Page 719 of 828
11-18
6. HYDRAULIC CIRCUIT OF ESP
MCP: Master Cylinder Primary
MCS: Master Cylinder Secondary
ESV: Electric Shuttle Valve
NO: Normal Open
NC: Normal Close
LPA: Low Pressure Accumulator
Page 720 of 828
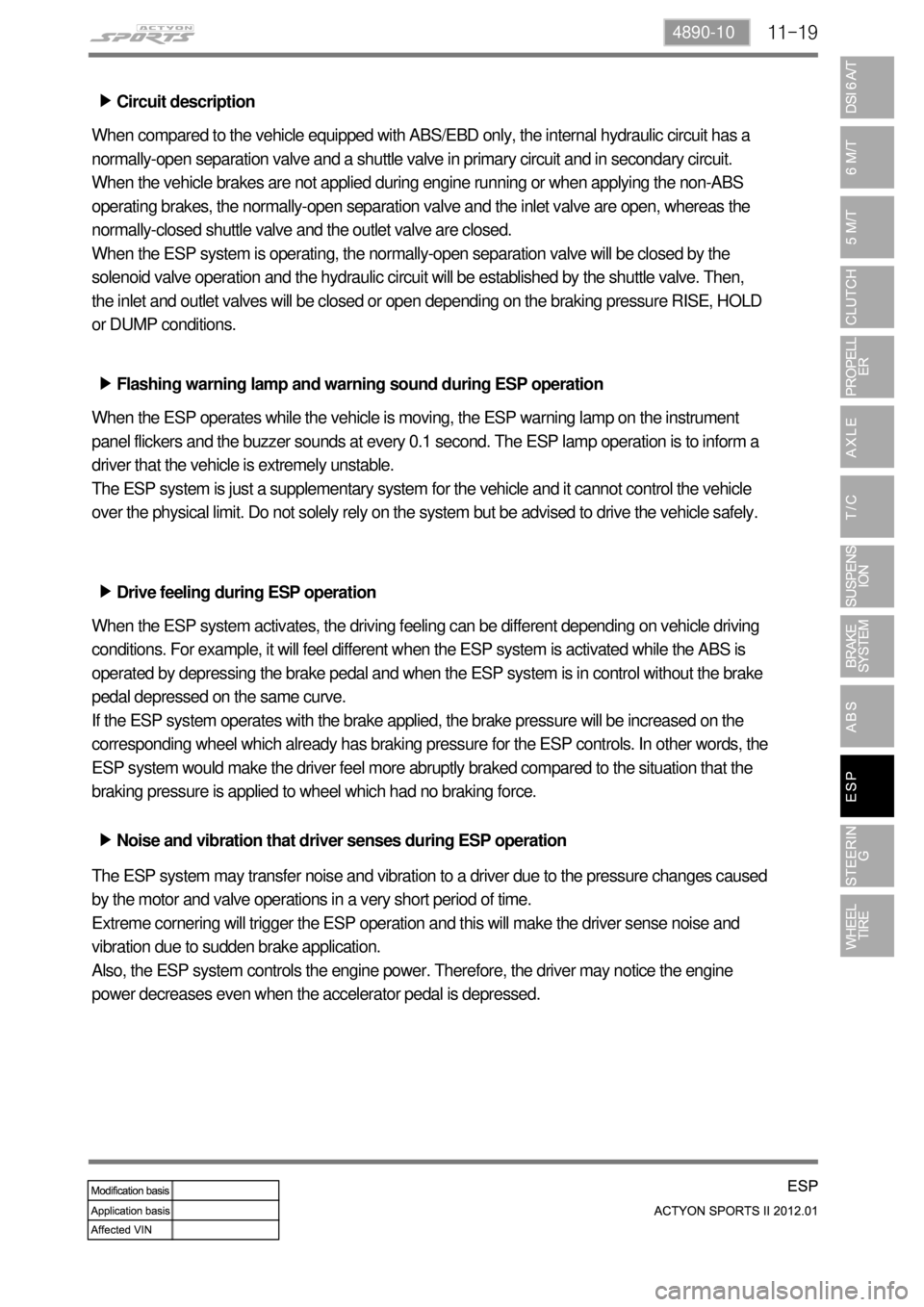
11-194890-10
Circuit description ▶
When compared to the vehicle equipped with ABS/EBD only, the internal hydraulic circuit has a
normally-open separation valve and a shuttle valve in primary circuit and in secondary circuit.
