Page 353 of 1556
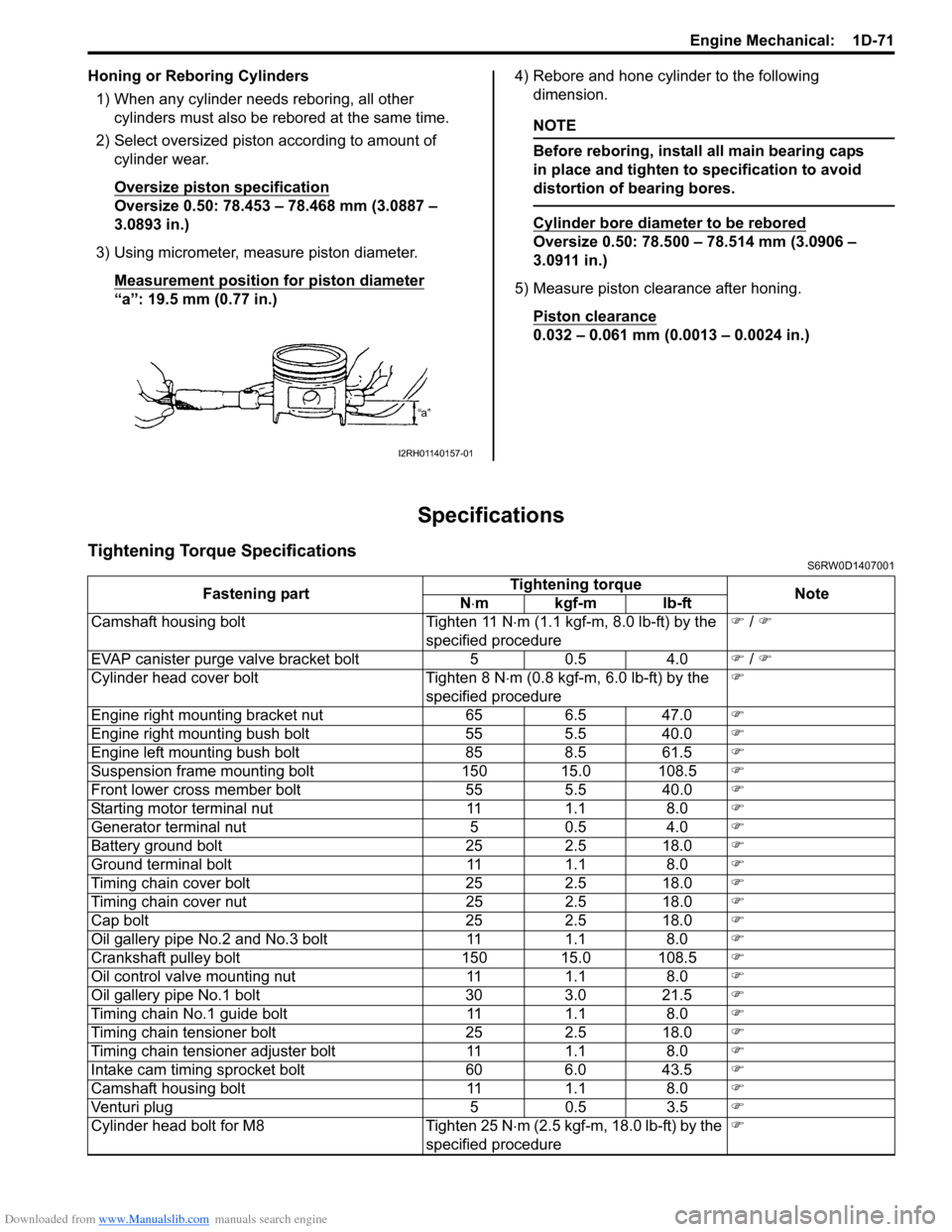
Downloaded from www.Manualslib.com manuals search engine Engine Mechanical: 1D-71
Honing or Reboring Cylinders
1) When any cylinder needs reboring, all other
cylinders must also be rebored at the same time.
