Page 958 of 3419
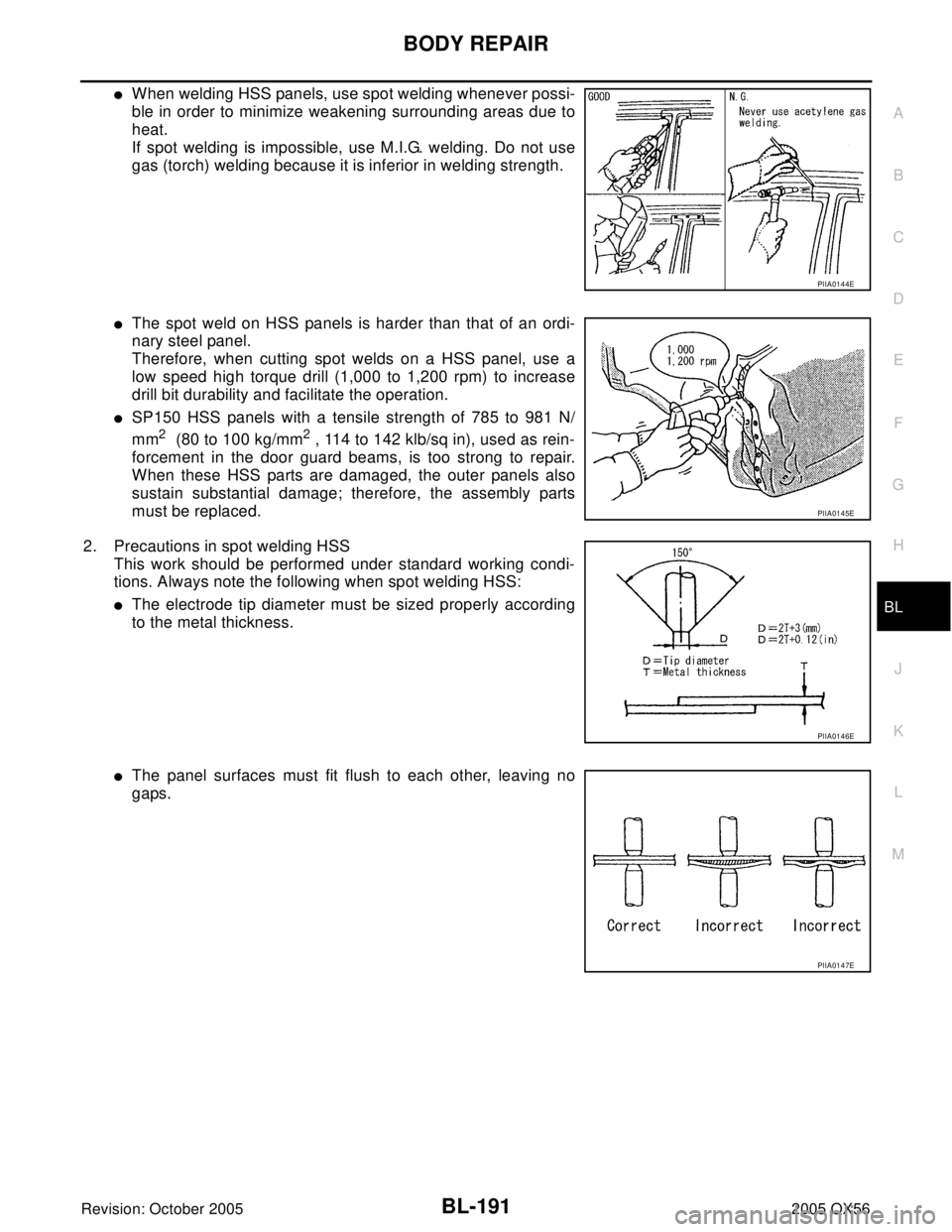
BODY REPAIR
BL-191
C
D
E
F
G
H
J
K
L
MA
B
BL
Revision: October 20052005 QX56
When welding HSS panels, use spot welding whenever possi-
ble in order to minimize weakening surrounding areas due to
heat.
If spot welding is impossible, use M.I.G. welding. Do not use
gas (torch) welding because it is inferior in welding strength.
The spot weld on HSS panels is harder than that of an ordi-
nary steel panel.
Therefore, when cutting spot welds on a HSS panel, use a
low speed high torque drill (1,000 to 1,200 rpm) to increase
drill bit durability and facilitate the operation.
