Page 2 of 3419
QUICK REFERENCE CHART: QX562005
QUICK REFERENCE CHART: QX56PFP:00000
Engine Tune-Up DataELS001U4
Cylinder arrangementV- 8
Displacement
5,552 cm
3 (338.80 in3 )
Bore and stroke98 x 92 mm (3.86 x 3.62 in)
Valve arrangementDOHC
Firing order1-8-7-3-6-5-4-2
Number of piston ringsCompression 2
Oil 1
Number of main bearings5
Compression ratio9.8:1
Compression pressureStandard
1,520 kPa (15.5 kg/cm
2 , 220 psi) / 200 rpm
Minimum
1,324 kPa (13.5 kg/cm
2 , 192 psi) / 200 rpm
Differential limit between cylinders
98 kPa (1.0 kg/cm
2 , 14 psi) / 200 rpm
Cylinder number
Valve timing
Unit: degree
abcde f
232°230°2°48°3°49°
SEM957C
PBIC0187E
Page 984 of 3419
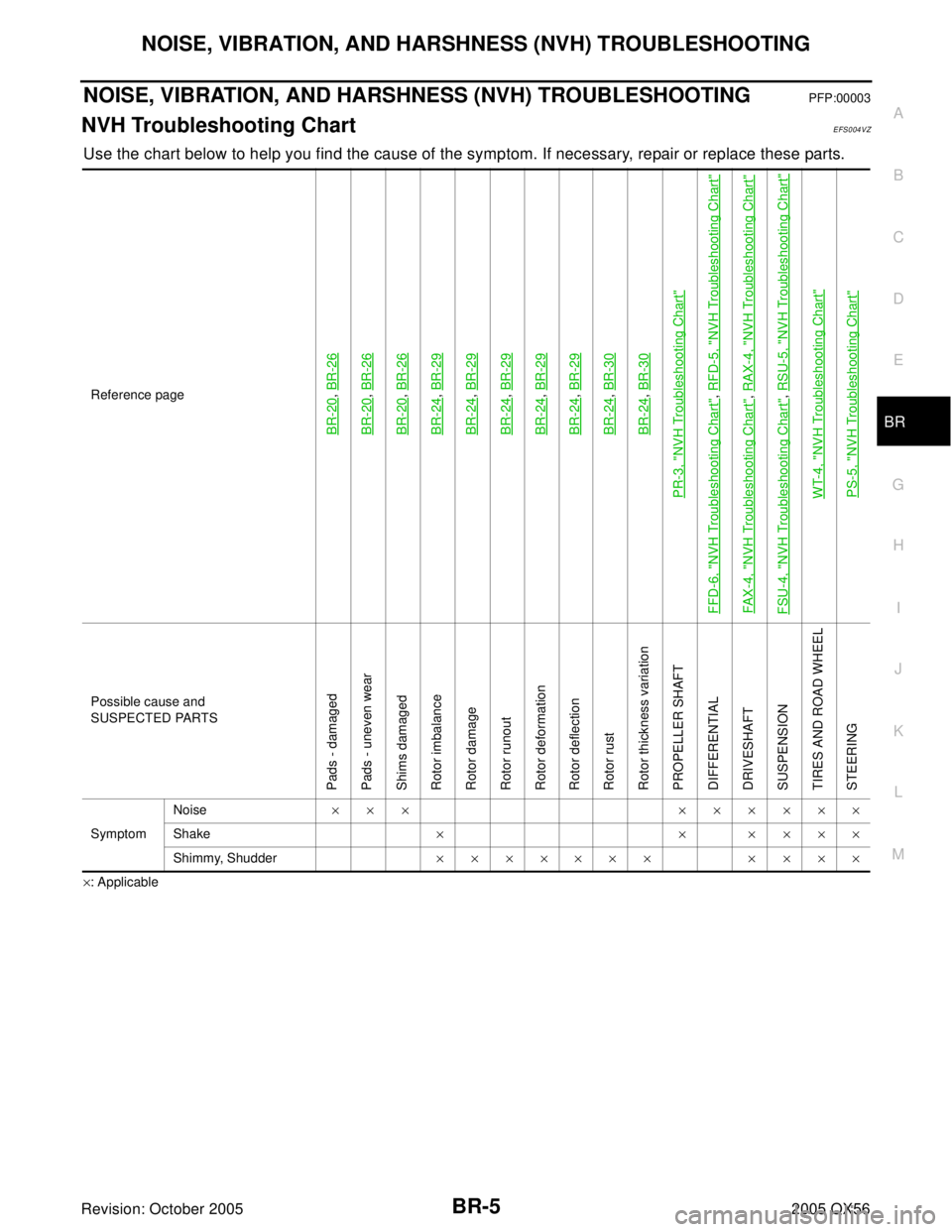
NOISE, VIBRATION, AND HARSHNESS (NVH) TROUBLESHOOTING
BR-5
C
D
E
G
H
I
J
K
L
MA
B
BR
Revision: October 20052005 QX56
NOISE, VIBRATION, AND HARSHNESS (NVH) TROUBLESHOOTINGPFP:00003
NVH Troubleshooting ChartEFS004VZ
Use the chart below to help you find the cause of the symptom. If necessary, repair or replace these parts.