2) Select oversized piston according to amount of
cylinder wear.
Oversize piston specification
Oversize 0.50: 78.453 – 78.468 mm (3.0887 –
3.0893 in.)
3) Using micrometer, measure piston diameter.
Measurement position for piston diameter
“a”: 19.5 mm (0.77 in.)4) Rebore and hone cylinder to the following
dimension.
NOTE
Before reboring, install all main bearing caps
in place and tighten to specification to avoid
distortion of bearing bores.
Cylinder bore diameter to be rebored
Oversize 0.50: 78.500 – 78.514 mm (3.0906 –
3.0911 in.)
5) Measure piston clearance after honing.
Piston clearance
0.032 – 0.061 mm (0.0013 – 0.0024 in.)
Specifications
Tightening Torque SpecificationsS6RW0D1407001
I2RH01140157-01
Fastening partTightening torque
Note
N⋅mkgf-mlb-ft
Camshaft housing bolt Tighten 11 N⋅m (1.1 kgf-m, 8.0 lb-ft) by the
specified procedure ) / )
EVAP canister purge valve bracket bolt 5 0.5 4.0 ) / )
Cylinder head cover bolt Tighten 8 N⋅m (0.8 kgf-m, 6.0 lb-ft) by the
specified procedure )
Engine right mounting bracket nut 65 6.5 47.0 )
Engine right mounting bush bolt 55 5.5 40.0 )
Engine left mounting bush bolt 85 8.5 61.5 )
Suspension frame mounting bolt 150 15.0 108.5 )
Front lower cross member bolt 55 5.5 40.0 )
Starting motor terminal nut 11 1.1 8.0 )
Generator terminal nut 5 0.5 4.0 )
Battery ground bolt 25 2.5 18.0 )
Ground terminal bolt 11 1.1 8.0 )
Timing chain cover bolt 25 2.5 18.0 )
Timing chain cover nut 25 2.5 18.0 )
Cap bolt 25 2.5 18.0 )
Oil gallery pipe No.2 and No.3 bolt 11 1.1 8.0 )
Crankshaft pulley bolt 150 15.0 108.5 )
Oil control valve mounting nut 11 1.1 8.0 )
Oil gallery pipe No.1 bolt 30 3.0 21.5 )
Timing chain No.1 guide bolt 11 1.1 8.0 )
Timing chain tensioner bolt 25 2.5 18.0 )
Timing chain tensioner adjuster bolt 11 1.1 8.0 )
Intake cam timing sprocket bolt 60 6.0 43.5 )
Camshaft housing bolt 11 1.1 8.0 )
Venturi plug 5 0.5 3.5 )
Cylinder head bolt for M8 Tighten 25 N⋅m (2.5 kgf-m, 18.0 lb-ft) by the
specified procedure )
Page 359 of 1556
Downloaded from www.Manualslib.com manuals search engine Engine Lubrication System: 1E-3
8) Start engine and check oil pressure switch for oil
leakage. If oil leakage is found, repair it.
9) Connect oil pressure switch coupler (1).
Repair Instructions
Oil Pan and Oil Pump Strainer ComponentsS6RW0D1506001
I2RH0B150006-01
1
23
4
(a) 5
(b) 6
(b) 8
(b) 9
(b) 7
10
(c)10
(c)
11 12
(d) 13
(d) 1514
I5RH0A150002-02
1. Oil pan:
Apply sealant 99000-31260 to
mating surface.6. Strainer bolt 11. Dowel pin : 35 N⋅m (3.5 kgf-m, 25.5 lb-ft)
2. Strainer 7. Bracket bolt 12. Baffle plate : Tighten 11 N⋅m (1.1 kgf-m, 8.0 lb-
ft) by the specified procedure.
