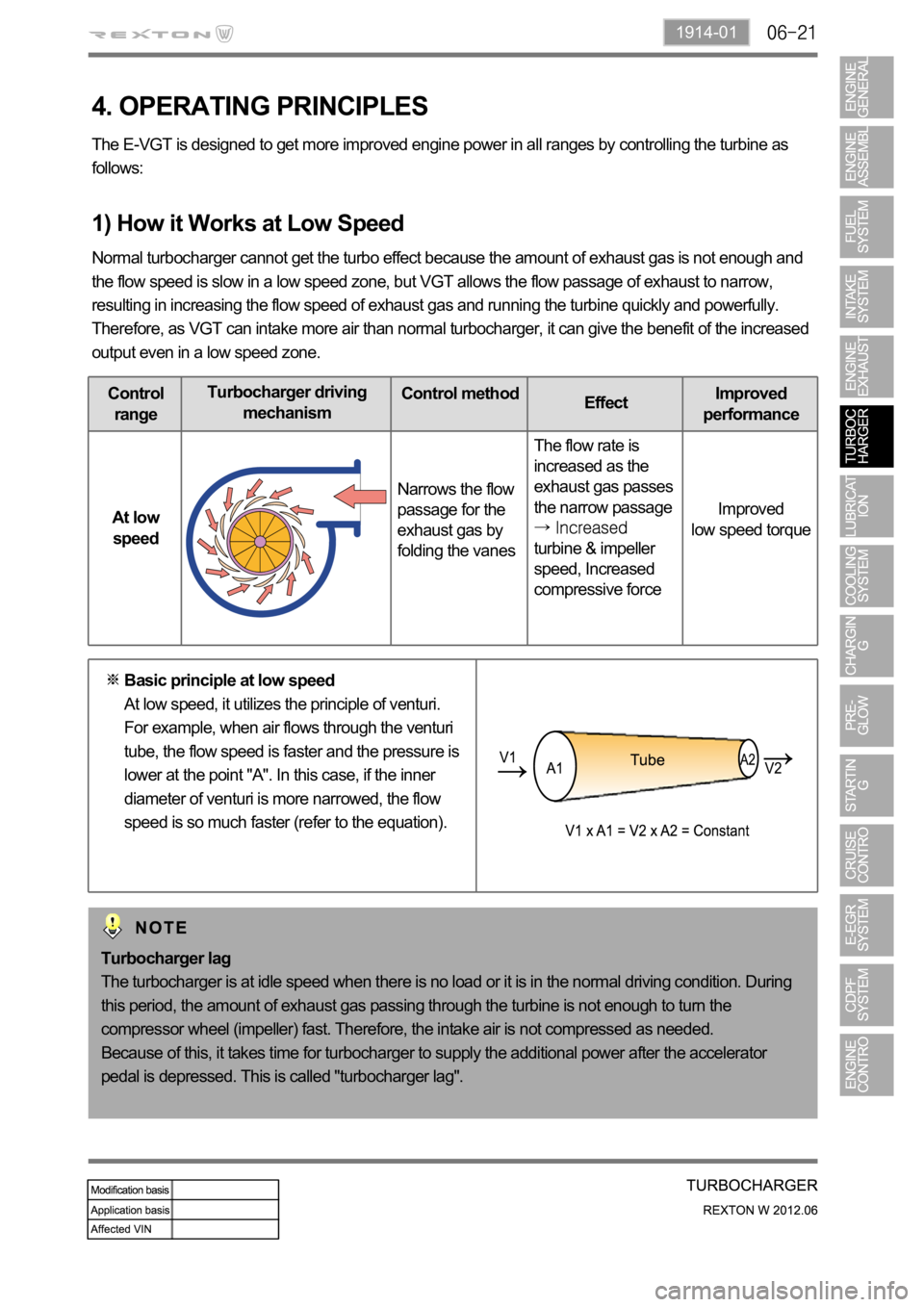
1914-01
Control
rangeTurbocharger driving
mechanismControl method
EffectImproved
performance
At low
speedNarrows the flow
passage for the
exhaust gas by
folding the vanesThe flow rate is
increased as the
exhaust gas passes
the narrow passage
turbine & impeller
speed, Increased
compressive forceImproved
low speed torque
4. OPERATING PRINCIPLES
The E-VGT is designed to get more improved engine power in all ranges by controlling the turbine as
follows:
1) How it Works at Low Speed
Normal turbocharger cannot get the turbo effect because the amount of exhaust gas is not enough and
the flow speed is slow in a low speed zone, but VGT allows the flow passage of exhaust to narrow,
resulting in increasing the flow speed of exhaust gas and running the turbine quickly and powerfully.
Therefore, as VGT can intake more air than normal turbocharger, it can give the benefit of the increased
output even in a low speed zone.
Turbocharger lag
The turbocharger is at idle speed when there is no load or it is in the normal driving condition. During
this period, the amount of exhaust gas passing through the turbine is not enough to turn the
compressor wheel (impeller) fast. Therefore, the intake air is not compressed as needed.
Because of this, it takes time for turbocharger to supply the additional power after the accelerator
pedal is depressed. This is called "turbocharger lag". Basic principle at low speed
At low speed, it utilizes the principle of venturi.
For example, when air flows through the venturi
tube, the flow speed is faster and the pressure is
lower at the point "A". In this case, if the inner
diameter of venturi is more narrowed, the flow
speed is so much faster (refer to the equation).
