Page 1770 of 3419
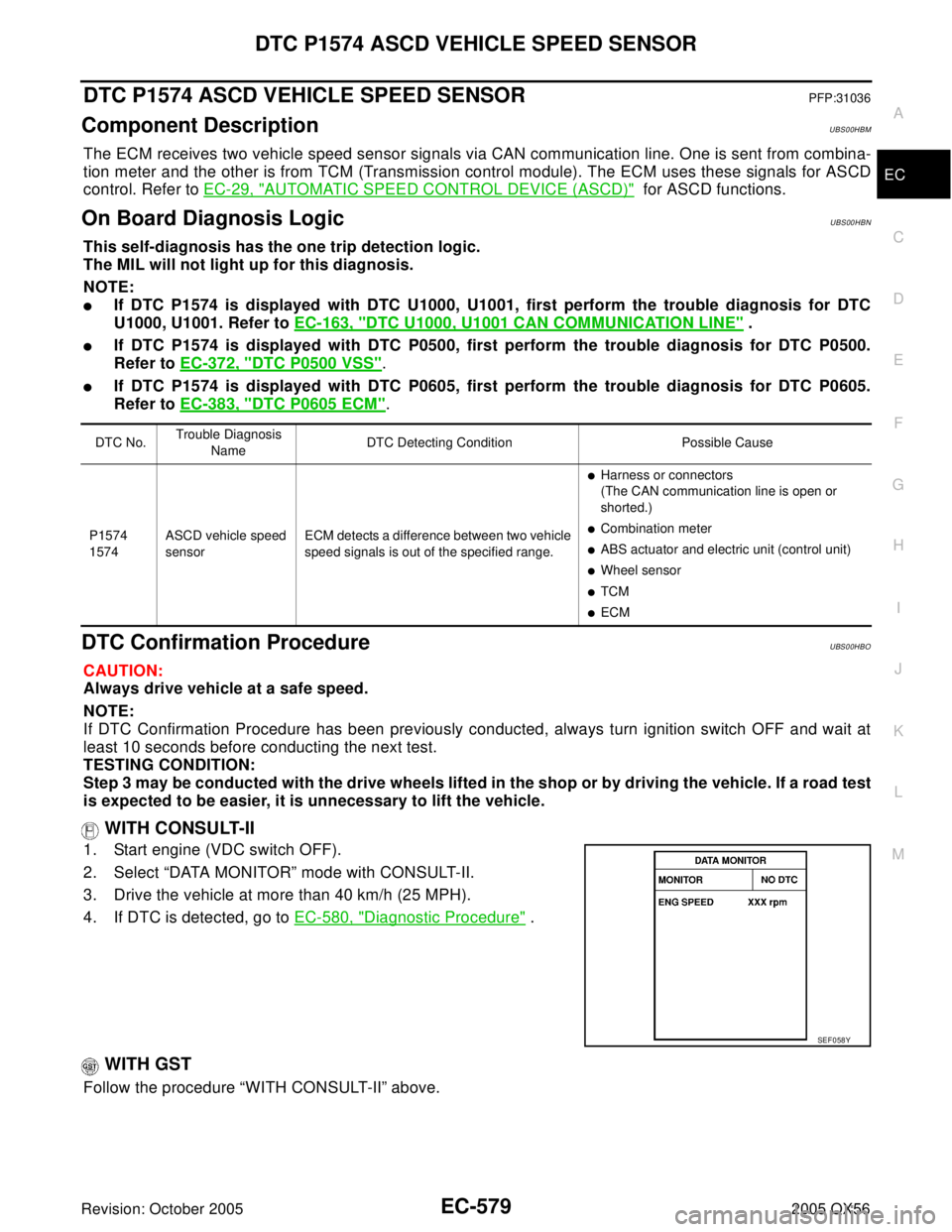
DTC P1574 ASCD VEHICLE SPEED SENSOR
EC-579
C
D
E
F
G
H
I
J
K
L
MA
EC
Revision: October 20052005 QX56
DTC P1574 ASCD VEHICLE SPEED SENSORPFP:31036
Component DescriptionUBS00HBM
The ECM receives two vehicle speed sensor signals via CAN communication line. One is sent from combina-
tion meter and the other is from TCM (Transmission control module). The ECM uses these signals for ASCD
control. Refer to EC-29, "
AUTOMATIC SPEED CONTROL DEVICE (ASCD)" for ASCD functions.