3. O-ring 8. Oil pan nut 13. Baffle plate bolt : 55 N⋅m (5.5 kgf-m, 40.0 lb-ft)
4. Gasket 9. Oil pan bolt
(M6)14. Clutch housing lower plate (M/T
vehicle) or torque converter housing
lower plate (A/T vehicle):11 N⋅m (1.1 kgf-m, 8.0 lb-ft)
5. Drain plug 10. Oil pan bolt
(M10)15. Lower plate bolt : Do not reuse.
Page 360 of 1556
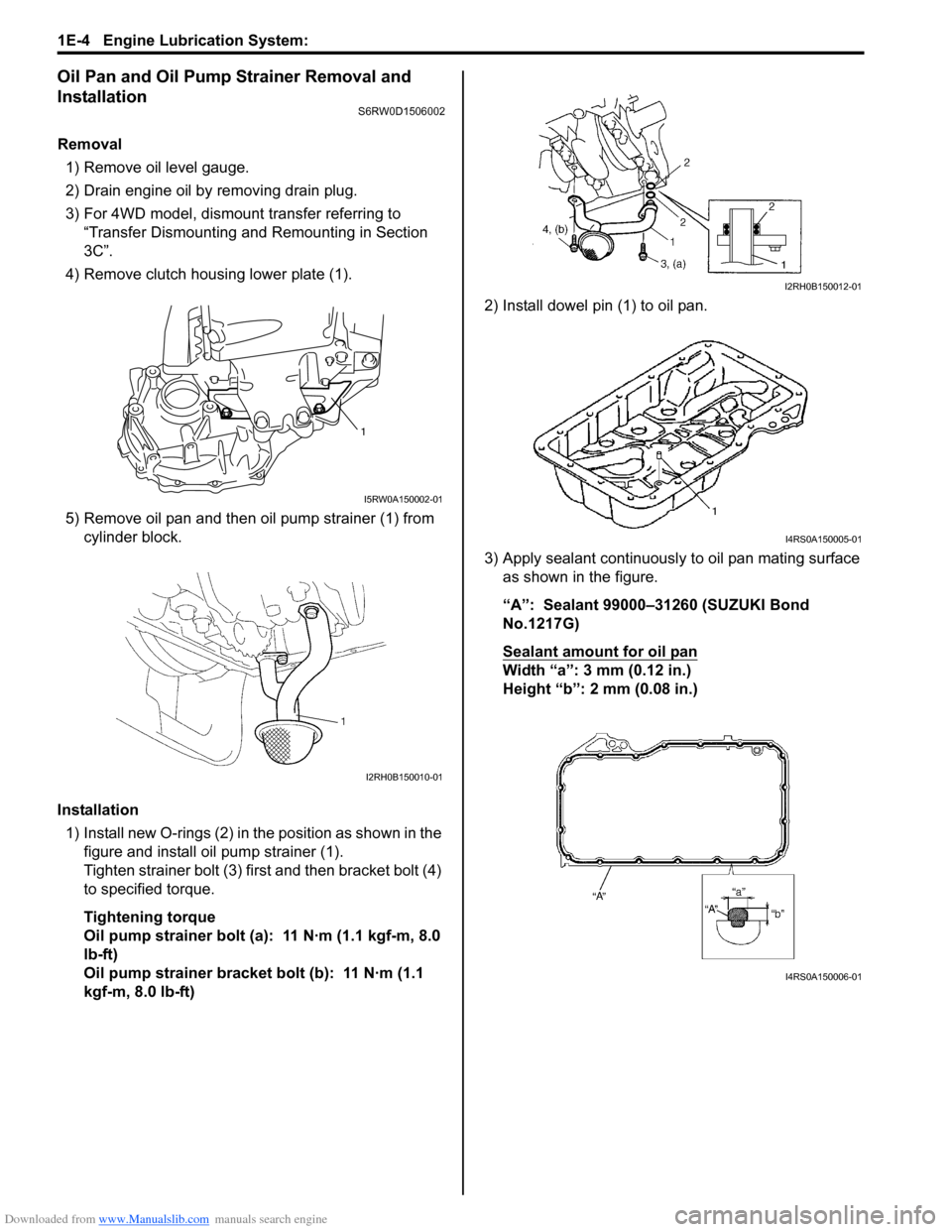
Downloaded from www.Manualslib.com manuals search engine 1E-4 Engine Lubrication System:
Oil Pan and Oil Pump Strainer Removal and
Installation
S6RW0D1506002
Removal
1) Remove oil level gauge.
