Page 1386 of 1500
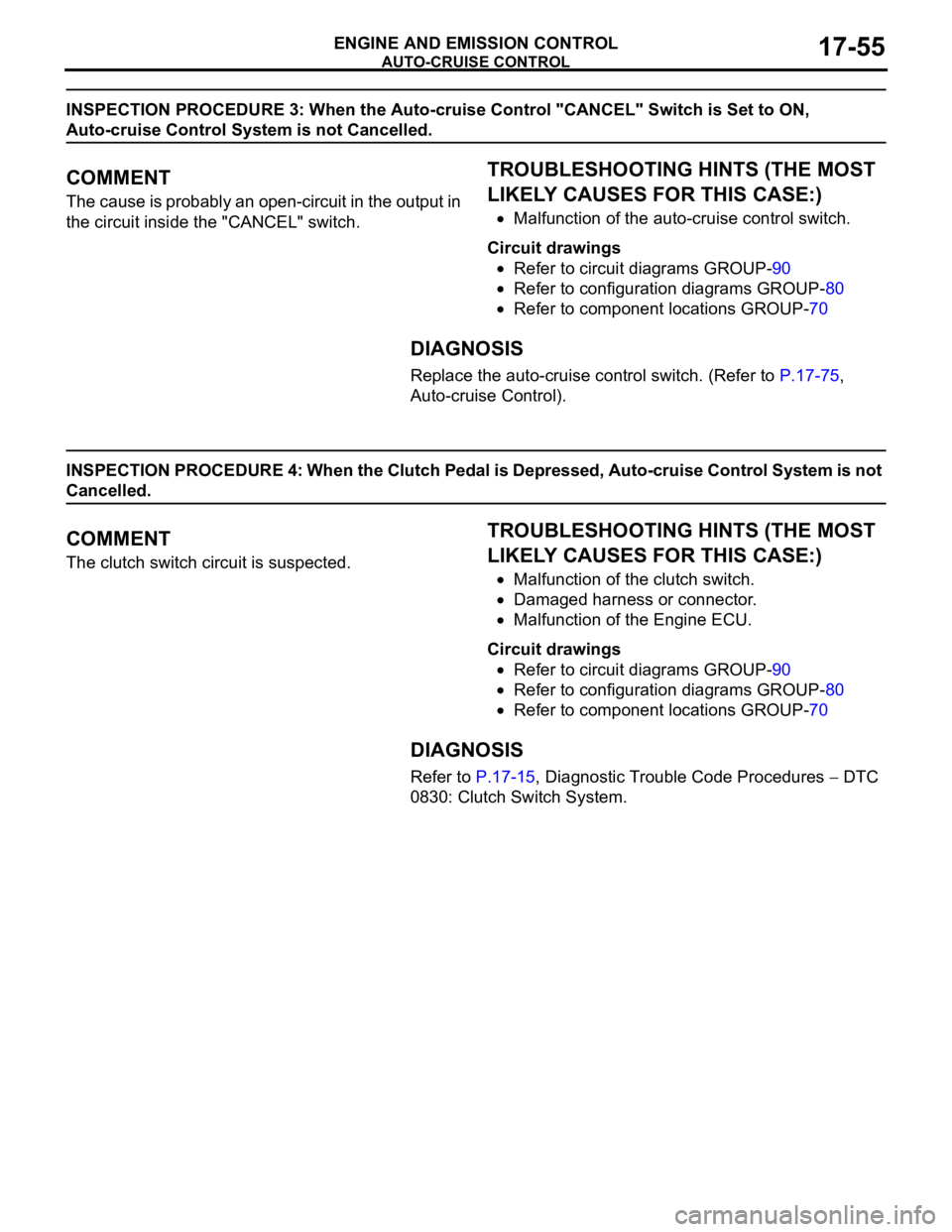
AUTO-CRUISE CONTROL
ENGINE AND EMISSION CONTROL17-55
INSPECTION PROCEDURE 3: When the Auto-cruise Control "CANCEL" Switch is Set to ON,
Auto-cruise Control System is not Cancelled.
.
COMMENT
The cause is probably an open-circuit in the output in
the circuit inside the "CANCEL" switch.
.
TROUBLESHOOTING HINTS (THE MOST
LIKELY CAUSES FOR THIS CASE:)
Malfunction of the auto-cruise control switch.
