Page 118 of 828
02-90000-00
1336-01 Timing gear case cover
Added the belt tension mounting boss
1130-01 Crankshaft assembly
- Reduced weight
- Deleted ring gear
1130-18 Drive plate assembly (A/T)
Changed the location of torque converter
mounting hole1130-13 Dual mass flywheel
Deleted centering sleeve
1115-02 Engine mounting bracket
D20DTR (Actyon Sports)
OldNew
OldNew
OldNew
Old
New
OldNew
with center bearingwithout center
bearing
Page 120 of 828
02-110000-00
3160-01 Manual transmission
Added 5 and 6-speed transmission
3680-01 Automatic transmission
Changed the torque conver & torque converter housing due to new engine
OldNew
OldNew
2412-02 CDPF
Introduced CDPF to meet EURO-5
regulation
2411-01 DOC
Introduced DOC to meet EURO III or
EURO IV regulation.
G23D
D20DTR
Page 131 of 828
01-10
5. STANDARD BOLTS SPECIFICATIONS
Metric bolt strength is embossed on the head of each bolt. The strength of bolt can be
classified as 4T, 7T, 8.8T, 10.9T, 11T and 12.9T in general.
Observe standard tightening torque during bolt tightening works and can adjust torque to be
proper within 15 % if necessary. Try not to over max. allowable tightening torque if not required
to do so.
Determine extra proper tightening torque if tightens with washer or packing.
If tightens bolts on the below materials, be sure to determine the proper torque. 1)
2)
3)
4)
Aluminum alloy: Tighten to 80 % of above torque table.
Plastics: Tighten to 20 % of above torque table. -
-
Page 138 of 828
01-170000-00
Name: Oil pan gasket
remover
Use to separate oil pan and
minimize damage when
removing oil pan.
Name: Torque angle gauge
Use to angle-tighten correctly
after torque-tightening
Name & Part number Tool How to use
Name: Engine stand (1 tone
or more)
Use to fix the removed engine
or engine with transmission.
Name: Engine crane (1 tone
or more)
Use to move the engine
module (including
transmission) to working
space or engine stand.
2. NORMAL EQUIPMENTS
Page 141 of 828
02-4
2. TIGHTENING TORQUE
Component SizeBolt
QuantitySpecified torque
(Nm)Remark
(Total torque)