2) Drain engine oil by removing drain plug.
3) For 4WD model, dismount transfer referring to
“Transfer Dismounting and Remounting in Section
3C”.
4) Remove clutch housing lower plate (1).
5) Remove oil pan and then oil pump strainer (1) from
cylinder block.
Installation
1) Install new O-rings (2) in the position as shown in the
figure and install oil pump strainer (1).
Tighten strainer bolt (3) first and then bracket bolt (4)
to specified torque.
Tightening torque
Oil pump strainer bolt (a): 11 N·m (1.1 kgf-m, 8.0
lb-ft)
Oil pump strainer bracket bolt (b): 11 N·m (1.1
kgf-m, 8.0 lb-ft)2) Install dowel pin (1) to oil pan.
3) Apply sealant continuously to oil pan mating surface
as shown in the figure.
“A”: Sealant 99000–31260 (SUZUKI Bond
No.1217G)
Sealant amount for oil pan
Width “a”: 3 mm (0.12 in.)
Height “b”: 2 mm (0.08 in.)
1
I5RW0A150002-01
I2RH0B150010-01
I2RH0B150012-01
I4RS0A150005-01
I4RS0A150006-01
Page 365 of 1556
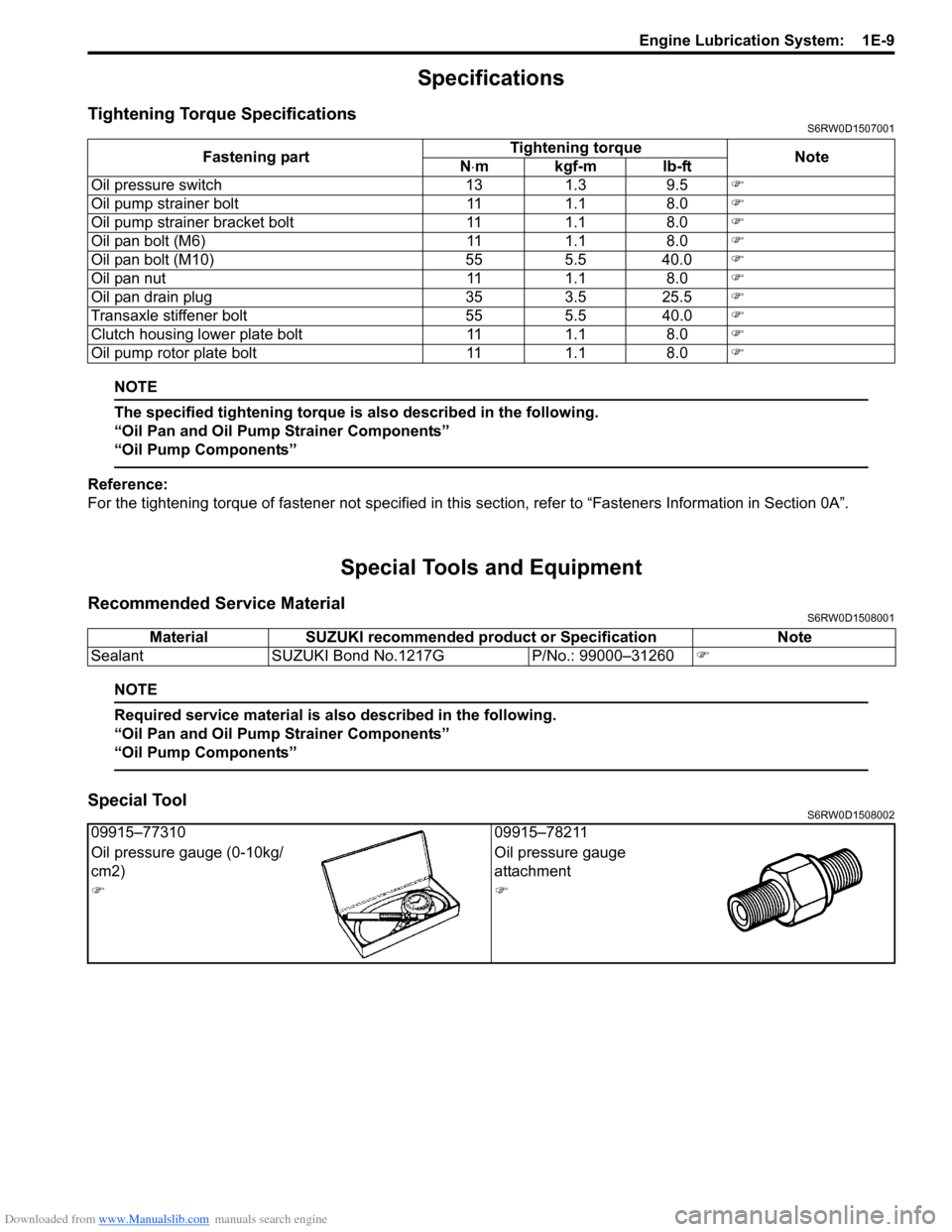
Downloaded from www.Manualslib.com manuals search engine Engine Lubrication System: 1E-9
Specifications
Tightening Torque SpecificationsS6RW0D1507001
NOTE
The specified tightening torque is also described in the following.
“Oil Pan and Oil Pump Strainer Components”
“Oil Pump Components”
Reference:
