Page 334 of 600
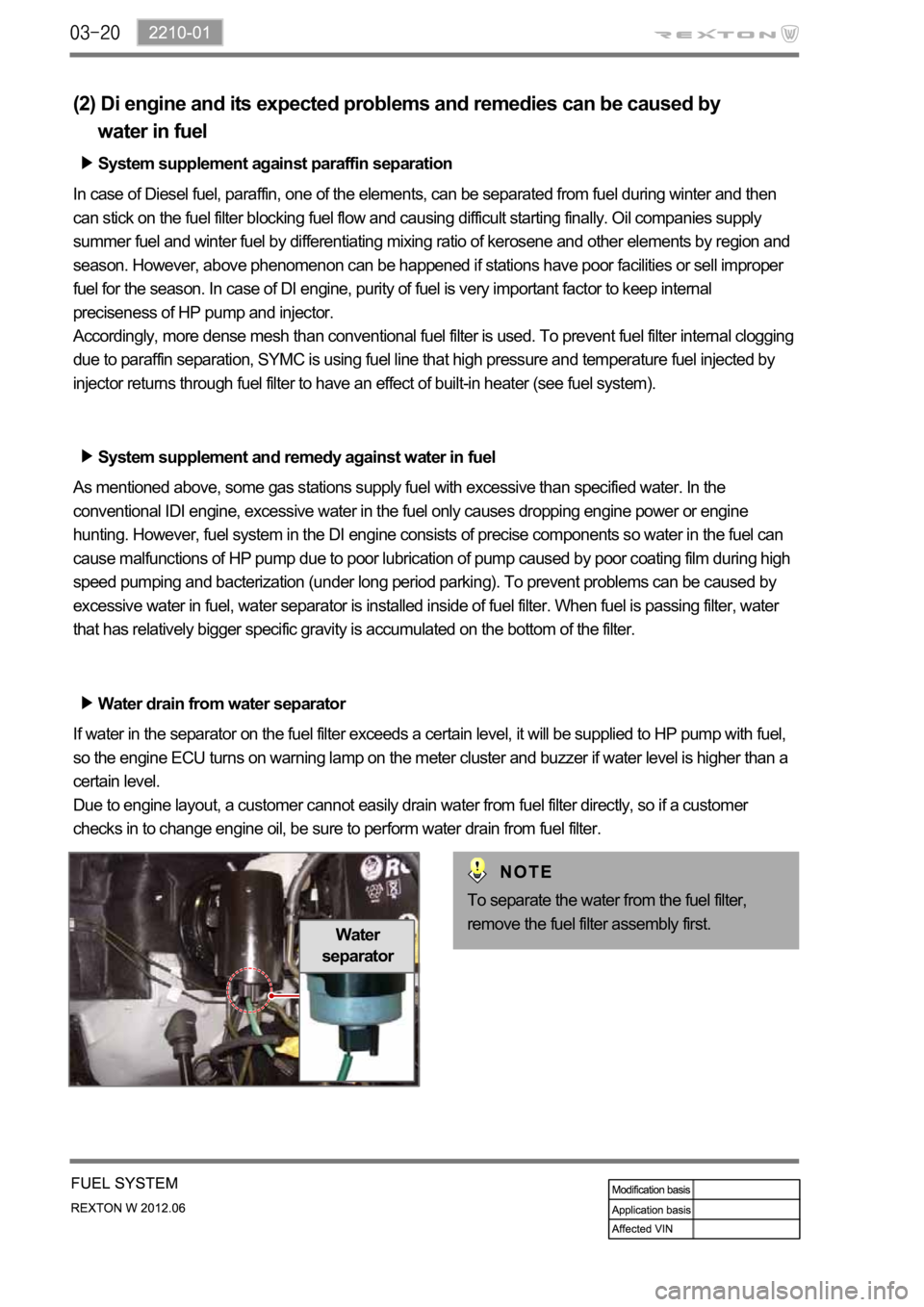
(2) Di engine and its expected problems and remedies can be caused by
water in fuel
System supplement against paraffin separation
In case of Diesel fuel, paraffin, one of the elements, can be separated from fuel during winter and then
can stick on the fuel filter blocking fuel flow and causing difficult starting finally. Oil companies supply
summer fuel and winter fuel by differentiating mixing ratio of kerosene and other elements by region and
season. However, above phenomenon can be happened if stations have poor facilities or sell improper
fuel for the season. In case of DI engine, purity of fuel is very important factor to keep internal
preciseness of HP pump and injector.