Circuit drawings
Refer to circuit diagrams GROUP-90
Refer to configuration diagrams GROUP-80
Refer to component locations GROUP-70
DIAGNOSIS
Replace the auto-cruise control switch. (Refer to P.17-75,
Auto-cruise Control).
INSPECTION PROCEDURE 4: When the Clutch Pedal is Depressed, Auto-cruise Control System is not
Cancelled.
.
COMMENT
The clutch switch circuit is suspected.
.
TROUBLESHOOTING HINTS (THE MOST
LIKELY CAUSES FOR THIS CASE:)
Malfunction of the clutch switch.
Damaged harness or connector.
Malfunction of the Engine ECU.
Circuit drawings
Refer to circuit diagrams GROUP-90
Refer to configuration diagrams GROUP-80
Refer to component locations GROUP-70
DIAGNOSIS
Refer to P.17-15, Diagnostic Trouble Code Procedures DTC
0830: Clutch Switch System.
Page 1387 of 1500
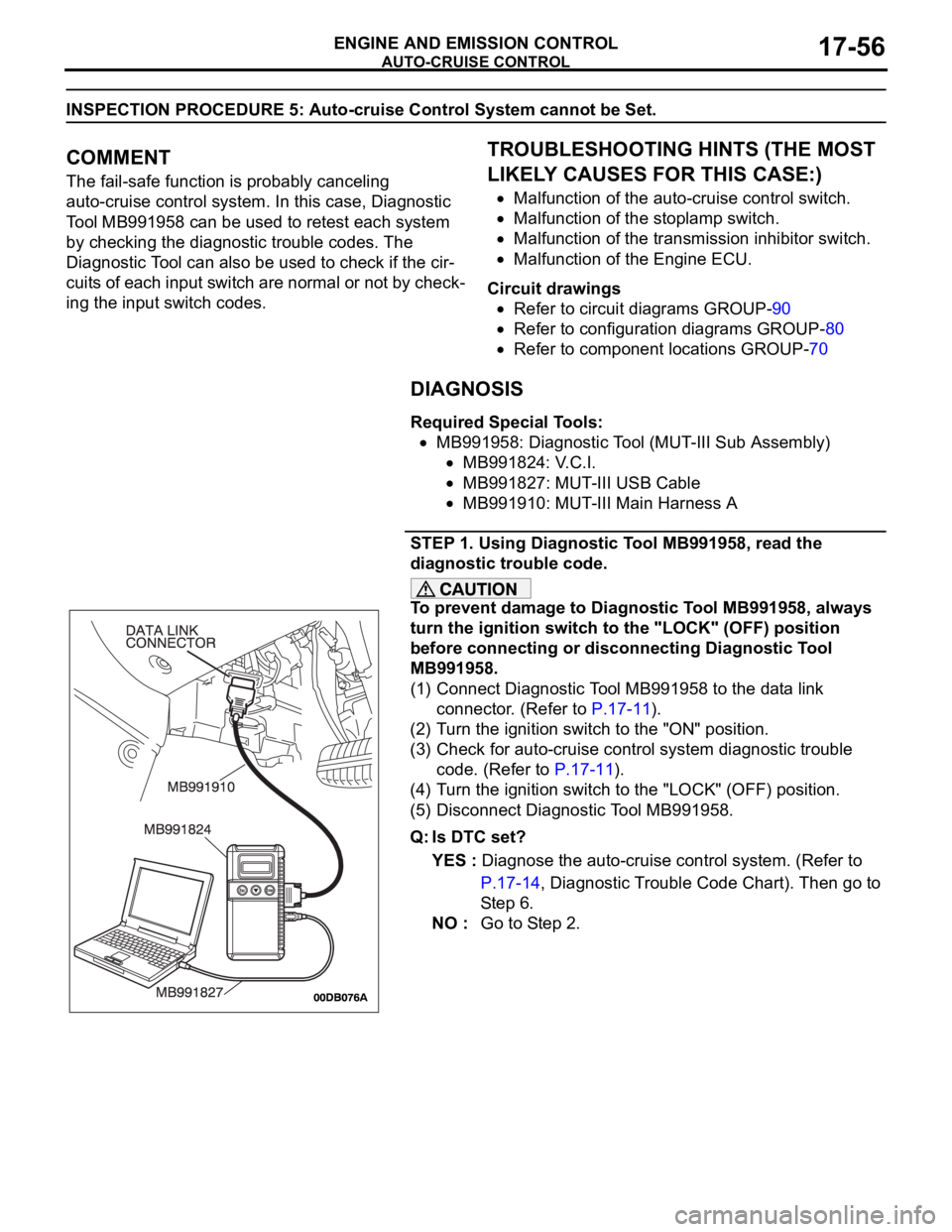
AUTO-CRUISE CONTROL
ENGINE AND EMISSION CONTROL17-56
INSPECTION PROCEDURE 5: Auto-cruise Control System cannot be Set.