Main bearing capM12×8210 55±5Nm,
180˚Not re-usable
Connecting rod capM9×52840±5Nm,
90˚+10˚50 to 80 Nm
Rear coverM6×20610 ± 1 Nm-
Oil pumpM8×35SOC325 ± 2.5 Nm-
FlywheelM10×22845 ± 5 Nm,
90˚+10˚60 to 100 Nm
Crankshaft center boltM20×851200 ± 20 Nm,
180˚+20˚660 to 720 Nm
Not re-usable
Oil panM6×201810 ± 1 Nm-
M6×35210 ± 1 Nm-
M6×85210 ± 1 Nm-
M6×120210 ± 1 Nm-
M8×40225 ± 2.5 Nm-
HP pump main nutM14×1.5-8-1165 ± 5 Nm-
HP pump boltM8×55325 ± 2.5 Nm-
Cylinder headM13×15012 85Nm
270°±10°-
Camshaft capM6×301610 ± 1 Nm -
M8×60425 ± 2.5 Nm -
Exhaust stud bolt 1015±1.5Nm-
Exhaust sprocket boltM11×40130 ± 3 Nm -
Chain tensioner screw
boltM38×1.5 125±2.5Nm -
Coolant temperature
sensor120±2.0Nm -
Auto tensionerM8×30(LOW) 125±2.5Nm -
M10×75(Upper) 155±5.5Nm -
Coolant pumpM6×50 110±1.0Nm -
Page 142 of 828
02-50000-00
Component SizeBolt
QuantitySpecified torque
(Nm)Remark
(Total torque)
Hot water inlet pipeM6×16 2 10±1Nm -
AlternatorM10×90 1 25±2.5Nm -
M10×116 1 46±4.6Nm -
A/C bracketM8×25 4 7.8~11.8Nm -
A/C sub bracketM6×25 4 10±1Nm -
Intake manifoldM8×35 2 25±2.5Nm -
M8×110 6 25±2.5Nm -
Oil filter moduleM8×40 6 25±2.5Nm -
M8×20 1 25±2.5Nm -
M8×140 2 25±2.5Nm -
Knock sensorM8×28 2 20±5Nm -
Cam position sensorM8×14 1 10~14Nm -
Booster pressure
sensorM6×20 2 10±1Nm -
Exhaust manifold M8 10 40±4Nm -
Turbocharger M8 3 25±2.5Nm -
Support bolt 1 25±2.5Nm -
Support nut M8 1 25±2.5Nm -
T/C oil supply pipe M6(block side) 1 10±1.0Nm -
M6(turbo side) 1 17±2.0Nm -
T/C oil return pipeM6×16(turbo side)2 10±1Nm -
M6×16(block side)2 10±1Nm -
EGR valveM8×22 2 25±2.5Nm -
EGR pipe bolt
(Intake side)M8×16 2
25±2.5Nm -
EGR pipe bolt
(EGR cooler side)M8×16 2 25±2.5Nm -
EGR combination boltM6×16 4 10±1Nm -
M8×16 16 25±2.5Nm -
Idle pulley/Tensioner
pulley1 45±4.5Nm -
Page 143 of 828
02-6
Component SizeBolt
QuantitySpecified torque
(Nm)Remark
(Total torque)
Glow plug M5 4 20±2Nm -
Vacuum pumpM8×25 3 10±1Nm -
Timing gear case coverM12×55 3 85±8.5Nm -
M6×25 7 10±1Nm -
M6×45 1 10±1Nm -
M6×50 3 10±1Nm -
Cylinder head coverM6×35 21 10±1Nm -
Oil gauge tubeM6×16 1 10±1Nm -