On Board Diagnosis LogicUBS00HBN
This self-diagnosis has the one trip detection logic.
The MIL will not light up for this diagnosis.
NOTE:
If DTC P1574 is displayed with DTC U1000, U1001, first perform the trouble diagnosis for DTC
U1000, U1001. Refer to EC-163, "
DTC U1000, U1001 CAN COMMUNICATION LINE" .
If DTC P1574 is displayed with DTC P0500, first perform the trouble diagnosis for DTC P0500.
Refer to EC-372, "
DTC P0500 VSS".
If DTC P1574 is displayed with DTC P0605, first perform the trouble diagnosis for DTC P0605.
Refer to EC-383, "
DTC P0605 ECM".
DTC Confirmation ProcedureUBS00HBO
CAUTION:
Always drive vehicle at a safe speed.
NOTE:
If DTC Confirmation Procedure has been previously conducted, always turn ignition switch OFF and wait at
least 10 seconds before conducting the next test.
TESTING CONDITION:
Step 3 may be conducted with the drive wheels lifted in the shop or by driving the vehicle. If a road test
is expected to be easier, it is unnecessary to lift the vehicle.
WITH CONSULT-II
1. Start engine (VDC switch OFF).
2. Select “DATA MONITOR” mode with CONSULT-II.
3. Drive the vehicle at more than 40 km/h (25 MPH).
4. If DTC is detected, go to EC-580, "
Diagnostic Procedure" .
WITH GST
Follow the procedure “WITH CONSULT-II” above.
DTC No.Trouble Diagnosis
NameDTC Detecting Condition Possible Cause
P1574
1574ASCD vehicle speed
sensorECM detects a difference between two vehicle
speed signals is out of the specified range.
Harness or connectors
(The CAN communication line is open or
shorted.)
Combination meter
ABS actuator and electric unit (control unit)
Wheel sensor
TCM
ECM
SEF 0 58 Y
Page 1771 of 3419
EC-580Revision: October 2005
DTC P1574 ASCD VEHICLE SPEED SENSOR
2005 QX56
Diagnostic ProcedureUBS00HBP
1. CHECK DTC WITH TCM
Check DTC with TCM. Refer to AT-37, "
OBD-II Diagnostic Trouble Code (DTC)" .
OK or NG
OK >> GO TO 2.
NG >> Perform trouble shooting relevant to DTC indicated.
2. CHECK DTC WITH ABS ACTUATOR AND ELECTRIC UNIT (CONTROL UNIT)
Refer to BRC-11, "
TROUBLE DIAGNOSIS" .
OK or NG
OK >> GO TO 3.
NG >> Repair or replace.
3. CHECK COMBINATION METER FUNCTION
Check combination meter function.
Refer to DI-5, "
COMBINATION METERS" .
