Page 766 of 1575
Page 768 of 1575
2007 > 2.7L V6 GASOLINE >
INSPECTION
1.There should be continuity between the NO.1 in the A and NO.10 in the B terminals when power and ground are
connected to the NO.7 and NO.13 in the A terminals. (Passenger compartment relay box)
2. There should be to no continuity btween the NO.1 in the A and NO.10 in the B terminals when power is
disconnected.
REAR BLOWER
1.There should be continuity between the NO.4in the A and NO.12n the B terminals when power and ground are
connected to the NO.2and NO.14in the A terminals. (Passenger compartment relay box)
2. There should be to no continuity btween the NO.4in the A and NO.12in the B terminals when power is
disconnected.
REPLACEMENT
1.Disconnect the negative ( - ) battery terminal.
2. Remove the crash pad center lower side cover. (Refer to BD group)
3. Loosen the relat box mounting nut, and then remove the relay box(A).
4.Install in the reverse order of removal.
Page 783 of 1575
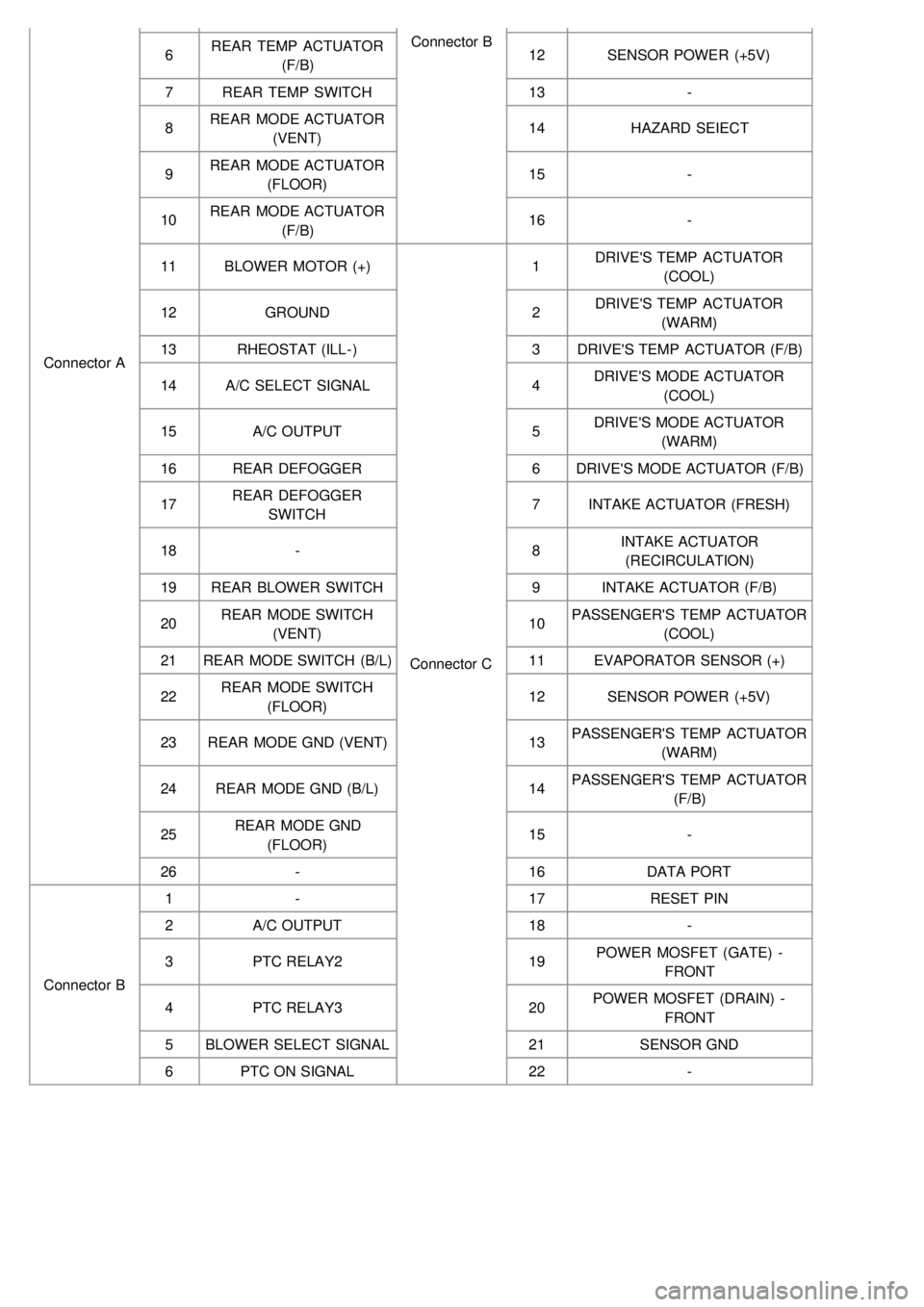
Connector AConnector B
6 REAR TEMP ACTUATOR
(F/B) 12
SENSOR POWER (+5V)
7 REAR TEMP SWITCH 13-
8 REAR MODE ACTUATOR
(VENT) 14
HAZARD SEIECT
9 REAR MODE ACTUATOR
(FLOOR) 15
-
10 REAR MODE ACTUATOR
(F/B) 16
-
11 BLOWER MOTOR (+)
Connector C1
DRIVE'S TEMP ACTUATOR