Accordingly, more dense mesh than conventional fuel filter is used. To prevent fuel filter internal clogging
due to paraffin separation, SYMC is using fuel line that high pressure and temperature fuel injected by
injector returns through fuel filter to have an effect of built-in heater (see fuel system).
System supplement and remedy against water in fuel
As mentioned above, some gas stations supply fuel with excessive than specified water. In the
conventional IDI engine, excessive water in the fuel only causes dropping engine power or engine
hunting. However, fuel system in the DI engine consists of precise components so water in the fuel can
cause malfunctions of HP pump due to poor lubrication of pump caused by poor coating film during high
speed pumping and bacterization (under long period parking). To prevent problems can be caused by
excessive water in fuel, water separator is installed inside of fuel filter. When fuel is passing filter, water
that has relatively bigger specific gravity is accumulated on the bottom of the filter.
Water drain from water separator
If water in the separator on the fuel filter exceeds a certain level, it will be supplied to HP pump with fuel,
so the engine ECU turns on warning lamp on the meter cluster and buzzer if water level is higher than a
certain level.
Due to engine layout, a customer cannot easily drain water from fuel filter directly, so if a customer
checks in to change engine oil, be sure to perform water drain from fuel filter.
Water
separator
To separate the water from the fuel filter,
remove the fuel filter assembly first.
Page 335 of 600
2210-01
1. OVERVIEW
The components in fuel system supply the fuel and generate the high pressure to inject the fuel to each
injector. They are controlled by the engine ECU.
The common rail fuel injection system consists of fuel tank, fuel line, low pressure line which supplies low
pressure fuel to the low pressure pump (including high pressure pump), common rail which distributes
and accumulates the high pressurized fuel from the fuel pump, high pressure line which connected to
the injector, and the engine control unit (ECU) which calculates the accelerator pedal position and
controls the overall performance of vehicle based on the input signals from various sensors.
1) Fuel Flow Diagram