>>INSPECTION END
Page 1782 of 3419
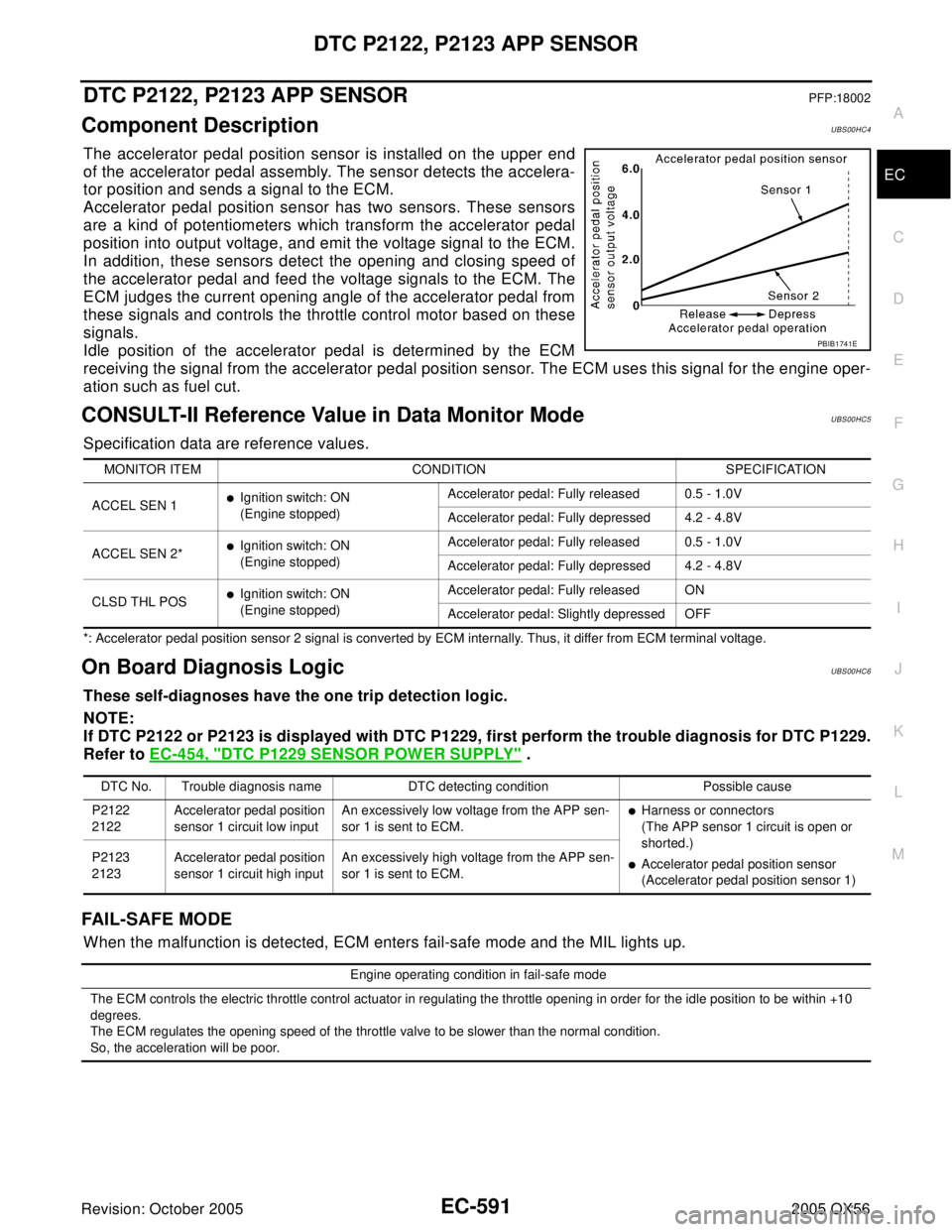
DTC P2122, P2123 APP SENSOR
EC-591
C
D
E
F
G
H
I
J
K
L
MA
EC
Revision: October 20052005 QX56
DTC P2122, P2123 APP SENSORPFP:18002
Component DescriptionUBS00HC4
The accelerator pedal position sensor is installed on the upper end
of the accelerator pedal assembly. The sensor detects the accelera-
tor position and sends a signal to the ECM.
Accelerator pedal position sensor has two sensors. These sensors
are a kind of potentiometers which transform the accelerator pedal
position into output voltage, and emit the voltage signal to the ECM.
In addition, these sensors detect the opening and closing speed of
the accelerator pedal and feed the voltage signals to the ECM. The
ECM judges the current opening angle of the accelerator pedal from
these signals and controls the throttle control motor based on these
signals.
Idle position of the accelerator pedal is determined by the ECM
receiving the signal from the accelerator pedal position sensor. The ECM uses this signal for the engine oper-
ation such as fuel cut.