.
COMMENT
The fail-safe function is probably canceling
auto-cruise control system. In this case, Diagnostic
Tool MB991958 can be used to retest each system
by checking the diagnostic trouble codes. The
Diagnostic Tool can also be used to check if the cir-
cuits of each input switch are normal or not by check-
ing the input switch codes.
.
TROUBLESHOOTING HINTS (THE MOST
LIKELY CAUSES FOR THIS CASE:)
Malfunction of the auto-cruise control switch.
Malfunction of the stoplamp switch.
Malfunction of the transmission inhibitor switch.
Malfunction of the Engine ECU.
Circuit drawings
Refer to circuit diagrams GROUP-90
Refer to configuration diagrams GROUP-80
Refer to component locations GROUP-70
DIAGNOSIS
Required Special Tools:
MB991958: Diagnostic Tool (MUT-III Sub Assembly)
MB991824: V.C.I.
MB991827: MUT-III USB Cable
MB991910: MUT-III Main Harness A
STEP 1. Using Diagnostic Tool MB991958, read the
diagnostic trouble code.
To prevent damage to Diagnostic Tool MB991958, always
turn the ignition switch to the "LOCK" (OFF) position
before connecting or disconnecting Diagnostic Tool
MB991958.
(1) Connect Diagnostic Tool MB991958 to the data link
connector. (Refer to P.17-11).
(2) Turn the ignition switch to the "ON" position.
(3) Check for auto-cruise control system diagnostic trouble
code. (Refer to P.17-11).
(4) Turn the ignition switch to the "LOCK" (OFF) position.
(5) Disconnect Diagnostic Tool MB991958.
Q: Is DTC set?
YES : Diagnose the auto-cruise control system. (Refer to
P.17-14, Diagnostic Trouble Code Chart). Then go to
St e p 6 .
NO : Go to Step 2.
Page 1391 of 1500