×: ApplicableReference page
BR-20
, BR-26
BR-20
, BR-26
BR-20
, BR-26
BR-24
, BR-29
BR-24
, BR-29
BR-24
, BR-29
BR-24
, BR-29
BR-24
, BR-29
BR-24
, BR-30
BR-24
, BR-30
PR-3, "
NVH Troubleshooting Chart
"
FFD-6, "
NVH Troubleshooting Chart
", RFD-5, "
NVH Troubleshooting Chart
"
FAX -4, "
NVH Troubleshooting Chart
", RAX-4, "
NVH Troubleshooting Chart
"
FSU-4, "
NVH Troubleshooting Chart
", RSU-5, "
NVH Troubleshooting Chart
"
WT-4, "
NVH Troubleshooting Chart
"
PS-5, "
NVH Troubleshooting Chart
"
Possible cause and
SUSPECTED PARTS
Pads - damaged
Pads - uneven wear
Shims damaged
Rotor imbalance
Rotor damage
Rotor runout
Rotor deformation
Rotor deflection
Rotor rust
Rotor thickness variation
PROPELLER SHAFT
DIFFERENTIAL
DRIVESHAFT
SUSPENSION
TIRES AND ROAD WHEEL
STEERING
SymptomNoise××× ××××××
Shake××××××
Shimmy, Shudder××××××× ××××
Page 2002 of 3419
SERVICE DATA AND SPECIFICATIONS (SDS)
EM-99
C
D
E
F
G
H
I
J
K
L
MA
EM
Revision: October 20052005 QX56
SERVICE DATA AND SPECIFICATIONS (SDS)PFP:00030
Standard and LimitEBS00LMM
GENERAL SPECIFICATIONS
DRIVE BELTS
EXHAUST MANIFOLD
Unit: mm (in) Cylinder arrangementV- 8
Displacement cm
3 (cu in)5,552 (338.80)
Bore and stroke mm (in)98 x 92 (3.86 x 3.62)
Valve arrangementDOHC
Firing order1-8-7-3-6-5-4-2
Number of piston ringsCompression 2
Oil 1
Number of main bearings5
Compression ratio9.8:1
Compression pressure
kPa (kg/cm
2 , psi)/rpmStandard 1,520 (15.5, 220)/200
Minimum 1,324 (13.5, 192)/200
Differential limit between cylinders 98 (1.0, 14)/200
Cylinder number
Va l v e t i m i n g
Unit: degree
abcde f
232°230°2°48°3°49°
SEM 95 7C
PBIC0187E
Tension of drive belts Auto adjustment by auto tensioner
ItemsLimit
Surface distortion Exhaust manifold 0.3 (0.012)
Page 2033 of 3419
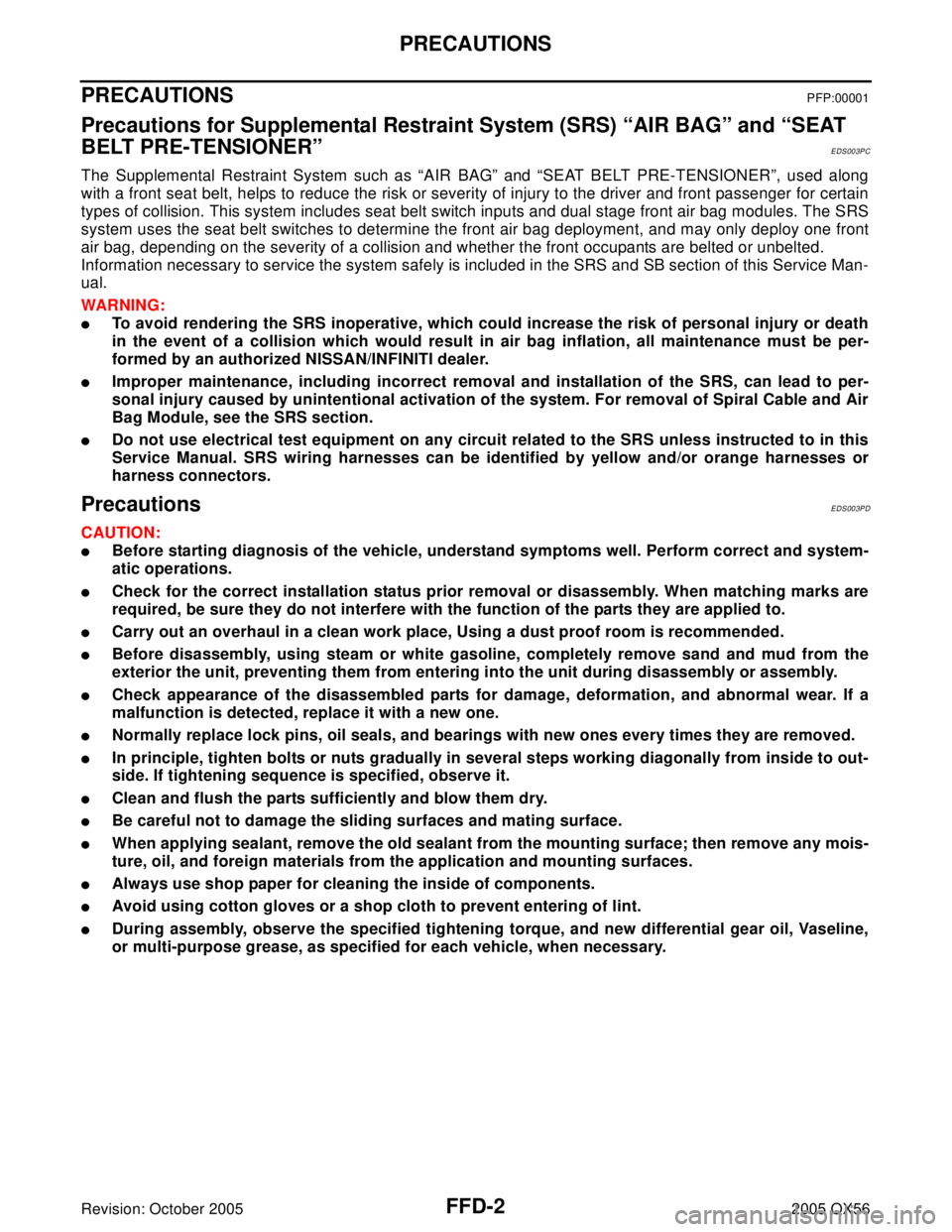
FFD-2
PRECAUTIONS