(COOL)
12 GROUND 2DRIVE'S TEMP ACTUATOR
(WARM)
13 RHEOSTAT (ILL- ) 3DRIVE'S TEMP ACTUATOR (F/B)
14 A/C SELECT SIGNAL 4DRIVE'S MODE ACTUATOR
(COOL)
15 A/C OUTPUT 5DRIVE'S MODE ACTUATOR
(WARM)
16 REAR DEFOGGER 6DRIVE'S MODE ACTUATOR (F/B)
17 REAR DEFOGGER
SWITCH 7
INTAKE ACTUATOR (FRESH)
18 - 8INTAKE ACTUATOR
(RECIRCULATION)
19 REAR BLOWER SWITCH 9INTAKE ACTUATOR (F/B)
20 REAR MODE SWITCH
(VENT) 10
PASSENGER'S TEMP ACTUATOR
(COOL)
21 REAR MODE SWITCH (B/L) 11EVAPORATOR SENSOR (+)
22 REAR MODE SWITCH
(FLOOR) 12
SENSOR POWER (+5V)
23 REAR MODE GND (VENT) 13PASSENGER'S TEMP ACTUATOR
(WARM)
24 REAR MODE GND (B/L) 14PASSENGER'S TEMP ACTUATOR
(F/B)
25 REAR MODE GND
(FLOOR) 15
-
26 - 16DATA PORT
Connector B 1
- 17RESET PIN
2 A/C OUTPUT 18-
3 PTC RELAY2 19POWER MOSFET (GATE) -
FRONT
4 PTC RELAY3 20POWER MOSFET (DRAIN) -
FRONT
5 BLOWER SELECT SIGNAL 21SENSOR GND
6 PTC ON SIGNAL 22-
Page 787 of 1575
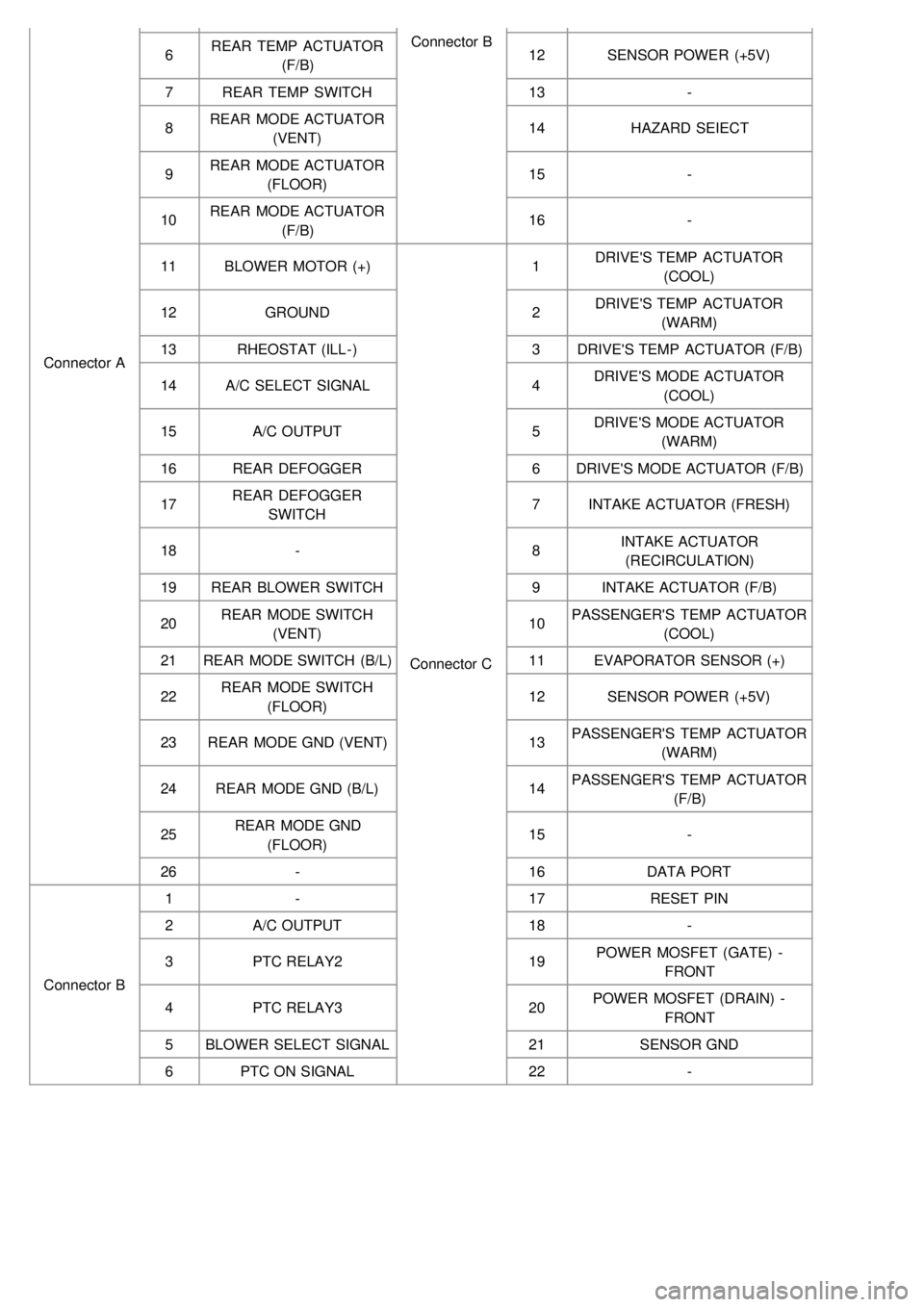
Connector AConnector B
6 REAR TEMP ACTUATOR
(F/B) 12
SENSOR POWER (+5V)
7 REAR TEMP SWITCH 13-
8 REAR MODE ACTUATOR
(VENT) 14
HAZARD SEIECT
9 REAR MODE ACTUATOR
(FLOOR) 15
-
10 REAR MODE ACTUATOR
(F/B) 16
-
11 BLOWER MOTOR (+)
Connector C1
DRIVE'S TEMP ACTUATOR
(COOL)
12 GROUND 2DRIVE'S TEMP ACTUATOR
(WARM)