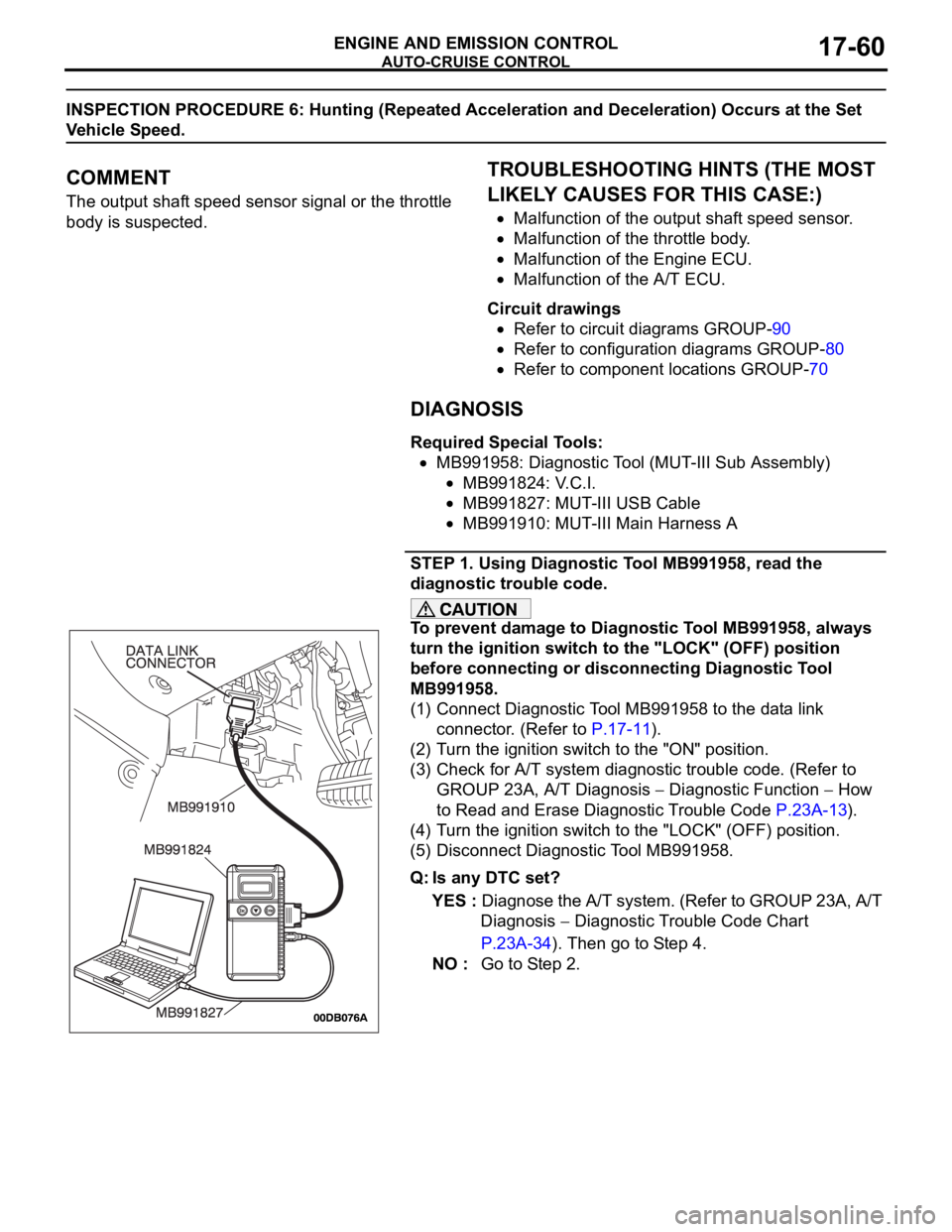
AUTO-CRUISE CONTROL
ENGINE AND EMISSION CONTROL17-60
INSPECTION PROCEDURE 6: Hunting (Repeated Acceleration and Deceleration) Occurs at the Set
Vehicle Speed.
.
COMMENT
The output shaft speed sensor signal or the throttle
body is suspected.
.
TROUBLESHOOTING HINTS (THE MOST
LIKELY CAUSES FOR THIS CASE:)
Malfunction of the output shaft speed sensor.
Malfunction of the throttle body.
Malfunction of the Engine ECU.
Malfunction of the A/T ECU.
Circuit drawings
Refer to circuit diagrams GROUP-90
Refer to configuration diagrams GROUP-80
Refer to component locations GROUP-70
DIAGNOSIS
Required Special Tools:
MB991958: Diagnostic Tool (MUT-III Sub Assembly)
MB991824: V.C.I.
MB991827: MUT-III USB Cable
MB991910: MUT-III Main Harness A
STEP 1. Using Diagnostic Tool MB991958, read the
diagnostic trouble code.
To prevent damage to Diagnostic Tool MB991958, always
turn the ignition switch to the "LOCK" (OFF) position
before connecting or disconnecting Diagnostic Tool
MB991958.
(1) Connect Diagnostic Tool MB991958 to the data link
connector. (Refer to P.17-11).
(2) Turn the ignition switch to the "ON" position.
(3) Check for A/T system diagnostic trouble code. (Refer to
GROUP 23A, A/T Diagnosis
Diagnostic Function How
to Read and Erase Diagnostic Trouble Code P.23A-13).
(4) Turn the ignition switch to the "LOCK" (OFF) position.
(5) Disconnect Diagnostic Tool MB991958.
Q: Is any DTC set?
YES : Diagnose the A/T system. (Refer to GROUP 23A, A/T
Diagnosis
Diagnostic Trouble Code Chart
P.23A-34). Then go to Step 4.
NO : Go to Step 2.