SP150 HSS panels with a tensile strength of 785 to 981 N/
mm
2 (80 to 100 kg/mm2 , 114 to 142 klb/sq in), used as rein-
forcement in the door guard beams, is too strong to repair.
When these HSS parts are damaged, the outer panels also
sustain substantial damage; therefore, the assembly parts
must be replaced.
2. Precautions in spot welding HSS
This work should be performed under standard working condi-
tions. Always note the following when spot welding HSS:
The electrode tip diameter must be sized properly according
to the metal thickness.
The panel surfaces must fit flush to each other, leaving no
gaps.
PIIA0144E
PIIA0145E
PIIA0146E
PIIA0147E
Page 982 of 3419
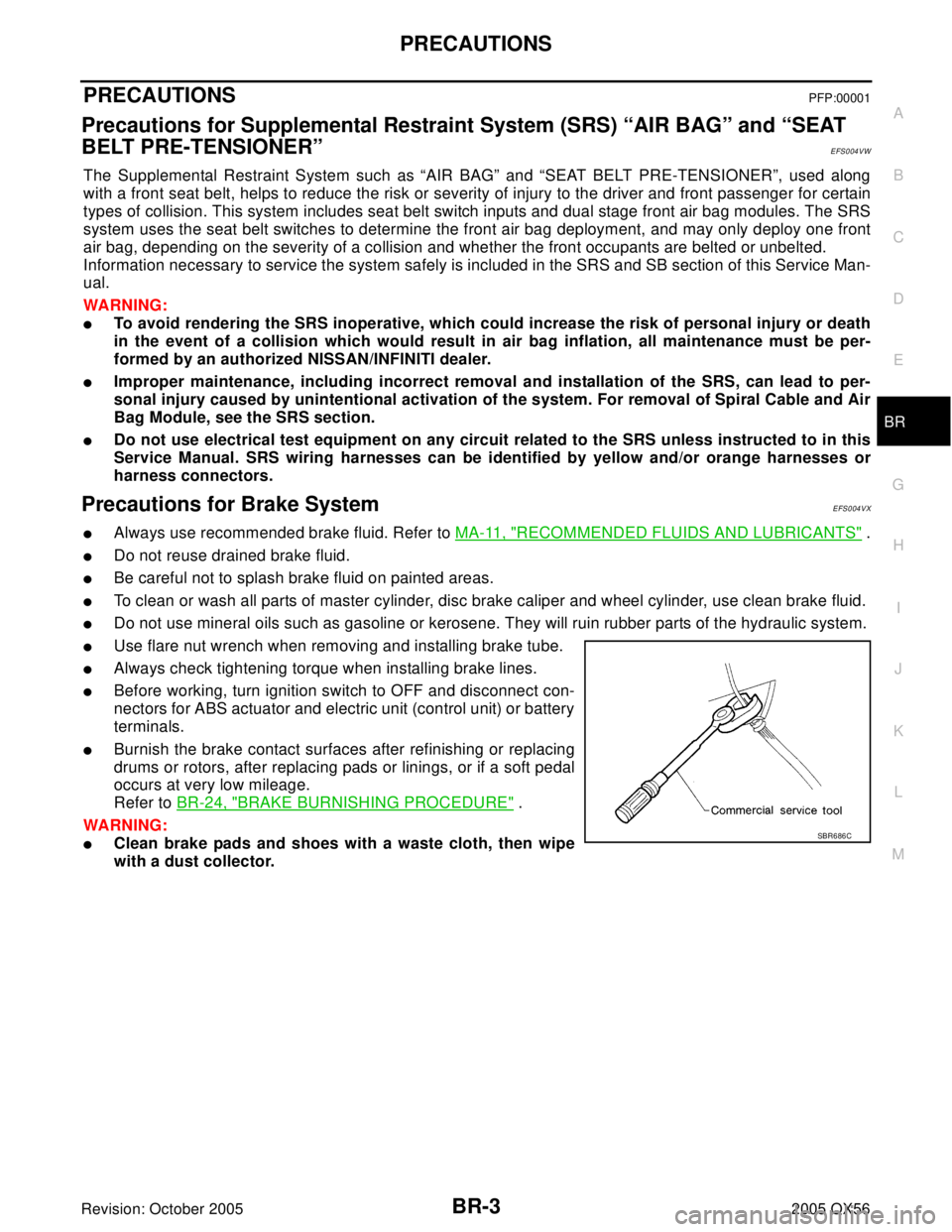
PRECAUTIONS
BR-3
C
D
E
G
H
I
J
K
L
MA
B
BR
Revision: October 20052005 QX56
PRECAUTIONSPFP:00001
Precautions for Supplemental Restraint System (SRS) “AIR BAG” and “SEAT
BELT PRE-TENSIONER”
EFS004VW
The Supplemental Restraint System such as “AIR BAG” and “SEAT BELT PRE-TENSIONER”, used along
with a front seat belt, helps to reduce the risk or severity of injury to the driver and front passenger for certain
types of collision. This system includes seat belt switch inputs and dual stage front air bag modules. The SRS
system uses the seat belt switches to determine the front air bag deployment, and may only deploy one front
air bag, depending on the severity of a collision and whether the front occupants are belted or unbelted.