Revision: October 20052005 QX56
PRECAUTIONSPFP:00001
Precautions for Supplemental Restraint System (SRS) “AIR BAG” and “SEAT
BELT PRE-TENSIONER”
EDS003PC
The Supplemental Restraint System such as “AIR BAG” and “SEAT BELT PRE-TENSIONER”, used along
with a front seat belt, helps to reduce the risk or severity of injury to the driver and front passenger for certain
types of collision. This system includes seat belt switch inputs and dual stage front air bag modules. The SRS
system uses the seat belt switches to determine the front air bag deployment, and may only deploy one front
air bag, depending on the severity of a collision and whether the front occupants are belted or unbelted.
Information necessary to service the system safely is included in the SRS and SB section of this Service Man-
ual.
WAR NIN G:
To avoid rendering the SRS inoperative, which could increase the risk of personal injury or death
in the event of a collision which would result in air bag inflation, all maintenance must be per-
formed by an authorized NISSAN/INFINITI dealer.
Improper maintenance, including incorrect removal and installation of the SRS, can lead to per-
sonal injury caused by unintentional activation of the system. For removal of Spiral Cable and Air
Bag Module, see the SRS section.
Do not use electrical test equipment on any circuit related to the SRS unless instructed to in this
Service Manual. SRS wiring harnesses can be identified by yellow and/or orange harnesses or
harness connectors.
PrecautionsEDS003PD
CAUTION:
Before starting diagnosis of the vehicle, understand symptoms well. Perform correct and system-
atic operations.
Check for the correct installation status prior removal or disassembly. When matching marks are
required, be sure they do not interfere with the function of the parts they are applied to.