Page 1394 of 1500
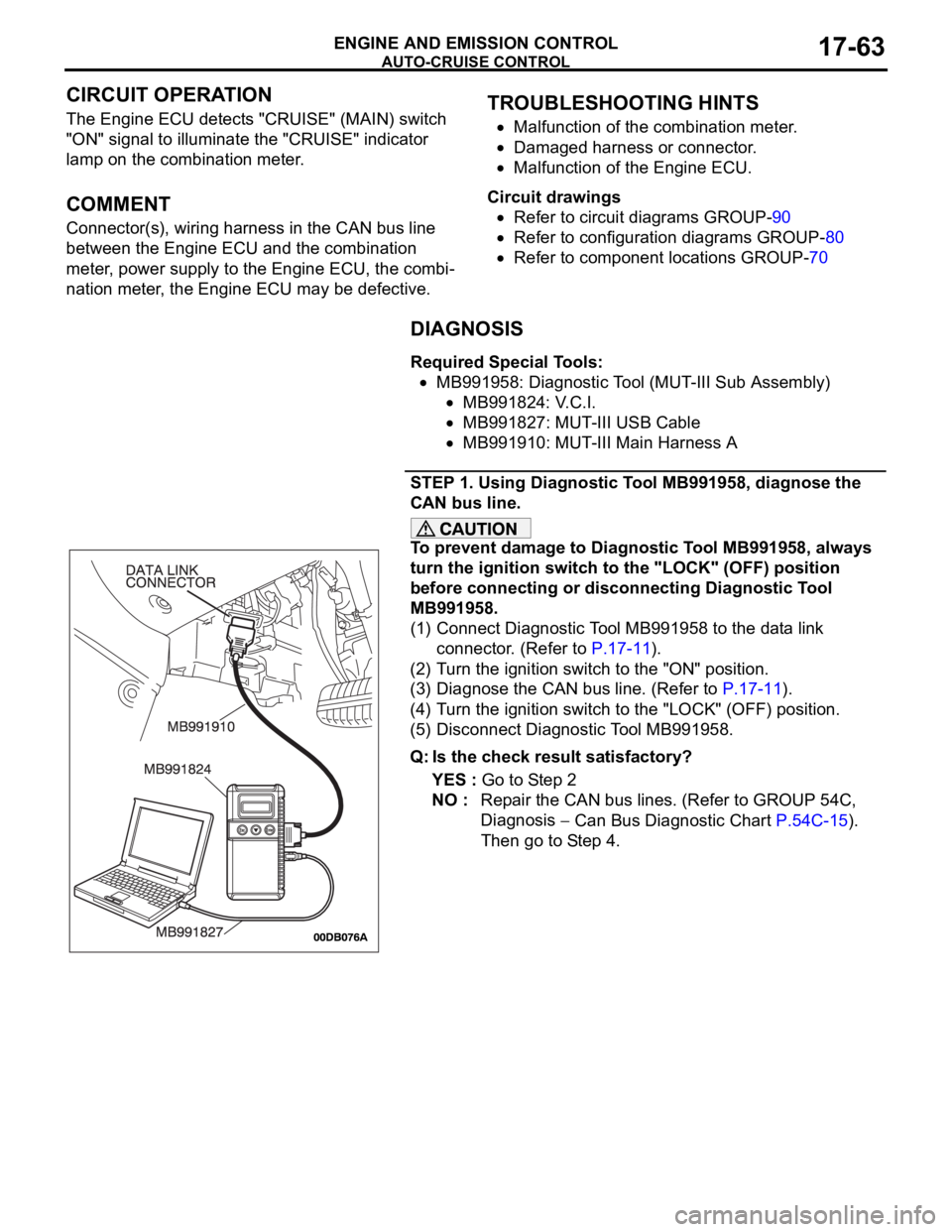
AUTO-CRUISE CONTROL
ENGINE AND EMISSION CONTROL17-63
CIRCUIT OPERATION
The Engine ECU detects "CRUISE" (MAIN) switch
"ON" signal to illuminate the "CRUISE" indicator
lamp on the combination meter.
.
COMMENT
Connector(s), wiring harness in the CAN bus line
between the Engine ECU and the combination
meter, power supply to the Engine ECU, the combi-
nation meter, the Engine ECU may be defective.
.
TROUBLESHOOTING HINTS
Malfunction of the combination meter.
Damaged harness or connector.
Malfunction of the Engine ECU.