CONSULT-II Reference Value in Data Monitor ModeUBS00HC5
Specification data are reference values.
*: Accelerator pedal position sensor 2 signal is converted by ECM internally. Thus, it differ from ECM terminal voltage.
On Board Diagnosis LogicUBS00HC6
These self-diagnoses have the one trip detection logic.
NOTE:
If DTC P2122 or P2123 is displayed with DTC P1229, first perform the trouble diagnosis for DTC P1229.
Refer to EC-454, "
DTC P1229 SENSOR POWER SUPPLY" .
FAIL-SAFE MODE
When the malfunction is detected, ECM enters fail-safe mode and the MIL lights up.
PBIB1741E
MONITOR ITEM CONDITION SPECIFICATION
ACCEL SEN 1
Ignition switch: ON
(Engine stopped)Accelerator pedal: Fully released 0.5 - 1.0V
Accelerator pedal: Fully depressed 4.2 - 4.8V
ACCEL SEN 2*
Ignition switch: ON
(Engine stopped)Accelerator pedal: Fully released 0.5 - 1.0V
Accelerator pedal: Fully depressed 4.2 - 4.8V
CLSD THL POS
Ignition switch: ON
(Engine stopped)Accelerator pedal: Fully released ON
Accelerator pedal: Slightly depressed OFF
DTC No. Trouble diagnosis name DTC detecting condition Possible cause
P2122
2122Accelerator pedal position
sensor 1 circuit low inputAn excessively low voltage from the APP sen-
sor 1 is sent to ECM.
Harness or connectors
(The APP sensor 1 circuit is open or
shorted.)
Accelerator pedal position sensor
(Accelerator pedal position sensor 1) P2123
2123Accelerator pedal position
sensor 1 circuit high inputAn excessively high voltage from the APP sen-
sor 1 is sent to ECM.
Engine operating condition in fail-safe mode
The ECM controls the electric throttle control actuator in regulating the throttle opening in order for the idle position to be within +10
degrees.
The ECM regulates the opening speed of the throttle valve to be slower than the normal condition.
So, the acceleration will be poor.
Page 1783 of 3419
EC-592Revision: October 2005
DTC P2122, P2123 APP SENSOR
2005 QX56
DTC Confirmation ProcedureUBS00HC7
NOTE:
If DTC Confirmation Procedure has been previously conducted, always turn ignition switch OFF and wait at
least 10 seconds before conducting the next test.
TESTING CONDITION:
Before performing the following procedure, confirm that battery voltage is more than 8V at idle.
WITH CONSULT-II
1. Turn ignition switch ON.
2. Select “DATA MONITOR” mode with CONSULT-II.
3. Start engine and let it idle for 1 second.
4. If DTC is detected, go to EC-594, "
Diagnostic Procedure" .
WITH GST
Follow the procedure “WITH CONSULT-II” above.