13 RHEOSTAT (ILL- ) 3DRIVE'S TEMP ACTUATOR (F/B)
14 A/C SELECT SIGNAL 4DRIVE'S MODE ACTUATOR
(COOL)
15 A/C OUTPUT 5DRIVE'S MODE ACTUATOR
(WARM)
16 REAR DEFOGGER 6DRIVE'S MODE ACTUATOR (F/B)
17 REAR DEFOGGER
SWITCH 7
INTAKE ACTUATOR (FRESH)
18 - 8INTAKE ACTUATOR
(RECIRCULATION)
19 REAR BLOWER SWITCH 9INTAKE ACTUATOR (F/B)
20 REAR MODE SWITCH
(VENT) 10
PASSENGER'S TEMP ACTUATOR
(COOL)
21 REAR MODE SWITCH (B/L) 11EVAPORATOR SENSOR (+)
22 REAR MODE SWITCH
(FLOOR) 12
SENSOR POWER (+5V)
23 REAR MODE GND (VENT) 13PASSENGER'S TEMP ACTUATOR
(WARM)
24 REAR MODE GND (B/L) 14PASSENGER'S TEMP ACTUATOR
(F/B)
25 REAR MODE GND
(FLOOR) 15
-
26 - 16DATA PORT
Connector B 1
- 17RESET PIN
2 A/C OUTPUT 18-
3 PTC RELAY2 19POWER MOSFET (GATE) -
FRONT
4 PTC RELAY3 20POWER MOSFET (DRAIN) -
FRONT
5 BLOWER SELECT SIGNAL 21SENSOR GND
6 PTC ON SIGNAL 22-
Page 866 of 1575
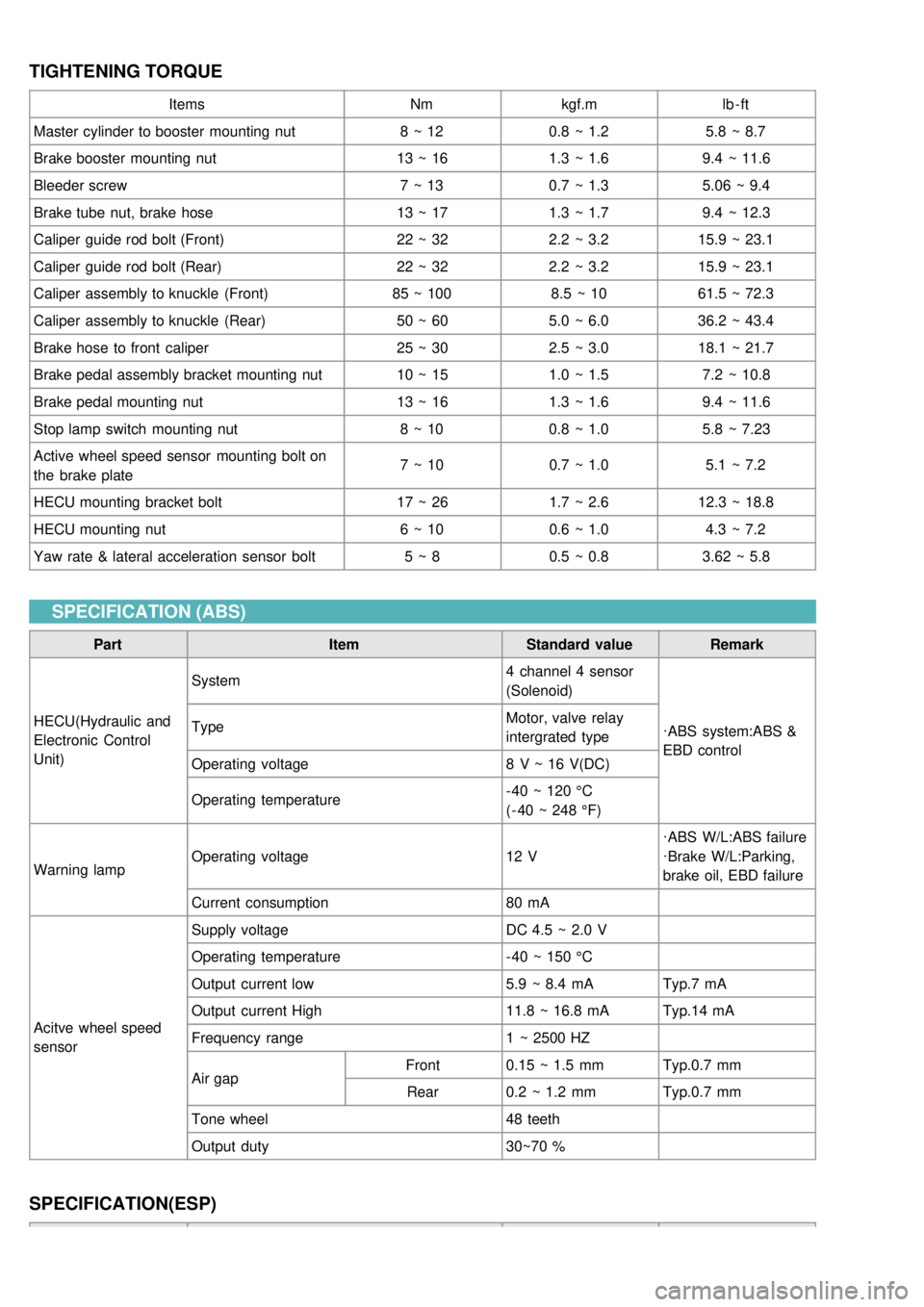
TIGHTENING TORQUE
ItemsNmkgf.m lb - ft
Master cylinder to booster mounting nut 8 ~ 120.8 ~ 1.2 5.8 ~ 8.7
Brake booster mounting nut 13 ~ 161.3 ~ 1.6 9.4 ~ 11.6
Bleeder screw 7 ~ 130.7 ~ 1.3 5.06 ~ 9.4
Brake tube nut, brake hose 13 ~ 171.3 ~ 1.7 9.4 ~ 12.3
Caliper guide rod bolt (Front) 22 ~ 322.2 ~ 3.215.9 ~ 23.1
Caliper guide rod bolt (Rear) 22 ~ 322.2 ~ 3.215.9 ~ 23.1