Circuit drawings
Refer to circuit diagrams GROUP-90
Refer to configuration diagrams GROUP-80
Refer to component locations GROUP-70
DIAGNOSIS
Required Special Tools:
MB991958: Diagnostic Tool (MUT-III Sub Assembly)
MB991824: V.C.I.
MB991827: MUT-III USB Cable
MB991910: MUT-III Main Harness A
STEP 1. Using Diagnostic Tool MB991958, diagnose the
CAN bus line.
To prevent damage to Diagnostic Tool MB991958, always
turn the ignition switch to the "LOCK" (OFF) position
before connecting or disconnecting Diagnostic Tool
MB991958.
(1) Connect Diagnostic Tool MB991958 to the data link
connector. (Refer to P.17-11).
(2) Turn the ignition switch to the "ON" position.
(3) Diagnose the CAN bus line. (Refer to P.17-11).
(4) Turn the ignition switch to the "LOCK" (OFF) position.
(5) Disconnect Diagnostic Tool MB991958.
Q: Is the check result satisfactory?
YES : Go to Step 2
NO : Repair the CAN bus lines. (Refer to GROUP 54C,
Diagnosis
Can Bus Diagnostic Chart P.54C-15).
Then go to Step 4.
Page 1409 of 1500
EMISSION CONTROL
ENGINE AND EMISSION CONTROL17-78
VACUUM CIRCUIT DIAGRAMM1173007100252
VACUUM HOSE INSTALLATIONM1173007200129
1. When connecting the vacuum hoses, they should be
securely inserted onto the nipples.
2. Connect the hoses correctly, using the VACUUM HOSE
ROUTING diagram as a guide.
Page 1410 of 1500
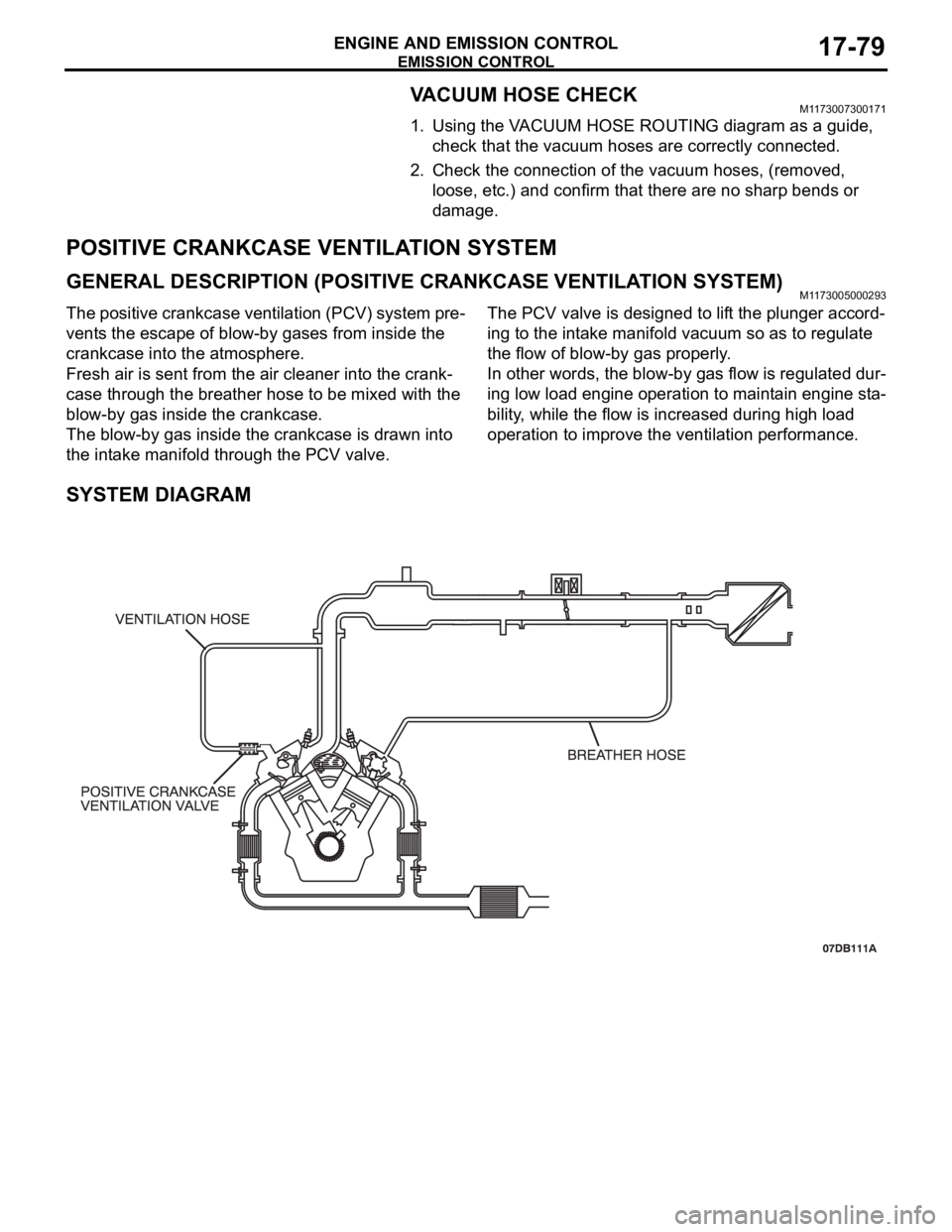
EMISSION CONTROL
ENGINE AND EMISSION CONTROL17-79
VACUUM HOSE CHECKM1173007300171
1. Using the VACUUM HOSE ROUTING diagram as a guide,
check that the vacuum hoses are correctly connected.
2. Check the connection of the vacuum hoses, (removed,
loose, etc.) and confirm that there are no sharp bends or
damage.
POSITIVE CRANKCASE VENTILATION SYSTEM