SEF 0 58 Y
Page 1784 of 3419
DTC P2122, P2123 APP SENSOR
EC-593
C
D
E
F
G
H
I
J
K
L
MA
EC
Revision: October 20052005 QX56
Wiring DiagramUBS00HC8
BBWA1706E
Page 1785 of 3419
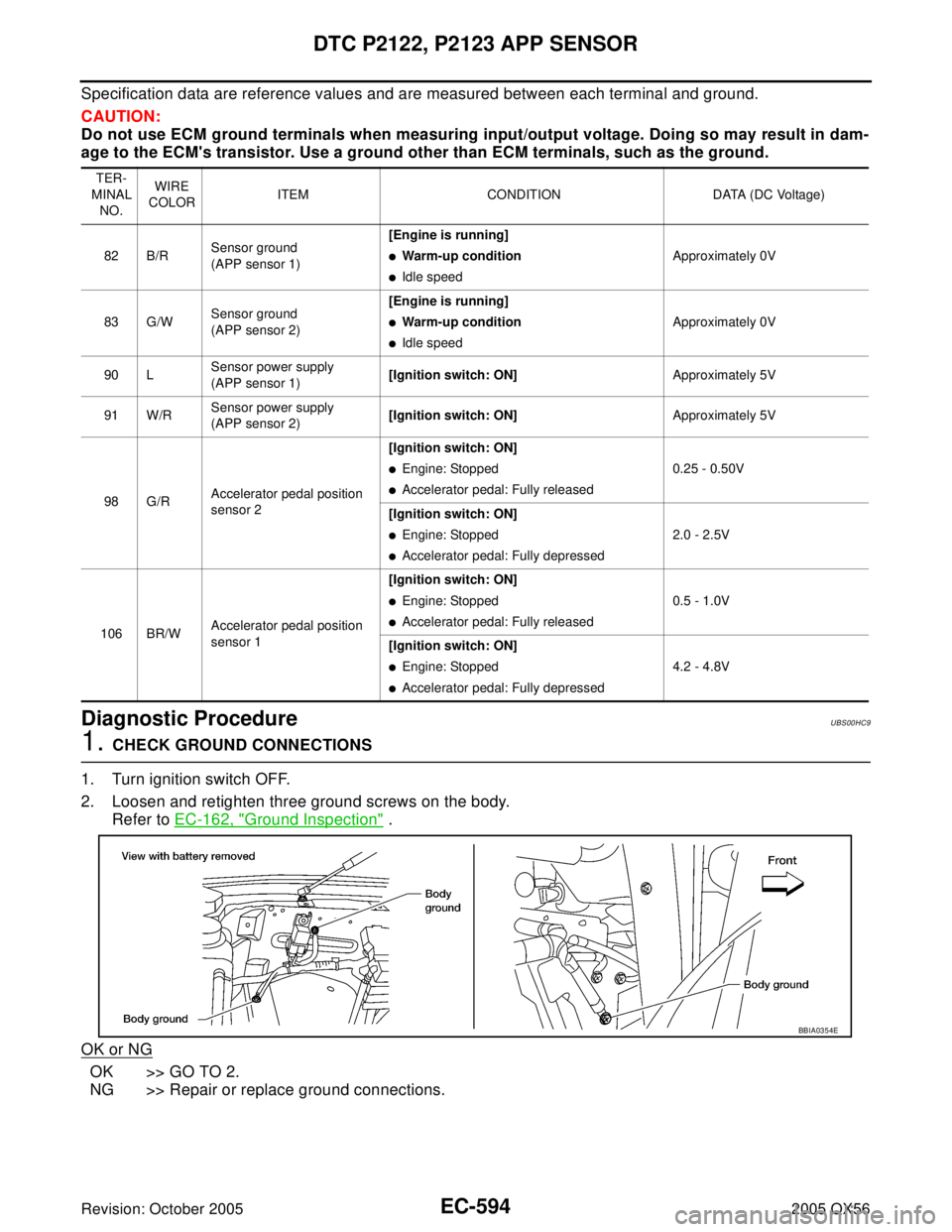
EC-594Revision: October 2005
DTC P2122, P2123 APP SENSOR
2005 QX56
Specification data are reference values and are measured between each terminal and ground.
CAUTION:
Do not use ECM ground terminals when measuring input/output voltage. Doing so may result in dam-
age to the ECM's transistor. Use a ground other than ECM terminals, such as the ground.
Diagnostic ProcedureUBS00HC9
1. CHECK GROUND CONNECTIONS
1. Turn ignition switch OFF.
2. Loosen and retighten three ground screws on the body.
Refer to EC-162, "
Ground Inspection" .
OK or NG
OK >> GO TO 2.
NG >> Repair or replace ground connections.