When the vehicle brakes are not applied during engine running or when applying the non-ABS
operating brakes, the normally-open separation valve and the inlet valve are open, whereas the
normally-closed shuttle valve and the outlet valve are closed.
When the ESP system is operating, the normally-open separation valve will be closed by the
solenoid valve operation and the hydraulic circuit will be established by the shuttle valve. Then,
the inlet and outlet valves will be closed or open depending on the braking pressure RISE, HOLD
or DUMP conditions.
Flashing warning lamp and warning sound during ESP operation ▶
When the ESP operates while the vehicle is moving, the ESP warning lamp on the instrument
panel flickers and the buzzer sounds at every 0.1 second. The ESP lamp operation is to inform a
driver that the vehicle is extremely unstable.
The ESP system is just a supplementary system for the vehicle and it cannot control the vehicle
over the physical limit. Do not solely rely on the system but be advised to drive the vehicle safely.
Drive feeling during ESP operation ▶
When the ESP system activates, the driving feeling can be different depending on vehicle driving
conditions. For example, it will feel different when the ESP system is activated while the ABS is
operated by depressing the brake pedal and when the ESP system is in control without the brake
pedal depressed on the same curve.
If the ESP system operates with the brake applied, the brake pressure will be increased on the
corresponding wheel which already has braking pressure for the ESP controls. In other words, the
ESP system would make the driver feel more abruptly braked compared to the situation that the
braking pressure is applied to wheel which had no braking force.
Noise and vibration that driver senses during ESP operation ▶
The ESP system may transfer noise and vibration to a driver due to the pressure changes caused
by the motor and valve operations in a very short period of time.
Extreme cornering will trigger the ESP operation and this will make the driver sense noise and
vibration due to sudden brake application.
Also, the ESP system controls the engine power. Therefore, the driver may notice the engine
power decreases even when the accelerator pedal is depressed.
Page 722 of 828
11-214890-10
2) DUMP (ESP is working) Mode
The pressure decreases just before the wheel speed drops and the wheels are locked.
The inlet valve closes and the outlet valve opens as in the ABS HECU and the oil is gathered at
the low pressure chamber while no additional oil is being supplied. Then the pump operates to
allow fast oil drainage. The shuttle valve and the separation valve do not operate while
decompression.
Page 723 of 828
11-22
3) HOLD (ESP is working) Mode
The Inlet valve and outlet valve will be closed to maintain the pressure in the hydraulic circuit
applied at the wheels. By closing the valves, the hydraulic pressure at the wheels will not be lost
or supplied any more. During ESP operation, the separation valve closes and only the shuttle valve
at the pump opens.
Page 724 of 828
11-234890-10
4) RISE (ESP is working) Mode
The shuttle valve and inlet valve will be open and the separation valve and outlet valve will be
closed. Then, the pump is operated. When ESP operates while the ABS is operating, the
pressure will be increased continuously until just before the corresponding wheel gets locked.
Page 725 of 828
11-24
5) Hydraulic Circuit of HBA
The above figure shows one front and one rear wheel and the same hydraulic circuit forms as in
the ESP operation. When HECU recognizes that it is an emergency and it is required for hard
braking, depending on the pressure value of the brake pressure sensor and pressure changes
caused by the pressure sensor timing, it operates the pump immediately to apply the brake
pressure at the wheels. Then, the pressure in the pump increases until just before the
corresponding wheel gets locked. The motor still keeps rotating and the outlet valve and the
separation valve will stay closed. When the wheel starts to lock, the HBA function cancels and
switches to ABS operation.