Caliper assembly to knuckle (Front) 85 ~ 1008.5 ~ 1061.5 ~ 72.3
Caliper assembly to knuckle (Rear) 50 ~ 605.0 ~ 6.036.2 ~ 43.4
Brake hose to front caliper 25 ~ 302.5 ~ 3.018.1 ~ 21.7
Brake pedal assembly bracket mounting nut 10 ~ 151.0 ~ 1.5 7.2 ~ 10.8
Brake pedal mounting nut 13 ~ 161.3 ~ 1.6 9.4 ~ 11.6
Stop lamp switch mounting nut 8 ~ 100.8 ~ 1.0 5.8 ~ 7.23
Active wheel speed sensor mounting bolt on
the brake plate 7 ~ 10
0.7 ~ 1.0 5.1 ~ 7.2
HECU mounting bracket bolt 17 ~ 261.7 ~ 2.612.3 ~ 18.8
HECU mounting nut 6 ~ 100.6 ~ 1.0 4.3 ~ 7.2
Yaw rate & lateral acceleration sensor bolt 5 ~ 80.5 ~ 0.8 3.62 ~ 5.8
SPECIFICATION (ABS)
Part ItemStandard valueRemark
HECU(Hydraulic and
Electronic Control
Unit) System
4 channel 4 sensor
(Solenoid)
·ABS system:ABS &
EBD control
Type
Motor, valve relay
intergrated type
Operating voltage 8 V ~ 16 V(DC)
Operating temperature - 40 ~ 120 °C
( - 40 ~ 248 °F)
Warning lamp Operating voltage
12 V·ABS W/L:ABS failure
·Brake W/L:Parking,
brake oil, EBD failure
Current consumption 80 mA
Acitve wheel speed
sensor Supply voltage
DC 4.5 ~ 2.0 V
Operating temperature - 40 ~ 150 °C
Output current low 5.9 ~ 8.4 mATyp.7 mA
Output current High 11.8 ~ 16.8 mATyp.14 mA
Frequency range 1 ~ 2500 HZ
Air gap Front
0.15 ~ 1.5 mm Typ.0.7 mm