Information necessary to service the system safely is included in the SRS and SB section of this Service Man-
ual.
WA RN ING:
To avoid rendering the SRS inoperative, which could increase the risk of personal injury or death
in the event of a collision which would result in air bag inflation, all maintenance must be per-
formed by an authorized NISSAN/INFINITI dealer.
Improper maintenance, including incorrect removal and installation of the SRS, can lead to per-
sonal injury caused by unintentional activation of the system. For removal of Spiral Cable and Air
Bag Module, see the SRS section.
Do not use electrical test equipment on any circuit related to the SRS unless instructed to in this
Service Manual. SRS wiring harnesses can be identified by yellow and/or orange harnesses or
harness connectors.
Precautions for Brake SystemEFS004VX
Always use recommended brake fluid. Refer to MA-11, "RECOMMENDED FLUIDS AND LUBRICANTS" .
Do not reuse drained brake fluid.
Be careful not to splash brake fluid on painted areas.
To clean or wash all parts of master cylinder, disc brake caliper and wheel cylinder, use clean brake fluid.
Do not use mineral oils such as gasoline or kerosene. They will ruin rubber parts of the hydraulic system.
Use flare nut wrench when removing and installing brake tube.
Always check tightening torque when installing brake lines.
Before working, turn ignition switch to OFF and disconnect con-
nectors for ABS actuator and electric unit (control unit) or battery
terminals.
Burnish the brake contact surfaces after refinishing or replacing
drums or rotors, after replacing pads or linings, or if a soft pedal
occurs at very low mileage.
Refer to BR-24, "
BRAKE BURNISHING PROCEDURE" .
WA RN ING:
Clean brake pads and shoes with a waste cloth, then wipe
with a dust collector.SBR6 86 C
Page 983 of 3419
BR-4
PREPARATION
Revision: October 20052005 QX56
PREPARATIONPFP:00002
Commercial Service ToolsEFS004VY
Tool nameDescription
1. Flare nut crowfoot
2. Torque wrenchRemoving and installing each brake
piping
a: 10mm (0.39 in)/12mm (0.47 in)
Power toolRemoving front and rear caliper as-
sembly, tires
S-NT360
PBIC0190E
PBIC0191E
Page 989 of 3419
BR-10
BRAKE FLUID
Revision: October 20052005 QX56
Bleeding Brake SystemEFS004W4
CAUTION:
While bleeding, pay attention to master cylinder fluid level.
1. Turn ignition switch OFF and disconnect ABS actuator and electric unit (control unit) connector or battery
negative cable.
2. Connect a vinyl tube to the rear right bleed valve.
3. Fully depress brake pedal 4 to 5 times.
4. With brake pedal depressed, loosen bleed valve to let the air out, and then tighten it immediately.
5. Repeat steps 3 and 4 until no more air comes out.
6. Tighten bleed valve to the specified torque. Refer to BR-20, "
Components" (front disc brake), BR-26,
"Components" (rear disc brake).
7. Repeat steps 2 through 6 at each wheel, with master cylinder reservoir tank filled at least half way, bleed
air in order from the front left, rear left, and front right bleed valves.