For the tightening torque of fastener not specified in this section, refer to “Fasteners Information in Section 0A”.
Special Tools and Equipment
Recommended Service MaterialS6RW0D1508001
NOTE
Required service material is also described in the following.
“Oil Pan and Oil Pump Strainer Components”
“Oil Pump Components”
Special ToolS6RW0D1508002
Fastening partTightening torque
Note
N⋅mkgf-mlb-ft
Oil pressure switch 13 1.3 9.5 )
Oil pump strainer bolt 11 1.1 8.0 )
Oil pump strainer bracket bolt 11 1.1 8.0 )
Oil pan bolt (M6) 11 1.1 8.0 )
Oil pan bolt (M10) 55 5.5 40.0 )
Oil pan nut 11 1.1 8.0 )
Oil pan drain plug 35 3.5 25.5 )
Transaxle stiffener bolt 55 5.5 40.0 )
Clutch housing lower plate bolt 11 1.1 8.0 )
Oil pump rotor plate bolt 11 1.1 8.0 )
Material SUZUKI recommended product or Specification Note
Sealant SUZUKI Bond No.1217G P/No.: 99000–31260 )
09915–77310 09915–78211
Oil pressure gauge (0-10kg/
cm2)Oil pressure gauge
attachment
) )
Page 441 of 1556
Downloaded from www.Manualslib.com manuals search engine Front Suspension: 2B-4
Front Strut Assembly ComponentsS6RW0D2206002
1
2 3 4 5 7
6 8 910 11
121314
15
(a)
(b)
(c)
(a)
I7RW01220003-03
1. Front strut 6. Coil spring upper seat 11. Strut nut : 50 N⋅m (5.0 kgf-m, 36.5 lb-ft)
2. Coil spring 7. Strut bearing 12. Strut bracket bolt
: Insert from vehicle front side.:55 N⋅m (5.5 kgf-m, 40.0 lb-ft)