Page 728 of 828
Page 758 of 828
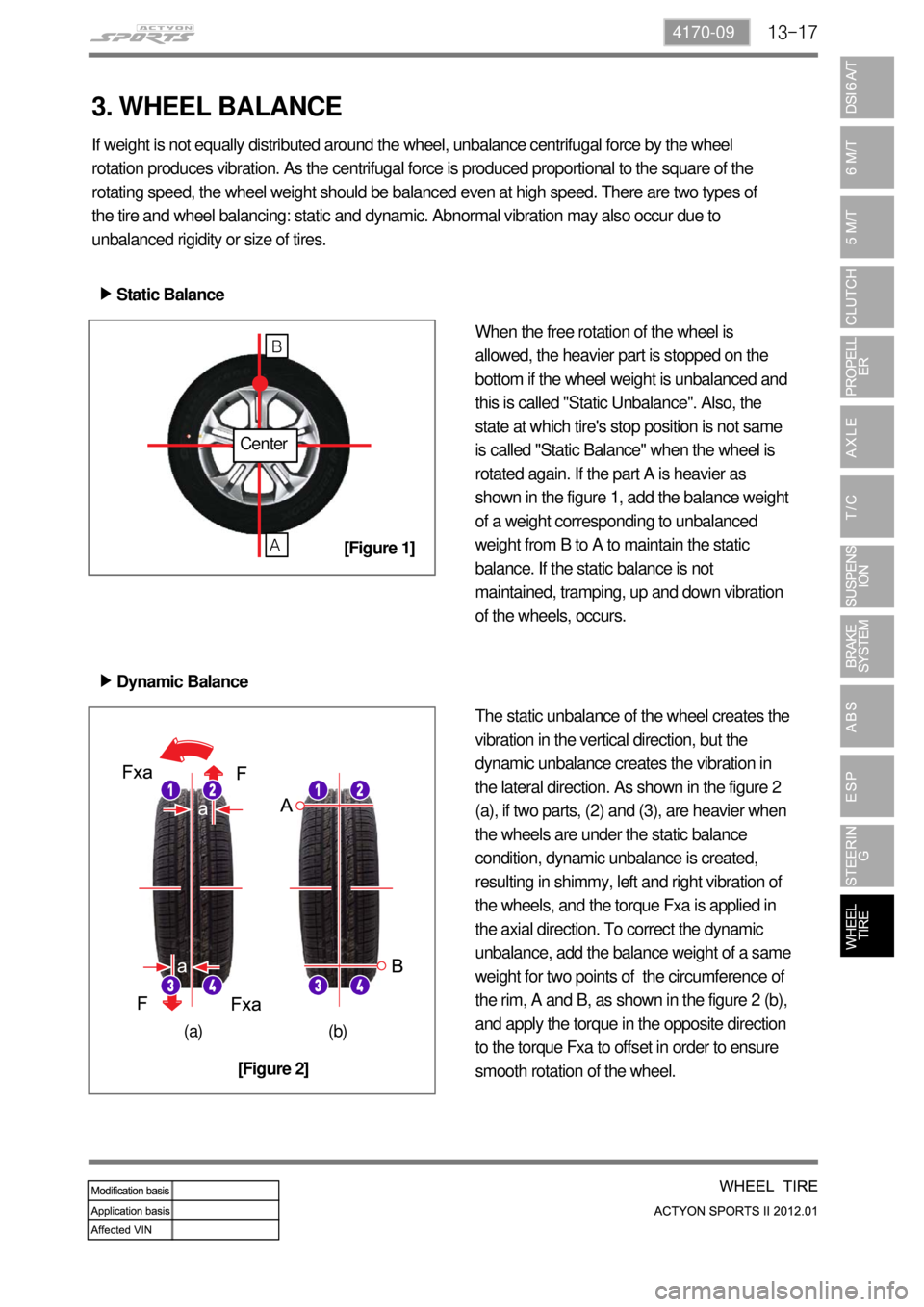
13-174170-09
If weight is not equally distributed around the wheel, unbalance centrifugal force by the wheel
rotation produces vibration. As the centrifugal force is produced proportional to the square of the
rotating speed, the wheel weight should be balanced even at high speed. There are two types of
the tire and wheel balancing: static and dynamic. Abnormal vibration may also occur due to
unbalanced rigidity or size of tires.
Static Balance ▶
When the free rotation of the wheel is
allowed, the heavier part is stopped on the
bottom if the wheel weight is unbalanced and
this is called "Static Unbalance". Also, the
state at which tire's stop position is not same
is called "Static Balance" when the wheel is
rotated again. If the part A is heavier as
shown in the figure 1, add the balance weight
of a weight corresponding to unbalanced
weight from B to A to maintain the static
balance. If the static balance is not
maintained, tramping, up and down vibration
of the wheels, occurs.
Dynamic Balance ▶
The static unbalance of the wheel creates the
vibration in the vertical direction, but the
dynamic unbalance creates the vibration in
the lateral direction. As shown in the figure 2
(a), if two parts, (2) and (3), are heavier when
the wheels are under the static balance
condition, dynamic unbalance is created,
resulting in shimmy, left and right vibration of
the wheels, and the torque Fxa is applied in
the axial direction. To correct the dynamic
unbalance, add the balance weight of a same
weight for two points of the circumference of
the rim, A and B, as shown in the figure 2 (b),
and apply the torque in the opposite direction
to the torque Fxa to offset in order to ensure
smooth rotation of the wheel.
Center
A
B
(a) (b)
[Figure 1]
[Figure 2]
3. WHEEL BALANCE