Page 996 of 3419
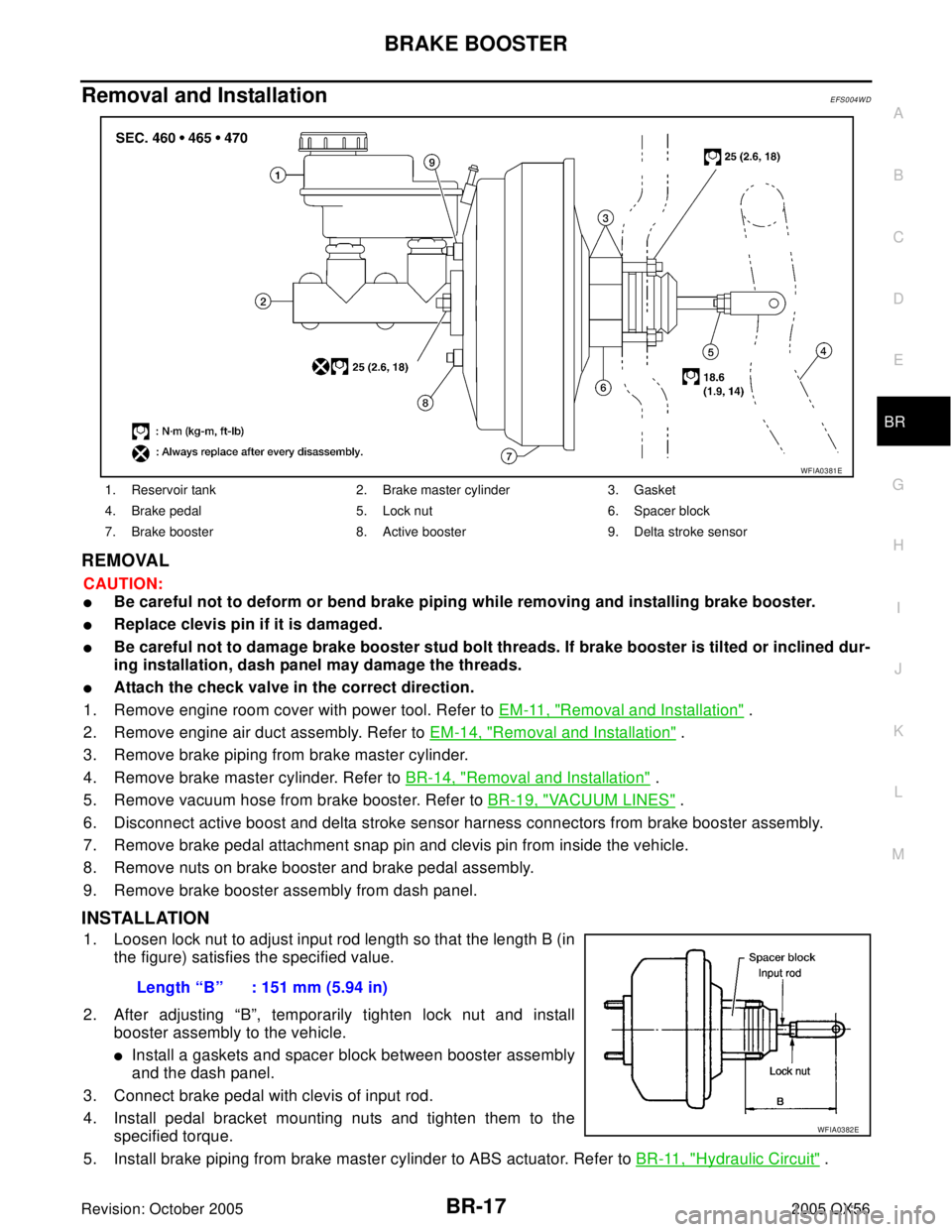
BRAKE BOOSTER
BR-17
C
D
E
G
H
I
J
K
L
MA
B
BR
Revision: October 20052005 QX56
Removal and InstallationEFS004WD
REMOVAL
CAUTION:
Be careful not to deform or bend brake piping while removing and installing brake booster.
Replace clevis pin if it is damaged.
Be careful not to damage brake booster stud bolt threads. If brake booster is tilted or inclined dur-
ing installation, dash panel may damage the threads.
Attach the check valve in the correct direction.
1. Remove engine room cover with power tool. Refer to EM-11, "
Removal and Installation" .
2. Remove engine air duct assembly. Refer to EM-14, "
Removal and Installation" .
3. Remove brake piping from brake master cylinder.
4. Remove brake master cylinder. Refer to BR-14, "
Removal and Installation" .
5. Remove vacuum hose from brake booster. Refer to BR-19, "
VACUUM LINES" .
6. Disconnect active boost and delta stroke sensor harness connectors from brake booster assembly.
7. Remove brake pedal attachment snap pin and clevis pin from inside the vehicle.
8. Remove nuts on brake booster and brake pedal assembly.
9. Remove brake booster assembly from dash panel.
INSTALLATION
1. Loosen lock nut to adjust input rod length so that the length B (in
the figure) satisfies the specified value.