3. Bump stopper 8. Strut support 13. Strut bracket nut : 140 N⋅m (14.0 kgf-m, 101.5 lb-ft)
4. Strut dust cover 9. Strut support lower nut 14. Stabilizer joint nut : Do not reuse.
5. Coil spring seat 10. Rebound stopper 15. Stabilizer joint
Page 442 of 1556
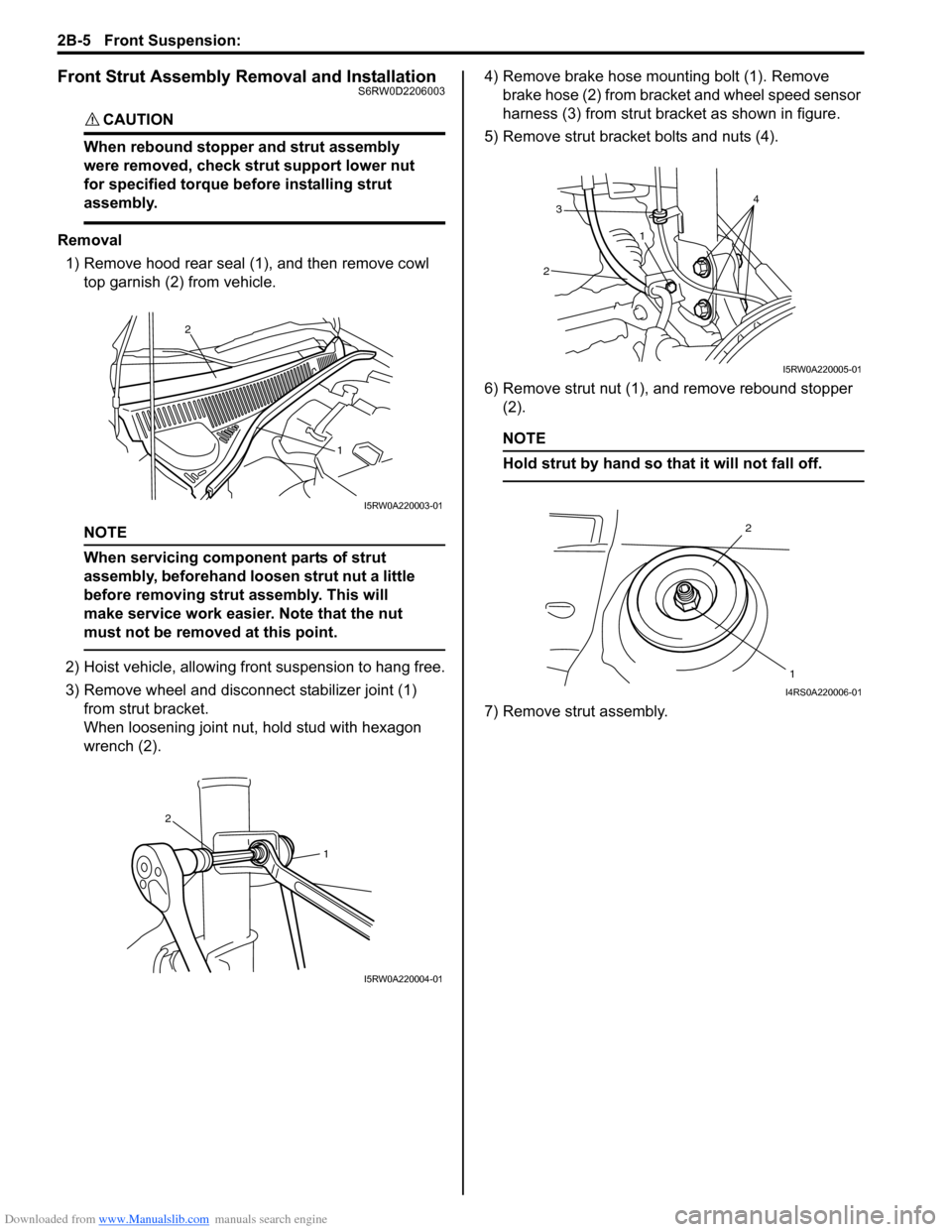
Downloaded from www.Manualslib.com manuals search engine 2B-5 Front Suspension:
Front Strut Assembly Removal and InstallationS6RW0D2206003
CAUTION!