TER-
MINAL
NO.WIRE
COLORITEM CONDITION DATA (DC Voltage)
82 B/RSensor ground
(APP sensor 1)[Engine is running]
Warm-up condition
Idle speedApproximately 0V
83 G/WSensor ground
(APP sensor 2)[Engine is running]
Warm-up condition
Idle speedApproximately 0V
90 LSensor power supply
(APP sensor 1)[Ignition switch: ON]Approximately 5V
91 W/RSensor power supply
(APP sensor 2)[Ignition switch: ON]Approximately 5V
98 G/RAccelerator pedal position
sensor 2[Ignition switch: ON]
Engine: Stopped
Accelerator pedal: Fully released0.25 - 0.50V
[Ignition switch: ON]
Engine: Stopped
Accelerator pedal: Fully depressed2.0 - 2.5V
106 BR/WAccelerator pedal position
sensor 1[Ignition switch: ON]
Engine: Stopped
Accelerator pedal: Fully released0.5 - 1.0V
[Ignition switch: ON]
Engine: Stopped
Accelerator pedal: Fully depressed4.2 - 4.8V
BBIA0354E
Page 1786 of 3419
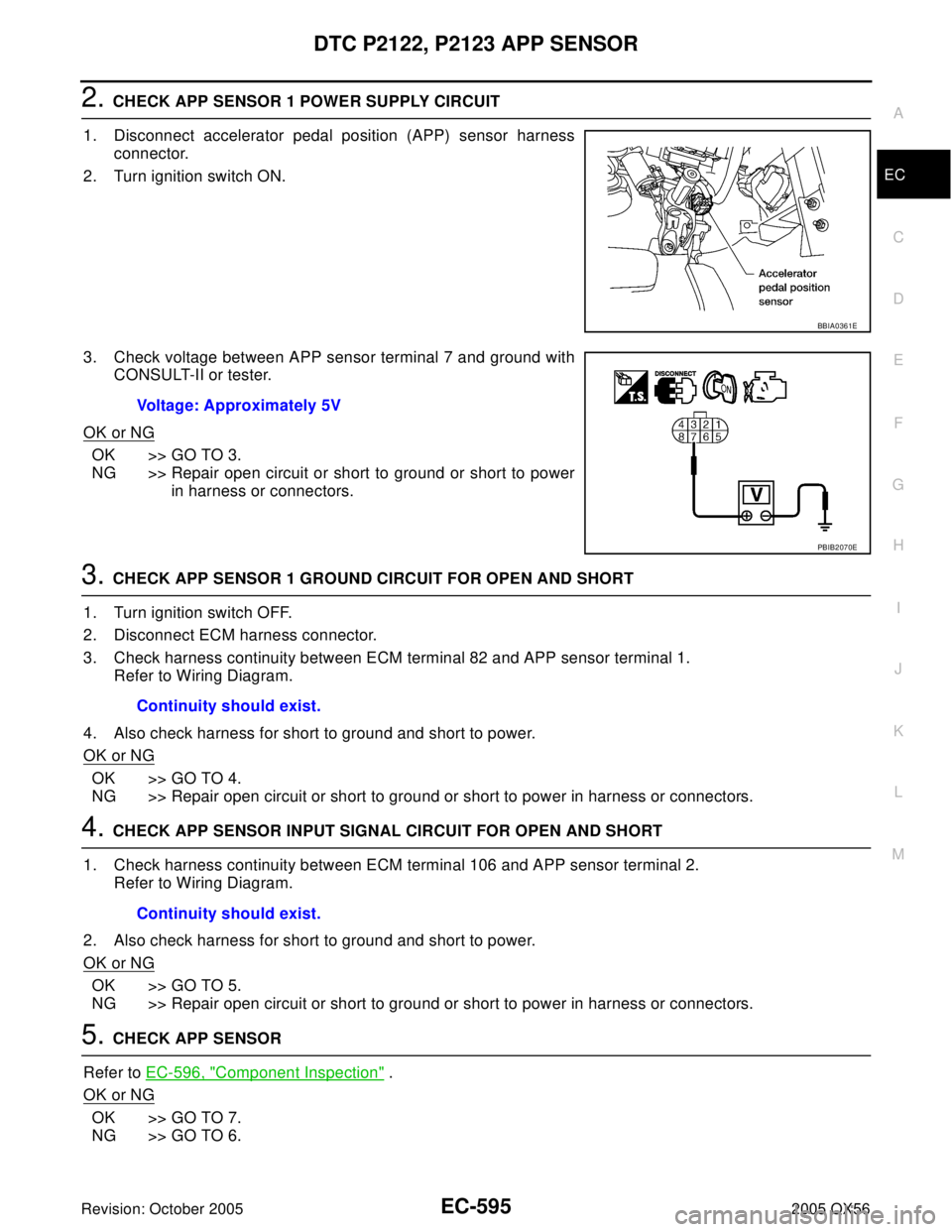
DTC P2122, P2123 APP SENSOR
EC-595
C
D
E
F
G
H
I
J
K
L
MA
EC
Revision: October 20052005 QX56
2. CHECK APP SENSOR 1 POWER SUPPLY CIRCUIT
1. Disconnect accelerator pedal position (APP) sensor harness
connector.