GENERAL DESCRIPTION (POSITIVE CRANKCASE VENTILATION SYSTEM)M1173005000293
The positive crankcase ventilation (PCV) system pre-
vents the escape of blow-by gases from inside the
crankcase into the atmosphere.
Fresh air is sent from the air cleaner into the crank-
case through the breather hose to be mixed with the
blow-by gas inside the crankcase.
The blow-by gas inside the crankcase is drawn into
the intake manifold through the PCV valve.The PCV valve is designed to lift the plunger accord-
ing to the intake manifold vacuum so as to regulate
the flow of blow-by gas properly.
In other words, the blow-by gas flow is regulated dur-
ing low load engine operation to maintain engine sta-
bility, while the flow is increased during high load
operation to improve the ventilation performance.
SYSTEM DIAGRAM
Page 1412 of 1500
EMISSION CONTROL
ENGINE AND EMISSION CONTROL17-81
EVAPORATIVE EMISSION CONTROL SYSTEM
GENERAL DESCRIPTION (EVAPORATIVE EMISSION SYSTEM)M1173005100706
The evaporative emission (EVAP) system prevents
fuel vapors generated in the fuel tank from escaping
into the atmosphere.
Fuel vapors from the fuel tank flow through the vapor
pipe/hose to be stored temporarily in the EVAP can-
ister.
When the vehicle is in operation, fuel vapors stored
in the EVAP canister flow through the EVAP purge
solenoid, purge port and intake manifold plenum to
the combustion chamber.When the engine coolant temperature is low or when
the intake air quantity is small (when the engine is at
idle, for example), the Engine-ECU brings the EVAP
purge solenoid into the OFF state to shut off the fuel
vapor flow to the intake manifold plenum. This
ensures driveability when the engine is cold or run-
ning under low load and also stabilizes the emission
level.