When rebound stopper and strut assembly
were removed, check strut support lower nut
for specified torque before installing strut
assembly.
Removal
1) Remove hood rear seal (1), and then remove cowl
top garnish (2) from vehicle.
NOTE
When servicing component parts of strut
assembly, beforehand loosen strut nut a little
before removing strut assembly. This will
make service work easier. Note that the nut
must not be removed at this point.
2) Hoist vehicle, allowing front suspension to hang free.
3) Remove wheel and disconnect stabilizer joint (1)
from strut bracket.
When loosening joint nut, hold stud with hexagon
wrench (2).4) Remove brake hose mounting bolt (1). Remove
brake hose (2) from bracket and wheel speed sensor
harness (3) from strut bracket as shown in figure.
5) Remove strut bracket bolts and nuts (4).
6) Remove strut nut (1), and remove rebound stopper
(2).
NOTE
Hold strut by hand so that it will not fall off.
7) Remove strut assembly.
2
1
I5RW0A220003-01
1
2
I5RW0A220004-01
3
214
I5RW0A220005-01
2
1
I4RS0A220006-01
Page 443 of 1556
Downloaded from www.Manualslib.com manuals search engine Front Suspension: 2B-6
Installation
Install strut assembly by reversing removal procedure,
noting the following instructions.
• Insert bolts in such direction as shown in figure.
• Tighten all fasteners to specified torque.
Tightening torque
Strut bracket nut (a): 140 N·m (14.0 kgf-m, 101.5
lb-ft)
Brake hose mounting bolt (c): 26 N·m (2.6 kgf-m,
19.0 lb-ft)
Stabilizer joint nut (d): 50 N·m (5.0 kgf-m, 36.5 lb-
ft)
CAUTION!
Never reuse the removed strut bracket nut.
• Lower hoist and vehicle in unloaded condition, tighten
strut nut (b) to specified torque.
Tightening torque
Strut nut (b): 50 N·m (5.0 kgf-m, 36.5 lb-ft)
NOTE
Don’t twist brake hose and wheel speed
sensor harness when installing them.
• Tighten wheel nut to specified torque.
Tightening torque
Wheel nut: 85 N·m (8.5 kgf-m, 61.5 lb-ft)