Page 374 of 600
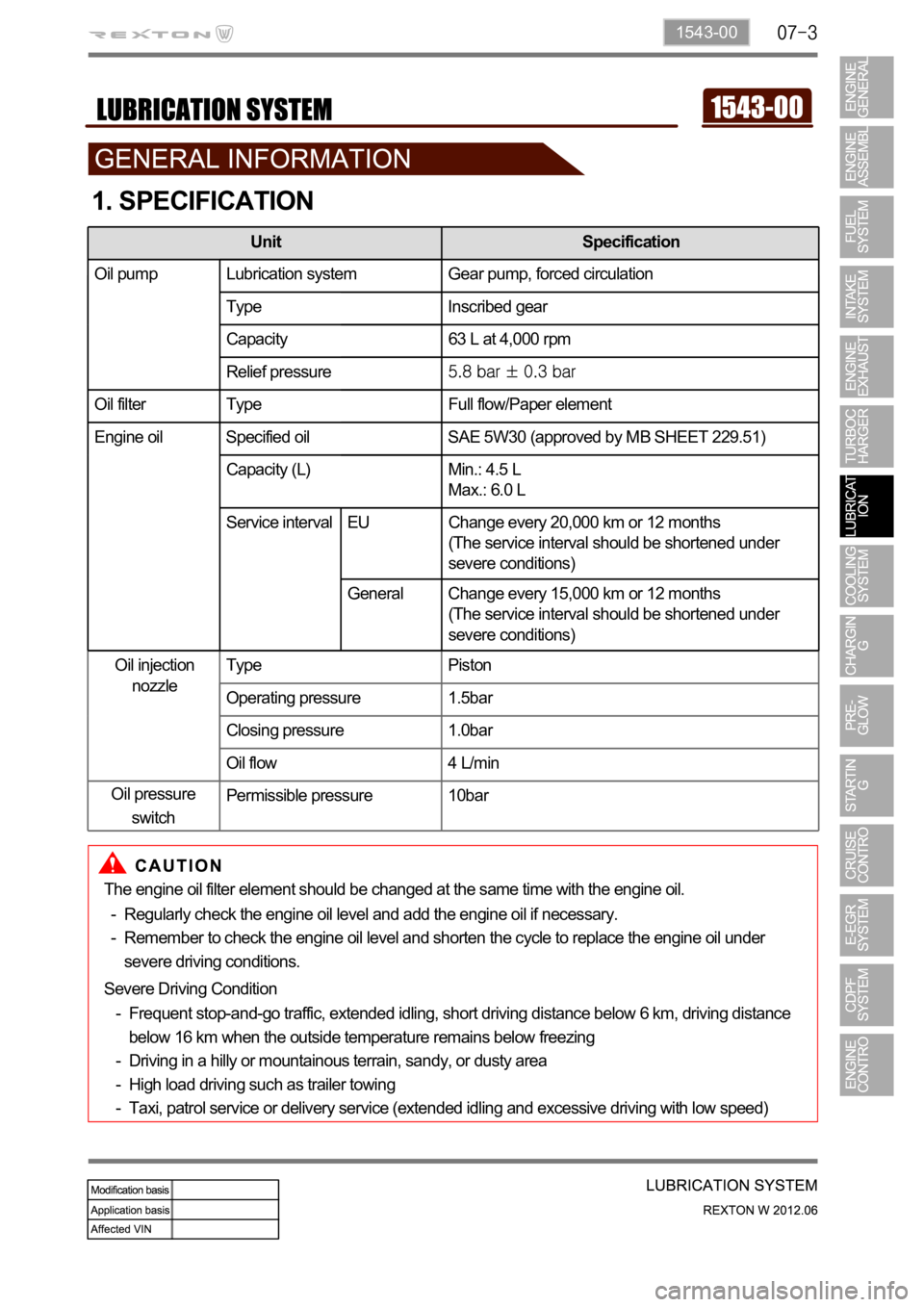
1543-00
1. SPECIFICATION
The engine oil filter element should be changed at the same time with the engine oil.
Regularly check the engine oil level and add the engine oil if necessary.
Remember to check the engine oil level and shorten the cycle to replace the engine oil under
severe driving conditions. -
-
Severe Driving Condition
Frequent stop-and-go traffic, extended idling, short driving distance below 6 km, driving distance
below 16 km when the outside temperature remains below freezing
Driving in a hilly or mountainous terrain, sandy, or dusty area
High load driving such as trailer towing
Taxi, patrol service or delivery service (extended idling and excessive driving with low speed) -
-
-
-
Unit Specification
Oil pump Lubrication system Gear pump, forced circulation
Type Inscribed gear
Capacity 63 L at 4,000 rpm
Relief pressure
Oil filter Type Full flow/Paper element
Engine oil Specified oil SAE 5W30 (approved by MB SHEET 229.51)
Capacity (L) Min.: 4.5 L
Max.: 6.0 L
Service interval Change every 15,000 km or 12 months (But, shorten
the service interval under severe condition)
Oil injection
nozzleType Piston
Operating pressure 1.5bar
Closing pressure 1.0bar
Oil flow 4 L/min
Permissible pressure 10bar
Unit Specification
Oil pump Lubrication system Gear pump, forced circulation
Type Inscribed gear
Capacity 63 L at 4,000 rpm
Relief pressure
Oil filter Type Full flow/Paper element
Engine oil Specified oil SAE 5W30 (approved by MB SHEET 229.51)
Capacity (L) Min.: 4.5 L
Max.: 6.0 L
Service interval EU Change every 20,000 km or 12 months
(The service interval should be shortened under
severe conditions)
General Change every 15,000 km or 12 months
(The service interval should be shortened under
severe conditions)
Oil pressure
switch