Rear 0.2 ~ 1.2 mm Typ.0.7 mm
Tone wheel 48 teeth
Output duty 30~70 %
SPECIFICATION(ESP)
Page 867 of 1575
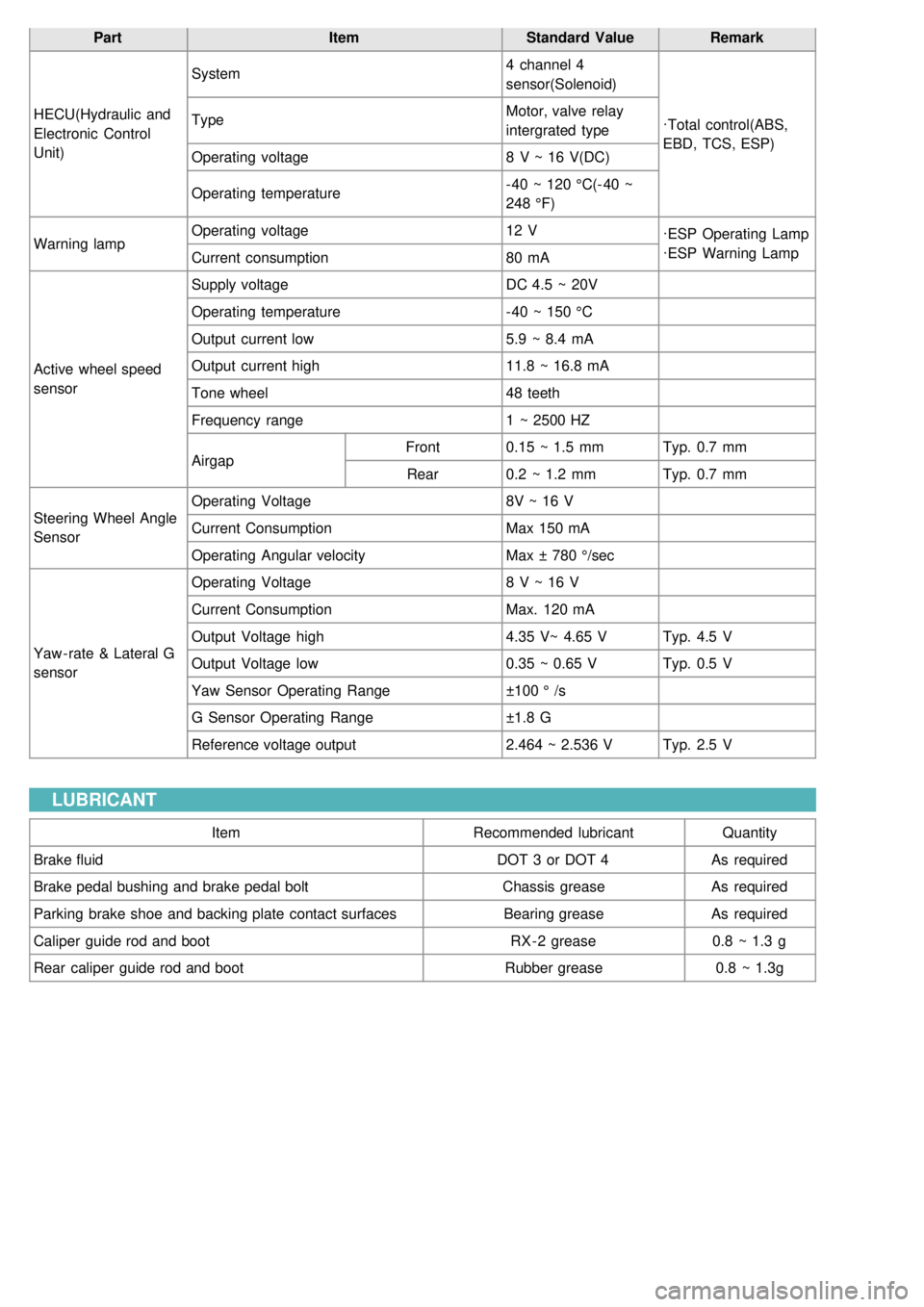
PartItemStandard ValueRemark
HECU(Hydraulic and
Electronic Control
Unit) System
4 channel 4
sensor(Solenoid)
·Total control(ABS,
EBD, TCS, ESP)
Type
Motor, valve relay
intergrated type
Operating voltage 8 V ~ 16 V(DC)
Operating temperature - 40 ~ 120 °C(- 40 ~
248 °F)
Warning lamp Operating voltage
12 V
·ESP Operating Lamp
·ESP Warning Lamp
Current consumption 80 mA
Active wheel speed
sensor Supply voltage
DC 4.5 ~ 20V
Operating temperature - 40 ~ 150 °C
Output current low 5.9 ~ 8.4 mA
Output current high 11.8 ~ 16.8 mA
Tone wheel 48 teeth
Frequency range 1 ~ 2500 HZ
Airgap Front
0.15 ~ 1.5 mm Typ. 0.7 mm
Rear 0.2 ~ 1.2 mm Typ. 0.7 mm
Steering Wheel Angle
Sensor Operating Voltage
8V ~ 16 V
Current Consumption Max 150 mA
Operating Angular velocity Max ± 780 °/sec
Yaw - rate & Lateral G
sensor Operating Voltage
8 V ~ 16 V
Current Consumption Max. 120 mA
Output Voltage high 4.35 V~ 4.65 VTyp. 4.5 V
Output Voltage low 0.35 ~ 0.65 VTyp. 0.5 V
Yaw Sensor Operating Range ±100 ° /s
G Sensor Operating Range ±1.8 G
Reference voltage output 2.464 ~ 2.536 VTyp. 2.5 V
LUBRICANT
Item Recommended lubricantQuantity