• After installation, confirm front wheel alignment.
(b)
(a)
(c)
(d)
I5RW0A220006-01
Page 445 of 1556
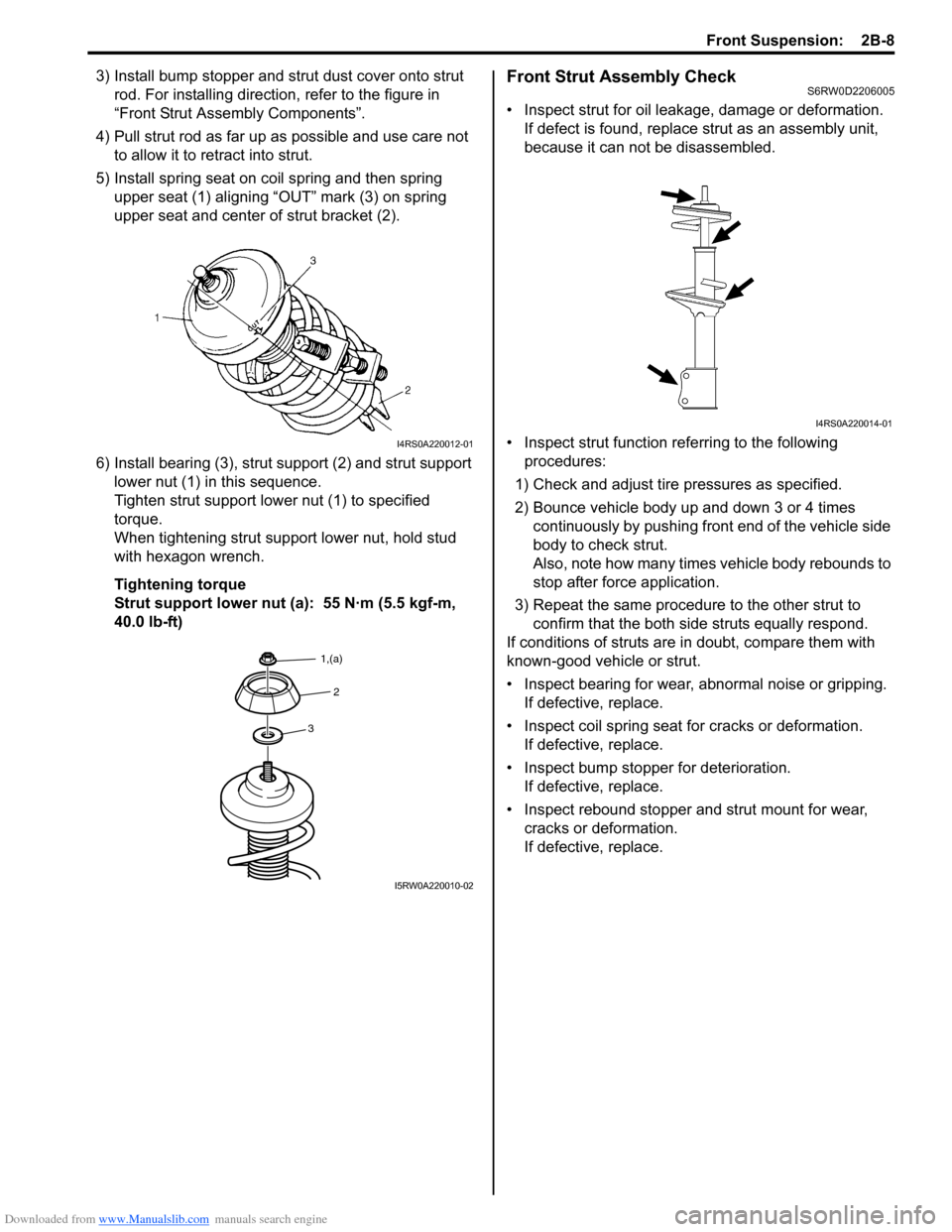
Downloaded from www.Manualslib.com manuals search engine Front Suspension: 2B-8
3) Install bump stopper and strut dust cover onto strut
rod. For installing direction, refer to the figure in
“Front Strut Assembly Components”.
4) Pull strut rod as far up as possible and use care not
to allow it to retract into strut.
5) Install spring seat on coil spring and then spring
upper seat (1) aligning “OUT” mark (3) on spring
upper seat and center of strut bracket (2).
6) Install bearing (3), strut support (2) and strut support
lower nut (1) in this sequence.
Tighten strut support lower nut (1) to specified
torque.
When tightening strut support lower nut, hold stud
with hexagon wrench.
Tightening torque
Strut support lower nut (a): 55 N·m (5.5 kgf-m,
40.0 lb-ft)Front Strut Assembly CheckS6RW0D2206005
• Inspect strut for oil leakage, damage or deformation.
If defect is found, replace strut as an assembly unit,
because it can not be disassembled.
• Inspect strut function referring to the following
procedures:
1) Check and adjust tire pressures as specified.
2) Bounce vehicle body up and down 3 or 4 times
continuously by pushing front end of the vehicle side
body to check strut.
Also, note how many times vehicle body rebounds to
stop after force application.
3) Repeat the same procedure to the other strut to
confirm that the both side struts equally respond.
If conditions of struts are in doubt, compare them with
known-good vehicle or strut.
• Inspect bearing for wear, abnormal noise or gripping.
If defective, replace.
• Inspect coil spring seat for cracks or deformation.
If defective, replace.
• Inspect bump stopper for deterioration.
If defective, replace.
• Inspect rebound stopper and strut mount for wear,
cracks or deformation.
If defective, replace.
I4RS0A220012-01
3
2
1,(a)
I5RW0A220010-02
I4RS0A220014-01