2. After adjusting “B”, temporarily tighten lock nut and install
booster assembly to the vehicle.
Install a gaskets and spacer block between booster assembly
and the dash panel.
3. Connect brake pedal with clevis of input rod.
4. Install pedal bracket mounting nuts and tighten them to the
specified torque.
5. Install brake piping from brake master cylinder to ABS actuator. Refer to BR-11, "
Hydraulic Circuit" .
1. Reservoir tank 2. Brake master cylinder 3. Gasket
4. Brake pedal 5. Lock nut 6. Spacer block
7. Brake booster 8. Active booster 9. Delta stroke sensor
WFIA0381E
Length “B” : 151 mm (5.94 in)
WFIA0382E
Page 997 of 3419
BR-18
BRAKE BOOSTER
Revision: October 20052005 QX56
6. Connect active boost and delta stroke sensor harness connectors to brake booster assembly.
7. Connect vacuum hose to brake booster.
8. Install master cylinder to booster assembly. Refer to BR-17, "
Removal and Installation" .
9. Adjust the height and play of brake pedal.
10. Tighten lock nut of input rod to the specified torque.
11. Install engine air duct assembly. Refer to EM-14, "
Removal and Installation" .
12. Install engine room cover with power tool. Refer to EM-11, "
Removal and Installation" .
13. Refill with new brake fluid and bleed air. Refer to BR-10, "
Bleeding Brake System" .
Page 999 of 3419
BR-20
FRONT DISC BRAKE
Revision: October 20052005 QX56
FRONT DISC BRAKEPFP:41000
On-vehicle InspectionEFS004WG
PAD WEAR INSPECTION
Inspect the thickness of pad through cylinder body inspection
hole. Use a scale for inspection if necessary.
ComponentsEF S0 04 WH
Standard thickness : 11.88 mm (0.468 in)
Repair limit thickness : 1.0 mm (0.039 in)
BRA0010D
1. Upper sliding pin 2. Sliding pin boot 3. Torque member bolt
4. Torque member 5. Piston seal 6. Piston
7. Inner pad 8. Pad retainer 9. Outer pad
10. Piston boot 11. Union bolt 12. Copper washer
13. Sliding pin bolt 14. Bleed valve 15. Cylinder body
16. Cap 17. Brake hose 18. Lower sliding pin
19. Outer shim 20. Inner shim A. Wear indicator
⇐: Front
WFIA0451E
Page 1000 of 3419
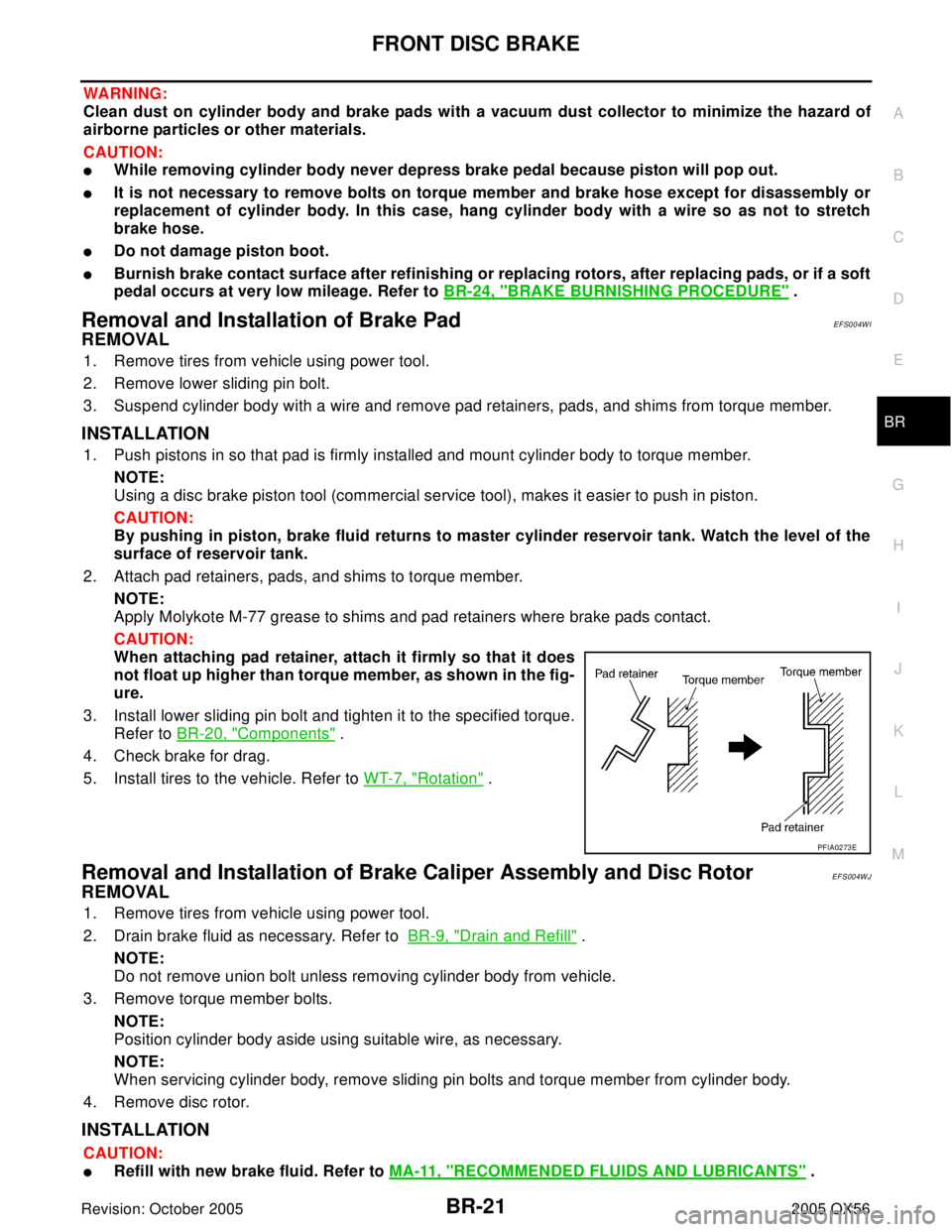
FRONT DISC BRAKE
BR-21
C
D
E
G
H
I
J
K
L
MA
B
BR
Revision: October 20052005 QX56
WA RN ING:
Clean dust on cylinder body and brake pads with a vacuum dust collector to minimize the hazard of