Page 336 of 600
Fuel tank
Fuel metering by sender
2. SYSTEM LAYOUT AND OPERATION
1) Layout
For sensor and actuator control logic, refer to Chapter "Engine Control".
Engine ECU (D20DTR)
Engine control by various
signals
Crankshaft position sensor
Measuring engine rpm
Injector (C3I)
Pre-injection, main injection,
after-injection by signals from
ECU
HFM sensor
Measuring intake air mass and
temperature
Camshaft position sensor
Determining injection order
Page 337 of 600
2210-01
Accelerator pedal position
sensor
Detecting driver's intention
for speed up/down
Fuel rail assembly
Relieving the pulsation.
Measuring the fuel pressure.
Distributing the fuel to injectors.
Fuel filter assembly
Supplying clean fuel/fuel
heating/water separation by
priming pump
Plunger type HP pump (1,800 bar)
Vane type LP pump (6 bar)
T-MAP sensor
Measuring booster pressure
and temperature
High pressure pump
Generating high pressurized fuel and
supplying it according to engine rpm,
required volume, required pressure
Page 339 of 600
2210-01
3) Input/Output devices
Refer to Chapter "Engine Control". *
Page 340 of 600
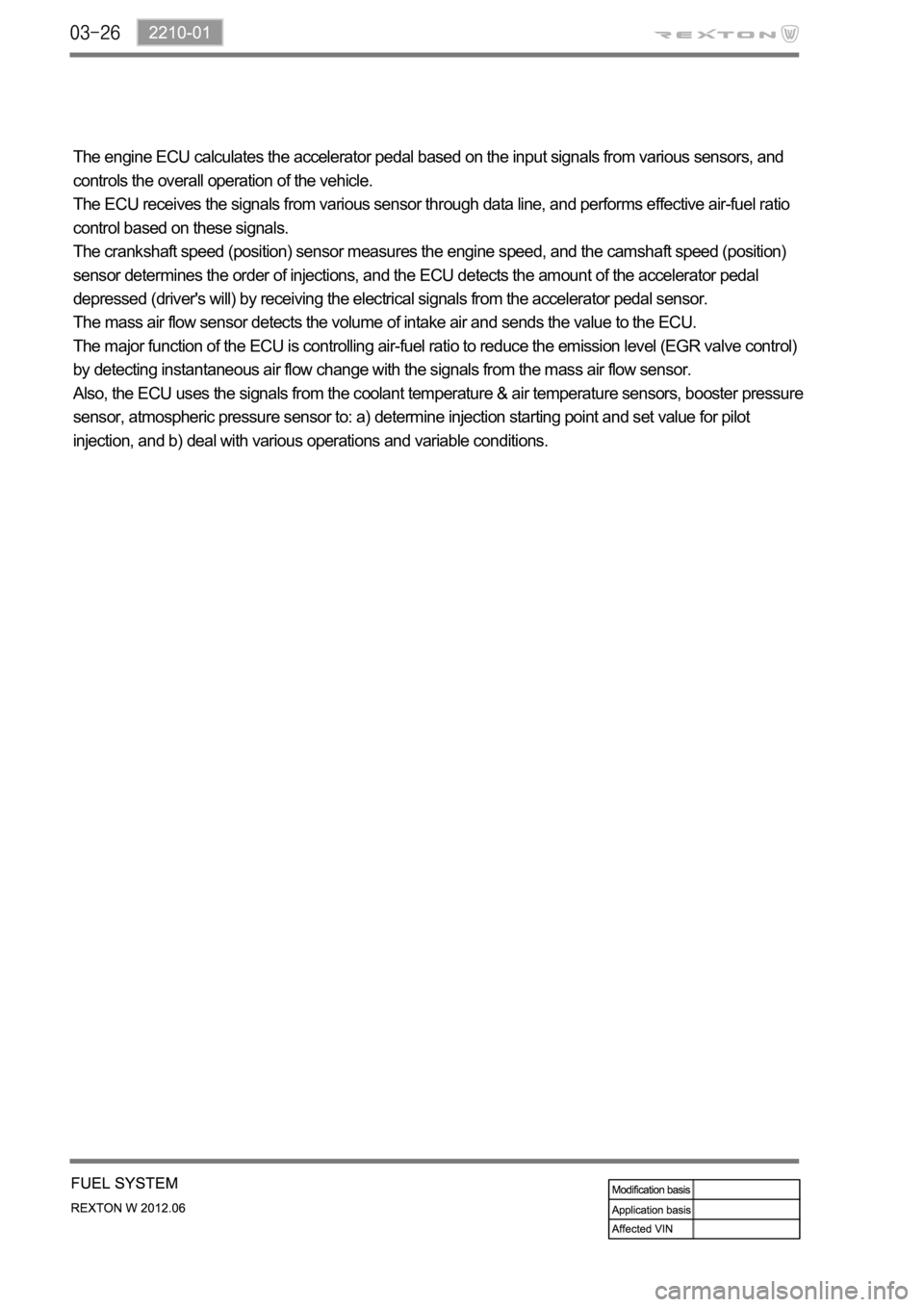
The engine ECU calculates the accelerator pedal based on the input signals from various sensors, and
controls the overall operation of the vehicle.
The ECU receives the signals from various sensor through data line, and performs effective air-fuel ratio
control based on these signals.
The crankshaft speed (position) sensor measures the engine speed, and the camshaft speed (position)
sensor determines the order of injections, and the ECU detects the amount of the accelerator pedal
depressed (driver's will) by receiving the electrical signals from the accelerator pedal sensor.
The mass air flow sensor detects the volume of intake air and sends the value to the ECU.
The major function of the ECU is controlling air-fuel ratio to reduce the emission level (EGR valve control)
by detecting instantaneous air flow change with the signals from the mass air flow sensor.
Also, the ECU uses the signals from the coolant temperature & air temperature sensors, booster pressure
sensor, atmospheric pressure sensor to: a) determine injection starting point and set value for pilot
injection, and b) deal with various operations and variable conditions.