Brake fluid DOT 3 or DOT 4As required
Brake pedal bushing and brake pedal bolt Chassis greaseAs required
Parking brake shoe and backing plate contact surfaces Bearing greaseAs required
Caliper guide rod and boot RX - 2 grease0.8 ~ 1.3 g
Rear caliper guide rod and boot Rubber grease0.8 ~ 1.3g
Page 927 of 1575
4FR Wheel speed sensor FR WHEELKm/h
5 RL Wheel speed sensor RL WHEELKm/h
6 RR Wheel speed sensor RR WHEELKm/h
7 ABS Warning lamp ABS LAMP-
8 EBD Warning lamp EBD LAMP-
9 Brake Lamp B/LAMP-
10 Pump relay state PUMP RLY-
11 Valve relay state VALVE RLY-
12 Motor MOTOR-
13 Front Left valve(IN) FL INLET-
14 Front Right valve (IN) FR INLET-
15 Rear Left valve (IN) RL INLET-
16 Rear Right valve (IN) RR INLET-
17 Front Left valve (OUT) FL OUTLET-
18 Front Right valve (OUT) FR OUTLET-
19 Rear Left valve(OUT) RL OUTLET-
20 Rear Right valve (OUT) RR OUTLET-
Page 928 of 1575
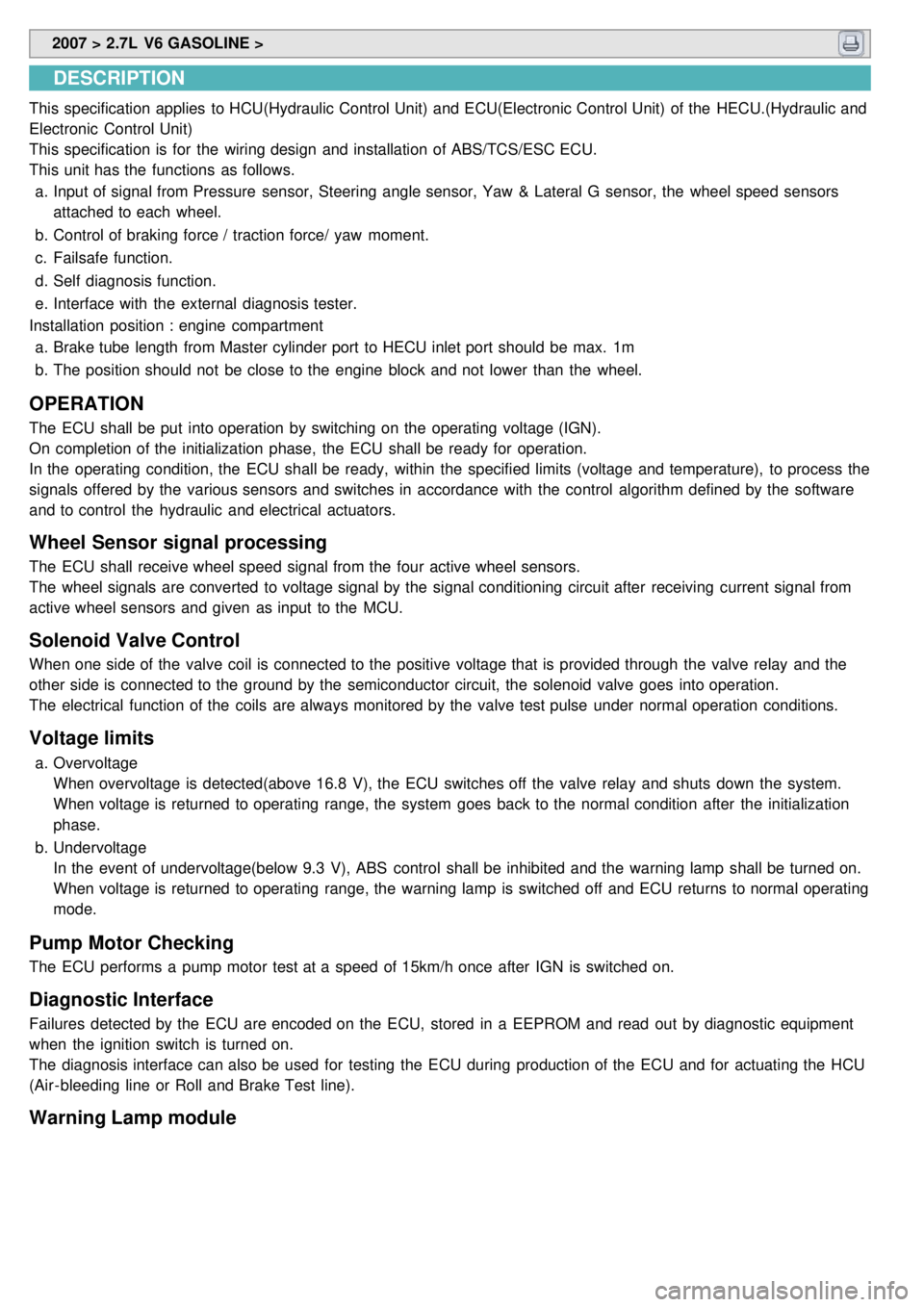
2007 > 2.7L V6 GASOLINE >
DESCRIPTION
This specification applies to HCU(Hydraulic Control Unit) and ECU(Electronic Control Unit) of the HECU.(Hydraulic and
Electronic Control Unit)
This specification is for the wiring design and installation of ABS/TCS/ESC ECU.
This unit has the functions as follows.