SYSTEM DIAGRAM
Page 1419 of 1500
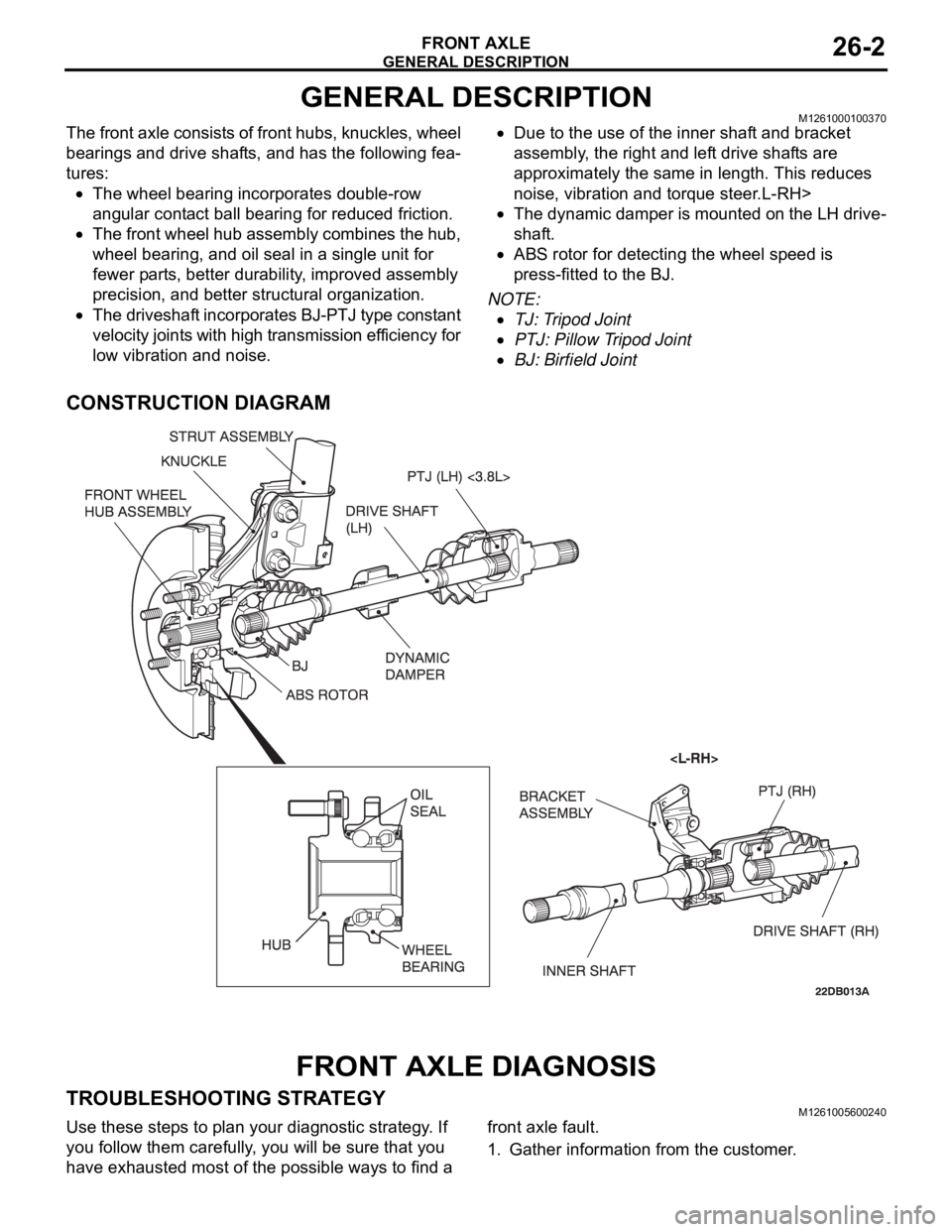
GENERAL DESCRIPTION
FRONT AXLE26-2
GENERAL DESCRIPTIONM1261000100370
The front axle consists of front hubs, knuckles, wheel
bearings and drive shafts, and has the following fea-
tures:
The wheel bearing incorporates double-row
angular contact ball bearing for reduced friction.
The front wheel hub assembly combines the hub,
wheel bearing, and oil seal in a single unit for
fewer parts, better durability, improved assembly
precision, and better structural organization.
The driveshaft incorporates BJ-PTJ type constant
velocity joints with high transmission efficiency for
low vibration and noise.
Due to the use of the inner shaft and bracket
assembly, the right and left drive shafts are
approximately the same in length. This reduces
noise, vibration and torque steer.L-RH>
The dynamic damper is mounted on the LH drive-
shaft.
ABS rotor for detecting the wheel speed is
press-fitted to the BJ.
NOTE: .
TJ: Tripod Joint
PTJ: Pillow Tripod Joint
BJ: Birfield Joint
CONSTRUCTION DIAGRAM
FRONT AXLE DIAGNOSIS
TROUBLESHOOTING STRATEGYM1261005600240
Use these steps to plan your diagnostic strategy. If
you follow them carefully, you will be sure that you
have exhausted most of the possible ways to find a front axle fault.
1. Gather information from the customer.