Page 342 of 600
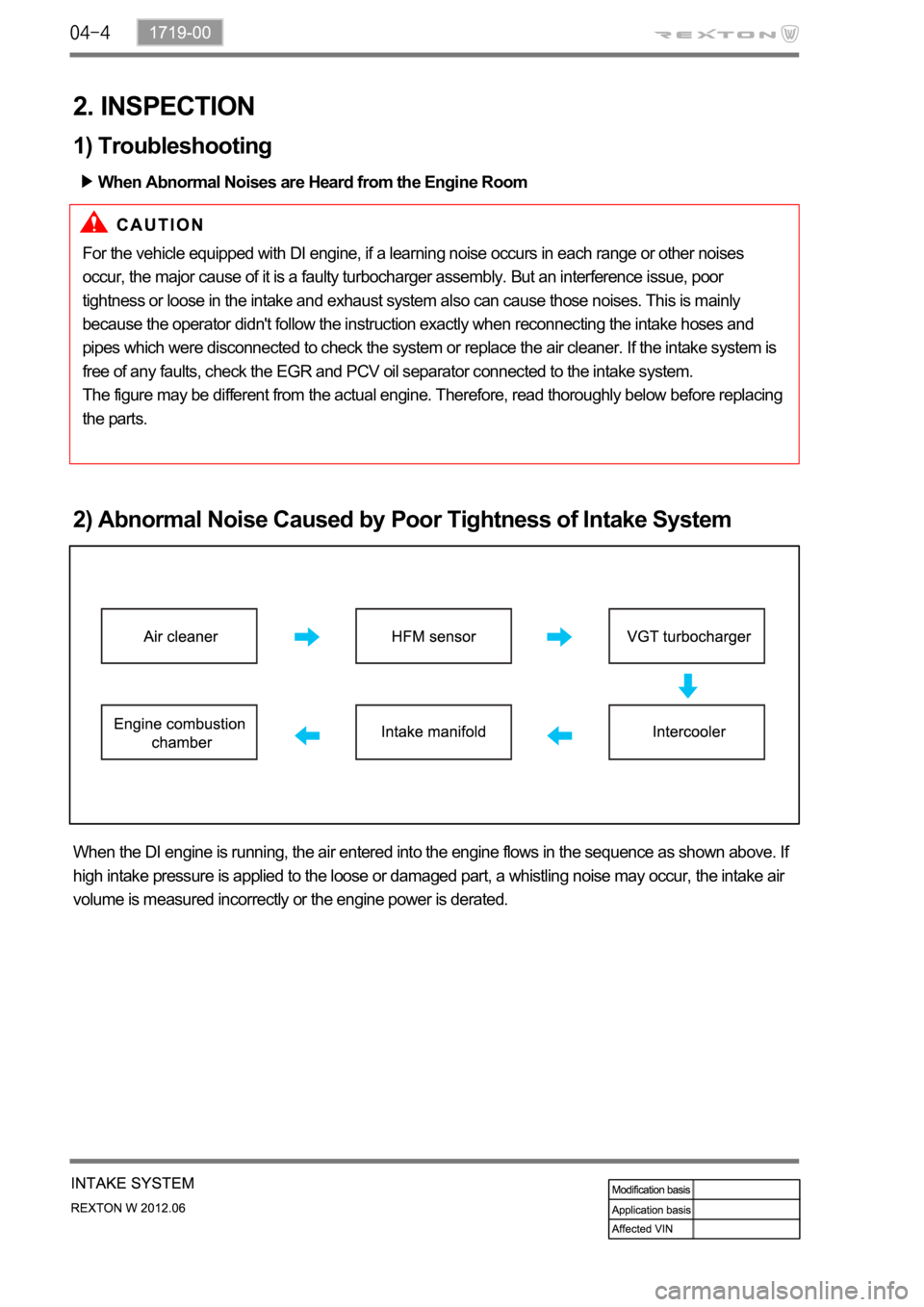
2. INSPECTION
1) Troubleshooting
When Abnormal Noises are Heard from the Engine Room
For the vehicle equipped with DI engine, if a learning noise occurs in each range or other noises
occur, the major cause of it is a faulty turbocharger assembly. But an interference issue, poor
tightness or loose in the intake and exhaust system also can cause those noises. This is mainly
because the operator didn't follow the instruction exactly when reconnecting the intake hoses and
pipes which were disconnected to check the system or replace the air cleaner. If the intake system is
free of any faults, check the EGR and PCV oil separator connected to the intake system.
The figure may be different from the actual engine. Therefore, read thoroughly below before replacing
the parts.
2) Abnormal Noise Caused by Poor Tightness of Intake System
When the DI engine is running, the air entered into the engine flows in the sequence as shown above. If
high intake pressure is applied to the loose or damaged part, a whistling noise may occur, the intake air
volume is measured incorrectly or the engine power is derated.
Page 343 of 600
1719-00
3) Troubleshooting Sequence
The basic checks for intake system are as follows:
Basic Checks for Intake System
Make sure to replace or clean the air cleaner
element periodically. Otherwise, engine will be
derated or work abnormally because of low
intake air volume.
Unlike the fuel system, which is a closed
circuit, the intake system is an open circuit
system. Therefore any malfunction may occur
due to dust and dirt.
Most of the connections consist of hoses so
the system cannot withstand high temperature
and pressure. Also it can be deformed or
loosened easily because it is a clamp
mounting system. Thus, when checking the
engine, basic inspections, such as tightened
status check and visual inspection for hose,
etc., should be carried out in advance.
Other Checks for Intake System
If the intake system is free of any faults, check
for EGR and PCV oil separator.