a. Input of signal from Pressure sensor, Steering angle sensor, Yaw & Lateral G sensor, the wheel speed sensors
attached to each wheel.
b. Control of braking force / traction force/ yaw moment.
c. Failsafe function.
d. Self diagnosis function.
e. Interface with the external diagnosis tester.
Installation position : engine compartment a. Brake tube length from Master cylinder port to HECU inlet port should be max. 1m
b. The position should not be close to the engine block and not lower than the wheel.
OPERATION
The ECU shall be put into operation by switching on the operating voltage (IGN).
On completion of the initialization phase, the ECU shall be ready for operation.
In the operating condition, the ECU shall be ready, within the specified limits (voltage and temperature), to process the
signals offered by the various sensors and switches in accordance with the control algorithm defined by the software
and to control the hydraulic and electrical actuators.
Wheel Sensor signal processing
The ECU shall receive wheel speed signal from the four active wheel sensors.
The wheel signals are converted to voltage signal by the signal conditioning circuit after receiving current signal from
active wheel sensors and given as input to the MCU.
Solenoid Valve Control
When one side of the valve coil is connected to the positive voltage that is provided through the valve relay and the
other side is connected to the ground by the semiconductor circuit, the solenoid valve goes into operation.
The electrical function of the coils are always monitored by the valve test pulse under normal operation conditions.
Voltage limits
a.Overvoltage
When overvoltage is detected(above 16.8 V), the ECU switches off the valve relay and shuts down the system.
When voltage is returned to operating range, the system goes back to the normal condition after the initialization
phase.
b. Undervoltage
In the event of undervoltage(below 9.3 V), ABS control shall be inhibited and the warning lamp shall be turned on.
When voltage is returned to operating range, the warning lamp is switched off and ECU returns to normal operating
mode.
Pump Motor Checking
The ECU performs a pump motor test at a speed of 15km/h once after IGN is switched on.
Diagnostic Interface
Failures detected by the ECU are encoded on the ECU, stored in a EEPROM and read out by diagnostic equipment
when the ignition switch is turned on.
The diagnosis interface can also be used for testing the ECU during production of the ECU and for actuating the HCU
(Air - bleeding line or Roll and Brake Test line).
Warning Lamp module