2. Turn ignition switch ON.
3. Check voltage between APP sensor terminal 7 and ground with
CONSULT-II or tester.
OK or NG
OK >> GO TO 3.
NG >> Repair open circuit or short to ground or short to power
in harness or connectors.
3. CHECK APP SENSOR 1 GROUND CIRCUIT FOR OPEN AND SHORT
1. Turn ignition switch OFF.
2. Disconnect ECM harness connector.
3. Check harness continuity between ECM terminal 82 and APP sensor terminal 1.
Refer to Wiring Diagram.
4. Also check harness for short to ground and short to power.
OK or NG
OK >> GO TO 4.
NG >> Repair open circuit or short to ground or short to power in harness or connectors.
4. CHECK APP SENSOR INPUT SIGNAL CIRCUIT FOR OPEN AND SHORT
1. Check harness continuity between ECM terminal 106 and APP sensor terminal 2.
Refer to Wiring Diagram.
2. Also check harness for short to ground and short to power.
OK or NG
OK >> GO TO 5.
NG >> Repair open circuit or short to ground or short to power in harness or connectors.
5. CHECK APP SENSOR
Refer to EC-596, "
Component Inspection" .
OK or NG
OK >> GO TO 7.
NG >> GO TO 6.
BBIA0361E
Voltage: Approximately 5V
PBIB2070E
Continuity should exist.
Continuity should exist.
Page 1787 of 3419
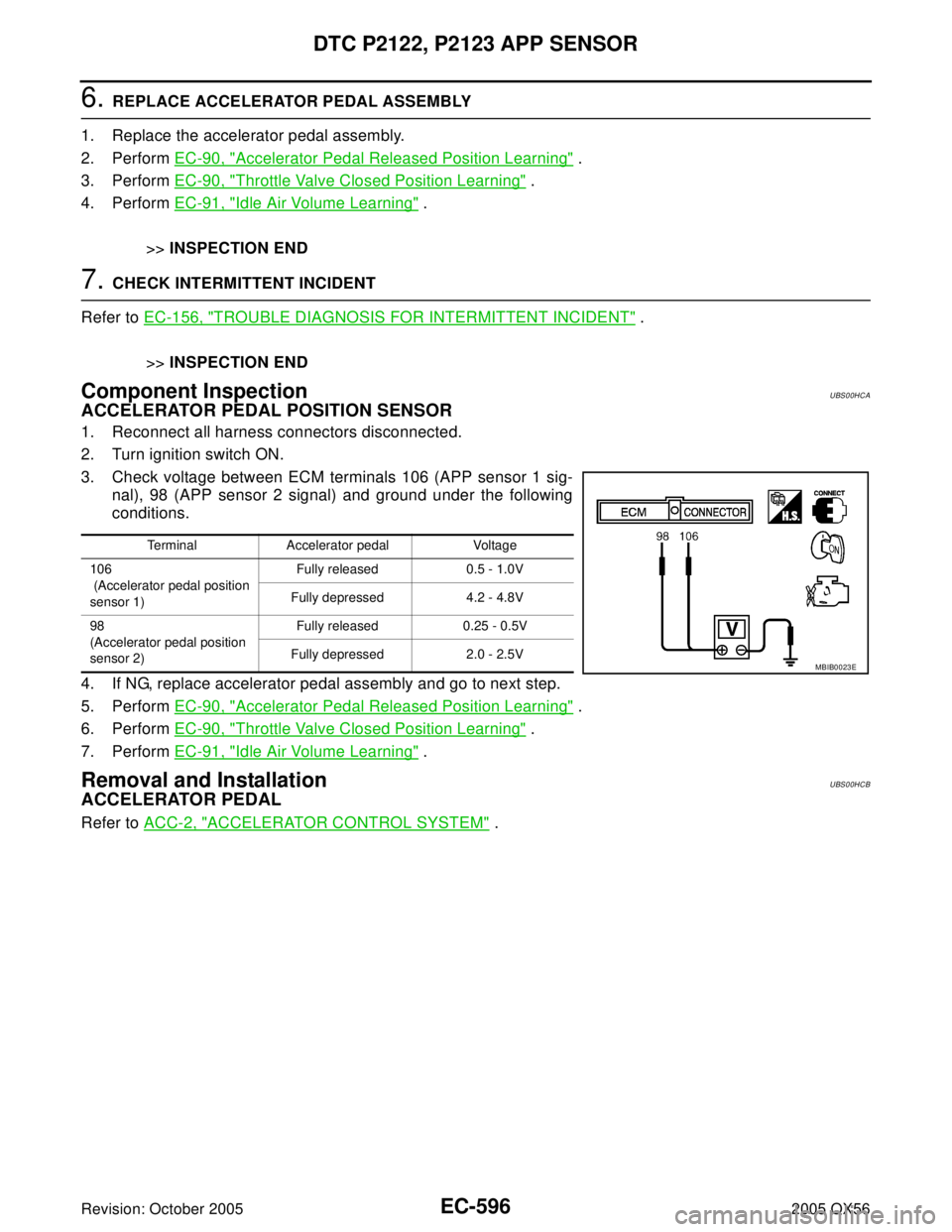
EC-596Revision: October 2005