Carry out an overhaul in a clean work place, Using a dust proof room is recommended.
Before disassembly, using steam or white gasoline, completely remove sand and mud from the
exterior the unit, preventing them from entering into the unit during disassembly or assembly.
Check appearance of the disassembled parts for damage, deformation, and abnormal wear. If a
malfunction is detected, replace it with a new one.
Normally replace lock pins, oil seals, and bearings with new ones every times they are removed.
In principle, tighten bolts or nuts gradually in several steps working diagonally from inside to out-
side. If tightening sequence is specified, observe it.
Clean and flush the parts sufficiently and blow them dry.
Be careful not to damage the sliding surfaces and mating surface.
When applying sealant, remove the old sealant from the mounting surface; then remove any mois-
ture, oil, and foreign materials from the application and mounting surfaces.
Always use shop paper for cleaning the inside of components.
Avoid using cotton gloves or a shop cloth to prevent entering of lint.
During assembly, observe the specified tightening torque, and new differential gear oil, Vaseline,
or multi-purpose grease, as specified for each vehicle, when necessary.
Page 2037 of 3419
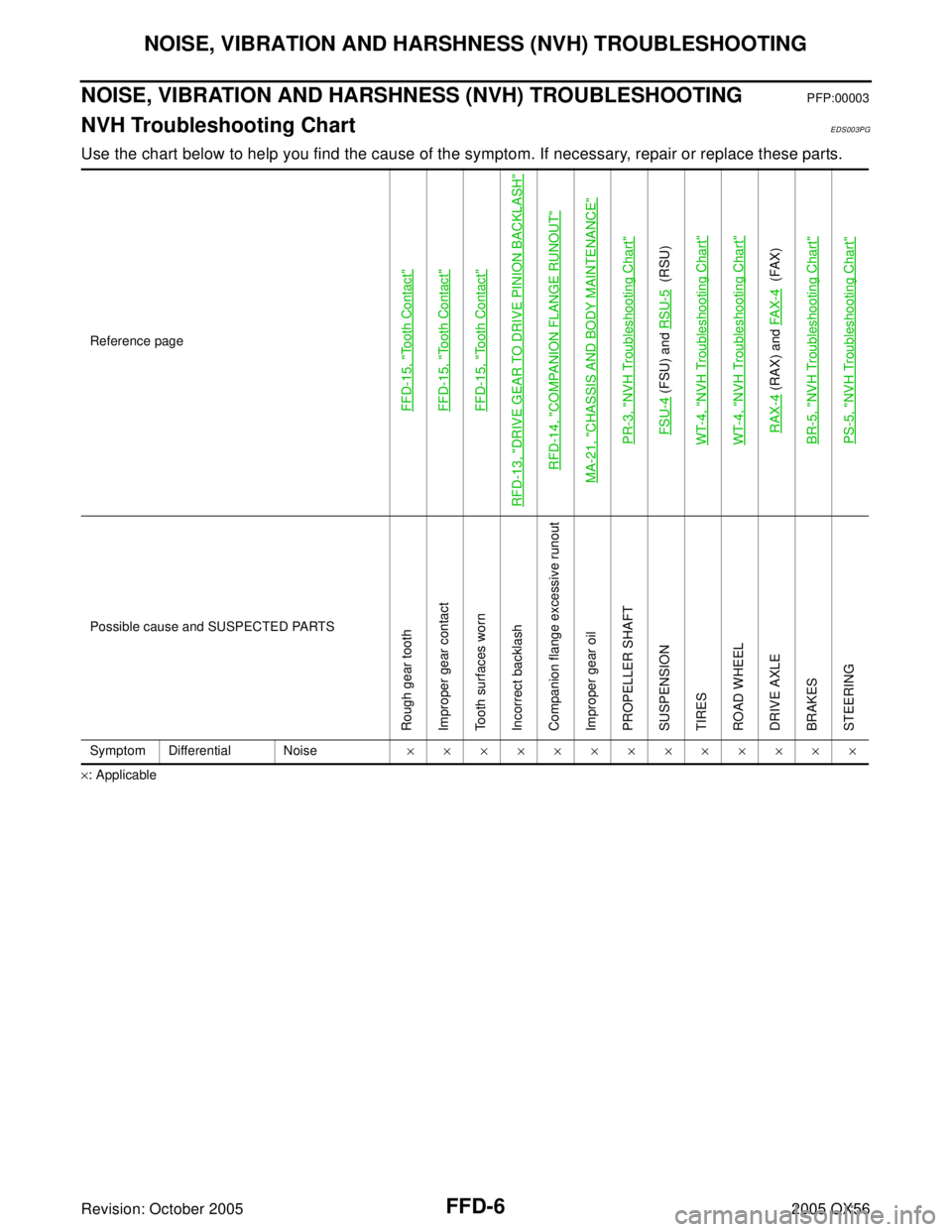
FFD-6
NOISE, VIBRATION AND HARSHNESS (NVH) TROUBLESHOOTING
Revision: October 20052005 QX56
NOISE, VIBRATION AND HARSHNESS (NVH) TROUBLESHOOTINGPFP:00003
NVH Troubleshooting ChartEDS003PG
Use the chart below to help you find the cause of the symptom. If necessary, repair or replace these parts.