airborne particles or other materials.
CAUTION:
While removing cylinder body never depress brake pedal because piston will pop out.
It is not necessary to remove bolts on torque member and brake hose except for disassembly or
replacement of cylinder body. In this case, hang cylinder body with a wire so as not to stretch
brake hose.
Do not damage piston boot.
Burnish brake contact surface after refinishing or replacing rotors, after replacing pads, or if a soft
pedal occurs at very low mileage. Refer to BR-24, "
BRAKE BURNISHING PROCEDURE" .
Removal and Installation of Brake PadEFS004WI
REMOVAL
1. Remove tires from vehicle using power tool.
2. Remove lower sliding pin bolt.
3. Suspend cylinder body with a wire and remove pad retainers, pads, and shims from torque member.
INSTALLATION
1. Push pistons in so that pad is firmly installed and mount cylinder body to torque member.
NOTE:
Using a disc brake piston tool (commercial service tool), makes it easier to push in piston.
CAUTION:
By pushing in piston, brake fluid returns to master cylinder reservoir tank. Watch the level of the
surface of reservoir tank.
2. Attach pad retainers, pads, and shims to torque member.
NOTE:
Apply Molykote M-77 grease to shims and pad retainers where brake pads contact.
CAUTION:
When attaching pad retainer, attach it firmly so that it does
not float up higher than torque member, as shown in the fig-
ure.
3. Install lower sliding pin bolt and tighten it to the specified torque.
Refer to BR-20, "
Components" .
4. Check brake for drag.
5. Install tires to the vehicle. Refer to WT-7, "
Rotation" .
Removal and Installation of Brake Caliper Assembly and Disc RotorEFS004WJ
REMOVAL
1. Remove tires from vehicle using power tool.
2. Drain brake fluid as necessary. Refer to BR-9, "
Drain and Refill" .
NOTE:
Do not remove union bolt unless removing cylinder body from vehicle.
3. Remove torque member bolts.
NOTE:
Position cylinder body aside using suitable wire, as necessary.
NOTE:
When servicing cylinder body, remove sliding pin bolts and torque member from cylinder body.
4. Remove disc rotor.
INSTALLATION
CAUTION:
Refill with new brake fluid. Refer to MA-11, "RECOMMENDED FLUIDS AND LUBRICANTS" .
PFIA0273E