DTC P2122, P2123 APP SENSOR
2005 QX56
6. REPLACE ACCELERATOR PEDAL ASSEMBLY
1. Replace the accelerator pedal assembly.
2. Perform EC-90, "
Accelerator Pedal Released Position Learning" .
3. Perform EC-90, "
Throttle Valve Closed Position Learning" .
4. Perform EC-91, "
Idle Air Volume Learning" .
>>INSPECTION END
7. CHECK INTERMITTENT INCIDENT
Refer to EC-156, "
TROUBLE DIAGNOSIS FOR INTERMITTENT INCIDENT" .
>>INSPECTION END
Component InspectionUBS00HCA
ACCELERATOR PEDAL POSITION SENSOR
1. Reconnect all harness connectors disconnected.
2. Turn ignition switch ON.
3. Check voltage between ECM terminals 106 (APP sensor 1 sig-
nal), 98 (APP sensor 2 signal) and ground under the following
conditions.
4. If NG, replace accelerator pedal assembly and go to next step.
5. Perform EC-90, "
Accelerator Pedal Released Position Learning" .
6. Perform EC-90, "
Throttle Valve Closed Position Learning" .
7. Perform EC-91, "
Idle Air Volume Learning" .
Removal and InstallationUBS00HCB
ACCELERATOR PEDAL
Refer to ACC-2, "ACCELERATOR CONTROL SYSTEM" .
Terminal Accelerator pedal Voltage
106
(Accelerator pedal position
sensor 1)Fully released 0.5 - 1.0V
Fully depressed 4.2 - 4.8V
98
(Accelerator pedal position
sensor 2)Fully released 0.25 - 0.5V
Fully depressed 2.0 - 2.5V
MBIB0023E