Oil filter cap 1 25±2.5Nm -
Fuel railM8×35SOC 2 25±2.5Nm -
Injector clamp boltM6×60 2 10±1Nm,
120˚+10˚ -
High pressure pipe
(between HP pump and
fuel rail)M17 1 30±3Nm -
High pressure pipe
(between fuel rail and
injector)M17 4 30±3Nm -
Crank position sensorM5×14 1 8±0.4Nm -
Main wiringM6×16 5 10±1Nm -
Intake duct M8x25 4 25±2.5Nm -
Power steering pumpM8×100 3 25±2.5Nm -
Cylinder head front
coverM6×10 5 10±1Nm -
Ladder frameM8×16 5 30±3Nm -
Oil pumpM8×35 3 25±2.5Nm
-
Page 148 of 828
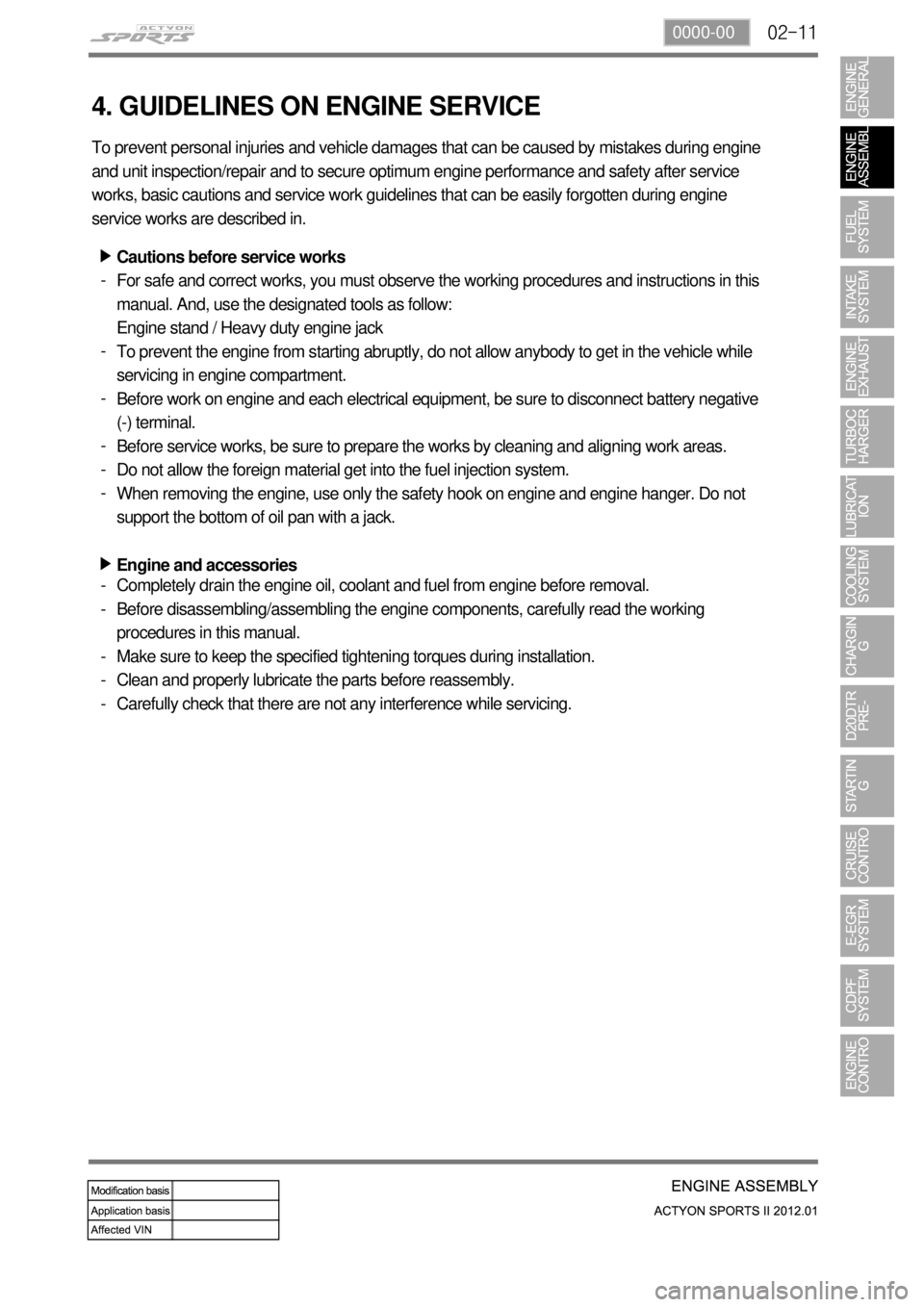
02-110000-00
4. GUIDELINES ON ENGINE SERVICE
To prevent personal injuries and vehicle damages that can be caused by mistakes during engine
and unit inspection/repair and to secure optimum engine performance and safety after service
works, basic cautions and service work guidelines that can be easily forgotten during engine
service works are described in.
Cautions before service works
For safe and correct works, you must observe the working procedures and instructions in this
manual. And, use the designated tools as follow:
Engine stand / Heavy duty engine jack
To prevent the engine from starting abruptly, do not allow anybody to get in the vehicle while
servicing in engine compartment.
Before work on engine and each electrical equipment, be sure to disconnect battery negative
(-) terminal.
Before service works, be sure to prepare the works by cleaning and aligning work areas.
Do not allow the foreign material get into the fuel injection system.
When removing the engine, use only the safety hook on engine and engine hanger. Do not
support the bottom of oil pan with a jack.
Engine and accessories ▶
-
-
-
-
-
-
▶
Completely drain the engine oil, coolant and fuel from engine before removal.
Before disassembling/assembling the engine components, carefully read the working
procedures in this manual.
Make sure to keep the specified tightening torques during installation.
Clean and properly lubricate the parts before reassembly.
Carefully check that there are not any interference while servicing. -
-
-
-
-