×: ApplicableReference page
FFD-15, "
Tooth Contact
"
FFD-15, "
Tooth Contact
"
FFD-15, "
Tooth Contact
"
RFD-13, "
DRIVE GEAR TO DRIVE PINION BACKLASH
"
RFD-14, "
COMPANION FLANGE RUNOUT
"
MA-21, "
CHASSIS AND BODY MAINTENANCE
"
PR-3, "
NVH Troubleshooting Chart
"
FSU-4
(FSU) and RSU-5
(RSU)
WT-4, "
NVH Troubleshooting Chart
"
WT-4, "
NVH Troubleshooting Chart
"
RAX-4
(RAX) and FA X - 4
(FAX)
BR-5, "
NVH Troubleshooting Chart
"
PS-5, "
NVH Troubleshooting Chart
"
Possible cause and SUSPECTED PARTS
Rough gear tooth
Improper gear contact
Tooth surfaces worn
Incorrect backlash
Companion flange excessive runout
Improper gear oil
PROPELLER SHAFT
SUSPENSION
TIRES
ROAD WHEEL
DRIVE AXLE
BRAKES
STEERING
Symptom Differential Noise×××××××××××××
Page 2040 of 3419
SIDE OIL SEALS
FFD-9
C
E
F
G
H
I
J
K
L
MA
B
FFD
Revision: October 20052005 QX56
SIDE OIL SEALSPFP:33142
Removal and InstallationEDS003PI
REMOVAL
1. Remove front final drive. Refer to FFD-11, "REMOVAL" .
2. Remove differential side shaft and side flange using suitable
tool.
3. Place a small hole in seal case, using suitable punch or drill.
4. Remove seal using suitable tool as shown.
5. Installation is in the reverse order of removal.
BDIA0006E
LDIA0129E
LDIA0130E
Page 2044 of 3419
FRONT FINAL DRIVE ASSEMBLY
FFD-13
C
E
F
G
H
I
J
K
L
MA
B
FFD
Revision: October 20052005 QX56
Disassembly and AssemblyEDS003PL
COMPONENTS
1. Side bearing adjust nut 2. Side bearing 3. Side gear thrust washer
4. Side gear 5. Lock pin 6. Pinion mate thrust washer
7. Pinion mate gear 8. Pinion mate shaft 9. Drive pinion
10. Drive pinion height adjusting washer 11. Drive pinion rear bearing 12. Collapsible spacer
13. Breather tube 14. Differential side flange 15. Dust shield
16. Circular clip 17. Side oil seal 18. Drive pinion front bearing
19. Front oil seal 20. Companion flange 21. Drive pinion nut
22. Drain plug 23. Differential side shaft 24. Axle shaft bearing
25. Extension tube 26. O-ring 27. Gear carrier
28. Plate 29. Differential case 30. Drive gear
31. Side bearing cap 32. Filler plug 33. Rear cover
SDIA3207E
Page 2046 of 3419
FRONT FINAL DRIVE ASSEMBLY
FFD-15
C
E
F
G
H
I
J
K
L
MA
B
FFD
Revision: October 20052005 QX56
Tooth Contact
1. Remove rear cover. Refer to FFD-17, "Differential Assembly" .
2. Thoroughly clean drive gear and drive pinion teeth.
3. Lightly apply a mixture of powdered ferric oxide and oil or the
equivalent. Apply it to 3 or 4 teeth of drive gear drive side.
4. Rotate drive gear back and forth several times, check drive pin-
ion gear to drive gear tooth contact.
CAUTION:
Check tooth contact on drive side and reverse side.
SDIA2248E
SDIA2249E
SDIA1796E